锅炉管道腐蚀的原因分析和建议
汽包锅炉给水分配管腐蚀原因分析
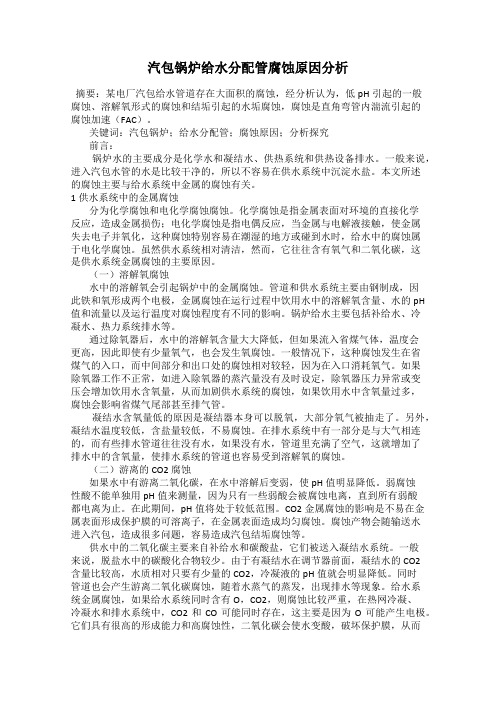
汽包锅炉给水分配管腐蚀原因分析摘要:某电厂汽包给水管道存在大面积的腐蚀,经分析认为,低pH引起的一般腐蚀、溶解氧形式的腐蚀和结垢引起的水垢腐蚀,腐蚀是直角弯管内湍流引起的腐蚀加速(FAC)。
关键词:汽包锅炉;给水分配管;腐蚀原因;分析探究前言:锅炉水的主要成分是化学水和凝结水、供热系统和供热设备排水。
一般来说,进入汽包水管的水是比较干净的,所以不容易在供水系统中沉淀水盐。
本文所述的腐蚀主要与给水系统中金属的腐蚀有关。
1供水系统中的金属腐蚀分为化学腐蚀和电化学腐蚀腐蚀。
化学腐蚀是指金属表面对环境的直接化学反应,造成金属损伤;电化学腐蚀是指电偶反应,当金属与电解液接触,使金属失去电子并氧化,这种腐蚀特别容易在潮湿的地方或碰到水时,给水中的腐蚀属于电化学腐蚀。
虽然供水系统相对清洁,然而,它往往含有氧气和二氧化碳,这是供水系统金属腐蚀的主要原因。
(一)溶解氧腐蚀水中的溶解氧会引起锅炉中的金属腐蚀。
管道和供水系统主要由钢制成,因此铁和氧形成两个电极,金属腐蚀在运行过程中饮用水中的溶解氧含量、水的pH 值和流量以及运行温度对腐蚀程度有不同的影响。
锅炉给水主要包括补给水、冷凝水、热力系统排水等。
通过除氧器后,水中的溶解氧含量大大降低,但如果流入省煤气体,温度会更高,因此即使有少量氧气,也会发生氧腐蚀。
一般情况下,这种腐蚀发生在省煤气的入口,而中间部分和出口处的腐蚀相对较轻,因为在入口消耗氧气。
如果除氧器工作不正常,如进入除氧器的蒸汽量没有及时设定,除氧器压力异常或变压会增加饮用水含氧量,从而加剧供水系统的腐蚀,如果饮用水中含氧量过多,腐蚀会影响省煤气尾部甚至排气管。
凝结水含氧量低的原因是凝结器本身可以脱氧,大部分氧气被抽走了。
另外,凝结水温度较低,含盐量较低,不易腐蚀。
在排水系统中有一部分是与大气相连的,而有些排水管道往往没有水,如果没有水,管道里充满了空气,这就增加了排水中的含氧量,使排水系统的管道也容易受到溶解氧的腐蚀。
生物质锅炉高温过热器腐蚀原因分析及对策

生物质锅炉高温过热器腐蚀原因分析及对策一、腐蚀原因分析1. 燃料成分生物质燃料中含有的灰分、硫分、氯分、碱金属等成分是高温过热器腐蚀的主要原因之一。
灰分中的硅酸盐、氧化铁等物质对过热器材料具有一定的腐蚀作用,而硫分则容易形成腐蚀性气体,如硫化氢、二氧化硫等。
氯分和碱金属也会对材料表面产生腐蚀破坏。
2. 燃烧温度生物质锅炉燃烧温度过高或不稳定会导致过热器的温度过高,使得材料受热和冷却的变化频繁,容易导致高温过热器材料的腐蚀破坏。
渣沉积、灰尘和燃料燃烧不完全等问题也会导致燃烧温度不稳定,从而加剧高温过热器的腐蚀程度。
3. 氧化腐蚀在生物质锅炉的高温过热器中,空气中的氧与金属表面的水蒸气和氧化物反应,会产生氧化腐蚀。
当燃料中含有硫分时,还容易形成硫酸腐蚀现象。
4. 结构设计生物质锅炉高温过热器的结构设计也会影响其腐蚀情况。
如过热器管道的焊缝处和弯头处易发生应力集中,容易导致腐蚀的加剧。
5. 操作维护生物质锅炉的操作维护情况也直接影响高温过热器的腐蚀程度。
如果操作不当或维护不到位,会导致锅炉燃烧不良,渣沉积过多,烟气中含有酸性物质,进而引发高温过热器的腐蚀问题。
