铝液净化工艺
铝及铝合金的熔体净化(baidu)

夹杂物的生成途径主要是: • 从炉村中吸收杂质; • 从熔剂和熔炼添加剂中吸收杂质; • 从炉气中反应并吸收杂质; • 从炉料及炉渣中吸收杂质。
•夹杂物的危害
并不是熔体中的所有异物都是有害夹杂。金属中 非金属异质点的形态和大小,对金属性质有重要影 响。细小,弥散均匀分布的夹杂颗粒,在金属凝固 时,可以成为结晶的异质核心,同时也可以阻碍晶 粒的长大,起到细化晶粒的作用。所以高纯铝较一 般的工业纯铝更容易形成粗大晶粒。
• 非金属夹杂的种类很多,按其化学成分可分为氧 化物(FeO,SiO2,Al2O3,TiO2,MgO,ZnO等);氮化 物(AlN,ZrN,TiN等);硫化物(Ni3S2,CeS,Cu2S 等);氯化物(NaCl,KCl,MgCl2等);氟化物 (CaF2,NaF等);硅酸盐(Al2O•SiO2等)。这些 夹杂以不同形态和大小分布在金属熔体中,对金 属性能产生不同影响。
铝及铝合金的熔体净化
• 有色金属及其合金熔体在熔炼过程存在气体、各 种非金属夹杂物等,影响金属的纯洁度,往往会使 产品产生气孔、夹杂、疏松、裂纹等缺陷,影响铸 锭的加工性能及制品强度、塑性、抗蚀性、阳极 氧化性和外观质量。同时,在有色金属中除气体 和非金属夹杂之外,还含有少量的金属杂质,如 铝合金的钠、钙等低熔点金属。钠在含镁量高的 镁-铝系合金中易引起热裂敏感性,合金热轧时易 产生开裂,通常称之谓“钠脆性”,此外还影响 熔体的流动性和铸造性。
Al中Al2O3夹杂物的形态(两维)
Al中Al2O3夹杂物的形态(三维)
AlN
采用先进的测渣方法捕捉到的夹渣
Refractories
采用先进的测渣方法捕捉到的夹渣
• 夹杂物的来源与危害 • 杂质的吸收和积累主要是熔炼过程中,金属熔体
铝厂净化车间工艺流程

铝厂净化车间工艺流程
《铝厂净化车间工艺流程》
铝厂净化车间是用于生产铝材的重要环节,需要进行严格的工艺流程来确保产品质量和生产安全。
下面是一般铝厂净化车间的工艺流程:
1. • 原料准备:铝厂净化车间的原料主要包括铝锭、添加剂和
其他辅助材料。
这些原料需要按照一定的比例准备好,并在车间内进行质量检测,确保其符合生产要求。
2. • 熔炼:准备好的原料被送入熔炼炉中进行加热熔化。
熔炼
的温度和时间需要严格控制,以确保熔炼后的铝液质量良好。
3. • 精炼:经过熔炼的铝液进入精炼炉内,通过吹氩等方法对
铝液进行精炼处理。
这个过程可以有效去除铝液中的气体和杂质,提高产品的纯度和质量。
4. • 浇铸:经过精炼处理的铝液被送入浇铸机进行成型。
浇铸
的过程需要注意温度、速度和压力的控制,以确保成型铝材的尺寸和表面质量。
5. • 固化:成型的铝材经过一定的时间后进入固化室进行冷却
和固化。
这个过程是为了确保铝材的内部结构和性能符合标准要求。
6. • 检测和包装:固化后的铝材需要进行各项技术指标的检测,
确保产品质量达标。
通过检测后,铝材会被打包包装,准备出厂销售。
这些是一般铝厂净化车间的工艺流程,通过严格的控制和管理,铝厂可以生产出高质量的铝材产品,满足市场的需求。
