FGB法船体曲面板高效焊接工艺方法
船舶曲面板列焊接自动化

船舶曲面板列焊接自动化李高进;伍朝晖;徐宝东;杨龙飞;苏娟娟;张剑锋【摘要】探讨采用定点支柱式可调曲形胎架、两轴旋转变位胎架和机械自动化焊接装备组成的模拟系统,以实现曲面板列自动化焊接工艺技术.采用自动化焊接小车,使其与可调曲形胎架协调运行,在胎架调节中运用比例-积分-微分(Proportion Integral Derivative,PID)控制技术,实时将曲面板列焊接的位置由大倾斜位置变为平位置,实现曲面板列的自动化焊接.【期刊名称】《造船技术》【年(卷),期】2017(000)002【总页数】5页(P68-72)【关键词】曲面板列;协调运行;PID控制技术;平位置【作者】李高进;伍朝晖;徐宝东;杨龙飞;苏娟娟;张剑锋【作者单位】上海船舶工艺研究所,上海200032;江南造船(集团)有限责任公司,上海201913;上海船舶工艺研究所,上海200032;江南造船(集团)有限责任公司,上海201913;上海船舶工艺研究所,上海200032;上海船舶工艺研究所,上海200032【正文语种】中文【中图分类】U671目前,焊接工时和成本各占船体建造工时和成本的30% ~50%[1],焊接技术水平的高低决定了造船质量的优劣。
在船体焊接生产设计中,确定焊接位置、正确选择焊接方法、使用合适的焊接材料和焊接设备,对提高生产效率、缩短造船周期、提高焊接质量以及降低焊接成本都具有重要意义[2] 。
船舶的船体建造以分段为基本建造单元,1艘船舶可由数十至数百个分段组成。
分段的形状大致可分为2类:曲面分段(主要是船艏、艉部以及舰船的大部分)和平直分段(主要是大型民用船舯部分)。
平直分段基本是矩形结构,焊缝趋于直线性,大多为平直焊缝,有利于实施机械自动化焊接。
船舶焊接质量是评价造船质量的重要指标,焊接生产效率是影响造船产量与生产成本的主要因素之一 [3] 。
为了提高船舶焊接质量,自20世纪90年代起,我国主要造船企业就陆续引进数十条平面分段生产流水线,用于平直分段的生产。
双底双壳船大接缝焊接方法(精)

双底双壳船大接缝焊接方法
1、FAB法:FAB焊接工艺是一项先进的技术,它是利用单丝自动埋弧焊机单面焊达到双面成型的效果,克服了大型分段进行双面焊接引发的翻身、起重等突出难题。
2、船体大接缝焊接:由于船体分段(结构分段)大合拢后各接缝所处的位置不同,有平、立、横等对接缝,也有各种位置的角接缝,因而所选用的焊接方法也不同。
3、陶质衬垫焊接:陶质衬垫焊接技术是一种以特殊陶质材料为衬托,正面焊接、反面强制成型的焊接方法。
陶质衬垫焊是以焊接材料(焊丝、焊剂、药芯)、衬垫为基础,采用配套的焊接方法组成的一个相关联的焊接工艺。
不同的焊接方法和焊接材料需要有适合的陶质衬垫相配合,才能满足各种焊接的设计要求。
4、立对接焊:根据板厚不同,可以分别采用向下立焊和向上立焊。
前者用于薄板和不要求强度的地方。
而后者主要用于厚度大于6mm的工件。
船舶行业拼板高效焊接技术_图文

船舶行业拼板高效焊接技术概述船舶制造涉及大量拼板工作,在船体等大型构件的制造过程中,拼板连接是非常重要的环节。
常见的拼板连接方式有钉接、焊接、铆接等,其中以焊接为主要方式。
传统的手动电弧焊接需要高技能的操作工人,效率低、质量难以稳定保证,热影响区大,还容易产生缺陷、质量问题,影响了整个船舶生产的进度和质量。