二、对策措施1. 选择适合的材料在设计生物质锅炉高温过热器时,应选择耐高温、抗腐蚀的优质材料。
一般情况下,高温过热器管道材料常采用优质碳素钢、合金钢等材料,并在需要时进行防腐处理,以增加其抗腐蚀能力。
对于生物质燃料的选择和处理要求,尽量降低灰分、硫分、氯分和碱金属的含量。
通过科学的燃料混合、燃烧调节等方式,减少燃料中有害成分对高温过热器的腐蚀影响。
合理控制生物质锅炉的燃烧温度,保持其在安全范围内稳定燃烧,避免燃烧温度过高或波动过大,减少高温过热器受热和冷却的变化频率,降低腐蚀程度。
通过在燃烧室设置适当的氧化物吸附剂、喷洒保护层、控制氧量等方式,防止氧化腐蚀的发生,增加高温过热器的使用寿命。
及时清理渣沉积、灰尘和污垢,定期对生物质锅炉进行检测监控,确保燃烧处于最佳状态,防止燃烧温度不稳定等问题,减少高温过热器的腐蚀风险。
高压蒸汽锅炉炉管腐蚀分析及探讨
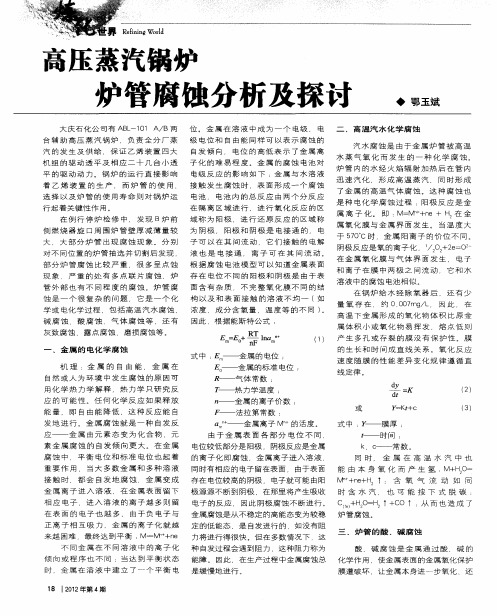
气 体 等 将 发 生 C , 。 — H +C O +HO O 一 +H O 一反 应 ,使 炉 水 中 C , 浓度增 加 ,
流 或 温 度 变 化 引 起 局 部 压 力 下 降 .空 泡 内 只 含 少 量 水 汽 ,存 在 时 间 非 常 短
水蒸 气 氧 化而 发 生 的一 种 化 学腐 蚀 。
炉 管 内 的 水 经 火 焰 辐 射 加 热 后 在 管 内
迅 速 汽 化 ,形 成 高 温 蒸 汽 .同 时形 成
了金 属 的 高 温 气 体 腐 蚀 。这 种 腐 蚀 也
选 择 以 及 炉 管 的 使 用 寿 命 则 对 锅 炉 运 电池 , 电池 内 的 总 反 应 由两 个 分 反 应 在 例 行 停 炉 检 修 中 .发 现 B炉 前 域 称 为 阳极 ,进 行 还 原 反 应 的 区域 称
在 锅 炉 给水 经 除 氧 器 后 , 还 有 少
浓 度 、成 分 含 氧 量 、温 度 等 的 不 同 ) 。
量 氧 存 在 ,约 0.0 mg L 因 此 , 在 07 / ,
高 温 下 金 属 形 成 的氧 化 物 体 积 比 原 金 属 体 积 小 或 氧 化 物 易 挥 发 ,熔 点 低 则
汽 的 发 生 及 供 给 保 证 乙 烯 装 置 四 大 平 的 驱 动 动 力 。 锅 炉 的 运 行 直 接 影 响 着 乙烯 装 置 的 生产 ,而 炉 管 的使 用、
行起 着 关 键 性作 用 。
自 发 倾 向 . 电 位 的 高 低 表 示 了 金 属 离
汽 水 腐 蚀 是 由于 金 属 炉 管 被 高 温
碱 腐 蚀 、 酸 腐 蚀 、 气 体 腐 蚀 等 还 有 因 此 ,根 据 能 斯 特 公 式 :
浅析蒸汽锅炉腐蚀原因与防范措施

浅析蒸汽锅炉腐蚀原因与防范措施蒸汽锅炉是工业生产中常用的一种设备,广泛应用于石化、化工、轻工、纺织等行业。
在蒸汽锅炉运行过程中,腐蚀问题一直是困扰工程师和运行人员的一个难题。
蒸汽锅炉腐蚀不仅会降低设备的寿命,还可能导致事故的发生。
了解蒸汽锅炉腐蚀的原因,采取科学的防范措施对于保障蒸汽锅炉的安全运行至关重要。
一、蒸汽锅炉腐蚀的原因1. 燃烧产物腐蚀(1)硫酸腐蚀硫酸腐蚀又称为湿烟气腐蚀,发生在燃煤、燃油或其他含硫燃料燃烧时,由于硫在燃烧产生的烟气中与水蒸气和氧气反应,生成硫酸气体,当硫酸气体与介质接触时,会引起腐蚀。