再生铝工艺流程
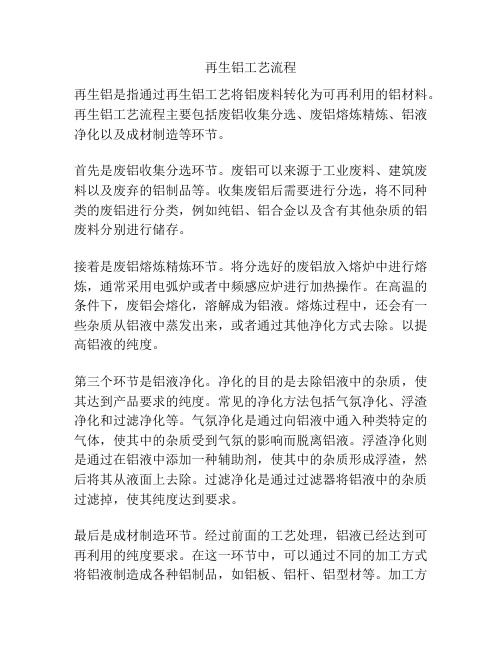
再生铝工艺流程再生铝是指通过再生铝工艺将铝废料转化为可再利用的铝材料。
再生铝工艺流程主要包括废铝收集分选、废铝熔炼精炼、铝液净化以及成材制造等环节。
首先是废铝收集分选环节。
废铝可以来源于工业废料、建筑废料以及废弃的铝制品等。
收集废铝后需要进行分选,将不同种类的废铝进行分类,例如纯铝、铝合金以及含有其他杂质的铝废料分别进行储存。
接着是废铝熔炼精炼环节。
将分选好的废铝放入熔炉中进行熔炼,通常采用电弧炉或者中频感应炉进行加热操作。
在高温的条件下,废铝会熔化,溶解成为铝液。
熔炼过程中,还会有一些杂质从铝液中蒸发出来,或者通过其他净化方式去除。
以提高铝液的纯度。
第三个环节是铝液净化。
净化的目的是去除铝液中的杂质,使其达到产品要求的纯度。
常见的净化方法包括气氛净化、浮渣净化和过滤净化等。
气氛净化是通过向铝液中通入种类特定的气体,使其中的杂质受到气氛的影响而脱离铝液。
浮渣净化则是通过在铝液中添加一种辅助剂,使其中的杂质形成浮渣,然后将其从液面上去除。
过滤净化是通过过滤器将铝液中的杂质过滤掉,使其纯度达到要求。
最后是成材制造环节。
经过前面的工艺处理,铝液已经达到可再利用的纯度要求。
在这一环节中,可以通过不同的加工方式将铝液制造成各种铝制品,如铝板、铝杆、铝型材等。
加工方式包括挤压、锻造、铸造以及轧制等。
总结起来,再生铝工艺流程主要包括废铝收集分选、废铝熔炼精炼、铝液净化以及成材制造等环节。
通过这些工艺流程,可以将废铝转化为可再利用的铝材料,实现循环经济的目标,并减少自然资源的浪费。
同时,再生铝工艺流程还可以减少环境污染,并降低生产成本,具有重要的经济和环境意义。
铝电解过程对电解铝液的净化作用分析

铝电解过程对电解铝液的净化作用分析李 斌,覃 鹏(广西来宾银海铝业有限责任公司,广西 来宾 546100)摘 要:本文综合分析了利用冰晶石溶液对氧化铝杂质进行溶解、清除电解铝液当中氧化铝杂质、电磁分离方法对铝液中氧化铝杂质进行清除以及当前利用铝电解对电解铝液进行净化中存在的问题,希望能够对相关行业的发展起到促进作用。
关键词:铝电解;电解铝液;净化中图分类号:F426.32 文献标识码:A 文章编号:1002-5065(2018)10-0029-2Purification effect of aluminum electrolysis process on electrolytic aluminum liquidLI Bin,QIN Peng(Guangxi Laibin Yinhai Aluminum Co., Ltd.,Laibin 546100,China)Abstract: In this paper, the comprehensive analysis of the aluminum oxide impurities to make use of cryolite solution dissolve, remove electrolytic aluminium liquid of alumina