镁合金板材轧制技术
轧制AZ31镁合金板材的显微组织和力学性能
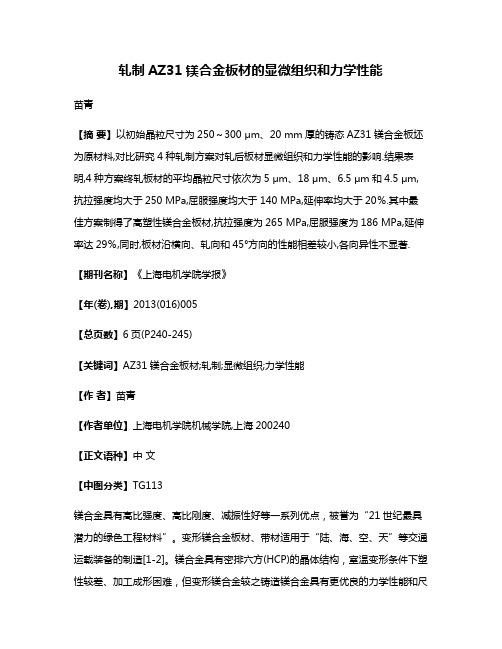
轧制AZ31镁合金板材的显微组织和力学性能苗青【摘要】以初始晶粒尺寸为250~300 μm、20 mm厚的铸态AZ31镁合金板坯为原材料,对比研究4种轧制方案对轧后板材显微组织和力学性能的影响.结果表明,4种方案终轧板材的平均晶粒尺寸依次为5 μm、18 μm、6.5 μm和4.5 μm,抗拉强度均大于250 MPa,屈服强度均大于140 MPa,延伸率均大于20%.其中最佳方案制得了高塑性镁合金板材,抗拉强度为265 MPa,屈服强度为186 MPa,延伸率达29%,同时,板材沿横向、轧向和45°方向的性能相差较小,各向异性不显著.【期刊名称】《上海电机学院学报》【年(卷),期】2013(016)005【总页数】6页(P240-245)【关键词】AZ31镁合金板材;轧制;显微组织;力学性能【作者】苗青【作者单位】上海电机学院机械学院,上海200240【正文语种】中文【中图分类】TG113镁合金具有高比强度、高比刚度、减振性好等一系列优点,被誉为“21世纪最具潜力的绿色工程材料”。
变形镁合金板材、带材适用于“陆、海、空、天”等交通运载装备的制造[1-2]。
镁合金具有密排六方(HCP)的晶体结构,室温变形条件下塑性较差、加工成形困难,但变形镁合金较之铸造镁合金具有更优良的力学性能和尺寸稳定性。
轧制技术是通过塑性成形工艺生产板、带材最经济有效的方法之一,具有在大规模工业化生产中快速应用、全面推广的价值和空间[3-4]。
因此,研究与开发高性能镁合金板材的轧制工艺具有重要意义。
据文献[5-6]报道,传统的AZ31镁合金热轧工艺,一般均从120mm左右厚的铸锭开始轧制,始轧温度为420~450℃,终轧温度为300~260℃,单道次变形量15%~25%,一般轧制到2~4mm厚的板材需要加热3~5次,总轧制道次为28~30次。
热轧后板材的性能为:抗拉强度≥250MPa,屈服强度≥145MPa,延伸率在12%~21%,轧制后板材的方向性较明显。
铸态AZ31镁合金板材等温轧制工艺及组织性能研究

铸态AZ31镁合金板材等温轧制工艺及组织性能研究王欣;杨闯;胡连喜【摘要】为研究铸态AZ31镁合金轧制工艺及轧制后组织性能,通过试验得到不同道次和变形量对铸态AZ31镁合金板材显微组织和力学性能的影响规律,并采用扫描电子显微镜研究了轧制后板材组织.结果表明,铸态AZ31镁合金板材经等温4道次、等变形量轧制后,板材厚度由20mm变化到4.8 mm,抗拉强度和屈服强度分别达到275 MPa和187 MPa,延伸率为32%,板材性能方向性小.研究表明,AZ31镁合金板材力学性能既受到平均晶粒尺寸影响,也受到晶粒取向制约.铸态AZ31镁合金板材采用等温4道次、等变形量轧制工艺,能够获得性能优异的轧制板材.【期刊名称】《材料科学与工艺》【年(卷),期】2011(019)002【总页数】4页(P34-37)【关键词】AZ31镁合金;轧制;力学性能【作者】王欣;杨闯;胡连喜【作者单位】哈尔滨工业大学,材料科学与工程学院,哈尔滨150001;黑龙江工程学院,材料与化学工程系,哈尔滨150050;哈尔滨工业大学,材料科学与工程学院,哈尔滨150001【正文语种】中文【中图分类】TG335.5镁合金具有密度低、比强度和比刚度高、抗震及减震能力强、电磁屏蔽效果优异以及易回收等一系列优点,在电子、电器、汽车、交通、航空、航天、医药材料等领域具有重要的应用价值和广阔的应用前景,被誉为21世纪最具发展前途的金属结构材料[1-2].但镁合金的室温塑性低,且与其他广泛使用的材料相比,强度比较低,这与其室温滑移系少,塑性变形能力差有关.大量研究表明[3-8],像热轧这种塑性变形方式可以有效细化晶粒,进而改变镁合金机械性能.为了提高镁合金的机械性能,优化轧制工艺参数是必不可少的,其中,非常重要的是轧制道次和变形量.Kim[9]等的研究表明,上下轧辊的速度比对提高镁合金板材的机械性能很有帮助.