硫酸腐蚀主要发生在锅炉的过热器、再热器、空气预热器、烟囱等部位。
(2)氯化物腐蚀氯化物腐蚀是因为燃料在燃烧过程中含有氯元素而引起的腐蚀。
氯化物腐蚀一般发生在烟道和锅筒内壁的金属表面,会降低金属的强度和耐腐蚀性能,导致金属的腐蚀和膨胀破裂。
2. 水质腐蚀(1)缺氧腐蚀缺氧腐蚀是因为锅炉水中缺乏氧气,导致金属表面发生腐蚀。
在蒸汽锅炉中,如果水质不好、水中氧气含量低,就容易发生缺氧腐蚀。
(2)碱性腐蚀在高压蒸汽锅炉中,碱性腐蚀也是一种常见的腐蚀形式。
它是因为水中碱度过高,导致金属表面发生腐蚀。
碱性腐蚀对锅炉管道和容器内壁造成一定的破坏。
3. 金属间腐蚀金属间腐蚀是指不同金属材料直接接触时,由于电化学反应引起的腐蚀。
在蒸汽锅炉中,金属间腐蚀主要发生在管道连接处、焊缝处以及不同金属接触的部位。
以上便是蒸汽锅炉腐蚀的主要原因,针对这些原因,我们需要采取相应的防范措施,以保证蒸汽锅炉的安全运行。
1. 水质控制水质是影响蒸汽锅炉腐蚀的重要因素,因此提高水质是防范腐蚀的关键。
首先要在锅炉水处理中控制水中氧气含量,保证水质中氧气的含量不超过规定值,避免缺氧腐蚀。
其次是控制水质的酸度和碱度,合理调整水质的PH值,防止发生碱性腐蚀。
定期对锅炉水进行化学处理和清洗,保证水质的清洁和稳定,也是防范腐蚀的有效手段。
锅炉管道腐蚀的原因分析和建议

锅炉管道腐蚀的原因分析和建议锅炉管道腐蚀的原因、分析及建议×××(××××××××××发电有限责任公司×××××× 044602)摘要:四管爆漏是火力发电厂中常见、多发性故障,而管道的腐蚀常常中四管泄漏的重要原因。
大部分管道腐蚀的初始阶段,其泄漏量和范围都不大,对于故障的部位不好确定和判断。
一般要经过几天或更长时间泄漏程度才会逐渐增大,发展成为破坏性泄漏或爆管,严重威胁着火力发电厂的安全稳定运行,故本文对锅炉四管腐蚀的原因进行了分析并根据相应的原因提出了一些建议。
关键词:腐蚀、硫化物、氯化物0 前言腐蚀是火力发电厂中常见的故障。
腐蚀的初始阶段,没有明显的现象或其泄漏量和范围都小,对于故障的部位不好确定和判断。
一般要经过几天或更长时间泄漏程度才会逐渐增大,同时局部的泄漏会冲刷周围邻近的管壁,造成连锁性破坏,危及到整个锅炉运行的安全。
1.腐蚀的原因广义的腐蚀指材料与环境间发生的化学或电化学相互作用而导致材料功能受到损伤的现象。
狭义的腐蚀是指金属与环境间的物理-化学相互作用,使金属性能发生变化,导致金属,环境及其构成系功能受到损伤的现象。
1.1管内壁腐蚀:也称水汽侧腐蚀。
1.1.1溶解氧腐蚀。
1.1.2垢下腐蚀。
1.1.3碱腐蚀1.1.4氢损伤。
1.1.5铜氨化合物腐蚀。
1.2烟气侧腐蚀。
1.2.1高温腐蚀。
1.2.2低温腐蚀。
1.3应力腐蚀,也称冲蚀。
指管道受到腐蚀和拉(压)应力的综合效应。
3.设备发生腐蚀的理论原因分析3.1管内壁腐蚀3.1.1溶解氧腐蚀由于Fe与O2、CO2之间存在电位差,形成无数个微小的腐蚀电池,Fe是电池中的阳极,溶解氧起阴极去极化作用,Fe比O2等的电位低而遭到腐蚀。
当pH值小于4或在强碱环境中,腐蚀加重,pH值介于4~13之间,金属表面形成致密的保护膜(氢氧化物),腐蚀速度减慢。
生物质锅炉高温过热器腐蚀原因分析及对策

生物质锅炉高温过热器腐蚀原因分析及对策一、引言随着生物质能源的重要性日益凸显,生物质锅炉作为生物质能源利用的重要设备,其高温过热器腐蚀问题也日益引起人们的重视。
