塑料挤出机的工作原理
挤出机的工作原理
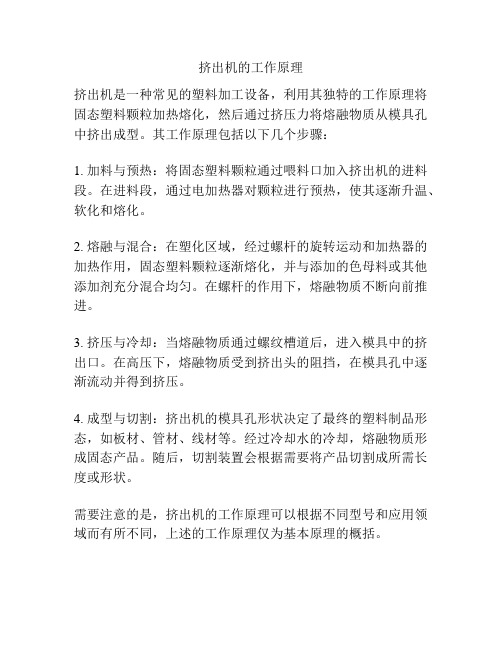
挤出机的工作原理
挤出机是一种常见的塑料加工设备,利用其独特的工作原理将固态塑料颗粒加热熔化,然后通过挤压力将熔融物质从模具孔中挤出成型。
其工作原理包括以下几个步骤:
1. 加料与预热:将固态塑料颗粒通过喂料口加入挤出机的进料段。
在进料段,通过电加热器对颗粒进行预热,使其逐渐升温、软化和熔化。
2. 熔融与混合:在塑化区域,经过螺杆的旋转运动和加热器的加热作用,固态塑料颗粒逐渐熔化,并与添加的色母料或其他添加剂充分混合均匀。
在螺杆的作用下,熔融物质不断向前推进。
3. 挤压与冷却:当熔融物质通过螺纹槽道后,进入模具中的挤出口。
在高压下,熔融物质受到挤出头的阻挡,在模具孔中逐渐流动并得到挤压。
4. 成型与切割:挤出机的模具孔形状决定了最终的塑料制品形态,如板材、管材、线材等。
经过冷却水的冷却,熔融物质形成固态产品。
随后,切割装置会根据需要将产品切割成所需长度或形状。
需要注意的是,挤出机的工作原理可以根据不同型号和应用领域而有所不同,上述的工作原理仅为基本原理的概括。
pvc挤出机挤出原理
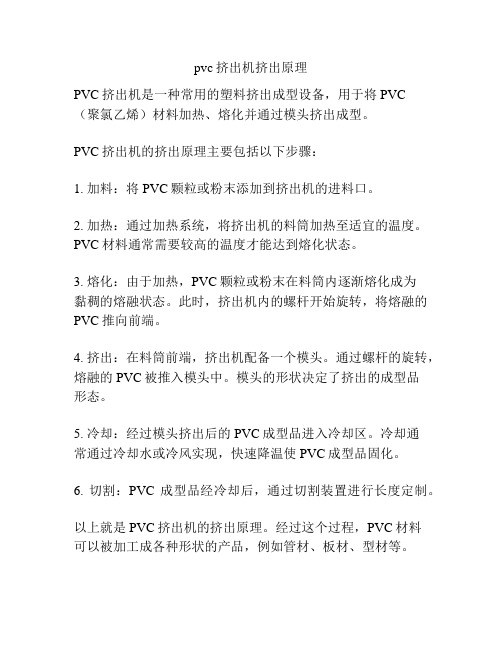
pvc挤出机挤出原理
PVC挤出机是一种常用的塑料挤出成型设备,用于将PVC
(聚氯乙烯)材料加热、熔化并通过模头挤出成型。
PVC挤出机的挤出原理主要包括以下步骤:
1. 加料:将PVC颗粒或粉末添加到挤出机的进料口。
2. 加热:通过加热系统,将挤出机的料筒加热至适宜的温度。
PVC材料通常需要较高的温度才能达到熔化状态。
3. 熔化:由于加热,PVC颗粒或粉末在料筒内逐渐熔化成为
黏稠的熔融状态。
此时,挤出机内的螺杆开始旋转,将熔融的PVC推向前端。
4. 挤出:在料筒前端,挤出机配备一个模头。
通过螺杆的旋转,熔融的PVC被推入模头中。
模头的形状决定了挤出的成型品
形态。
5. 冷却:经过模头挤出后的PVC成型品进入冷却区。
冷却通
常通过冷却水或冷风实现,快速降温使PVC成型品固化。
6. 切割:PVC成型品经冷却后,通过切割装置进行长度定制。
以上就是PVC挤出机的挤出原理。
经过这个过程,PVC材料
可以被加工成各种形状的产品,例如管材、板材、型材等。
热熔挤出工作原理

热熔挤出工作原理
热熔挤出是一种通过将塑料加热熔化后,通过挤出机的作用将熔化的塑料物料挤压成所需的形状的加工方法。
其工作原理可以分为以下几个步骤:
1. 加料和预热:将塑料颗粒或粉末通过料斗加入挤出机的进料口。
在进入挤出机之前,塑料物料会经过加热器进行预热,使其达到适合挤出的熔化温度。
2. 挤出:预热后的塑料物料进入挤出机的螺杆腔体,由于螺杆的旋转运动,将塑料物料推进到腔体的末端。
在腔体末端处,塑料物料被加热到足够的温度并熔化。
3. 挤出头:在腔体的末端,有一个挤出头,其内部有一个模具,其形状和尺寸可以根据所需的产品进行定制。
熔化的塑料物料通过挤出头的模具孔挤出,并按照模具的形状得到所需的产品。
