超声波无损探伤分解
焊接球节点钢网架焊缝超声波探伤及质量分级法
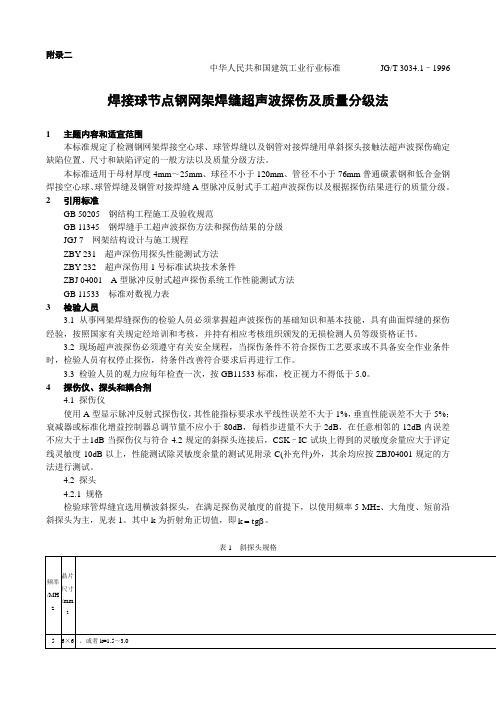
附录二中华人民共和国建筑工业行业标准JG/T 3034.1–1996 焊接球节点钢网架焊缝超声波探伤及质量分级法1 主题内容和适宜范围本标准规定了检测钢网架焊接空心球、球管焊缝以及钢管对接焊缝用单斜探头接触法超声波探伤确定缺陷位置、尺寸和缺陷评定的一般方法以及质量分级方法。
本标准适用于母材厚度4mm~25mm、球径不小于120mm、管径不小于76mm普通碳素钢和低合金钢焊接空心球、球管焊缝及钢管对接焊缝A型脉冲反射式手工超声波探伤以及根据探伤结果进行的质量分级。
2 引用标准GB 50205 钢结构工程施工及验收规范GB 11345 钢焊缝手工超声波探伤方法和探伤结果的分级JGJ 7 网架结构设计与施工规程ZBY 231 超声深伤用探头性能测试方法ZBY 232 超声深伤用1号标准试块技术条件ZBJ 04001 A型脉冲反射式超声探伤系统工作性能测试方法GB 11533 标准对数视力表3 检验人员3.1 从事网架焊缝探伤的检验人员必须掌握超声波探伤的基础知识和基本技能,具有曲面焊缝的探伤经验,按照国家有关规定经培训和考核,并持有相应考核组织颁发的无损检测人员等级资格证书。
3.2 现场超声波探伤必须遵守有关安全规程,当探伤条件不符合探伤工艺要求或不具备安全作业条件时,检验人员有权停止探伤,待条件改善符合要求后再进行工作。
3.3 检验人员的观力应每年检查一次,按GB11533标准,校正视力不得低于5.0。
4 探伤仪、探头和耦合剂4.1 探伤仪使用A型显示脉冲反射式探伤仪,其性能指标要求水平线性误差不大于1%,垂直性能误差不大于5%;衰减器或标准化增益控制器总调节量不应小于80dB,每档步进量不大于2dB,在任意相邻的12dB内误差不应大于±1dB当探伤仪与符合4.2规定的斜探头连接后,CSK–IC试块上得到的灵敏度余量应大于评定线灵敏度10dB以上,性能测试除灵敏度余量的测试见附录C(补充件)外,其余均应按ZBJ04001规定的方法进行测试。
超声波检测—超声波探伤技术(无损检测课件)

1.4 工件对定位精度的影响
工件温度
• 当检测的工件温度 发生变化时,工件 中的声速发生变化, 探头折射角也随之 发生变化。
温度对折射 角的影响
1.5 缺陷对定位精度的影响
• 工件内缺陷方向也会 影响缺陷定位精度。
• 缺陷倾斜时,扩散波 束入射至缺陷时回波 较高,而定位时就会 误认为缺陷在轴线上, 从而导致定位不准。
• 当工件尺寸较小, 缺陷位于3N以内 时,利用底波调 灵敏度并定量, 将会使定量误差 增加。
2.5 缺陷状态对定量精度的影响
① 缺陷形状的影响
• 缺陷的形状:圆片形、球形和圆柱形 • 缺陷距离一定,缺陷波高随缺陷直径的变化:圆片形缺陷最快,长圆
柱形缺陷最慢; • 缺陷直径一定,缺陷波高随距离的变化:圆片形和球形缺陷较快,长
2.2 仪器及探头性能对定量精度的影响
④ 探头K值的影响
• 不同K值的探头的灵敏度不同。 • 当K=0.7-1.5(=35°~55°)时,回波较高。 • 当K=1.5~2.0(=55°~63°)时,回波很低,容易引起漏检。