高温过热器是生物质锅炉中起着重要作用的部件,其腐蚀问题直接影响着生物质锅炉的运行安全和经济性。
对生物质锅炉高温过热器腐蚀原因进行深入分析,寻找出有效的对策和解决方法,对于提高生物质锅炉的效率、延长设备的使用寿命具有重要意义。
二、生物质锅炉高温过热器腐蚀原因分析1.水质问题生物质锅炉高温过热器腐蚀问题的一个重要原因是水质问题。
生物质燃烧会产生高浓度的氢氯酸和含有酸性物质的燃料灰渣,这些酸性物质会轻易造成过热器的内外融蚀。
水中的氧化性物质和碱性物质也可能会造成高温过热器的腐蚀。
而且水中的杂质、离子、微生物等也会对高温过热器的腐蚀起到直接或间接作用。
2.燃料灰渣腐蚀生物质锅炉燃烧的燃料灰渣中含有一定量的硫、氯等化学元素,这些元素在高温下会造成过热器管道和受热面的腐蚀。
特别是当燃烧温度低于硫酸露点时,硫酸盐会在过热器管道表面凝结,加剧腐蚀的程度。
3.金属氧化腐蚀生物质锅炉高温过热器内部的金属受到氧化和氧腐蚀的双重作用,这也是高温过热器腐蚀的一个重要原因。
高温下金属材料容易发生氧化反应,导致材料表面的氧化物不断增厚,也会造成氧化物的脱落,从而形成氧腐蚀。
4.烟气中的酸性物质腐蚀生物质锅炉燃烧产生的烟气中含有酸性物质,比如氢氯酸、二氧化硫等,这些酸性物质会直接对高温过热器受热面造成腐蚀。
燃烧过程中,这些酸性物质会在高温过热器受热面凝结,形成酸性络合物,造成受热面的化学腐蚀。
5.操作管理问题生物质锅炉的操作管理也可能影响到高温过热器的腐蚀情况。
过高的燃烧温度、超负荷运行、过分频繁的启停等操作管理不当都会加剧高温过热器的腐蚀情况。
三、生物质锅炉高温过热器腐蚀对策1.改善水质改善水质是最有效的防止高温过热器腐蚀的方法之一。
选择合适的水处理剂、定期对水进行化学分析,确保水质满足要求。
生物质锅炉受热面高温腐蚀分析及预防

生物质锅炉受热面高温腐蚀分析及预防生物质锅炉受热面腐蚀造成承压部件泄漏是制约生物质机组安全稳定长周期运行的主要原因之一,从而直接影响了生物质发电企业的经济效益。
通过长期分析生物质锅炉运行情况,结合生物质入炉燃料品质不稳定,生物质锅炉燃烧不稳定的特点,除一般锅炉均有发生的汽、水、烟侧腐蚀外,发现造成生物质锅炉受热面腐蚀减薄的主要原因就是高温腐蚀。
所以,如何避免受热面壁温超限就是控制生物质锅炉受热面腐蚀减薄的主要方法。
0引言锅炉受热面腐蚀减薄损坏,一般会造成受热面爆管[1]。
故障一旦发生常导致锅炉故障停炉,涉及范围较大,检查、更换不到位则会重复泄漏停炉,而且检修工作量较大。
国内一些生物质锅炉曾因受热面腐蚀造成一年内停炉十几次,对设备安全运行、电厂经济效益造成巨大影响。
1生物质锅炉受热面腐蚀特点及分析生物质锅炉受热面腐蚀多为高温腐蚀[2]。
高温腐蚀的形成主要包括缺氧、高温、还原性气氛的形成,燃料的腐蚀性元素(氯、钾、硅、铁、铬和硫)含量高等因素,锅炉受热面长期在高温下运行,出现还原氧化交替剥离受热面管排壁面现象,导致管壁达到承压极限值发生爆管[3-4]。
生物质燃料的成分复杂,通过对燃料化验分析得出,燃料可燃成分中硫分较低,氯含量较高,还含有钾、氟等。
灰成分中钾、钠含量高,锰含量高,铝成分较低。
通过分析生物质燃料成分,试验及研究,目前公认的高温腐蚀主要分为气相、固相和液相3种形式。