material, electromagnetic separation method of alumina in aluminum liquid impurity removal and the current use of aluminum electrolysis to problems in the purification of electrolytic aluminium liquid, hope to be able to play a promoting effect on the development of related industries.Keywords: aluminum electrolysis; Electrolytic aluminium liquid; purification在进入新的发展时代后,人们的生活质量的到显著的提升,因此对所使用的生活用品质量也提出了越来越高的要求。
铝液循环技术
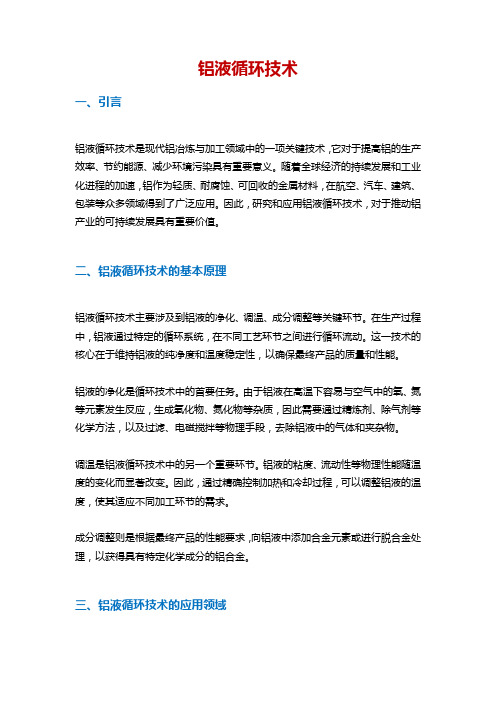
铝液循环技术一、引言铝液循环技术是现代铝冶炼与加工领域中的一项关键技术,它对于提高铝的生产效率、节约能源、减少环境污染具有重要意义。
随着全球经济的持续发展和工业化进程的加速,铝作为轻质、耐腐蚀、可回收的金属材料,在航空、汽车、建筑、包装等众多领域得到了广泛应用。
因此,研究和应用铝液循环技术,对于推动铝产业的可持续发展具有重要价值。
二、铝液循环技术的基本原理铝液循环技术主要涉及到铝液的净化、调温、成分调整等关键环节。
在生产过程中,铝液通过特定的循环系统,在不同工艺环节之间进行循环流动。
这一技术的核心在于维持铝液的纯净度和温度稳定性,以确保最终产品的质量和性能。
铝液的净化是循环技术中的首要任务。
由于铝液在高温下容易与空气中的氧、氮等元素发生反应,生成氧化物、氮化物等杂质,因此需要通过精炼剂、除气剂等化学方法,以及过滤、电磁搅拌等物理手段,去除铝液中的气体和夹杂物。
调温是铝液循环技术中的另一个重要环节。
铝液的粘度、流动性等物理性能随温度的变化而显著改变。
因此,通过精确控制加热和冷却过程,可以调整铝液的温度,使其适应不同加工环节的需求。
成分调整则是根据最终产品的性能要求,向铝液中添加合金元素或进行脱合金处理,以获得具有特定化学成分的铝合金。
三、铝液循环技术的应用领域铝冶炼领域:在铝冶炼过程中,铝液循环技术有助于提高冶炼效率,减少能源消耗。
通过优化铝液的流动路径和温度控制,可以降低电解槽的能耗,提高电流效率,从而降低生产成本。
铝合金制备领域:铝液循环技术在铝合金制备过程中具有广泛应用。
通过精确控制铝液的成分和温度,可以制备出具有优良力学性能和加工性能的铝合金材料。
这些材料被广泛应用于航空、汽车、轨道交通等高端制造领域。
铝材加工领域:在铝材加工过程中,如铸造、轧制、挤压等环节,铝液循环技术有助于提高产品的表面质量和内在性能。
通过优化铝液的流动和温度分布,可以减少产品的表面缺陷和内部应力,提高产品的成品率和使用寿命。
铝电解过程对电解铝液的净化作用探讨

