色差的控制
染色工艺色差控制的关键点
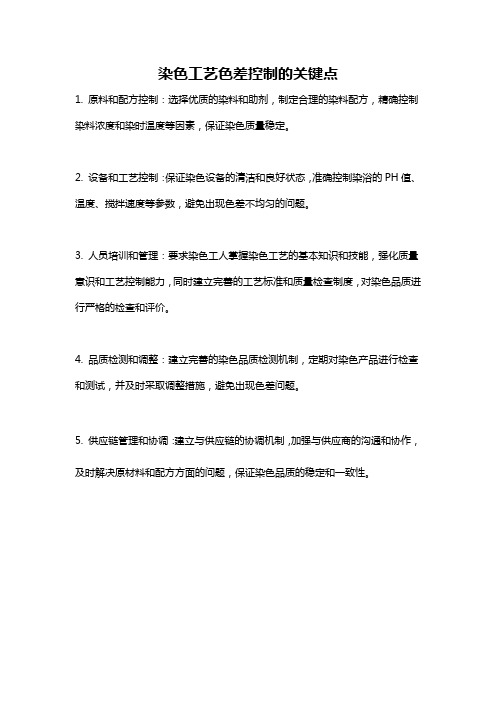
染色工艺色差控制的关键点
1. 原料和配方控制:选择优质的染料和助剂,制定合理的染料配方,精确控制染料浓度和染时温度等因素,保证染色质量稳定。
2. 设备和工艺控制:保证染色设备的清洁和良好状态,准确控制染浴的PH值、温度、搅拌速度等参数,避免出现色差不均匀的问题。
3. 人员培训和管理:要求染色工人掌握染色工艺的基本知识和技能,强化质量意识和工艺控制能力,同时建立完善的工艺标准和质量检查制度,对染色品质进行严格的检查和评价。
4. 品质检测和调整:建立完善的染色品质检测机制,定期对染色产品进行检查和测试,并及时采取调整措施,避免出现色差问题。
5. 供应链管理和协调:建立与供应链的协调机制,加强与供应商的沟通和协作,及时解决原材料和配方方面的问题,保证染色品质的稳定和一致性。
色差控制管理规定

1、目的规范生产过程产品色差控制流程,保证生产过程中产品颜色与标样一致。
2、范围本程序适用于公司各生产工序。
3、定义无4、参考文件无5、职责5.1品管部负责标样的签发。
5.2品管部IPQC负责过程生产中的监控。
5.3生产车间负责按照标准操作。
6、工作内容6.1晒版6.1.1晒版须根据作业指导书要求设置曝光时间、显影时间。
晒版标准为阳图2%有点子,98%有轮廓,3%点子结实完整,97%的网点清晰透亮无灰雾。
6.1.2对于网点版,必须如实记录灯使用情况、爆光时间、药水情况,便于下次生产时还原工艺参数,以保障每次晒出的网点版的一致性。
6.1.3各种色彩控制条齐全完整。
6.2机台开机签样与标样色差的控制6.2.1公司所有生产的产品菲林必需有标准的颜色测控条。
6.2.2所有金银卡纸、镭射纸和珠光打底的产品(包括烟标和社会单)机台在签样与生产时按以下要求操作。
6.2.2.1颜色要求:目测与标样一致,以标样为准取五点平均后设值,用CRII5检测,△a≤1.5,△b≤1.5△E≤3.0,a,b值尽量与标样a,b值接近。
6.2.2.2取值要求:雪花油类在印刷雪花油后直接测量,非雪花油类用蒙片蒙住后测量取值,有渐变网在渐变网为零和100%处分别取值。
纸张有阴阳面的在同一面取值。
6.2.2.3测量要求:雪花油类产品在印刷雪花油后直接测量,非雪花油类用蒙片蒙住后测量,有渐变网在渐变网为零和100%处分别测量6.2.2.4蒙片要求:干净,统一,细哑光,与被检测色接触紧密。
6.2.2.5签样要求:目测与标样一致,△a≤1.5,△b≤1.5△E≤3.0,a,b值尽量与标样a,b值接近,横向密度D±0.03,D值尽量与标样一致。
6.2.2.6控制要求:目测与标样一致,△a≤1.5,△b≤1.5△E≤3.0,a,b值尽量与标样a,b值接近,横向密度D±0.03,D值尽量与标样一致,整批密度D±0.05,白卡或铜版纸密度D±0.02.6.2.3直接在白卡纸或铜版纸上面印刷的产品(包括烟标和社会单)机台在签样和生产时,颜色以仪器检测△a≤1.0,△b≤1.0,深色△E≤1.3,浅色△E≤0.8,横向密度D ±0.02,整批密度D±0.03.目测与标样一致。
注塑产品的色差控制
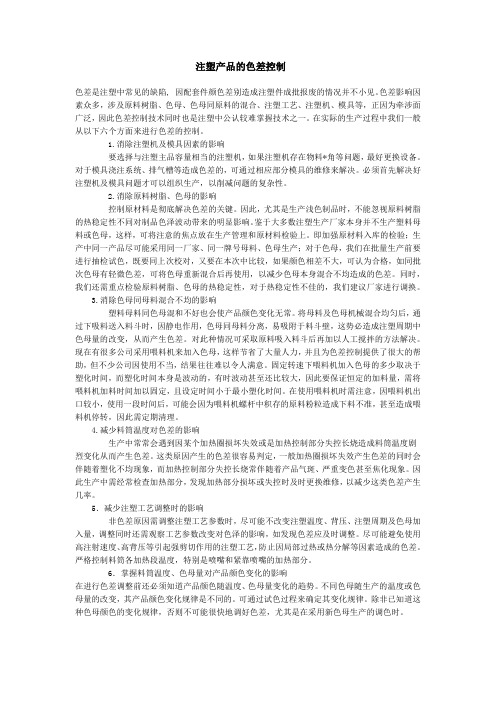
注塑产品的色差控制色差是注塑中常见的缺陷, 因配套件颜色差别造成注塑件成批报废的情况并不小见。
