分解炉的温度控制
分解炉温度的控制目的在于控制分解率

分解炉温度的控制目的在于控制分解率分解炉温度的控制目的在于控制分解率。
C1出口温度主要受入窑生料量的影响,其次是预热器排风量及尾煤燃烧情况。
对于前者,控制入窑生料量的稳定是控制热工制度稳定的关键。
我们常说“五稳保一稳”,“五稳”指“入窑生料量、生料成分稳,给煤量、燃煤成分稳,设备运转稳定”,“一稳”指“热工制度稳定”。
在“五稳”中烧成操作可控制的只有入窑生料量和给煤量两个,而给煤量是由入窑生料量的大小来决定。
所以说控制入窑生料量的稳定是控制热工制度稳定的关键。
对于后者,预热器出口CO%与预热器排风量及尾煤燃烧情况的好坏密切相关。
二、压力与气氛制度:压力与气氛是相互联系密不可分的。
例如我们要求窑尾O2%0.7-1.0%,CO%无或者很少,亦即保持窑内的还原或氧化气氛。
在窑头给煤量一定的情况下,要达到上述要求就必须通过调节喷煤管的风量匹配及窑炉风量匹配来达到。
对于分解炉出口要求O2%3.0-4.0%,预热器出口一般要求3.0%左右.根据我在操作和生产调试的经验认为,预热器出口O2%偏下限控制在2.5-3.0%时在烧成上比较易于控制,电耗煤耗方面也比较经济。
前提条件是分解炉炉容合适,尾煤能在分解炉内完全燃烧或只有少量在五级旋风筒内燃烬。
预热器出口O2%2.5-3.0%与3.0-3.5%的区别在于,相同投料量的情况下拉风量不一样,亦即C1出口负压比3.0-3.5%时要小一些。
产生的后果是分解炉内风速降低物料滞留时间延长,炉内煤粉燃烬度提高,旋风筒收尘效率增加。
明显的区别是O2%2.5-3.0%时C1出口温度要比3.0-3.5%时要低5-10度。
三、热平衡制度:“热平衡”比较容易理解,“热量收入=热量支出”,热量收入包括煤粉燃烧产生热、物料化学反应热、熟料回收热等,热量支出包括生料分解吸热、加热空气和物料耗热、胴体散热、熟料和空气带走的热量等。
热平衡牵涉到物料与气流的平衡。
稳定的热工制度反映在热平衡上,收入与支出的各子项也相对稳定。
分解炉的工作原理

(二)、分解炉的工作原理与结构概述--------------------------------------------------------------------------------(作者:佚名本信息发布于2009年08月19日,共有399人浏览) [字体:大中小] 分解炉是把生料粉分散悬浮在气流中,使燃料燃烧和碳酸钙分解过程在很短时间(一般1.5~3秒)内发生的装置,是一种高效率的直接燃烧式固相一气相热交换装置。
在分解炉内,由于燃料的燃烧是在激烈的紊流状态下与物料的吸热反应同时进行,燃料的细小颗粒呈一面浮游,一面燃烧,使整个炉内几乎都变成了燃烧区。
所以不能形成可见辉焰,而是处于820~900℃低温无焰燃烧的状态。
水泥烧成过程大致可分为两个阶段:石灰质原料约在900℃时进行分解反应(吸热);在1200~1450℃时进行水泥化台物生成反应(放热、部分熔融)。
根据理论计算,当物料由750℃升高到850℃,分解率由原来的25%提高到85~90%时。
每千克熟料尚须1670千焦的热量。