2.3 耦合与衰减对定量精度的影响
耦合的影响
• 耦合层厚度等于半波长的整数倍时,声强 透射率与耦合剂性质无关。
时,声波在有机玻璃内反射回到 晶片,也会引起一些杂波。 • 更换探头的方法来鉴别探头杂波。
3.1 纵波探头非缺陷回波的判别
② 工件轮廓回波
• 当超声波射达工件的
台阶、螺纹等轮廓时
轮
廓
在示波屏上将引起一
回
些轮廓回波。
波
3.1 纵波探头非缺陷回波的判别
③ 幻象波 • 当重复频率过高时,在示波屏上就会产生幻象波,
2.2 穿透法
优 不存在探测盲区,判定缺陷方法简单,适用于连续的自动化 点 探测较薄的工件。
隋亚军-超声波无损探伤检测技术

2010年优秀科技论文(技术总结)超声波无损探伤检测技术超声波无损探伤检测技术—中铁十三局厦深铁路(广东段)工程指挥部隋亚军【内容提要】榕江特大桥全长7373.921km[主跨为110m+2×220m+110m钢桁梁柔性拱,在亚洲同类桥梁单跨跨度居首位,是厦深铁路控制性工程,本文通过介绍厦深铁路-5标榕江特大桥主桥钢桁梁埋弧自动焊接的检测技术,并对焊接效果进行了总结,为钢桁梁的顺利施工提供依据。
【关键词】超声波检测方法检测过程结果分析一.超声波检测1.超声波简介声波频率超过人耳听觉,频率比20千赫兹高的声波叫超声波。
用于探伤的超声波,频率为0.4-25兆赫兹,其中用得最多的是1-5兆赫兹。
利用声音来检测物体的好坏,这种方法早已被人们所采用。
由于超声波探伤具有探测距离大,探伤装置体积小,重量轻,便于携带到现场探伤,检测速度快,而且探伤中只消耗耦合剂和磨损探头,总的检测费用较低等特点,目前建筑业市场主要采用此种方法进行检测。
1.2超声波探伤的原理1.2.1超声波探伤是利用材料及其缺陷的声学性能差异对超声波传播波形反射情况和穿透试件的能量变化来检验材料内部缺陷的无损检验方法。
1.2.2利用现在广泛采用的是观测声脉冲在材料中反射情况的超声脉冲反射法,此外还有观测穿过材料后的入射声波振幅变化的穿透法和共振法。
常用的频率在0.5~5MHz之间。
1.3超声波检测方法超声波具有向一个方向直进的性质,因此从一个轧辊的表面向内部发射时,它就会直进到对面表面后反身而归,如果途中遇有缺陷,一部分超声波就会被反射而回,而返回的信号被阴极射线管接收,根据超声波走过的距离按比例在示波器上描出图形,从这个缺陷波与底面波的尺寸关系就可以确定缺陷的位置,根据其波形的大小,从缺陷波的形状可判断缺陷的形状和性质,但需要经验。
1.3.1脉冲反射法超声波以持续极短的时间发射脉冲到被检试件内,根据反射的情况来检测试件缺陷的一种方法脉冲反射式超声波法同其他无损检验方法相比主要优点是:穿透能力强,探测深度可达数米灵敏度高,可发现与直径约十分之几毫米的空气隙反射能力相当的反射体,在确定内部反射体的位向、大小、形状及性质等方面较为准确仅须从一面接近被检验的物体可立即提供缺陷检验结果、操作安全、设备轻便。
无人机传感器技术 4.4.4 超声波探伤