4. 冷却和固化:挤出机出来的塑料产品通过冷却装置进行冷却,使其迅速降温,帮助固化和保持所需形状。
通常,冷却装置会通过水或气体进行冷却。
5. 切割和整形:冷却固化后的塑料产品通过切割装置进行切割,并经过必要的整形和加工,以得到最终的产品形状。
总的来说,热熔挤出工作原理是通过将塑料预热熔化后,通过挤出机的作用将其挤压成所需形状,并通过冷却和固化来得到
最终的产品。
这种加工方法通常用于生产塑料管道、板材、膜等各种形状的塑料制品。
塑料挤出机的工作原理

塑料挤出机的工作原理塑料挤出机(Plastic Extruder)是一种常见的塑料成型设备,广泛应用于塑料加工领域中。
它以塑料为原料,通过机械加工方式来进行塑料加工,生产出各种形状和大小的塑料制品。
本文将介绍塑料挤出机的工作原理。
塑料挤出机的组成通常情况下,塑料挤出机主要由以下部分组成:1.进料系统:主要由料斗、传送装置和分散装置组成。
2.挤出系统:主要由挤出机筒、螺杆和储料仓组成。
3.模头系统:主要由模头、模头加热系统和调节器组成。
4.切割系统:主要由切割装置、切料机和运料装置组成。
塑料挤出机的工作原理进料系统进料系统主要负责将塑料原料送入挤出机的筒内,再通过挤压螺杆进行混合和加热。
在进料系统中,传送装置将塑料颗粒从料斗中传送到挤出机筒内,同时分散装置将颗粒均匀分散,确保混合充分。
挤出系统挤出系统是整个挤出机的核心部分。
在此部分中,挤出机筒内部有一根双螺杆,分别为主螺杆和辅助螺杆,主螺杆通过电机带动转动,同时负责将塑料颗粒进行混合加热,辅助螺杆则帮助主螺杆将塑料颗粒顺序推动到模头处。
在挤出系统中,塑料原料经过一系列的过滤、熔化、混合和加压,最终在模头中形成所需的产品。
模头系统模头是挤出机生产塑料制品的关键部分。
模头将塑料熔体通过特定的形状和尺寸进行成型,同时负责控制产品的厚度和质量。
在模头系统中,模头先通过预热系统进行加热,然后通过调节器对模头进行调节,确保产品的尺寸和形状符合要求。
切割系统切割系统负责将成型的塑料制品切割、制成所需的长度,并通过运料装置将产品送到下一个加工流程中。
在切割系统中,切割装置通过特定的切割方式将产品切成所需的长度,然后通过运料装置将其送往下一个加工环节。
结语通过以上介绍,我们了解到塑料挤出机的工作原理和组成结构。
挤出机在现代工业生产中具有广泛的应用,生产出的各种塑料制品可用于包装、建材、汽车、电子设备等领域,是创造人类生活的重要设备之一。
挤出机原理

挤出机原理
挤出机是一种常用的塑料加工设备,其原理是利用螺杆旋转将塑料颗粒加热、
熔化,并通过一定的压力将熔融塑料挤出成型。
挤出机的工作原理可以分为三个主要步骤,加料、熔化和挤出。
首先,塑料颗粒被输送到挤出机的进料口,然后通过螺杆的旋转和推进,塑料
颗粒被逐渐推送到机筒的加热区。
在加热区,塑料颗粒受到高温加热,逐渐熔化成为熔融状态的塑料熔体。
同时,螺杆的旋转还起到了混合和均匀加热的作用,确保塑料熔体的温度和性能均匀一致。
接下来,熔化的塑料熔体被推送到机筒的压力区,通过螺杆的旋转和挤压,塑
料熔体受到一定的压力,使其在机筒内得到进一步的挤压和塑形。
在这个过程中,塑料熔体的温度和压力得到了精确的控制,以确保挤出成型的塑料制品具有良好的物理性能和外观质量。