因此,在船舶制造中引入高效的自动化焊接技术已经成为了拼板连接的主流方式,有助于提高生产效率和质量,大大降低生产成本。
拼板高效焊接技术分类1.MAG焊接(金属活性气体保护焊接)主要用于船体板焊接,最大焊接速度可达15m/min,高效性得到广泛认可。
2.MIG焊接(惰性气体保护焊接)主要用于钢架等小型元器件焊接,适用于多种种类的金属材料,可控性较MAG 焊接更强。
工艺特点高效自动化焊接,一般采用龙门式自动焊接机进行生产效率高,成本低廉,同时焊接质量可控,无需高技能的焊接人员。
质量高传统的手动焊接技术难以保证焊接质量,但是自动化焊接技术的应用,使得焊接质量更加即得可靠,同时焊接的热影响区域小,对焊接件本身的材质影响也较低。
环保自动化焊接技术一般采用环保型焊接材料,减少了焊接产生的气体和化学物质排放对环境污染的危害,更美观,符合环保要求。
切换快自动化焊接机还可实现不同焊接工艺间的快速切换,且在同一焊缝内可实现不同工艺的焊接进行,具有非常大的灵活性。
发展趋势未来,随着船舶制造技术的不断进步,高效焊接技术将会更广泛应用。
据行业专家预测,龙门式自动化焊接机将逐渐被弯臂式自动化焊接机所替代,其具有更好的定位精度,更高的稳定性和一定的灵活性。
同时,焊接机器人也将更多应用于船舶制造中,实现现场全自动化在线焊接,将为船舶制造工业增添一道亮丽的风景线。
船体焊接工艺

船体焊接工艺船体焊接工艺规程一、执行标准CB/T3195-95《中小型船舶船体建造精度》CB999-82《船体焊缝表面质量检验》CB/T3761-1996《船体结构焊缝缺陷修补技术要求》二、职责焊工职责:A从事船舶焊接的电焊工必须培训,参加舰艇建造的电焊工必须持有中华人民共和国船检局印发的《焊工合格证书》,方能上岗。
B持证焊工应严格安装资格证书规定的工作范围进行施工,并应随时接受检查人员对焊工资格证书的检查。
C焊工在焊前应检查焊缝装配是否满足标准和焊接工艺的要求,未达到要求禁止施焊。
D按焊接工艺的要求领取和使用焊接材料。
E按焊接工艺规定的焊接参数和焊接顺序进行焊接。
F焊后应对焊缝表面及两边的熔渣及飞溅进行清理,并自检焊缝表面质量。
G对互检、专检认为不合格焊缝进行修补。
H每天施工结束后,对施工现场进行清扫,焊条头回收,剩余低氢焊条返回仓库,非低氢焊条放在干燥不易受潮处。
三、环境、设备、材料控制(1)环境要求A环境温度低于负5摄氏度时,施焊时必须采取一定的低温焊接措施,可用氧一乙火焰对焊缝进行70—100℃预热。
B室外焊接作业风力大于4级风时,应采取适当的挡风措施。
(2)材料要求焊接用材料要严格按设计要求选取,焊接材料应具有出厂合格证等必要的质量证明。
四、焊接前的准备1、焊接之前应对焊条进行烘焙,常用焊条烘焙温度、时间和保存温度见下表药皮类型焊条牌号烘焙温度时间(分)保存温度氧化钛钙结422 150-200 30-60低氢结506,结507 300-350 60-90 1002、对要焊接的构件装配精度进行检验,确定无误方可开始焊接。
3、对装配时的定位焊接进行检查,对有缺陷的定位焊,可在其前后用定位焊固定,然后气刨或风铲去除有缺陷的定位焊。
4、施焊前将焊缝两侧各30mm表面清理干净,要求无水、无锈、无油污、无氧化铁、无冰雪等。
5、焊前焊工应明确图纸中的焊接技术要求及焊接尺寸。
6、电焊工常备工具:手锤、扁铲、尖锤、刷帚、粉笔、钢丝刷子、焊条箱。