因此,全燃料的60%左右用于分解炉的燃烧,40%用在窑内燃烧。
近几年来窑外分解技术发展很快,虽然分解炉的结构型式和工作原理不尽相同,它们各有自己的特点,但是从入窑碳酸钙分解率来看,都不相上下,一般都达到85%以上。
由此看来,分解炉的结构型式对于入窑生料碳酸钙分解率的影响是不太大的。
关键在于燃料在生料浓度很高的分解炉内能稳定、完全燃烧,炉内温度分布均匀,并使碳酸钙分解在很短时间内完成。
我国某厂烧煤分解炉的结构示意于图3—18。
分解炉由预燃室和炉体两部分组成,预燃室主要起预燃和散料作用,炉体主要起燃料燃烧和碳酸钙分解作用。
在钢板壳体内壁镶砌耐火砖。
由冷却机来的二次空气分成两路进入预燃室。
三级旋风筒下来的预热料,由二次空气从预燃室柱体的中上部带入预燃室。
约四分之一的分解炉用煤粉,从预燃室顶部由少量二次空气带入并着火燃烧,约四分之三左右的煤粉在分解炉锥体的上部位置喂入,以此来提高和调整分解炉的温度,使整个炉内温度分布趋于均匀,担任分解碳酸钙的主力作用。
分解炉的温度控制

B56T1(℃) 793 780 767 767 759
CO含量(%) 0.07 0.06 0.06 0.07 0.09
从表中可见,该预分解窑在一定的范围内,分解炉的燃烧用量比例存在着一个最佳值。在该条件下,最佳值为约61.5%,此时其热耗最低。大于或少于此值,热耗均增加。也就是说,在一定产量范围内的某窑,分解炉喂煤量既不是越高越好,也不是越低越好。分解炉喂煤的比例与热耗的关系不是线性的,而是非线性的。有的统计得出两者的关系是线性的结论,认为窑头喂煤越多越好或分解炉喂煤越多越好,实际上是最佳值的某一侧,从而产生分解炉用燃料比例与热耗关系是线性关系的错觉而已。
从燃料燃烧的角度来看,分解炉内燃料的燃烧与回转窑内燃料燃烧有许多不同之处。回转窑内燃料燃烧温度比分解炉内高得多,回转窑内燃料燃烧明显是受扩散控制的,而分解炉内燃料燃烧则有所不同。由于分解炉温度远低于回转窑内燃料燃烧温度,故煤在分解炉内的燃烧时间受煤种类的影响比回转窑内的影响大得多。如广东云浮水泥厂FCB分解炉容积偏小,结构上亦存在一些问题,当使用低挥发分、高灰分的低热值煤时,还原气氛十分严重,迅速导致结皮堵塞;而采用高挥发分、低灰分的高热值煤时情况则有所改善。煤粉细度对于回转窑内的燃烧是相当敏感的,因为其是受扩散控制,即受边界层扩散时输送速率的控制;而煤粉细度对分解炉内燃烧的影响就没有在回转窑内那样敏感了。
还需说明的是,分解炉的通风量对分解炉出口温度及末级旋风筒下部温度亦有影响。即使分解炉的喂煤量、物料量不变,但通风量改变,亦会产生影响。当通风量过大,分解炉内气流速度过快,燃料及物料在分解炉内停留时间不足;反之,当通风量过小,供气不足,燃料燃烧同样受影响。总之,通风量的波动,窑风量与分解炉风量的分配不当,都会影响分解炉燃料的燃烧,从而导致分解炉出口温度与最末一级旋风筒下部温度的异常。
裂解炉横跨温度的控制
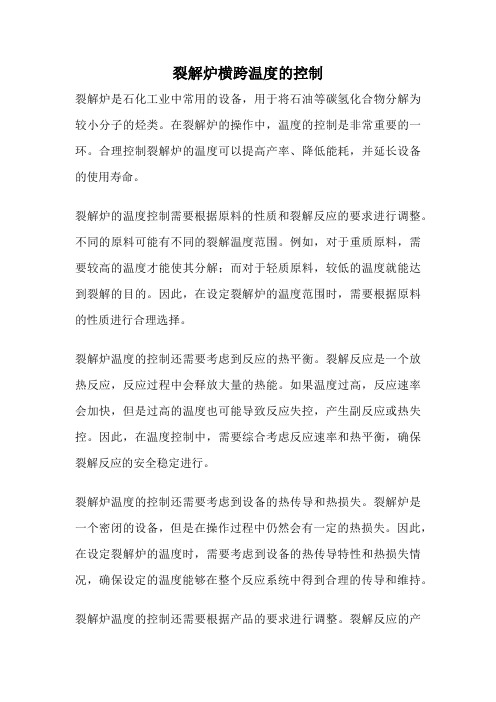
裂解炉横跨温度的控制裂解炉是石化工业中常用的设备,用于将石油等碳氢化合物分解为较小分子的烃类。
在裂解炉的操作中,温度的控制是非常重要的一环。
