镁及镁合金板材的生产工艺流程
镁合金板材轧制技术

镁合金板材轧制技术变形镁合金板材在电子、通讯、交通、航空航天等领域有着十分广泛的应用前景,但目前镁合金板材的应用仍然受到很大的限制,其产量及用量远不及钢铁及铝、铜等有色金属。
制约镁合金板材发展的因素主要有两个:大部分的镁合金室温塑性变形能力较差,且轧制板材中存在严重的各向异性;镁合金板材制备工艺不够成熟,力学性能尚需进一步提高。
镁合金板材一般采用轧制的方法生产,因此了解镁合金轧制工艺流程、阐明轧制过程中组织性能的变化规律,对促进镁合金板材的轧制技术的发展是十分必要的。
1 镁合金轧制工艺流程镁合金板材的轧制设备与铝合金相似,根据生产规模2、3或4辊轧机。
镁合金轧制时所用的坯料可以是铸坯、挤压坯或锻坯。
锭坯在轧制前需进行铣面,以除掉表面缺陷。
塑性加工性能较好的镁合金如镁-锰(Mn<2.5%)和镁-锌-锆合金可直接用铸锭进行轧制,但铸锭轧制前一般应在高温下进行长时间的均匀化处理。
对含铝量较高的镁-铝-锌系镁合金,用常规方法生产的铸锭轧制性能较差,因此常采用挤压坯进行轧制。
镁合金轧制工艺流程如下:原料→熔炼→铸造→扁锭→锯切→铣面→一次加热→一次热轧→二次加热→二次热轧→剪切→三次加热→三次热轧→冷轧→酸洗→精轧→成品剪切→退火→涂漆→固化处理→检查→包装→运输。
1.1扁锭铸造镁合金铸锭可用铁模铸造,也可用半连续或连续工艺铸造。
铁模铸造时,铸锭厚度一般不大于60mm。
而半连续或连续铸造时,铸锭厚度可达300mm以上,长度则可通过铸造井内安装的同步锯切设备锯切成所需尺寸。
通常镁合金的注定尺寸为:(127~305)mm×(406~1041)mm×(914~2032)mm,宽度与厚度之比应控制在4.0左右为宜。
铸锭的质量主要取决于冷却速度、金属凝固时结晶的方向性、熔体补给情况、铸造压力及铸造温度等工艺参数。
1.2铸锭加热镁合金铸锭特别是含铝量较高的合金铸锭,在轧制前需要进行均匀化处理,以减小或消除成分偏析、提高铸锭的塑性成形能力。
镁合金生产工艺流程
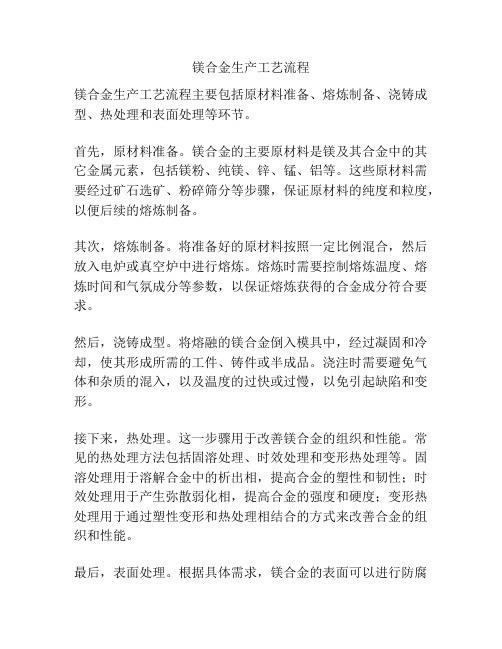
镁合金生产工艺流程
镁合金生产工艺流程主要包括原材料准备、熔炼制备、浇铸成型、热处理和表面处理等环节。
首先,原材料准备。
镁合金的主要原材料是镁及其合金中的其它金属元素,包括镁粉、纯镁、锌、锰、铝等。
这些原材料需要经过矿石选矿、粉碎筛分等步骤,保证原材料的纯度和粒度,以便后续的熔炼制备。
其次,熔炼制备。
将准备好的原材料按照一定比例混合,然后放入电炉或真空炉中进行熔炼。
熔炼时需要控制熔炼温度、熔炼时间和气氛成分等参数,以保证熔炼获得的合金成分符合要求。
然后,浇铸成型。
将熔融的镁合金倒入模具中,经过凝固和冷却,使其形成所需的工件、铸件或半成品。
浇注时需要避免气体和杂质的混入,以及温度的过快或过慢,以免引起缺陷和变形。
接下来,热处理。