最后,经过压力区的挤出成型后的塑料制品通过模具头,按照模具的形状和尺
寸得到所需的成型产品。
挤出成型的塑料制品可以是管材、板材、薄膜、型材等不同形状和尺寸的制品,广泛应用于塑料加工行业。
总的来说,挤出机的工作原理是通过螺杆的旋转和推进,将塑料颗粒加热、熔化,并通过一定的压力将熔融塑料挤出成型。
这种工作原理简单高效,能够满足不同形状和尺寸的塑料制品的生产需求,是塑料加工行业中不可或缺的重要设备之一。
塑料挤出机的工作原理

塑料挤出机的工作原理挤出机参数作用及工作原理挤出机出机的功能是采用加热、加压和剪切等方式,将固态塑料转变成均匀一致的熔体,并将熔体送到下一个工艺。
熔体的生产涉及到混合色母料等添加剂、掺混树脂以及再粉碎等过程。
成品熔体在浓度和温度上必须是均匀的。
加压必须足够大,以将粘性的聚合物挤出。
挤出机通过一个带有一个螺杆和螺旋道的机筒完成以上所有的过程。
塑料粒料通过机筒一端的料斗进入机筒,然后通过螺杆传送到机筒的另一端。
为了有足够的压力,螺杆上螺纹的深度随着到料斗的距离的增加而下降。
外部的加热以及在塑料和螺杆由于摩擦而产生的内热,使塑料变软和熔化。
图1是一个简化挤出机。
不同的聚合物及不同的应用,对挤出机的设计要求常常也是不同的。
许多选项涉及到排出口、多个上料口,沿着螺杆特殊的混合装置,熔体的冷却及加热,或无外部热源(绝热挤出机),螺杆和机筒之间的间隙变化相对大小,以及螺杆的数目等。
例如,双螺杆挤出机与单螺杆挤出机相比,能使熔体得到更加充分的混合。
串联挤压是用第一个挤出机挤出的熔体,作为原料供给第二个挤出机,通常用来生产挤出聚乙烯泡沫图1简化挤出机挤出机的特征尺寸是螺杆的直径(D)和螺杆的长度(L)与直径(D)的比率(L/D)。
挤出机通常至少由三段组成。
第一段,靠近加料斗,是加料段。
它的功能让物料以一个相对平稳的速率进入挤出机。
一般情况下,为避免加料通道的堵塞,这部分将保持相对低的温度。
第二部分为压缩段,在这段形成熔体并且压力增加。
由加料段到压缩段的过渡可以突然的也可以是逐步(平缓)的。
最后一个部分计量段,紧靠着挤出机出口。
主要功能是流出挤出机的物质是均匀一致的。
在这部分为确保组成成分和温度的均匀性,物料应有足够的停留时间。
在机筒的尾部,塑料熔体通过一个机头离开挤出机,这个机头设计成理想的形状,挤出的熔体流在这里通过。
另一个重要的部分是挤出机的驱动机构。
它控制螺杆的旋转速度,螺杆的旋转速度决定着挤出机的产量。
所需的功率由聚合物的粘性(流动阻力)决定。
塑料挤出机的工作原理及流程
塑料挤出机的工作原理及流程一、塑料挤出机的工作原理塑料挤出机是一种将塑料颗粒加热熔融后,通过挤出机螺杆的旋转运动,使熔化的塑料挤出成型的设备。
其工作原理可分为以下几个步骤:1. 加料:将塑料颗粒投入到挤出机的料斗中,通过输送装置将塑料颗粒送入挤出机的螺杆区。
2. 加热和熔融:进入螺杆区的塑料颗粒会受到加热器的加热,使塑料颗粒熔化成为熔融状态。
3. 挤出:螺杆旋转推动熔融的塑料向前挤压,并通过模头的形状和尺寸决定挤出物的形状。