合理控制裂解炉的温度可以提高产率、降低能耗,并延长设备的使用寿命。
裂解炉的温度控制需要根据原料的性质和裂解反应的要求进行调整。
不同的原料可能有不同的裂解温度范围。
例如,对于重质原料,需要较高的温度才能使其分解;而对于轻质原料,较低的温度就能达到裂解的目的。
因此,在设定裂解炉的温度范围时,需要根据原料的性质进行合理选择。
裂解炉温度的控制还需要考虑到反应的热平衡。
裂解反应是一个放热反应,反应过程中会释放大量的热能。
如果温度过高,反应速率会加快,但是过高的温度也可能导致反应失控,产生副反应或热失控。
因此,在温度控制中,需要综合考虑反应速率和热平衡,确保裂解反应的安全稳定进行。
裂解炉温度的控制还需要考虑到设备的热传导和热损失。
裂解炉是一个密闭的设备,但是在操作过程中仍然会有一定的热损失。
因此,在设定裂解炉的温度时,需要考虑到设备的热传导特性和热损失情况,确保设定的温度能够在整个反应系统中得到合理的传导和维持。
裂解炉温度的控制还需要根据产品的要求进行调整。
裂解反应的产物主要是烃类化合物,不同的产品对温度的要求也不同。
一般来说,裂解温度越高,轻质产品的产率越高;而裂解温度越低,重质产品的产率越高。
因此,在温度控制中,需要根据产品的要求进行调整,以获得满足市场需求的产品。
裂解炉温度的控制是石化工业中非常重要的一环。
合理控制裂解炉的温度可以提高产率、降低能耗,并确保反应的安全稳定进行。
通过根据原料性质、反应要求、热平衡、热传导和产品要求等因素进行综合考虑,可以实现对裂解炉温度的有效控制,从而获得高效、安全的裂解反应。
在DCS系统中实现分解炉温度与喷煤量自动控制

个 相 对稳定 的温度且 不 可太高 或太低 。因温度 太
的, 具 体温度 控 制系统 结构 框 图见 图 1 。
高 会造 成 预热 器堵 塞 ;太低 则导 致碳 酸 盐分 解不 充
分, 加大了窑系统的分解任务。因此分解炉 的温度 控 制 对整 个 回转 窑 运 转热 工 状 况 的稳 定至 关 重要 , 降低分解炉温度波动并与喂煤量达到协调控制是生
泵 用模 糊 P I D控 制 系 统 试 运行 以来 效 果 良好 。
当分解炉温度在上位机界面的设定值 为 8 4 5℃时 , 温度稳定控制在 8 4 5 c I = 左右 , 波动非常小 ( ± 5 ℃) , 线 性关 系良好 。表 1 为 回转窑运行的部分数据。
表1 2 0 1 0 年9 至1 1 月窑运行数据数据
率来 达 到调 节分解 炉 出 口温 度 的 目的。 D C S 程序中 P I D功 能 可 以实 现对 控制 对 象 的精
分解炉的温度是一个纯滞后 、 大惯性 、 非线性的 复杂控制对象, 影响 因素很多, 各因素之间耦合性 强, 因而难 以用 常规控制方法进行控制, 实际生产 中主要靠操作者凭经验来操控 。当温度过低时, 需
1 问题及 其原 因分 析
系统 的对 象惯 性小 , 工 作频率 高 , 可 以提 高系统 误差
葛 洲坝 宜城 水 泥有 限公 司 5 0 0 0 t / d 新 型 干法 水 泥 生 产线 于 2 0 0 9年 1 0月投 产 。 在试 生 产 过程 中出 现 了 因分解 炉温 度波