这一步骤用于改善镁合金的组织和性能。
常见的热处理方法包括固溶处理、时效处理和变形热处理等。
固溶处理用于溶解合金中的析出相,提高合金的塑性和韧性;时效处理用于产生弥散弱化相,提高合金的强度和硬度;变形热处理用于通过塑性变形和热处理相结合的方式来改善合金的组织和性能。
最后,表面处理。
根据具体需求,镁合金的表面可以进行防腐
蚀处理、电镀、喷涂、阳极氧化等。
这些处理可以提高镁合金的耐蚀性、外观质量和装饰效果,从而满足不同应用领域的需求。
总之,镁合金生产工艺流程包括原材料准备、熔炼制备、浇铸成型、热处理和表面处理等环节。
每个环节都需要严格控制工艺参数,以确保生产出符合要求的镁合金产品。
镁板生产工艺

镁板生产工艺镁板是一种轻质、高强度、防火、耐腐蚀的新型建筑装饰材料,广泛应用于建筑、家具、船舶、汽车、电子等行业。
下面,我将为您介绍镁板的生产工艺。
一、原材料准备镁板的原材料主要包括高纯氧化镁粉、降温剂、增强材料以及其他添加剂。
首先,将高纯氧化镁粉进行破碎和干燥处理,然后与降温剂、增强材料进行混合搅拌,以获得均匀的混合物。
二、制板工艺1. 混合物压制:将混合物放入压制机中,施加一定的压力进行压制。
通过调节压力和时间,使得混合物中的粉末颗粒形成一定的结构。
2. 烘烤:将压制后的板材放入烘箱中进行热处理。
通过控制烘烤温度和时间,使得板材中的结晶程度逐渐增加,提升板材的强度和硬度。
3. 切割:烘烤后的板材经过冷却后,进行切割,以获得符合规格的镁板。
三、表面处理1. 磨光:对板材的表面进行磨平处理,以获得平整、光滑的表面。
2. 清洗:使用特殊清洗剂对板材的表面进行清洗,去除杂质和污物。
同时,也可以进行防腐处理,提升板材的使用寿命。
四、涂层处理根据镁板的使用需求,可以进行涂层处理。
常见的涂层包括防火涂层、防腐涂层、装饰性涂层等。
涂层通过喷涂、滚涂、刷涂等方式进行,并通过烘烤固化,使涂层与板材牢固结合。
五、包装与质检镁板生产完成后,进行包装和质检。
将板材进行分类、计数,并采取适当的包装方式,以保护板材的完整性。
同时,还要进行质量检测,确保板材符合标准要求。
以上是镁板的生产工艺,生产过程中需严格控制各个环节,确保产品质量。
随着科技的不断进步,镁板的生产工艺也在不断创新,为人们提供更好的产品和服务。
镁合金的生产工艺流程

镁合金的生产工艺流程
《镁合金的生产工艺流程》
镁合金是一种重要的轻金属材料,具有优异的力学性能和耐腐蚀性能,被广泛应用于航空航天、汽车制造、电子设备等领域。
其生产工艺流程主要包括镁矿选矿、精炼、合金化和铸造等环节。
首先是镁矿选矿。
镁矿一般是以镁石和白镁矿为主要原料,通过挖掘、破碎、磨矿等步骤进行选矿,以获得含有较高镁含量的矿石。
接下来是精炼。
选矿后的镁矿需要进行精炼处理,主要包括熔炼、分离、提纯等步骤。
熔炼是将镁矿放入高温熔炼炉中,以将镁矿中的杂质分离出来,提高镁含量。
分离和提纯则是通过化学反应或其他方法,进一步提高镁的纯度。