气相腐蚀即氧化性气氛腐蚀、还原性气氛腐蚀、气态碱金属氯化物腐蚀,主要特点为由于生物质中氯元素的含量较高,气相中含有的氯气及含氯化物与受热面金属反应,加速金属合金的氧化所引起的腐蚀,如图1、2、3所示。
固相腐蚀即沉积物碱金属硫酸盐化腐蚀、沉积物中氯化物对金属表面的腐蚀、碱金属氯化物对金属碳化物的腐蚀,主要特点为烟气中的有害元素在受热面表面凝结、沉积,加速金属合金的氧化所引起的腐蚀,如图4、5、6所示。
液相腐蚀即液相氯化物的腐蚀、液相硫酸盐化腐蚀,主要特点为积灰中的有害元素在受热面表面形成局部液相,增加了受热面腐蚀速率,如图7、8所示。
浅析蒸汽锅炉腐蚀原因与防范措施

浅析蒸汽锅炉腐蚀原因与防范措施蒸汽锅炉作为工业生产中常用的热能转化设备,发挥着巨大的作用。
然而,长期使用中其可能存在一些腐蚀问题,这会影响到锅炉的可靠性和运行效率。
因此,加强对蒸汽锅炉腐蚀原因进行分析,制定科学的预防措施,对确保锅炉安全稳定运行具有重要意义。
1.化学腐蚀蒸汽锅炉水系统中经常含有一些酸性物质,这些物质会与金属壁面接触,形成化学反应。
例如,水中的碳酸氢钙等物质与金属反应产生的孔隙可导致壁面腐蚀。
电化学腐蚀是由于金属与液体当中的电极电势差而引起的,主要包括阳极腐蚀和阴极腐蚀。
(1)阳极腐蚀当锅炉中金属和水之间的电位差达到一定值时,金属便会被氧化,对金属部分产生腐蚀。
例如,铁表面会因为结构性腐蚀而造成铁离子被释放到水中,这一过程被称为焊渣腐蚀。
阴极腐蚀与阳极腐蚀相反,是指金属在接触的水中依靠氧的还原而遭受腐蚀。
例如,水中的氧会与铁反应产生氢离子,在膜缝穴处被还原为H2O,造成阴极腐蚀。
3.黏土粒子和有机物腐蚀蒸汽锅炉运行过程中,水中可能存在一些黏土粒子和有机物质,这些杂质会沉积在锅炉壁面上,对壁面产生腐蚀作用。
例如,沉积在金属表面的有机物质会通过催化作用而引发腐蚀。
1.完善水质管理锅炉水的选择要保证水质清洁,试图避免水中存在硫化氢、碳酸钙、铁等杂质。
为了保证水质的缺失,可以采用化学清洗和离子交换等技术,消除水中的有害物质。
2.选择防腐材料为了适应不同的水质和蒸汽组分,应使用合适的防腐材料。
一般防腐材料有镍、铬、钼、钛等高合金材料。
3.进行腐蚀监测通过在锅炉内插入电极,实时监测锅炉内金属与水之间的电势差,检测锅炉壁面的腐蚀程度,及时采取修复措施。
4.进行锅炉化学清洗化学清洗是针对锅炉内壁面长期沉积,难以通过物理力量清洗的铁锈和水垢的处理办法。
5.增加非金属保护层在金属表面涂一层可实现防腐的非金属薄层,如全氟化合物膜、奥克里塞腐蚀膜和氟酸盐等,以提高蒸汽锅炉的防腐性。
三、总结腐蚀是蒸汽锅炉长期运行过程中难以避免的问题,只有采取科学的防腐策略,才能保证蒸汽锅炉的稳定运行。
- 1、下载文档前请自行甄别文档内容的完整性,平台不提供额外的编辑、内容补充、找答案等附加服务。
- 2、"仅部分预览"的文档,不可在线预览部分如存在完整性等问题,可反馈申请退款(可完整预览的文档不适用该条件!)。
- 3、如文档侵犯您的权益,请联系客服反馈,我们会尽快为您处理(人工客服工作时间:9:00-18:30)。
锅炉管道腐蚀的原因分析和建议公司标准化编码 [QQX96QT-XQQB89Q8-NQQJ6Q8-MQM9N]锅炉管道腐蚀的原因、分析及建议×××(××××××××××发电有限责任公司×××××× 044602)摘要:四管爆漏是火力发电厂中常见、多发性故障,而管道的腐蚀常常中四管泄漏的重要原因。