分分解 , 提高了熟料 的产质量 、 降低操作员劳动强 度、 大幅降低了尾煤煤耗 。
3 结 语
通 过 对 分解 炉生 产 工 艺 的分 析 , 设 计 了一 种 适
氨分解炉参数

氨分解炉参数1. 简介氨分解炉是用来分解液氨的装置,其主要作用是将液氨气化并分解。
氨分解炉是化工、制氢等行业中常见的设备之一,其参数对于氨分解炉的性能和安全保障至关重要。
2. 氨分解炉的参数(1)炉体压力炉体压力是氨分解炉的重要参数之一。
其设置的原则是在保证工艺条件的前提下,按照炉管的承压能力来确定。
通常情况下,炉体压力设置为0.3~0.5MPa。
(2)炉体温度炉体温度是氨分解炉另一个关键参数。
氨气的分解需要一定的温度和热量,炉体温度设置在600℃ ~800℃之间比较合适,一般设定为700℃左右。
(3)氨气流量通常情况下,氨气的分解速度是很慢的,为了提高分解速度,需要增大氨气的流量,一般设置在200~400m³/h之间。
(4)催化剂数量选择适量催化剂对于氨分解炉的运行有极大帮助。
过多的催化剂会使催化剂的活性质减弱,使得反应效率下降;过少的催化剂则可能需要增加反应时间,影响生产效率。
一般情况下,催化剂的添加量为6%~10%左右。
(5)氨分解炉设计氨分解炉的设计也是十分重要的。
炉体内应设置适当的隔板和搅拌装置,以均匀分布氨气和催化剂。
并且在炉管连接处需要设置密封装置,以保证气体的流动性能。
3. 注意事项氨分解炉工艺条件的设置应根据具体情况进行调整。
不同的原料质量、生产工艺、生产规模等都会对工艺参数有所影响。
在确定工艺参数时,需要进行适当的试验和检测,以保证氨分解炉的高效稳定运行。
此外,氨分解炉的安全性也需要引起重视。
在分解过程中,需要保证气体不外漏,并通过相应的防爆装置以保证运行的安全性。
4. 总结氨分解炉的参数对氨气分解效率和安全有着重要的影响。
在生产和实验中,应根据实际工艺条件合理设置各项参数,并保证设备的安全性。
同时,需要依靠实验和检测结合工艺条件的优化来提高氨分解炉的效率和稳定性。
材料工程技术专业《分解炉的热工性能》

分解炉的热工性能分解炉生产工艺对热工条件的要求如下。
①炉内气流温度不宜超过950°C,以防系统产生结皮、堵塞。
②燃烧速度要快,以保证供应碳酸盐分解所需要的大量的热量。
③保持窑炉系统较高的热效率和生产效率。
〔一〕分解炉内燃料的燃烧1、无焰燃烧与辉焰燃烧当煤粉进入分解炉后,悬游于气流中,经预热、分解、燃烧发出光和热,形成一个个小火星,无数的煤粉颗粒便形成无数的迅速燃烧的小火焰。
这些小火焰浮游布满炉内,从整体看,看不见一定轮廓的有形火焰。
所以分解炉中煤粉的燃烧并非一般意义的无焰燃烧,而是充满全炉的无数小火焰组成的燃烧反响。
有人把分解炉内的燃烧称为辉焰燃烧,这主要指分解炉内将料粉或煤粉均匀分散于高温气流中,使粉料颗粒受热达一定温度后,固体颗粒发出光、热辐射而呈辉焰。
但并不能看到有形的火焰而只见满炉发光。
分解炉内无焰燃烧的优点是燃料均匀分散,能充分利用燃烧空间,不易形成局部高温。
燃烧速度较快,发热能力较强。
燃烧大致有两种动力学机制。
〔1〕以化学反响控制的机制,其燃烧特点如下。