在镁矿精炼后,需要进行合金化。
镁合金通常是通过在纯镁中添加其他金属元素形成的。
合金化一般通过熔炼、搅拌等方法进行,以获得具有特定性能的镁合金。
最后是铸造。
将合金化后的镁合金液态熔体浇铸成各种产品,包括板材、棒材、型材、铸件等。
铸造过程中需要严格控制温度、压力和铸模等参数,以确保所铸成的产品具有良好的力学性能和表面质量。
除了上述核心环节外,镁合金的生产工艺流程还包括原材料储
存、设备维护、环境保护等环节。
通过严格控制每一个环节,可以确保镁合金的生产工艺流程稳定、高效,满足各种工业领域对于镁合金产品的需求。
镁合金加工工艺流程以及切削加工要点
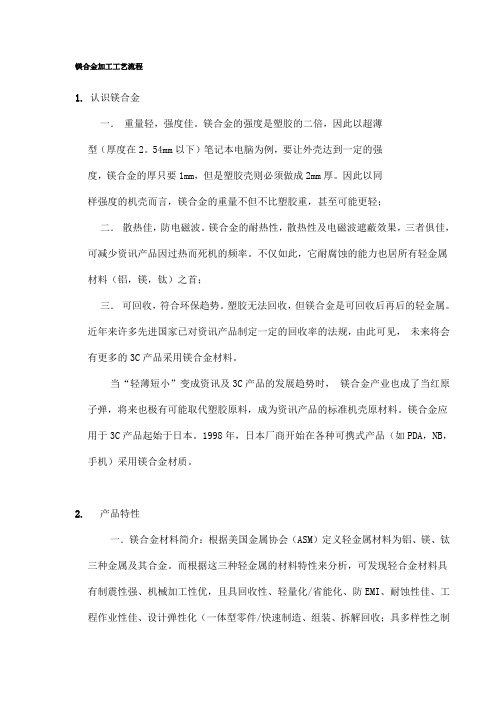
镁合金加工工艺流程1. 认识镁合金一.重量轻,强度佳。
镁合金的强度是塑胶的二倍,因此以超薄型(厚度在2。
54mm以下)笔记本电脑为例,要让外壳达到一定的强度,镁合金的厚只要1mm,但是塑胶壳则必须做成2mm厚。
因此以同样强度的机壳而言,镁合金的重量不但不比塑胶重,甚至可能更轻;二.散热佳,防电磁波。
镁合金的耐热性,散热性及电磁波遮蔽效果,三者俱佳,可减少资讯产品因过热而死机的频率。
不仅如此,它耐腐蚀的能力也居所有轻金属材料(铝,镁,钛)之首;三.可回收,符合环保趋势。
塑胶无法回收,但镁合金是可回收后再后的轻金属。
近年来许多先进国家已对资讯产品制定一定的回收率的法规,由此可见,未来将会有更多的3C产品采用镁合金材料。
当“轻薄短小”变成资讯及3C产品的发展趋势时,镁合金产业也成了当红原子弹,将来也极有可能取代塑胶原料,成为资讯产品的标准机壳原材料。
镁合金应用于3C产品起始于日本。
1998年,日本厂商开始在各种可携式产品(如PDA,NB,手机)采用镁合金材质。
2.产品特性一.镁合金材料简介:根据美国金属协会(ASM)定义轻金属材料为铝、镁、钛三种金属及其合金。
而根据这三种轻金属的材料特性来分析,可发现轻合金材料具有制震性强、机械加工性优,且具回收性、轻量化/省能化、防EMI、耐蚀性佳、工程作业性佳、设计弹性化(一体型零件/快速制造、组装、拆解回收;具多样性之制程及表面处理应用技术)、高质感/时尚感等,而广泛用于运输工具、航天、国防、石化、能源、包装、信息电子与营建业等;特别是镁合金方面,由于比重低(质轻,镁合金比重仅1.8,已经接近工程塑料1.2-1.7)且强度足(质硬),加上加工性优、质感佳与热传导快(散热佳优于铝、钛),不仅已经逐渐取代工程塑料,同时且替代原有铝合金产品,而广泛应用于笔记性计算机、PDA、手机等携带式装置(Hand-Held),据了解2000年已有1/3左右笔记型计算机改用镁合金背板与框架,显示该产品所具有的潜力。
镁合金制程详解

噴面漆 保護作用
面漆噴塗
1.按照標准參數表上要求把噴槍設定到預定參數. 2.把噴槍調到最佳噴塗狀態. 3.保証塗膜均勻到位.