利用塑性变形方式提高镁合金机械性能主要是细化晶粒,而通过其他方法同样可以获得超细的镁合金晶粒以提高其力学性能,如粉末冶金[10]、快速凝固[11]以及侧向挤压[12]等方法,但对于大尺寸材料,这些方法稍显不足.本文实验研究了轧制条件下,不同轧制道次和变形量对铸态AZ31镁合金板材晶粒细化效果以及力学性能影响.本实验采用的铸态AZ31镁合金是从半连续铸锭切割下的坯料,坯料尺寸为20 mm(厚)× 140 mm(宽)×200 m(长).坯料的组织由粗大的铸造晶粒组成,平均晶粒尺寸约为350 μm.轧制试验在3150 kN压力机上进行.实验用铸态AZ31镁合金的化学成分见表1,其力学性能见表2.第1道次实验对20 mm厚铸态AZ31镁合金板材坯料进行轧制,轧制温度为400℃,轧制速度为5 m/min,分别对板材坯料进行变形程度为20%,30%,40%,50%的轧制,具体方案见表3.第2道次实验同样是400℃等温轧制,只是坯料选取第1道次轧下量为30%的14 mm厚板坯,轧制速度为5 m/min,分别进行变形程度为20%,30%,40%,50%的轧制,具体方案见表3.在上述实验研究基础上,本文制定了铸态AZ31镁合金板材坯料4道次轧制工艺.其中第1、2道次为400℃等温轧制,第3、4道次为300℃等温轧制,变形程度同为30%,具体方案见表4.对不同工艺等温轧制AZ31镁合金板材取金相试样,金相组织分析在奥林巴斯GX71金相显微镜上进行,晶粒尺寸计算由光学显微镜通过线性插值法测定.采用Instron5569拉伸试验机对轧制后AZ31镁合金板材的室温力学性能进行测试,拉伸试验的应变速率为1×10-3s-1,拉伸试样尺寸如图1所示.图2所示为第1道次、不同变形量轧制后金相组织照片.从图2可以看出,随着变形程度增大,细小晶粒越来越多,粗大晶粒越来越少,平均晶粒尺寸随着变形量的增加逐渐增大.但晶粒大小的不均匀普遍存在,基本上还是混晶组织.这是由于在等温轧制过程中发生了动态再结晶,基本上消除了原始铸态组织形态.产生动态再结晶的原因是由于镁的层错能较低,与面心立方结构的金属相比滑移系较少,且镁合金的晶界扩散速度较高.图3所示为第2道次不同变形程度400℃等温轧制后 AZ31镁合金的金相组织,变形量为20%,30%,40%,50%,原始坯料选取第1道次轧下量为30%的14 mm板坯,但由于40%和50%轧下量板材破裂严重,无法进行力学性能测试,故第2道次仅选择20%和30%轧制变形量的板材进行组织分析.由图3可以看出,随着轧制变形量的进一步加大,晶粒大小并没有太多变化,只是晶粒尺寸逐渐变得均匀,平均晶粒尺寸大约在20 μm.由于第2道次大变形量轧制情况下板材破裂严重,因此,接下来通过降低轧制温度,即300℃的等温轧制,坯料采用第2道次30%变形量的板材,厚度为9.8 mm,进行变形量为30%共2道次轧制,即第3和第4道次轧制,结果如图4所示。
ZK61镁合金薄板轧制与组织、织构及性能研究共3篇

ZK61镁合金薄板轧制与组织、织构及性能研究共3篇ZK61镁合金薄板轧制与组织、织构及性能研究1ZK61镁合金薄板轧制与组织、织构及性能研究摘要:为了研究ZK61镁合金薄板的轧制工艺对其组织、织构及性能的影响,本文采用了压下式轧制工艺,通过金相显微镜、SEM、XRD等手段对材料进行了组织、织构及性能的表征。
结果表明,通过选取合适的轧制参数,可以得到具有优异织构性能的ZK61镁合金薄板,并且该薄板具有良好的力学性能、耐腐蚀性能和耐磨性能,可以满足航空、汽车和轻量化领域的应用需求。
关键词:ZK61镁合金薄板;轧制工艺;组织;织构;力学性能1. 引言随着航空、汽车和轻量化领域的不断发展,对于轻量、高强、耐腐蚀的材料需求越来越高。
镁合金作为一种轻质高强、耐腐蚀的材料,已成为这些领域中的重要材料之一。
ZK61镁合金薄板作为一种广泛应用的材料之一,其具有优异的机械性能、良好的耐腐蚀性能和较高的加工性能,在航空、汽车和轻量化领域有着广泛的应用。
然而,由于ZK61镁合金材料具有低的塑性和低的机械性能,为了提高其塑性和机械性能,需要对其进行适当的加工工艺调控。