大部分管道腐蚀的初始阶段,其泄漏量和范围都不大,对于故障的部位不好确定和判断。
一般要经过几天或更长时间泄漏程度才会逐渐增大,发展成为破坏性泄漏或爆管,严重威胁着火力发电厂的安全稳定运行,故本文对锅炉四管腐蚀的原因进行了分析并根据相应的原因提出了一些建议。
关键词:腐蚀、硫化物、氯化物0 前言腐蚀是火力发电厂中常见的故障。
腐蚀的初始阶段,没有明显的现象或其泄漏量和范围都小,对于故障的部位不好确定和判断。
一般要经过几天或更长时间泄漏程度才会逐渐增大,同时局部的泄漏会冲刷周围邻近的管壁,造成连锁性破坏,危及到整个锅炉运行的安全。
1.腐蚀的原因广义的腐蚀指与间发生的或相互作用而导致材料功能受到的现象。
狭义的腐蚀是指与环境间的-化学相互作用,使金属性能发生变化,导致金属,环境及其构成系功能受到损伤的现象。
1.1管内壁腐蚀:也称水汽侧腐蚀。
1.1.1溶解氧腐蚀。
1.1.2垢下腐蚀。
1.1.3碱腐蚀1.1.4氢损伤。
1.1.5铜氨化合物腐蚀。
1.2烟气侧腐蚀。
1.2.1高温腐蚀。
1.2.2低温腐蚀。
1.3应力腐蚀,也称冲蚀。
指管道受到腐蚀和拉(压)应力的综合效应。
3.设备发生腐蚀的理论原因分析3.1.1溶解氧腐蚀由于Fe与O2、CO2之间存在电位差,形成无数个微小的腐蚀电池,Fe是电池中的阳极,溶解氧起阴极去极化作用,Fe比O2等的电位低而遭到腐蚀。
当pH值小于4或在强碱环境中,腐蚀加重,pH值介于4~13之间,金属表面形成致密的保护膜(氢氧化物),腐蚀速度减慢。
腐蚀速度与溶解氧的浓度成正比,随着给水速度提高、锅炉热负荷增加、溶解氧腐蚀也随之加剧。
3.1.2垢下腐蚀由于给水质量不良或结构缺陷防碍汽水流通,造成管道内壁结垢。
垢下腐蚀介质浓度高,又处于停滞状态,会使管内壁发生严重的腐蚀,这种腐蚀与炉水的局部浓缩有关。
如果补给水或因凝汽器泄漏(河水)使炉水含碳酸盐,其沉积物下局部浓缩的炉水(沉积着高浓度的OH-)pH值上升到13以上时发生碱对金属的腐蚀。
如果凝汽器泄漏的是海水或含Cl-的天然水,水中的MgCl2、CaCl2将进入锅炉、产生强酸HCl,这样沉积物下浓缩的炉水(很高浓度的H+)pH值快速下降,而发生对金属的酸性腐蚀。
3.1.3碱腐蚀游离碱会在多孔性沉积物和管内表面浓缩,浓缩的强碱会溶解金属保护膜而形成铁酸根与次铁酸根离子的混合物,当管壁表面局部碱浓度超过40%时,会释放出氢气,从而形成金属表面深而广的腐蚀,也称延性腐蚀。
3.1.4氢损伤(氢损伤实际就是酸性腐蚀)一般情况下给水与管壁(Fe)发生反应生成H2和Fe3O4。
保护膜Fe3O4阻隔H2进入管壁金属而被炉水带走,当给水品质不佳或管内结垢会生成Fe2O3和FeO。
Fe2O3、FeO比较疏松、附着性很差,有利于H2向管壁金属的扩散,高温下晶界强度低,H2与钢中的碳和FeC反应生成CH4。
管壁金属脱碳,CH4积聚在晶界上的浓度不断升高,形成局部高压以致应力集中,晶界断裂,产生微裂纹并发展成网络,导致金属强度严重降低,使金属变脆而断裂。
3.1.5铜氨化合物腐蚀在炉水处理中使用脱氧剂和中和胺等均可能产生游离氨。
在pH值大于且含溶解氧的情况下,氨会侵蚀以铜合金为材质的冷凝管。
一旦铜离子进入锅炉而沉积在管壁上,便会产生电化学腐蚀而损伤炉管。
燃烧过程中,燃料中的硫氧化成SO2,部分氧化成SO3,SO3与高温水蒸汽结合生成H2SO4,使受热面产生腐蚀。