①燃烧与温度的关系,提高温度可大大提高反响速度。
燃烧速率与温度成指数关系。
②炭粒燃尽时间T与其初始直径成正比。
〔2〕以氧气向煤粒外表扩散控制的机制,特点如下。
①燃烧受温度的影响较小。
②炭粒燃尽时间与其初始直径的平方成正比。
③燃烧与气流流速和湍流度密切相关。
通常煤燃烧在低温下受化学反响控制,在高温下受扩散控制,大约在1000°C左右时发生转变。
2、煤粉的着火着火就是煤的燃烧速率大于系统散热速率时的状态,而煤的着火点也就是导致燃烧速率大于散热速率时的分界点的温度值。
因而煤的着火点并不是一个固有的物理性质常数,它与具体系统的散热条件有关,不同的散热特性方程将有不同的着火点。
在无CaCO3的条件下,一般燃烧炉中气流温度非恒温,而是随燃烧而变化。
在这种条件下,煤的着火点可下降。
这是因为分解炉炉体向周围环境的散热较燃烧的放热可忽略不计,而CaCO3分解吸热很大,往往超过煤的放热速率。
氨分解岗位操作规程
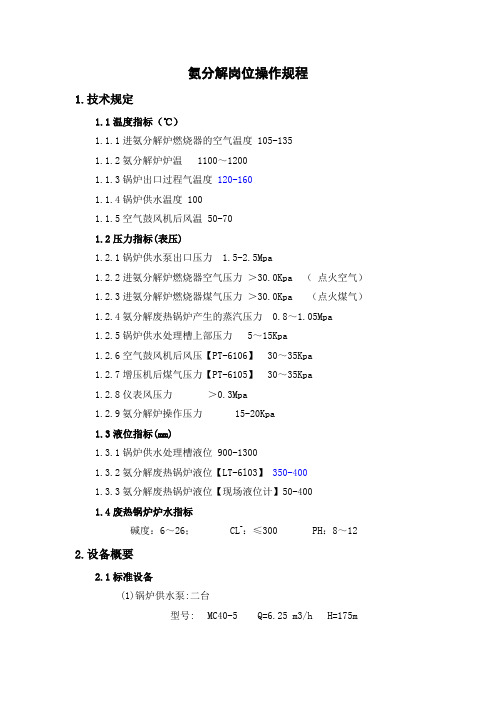
氨分解岗位操作规程1.技术规定1.1温度指标(℃)1.1.1进氨分解炉燃烧器的空气温度 105-1351.1.2氨分解炉炉温1100~12001.1.3锅炉出口过程气温度120-1601.1.4锅炉供水温度 1001.1.5空气鼓风机后风温 50-701.2压力指标(表压)1.2.1锅炉供水泵出口压力 1.5-2.5Mpa1.2.2进氨分解炉燃烧器空气压力>30.0Kpa (点火空气)1.2.3进氨分解炉燃烧器煤气压力>30.0Kpa (点火煤气)1.2.4氨分解废热锅炉产生的蒸汽压力 0.8~1.05Mpa1.2.5锅炉供水处理槽上部压力 5~15Kpa1.2.6空气鼓风机后风压【PT-6106】 30~35Kpa1.2.7增压机后煤气压力【PT-6105】 30~35Kpa1.2.8仪表风压力>0.3Mpa1.2.9氨分解炉操作压力 15-20Kpa1.3液位指标(mm)1.3.1锅炉供水处理槽液位 900-13001.3.2氨分解废热锅炉液位【LT-6l03】350-4001.3.3氨分解废热锅炉液位【现场液位计】50-4001.4废热锅炉炉水指标碱度:6~26; CL-:≤300 PH:8~12 2.设备概要2.1标准设备(1)锅炉供水泵:二台型号:MC40-5 Q=6.25 m3/h H=175m附电机:Y180M-2W N=22kW(2)煤气增压机:型号: ML32WD Q=7.49m3/min P=39kPa附电机:YB160m-4 N=11KW(3)空气鼓风机:二台型号:D30-61-1.5 Q=30m3/min P=49kPa附电机: YB225M-2 N=45kW2.2非标准设备(1)氨分解炉: 一台总重64.053t DN1800/2600 H=8070(2)废热锅炉: 一台单重:8.000t F=115m2(3)锅炉供水处理槽:一台单重:4.215t V=23.4m3(4)空气预热器:一台单重:1.425t F=38.1m2(5)燃烧器:一台单重:1.705t3.工艺说明从蒸氨塔C-2302来的氨汽,在蒸汽夹套管内预热,然后进入氨分解炉H-6101,在1100℃-1200℃高温和镍催化剂的作用下,氨和氰化氢等氮化物被催化分解,生成氮、氢和一氧化碳。