流平
1.流平間溫度要適中﹐溫度太高和太低都會改變溶劑揮發 速度影響流平效果.
乾燥面漆 PU漆
二者選一 乾燥面漆 UV漆
面漆烘烤
1.按照標准參數表上要求把烤爐設定到規定溫度. 2.塗膜要烤干﹐否則會影響耐磨﹑硬度等性能測試.
2) 面漆:透明狀,起保護作用.分為:
3) 1) UV漆---UV炉(UV: Ultraviolet 紫外線) 2) PU漆---主烤炉(PU: Polyurethane 聚亞安脂) 面漆附加溶劑:亮光劑/啞光劑---調光澤
四. 工藝流程
預組==>上挂==>素材擦拭==>人工除塵==> 自動除塵==>底塗1==>流平1 ==>預烤1==>冷卻1==> 底塗2==>流平2==>預烤2==> 冷卻2==> 面塗1==> 流平3==> 預烤3==> 冷卻3 ==>UV照射 / PU主烤==> 冷卻4 ==>下挂==> 外觀檢驗==>打碼==>包裝==>送檢 ==>入庫
機加概述
粗加工,起到整形去毛邊的作用.
化成概述
鎂合金暴露在空氣中會氧化﹐將鎂合金產品化學處理﹐在表面形成防氧化保護膜,可 避免氧化.
產品特性
1) 2) 3) 4) 5) 6) 7) 8) 9) 輕量化,比重1.7,僅鐵的1/4,鋁的2/3,與塑膠相近. 強度高、剛性佳,優於鐵、鋁. 極佳防震性、耐衝擊、耐磨耗性良好. 優良熱傳導性,改善電子產品散熱問題. 非磁性金屬,抗電磁波干擾,電磁遮蔽性佳(EMI). 金屬材質,成品外觀美麗,質感佳. 無可燃性(燃點427℃) 材料可回收,符合環保法規. 尺寸穩定,收縮率小,不易因環境溫度變化而改變.
镁合金的生产工艺流程
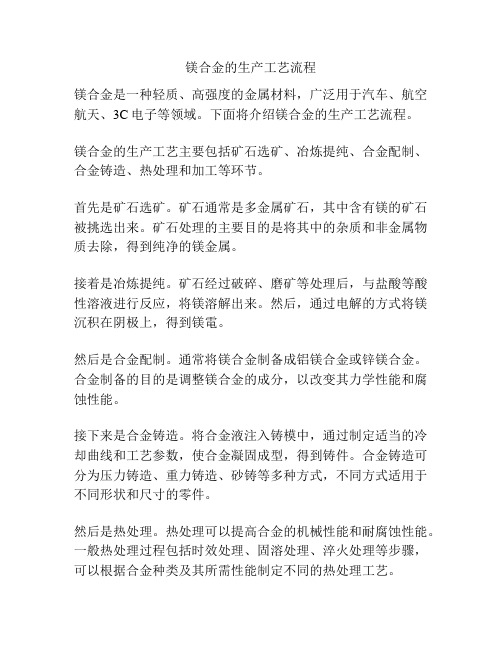
镁合金的生产工艺流程
镁合金是一种轻质、高强度的金属材料,广泛用于汽车、航空航天、3C电子等领域。
下面将介绍镁合金的生产工艺流程。
镁合金的生产工艺主要包括矿石选矿、冶炼提纯、合金配制、合金铸造、热处理和加工等环节。
首先是矿石选矿。
矿石通常是多金属矿石,其中含有镁的矿石被挑选出来。
矿石处理的主要目的是将其中的杂质和非金属物质去除,得到纯净的镁金属。
接着是冶炼提纯。
矿石经过破碎、磨矿等处理后,与盐酸等酸性溶液进行反应,将镁溶解出来。
然后,通过电解的方式将镁沉积在阴极上,得到镁電。
然后是合金配制。
通常将镁合金制备成铝镁合金或锌镁合金。
合金制备的目的是调整镁合金的成分,以改变其力学性能和腐蚀性能。
接下来是合金铸造。
将合金液注入铸模中,通过制定适当的冷却曲线和工艺参数,使合金凝固成型,得到铸件。
合金铸造可分为压力铸造、重力铸造、砂铸等多种方式,不同方式适用于不同形状和尺寸的零件。
然后是热处理。
热处理可以提高合金的机械性能和耐腐蚀性能。