4. 冷却:挤出的塑料通过冷却装置进行快速冷却,以便使其保持所需的形状和尺寸。
5. 切割:冷却后的塑料通过切割装置进行切割,得到所需的长度。
二、塑料挤出机的工作流程塑料挤出机的工作流程可以简单分为以下几个环节:1. 准备工作:根据生产需求选择合适的塑料颗粒,并将其加入到挤出机的料斗中。
同时,还需要根据产品要求调整挤出机的参数,如温度、转速等。
2. 加料和加热:启动挤出机,将塑料颗粒从料斗中输送到螺杆区。
在输送过程中,塑料颗粒会受到加热器的加热,逐渐熔化成为熔融状态。
3. 挤出和成型:熔融的塑料通过螺杆的旋转运动,被推送向模头。
模头的形状和尺寸将决定最终挤出物的形状。
挤出物通过模头的出口,形成所需的截面形状。
4. 冷却和固化:挤出的塑料通过冷却装置进行快速冷却,使其保持所需的形状和尺寸。
冷却后的挤出物将逐渐固化,变得坚硬。
5. 切割和收集:冷却固化后的挤出物通过切割装置进行切割,得到所需的长度。
切割后的产品被收集起来,作为成品。
三、工作环节和要求在塑料挤出机的工作过程中,需要注意以下几个环节和要求:1. 温度控制:挤出机的温度控制是非常重要的,需要根据不同的塑料材料和产品要求,调整适当的温度。
温度过高或过低都会影响挤出物的质量和成型效果。
2. 螺杆运动:螺杆的旋转速度和推进力度直接影响挤出物的产量和成型质量。
需要根据产品要求和材料特性进行调整。
3. 模头设计:模头的形状和尺寸对最终挤出物的形状和尺寸有着重要影响。
单螺杆挤出机工作的原理
单螺杆挤出机工作的原理
单螺杆挤出机是一种常用的塑料加工设备,用于将塑料颗粒或粉末加热熔融后挤出成型。
单螺杆挤出机的工作原理如下:
1. 加料:塑料颗粒或粉末通过进料口加入到螺杆挤出机的进料段。
2. 进料和融化:螺杆在机筒中旋转推动塑料颗粒向前移动,并同时施加高温和高压力。
随着塑料在螺杆和机筒内摩擦加热,塑料开始融化并形成均匀的熔体。
3. 压力增加和融化区:螺杆的螺纹逐渐变浅,使得交通道变窄,从而增加了塑料在机筒中的压力,并进一步加热、融化和混合塑料。
4. 挤出:在融化区后面的机筒中,螺杆开始改变形状,将熔融的塑料推向机筒出口,并进一步加压,使塑料通过机筒的模具孔挤出。
5. 冷却和定型:挤出的塑料通过模具孔进入到冷却水中进行快速冷却,使之硬化和定型。
通常,挤出机的模具孔和冷却系统都是根据所需的产品形状来设计的。
6. 切割和收集:挤出的成型物从模具孔中连续挤出,然后被切割成所需的长度,并通过传送带或其他收集装置进行收集和包装。
总结:单螺杆挤出机的工作原理是通过螺杆的旋转和设计,将塑料颗粒加热、融化和压力推向模具孔进行挤出,最后冷却和定型。
这种工作原理可以实现连续、高效、精确的塑料挤出成型过程。
挤塑机的工作原理
挤塑机的工作原理
挤塑机是一种常用的塑料加工设备,其工作原理是通过加热和压力将塑料料粒或者粉末形态的塑料原料转化为连续且可定型的塑料制品。
首先,将塑料原料装入挤塑机的料斗中,通过传送系统将塑料送入加热机筒内。
加热机筒内设置有一对旋转的螺杆,称为螺杆组。
螺杆由电机带动转动,在转动的过程中将塑料原料推入机筒。
在机筒内,电加热器将机筒加热到塑料的熔化温度。