FGB法船体曲面板高效焊接工艺方法

说明书摘要本发明公开了一种船体曲面板高效焊接工艺方法,其包括以下步骤:S1、曲面板胎位布置阶段:将若干曲面板分布在胎架上,按照严格的精度要求进行定位,并对焊缝进行点焊固定;S2、焊接前期准备阶段:焊缝V型坡口的角度要按照一定要求,坡口附近20mm区域清理干净。
两块板焊缝底部距离按要求严格控制。
引熄弧板要安装好,另外对于预热温度的规定要求是当周围环境温度低于0℃时需要进行预热;S3、衬垫安装以及焊缝布置阶段:焊接试板装配完成之后要按照要求进行衬垫的安装及铁粉的铺设;S4、焊接过程阶段:焊接过程中要注意按要求控制焊接电流、电压和焊接速度等参数,焊后需让板冷却6小时。
本发明大大缩短了船体曲面板拼板焊接周期,可以将大量的减少辅助焊接工具的使用;同时提高了焊接自动化率,减少了人力资源的浪费。
权利要求书1、一种船体总段移位方法,其特征在于,其包括以下步骤:S1、曲面板胎位布置阶段:将若干曲面板分布在胎架上,按照严格的精度要求进行定位,并对焊缝进行点焊固定;S2、焊接前期准备阶段:焊缝V型坡口的角度要按照一定要求,坡口附近20mm区域清理干净。
两块板焊缝底部距离按要求严格控制。
引熄弧板要安装好,另外对于预热温度的规定要求是当周围环境温度低于0℃时需要进行预热;S3、衬垫安装以及焊缝布置阶段:焊接试板装配完成之后要按照要求进行衬垫的安装及铁粉的铺设;S4、焊接过程阶段:焊接过程中要注意按要求控制焊接电流、电压和焊接速度等参数,焊后需让板冷却6小时。
2、如权利要求1所述的船体曲面板焊接工艺方法,其特征在于,步骤S2中,通常坡口形式为V型坡口,角度为40o。
焊件装配时板材必须放平整,装配间隙最大不能超过3mm。
采用尺寸为250mm×300mm的弹性引熄弧板,板厚与母材相同或正负2mm以内。
3、如权利要求1所述的船体曲面板焊接工艺方法,其特征在于,步骤S3中,所述FGB法选用的衬垫必须是专用的、特殊的衬垫。
船体曲面外板装配工艺流程
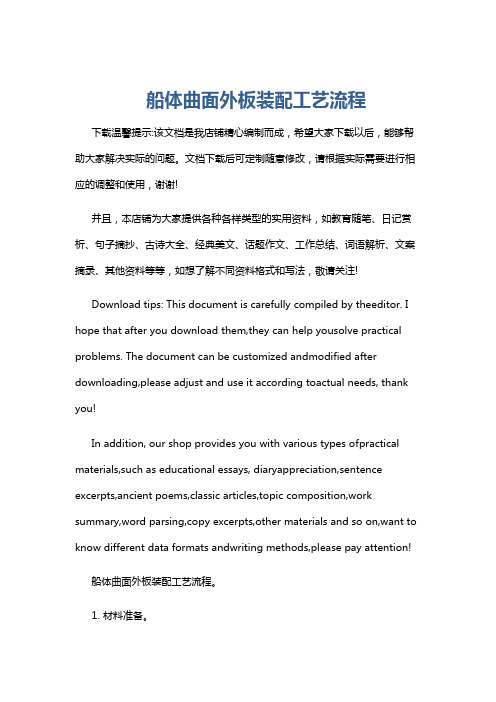
船体曲面外板装配工艺流程下载温馨提示:该文档是我店铺精心编制而成,希望大家下载以后,能够帮助大家解决实际的问题。
文档下载后可定制随意修改,请根据实际需要进行相应的调整和使用,谢谢!并且,本店铺为大家提供各种各样类型的实用资料,如教育随笔、日记赏析、句子摘抄、古诗大全、经典美文、话题作文、工作总结、词语解析、文案摘录、其他资料等等,如想了解不同资料格式和写法,敬请关注!Download tips: This document is carefully compiled by theeditor. I hope that after you download them,they can help yousolve practical problems. The document can be customized andmodified after downloading,please adjust and use it according toactual needs, thank you!In addition, our shop provides you with various types ofpractical