铝电解过程对电解铝液的净化作用探讨作者:丁辉来源:《山东工业技术》2017年第15期摘要:铝制品对于居民日常生活当中具有重要的作用,在早期铝制品生产制作过程当中,因为自身工艺手段不完善,导致在电解铝液当中含有大量的氧化铝残留,这种残留物质严重的影响到铝制品自身质量。
因此如何有效的清除电解铝液当中的氧化铝杂质,是目前在该行业当中亟需解决的问题之一。
随着时代的发展,人们在生产制作铝制品的过程当中,开始逐渐转变工艺,不在如之前使用长流程制作工艺,对生产手段其进行精简处理,使用电解对于电解铝液当中的氧化铝等杂质进行清除,使铝制品的质量获得上升。
可以说铝电解技术使我国有关铝制品制造工艺真正上升一大步。
因此文章将以冰晶石熔体溶解氧化铝杂质、电解铝液当中氧化铝杂质清除、电磁分离电解铝液中氧化铝夹杂物、铝电解过程对电解铝液的净化中存在的问题四方面进行综合论述。
关键词:铝电解;电解铝液;净化DOI:10.16640/ki.37-1222/t.2017.15.1990 前言随着时代的发展,居民对于自身日常用品质量要求逐渐升高。
之前在铝制品制作过程当中,普遍使用的是长流程制作工艺,在该制作流程当中,对于电解铝液当中氧化铝等杂质没有办法及时进行清除,严重影响铝制品质量。
之前铝制品因为品质问题一直没有办法真正打开市场。
但是伴随着生产工艺逐渐提升,在铝制品生产制作过程中,开始使用电解方式消除其中的氧化铝等杂质,不仅操作流程简单,同时对于铝制品质量提升效果明显。
因此,文章着重介绍了如何使用冰晶石熔体溶解氧化铝、电磁分离技术处理电解铝液当中的氧化铝以及如何电解氧化铝。
1 冰晶石熔体溶解氧化铝杂质在传统长流程的铝制品生产中,因为初步生产出的铝制品当中含有大量的杂质,不仅是氧化铝,还有很多其他杂质。
因此,在进行氧化铝分解之前,需要对于其中其他杂质进行初步的清理。
在实际清理的过程当中需要有效依赖于冰晶石熔体,在该熔体当中,存在这二氧化碳等物质,能够与电解铝液当中存在的氢化物等杂质进行反应,形成固体,以过滤的形式将其分离。
原铝中杂质Fe_的控制及净化方法

作者简介:彭宇(1995-),男,河北唐山人,硕士,主要从事铝电解工艺研究。
收稿日期:2023-01-29原铝中杂质Fe 的控制及净化方法彭宇1,2,程鸿鹏3,郭丰佳2(1.山东南山铝业股份有限公司国家铝合金压力加工工程技术研究中心,龙口265713;2.山东南山科学技术研究院有限公司有色金属产业研究院,龙口265713;3.山东南山铝业股份有限公司电解铝公司,龙口265713)摘要:铝的纯度是衡量铝用途的一项重要指标,而电解铝工业生产的铝液常含有一些杂质元素,如Fe 、Si 、V 。
其中原铝中含量最多的杂质元素是Fe 。
本文介绍了原铝中杂质Fe 的来源,研究和讨论了原铝中杂质Fe 的控制及铝熔体中杂质Fe 去除方法,其中偏析法具有低能耗、环保的特点,是原铝净化提纯的发展方向。
关键词:铝电解;杂质;偏析;铝熔体中图分类号:TF821,TG146.21文献标识码:A文章编号:1005-4898(2023)05-0003-06doi:10.3969/j.issn.1005-4898.2023.05.010前言铝是一种最常见的轻量化金属,具有密度小、比强度高和耐腐蚀等优点,被广泛应用于交通运输、电子和石油化工等诸多领域,被工业界誉为万能金属[1-3]。