本文对ZK61镁合金薄板的轧制工艺进行了研究,通过对材料的组织、织构及性能进行表征,为该材料的应用提供了理论依据和实验基础。
2. 实验方法2.1 材料制备选取ZK61镁合金作为实验材料,在真空熔炼炉中进行高纯度的熔炼,得到ZK61镁合金毛坯。
然后对毛坯进行热轧工艺,将其制备成为初始厚度为3mm的扁平坯。
之后,在热轧之后进行冷轧,将材料制备成为厚度约为0.5mm的镁合金薄板。
最后对薄板进行退火处理,使其组织稳定。
2.2 薄板表征对制备好的ZK61镁合金薄板进行金相显微镜、SEM、XRD等手段对其组织、织构及性能进行表征。
其中金相显微镜用于对薄板的组织进行观测和分析,SEM用于对其表面形貌进行观察和表征,XRD用于对其晶体结构进行分析和确定。
2.3 力学性能测试将制备好的ZK61镁合金薄板进行拉伸试验和硬度测试,得到其力学性能数据。
镁合金轧制工艺

镁合金轧制工艺绪论1 绪论镁是结构材料中最轻的金属,近年来已经逐渐被应用到航空航天、国防军工、汽车、电子通讯等领域,同时这些领域对其力学性能的要求也在不断提高。
传统的铸造镁合金已经渐渐无法满足要求,而通过挤压、锻造、轧制等工艺生产的变形镁合金产品具有更高的强度、更好的延展性、更多样化的力学性能。
其中,轧制作为镁合金塑性加工的重要手段得到了长足的发展。
镁合金是密排六方晶体结构,c/a 轴比为1.6236,在室温下仅具有一个滑移面,在滑移面上有3个密排方向,即有3个滑移系,根据多晶体塑性变形协调性原则,要使多晶体在晶界处的变形相互协调,必须有5个独立滑移系,显然密排六方结构的镁合金不满足该条件。
因此,在室温下,镁合金的塑性很低。
当变形温度达到225℃时,高温滑移面(棱柱面)被激活,镁合金的塑性有所改善。
镁及其合金的另一个重要特征是加热升温与散热降温比其他金属都快。
因此,在塑性加工过程中,温度下降很快且不均匀,则易发生边裂和裂纹,相对于其它金属材料而言,镁及其合金的热加工温度范围较窄。
镁合金滑移系较少,在室温和低温条件下塑性较差,而且迄今对镁合金塑性变形机理的认识还不够全面和深入,镁合金板材制备及其轧制成形工艺的研究尚处于初级阶段。
镁合金板材轧制成形的以下特点制约了镁合金板材的发展与应用:1)镁合金室温塑性变形能力差,轧制过程中易出现裂纹等变形缺陷;2)目前镁合金板材制备多采用普通的对称轧制,轧制后的组织有强烈的(0002)基面织构,存在严重的各向异性,不利于后续加工;3)镁合金轧制道次压下量较钢和铝小很多,生产效率不高。
制备优质的镁合金板材,大部分工艺都需要经过多道次轧制工序,轧制过程受许多因素的影响,这些因素可以分为两大类:第一类为影响轧制金属本身性能的一些因素,即金属的化学成分和组织状态以及热力学条件;第二类为轧制的工艺因素,如轧制温度、轧制变形量和轧制速度以及后续的热处理工艺。
国内外很多学者针对如何改进镁合金轧制工艺和轧制技术,以获得二次成形性能优良的板材做了大量的研究工作。
专利一种用于镁合金中厚板及带卷坯生产的轧制装置

权利要求书1.一种用于镁合金中厚板及带卷坯生产的轧制装置,包括轧机、张力辊、换向辊、卷取机、辊道加热保温炉、卷取加热保温炉,辊道(2)和(9)分别设置在轧机(6)的两侧,其特征在于,辊道上安装辊道加热保温炉(1)和(10),卷取机(5)和(7)分别设置在轧机(6)的两侧以及辊道(2)和(9)的下方,并同时分别安装在卷取加热保温炉(3)和(8)内,辊道加热保温炉(1)和(10)中分别装有张力辊(14)和(13),在辊道(2)和(9)上方分别安装有换向辊(15)和(12),在卷取加热保温炉(3)和(8)的进口处分别安装有卷取导辊(16)和(11),在卷取加热保温炉(3)和(8)的内壁装有3~4个成型辊(4)。
2.如权利要求1所述的用于镁合金中厚板及带卷坯生产的轧制装置,其特征在于,辊道加热保温炉的外形为长方形,其宽度与轧机的轧辊辊宽相同,炉内高度大于辊道下表面至张力辊抬升到最高处高度的10-50mm,;3.如权利要求1所述的用于镁合金中厚板及带卷坯生产的轧制装置,其特征在于,卷取加热保温炉的外形为长方形或垂直面上为圆型的圆柱形,卷取加热保温炉的宽度与轧机的轧辊辊宽相同,其炉内直径根据所轧板卷的最大重量确定。