materials,such as educational essays, diaryappreciation,sentence excerpts,ancient poems,classic articles,topic composition,work summary,word parsing,copy excerpts,other materials and so on,want to know different data formats andwriting methods,please pay attention!船体曲面外板装配工艺流程。
1. 材料准备。
根据图纸要求,准备所需的曲面外板、龙骨、肋骨等材料。
船舶高效焊接工艺及装备
1 概述焊接技术是船舶建造工程的关键工艺技术,是建立现代造船模式的支撑技术。
焊接技术的发展带动了造船技术的进步。
20世纪初,由于船舶业引进了焊接技术,造船模式由整体拼装发展到分段建造,使大型和巨型船舶得以顺利建造。
高效焊接技术对船舶建造具有特别重要的意义。
船舶结构复杂,服役条件苛刻,且为全焊接结构。
船体建造中焊接工作量约占70%,焊接成本约占船体建造总成本的30%~50%。
因此,在船舶建造过程中通过高效焊接手段来满足缩短建造周期、降低建造成本的需求,同时保证良好的焊接质量。
实现高效焊接的基本途径有:(1)提高焊接熔敷效率,如采用多丝焊、垂直气电焊、搅拌摩擦焊等。
(2)减少坡口断面及熔敷金属量,如采用窄间隙焊、激光复合焊等。
(3)自动化焊接,如采用生产线、机器人焊接等。
2 船舶高效焊接工艺及装备发展现状纵观国内外船舶建造企业的造船模式,主要流程基本相同,为零件→部件→分段→总段→船台(坞)搭载。
与此相对应的,所采用的焊接技术及装备也是大同小异。
在部件、分段、总段等中间产品的生产制造阶段采用自动化程度很高的大型焊接生产装置(流水线),在船台(坞)搭载时则采用单机自动化焊接设备。
所不同的是,国外先进造船企业擅于和敢于将更多先进的高效焊接技术应用到实际生产中,所采用的高效焊接设备自动化、智能化程度更高。
2.1 国外船舶高效焊接工艺及装备发展情况2.1.1 日本日本造船焊接技术的发展历经简易机械化、机械自动化和机器人智能化三个阶段,利用各种先进的焊接设备实现高效的焊接工艺。
从1970年代开始发展半自动CO2气保护焊取代手工焊条电弧焊为第一阶段;从1980年代末开始发展独立台车形式的焊接设备为第二阶段,采用MAG焊接工艺,通过跟踪或仿形焊缝自动完成焊接,焊接效率成倍甚至数倍提高,焊接质量优良,有效地控制了焊接变形和提高船体建造精度,焊接工人劳动强度和环境得到很大改善。
1995年神户制钢和NKK津船厂合作开发世界上第一套造船焊接机器人系统并用于小合拢生产标志着第三阶段的开始。
船厂的板缝焊接工艺流程
船厂的板缝焊接工艺流程船厂的板缝焊接工艺流程是指在船舶制造过程中,对船体板材的焊接工艺流程。
船体板材焊接是船舶制造中的一项关键工艺,直接关系到船体的强度和密封性能。
下面将详细介绍船厂的板缝焊接工艺流程。
船厂进行焊接前的准备工作。
这包括对焊接设备的检查和准备,确保设备正常运行;对工作场地进行清洁和整理,确保焊接环境安全和整洁;对板材进行检查和准备,包括清洁表面、切割板材等。
第二步是焊缝的准备。
在板材上标记焊缝的位置和长度,并根据焊接要求进行切割和准备。