色差影响因素众多,涉及原料树脂、色母、色母同原料的混合、注塑工艺、注塑机、模具等,正因为牵涉面广泛,因此色差控制技术同时也是注塑中公认较难掌握技术之一。
在实际的生产过程中我们一般从以下六个方面来进行色差的控制。
1.消除注塑机及模具因素的影响要选择与注塑主品容量相当的注塑机,如果注塑机存在物料*角等问题,最好更换设备。
对于模具浇注系统、排气槽等造成色差的,可通过相应部分模具的维修来解决。
必须首先解决好注塑机及模具问题才可以组织生产,以削减问题的复杂性。
2.消除原料树脂、色母的影响控制原材料是彻底解决色差的关键。
因此,尤其是生产浅色制品时,不能忽视原料树脂的热稳定性不同对制品色泽波动带来的明显影响。
鉴于大多数注塑生产厂家本身并不生产塑料母料或色母,这样,可将注意的焦点放在生产管理和原材料检验上。
即加强原材料入库的检验;生产中同一产品尽可能采用同一厂家、同一牌号母料、色母生产;对于色母,我们在批量生产前要进行抽检试色,既要同上次校对,又要在本次中比较,如果颜色相差不大,可认为合格,如同批次色母有轻微色差,可将色母重新混合后再使用,以减少色母本身混合不均造成的色差。
同时,我们还需重点检验原料树脂、色母的热稳定性,对于热稳定性不佳的,我们建议厂家进行调换。
3.消除色母同母料混合不均的影响塑料母料同色母混和不好也会使产品颜色变化无常。
将母料及色母机械混合均匀后,通过下吸料送入料斗时,因静电作用,色母同母料分离,易吸附于料斗壁,这势必造成注塑周期中色母量的改变,从而产生色差。
对此种情况可采取原料吸入料斗后再加以人工搅拌的方法解决。
现在有很多公司采用喂料机来加入色母,这样节省了大量人力,并且为色差控制提供了很大的帮助,但不少公司因使用不当,结果往往难以令人满意。
固定转速下喂料机加入色母的多少取决于塑化时间,而塑化时间本身是波动的,有时波动甚至还比较大,因此要保证恒定的加料量,需将喂料机加料时间加以固定,且设定时间小于最小塑化时间。
专业的色彩管理和色差控制详解

四色 测量
印张测控条
(客户首签和大货首签)
分光密度仪
合格 收货
色差 ⊿E≦2.5
不合格 拒收
THANKS
ISO 12647-2∶2013标准的胶印过程控制
不同批次纸张色差
3%以下网点再现
50%网点扩大
实地密度浮动
中性灰的偏色
色彩的定义参数
L*= 100 white
L*= 50 grey
L*= 0 black
a*= - xx green
b*= + xx yellow
a*= + xx red b*= + xx blue
色差的定义公式
目录
01
色差的管理规范
02
色差的检测操作
观察标准三要素
c、
相同的标准光源-灯箱(D65和D50混合型)
相同的分光密度计-Xrite Exact 相同的测量位置(需标注)
b、记录标准灯管所使用的时间 所有标准的对色光源也是由灯管或灯炮所产生,而生产商也会列明其产 品在若干时间的运作内,其产品质量仍保持在可接受的公差内。 故此一个准确的时间记录器是不可缺少的。 通常这些灯管如果使用超过2000小时或一年,便需做出更换。
色差的颜色分析
当△L *<0,说明印刷样张的颜色比标准样张的颜色深,暗调部分图像易损失, 印刷时黑墨含量过高或油墨转移量不够。
若△a *>0、△b *>0,则说明印刷样张偏橙色,配墨时黄墨和品红墨含量过高或油 墨转移量过多;
若△a *>0、△b *<0,则说明印刷样张偏红,配墨时品红墨含量过高或油墨转移量 过多;