该腐蚀可以分高温腐蚀,低温腐蚀两类。
3.2.1高温腐蚀高温腐蚀是受热面在烧结性灰垢下产生的金属腐蚀。
燃料中的碱性氧化物(Na2O、K2O)在高温下气化,流过受热面时会凝结其管壁上。
当管壁周围为还原性气氛时,游离态的S与金属表面发生急剧反应,生成FeS和氧化成Fe2O3。
SO3与碱性氧化物及金属保护膜Fe2O3作用产生复合硫酸盐。
或熔点较低的复合硫酸盐,在高温熔融或半溶融状态下,对金属产生强烈的腐蚀,特别在650~700℃时,腐蚀更剧烈。
烟气中通常含有腐蚀性气体(Cl、H2S、NaOH、SO2、SO3),这些气体与金属管壁发生作用,破坏氧化膜,造成金属腐蚀。
如果还原性气氛与氧化性气氛交替出现时,会使氧化层(保护膜)变成疏松的海绵状,更能促使腐蚀的发生。
在锅炉水冷壁会发生高温硫腐蚀,锅炉水冷壁管向火侧的高温腐蚀,也称为“还原气氛腐蚀”,是在锅炉燃用煤种含硫量偏高、炉内局部缺氧而存在一氧化碳的还原气氛、并有未完全燃烧的煤粉冲刷水冷壁表面的条件下形成的。
高温硫腐蚀主要有2 种类型:硫酸盐型,氯化物型。
3.2.1.1硫酸盐型高温腐蚀煤粉在炉内燃烧时,矿物质中的钠挥发、升华,非挥发性硅酸盐中的钾通过置换反应释放出来,钠和钾与烟气中的SO3反应生成硫酸钠和硫酸钾,其露点温度在877℃左右。
当汽态的硫酸钠与硫酸钾扩散到“较冷的水冷壁管表面”时,便凝结在管壁氧化膜上。
由于汽相扩散速率较硅酸盐灰粒惯性撞击沉积的速率快,所以炉管表面上首先沉积的是硫酸钠(Na2SO4)和硫酸钾(K2SO4),其沉积速度与挥发钠的数量及烟气温度有关,特别是与烟气及壁面的温度梯度有关。
经对腐蚀的钢管分析发现,当管壁附近呈还原性气氛并存在含量很高的H2S气体时,则会产生严重的硫化物型锅炉水冷壁腐蚀,而且腐蚀速度与烟气中H2S的浓度几乎成正比。
由黄铁矿硫造成的腐蚀,黄铁矿粉末随高温烟气流动到管壁上,在还原性气氛下受热分解释放出硫化亚铁和自由原子硫:FeS2 → FeS + [S]当管壁附近有一定浓度的H2S和SO2 时,也可能生成自由原子硫:2H2S + SO2 → 2H2O + 3[S]在还原性气氛中,自由原子硫由于缺氧可单独存在,当管壁温度达到350 ℃时会发生硫化反应:Fe + [S] → FeSH2S还可以透过疏松的Fe2O3,与较致密的磁性氧化铁( Fe3O4 即Fe2O3—FeO)中复合的FeO 反应生成FeS:FeO + H2S → FeS + H2OFeS缓慢氧化生成黑色磁性氧化铁,使管壁受到腐蚀:3FeS + 5O2 → Fe3O4 + 3SO2硫化物型腐蚀所生成的FeS,熔点为1195℃,在温度较低的腐蚀前沿可稳定存在。
但当外层温度较高时,FeS则与介质中的氧反应,转化为Fe3O4,从而使腐蚀进一步扩展。
硫化氢气体腐蚀, H2S除了能促进硫化物型腐蚀外,还会对管壁直接产生腐蚀作用,是水冷壁管腐蚀的另一主要因素,其腐蚀反应为:2H2S + Fe → FeS + H22H2S + FeO → FeS + H2O生成的硫化亚铁又进一步氧化形成氧化亚铁。
FeS与FeO的混合物是多孔性的,不起保护作用,可使腐蚀继续进行。
另外,贴管壁气氛中的CO也是发生高温腐蚀的必要条件。