4.如权利要求1所述的用于镁合金中厚板及带卷坯生产的轧制装置,其特征在于,卷取机的宽度与轧机的轧辊辊宽相同,卷筒的外径为300~600mm。
5.如权利要求1、2、3或4所述的用于镁合金中厚板及带卷坯生产的轧制装置,其特征在于,轧机(6)是单机架或多机架。
说明书技术领域本实用新型涉及镁合金轧制,特别涉及镁合金中厚板及带卷坯轧制装置。
背景技术镁合金是最轻的金属结构材料,具有优异的特性,在汽车、3C、建筑、航空航天等领域受到业界的广泛关注,并得到一定应用。
我国有丰富的镁资源,是镁产量大国,也是镁出口大国。
但多年来我国的镁都是以廉价的原材料镁出口,很少有高附加值的镁深加工件出口或大批应用。
传统的镁合金板带材因其长加工周期、低成材率、较高的加工成本及较低的力学性能,使用范围受到很大限制。
镁合金板材轧制成型的研究进展_张丁非

镁合金板材轧制成型的研究进展Prog ress in the Research on Rolling Form ation ofM ag nesium A lloy Sheet张丁非1,戴庆伟1,胡耀波1,兰 伟2,方 霖1(1重庆大学材料科学与工程学院国家镁合金材料工程技术研究中心,重庆400030;2重庆科技学院,重庆401331)ZHA NG Ding-fei1,DAI Qing-w ei1,H U Yao-bo1,LAN Wei2,FANG Lin1(1Natio nal Research Center fo r M agnesium Alloy s,Co lleg e of M aterials Science andEngineering,Chongqing University,Chong qing400030,China;2Cho ng qingU niversity of Science and Technology,Cho ng qing401331,China)摘要:镁合金板材在变形镁合金中占有重要的地位,但其轧制成型工艺还不是很成熟。
分析了镁合金轧制成型的特点,论述了镁合金板材轧制成型的工艺,及异步轧制、等径角轧制、交叉棍轧制、累积叠轧等轧制方式对轧制成形性及板材组织性能的影响。
重点阐述了通过调整轧制工艺和选择轧制方式提高镁合金的轧制成形性。
指出了镁合金板材轧制中存在的问题和今后发展的方向。
关键词:镁合金;轧制方式;轧制工艺;轧制成型中图分类号:TG335.5 文献标识码:A 文章编号:1001-4381(2009)10-0085-06A bstract:M agnesium alloy sheet play s an im po rtant role in the w rought mag nesium allo y.H ow eve r, the processes of rolling fo rmatio n are unsatisfacto ry.The characteristics and pro cess of rolling fo rma-tion o f magnesium alloy sheet are analy zed.The effects of diffe rent ro lling w ay s,like asynchro nous, equal channel ang ular cro ss and accumulative rolling,on microstructure and properties are also dis-cussed.And adjusting the rolling process and selecting rolling w ay s to enhance magnesium alloy ro lled fo rmability are mainly dem onstrated.Finally the problem s,to gether with the future development of magnesium alloy sheet ro lling process,are pointed o ut.Key words:magnesium alloy;rolling w ay;ro lling process;fo rming rolling 镁合金作为最轻的结构合金,已经逐渐被应用到航空航天、汽车、摩托车、电子产品等领域,而对其力学性能的要求也越来越高。