4.4.4 超声波探伤超声波探伤是无损探伤技术中的一种主要的检测手段,它主要用于检测板材、管材、锻件和焊缝等材料中的缺陷(如裂缝、气孔、夹渣等)、测定材料的厚度、检测材料的晶粒、配合断裂力学对材料使用寿命进行评价等。
超声波探伤因具有检测灵敏度高、速度快、成本低等优点,而得到人们普遍的重视,并在生产实践中得到广泛的应用。
1.穿透法探伤穿透法探伤是根据超声波穿透工件后能量的变化状况来判断工件内部质量的方法。
穿透法探伤使用两个超声波探头,置于工件相对两面,一个发射声波,一个接收声波。
发射波可以是连续波,也可以是脉冲。
超声波穿透法探伤原理图如图4-13所示,当在探测中工件内无缺陷时,接收能量大,仪表指示值大;当工件内有缺陷时,因部分能量被发射,接收能量小,仪表指示值小。
根据接收探头接收到的能大小,就可以把工件内部的缺陷检测出来。
图4-13 超声波穿透法探伤原理图穿透法探伤可避免盲区,适用于自动探伤,适宜探测薄板和超声波衰减大的材料。
但探测灵敏度较低,不能发现小缺陷;根据能量的变化可判断有无缺陷,但不能定位;对两探头的相对距离和位置要求较高。
2.反射法探伤反射法探伤是以超声波在工件中反射情况的不同来探测工件内部缺陷的。
反射法探伤又分为一次脉冲反射法和多次脉冲反射法。
(1)一次脉冲反射法一次脉冲反射法是以一次底波为依据进行探伤的方法,如图4-14所示。
高频脉冲发生器产生脉冲(发射波)施加在探头上,激励探头的压电晶体振动,从而产生超声波。
超声波以一定速度向工件内部传播,一部分超声波遇到缺陷F 时反射回米,另一部分超声波继续传到工件底面B后反射回来,二者都被探头接收并转换成电脉冲。
发射脉冲T、缺陷脉冲F及底脉冲B经放大后,在显示屏上显示出来。
图4-14 发射法探伤原理若工件中没有缺陷,则超声波传到工件底部才发生反射,在荧光屏上只出现发射脉冲T和底脉冲B。
若工件中有缺陷,一部分脉冲在缺陷处产生反射,另一部分继续传播到工件底面产生反射,在荧光屏上除出现发射脉冲T和底脉冲B 外,还出现缺陷脉冲F。
无损检测超声波探伤仪的分类工作原理及操作使用

无损检测超声波探伤仪的分类、工作原理及操作使用无损检测包括射线检测(RT)、超声检测(UT)、磁粉检测(MT)、渗透检测(PT)和涡流检测(ET)等五种检测方法。
主要应用于金属材料制造的机械、器件等的原材料、零部件和焊缝,也可用于玻璃等其它制品。
射线检测适用于碳素钢、低合金钢、铝及铝合金、钛及钛合金材料制机械、器件等的焊缝及钢管对接环缝。
射线对人体不利,应尽量避免射线的直接照射和散射线的影响。
超声检测系指用A型脉冲反射超声波探伤仪检测缺陷,适用于金属制品原材料、零部件和焊缝的超声检测以及超声测厚。
磁粉检测适用于铁磁性材料制品及其零部件表面、近表面缺陷的检测,包括干磁粉、湿磁粉、荧光和非荧光磁粉检测方法。
渗透检测适用于金属制品及其零部件表面开口缺陷的检测,包括荧光和着色渗透检测。
涡流检测适用于管材检测,如圆形无缝钢管及焊接钢管、铝及铝合金拉薄壁管等。
磁粉、渗透和涡流统称为表面检测。
超声波探伤的物理基础第一节基本知识超声波是一种机械波,机械振动与波动是超声波探伤的物理基础。
物体沿着直线或曲线在某一平衡位置附近作往复周期性的运动,称为机械振动。