通常情况下,船厂采用等离子切割、气割或机械切割等方法进行焊缝的准备。
第三步是焊缝的组织和对位。
根据焊接图纸要求,将板材进行对位,确保焊缝的位置和角度正确。
船厂通常采用夹具或定位装置来保持板材的对位。
第四步是焊接的设备和工艺选择。
根据板材的材质、板厚和焊接要求,选择合适的焊接设备和工艺。
船厂常用的焊接设备包括电弧焊机、气体保护焊机和激光焊机等。
第五步是焊接的操作。
根据焊接工艺要求,进行焊接操作。
焊接操作包括焊接电流的选择、焊接速度的控制、焊接条的使用等。
在焊接过程中,要注意焊接时的保护措施,如佩戴焊接面罩和焊接手套等。
第六步是焊后处理。
焊接完成后,进行焊缝的清理和整理。
船厂通常采用砂轮或刷子等工具对焊缝进行打磨和抛光,以提高焊缝的光洁度和外观。
最后一步是焊接质量的检验。
船厂对焊接质量进行检验和评估,包括焊缝的外观质量、焊缝的尺寸和形状、焊缝的内部质量等。
常用的检验方法包括目视检验、X射线检验、超声波检验等。
总结起来,船厂的板缝焊接工艺流程包括焊前准备、焊缝准备、焊缝组织和对位、焊接设备和工艺选择、焊接操作、焊后处理和焊接质量的检验。
通过严格按照这个工艺流程进行焊接,可以确保船体板材的焊接质量和船舶的安全性能。
船厂在实施板缝焊接工艺流程时应注重操作规范,严格遵守焊接标准和要求,以确保焊接质量和船舶制造的顺利进行。
(完整版)建造船舶船体焊接工艺
建造船舶船体焊接工艺一、总则:1、要求施工者严格按照《焊接规格表》进行施工;2、船体艏艉外板的对接缝(非自动焊拼板部分)应先焊横向焊缝,后焊纵向焊缝;3、在建造过程中,先焊对接焊缝,后焊角焊缝;4、整体建造部分和箱体分段等应从结构的中央向左右和前后逐格对称的进行焊接,由双数焊工对称施焊;5、凡超过1m以上的收缩变形量大的长焊缝,应采用分段退焊法或分中分段退焊进行焊接缝;6、在焊接过程中,先焊收缩变形量大的焊缝,再焊变形量小的焊缝;7、边箱分段、内底分段、甲板分段、艏艉分段分层建造,在合拢口两边应留出200~300mm的外板缝暂不接焊,以利合拢时装配对接,且肋骨、舱壁及平台板等结构靠近合拢口一边的角焊缝也暂不焊接,等合拢缝焊完后再焊;8、靠舷侧的内底边板与纵骨、底外板与纵骨至少要留一条纵骨暂不焊接,避免自由边波浪变形太大,不利于边箱合拢;9、二层底分段艏艉分段大合拢,边箱分段合拢的对接缝要用低氢型(碱性)焊条或用相同级别的711、712的CO2焊丝对称焊接,一次性连续焊完;10、构件、分段、分片等部件各自完工后要自检、互检、报检,把缺陷修补完毕,把合格品送下一道工序组装,没有拿到合格单的部件不能放到下一道工序组装。
二、焊接材料使用范围的规定(一)焊接下列船体结构和部件应采用低氢型焊条(碱性焊条)或相同级别的711、712系列的CO2焊丝。
1、船体环型对接焊缝,中桁材对接缝,合拢口处骨材对接焊缝;2、主机座及其相连接的构件;3、艏柱、艉柱、艉轴管、美人架等;4、桅杆座及腹板、带缆桩、导缆孔、锚机座、链闸及其座板等;5、艉拖沙与外板结构等;6、上下舵杆与法兰,舵杆套管与船体结构之间的连接。