印刷标准上下限
同一产品的颜色标准和上下限样册 相同的颜色标准:Pantone PMS+色样册
色差管理方法

色差管理方法
以下是一些常见的色差管理方法:
1. 标准制定:明确产品的颜色标准,包括颜色的数值、公差范围等,确保生产和质量控制有明确的依据。
2. 光源控制:使用标准光源进行颜色评估,如D65 光源或其他特定光源,以减少光源差异对色差的影响。
3. 仪器测量:使用色差仪等专业仪器对样品进行测量,获取客观的颜色数据,以便准确评估色差。
4. **样本比较**:建立颜色标准样本或参考样本,与实际产品进行对比,直观判断色差是否符合要求。
5. 数据分析:对测量得到的颜色数据进行分析,统计色差的分布情况,找出问题的根源并采取改进措施。
6. 供应商管理:对原材料和零部件的供应商进行色差管理,要求其提供符合颜色标准的产品。
7. 生产过程控制:在生产过程中,对关键环节进行色差监测,及时发现并解决可能出现的色差问题。
8. 员工培训:培训相关人员,使其了解色差管理的重要性和方法,提高颜色识别和控制的能力。
9. 持续改进:定期评估色差管理的效果,总结经验教训,不断完善管理方法和流程。
10. 色彩管理系统:采用专业的色彩管理软件和设备,实现对颜色的精确控制和管理。
需要注意的是,具体的色差管理方法应根据实际情况和产品特点进行选择和调整。
同时,色差管理应贯穿整个生产过程,从设计、采购、生产到质量检验等环节都要加以重视,以确保产品的颜色质量符合要求。
色差管控标准

色差管控标准全文共四篇示例,供读者参考第一篇示例:色差管控标准是指在生产和加工过程中,为了确保产品的色彩一致性和质量稳定性,制定并执行的一系列措施和规范。
色差是指不同样品或产品之间在色彩方面的差异程度,色差管控标准的制定对于降低产品质量风险,提升生产效率,增强产品竞争力具有重要意义。
色差的出现可能源自原材料的差异、生产工艺的不足、设备的不稳定性等多方面因素,而严格的色差管控是防止这些因素带来色彩差异的有效手段。
在现代化生产加工中,色差管控标准已经成为企业保证产品色彩一致性、降低经营风险的基本要求。
色差管控标准的制定要根据具体产品的特性和生产工艺流程来确定,一般包括以下几个方面:确定色差的测量标准和方法。
对于不同产品来说,需要确定相应的色彩空间和色彩参数,以及使用何种色差仪器进行测量和检验。
明确色差的容忍度和界限。
必须根据产品的使用环境和需求,确定适宜的色差范围,确保在一定范围内的色差不会影响产品的质量和形象。
建立良好的色彩管理体系。
包括明确责任和权利、制定相应的SOP标准操作规范、配备合适的检测设备和人员等。
持续进行色差监控和改进。
通过定期监测产品的色差情况,及时发现问题并采取纠正措施,保证产品色彩的一致性和稳定性。
色差管控标准的实施有利于提高产品的质量稳定性和一致性,有效地降低产品的赔偿风险和投诉率。
对于消费者来说,也可以增加购买信心和满意度,提升品牌形象和市场竞争力。
色差管控标准的制定和执行是现代生产加工中的重要环节,对于提升企业产品质量、节约生产成本、提高客户满意度具有重要意义。
只有不断完善和执行色差管控标准,才能确保产品色彩的一致性和稳定性,提升企业的市场竞争力和可持续发展能力。
【色差管控标准】。
第二篇示例:色差是指在同一种颜色下,由于不同光源、不同材料或不同观察条件下所引起的颜色不一致现象。
在工业生产和质量控制中,色差一直是一个重要的指标,影响着产品的质量和外观。