镁合金板材轧制成形现状及其发展
镁合金板材轧制成形现状及其发展镁合金板材轧制成形现状及其发展1. 引言镁合金是一种重要的结构功能材料,具有低密度、高比强度、良好的耐腐蚀性和优异的导热性能。
镁合金在航空航天、汽车、电子设备等领域得到了广泛应用。
镁合金板材作为镁合金制造业的重要部分,其轧制成形技术是一项关键的工艺,对于提高镁合金板材的性能和质量具有重要意义。
2. 镁合金板材轧制成形技术现状目前,镁合金板材轧制成形技术已经取得了显著的进展。
根据研究和应用的结果,镁合金板材主要通过单面轧制、双面轧制和多次轧制等方式来实现成形。
其中,双面轧制技术是最常用的方法之一。
这种方法通过先进行初轧,然后进行再轧制,最终得到高质量的镁合金板材。
也有一些新型的轧制技术被引入,例如单通道轧制、多通道轧制和连续轧制等。
这些新技术能够提高板材的形尺寸精度和表面质量,进一步推动了轧制成形技术的发展。
3. 镁合金板材轧制成形技术的发展趋势随着对镁合金板材性能要求的不断提高,轧制成形技术也在不断发展。
未来的研究重点主要集中在以下几个方面:3.1. 工艺参数优化工艺参数是影响轧制成形质量和性能的关键因素之一。
通过优化轧制工艺参数,可以进一步提高镁合金板材的力学性能和表面质量。
合理选择轧制温度、轧制速度和轧制力等参数,可以有效控制晶粒细化、纵横比和内部应力等因素,从而实现良好的板材成形效果。
3.2. 强化技术应用强化技术是提高镁合金板材性能的重要手段。
常用的强化技术包括热处理、冷变形和合金元素调整等。
通过对镁合金板材的热处理,可以优化其晶体结构和晶粒尺寸,从而提高材料的强度和硬度。
通过适当的冷变形和合金元素调整,还可以改善材料的塑性和耐腐蚀性能。
3.3. 轧制设备改进轧制设备的改进也是促进镁合金板材轧制成形技术发展的重要因素。
目前,国内外已经出现了一些先进的轧机设备,如超声波振动轧制机和水压轧制机等。
这些设备可以通过引入振动或水压技术,进一步优化轧制过程中的摩擦和变形行为,提高板材的成形性能和表面质量。
ZK60镁合金细晶板材轧制工艺研究
ZK60镁合金细晶板材轧制工艺研究镁合金板材广泛应用于电子、交通和航空航天等领域。
通过强化轧制变形过程中的动态再结晶行为来细化晶粒和调控纳米析出相的析出,是改善镁合金板材强度和塑性的有效手段。
本文以ZK60镁合金为研究目标,采用单道次大变形量(80%)轧制,研究轧制温度(275℃~350℃),应变速率(5 s-1~25 s-1)对板材显微组织和力学性能的影响规律;探讨轧制过程中应变速率对动态析出行为的影响,以及析出相与各变形机制之间的交互作用。
得到了以下主要结论:(1)提高轧制温度和增大应变速率,均能提高ZK60合金的再结晶程度,在温度为350℃,应变速率为25 s-1轧制时,板材的再结晶体积分数最高,达到了 96.7%。
当温度低于300℃时,随着应变速率的增加,再结晶晶粒尺寸先减小后增大,在温度为300℃,应变速率为10 s-1时晶粒尺寸最小,为1.2μm。
当温度高于300℃时,再结晶晶粒尺寸随应变速率的增加先增大后减小,而后又增大。
(2)在低应变速率(5 s-1)下轧制时,再结晶程度低,未再结晶区域内含有大量的位错,板材强度高,但塑性差;提高应变速率到10s-1~20s-1,能获得细小均匀的再结晶组织,使得板材具有较好的强度和塑性;应变速率达到25 s-1时,晶粒发生粗化,降低了板材的强度。
在300℃下以10 s-1的应变速率轧制板材的综合力学性能最佳,其抗拉强度、屈服强度和伸长率分别为358MPa、291MPa和21.5%。