3.2.1.2氯化物型高温腐蚀煤中存在一定量的NaCl,其熔点(801℃)和蒸发点远低于火焰温度,进入炉膛以后即迅速汽化,以气态的形式存在,在炉膛内可能发生如下一些反应:NaCl + H2O → NaOH + HCl2NaCl + SO2 + 1/2O2 + H2O → Na2SO4 + 2HCl2NaCl + SiO2 + H2O → Na2SiO3 + 2HCl生成的HCl气体使管壁的氧化膜受到严重的破坏,形成汽化点很低的FeCl2,FeCl2 马上完全挥发,从而使管壁金属直接受到HCl的腐蚀,同时由于氧化膜受到破坏,使H2S 也能达金属表面,加速管壁金属的腐蚀速度。
HCl气体对管壁可能发生的腐蚀反应如下:Fe + 2HCl → FeCl2 + H2FeO + 2HCl → FeCl2 + H2OFe2O3 + 2HCl + CO → FeO + FeCl2 + H2O + CO2Fe3O4 + 2HCl + CO → FeO + FeCl2 + H2O + CO2上述反应在400~600℃范围内最为活跃。
当煤质中氯的含量较高时(大于%)才可能发生比较严重的氯化物型高温腐蚀, 一般情况下这种腐蚀发生的可能性不是很大。
4.设备发生腐蚀的实际原因分析4.1煤中含硫量高煤中的硫是造成水冷壁高温腐蚀的重要原因。
煤中的硫可分为无机硫和有机硫。
在无机硫中, 绝大多数为黄铁矿硫,硫酸盐硫只占较少比例。
而黄铁矿对结渣和腐蚀影响极大,故有必要测定电厂燃煤的全硫及各种形态硫。
4.2管壁温度与热负荷较高较高的管壁温度为高温腐蚀提供了条件,因在H2S浓度不变时,若管壁温度低于300℃,则水冷壁不腐蚀或腐蚀很慢;若壁温在300~500℃范围内,则腐蚀速度与壁温呈指数关系,即壁温每升高50℃,腐蚀速度增加一倍。
因此,高参数锅炉容易出现水冷壁的高温腐蚀。
4.3煤粉细度太粗的煤粉不易燃尽,火焰拖长,从而使水冷壁表面附近集中了大量煤粉颗粒,冲刷并磨损水冷壁,破坏了水冷壁管的氧化保护膜,使管子的腐蚀减薄恶化;另外,煤粉在缺氧的条件下燃烧,形成还原性气氛,也会产生腐蚀。
4.4炉内燃烧的风粉分离炉内燃烧的风粉分离是四角切圆燃烧锅炉普遍存在的问题,这是导致水冷壁高温腐蚀的空气动力因素。
实际运行操作中,为了保证稳定燃烧,往往采用较低的一次风率和风速(贫煤、无烟煤:20~25m/s),而二次风速一般为40~45m/s,致使一、二次风的射流刚性相差较大。
一、二次风射流喷出燃烧器后,由于炉内旋转气流的横向推力的作用及射流两侧补气能力的不同,即偏离了喷口的几何轴线、向背火侧偏转,同时因射流刚性差异而导致一、二次风分离。
部分煤粉在射流下游水冷壁附近缺氧燃烧,形成局部还原性气氛,从而导致高温腐蚀。
4.5炉内切圆直径偏大实践表明,由于四角切圆燃烧的锅炉炉内气流旋转的切圆太大,有的锅炉的最大风速处距水冷壁只有1~2m,且由于热态时气流膨胀,实际燃烧的直径还会进一步增大,严重时会引起炉内火焰的冲墙贴壁,这就使水冷壁附近形成强烈燃烧区,而炉膛中心却相对成为弱燃烧区,一方面造成水冷壁温升高且附近缺氧而生成大量的还原性气体,另一方面贴壁风速高加强了煤粉颗粒对水冷壁管表面的冲刷磨损而使新的壁面暴露出来,从而加剧了高温腐蚀过程。
4.6配风状况差如果在运行中操作不当,加上风、粉配比不合理,则会导致炉内配风状况很差,炉内氧量及温度的波动过于剧烈,氧化气氛与还原气氛交替在水冷壁附近出现,一、二次风混合不完全,煤粉着火和燃尽程度差,且形成海绵状的氧化层更有利于腐蚀介质发生反应。