(二)普通钢结构的焊接用酸性E4303焊条焊接或JM-56系列CO2焊丝焊接;(三)埋弧自动拼板,板厚≥8mm,用Ф4.0mm焊丝焊接,板厚5~8mm,用Ф3.2mm焊丝焊接;三、间断焊角接焊缝,局部加强焊的规定1)组合桁材、强横梁、强肋骨的腹板与面板的角焊接缝在肘板区域内应为双面连续焊;2)桁材、肋板、强横梁、强肋骨的端部加强焊长度应不小于腹板的高度,但间断的旁桁材端部可适当减小但要≥300mm;3)纵骨切断处端部的加强焊长度应不小于1个肋距;4)骨材端部削斜时,其加强焊长度不小于削斜长度,在肘板范围内应双面连续焊;5)用肘板连接的肋骨、横梁、扶强材的端部的加强焊,在肘板范围内应双面连续焊;6)各种构件的切口、切角、开孔(如流水孔、透气孔、通焊孔等)的两端应按下述长度进行包角焊;①当板厚>12mm时,包角焊长度≥75mm;②当板厚≤12mm时,包角焊长度≥50mm;7)各种构件对接接头的两侧应有一段对称的角焊缝其长度不小于75mm;四、其他的规定:1)锚机座、链闸、系缆桩底座、桅杆底座等受力部位的甲板与横梁、纵骨等是间断焊缝的应改为双面连续角缝。
船舶高效焊接工艺
船舶高效焊接工艺船舶焊接技术作为现代造船模式中的关键技术之一,对我国船舶行业的快速发展起到了重要作用。
高效焊接方法,是指与常规药皮焊条电弧焊相比熔敷效率高、焊接速度快、操作方便且易于自动化的焊接工艺方法。
在过去的一段时间内,国内各大船厂围绕现代造船模式的总体要求,以推进造船总装化、管理精细化为重点,结合产品载体,将先进焊接技术及焊接自动化工艺装备在生产中发挥作用。
作者近年来调研了国内各大型船厂的高效焊接技术,整理了主要的船舶高效焊接工艺、船舶制造中的高新焊接技术以及亟待解决的焊接问题等内容。
一、船舶高效焊接工艺的现状先进的船舶高效焊接技术涉及到船舶制造中的工艺设计、小合拢、中合拢、大合拢、平面分段、曲面分段、平直立体分段、管线法兰焊接、型材部件装焊等工序和工位的焊接工程。
我国的船舶建造焊接技术基本满足船厂生产的需要,高效焊接在船舶建造中发挥着极其重要的作用。
对于技术含量高的高端焊材,则仍需进口来满足生产的需求。
我国造船工业中常见的高效焊接技术主要有:1、焊条电弧焊⑴向下立焊焊条:与向上立焊相比,效率提高1~2倍。
⑵铁粉焊条焊接工艺:工艺简单实用,通过提高熔敷效率达到高的生产效率,一般提高50%以上。
⑶重力焊条:采用高效铁粉焊条(一般直径为5~8mm,长度为550mm和700mm、900mm),,熔敷率在130%~180%之间,常见的焊条牌号有CJ501FeZ等。
2、CO2气体保护焊⑴实芯焊丝我国气体保护实芯焊丝的品种太少,今后大力扩大品种的同时,也需进一步改进实芯焊丝的工艺性能,降低飞溅、成形美观等。
焊丝表面应具有防锈、润滑功能。
国内常见的牌号是E49-1、E50-6焊丝。
⑵药芯焊丝药芯焊丝将是CO2气体保护焊的主要焊材,配合各种类型的衬垫可以实现单面焊一次成形。
特点是焊道成形美观、电弧稳定、飞溅小、全位置焊接、工艺性能良好、焊接熔敷速度快、生产率高等特点。
现在船厂普遍采用药芯焊丝来焊接船舶结构,以后CO2气保护药芯焊丝焊接将成为船厂的主要焊接材料和工艺。
- 1、下载文档前请自行甄别文档内容的完整性,平台不提供额外的编辑、内容补充、找答案等附加服务。
- 2、"仅部分预览"的文档,不可在线预览部分如存在完整性等问题,可反馈申请退款(可完整预览的文档不适用该条件!)。
- 3、如文档侵犯您的权益,请联系客服反馈,我们会尽快为您处理(人工客服工作时间:9:00-18:30)。
FGB法船体曲面板高效焊接工艺方法
说明书摘要