振动的传播过程,称为波动。
波动分为机械波和电磁波两大类。
机械波是机械振动在弹性介质中的传播过程。
超声波就是一种机械波。
机械波主要参数有波长、频率和波速。
波长λ:同一波线上相邻两振动相位相同的质点间的距离称为波长,波源或介质中任意一质点完成一次全振动,波正好前进一个波长的距离,常用单位为米(m);频率f:波动过程中,任一给定点在1秒钟内所通过的完整波的个数称为频率,常用单位为赫兹(Hz);波速C:波动中,波在单位时间内所传播的距离称为波速,常用单位为米/秒(m/s)。
由上述定义可得:C=λ f ,即波长与波速成正比,与频率成反比;当频率一定时,波速愈大,波长就愈长;当波速一定时,频率愈低,波长就愈长。
次声波、声波和超声波都是在弹性介质中传播的机械波,在同一介质中的传播速度相同。
无损检测-超声波探伤

pd
3.5 垂直入射超声波在界面两侧声压的分配
界面声压反射率: 界面声压反射率
Rp=pr/pe=(Z2-Z1)/(Z2+Z1)
界面声压透射率: 界面声压透射率:
Dp=pd/pe=2Z2/(Z2+Z1)
由上两式可见: ① 如Z1≈Z2 则 Rp ≈0 Dp ≈1
超声波检测无法检出声阻抗与焊缝金属很接近的金 属夹杂物的原因。 ②如Z2<<Z1 则 Rp ≈-1 Dp ≈0
αL
有机玻璃
α
钢 γ
3.12
外壳形状
5P8×12k2.5 k=折射角γ的正切值 晶片面积8×12mm2 发射接收f=5MHz 的超声波
2 横波探头的主要性能 ⑴折射角γ值(k值) 决定了声束入射于工件的方向和声波传播途 径,是缺陷定位计算的重要数据。 公称折射角:45 50 60 K值: 1.0 1.5 2.0 2.5 70
对奥氏体钢焊缝进行探伤时,宜选用频率较低的探头。
⑵吸收引起的衰减 因介质的粘滞性使部分声能转变为热 能而导致的声能损耗 ⑶声束扩散引起的衰减 随着传播距离的增大,波束截面增大 使单位面积上声能逐渐减小所致。
2 衰减表示方法与衰减系数 ⑴用底波高度或底波反射次数的多少粗略估计。
δ
(a) 3.8
(b)
L
α
αs αL
S1
L1
介质Ⅰ 介质Ⅱ γL γs L2 S2
3.7有耦合剂的反、折射
② 横波入射到钢/空气界面将 会产生反射纵横波
L 有机玻璃 α3m S 钢 L 空气 3.8 α3m示意图
α3m=33.2o
⑶ 聚焦
五、超声波的衰减
随着声程的增加,超声波的能量逐渐减弱的现象 1 衰减的原因 ⑴散射引起的衰减 超声波遇到尺寸与波长可比的障碍物,并因此而产生球 面波的现象称为超声波的散射。
超声波无损探伤在油管检测中的应用
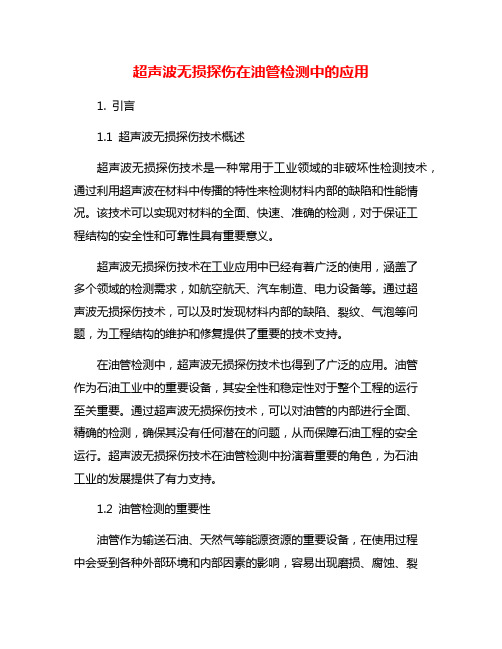
超声波无损探伤在油管检测中的应用1. 引言1.1 超声波无损探伤技术概述超声波无损探伤技术是一种常用于工业领域的非破坏性检测技术,通过利用超声波在材料中传播的特性来检测材料内部的缺陷和性能情况。
该技术可以实现对材料的全面、快速、准确的检测,对于保证工程结构的安全性和可靠性具有重要意义。
超声波无损探伤技术在工业应用中已经有着广泛的使用,涵盖了多个领域的检测需求,如航空航天、汽车制造、电力设备等。