2020年全世界的原铝总量65267kt ,中国原铝产量约为世界总量的57.2%[4]。
2021年,我国电解铝、铝材产量分别为38500kt 、61050kt ,但其用途更集中于中低端产品。
为缓解铝加工行业低端产品产能过剩的现状,我国大力推动铝行业向高附加值领域转型,而应用在航空、航天、汽车及船舶等行业的高端铝产品对原铝纯度控制有严格要求[5-6]。
铝的纯度是衡量铝用途的一项重要指标。
纯度越高,铝的物理化学性能越优异。
而电解铝工业生产的铝液由于其工艺本身的特点,常含有一些杂质[7-8],如Fe 、Si 、V 。
其中的杂质元素可能导致原铝材结构中出现诸多的“孔洞”缺陷,为外界物质破坏铝结构提供更加便捷的“入侵通道”,从而严重影响原铝合金的抗蚀能力、导电性、白光和反射性等[9-10]。
铝灰处理设备工艺流程

铝灰处理设备工艺流程一、引言铝灰处理设备是用于处理铝渣、铝灰等废料的专业设备,其工艺流程是指将废弃的铝渣、铝灰进行预处理、熔炼、冷却等一系列工序,最终得到铝合金或铝材料的过程。
本文将详细介绍铝灰处理设备的工艺流程。
二、铝灰预处理铝灰预处理是铝灰处理的第一步,主要是对废弃的铝渣、铝灰进行清洗、筛分和破碎等处理。
首先,将废弃的铝渣、铝灰进行清洗,去除其中的杂质和污染物。
然后,进行筛分,分离出不同粒度的铝渣、铝灰。
最后,对铝渣、铝灰进行破碎,使其粒度更加均匀。
三、铝灰熔炼铝灰熔炼是铝灰处理的核心步骤,通过高温将铝渣、铝灰熔化,得到铝液。
首先,将预处理后的铝渣、铝灰放入熔炉中,加入适量的熔剂,如纯碳或氢化铝等,以提高熔化效率。
然后,通过电阻加热或火焰加热等方式,使炉内温度升至铝的熔点,使铝渣、铝灰熔化成为铝液。
在熔炼过程中,需注意控制炉内的温度和熔炼时间,以确保铝液的质量和纯度。
四、铝液净化铝液净化是指对铝液进行脱气、脱渣和脱杂等处理,以提高铝液的纯度和质量。
脱气通常通过加入氩气或真空条件下进行,以去除铝液中的氧气和其他气体。
脱渣则是通过加入脱渣剂,如氟化钠或氟化铝等,使铝液中的杂质和氧化物凝聚成团,然后通过过滤等方式将其去除。
脱杂是通过加入脱杂剂,如氯化钠或氯化铝等,使铝液中的杂质和夹杂物与脱杂剂发生反应,形成易于分离的化合物,然后通过过滤或离心等方式将其分离。
五、铝液成型铝液成型是将净化后的铝液进行成型、冷却和固化等工序,得到铝合金或铝材料的过程。
成型通常采用铸造或挤压等方式,将铝液注入铸型或模具中,使其形成所需的形状和尺寸。
冷却是指将铝液在成型过程中进行冷却,使其固化成为铝合金或铝材料。
固化是指通过自然冷却或加热处理等方式,使铝合金或铝材料的结构稳定,获得所需的力学性能和物理性能。
六、铝材处理铝材处理是对铝合金或铝材料进行热处理、表面处理和加工等工序,以进一步提高其性能和质量。
热处理通常包括时效处理、固溶处理和淬火处理等,通过控制铝材的温度和时间,改变其晶体结构和组织,提高其强度和硬度等性能。