(3)在300℃下轧制时,提高应变速率能显著弱化ZK60板材的基面织构,这使得板材在室温拉伸变形时,有利于基面滑移系的启动,从而提高板材的塑性。
(4)在轧制过程中,第二相主要在位错上形核析出。
应变速率对析出相的尺寸和分布有明显的影响,在应变速率为5 s-1时,析出相的尺寸最大,密度最高;随着应变速率的提高,其尺寸和密度逐渐减小。
(5)动态析出相通过钉扎位错和晶界,从而阻碍再结晶的进行。
镁合金板材轧制
5.4镁合金板材轧制变形镁合金板材在电子、通汛、交通、航空航天等领域有着卜分J‘泛的血用前景,但目前镁合金板材的应用仍然受到很大限制.其产量和用量均远不及钢铁及铝.铜等有色金属。
制约镁合金板材发展的因素主要有两个:①大部分镁合金的室温塑性变形能力较差,且轧制板材中存在严重的各向异性;②镁合金板材制备工艺不够成熟,力学性能尚需进一步提高。
镁合金板材一般采用轧制方法生产.因此了解镁合金轧制工艺流程、阐明轧制过程中组织性能的变化规律,对促进镁合金板材轧制技术的发展是十分必要的,5.4.1镁合金轧制工艺流程·i””\,.镁合金板材的生产工艺流程如图5—76所示。
轧制设备与铝合金相似,根据乍产规模可采用2,3或4辊轧机(批量较小时可采用2辊轧机,大批量生产时则常用3辊或4辊轧机)。
镁合金轧制用的坯料可以是铸坯、挤压坯或锻坯,锭坯在轧制前需进行铣面,以除掉表面缺陷。
塑性加工性能较好的镁合金如镁—锰(Mn<2.5%)和镁—锌—锆合金可直接用铸锭进行轧制,但铸锭轧制前一般应在高温下进行长时间的均匀化处理。
对含铝量较高的镁—铝—锌系镁合金,用常规方法生产的铸锭轧制性能较差,因此常采用挤压坯进行轧制。
际tl堉焯铸造扁锭锯切铣面。
图。
令。
图。
令。
抖。
图次bU热二次0U 热—二次热轧啊训-:次加热次坤轧寸轧酞f;《枯轧6《川,蓟川退火汁漆闹/t:处煅检古包装运输图5~76镁合金板材轧制工艺流程·:239陈振华主编.变形镁合金.化学工业出版社,2005年06月.常用的镁合金为密排六方晶格结构,塑性加工性能较差,因此不能像铝合金、铜合金等立方晶格结构金属那样以很大的道次变形率(可达50%一60%)进行轧制。
镁合金在室温附近轧制时,一般应将道次变形率控制在10%一15%左右。
道次变形率过大时易发生严重的裂边,甚至表面开裂而使轧制过程无法继续进行。
在再结晶温度以上轧制时,镁合金的塑性因棱柱面及锥面等潜在滑移系的启动而大幅度提高,因而大部分镁合金板材生产均采用热轧的方式,且在热轧过程中应进行反复加热。
镁合金双辊铸轧工艺
21 年 第 5 00 期
镁合金双辊铸轧工艺
目前, 双辊铸轧技术 己广泛用于制备轻型镁合金板材, 这类板材对于对重量敏感的应用 领域具有很大吸引力。 本文综述 了镁合金的双辊铸轧工艺现状,主要内容集中在与镁合金带 材的固化行为有紧密关系的问题。另外, 也涉及到在这种先进的铸轧工艺的帮助下利用冶金 的优势开发新的镁合金的问题。 引言 、 镁合金是广泛应用的具有超强度和硬度的轻型结构合金,镁合金具有优 良的可铸造性、
表 1 M RI 艺的研 发现 状 gT C 国家 公 司厮 究所
韩 国 日本 P C ( IT OS O R S ) Mi u i i u n m  ̄ bs miu h Al
Go d eM n aM t
铸 造 带材尺 寸 ( ×,rm) W Ia
6 0 45 0x. 205 5 x
机械加工性、阻尼容量、屏蔽能力并可再生循环利用, 所有这些特性都优于其他有竞争性的 金属材料如钢和铝合金等。 尽管人们 已对铸造镁合金工艺进行了大量的研发工作, 但对锻造