- 1、下载文档前请自行甄别文档内容的完整性,平台不提供额外的编辑、内容补充、找答案等附加服务。
- 2、"仅部分预览"的文档,不可在线预览部分如存在完整性等问题,可反馈申请退款(可完整预览的文档不适用该条件!)。
- 3、如文档侵犯您的权益,请联系客服反馈,我们会尽快为您处理(人工客服工作时间:9:00-18:30)。
分解炉的温度控制
关键字: 分解炉--预分解窑--旋风筒
摘要: 1.分解炉温度与燃料燃烧2.分解炉温度与燃料燃烧比例及三次风温3.分解炉温度与末级旋风筒温度及物料、燃料情况
分解炉有多种形式,其结构性能虽有差异,但是要起的作用是相同的:要使燃料燃烧的放热过程与生料碳酸盐分解的吸热过程在其中以悬浮态或流化态下极其迅速地进行,使入窑生料碳酸盐分解率提高,从而减轻窑的热负荷,提高窑的运转周期,提高产质量.而分解炉的温度控制对整个预分解窑系统的热力分布,热工制度的稳定至关重要.为此,对分解炉温度控制的有关几个问题进行讨论.
1.分解炉温度与燃料燃烧:
分解炉的温度取决于燃料燃烧过程的放热速率与生料分解过程的吸热速率.当燃料燃烧放热速率慢,生料分解在接近平衡的条件下进行,分解炉的温度于860--920度范围,燃料燃烧放出的热量就会迅速传递给生料,并被分解反应吸收.但是,当燃料燃烧速率大于生料分解过程的吸热速率,燃料燃烧的热量大于生料分解所需的吸热量,此时分解炉的温度就会超过平衡温度范围.
从燃料燃烧的角度来看,分解炉内燃料的燃烧与回转窑内的燃料燃烧有许多不同之处.回转窑内燃料燃烧温度比分解炉内高的多,回转窑内燃料燃烧明显是受扩散控制的,而分解炉内燃料燃烧则有所不同.由于分解炉温度远低于回转窑内燃料燃烧温度,故煤在分解炉内的燃烧时间受煤种类的影响比回转窑内的影响大的多.如广东云浮水泥厂FCB分解炉容积偏小,结构上亦存在一些问题.当使用低挥发分、高灰分的低热值煤时,还原气氛十分严重,迅速导致结皮堵塞;而采用高挥发分,低灰分的高热值煤时情况则有所改善。
煤粉
细度对于回转窑的燃烧是相当敏感的,因为其是受扩散控制的,即受边界层扩散时输送速率的控制;而煤粉细度对分解炉内燃烧的影响就没有在回转窑内那麽敏感了。
问题还要回到分解炉温度与燃料燃烧的关系上来。
由于回转窑内燃料燃烧是受扩散控制的,增减10--20度对于燃料的燃烧影响是甚微的。
但在分解炉内则明显不同。
如有的分解炉容积偏小,煤粉燃尽时间不足,以至还原气氛重,而降低分解炉的温度,减少分解炉的用煤量,以图改变煤粉燃烧不完全、还原气氛的问题,但往往是事与愿违。
因在不减产量的情况下,分解炉用煤减少,分解炉温度会降低,煤的燃烧速度随温度降低而迅速下降,煤粉始终燃烧不完全。
适当增大分解炉的容积已成为一个发展动向。
在分解炉偏小媒质差的情况下,可适当降产量,而不宜降低分解炉的温度。
2.分解炉温度与燃料用量比例及三次风温:
分解炉与窑头燃料用量的比例对整个预分解窑系统的热力分布有着重要影响,而分解炉的燃料用量又与分解炉温度控制有关.以珠江水泥厂SLC窑为例,对此问题进行讨论.