一般热处理过程包括时效处理、固溶处理、淬火处理等步骤,可以根据合金种类及其所需性能制定不同的热处理工艺。
最后是加工。
加工是将铸件或热处理后的合金进行进一步加工,以得到所需的形状和尺寸。
常见的加工方式有压力加工、锻造、挤压、铸造等。
综上所述,镁合金的生产工艺流程主要包括矿石选矿、冶炼提纯、合金配制、合金铸造、热处理和加工等环节。
这一工艺流程可以根据具体需求进行调整和改进,以满足不同应用领域的要求。
镁合金的生产工艺流程

镁合金的生产工艺流程镁合金是一种具有轻重量、高强度和良好的耐腐蚀性能的金属材料,广泛应用于航空航天、汽车、电子等领域。
下面我将介绍镁合金的生产工艺流程。
首先,镁合金的生产通常是通过熔炼法进行。
熔炼法的基本原理是将镁矿石经过破碎、磨粉等预处理后,与金属锍或金属相混合,在高温下进行熔炼,使镁矿石中的金属元素与金属锍中的金属元素发生反应,生成镁合金。
其次,熔炼法的具体步骤如下:1. 镁矿石的预处理:将镁矿石经过破碎、磨粉的处理,使其粒径适合熔炼反应的要求。
2. 镁矿石的混合:将预处理好的镁矿石与金属锍或金属相混合,按照一定的配比放入熔炼炉中。
3. 熔炼反应:在高温的条件下,通过加热炉中的熔炼材料使其熔化,形成熔体。
在熔体中,镁矿石中的金属元素与金属锍中的金属元素发生反应,生成镁合金。
熔炼反应通常需要添加适量的助熔剂或变质剂,以提高反应的速度和效率。
4. 熔炼渣的处理:在熔炼过程中,熔炼材料中的杂质和氧化物会形成熔渣。
熔渣通常需要进行去渣处理,以保证熔体中的杂质含量符合要求。
5. 熔体的浇铸:在熔体达到一定的温度和成分后,将其倒入预先准备好的铸型中。
通过控制浇铸的速度和温度,可以获得具有良好力学性能的镁合金铸件。
6. 铸件的后处理:铸件通常需要经过去渣、除气、退火等后处理工艺,以消除内部和表面的缺陷,并进一步提高其力学性能。
需要注意的是,镁合金的生产工艺流程还受到工艺设备、材料性质以及产品要求等多个因素的影响。
不同的镁合金种类和应用领域可能有不同的生产工艺流程。
因此,在具体生产过程中,还需要根据实际情况进行调整和改进。
总结起来,镁合金的生产工艺流程包括预处理、混合、熔炼反应、熔渣处理、浇铸和后处理等步骤。
这些步骤的合理组合和控制,可以保证镁合金的质量和性能,满足其在各个领域的应用要求。
- 1、下载文档前请自行甄别文档内容的完整性,平台不提供额外的编辑、内容补充、找答案等附加服务。
- 2、"仅部分预览"的文档,不可在线预览部分如存在完整性等问题,可反馈申请退款(可完整预览的文档不适用该条件!)。
- 3、如文档侵犯您的权益,请联系客服反馈,我们会尽快为您处理(人工客服工作时间:9:00-18:30)。
镁及镁合金板材的生产工艺流程(一)
镁及镁合金板材的生产工艺流程为:
1、熔炼与铸锭
熔炼包括熔化、合金化、精炼、晶粒细化、过滤等冶金和物理化学过程,通常在反射炉或坩埚炉内进行。
