SPC统计制程控制程序
SPC控制程序--范本

1. 目的:
为了不断地对生产过程进行改进并满足客户对生产过程的能力要求,特规定本程序来对生产过程的稳定状态和过程能力指数进行研究,以达到生产过程预防的效果。
2. 适用范围:
适用于与汽车产品特殊特性相关的关键过程的初始过程和稳定过程的能力研究,及过程控制;
3.定义
4. 职责
4.1 品质部
1)负责SPC过程控制;
2)制定与检讨SPC的操作规格,包括样本大小,抽样频率,管制界限等。
3)负责量测、记录、判读数据,并输入控制图的对应位置,将SPC异常通知给生产部,并要求停
止生产,当SPC数据超出规格限时,需立即组织相关部门采取改善措施;
4)确认SPC异常的回复及改善结果。
5)依客户要求定期向客户提交CPK报告;
6)负责保存及维护SPC相关数据。
7)负责对SPC作业相关人员作有关SPC作业规范的培训和异常判读培训。
4.2 生产部: 配合品质部进行SPC过程控制,并对异常情况采取相对应的改善对策。
4.3 APQP小组:负责策划使用哪种SPC控制图,和控制图样品取样数和取样频次。
5. 程序内容
6. 记录
各种控制图表。
32统计技术程序(SPC)
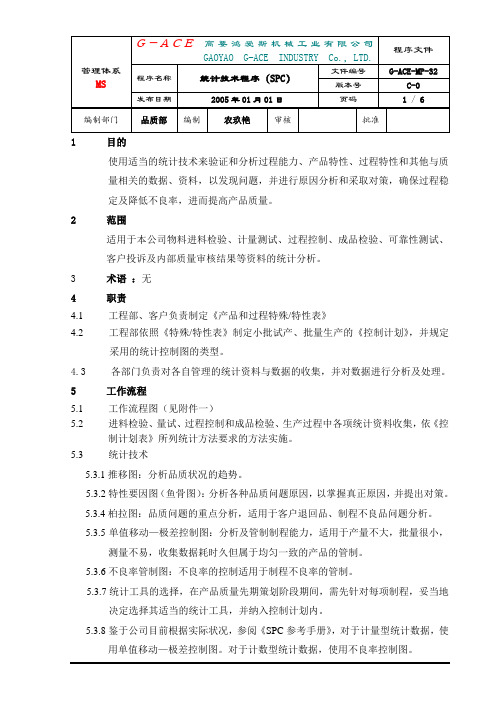
1目的使用适当的统计技术来验证和分析过程能力、产品特性、过程特性和其他与质量相关的数据、资料,以发现问题,并进行原因分析和采取对策,确保过程稳定及降低不良率,进而提高产品质量。
2范围适用于本公司物料进料检验、计量测试、过程控制、成品检验、可靠性测试、客户投诉及内部质量审核结果等资料的统计分析。
3术语:无4职责4.1 工程部、客户负责制定《产品和过程特殊/特性表》4.2 工程部依照《特殊/特性表》制定小批试产、批量生产的《控制计划》,并规定采用的统计控制图的类型。
4.3 各部门负责对各自管理的统计资料与数据的收集,并对数据进行分析及处理。
5工作流程5.1 工作流程图(见附件一)5.2 进料检验、量试、过程控制和成品检验、生产过程中各项统计资料收集,依《控制计划表》所列统计方法要求的方法实施。
5.3 统计技术5.3.1推移图:分析品质状况的趋势。
5.3.2特性要因图(鱼骨图):分析各种品质问题原因,以掌握真正原因,并提出对策。
5.3.4柏拉图:品质问题的重点分析,适用于客户退回品、制程不良品问题分析。
5.3.5单值移动—极差控制图:分析及管制制程能力,适用于产量不大,批量很小,测量不易,收集数据耗时久但属于均匀一致的产品的管制。
5.3.6不良率管制图:不良率的控制适用于制程不良率的管制。
5.3.7统计工具的选择,在产品质量先期策划阶段期间,需先针对每项制程,妥当地决定选择其适当的统计工具,并纳入控制计划内。
5.3.8鉴于公司目前根据实际状况,参阅《SPC参考手册》,对于计量型统计数据,使用单值移动—极差控制图。
对于计数型统计数据,使用不良率控制图。
5.4 单值移动—极差控制图的绘制5.4.1选取运作稳定的工序,收集质量特性值,数据收集需100个以上。
5.4.2以每4个或5个数据为一组,将数据分成20---25组(首次使用控制图选用35组数据以便调整),并从左到右记录单值到数据图上。