随着螺杆的转动,熔化的塑料被推向挤出口方向,并且在螺杆的作用下进行塑料均化和混合。
当塑料原料从机筒进入到挤出口时,会遇到安装在机筒口的挤出模具。
挤出模具中的形状决定了挤塑机最终制造的产品形状和尺寸。
当塑料通过挤出模具时,受到模具的限制,塑料被挤压成所需形状,并且经过冷却后固化。
在冷却过程中,通常会使用风冷或者水冷系统来快速降低塑料温度,使其迅速硬化。
硬化后的塑料制品可以通过切割机等设备进行切割和整形,最终得到成品。
挤塑机的工作原理可以总结为:将塑料原料加热到熔化温度,通过螺杆的作用将熔化的塑料均匀推向挤出口,并在挤出模具内冷却和固化,最终得到所需形状和尺寸的塑料制品。
塑胶挤出机工作原理
塑胶挤出机工作原理
塑胶挤出机的工作原理:塑胶挤出机是一种以塑料为原料,利用螺杆和机筒的旋转作用,通过加热塑化、混合、剪切和塑化等过程,使物料在机筒内形成均匀的容积压力,然后从螺杆顶端不断挤出,形成一定长度和一定规格的塑料制品。
塑料在机头内塑化过程中产生大量热量,使机头温度升高,当机头温度达到设定值时,螺杆便开始反转。
机头反转后,一部分物料从机头压入螺杆的螺纹孔中。
当螺杆反转时,物料进入机筒内与螺杆一起继续转动。
当机筒温度达到设定值时,机头和机筒停止转动并开始冷却。
在挤出过程中,由于螺杆和机筒的旋转作用,物料在机筒内不断受到挤压、拉伸、剪切等作用而塑化、混合、破碎、塑化、加热固化。
从挤出的塑料看是由若干个单体或聚合物分子在螺杆和机筒的剪切应力作用下被挤出并形成塑料制品。
塑化过程主要是物料温度的提高和压力的降低;熔融过程主要是压力的提高和温度的降低;塑化过程主要是压力的提高和温度的降低;塑化与熔融之间存在着一种过渡关系。
—— 1 —1 —。
- 1、下载文档前请自行甄别文档内容的完整性,平台不提供额外的编辑、内容补充、找答案等附加服务。
- 2、"仅部分预览"的文档,不可在线预览部分如存在完整性等问题,可反馈申请退款(可完整预览的文档不适用该条件!)。
- 3、如文档侵犯您的权益,请联系客服反馈,我们会尽快为您处理(人工客服工作时间:9:00-18:30)。
塑料挤出机的工作原理挤出机参数作用及工作原理挤出机出机的功能是采用加热、加压和剪切等方式,将固态塑料转变成均匀一致的熔体,并将熔体送到下一个工艺。
熔体的生产涉及到混合色母料等添加剂、掺混树脂以及再粉碎等过程。
成品熔体在浓度和温度上必须是均匀的。
加压必须足够大,以将粘性的聚合物挤出。
挤出机通过一个带有一个螺杆和螺旋道的机筒完成以上所有的过程。
塑料粒料通过机筒一端的料斗进入机筒,然后通过螺杆传送到机筒的另一端。
为了有足够的压力,螺杆上螺纹的深度随着到料斗的距离的增加而下降。
外部的加热以及在塑料和螺杆由于摩擦而产生的内热,使塑料变软和熔化。
图1是一个简化挤出机。
不同的聚合物及不同的应用,对挤出机的设计要求常常也是不同的。
许多选项涉及到排出口、多个上料口,沿着螺杆特殊的混合装置,熔体的冷却及加热,或无外部热源(绝热挤出机),螺杆和机筒之间的间隙变化相对大小,以及螺杆的数目等。
例如,双螺杆挤出机与单螺杆挤出机相比,能使熔体得到更加充分的混合。