本发明公开了一种船体曲面板高效焊接工艺方法,其包括以下步骤:S1、曲面板胎位布置阶段:将若干曲面板分布在胎架上,按照严格的精度要求进行定位,并对焊缝进行点焊固定;S2、焊接前期准备阶段:焊缝V型坡口的角度要按照一定要求,坡口附近20mm区域清理干净。
两块板焊缝底部距离按要求严格控制。
引熄弧板要安装好,另外对于预热温度的规定要求是当周围环境温度低于0℃时需要进行预热;S3、衬垫安装以及焊缝布置阶段:焊接试板装配完成之后要按照要求进行衬垫的安装及铁粉的铺设;S4、焊接过程阶段:焊接过程中要注意按要求控制焊接电流、电压和焊接速度等参数,焊后需让板冷却6小时。
本发明大大缩短了船体曲面板拼板焊接周期,可以将大量的减少辅助焊接工具的使用;同时提高了焊接自动化率,减少了人力资源的浪费。
权利要求书
1、一种船体总段移位方法,其特征在于,其包括以下步骤:
S1、曲面板胎位布置阶段:将若干曲面板分布在胎架上,按照严格的精度要求进行定位,并对焊缝进行点焊固定;
S2、焊接前期准备阶段:焊缝V型坡口的角度要按照一定要求,坡口附近20mm区域清理干净。
两块板焊缝底部距离按要求严格控制。
引熄弧板要安装好,另外对于预热温度的规定要求是当周围环境温度低于0℃时需要进行预热;
S3、衬垫安装以及焊缝布置阶段:焊接试板装配完成之后要按照要求进行衬垫的安装及铁粉的铺设;
S4、焊接过程阶段:焊接过程中要注意按要求控制焊接电流、电压和焊接速度等参数,焊后需让板冷却6小时。
2、如权利要求1所述的船体曲面板焊接工艺方法,其特征在于,步骤S2中,通常坡口形式为V型坡口,角度为40o。
焊件装配时板材必须放平整,装配间隙最大不能超过3mm。
采用尺寸为250mm×300mm的弹性引熄弧板,板厚与母材相同或正负2mm以内。
3、如权利要求1所述的船体曲面板焊接工艺方法,其特征在于,步骤S3中,所述FGB法选用的衬垫必须是专用的、特殊的衬垫。
在安装衬垫时,需要特别注意衬垫与焊接试板的背面紧密粘合,并且衬垫与衬垫的衔接处应相互无间隙。
铁粉铺设的厚度约小于板厚2mm。
4、如权利要求1所述的船体曲面板焊接工艺方法,其特征在于,步骤S4中,对不同的板厚,需要采用不同的焊接参数,FGB法采用的焊丝直径
4.5mm,电流为900A以上。
5、如权利要求1所述的船体曲面板焊接工艺方法,其特征在于,所述移位装置为埋弧自动焊小车。
说明书
FGB法船体曲面板高效焊接工艺方法
技术领域
本发明涉及一种高效焊接工艺方法,特别是涉及船体小曲率曲面板的拼板焊接。
背景技术
随着我国焊接技术的迅速发展,各大企业不断推广自动化焊接来提高自身的生产质量和效率,因此各行各业对于高质量、高效率自动化焊接技术的需求也就越来越迫切。
众所周知,在造船业的船体曲面结构建造中,因受胎架条件的限制,通常不能把工件进行翻转施工,大多采用CO2陶质衬垫单面焊双面成形来完成,这种方法由于受焊接变形、焊工技能、焊接材料及性能等多种因素的影响,存在着焊工劳动强度相对较大、耗费工时多,质量可靠性与焊工技能关联大,辅助材料多等实际情况。
FGB(Flexible Glassfiber backing)法埋弧自动焊系全自动高效焊接工艺,克服了以往老工艺中因背面需要手工碳刨操作带来的人为的不稳定因素,故而具有焊接质量稳定,焊接成形美观、生产效率高等明显的优点。
发明内容
本发明要解决的技术问题是为了克服现有技术中船舶曲面板拼板焊接占用胎位周期长、成本高效率低的缺陷,提供一种低成本高效率的全自动化的船体曲面板高效焊接工艺方法。