对色差进行管控是十分必要的。
精装饰面层色差控制方案

精装饰面层色差控制方案
首先,材料的选取非常关键。
在选择装饰面层材料时,应该尽量选择具有稳定色彩的材料,避免颜色在不同批次之间出现较大的差异。
此外,要确保材料的质量稳定,生产厂家的信誉和实力也是一个重要考量因素。
其次,在生产过程中,需要建立严格的质量控制体系。
对于颜料的配比、搅拌工艺、干燥工艺等都需要进行严格的控制,以确保每一批产品的色彩稳定性。
在施工环节,也需要注意多个方面。
首先,施工前需要对基层墙面进行处理,确保墙面平整、干燥,这有利于后续涂料的附着力和色彩稳定性。
其次,在施工过程中,要严格控制涂料的厚度和均匀性,避免因为涂料厚度不一致导致色彩差异。
同时,施工环境也需要注意控制,避免灰尘、湿度等外界因素对涂料造成影响。
此外,还需要建立完善的质量管理体系,包括对原材料、半成品和成品进行抽检和记录,及时发现问题并进行调整。
同时,也要加强与供应商的沟通和协调,确保原材料的质量稳定。
总之,精装饰面层色差控制方案需要从材料选取、生产过程、施工环节以及质量管理等多个方面进行全面考虑和管理,只有这样才能确保最终的装饰效果达到设计要求。
石材色差控制措施

石材色差控制措施
1、要求荒料生产商将每一块荒料的下锯方向标注清楚,保证大板块的基色一致,相邻产出的荒料按顺序编号。
2、在加工厂将荒料锯成大板后,进行磨光或水喷处理,再进行初步拼色。
3、按幕墙公司的石材编号及加工单切割成工程板,再次按每一单元板块内的编号进行预拼,合格后,在板块上标上编号,按顺序装箱,运至幕墙装配车间或工地现场。
4、要用大锯切割荒料,按照石材加工图尺寸,合理选择荒料尺寸,避免石材与荒料尺寸相差较大而浪费荒料。
5、小面处理:石材是脆性材料,切成棱角分明的板块后,极易在装箱运输及安装过程中造成崩边掉角,由于崩边掉角的产生会使整个立面效果大打折扣,俗话说是经不住细看。
因此,我司通常的做法是对每条边进行倒边3mm处理,同时对倒边后的小面也进行磨光处理,这样,可以使拼装后的立面非常精美。
对于外露的阳台小角,也一定要进行磨光处理。
6、要留适当的备板。
在整个组装及安装过程中,在幕墙投入使用后,难免会产生一些破损,如无备板,可能会造成极大的麻烦,或是破损的石材不能及时更换,不但影响美观,还造成安全隐患。
一般需要1-2%的备板。
7、包装:须用木箱包装,同时四周均要用白色泡沫垫加以保护,切忌用其他易褪色的物质作保护,否则会造成石材表面的污染。
8、现场施工:石材进场后,项目部技术负责人组织质量员及施工员等进行拼版检查,将石材按照色差进行分级,对色差非常明显的板块清除出场,要求供货商进行更换。
9、施工过程:在施工过程中,对安装在同一立面的石材进行色差对比,无色差或肉眼很难分辨的安装在幕墙正立面中央,根据色差大小逐渐向两边过渡,将色差较大的安装在幕墙边缘,防止幕墙整体出现色差。
- 1、下载文档前请自行甄别文档内容的完整性,平台不提供额外的编辑、内容补充、找答案等附加服务。
- 2、"仅部分预览"的文档,不可在线预览部分如存在完整性等问题,可反馈申请退款(可完整预览的文档不适用该条件!)。
- 3、如文档侵犯您的权益,请联系客服反馈,我们会尽快为您处理(人工客服工作时间:9:00-18:30)。
在印染行业中,连续轧染色差的概念范围很广,有对样色差,批间色差、底面色差、左中右色差、批内色差等。