通过超声波无损探伤技术,可以及时发现材料内部的缺陷、裂纹、气泡等问题,为工程结构的维护和修复提供了重要的技术支持。
在油管检测中,超声波无损探伤技术也得到了广泛的应用。
油管作为石油工业中的重要设备,其安全性和稳定性对于整个工程的运行至关重要。
通过超声波无损探伤技术,可以对油管的内部进行全面、精确的检测,确保其没有任何潜在的问题,从而保障石油工程的安全运行。
超声波无损探伤技术在油管检测中扮演着重要的角色,为石油工业的发展提供了有力支持。
1.2 油管检测的重要性油管作为输送石油、天然气等能源资源的重要设备,在使用过程中会受到各种外部环境和内部因素的影响,容易出现磨损、腐蚀、裂纹等问题,导致泄漏、爆炸等安全事故。
油管检测的重要性不言而喻。
油管检测可以及时发现管道内部的问题,做到预防于未然。
通过定期对油管进行检测,可以发现管道内部存在的各种隐患,及时修复或更换受损部分,避免了事故的发生,保障了生产和运输的安全。
油管检测可以提高设备的利用率和运行效率。
通过及时检测和维护,可以确保油管设备处于良好的工作状态,减少了停机维修时间,提高了设备的利用率,降低了生产成本。
油管检测还可以保护环境和人身安全。
一旦发生泄漏或爆炸事故,不仅会造成能源资源的浪费,还会对周围环境和人员造成严重危害。
通过油管检测,可以有效地减少这类事故的发生,保护生态环境和人民生命财产安全。
油管检测的重要性不仅体现在保障生产运营的顺利进行,还关乎环境与人身安全。
超声波无损检测方案及工作分解

超声波无损检测方案及工作分解1、检测依据GB 50205-2001 钢结构工程施工质量验收规范GB/T 29712-2013 焊缝无损检测超声波检测验收等级GB/T 11345-2013 焊缝无损检测超声波检测技术、检测等级和评定2、主要检测仪器设备仪器、探头、试块及耦合剂选择:2.1检测仪器选用南通探神数字式TS-2007L超声波探伤仪。
2.2探头选择:斜探头,探头折射角在35°~70°之间,换算成K值为0.7~2.7,探测频率2~5MHz。
根据工件厚度适当选择。
2.3试块选择:试块使用CSK-ⅠB和RB-1试块。
根据实际检测中需求选择适当的试块。
2.4耦合剂使用机油或浆糊。
3、检测工件的要求及检测比例3.1检测工件探头移动区表面应平滑,无焊接飞溅、铁屑、油污及其他外部杂质。
探头移动区表面的不平整度,不应引起探头和工件的接触间隙超过0.5mm。
工件检测时温度应在0~60℃。
3.2检测比例见表1表1 一、二级焊缝质量等级及缺陷分级4、仪器调整及校验4.1 时基线和灵敏度设定时基线和灵敏度设定时的温度与焊缝检测时的温度之差不应超过15℃。
检测过程中至少4小时或检测结束时,应对时基线和灵敏度设定进行效验。
如果在检测过程中发现偏离,应按表2要求进行修正。
表2灵敏度和时基线修正5.2设定参考灵敏度应选用下列任一技术设定参考灵敏度:技术1:以直径3mm横孔作为基准反射体,制作距离-波幅曲线(DAC)。
技术2:以规定尺寸的平底孔(见表3和表4)作为基准反射体,制作纵波/横波距离-增益-尺寸曲线(DSG)。
技术3:应以宽度和深度为1mm的矩形槽作为基准反射体。