镁合金工艺的研发工作相对少一些。目前的状况是缺乏有竞争能力的镁合金板材产品, 而对 于重量敏感的应用领域例如汽车车体对这类产品却有很大的需求。 由于镁合金的热容低和可 加工性差, 造成 了镁合金板材热轧过程中需进行频繁地再加热, 工艺的复杂性是导致其缺乏 竞争能力的主要原因。因此,用直接冷铸 (i cci,D )法 的铸锭来制备镁合金板材的 d e hl C rt l 成本要高于钢和铝合金,影响了镁合金板材产品在汽车领域的应用。 目前 ,利用 双辊铸 轧 工艺 ( R T C),也被 称为 双辊 带材铸 轧 工艺 ,能够有 效地 生产镁 合 金板材, 用这种工艺生产的产品与用常规的镁合金铸锭工艺生产的产品具有 同等强度 。 由于 TC R 工艺能够生产厚度小于lm 的较薄的产品,而常规的铸锭工艺只能生产厚度大于30m Om 0r a 的厚板,所 以TC R I艺的优点是可以省去后续的轧制,具有经济方面的优势。双辊铸轧工艺 可以提供比常规的固化速度 (  ̄5K s 1 0 / )更快的固化速度 ( o 0 / ),TCK 12 3 s ~1 K R Z 艺的较快
- 1、下载文档前请自行甄别文档内容的完整性,平台不提供额外的编辑、内容补充、找答案等附加服务。
- 2、"仅部分预览"的文档,不可在线预览部分如存在完整性等问题,可反馈申请退款(可完整预览的文档不适用该条件!)。
- 3、如文档侵犯您的权益,请联系客服反馈,我们会尽快为您处理(人工客服工作时间:9:00-18:30)。
镁合金板材轧制技术
变形镁合金板材在电子、通讯、交通、航空航天等领域有着十分广泛的应用前景,但目前镁合金板材的应用仍然受到很大的限制,其产量及用量远不及钢铁及铝、铜等有色金属。
制约镁合金板材发展的因素主要有两个:大部分的镁合金室温塑性变形能力较差,且轧制板材中存在严重的各向异性;镁合金板材制备工艺不够成熟,力学性能尚需进一步提高。
镁合金板材一般采用轧制的方法生产,因此了解镁合金轧制工艺流程、阐明轧制过程中组织性能的变化规律,对促进镁合金板材的轧制技术的发展是十分必要的。
1 镁合金轧制工艺流程
镁合金板材的轧制设备与铝合金相似,根据生产规模2、3或4辊轧机。
镁合金轧制时所用的坯料可以是铸坯、挤压坯或锻坯。
锭坯在轧制前需进行铣面,以除掉表面缺陷。
塑性加工性能较好的镁合金如镁-锰(Mn<2.5%)和镁-锌-锆合金可直接用铸锭进行轧制,但铸锭轧制前一般应在高温下进行长时间的均匀化处理。
对含铝量较高的镁-铝-锌系镁合金,用常规方法生产的铸锭轧制性能较差,因此常采用挤压坯进行轧制。
镁合金轧制工艺流程如下:原料→熔炼→铸造→扁锭→锯切→铣面→一次加热→一次热轧→二次加热→二次热轧→剪切→三次加热→三次热轧→冷轧→酸洗→精轧→成品剪切→退火→涂漆→固化处理→检查→包装→运输。
1.1扁锭铸造
镁合金铸锭可用铁模铸造,也可用半连续或连续工艺铸造。
铁模铸造时,铸锭厚度一般不大于60mm。
而半连续或连续铸造时,铸锭厚度可达300mm以上,长度则可通过铸造井内安装的同步锯切设备锯切成所需尺寸。
通常镁合金的注定尺寸为:(127~305)mm×(406~1041)mm×(914~2032)mm,宽度与厚度之比应控制在4.0左右为宜。
铸锭的质量主要取决于冷却速度、金属凝固时结晶的方向性、熔体补给情况、铸造压力及铸造温度等工艺参数。
1.2铸锭加热
镁合金铸锭特别是含铝量较高的合金铸锭,在轧制前需要进行均匀化处理,以减小或消除成分偏析、提高铸锭的塑性成形能力。
均匀化处理的温度范围为
643~703K,时间一般为8~12h以上。
下表1几种常见镁合金的均匀化处理制度。
AM60镁合金均匀化处理前后的组织有较大差别。
表1 镁合金铸锭均匀化处理制度
1.3热轧
尽管镁合金冷加工性能较差,但在热态下大部分镁合金都具有较好的轧制性能。
热轧时的道次压下量通常控制在10%~25%,加热一次后可多道次轧制。
但用不带加热装置的轧辊进行单板轧制时,轧板温度会下降,此时需重新加热以保证加热温度。
镁合金板材的热轧多采用二辊轧机,大批量生产时则常用3辊或4辊轧机。
为了降低轧制力并改善轧制性能,轧制时通常使用润滑剂,可将含2%(质量)的调水油均匀地喷涂于加热的轧辊表面。
在粗轧时为了防止粘辊,可用猪油、石蜡、硼氮化合物或石墨+四氯化碳溶液作为润滑剂。
1.4冷轧
镁合金板材的冷轧能力取决于合金成分及热轧工艺和热轧板组织。
为防止轧制时板材开裂,应严格控制道次压下量及冷轧总变形量。
通常AZ31的冷轧总变形量可达16%,而MAl镁合金的冷轧总变形量可达50%以上。