这是印染工作者长期遇到的复杂而又难以解决的质量问题。
随着我国纺织品出口扩大,参与国际性竞争愈趋激烈,品质的要求也愈趋严格。
目前出口染色产品中,左中右色差和批内色差的标准要求在4.5级以上,远远高于我国国家标准。
同时色差的评定,也由传统的目光评级转向电脑的测色和鉴定。
即由传统的匠人技艺上升为科学技术,颜色的传递开始由实物色扳向数字化过渡到电脑的对色为CMC、DE值控制在0.6以内,批内色差是0.9以内。
而且对色光源亦从普通的办公室灯光D65、CWF、TL84、D75发展到U3O、HORIZON、INCA等灯光光源对色,并且由一灯对色增加到两灯,叁灯分别对色而要求色光不变。
为了达到客户的品质要求,提高企业出口竞争能力,控制、减少以至克服染色色差已成为印染工作者一个重要课题。
本文笔者主要针对如何控制减少左中右色差(俗称边色)和批内色差(俗称LOT色)。
根据多年实践体会,仅供参考。
一.抓好原材料的稳定性,可靠性,是控制色差的基础。
染色产品的原材料,主要指坯布和染化料,无论批量大小,要求原材料前后品质一致是确保克服LOT色的重要条件。
即使客观上原材料品质有异,也必须做到心中有数,处理有别,把LOT色严格控制在最少量的范围内。
具体有如下做法:l、同一色号的坯布,要求采购部门尽量购入同一棉织厂,同一个批次产地配棉的坯布。
2、如中间商供坯,必须分清不同棉织厂的产品,如有两个厂的坯布,投产时需按批号分别投产。
必要时前处理及染色工艺用料要作适当调整,以克服该批产品的批内色差。
3、对一些特殊产品,如亚麻、亚麻棉等半漂坯,虽经前处理,但敏感色仍难以控制其LOT色变化。
控制的方法可先在每卷取样l米,做好每卷与试样的编号记录,试染较敏感的颜色。
然后根据试样LOT色的结果,将每卷分批投产。
染色时分批调整,可减少LOT色的产生。
4、凡同一色号产品,遇原材料变化(包括坯布产地来源,染料,整理剂)供应部门必须通知技术部门,分类堆放,严格对比测试,以便工艺、技术上的合理调整,不能以不变应万变。
5、染化料要坚持按批次需用量备足,一个颜色不论大小,首先要求是同一产地、同一批次、同一色光、浓度的染料。
染料最好采用全验的办法,发现有异,要分开使用,重新试样,避免因染料的色光、力度不同产生LOT色。
6、不要忽视柔软剂等后整理剂对色光,深浅及边色的影响。
一个批量大的颜色,在柔软整理过程中,最好使用同一批产品在同一机台上生产。
同时也要剪样对色跟踪控制,否则批内LOT色和边色都难以控制。
7、染料选择是否正确,是控制LOT色及边色的又一关键。
许多企业接到客户来样后就交化验室打样,染料的配伍由打样人员决定。
问题是一些打样人员,恰恰缺乏生产实践经验。
他们只管对准小样与客户来样,而对染色上染率高低、色光变化快慢、配伍性的稳定、不同色样同色异谱的变化大小难以掌握。
经常小样送交客户确认,到生产时才发现问题的存在,这时再去更改染料配伍,又受到色光,对灯变化的制约,显得十分被动。
为此,我们采用的是由电脑配色,根据平时选定的染料组合,选择DE值最理想的配伍,一式六个的配伍,再送染色主管根据品质好、稳定性强(上染曲线大体相同)、成本低的原则挑选其中一组配伍,再交试化验室打样,这样的小样既符合客户要求,又保证生产时色差能控制到最稳定。
8、三原色虽有万种变化,但三原色并非万能。
实践证明:不能全部依靠三原色配搭,面对任何一个颜色,最好的办法是选择一个近似色染料为主色,根据色光再以其它染料微调。