串联挤压是用第一个挤出机挤出的熔体,作为原料供给第二个挤出机,通常用来生产挤出聚乙烯泡沫图1简化挤出机挤出机的特征尺寸是螺杆的直径(D)和螺杆的长度(L)与直径(D)的比率(L/D)。
挤出机通常至少由三段组成。
第一段,靠近加料斗,是加料段。
它的功能让物料以一个相对平稳的速率进入挤出机。
一般情况下,为避免加料通道的堵塞,这部分将保持相对低的温度。
第二部分为压缩段,在这段形成熔体并且压力增加。
由加料段到压缩段的过渡可以突然的也可以是逐步(平缓)的。
最后一个部分计量段,紧靠着挤出机出口。
主要功能是流出挤出机的物质是均匀一致的。
在这部分为确保组成成分和温度的均匀性,物料应有足够的停留时间。
在机筒的尾部,塑料熔体通过一个机头离开挤出机,这个机头设计成理想的形状,挤出的熔体流在这里通过。
另一个重要的部分是挤出机的驱动机构。
它控制螺杆的旋转速度,螺杆的旋转速度决定着挤出机的产量。
所需的功率由聚合物的粘性(流动阻力)决定。
而聚合物的粘性取决于温度和流动速率,随着温度和剪切力的增加而下降。
挤出机都带有滤网,能将杂质阻挡在滤网上。
为避免停工,滤网应能自动更换。
当加工带有杂质的树脂时,比如回收料,这一点特别重要。
挤塑机的螺杆分进料段,塑化,熔融段,温度根据塑料粒子的工艺参数,型号按螺杆直径分45 65 75 80 90 120 150 200,螺杆长度常用有D20 D25,加热段一般机身5区,哈夫1区或2区,机头2区,至于配驱动,正规挤塑机厂家都会提供参数。
塑料颗粒加热后由螺杆的运动来改变原来的状态,类型就很多了,看具体应用.变频的容量跟螺杆的直径成正比,再根据原料的不同调整单螺杆一般在有效长度上分为三段,按螺杆直径大小螺距螺深确定三段有效长度,一般按各占三分之一划分。
料口最后一道螺纹开始叫输送段:物料在此处要求不能塑化,但要预热、受压挤实,过去老挤出理论认为此处物料是松散体,后来通过证明此处物料实际是固体塞,就是说这里物料受挤压后是一固体象塞子一样,因此只要完成输送任务就是它的功能了。
第二段叫压缩段,此时螺槽体积由大逐渐变小,并且温度要达到物料塑化程度,此处产生压缩由输送段三,在这里压缩到一,这叫螺杆的压缩比--3:1,有的机器也有变化,完成塑化的物料进入到第三段。
第三段是计量段,此处物料保持塑化温度,只是象计量泵那样准确、定量输送熔体物料,以供给机头,此时温度不能低于塑化温度,一般略高点。
螺杆热处理螺杆不是淬火的,是氮化的。
要是淬火的话在高温下会回火的。
热处理有很多方法,这还要看螺杆材质的不同来区分。
一般38GrMoAlA氮化就可以,但象特殊的不锈钢螺杆,SKD61的螺杆。
HPT系列的全硬螺杆等一般都要先淬火,而且最好是用盐液炉。
但因为这样的热处理硬度过高,所以一般都要再进行回火。
根据要求不同进行氮化处理。
也可以不用氮化一:如果用于生产一般性的2次料或新料,可以用氮化料筒/螺杆组.也可以用氮化料筒配合金螺杆这样更好(因为同等材质下螺杆要早于料筒先磨损)二:生产填充型的料,如加玻纤/碳酸钙等那就要使用合金料筒/螺杆组,这样性价比会高点氮化就是通过炉子加温把氨气参进机筒螺杆的表面,使之产生一层硬的表面。
一般能渗透0.5-0.7的深度。