5.4.3 计算控制限x= (X1+X2+X3+….+Xn)/nR=(MR1+ MR2+ MR3+….+ MR n)/ n-1USL MR=D4RLSL MR=D3RUSL X=x+E2RLSL X=x-E2R5.4.4 画控制线x图画在上方, R画在下方以组号或时间为横坐标,以x值或R值为纵坐标在图上描出各点,并将各点用折线连线。
SPC(质量管理与控制)

1.在质量诊断方面,可以用来度量过程的稳定性,即过程是否处于统计控制状态; 2.在质量控制方面,可以用来确定什么时候需要对过程加以调整,而什么时候则需使过程保持相应的稳定状态; 3.在质量改进方面,可以用来确认某过程是否得到了改进。 应用步骤如下: 1.选择控制图拟控制的质量特性,如重量、不合格品数等; 2.选用合适的控制图种类; 3.确定样本容量和抽样间隔; 4.收集并记录至少20~ 25个样本的数据,或使用以前所记录的数据; 5.计算各个样本的统计量,如样本平均值、样本极差、样本标准差等; 6.计算各统计量的控制界限; 7.画控制图并标出各样本的统计量; 8.研究在控制线以外的点子和在控制线内排列有缺陷的点子以及标明异常(特殊)原因的状态; 9.决定下一步的行动。 应用控制图的常见错误: 1.在5M1E因素未加控制、工序处于不稳定状态时就使用控制图管理工作; 2.在工序能力不足时,即在CP< 1的情况下,就使用控制图管理工作; 3.用公差线代替控制线,或用压缩的公差线代替控制线; 4.仅打“点”而不做分析判断,失去控制图的报警作用; 5.不及时打“点”,因而不能及时发现工序异常; 6.当“5M1E”发生变化时,未及时调整控制线; 7.画法不规范或不完整; 8.在研究分析控制图时,对已弄清有异常原因的异常点,在原因消除后,未剔除异常点数据。
1) 异常变动
过程中变动因素是不在统计管理状态下的非随机性原因,由于异常因素不是过程所固有,固不难除去,一般情况现场人员对异常因素的消除可以自行决定采取措施,而不必要请示更高级的管理人员,所以也称之为减少变动的局部措施。
2)偶然变动
过程中的变动因素是统计管理的状态下,其产品的特性有固定的分布,即分布位置、分布及分布形状三种,由于偶然因素是过程所固有的,难于消除,要消除偶然因素必须涉及到人、机、料、法、环境等整个系统的改造问题,需要投入大量的资金,故不是现场人员所能决定的,而必须经过深入的调查研究和做出全面的可行性报告后,再经高层领导做最后的定夺,所以称之为减少变动的系统措施。 特殊原因 一种间断性的,不可预计的,不稳定的变差来源。有时被称为可查明原因,存在它的信号是:存在超过控制线的点或存在在控制线之内的链或其他非随机性的情形。 普通原因 造成变差的一个原因,它影响被研究过程输出的所有单值;在控制图分析中,它表现为随机过程变差的一部分。 合理使用控制图的益处 ? 供正在进行过程控制的操作者使用 ? 有助于过程在质量上和成本上能持续的、可预测的保持下去 ? 使过程达到: ? 更高的质量 ? 更低的单件成本 ? 更高的有效能力 ? 为讨论过程的性能提供共同的语言 ? 区分变差的特殊原因和普通原因,作为采取局部措施或对系统采取措施的指南 在实际应用中,当各组容量与其平均值相差不超过正负25%时,可用平均样本容量( )来计算控制限. 