该技术仅应用于斜探头(折射角)≥70°)检测厚度8mm≤t〈15mm的焊缝。
技术4:串列技术。
以直径为6mm平底孔(所有厚度)作为基准反射体,垂直于探头移动区。
该技术仅用于斜探头(折射角为45°)检测厚度t≥15mm的焊缝。
- 1、下载文档前请自行甄别文档内容的完整性,平台不提供额外的编辑、内容补充、找答案等附加服务。
- 2、"仅部分预览"的文档,不可在线预览部分如存在完整性等问题,可反馈申请退款(可完整预览的文档不适用该条件!)。
- 3、如文档侵犯您的权益,请联系客服反馈,我们会尽快为您处理(人工客服工作时间:9:00-18:30)。
3、探头的主要参数与型号
1)探头K值
– K值大小决定声束入射工件的方向和在工件中的传
播途径,可以依据该值进行缺陷的定位计算,因此 探头使用磨损后应重新测量K值。
2)前沿长度
– 声束入射点至探头前端面的距离称为前沿长度。
3、探头的主要参数与型号
2.5 B 20 Z
直探头
5 P 6x6 K 3 斜探头k=3 以K值表示的斜探头 方形晶片尺寸 锆钛酸铅陶瓷晶片 基本频率5.0Mz
测定探头值
– 利用Φ50mm孔的反射,用同样方法找出其最高反射
波,此时与入射点对应的K值,即为探头K值。
4、探伤仪的调节
探伤范围的调节 扫描速度的调节 探伤灵敏度的选定及其调整
二、实时探伤操作
1.确定检验区宽度
–
检验区宽度应是焊缝宽度加上焊缝两侧相当于母材厚度30%的 区域,一般为10~20 mm 直射法探伤时,移动区宽度L﹥0.75P; 一次反射法时,移动区宽度L﹥1.25P 锯齿形扫查、基本扫查、平行扫查、斜平行扫查
范围很宽,按照人的听力极限,将声波划分为三种: 即次声波、声波和超声波。其中:
当f<20Hz时,叫做次声波; 当f为20Hz~20kHz时,叫做声波; 当f>20kHz时,叫做超声波。
注:声波是人耳可以听得见的,而次声波和超声波则 是人耳听不见也感觉不到的 。
一、超声波的产生与接收
2、斜探头
利用透声斜楔块使声束倾斜于工件表面射入工 件的探头称为斜探头。 用于发射和接收横波。 组成:
– 探头蕊(压电元件和吸收块组成,与直探头相似) – 斜楔块 – 壳体
斜楔块
斜楔块由有机玻璃制成,它与工件组成固定倾斜的异 质界面,使压电元件发射的超声波通过波形转换,使 在工件中传播的只有折射横波。 斜楔块的角度不同就使得入射工件的超声波的角度不 同,因而可以探测不同厚度的工件。 通常斜探头是以横波在钢中的折射角标称:γ=400 、 450 、 500 、 600 、 700 ; 或 以 折 射 角 的 正 切 值 标 称 : k=tgγ=1.0、1.5、2.0、2.5、3.0。
表 3 —7
相应检验等级的主要检验项目
检验等级 板厚 A δ≤ 50 1 1 1 δ≤ 100 B δ> 100 2 2 2 δ≤ 100 2 1 2 C δ> 100 2 2 2
项目
探头角度数量
探伤面数量 探伤侧数量
1或 2
1或 2 2
串列扫查
母材检验 纵向缺陷探测方向与次数 横向缺陷探测方向与次数 1 0 2或 4 0或 4 4 0或 4