- 1、下载文档前请自行甄别文档内容的完整性,平台不提供额外的编辑、内容补充、找答案等附加服务。
- 2、"仅部分预览"的文档,不可在线预览部分如存在完整性等问题,可反馈申请退款(可完整预览的文档不适用该条件!)。
- 3、如文档侵犯您的权益,请联系客服反馈,我们会尽快为您处理(人工客服工作时间:9:00-18:30)。
铝及铝合金对熔体净化的要求,根据材料用途不一样而 有所不同,一般来说,对于一般要求的制品,其氢含量宜
控制在0.15-0.2mL/(100gAl)以下,非金属夹杂的单个颗粒 应小于10 μm ;而对于特殊要求的航空材料,双零箔等氢 含量应控制在0.1mL/(100gAl)以下,非金属夹杂的单个颗 粒应小于5μm 。当然由于检测方法的不同,所测氢含量值 会有所差异。非金属夹杂一般通过铸锭低倍和铝材超声波 探伤定性检测,或测渣仪定量检测。碱金属钠一般应控制 在5*10-4%以下。
第三节:铝及铝合金熔体净化原理
3.1. 脱气原理 脱气的主要方法有三种,分别是分压脱气、预凝固 脱气和振动脱气。 3.1.1.分压脱气原理 利用气体分压对熔体中气体溶解度影响的原理,控 制气相中氢的分压,造成与熔体中溶解气体平衡的氢分 压和实际气体的氢分压间存在很大的分压差,这就产生 来了较大的脱氢驱动力,使氢很快的排除。 如向熔体中通入纯净的惰性气体,或将熔体置于真 空中,因为最初惰性气体和真空中氢的分压PH2≈0,而熔 体中溶解氢的平衡分压PH2远大于0,在熔体与惰性气体 的气泡间及熔体与真空之间,存在较大的分压差,
其中σ金﹣杂 ——熔融金属与杂质之间的表面张力; σ金﹣剂——熔融金属与精炼剂之间的表面张力; σ剂﹣杂—-精炼剂与杂质之间的表面张力;
因为铝液和氧化夹杂物Al2O3是相互不润湿的。即金属与 杂质之间的触角θ≧120℃,如图所示其力的平衡应有如下关系: 因σ金﹣剂为正值,故符合热力学的表面能关系,所以铝液中的 夹杂物Al2O3能自动吸附在精炼剂表面上而被除去。
3.1.3 振动脱气原理 金属液体在振动状态下凝固时,能使晶粒细化,这 是由于振动能促使金属中产生分布很广的细晶核心。实 验也表明振动也能有效的达到除气的目的,而且振动频 率越大效果越好。一般使用5000—20000Hz的频率,可使 用声波、超声波、交变电流或磁场等方法作为阵源。 振动除气的基本原理就是液体分子在极高频率的振 动下发生移位运动。在运动时,一部分分子与另一部分 的分子之间的运动是不和谐的,所以在液体内部产生无 数显微空穴都是真空的,金属液体中的气体很容易扩散到 这些空穴中去,结合形成分子态,形成气泡而上升逸出。
பைடு நூலகம்
这样熔体中的氢气就会很快的向气泡或真空中扩散,进入 气泡或真空中,复合成分子状态排除。这一过程一直进行 到气泡内氢分压与熔体中氢的平衡分压相等,即处于一种 新的平衡状态时为止,该方法是目前应用最广泛最有效的 方法。 3.1.2 预凝固脱气原理 影响金属熔体中气体溶解度的因素除气体的分压外, 就是熔体的温度。气体的溶解度随着金属温度的降低而减 小,特别在熔点温度上气体溶解度变换最大。根据这一原 理,让熔体缓慢冷却到凝固,这样就可使熔体中的大部分 气体自行扩散析出。然后再快速重熔,即可得到气体含量 较低的熔体。但要特别注意熔体的保护,防止重新吸气。