镁及镁合金的熔点都在650℃左右,它们极易氧化且随温度的升高而加剧。
当温度超过约850℃时,熔体的表面立即燃烧,故熔炼时必须用熔剂覆盖或以保护性气体保护。
镁及镁合金在熔融和燃烧状态下遇水、含水(包括结晶水)物质和液态防火介质都可能导致剧烈爆炸,因此,在生产的全过程中注意安全是至关重要的。
以隔离空气为主的覆盖熔剂和以提高熔体质量为主的精炼熔剂都是碱金属或碱土金属的氯化物和氟化物。
除气(主要是氢)随熔剂精炼进行,也可向熔体中通入活性气体(如氯气)。
对凝固时的晶粒粗大倾向,据合金的不同可采取控制熔体温度、向熔体加入微量元素进行变质处理等加以抑制,即晶粒细化(见铸锭晶粒的细化处理)。
铸锭通常采用半连续铸锭法。
除封闭式铸锭外,流槽和结晶器中裸露的金属,必须用s0:或SF。
等气体保护。
要科学地确定和控制各项铸造参数,以防止铸锭发生热裂,并降低冷隔深度和减少金属间化合物的形成和聚集。
除镁一钇系合金外,铸锭的冷裂倾向小。
2、加热与热轧
铸锭在加热前必须铣面(见有色金属合金锭坯铣面),彻底去除冷隔和偏析物等表面缺陷;合金元素含量高和含锆、钇等的合金还要经均匀化处理(见有色金属合金锭坯均匀化)。
铸锭加热时应避免直接热辐射和避免火焰同铝接触,以防局部过热、熔化或燃烧。
根据合金的不同加热温度控制在370~510℃范围内。
除含锂高的超轻合金有晶型转变外,余者皆为密排六方晶型,塑性差,但变形能力随加热温度的提高和晶粒尺寸的减小而提高,并比立方晶型的金属提高得更快。
热轧的总变形量可以达到96%。
严格控制终轧温度是保证热加工状态成品板材的力学性能并防止板坯及薄板产生裂纹的重要途径。
晶粒粗大的铸锭和厚度较小的热轧成品,有的要进行二
次加热和热轧。
热轧要求轧辊保持良好的温度条件。
轧辊温度的高低和分布状况能影响轧制的成败。
工艺润滑(见塑性加工工艺润滑)不可采用通常的水溶性乳化液,为防止金属粘辊和控制辊型(见辊型控制),可向辊面喷射少量多碳原子的单烷烃水溶液。
热轧最小的终了厚度为6~10mm。
3、温轧
温轧又可分为温粗轧和温精轧。
温轧要反复进行多次,两次温轧之间应对坯料进行中间加热,加热温度要高于再结晶退火温度。
温粗轧的终轧温度一般不低于250℃,总变形量可达65%。
随着坯料或成品厚度的减小,加热温度和随后的终轧温度可相应降低。
每次温轧的总变形量视合金的不同控制在26%~65%的范围内。
轧辊的温度条件也是进行有效轧制的重要保障。
因此,充分利用坯料和轧辊的温度条件是十分重要的。
工艺润滑可用分子量较小的单烷烃水溶液,也可用煤油等。
厚度较薄(如0.5mm)的低成分镁合金还可进行叠轧(见叠轧薄板生产)。
为提高板材的表面质量,温粗轧之后,对坯料应进行一次较彻底的清理,最有效的方法是在硝酸溶液中浸洗。