时间大概需要96个小时主要参数:压缩比,长径比,导程.硬度,直线度等....压缩比:就是进料段螺槽的容积和计量段螺槽的容积比.长径比就是指螺杆的外径和有效螺纹部分长度之比.导程:就是螺纹间的距离.计算压缩比:是进料段螺槽的容积和计量段螺槽的容积之比螺槽的体积:加料段第一个螺槽的深度和均化段最后一个螺槽的深度的比值约等于压缩比螺杆的压缩比:是最重要的,根据不筒的原料设计不同的压缩比,然后考虑的是螺杆的产量问题。
塑料挤出机的工作原理挤塑机的螺杆分进料段,塑化,熔融段,温度根据塑料粒子的工艺参数,型号按螺杆直径分45 65 75 80 90 120 150 200,螺杆长度常用有D20 D25,加热段一般机身5区,哈夫1区或2区,机头2区,至于配驱动,正规挤塑机厂家都会提供参数。
塑料颗粒加热后由螺杆的运动来改变原来的状态,类型就很多了,看具体应用.变频的容量跟螺杆的直径成正比,再根据原料的不同调整.螺杆的基本参数一般螺杆分为三段即加料段,压缩段,均化段。
加料段——底经较小,主要作用是输送原料给后段,因此主要是输送能力问题,参数(L1,h1),h1=(0.12-0.14)D。
压缩段——底经变化,主要作用是压实、熔融物料,建立压力。
参数压缩比ε=h1/h3及L2。
准确应以渐变度A=(h1-h3)/L2。
均化段(计量段)——将压缩段已熔物料定量定温地挤到螺杆最前端、参数(L3,h3),h3=(0.05-0.07)D。
对整条螺杆而言,参数L/D-长径比L/D利弊:L/D与转速n,是螺杆塑化能力及效果的重要因素,L/D大则物料在机筒里停留时间长,有利于塑化,同时压力流、漏流减少,提高了塑化能力,同时对温度分布要求较高的物料有利,但大之后,对制造装配使用上又有负面影响,一般L/D为(18~20),但目前有加大的趋势。
其它螺距S,螺旋升角φ=πDtgφ,一般D=S,则φ=17°40′。
φ对塑化能力有影响,一般来说φ大一些则输送速度快一些,因此,物料形状不同,其φ也有变化。
粉料可取φ=25°左右,圆柱料φ=17°左右,方块料φ=15°左右,但φ的不同,对加工而言,也比较困难,所以一般φ取17°40′。
棱宽e,对粘度小的物料而言,e尽量取大一些,太小易漏流,但太大会增加动力消耗,易过热,e=(0.08~0.12)D。
总而言之,在目前情况下,因缺乏必要的试验手段,对螺杆的设计并没有完整的设计手段。
大部分都要根据不同的物料性质,凭经验制订参数以满足不同的需要,各厂大致都一样。
一.PC料(聚碳酸酯)特点:①非结晶性塑料,无明显熔点,玻璃化温度140°~150℃,熔融温度215℃~225℃,成型温度250℃~320℃。
②粘度大,对温度较敏感,在正常加工温度范围内热稳定性较好,300℃长时停留基本不分解,超过340℃开始分解,粘度受剪切速率影响较小。
③吸水性强参数选定:a.L/D针对其热稳定性好,粘度大的特性,为提高塑化效果尽量选取大的长径比,本厂取26。
由于其融熔温度范围较宽,压缩可较长,故采用渐变型螺杆。
L1=30%全长,L2=46%全长。