对合金化程度较高的难变形镁合金,可采用温轧的方法成形,即将轧制开轧温度控制在503K左右。
当压下量为25%时,轧后板材温度约为423~433K,在卷绕前将其冷却至393K以下。
大部分镁合金对冷加工硬化很敏感,对冷轧板材进行不同程度的中间退火或成品退火,可改善其冷变形能力,并获得不同状态和性能的制品。
2镁合金轧制制度的确定
镁合金轧制制度主要包括压下制度、速度制度、温度制度、辊型制度和张力制度等,其中最关键的是压下制度、速度制度和温度制度,而三者之间又是相互影响和关联的。
确定合理的轧制制度,对提高生产效率和质量是十分重要的。
2.1确定轧制制度的基本原则
轧制制度的确定需要综合考虑设备、产量、效益及操作等多方面的因素,要求充分发挥设备潜力、保证产品质量,并确保操作过程安全、方便。
具体来说应做到如下两点。
(1)充分发挥设备生产能力,尽量提高产量。
从设备角度考虑,限制压下量和速度提高的因素主要有三点,即板材咬入条件、机架和轧辊的强度条件以及电机功率的限制。
(2)优化轧制工艺,尽量提高产品质量。
应确定合理的压下制度、速度制度、温度制度、辊型制度和张力制度等,以获得组织细小均匀、板型良好、表面光洁度高、力学性能优异的板材。
2.2压下制度的确定
压下制度是板材轧制制度最核心的内容,直接关系着生产效率和产品质量。
压下制度的中心内容就是要确定由一定尺寸的板坯轧成规定尺寸的成品过程中,所需采用的道次压下量和轧制道次。
确定压下制度的方法很多,可归纳为理论计算法和经验法。
要确定最佳的压下制度,最好是结合两种方法,即在物理模拟和数值模拟的基础上,结合操作人员的实践经验,在生产过程中视具体情况随即应变。
2.3轧制速度的确定
从提高产量和细化晶粒的角度来讲,希望采用尽可能高的轧制速度。
但镁合金的塑性一般随应变速率的增大而下降,因此热轧时的轧制速度要远小于钢铁及铜、铝合金,以牺牲生产效率来换取制品性能的提高。
由于轧制工艺的特殊性,在不可调速轧机上轧制时,轧制速度受道次压下量的影响,在制定轧制速度时应综合考虑。
3轧制工艺对镁合金板材组织性能的影响
材料的力学性能是由其微观组织决定的。
具体来说,变形镁合金板材的力学性能主要受晶粒度、晶粒尺寸分布及晶粒取向分布的综合影响。
而轧制工艺参数可通过影响镁合金的塑性变形机制及回复和动态再结晶过程来左右材料的最终组织,并成为决定板材性能最重要的因素。
3.1轧制温度的影响
轧制温度对镁合金板材组织性能的影响,其实质是通过对轧制时的塑性变形
机制和动态再结晶过程的影响来实现的。
低温轧制时,非基面滑移难以启动,孪生成为主要的变形方式,晶粒中往往出现大量孪晶。
同时,由于达不到动态再结晶所需的温度,因此不能细化晶粒。
在再结晶温度以上进行热轧时,可通过形成细小的新晶粒而使平均晶粒尺寸下降,综合力学性能提高。
3.2变形程度的影响
道次压下和总变形量均对镁合金轧制板材的组织和性能有很大影响。
一般来说,随着变形量的增大,热轧板材的晶粒尺寸减小,且大小更加均匀。
但压下量过大时,容易出现裂边和表面裂纹。
当道次变形量为20%时,微观组织即发生了显著的变化。
主要表现在孪晶清晰可见,部分晶界发生弯曲,且在晶界和孪晶附近形成了少量细小的再结晶晶粒,但其所占比例较小,故晶粒无明显细化。
随着道次变形量的增大,再结晶新晶粒比例不断增加,晶粒得到明显细化。
当道次变形量到达68%和80%时,平均晶粒尺寸为3μm和1μm。
3.3锭坯厚度的影响
在坯料具有初始织构的情况下,除了变形程度对板材的组织性能有很大的影响外,在相同的变形量和其他变形条件下,坯料的厚度对板材的组织性能也有很大影响。
这是因为坯料厚度的改变将引起轧板法向和径向轧制力P r之间的夹角θ发生变化,从而改变材料的变形机制并影响合金的力学性能。
3.4轧制方式的影响
镁合金在轧制的过程中易形成(0001)基面织构,成品板材通常具有很强的各向异性,这对冲压特别是拉伸极为不利。
采用交叉轧制的方法,轧向和横向交替变化,不仅可以使锭坯长宽比灵活配合,而且能导致晶粒均匀化和等轴化,降低各向异性,改善板材性能。