探头;大厚度工件宜采用 K 值小的探头。且探头K 值在每次使用前和使用过程中要重新测定。
探头K值测定
测定探头入射点
–
把探头放在CSK—IB试块上前后移动,找出R100mm 圆弧面最高反射波,此时在斜楔块上与R100mm圆弧 面圆心对应的点即为探头的入射点,同时还可求得 入射点至探头底面前端的距离,即前沿长度。
0或 2
1 ≥6 4
2
1 10 4
2、探伤面及探伤方法的选择
选择探伤方法要根据工件的结构特点和采用的 焊接方法的特点,并结合有关标准进行,见表 3—8 探伤面应根据不同的检验等级和板厚来选择, 见表3—7、表3—8的规定。
表3—8
板厚/mm
探伤面及使用折射角
探 A级 伤 B级 面 C级 探伤方法 使用K值
– 利用R100mm圆弧面测定探头入射点和前沿长度,
利用Φ50mm孔的反射波测定斜探头折射角或K值。 – 校验探伤仪的水平线性和垂直线性。 – 利用Φ1.5mm横通孔的反射波调整探伤灵敏度,利 用R100mm圆弧面调整探测范围。
对比试块(RB试块)
RB试块主要用于绘制距离—波幅曲线,调整探测范围 和扫描速度,确定探伤灵敏度和评定缺陷大小。 试块有三种,分别适用于不同的板厚 。
3230
2260 1460 3500 — — —
3、异质界面上的 透射、反射、折射和波形转换
垂直入射:透射、反射和绕射 倾斜入射:反射、折射和波形转换
4、具有可穿透物质 和在物质中有衰减的特性
1.散射引起的衰减
–
超声波在传播过程中,遇到不均匀的和各向异性的金属晶粒时 则会在界面上发生散乱反射、折射和波形转换,从而消耗超声 波的能量,这种衰减称为散射衰减。 由于质点之间的相对运动和相互摩擦使部分声能转换为热能, 通过热传导引起衰减,这种衰减称为介质吸收引起的衰减。 超声波在传播过程中会发生扩散,且随传播距离的增加,扩散 程度也将会增大。声束扩散导致声束的截面增大,从而使单位 面积上的声能减小。这种形式引起的超声波能量衰减称为扩散 衰减。
第四节
直接接触法超声波探伤
一、探伤前的准备 二、实时探伤操作 三、缺陷性质估判和定位 四、焊缝质量评定
一、探伤前的准备
1、检验等级的确定 2、探伤面及探伤方法的选择 3、探头的选择 4、探伤仪的调节
1、检验等级的确定
GB/T11345—1989标准中把检验划分为A、B、C三个 级别: A级—检验时完善程度最低,难度系数最小。适用于 普通钢结构检验。 B级—检验时完善程度一般,难度系数较大。适用于 压力容器检验、船舶等。 C级—检验时完善程度最高,难度系数最大。适用于 核容器与管道等检验。 各检验等级的的检验范围见表3—7。
第三节
超声波探伤原理及应用
直接接触法超声波探伤
– 垂直入射法 – 斜角探伤法
液浸法超声波探伤
垂直入射法
垂直入射法(简称垂直法)是采用直探头将 声束垂直入射工件表面进行探伤。 该法是利用纵波进行探伤,故又称纵波法
垂直法探伤能发现与探伤面平行或近似于平 行的缺陷,适用于厚钢板、轴类、轮等几何 形状简单的工件。
束射性
– 声源发出的超声波能集中在一定区域内定向辐射。
2、超声波能在弹性介质中传播, 不能在真空中传播