b.压缩比ε由渐变度A需与熔融速率相适应,但目前融熔速率还无法计算得出,根据PC从225℃融化至320℃之间可加工的特性,其渐变度A值可相对取中等偏上的值,在L2较大的情况下,普通渐变型螺杆ε=2~3,本厂取2.6。
c.因其粘度高,吸水性强,故在均化段之前,压缩段之后于螺杆上加混炼结构,以加强固体床解体,同时,可使其中夹带的水份变成气体逸出。
d.其它参数如e,s,φ以及与机筒的间隙都可与其它普通螺杆相同。
二.PMMA(有机玻璃)特点:①玻璃化温度105℃,熔融温度大于160℃,分解温度270℃,成型温度范围很宽。
②粘度大,流动性差,热稳定性较好。
③吸水性较强。
参数选择a.L/D选取长径比为20~22的渐变型螺杆,视其制品成型的精度要求一般L1=40%,L2=40%。
b.压缩比ε,一般选取2.3~2.6。
c.针对其有一定亲水性,故在螺杆的前端采用混炼环结构。
d.其它参数一般可按通用螺杆设计,与机筒间隙不可太小。
三.PA(尼龙)特性:①结晶性塑料,种类较多,种类不一样,其熔点也不一样,且熔点范围窄,一般所用PA66其熔点为260℃~265℃。
②粘度低,流动性好,有比较明显的熔点,热稳定性差。
③吸水性一般。
参数选择a.L/D选取长径比18~20的突变型螺杆。
b.压缩比,一般选取3~3.5,其中防止过热分解h3=0.07~0.08D。
c.因其粘度低,故止逆环处与机筒间隙应尽量小,约0.05,螺杆与机筒间隙约0.08,如有需要,视其材料,前端可配止逆环,射嘴处应自锁。
d.其它参数、可按通用螺杆设计。
四.PET(聚酯)特性:①熔点250℃~260℃,吹塑级PET则成型温度较广一点,大约255℃~290℃。
②吹塑级PET粘度较高,温度对粘度影响大,热稳定性差。
参数选择①L/D一般取20,三段分布L1=50%-55%,L2=20%。
②采用低剪切、低压缩比的螺杆,压缩比ε,一般取1.8~2,同时剪切过热导致变色或不透明h3=0.09D。
③螺杆前端不设混炼环,以防过热,藏料。
④因这种材料对温度较敏感,而一般厂家多用回收料,为提高产量,我厂采用的是低剪切螺杆,所以可适当提高马达转速,以达到目的。
同时在使用回收料方面(大部分为片料),本厂根据实际情况,为加大加料段的输送能力,也采取了加大落料口径在机筒里开槽等方式,取得了比较好的效果。
五.PVC(聚氯乙烯)热敏性物料,一般分为硬质和软质,其区别在于原料中加入增塑剂的多少,少于10%的为硬质,多于30%为软质。
特点:①无明显熔点,60℃变软,100℃~150℃粘弹态,140℃时熔融,同时分解,170℃分解迅速,软化点接近于分解点,分解释放于HC1气体。
②热稳定性差,温度、时间都会导致分解,流动性差。
设计原则a.温度控制严格,螺杆设计尽量要低剪切,防止过热。
b.螺杆、机筒要防腐蚀。
c.注塑工艺需严格控制。
一般讲,螺杆参数为L/D=16~20,h3=0.07D,ε =1.6~2 ,L1=40%,L2=40%。
为防止藏料,无止逆环,头部锥度20°~30°,对软胶较适应,如制品要求较高,可采用无计量段,分离型螺杆,此种螺杆对硬质PVC较适合,而且为配合温控,加料段螺杆内部加冷却水或油孔,机筒外加冷水或油槽,温度控制精度±2℃左右。