下表是珠江水泥厂SLC窑在双列运转,熟料产量为3840--4160t/d,在一段期间内,分解炉喂煤量所占的比例、分解炉出口温度B55T1、炉列出口废气温度B50T1、窑列出口废气温度A50T1、三次风温B56T1、废气CO含量及煤耗的统计参数。
分解炉燃料用量比例与其他热工参数的关系:
分解炉燃料用量比例[%]60.3 61.5 63.1 64.8 66.0
热耗{kj/kg熟料} 3265 3190 3325 3410 3590
A50T1{度} 346 338 340 338 333
B50T1{度} 317 298 328 329 350
B55T1{度} 880 880 873 863 843
B56T1{度} 793 780 767 767 759
CO含量{%} 0.07 0.06 0.06 0.07 0.09
从表中可见,该预分解窑在一定的范围内,分解炉的燃料用量比例存在着一个最佳值。
在该条件下,最佳值为61.5%,此时其热耗最低.大于或少于此值,热耗都增加.也就是说,在一定产量范围内的某窑,分解炉喂煤量既不是越高越好也不是越低越好.分解炉喂煤的比例与热耗的关系不是线性的,而是非线性的.有的统计得出两者的关系是线性的结论,认为窑头喂煤越多越好或分解炉喂煤越多越好,实际上是最佳值的某一侧,从而产生分解炉用燃料比例与热耗关系是线性关系的错觉而已.
为何对于某特定的预分解其燃料用量比例存在一个最佳范围,高于或低于此最佳范围热耗会增加?尽管对于不同的预分解窑相应的最佳是不同的,但都应有类似的关联.
当分解炉喂煤量比例增大,既窑头喂煤量减少.从表中可知,尽管窑列废气温度A50T1有所降低,但炉列废气温度B50T1都明显增高,炉列的废气量比窑列的废气量大,即总的废气带走的热损失是增加的.另外,分解炉加过多的煤,使废气中CO含量增加.反之,当分解炉喂煤量比例过低,同样也会使热耗增加.窑头烧过多的煤,窑列废气温度
A50T1明显上升,废气中CO含量亦会增加,导致热耗增加.而且这样做还会影响回转窑耐火材料的寿命,影响运转的时间.
虽然许多预分解窑并非是双系列的,但其本质是相同的.在一定的产量范围内,分解炉与窑头燃料用量比例都存在一个最佳的范围,在此范围内就可为预分解窑的合理热力分布提供好的基础.分解炉燃料用量比例过高或过低都是不利的.
分解炉的燃料用量比例与分解炉温度控制又有何关联呢?具体对于珠江水泥厂SLC窑分解炉来说,是分解炉出口温度B55T1与其喂煤量比例的关联.在该处设置了一个PID调节器,根据设定的温度由PID调节器自动增减燃料用量.自动模拟PID调节器有三种作用: P作用{proportional}:比例作用,调节器的修正动作与偏差成比例. I作用{INTEGRAL}:积分作用,调节器的修正动作随偏差存在时间的
延长而增大.
D作用{Derivate}:微分作用,调节器的修正动作开始时较大,随后变小,偏差渐趋于零.
总的来说,PID作用为,修正作用在开始时大{D作用}随后减少到一个数值,此值与偏差成比例{P作用},但随时间再度增大{I作用},而且在有偏差时一直存在.