cosθ = (σ 剂﹣杂- σ
σ
金﹣剂
金﹣杂
/ σ 金﹣剂﹤0 金属液
力于研试应用先进的熔体净化新技术。铝液净化成为 铝合金极其重要的生产环节,先进的净化技术对于确 保铝合金的冶金质量,提高产品的最终使用性能具有 非常重要的意义。
铝合金在熔铸过程中易于吸气和氧化,因此在熔体中不同 程度地存在气体和各种非金属夹杂物,使铸锭产生疏松、气孔、 夹杂等缺陷,显著降低铝材的力学性能、加工性能、疲劳抗力、 抗蚀性、阳极氧化性等性能,甚至造成产品报废。此外,受原 辅材料的影响,在熔体中可能存在一些对熔体有害的其它金属, 如Na、Ca等碱及碱土金属,部分碱金属对多数铝合金的性能 有不良影响,如钠在含镁高的Al-Mg系合金中除易引起“钠脆
3.2.2 吸附除渣原理 吸附净化主要是利用精炼剂的表面作用,当气体精炼 剂或熔剂精炼剂在熔体中与氧化物夹杂相遇时,杂质被精 炼剂吸附在表面上,从而改变了杂质颗粒的物理性质,随 精炼剂一起被除去。若夹杂物能自动吸附到精炼剂上,则 根据热力学第二定律,熔体、杂质和精炼剂三者之间满足 下列关系: σ金﹣杂﹢σ金﹣剂﹥ σ剂﹣杂
性”外,还降低熔体流动性而影响合金的铸造性能。因此,在 熔铸过程中需要采取专门的工艺措施,去除铝合金中的气体、 非金属夹杂物和其它有害金属,保证产品质量。
第二节:熔体净化的定义
过去几十年,冶金工业者采用精炼的措施提高熔体 的质量,所谓精炼就是向熔体中通入氯气、惰性气体或
某种氯盐去除铝合金中的气体、夹杂物和碱金属。随着 现代科学技术的发展,出现许多新的铝合金熔体净化的 方法,这些方法的内容已经超出了精炼一词所包含的意 义,因此现代科学技术引进了熔体净化的概念。所谓熔 体净化,就是利用一定的物理化学原理和相应的工艺措 施,去除铝合金熔体中的气体、夹杂物和有害元素的过 程,它包括炉内精炼、炉外精炼及过滤等过程。
铝液净化工艺
**
**
第一节
概述
随着铝合金在航空航天、导弹、汽车工业等行业 的广泛深入的应用,对铝合金的质量要求日益严格, 除要求合格的化学成分和力学性能外,还要求有合格 的内在质量和表面质量,而传统的熔铸工艺,因其所 含气体和非金属杂质超标,不能满足这些要求。为了 减少气体和非金属杂质的影响,人们一方面对配制合 金的原材料及熔炼过程提出了严格的要求,一方面致
3.2. 除渣原理 目前主要的除渣方法有澄清除渣、吸附除渣和过滤除渣三 种方法。 3.2.1 澄清除渣原理 一般金属氧化物与金属本身之间的密度总是有差异的。如 果这种差异较大,再加上氧化物的颗粒也较大,在一定的过热 条件下,金属的悬混氧化物渣可以与金属分离,这种分离作用 也叫澄清作用。 澄清除渣对许多金属,特别是轻金属合金不是主要有效的 方法,还必须辅以其他方法。但是根据物理学的基本原理,它 仍不失为一种基本的方法。在铝合金精炼过程中,首先仍要用 这一简单的方法来将一部分固体杂质和金属分开。一般静置炉 的应用就是为了这个目的。当然静置炉的作用不仅是为澄清分 离,还有保温和控制铸造温度的作用,所以有时也称保温炉。