同时染料的配伍要坚持宜少不宜多,越少越好的原则。
二、改革强化企业内部管理,是减少色差的保证。
印染产品之所以难做,印染厂之所以经营艰难,是印染产品的生产特点所致。
印染产品从坯布到成品往往经过10多道工序。
生产过程结合着化学、物理、机械、环境、人为等因素的变化。
10多个生产环节,任何一个环节出现问题,都会影响到最终产品的质量。
因此不断改革,强化印染产品的生产管理是控制减少色差、确保产品质量的需要。
1、坚持以技术为主导的生产运转管理,是控制色差的可行办法:印染厂传统的企业管理,存在着计划与技术,车间与技术,技术与设备各自为政的弊病。
对突出工艺技术和产品质量的位置不利。
几年前,我们把技术和计划合并为工务部,全厂生产只由工务部一个部门统领。
同时把生产运转管理方式改革为以技术为主导,以品质为重点的管理模式。
在确保色差小的前提下,针对难度大的颜色、品种、专门设计前处理工艺。
改变了以前多个品种千遍一律的炼漂工艺。
强调在生产运转管理中技术唱主角,计划、车间,设备当好配角。
并把染化料采购划属工务部统管。
在生产过程中,不论是计划的调整还是问题的处理,无论是日班还是中夜班,决策权,指挥权在技术主管手里。
这样避免了互相扯皮、重产轻质的矛盾,体现出"以工艺为核心"的作用确保了质量。
2、强化生产运转中的现场技术管理,是减少色差的关键:鉴于印染产品生产的特点,绝大多数色差或其它质量问题都是在生产运转中产生的。
长期以来,印染厂经常提及“预防为主”。
但如何体现在实际运转中呢? 我们认为印染厂的现场监控,质量跟踪、防微杜渐是最切实的“预防为主”,多年来,我们十分重视生产现场的管理。
一切生产计划、工艺技术人员、办公地点都设在生产工场里面。
无论工务部经理、车间主任,还是炼漂、卷染、轧染、后整理的技术主管及技术员,每天工作的重点就在车间现场,工场(车间)就是办公室。
这样,技术员对产品的运作、机台的运转、员工的操作、品质的变化都能了如指掌。
同时要求他们要做到 "三到现场"(开机时、转品种、因故停台必到现场),检查"四个第一"(接班第一件布、转品种第一件布、清机后第一件布、设备维修后第一件布),以及认真"抓好三化"(技术操作统一化、工艺上车检查制度化、下机质量标准化),擞到产品运转中工艺上车的"三度"(温度、速度、浓度)能保持正确及前后一致,从而各下机半制品质量也能稳定一致,是控制减少色差的关键。
3、履行各级质量否决权是控制减少色差的保证:印染生产最致命的弊病是松散的管理,马虎的把关。
经常出现大量质量问题才去追根寻源。
有效治理色差的办法,除严格的管理外,亟需各级对品质认真细致把关。
我们履行的是各级质量否决权,实践证明是减少色差的又一保证。
①使用部门发现原材料品质差异,有权责成其退货,更换的职权。
②工艺技术人员对设备状况要有严谨的检查制度。
发现设备问题而影响产品质量时,有权暂停生产。
通知设备部门维修到完好为止。
③染色技术主管对前处理品质拥有质量否决权。
凡发现炼漂半制品影响到染色质量时,有权责成其返工至达标。
④质检人员对染色产品中边色和LOT色的检查,达不到标准的,有权退回染色主管返修到达标为止。
⑤各级技术主管,对属下员工操作水平和表现,拥有奖惩、调整、辞退权力。
凡不符合该岗位技术操作要求的员工都要坚持处理,妥善安置。
⑥客户是“皇帝”,凡客户因品质问题要求产品返修,要无条件接受,不得扯皮拖延。
三、认真抓好各环节技术组织措施,才能达到减少色差的目的:染色的边色和LOT色,并非只有染色过程才会产生的。