进分解炉的三次风温对分解炉内煤粉的燃烧及分解炉的出口温度亦有着重要的影响.从表中可见,当窑头喂煤量下降,致使物料煅烧温度不足,一方面会影响熟料质量,另一方面使落入蓖冷机的熟料温度亦降低,在同等的操作条件下,其三次温风降低.三次风温降低就会对分解炉内燃料燃烧产生影响,特别是对于挥发分低、灰分高的煤粉,影响就更为显著。
珠江水泥厂SLC窑分解炉的喂煤点与喂料点很接近,生料碳酸盐分解大量吸热,若三次风温低,进一步延滞了煤粉的燃烧.此时即使在分解炉多加煤,煤粉燃烧不完全,废气中CO含量增加,分解炉温度并不高.
适当提高及稳定三次风温,亦即提高及稳定了二次风温,对分解炉及窑头的煤粉燃烧有着十分重要的影响.在熟料温度、结粒情况及冷却用风量变化不大的清况,稳定一定的篦冷机篦下压力,意味着可保证篦床上的熟料层厚度一定,从而可得到稳定的二、三次风温,为良好与稳定的燃烧创造条件。
3.分解炉温度与末级旋风筒及物料、燃料情况
燃料在分解炉内燃烧放热,料粉在其中吸热分解;随后,气固两相流离开分解炉进入末级旋风筒,进行气固分离;分离后的物料进入回转窑,而气体进入上一级旋风预热器。
正常情况下,煤粉在分解炉燃烧完全,分解炉的出口温度会高于最末一级旋风筒下部及其物料的温度。
但是,当分解炉内燃料的燃烧速度慢,燃料燃烧不完全,则未完全燃烧的煤粉在旋风筒内继续燃烧,此时则会使最末一级旋风筒下部及物料的温度比分解炉出口温度还要高。
如云浮水泥厂在1993年8月煤粉质量明显下降,灰分高、热值低,FCB型
预分解窑窑头三通道喷煤管未能适应烧这些质量差的煤,熟料煅烧温度低,三次风温明显下降,而低的三次风温有进一步延滞了分解炉内煤粉的燃烧,可谓雪上加霜。
就这样不完全燃烧的煤粉进入五级旋风筒内继续燃烧,五级旋风筒内下部温度比分解炉出口温度还高。
在这种情况下,废气中的CO含量高,还原气氛重,易结皮堵塞,而分解炉的平均温度并不高,入窑物料碳酸盐分解率亦较低,熟料产量下降。
还需说明的是,分解炉的通风量对分解炉出口温度及末级旋风筒下部温度亦有影响即使分解炉的喂煤量、物料量不变,但通风量改变,亦会产生影响。
当通风量过大,分解炉内气流速度过快,燃料及物料在分解炉内停留时间不足;反之,当通风量过小,供气不足,燃料燃烧同样受影响。
总之,通风量的波动,窑风量与分解炉风量的分配不当,都会影响分解炉燃料的燃烧,从而导致分解炉出口温度与最末一级旋风筒下部温度的异常。
分解炉的温度控制还应考虑产量及物料的情况。
当产量较低,即喂料量较小,回转窑的转速亦较慢,此时应相应降低分解炉温度。
因分解炉温度过高,一方面会增加热耗,另一方面还不利于热工制度的稳定,不利于熟料的烧成。
反之,当产量较高,在分解炉能力许可的情况下适当提高分解炉的温度,减轻回转窑的热负荷。
但是,当设备富裕能力小,超产时窑系统的平衡是相当脆弱的,遇到小小的波动亦难以调整,故提高分解炉温度,提高产量适度为宜。
而当物料反应活性较差,石灰石结晶状况较好,晶体尺寸较大,其分解炉温度较高。
此时应在可能的条件下把分解炉温度控制高一些,以保证入窑物料的分解率。
完成于2007年5月19日星期六。