超声波也有不同的波形,并且各类型波的传播介质、 传播速度和本身具有的特点也不完全相同。(表3-1、 表3-2) 超声波在同一介质中传播时,纵波速度最快,横波次 之,表面波最慢。 对同一频率在同一介质中传播的超声波纵波波长最长, 横波次之,表面波最短。 由于探测缺陷的分辨力(超声波分辨相邻缺陷的能力) 与波长有关,波长越短分辨力越高,因此表面波的分 辨力最高,横波次之,纵波最低。
裂
纹
缺陷回波高度大,波幅宽,常出现多峰。 探头平移时,反射波连续出现,波幅有 变动;探头转动时,波峰有上下错动现 象。
夹
渣
点状夹渣的回波信号类似于单个气孔。 条状夹渣回波信号多呈锯齿状,波幅不 高且形状多呈树枝状。探头平移和绕缺 陷移动时,波幅都会发生变化。
未焊透
未焊透的回波波幅均较高。探平头移 时,波形较稳定。在焊缝两侧探伤时, 均能得到大致相同的反射波幅。
水平调节法定位
缺陷在探头前方的下面,其位置可用入射点至 缺陷的水平距离Lf、缺陷到探伤面的垂直距离Zf 两个参数来确定。 探伤仪按水平1:n调节横波扫描速度
斜角探伤法
斜角探伤法(简称斜射法)是采用斜探头将声 束倾斜入射工件表面进行探伤。 该法是利用横波进行探伤,故又称横波法。 斜角探伤法能发现与探测表面成角度的缺陷, 常用于焊缝、环状锻件、管材的检查。
– 直射法:在0.5跨距的声程以内,超声波不经底面
反射而直接对准缺陷的探伤方法,又称一次波法。 – 一次反射法:超声波只在底面反射一次而对准缺陷 的探伤方法,又称二次波法。
2.确定探头移动区
– –
3.单探头的扫查方法
–
4.双探头的扫查方法
–
串列扫查、交叉扫查和V形扫查
三、缺陷性质估判
气孔 裂纹 夹渣 未焊透 未熔合
气
孔
单个气孔回波高度低,波形为单峰,较稳定, 当探头绕缺陷转动时,缺陷波高大致不变,但 探头定点转动时,反射波立即消失;密集气孔 会出现一簇反射波,其波高随气孔大小而不同, 当探头作定点转动时,会出现此起彼伏现象。
第三章
超声波探伤
本章将重点讲述超 声波的性质,直接接触 法超声波探伤;简单介 绍超声波探伤设备。
超声波探伤
第一节 第二节 第三节 第四节 超声波的产生、性质及衰减 超声波探伤设备简介 超声波探伤原理及其应用 直接接触法超声波探伤
第一节 超声波的产生、性质及衰减
声波及其分类
– 声波是一种机械波,它的频率(通常用字母 f 表示)
未熔合
当声波垂直入射该缺陷表面时,回波高 度大。探头平移时,波形稳定。焊缝两 侧探伤时,反射波幅不同,有时只能从 一侧探测到。
四、缺陷定位
垂直入射法缺陷定位 斜角探伤法缺陷定位
– 水平调节法定位 – 深度调节法定位
垂直入射法缺陷定位
用垂直入射法探伤时,缺陷就在直探头的下面, 缺陷定位只需确定缺陷在工件中的深度即可。 当探伤仪按1:n调节纵波扫描速度时,则有 Zf=nτf
表3—2
材料种类
铝 铸铁
常见固体材料的声速
密度(g/cm3) 2.7
7.3
纵波CL(m/s) 6260
5600
横波CS(m/s) 3080
3200
钢
铜 有机玻璃 陶瓷 机油 水(20℃) 空气
7.8
8.9 1.18 2.4 0.92 1.0 0.0012
5950
4700 2730 5600 1400 1500 340