边色和LOT色的控制,除涉及企业的管理和原材料外,还有工艺、技术、设备、操作及其控制方法等。
整个过程错综复杂,任何一个环节的失误,都会“触一发而动全身”,而造成色差。
1、前处理是控制色差的基础:染色出现边色和LOT色,多数人把注意力集中在染色工序里检查原因。
而忽视前处理这个产生色差的基础。
这个片面的倾向,显然是错误的。
可以说:前处理毛效、白度的一致,对色差的产生有着举足轻重的作用。
因此,要达到控制减少色差的目的,就必须花力气先抓好前处理这个基础工作。
①退浆净煮炼透:许多企业由于设备的局限或是计划及成本因素,往往把退浆煮炼合二为一。
但是这种退煮工艺,对于一些含浆率较高的产品(如灯芯绒,巴基斯坦及印度的坯布),其煮漂后毛效十分不稳定。
经过摸索,我们认为: 纯棉织物的前处理不能忽视退浆的重要性。
退浆净才能煮透,而只有退浆净才可以给前处理一个稳定的先决条件。
实践中,我们认为: 缝头→退浆→烧毛→煮漂是最理想的工艺设计,染色产品毛效一般要求8cm以上,左中右及前后的毛效波动要控制2cm以内。
②轧车轧液率一致:前处理轧车的轧液率,是否保持前后及左中右轧液一致是印染厂容易忽视的问题。
尤其是煮漂和丝光轧液的轧车,如轧液率不稳定,必然会引起染色色差产生。
因此,要把前处理重点轧车的维护保养提升到染色轧车水平去处理。
每周休息天,设备部都要重点去检修,每周的头班,技术人员都要测定轧车左中右的轧液率,符合要求才能投入生产。
③印染生产中,难以避免突发机电故障,这对容布量较大(600-800M)的连续性退煮漂机台影响较大。
发生此类问题,煮漂停放时间超过规定时,各厂应根据实际制定严谨的返工措施,并把返工的数量,箱号准确无误通知染色主管,以便染色时分别试样投产,可避免色差的产生。
④坚持前处理质量检查和明确移交标准。
前处理半制品的外观质量检查是较简单的。
内在质量检查如毛效、PH值、含浆率的检查也非难事。
本文前面已提及"下机质量标准化"必须持之以恒、认真落实。
但是上述的检查仍不能满足染色色差的实际要求。
我们的做法是: 在染色前一个工序,每箱布取样 1米,并连接缝头,送染色主管检查并搭染相同或接近的颜色去鉴定。
如染出的头子布每段深、浅光色及左、中、右一致,即为合格品,相反为不合格品。
前处理要采取措施修正,如出现试样有边色,可把染前白布样转90度车缝,以纬向调作经向,再染一次。
这样,可求证是染色还是前处理产生的边色。
⑤保持工艺、设备路线的稳定性:生产计划调度,绝对要服从工艺技术的需要,即一个批次或同色翻单再生产的品种,必须在同一工艺、同一设备上施工。
如确需要调整机台生产,必须事先征得技术部门的同意后执行,不得先斩后奏或斩了也不奏的现象出现。
另外: 目前宽幅染色产品 (60-63"坯布)越来越多,而较多的印染厂由于设备的局限,被迫一机多用,即同一机台生产宽幅和窄幅产品。
这种情况如何减少色差? 我们的做法是以技术为主导,要求计划编排把宽幅产品集中投产,生产前并要设备部门更换前处理重要部位的轧车,同时在轧染机前多配一台均匀轧车,专门生产宽幅产品。
这样边色的控制较为理想。
当然宽幅产品能做到专机专用就最理想了。
⑥磨毛产品的色差控制:随着服装市场的需要,磨毛后加工的产品越来越多,目前,除了纯棉织物外,还发展到弹力斜,弹力府,尼龙棉交织的磨毛。
由于磨毛的毛度前后和两边不一·也就易造成染色的边色和LOT色。