本发明是通过下述技术方案来解决上述技术问题的:
一种船体总段移位方法,其特点在于,其包括以下步骤:
S1、曲面板胎位布置阶段:将若干曲面板分布在胎架上,按照严格的精度要求进行定位,并对焊缝进行点焊固定;
S2、焊接前期准备阶段:焊缝V型坡口的角度要按照一定要求,坡口附近20mm区域清理干净。
两块板焊缝底部距离按要求严格控制。
引熄弧板要安装好,另外对于预热温度的规定要求是当周围环境温度低于0℃时需要进行预热;
S3、衬垫安装以及焊缝布置阶段:焊接试板装配完成之后要按照要求进行衬垫的安装及铁粉的铺设;
S4、焊接过程阶段:焊接过程中要注意按要求控制焊接电流、电压和焊接速度等参数,焊后需让板冷却6小时。
其中,步骤S2中,通常坡口形式为V型坡口,角度为40o。
焊件装配时板材必须放平整,装配间隙最大不能超过3mm。
采用尺寸为250mm×300mm 的弹性引熄弧板,板厚与母材相同或正负2mm以内。
其中,步骤S3中,所述FGB法选用的衬垫必须是专用的、特殊的衬垫。
在安装衬垫时,需要特别注意衬垫与焊接试板的背面紧密粘合,并且衬垫与衬垫的衔接处应相互无间隙。
铁粉铺设的厚度约小于板厚2mm。
其中,步骤S4中,对不同的板厚,需要采用不同的焊接参数,FGB法采用的焊丝直径4.5mm,电流为900A以上。
其中,所述焊接装置为埋弧自动焊小车。
本发明的积极进步效果在于:本发明大幅减少船体曲面板材焊接装配过程中用来定位的临时马板的使用,提升自动化焊接率,减少焊后打磨修整工作量,从而减低人员劳动强度,缩短胎位周期,进而实现降低生产成本,提高生产效率的目的。
附图说明
图1为本发明的曲面板精度定位示意图。
具体实施方式
下面结合附图给出本发明较佳实施例,以详细说明本发明的技术方案。
如图1,本实施例中将两块船体曲面板进行拼板焊接,第一阶段为曲面板定位阶段,首先将两块板固定在胎架上,焊缝按照精度要求对合好,通过点焊固定。
第二阶段为焊缝前期准备阶段:本实施例坡口角度为40o;坡口的清理要求规定必须将焊接坡口及坡口两侧各宽20mm范围内的氧化物、水分、油污等清除干净。
曲面板装配时焊缝必须对接平整,装配间隙最大不能超过3mm。
在装配定位焊时,不允许有气孔、夹渣、裂纹、焊穿等焊接缺陷。
试件采用尺寸为250mm×300mm的弹性引熄弧板,板厚与母材相同或正负2mm以内。
另外对于预热温度的规定要求是当周围环境温度低于0℃时需要进行预热。
第三阶段衬垫安装及焊道布置阶段,焊接试板装配完成之后要进行衬垫的安装及铁粉的铺设。
FGB法是将软衬垫粘贴在钢板接缝反面,正面实施埋弧自动焊,因此FGB法选用的衬垫必须是专用的、特殊的衬垫。
在安装衬垫时,需要特别注意衬垫与焊接试板的背面紧密粘合,并且衬垫与衬垫的衔接处应相互无间隙,防止在焊接过程中造成衬垫与衬垫衔接处的焊缝焊穿等现象。
铁粉应按照小于板厚2mm的厚度铺设在焊缝内。
第四阶段为焊接过程阶段:启动焊接小车,调整焊接参数,焊接过程中需有专门人员关注,开始阶段根据需要调整焊接参数。
焊接完成之后需冷却6小时。
虽然以上描述了本发明的具体实施方式,但是本领域的技术人员应当理解,这些仅是举例说明,在不背离本发明的原理和实质的前提下,可以对这些实施方式做出多种变更或修改。
因此,本发明的保护范围由所附权利要求书限定。