在什么条件下分析阶段确定的控制限可以转入控制阶段使用: ? 控制图是受控的 ? 过程能力能够满足生产要求 控制图是根据稳定状态下的条件(人员、设备、原材料、工艺方法、测量系统、环境)来制定的。如果上述条件变化,则必须重新计算控制限,例如: ? 操作人员经过培训,操作水平显著提高; ? 设备更新、经过修理、更换零件; ? 改变工艺参数或采用新工艺; ? 改变测量方法或测量仪器; ? 采用新型原材料或其他原材料; ? 环境变化。 使用一段时间后检验控制图还是否适用,控制限是否过宽或过窄,否则需要重新收集数据计算控制限; 过程能力值有大的变化时,需要重新收集数据计算控制限。 对于p,np图, 过程能力是通过过程平均不合格品率 来表示,当所有点都受控后才计算该值. 当Cpk指数值降低代表要增加: ? 控制 ? 检查 ? 返工及报废, 在这种情况下,成本会增加,品质也会降低, 生产能力可能不足。 当Cpk指数值增大,不良品减少,最重要是产品/零件接近我们的“理想设计数值/目标”,给予顾客最大满足感。 当Cpk指数值开始到达1.33或更高时对检验工作可以减少,减少我们对运作审查成本。 ? 普通原因变差 ? 影响过程中每个单位 ? 在控制图上表现为随机性 ? 没有明确的图案 ? 但遵循一个分布 ? 是由所有不可分派的小变差源组成 ? 通常需要采取系统措施来减小 ? 特殊原因变差 ? 间断的,偶然的,通常是不可预测的和不稳定的变差 ? 在控制图上表现为超出控制限的点或链或趋势 ? 非随机的图案 ? 是由可分派的变差源造成该变差源可以被纠正 ? 工业经验建议为: ? 只有过程变差的15%是特殊的可以通过与操作直接有关的人员纠正 ? 大部分 (其余的85%) 是管理人员通过对系统采取措施可纠正的 ? 控制图可以区分出普通原因变差和特殊原因变差 ? 特殊原因变差要求立即采取措施 ? 减少普通原因变差需要改变产品或过程的设计 控制图 - 过程的声音 ? 试图通过持续调整过程参数来固定住普通原因变差,称为过度调整,结果会导致更大的过程变差造成客户满意度下降 ? 试图通过改变设计来减小特殊原因变差可能解决不了问题,会造成时间和金钱的浪费 ? 控制图可以给我们提供出出现了哪种类型的变差的线索,供我们采取相应的措施 ? 能力指数的计算基于以下假设条件: ? 过程处于统计稳定状态 ? 每个测量单值遵循正态分布 ? 规格的上、下限是基于客户的要求 ? 测量系统能力充分 ? 如果理解关满足了这些假设后,能力指数的数值越大,潜在的客户满意度越高 过程能力分析的用途 -设计部门可参考目前之制程能力,以设计出可制 造的产品 -评估人员、设备、材料与工作方法的适当性 -根据规格公差设定设备的管制界限 -决定最经济的作业方式 过程控制和过程能力 ◎目标:过程控制系统目标,是对影响过程的措 施作出经济合理的决定, 避免过度控制 与控制不足 ◎过程能力讨论:必需注意二个观念 ○由造成变差的普通原因来确定 ○内外部顾客开心过程的输出及与他 们的要求的关系如何。 SPC就是利用统计方法去: 1.分析过程的输出并指出其特性. 2.使过程在统计控制情况下成功地进行和维持. 3.有系统地减少该过程主要输出特性的变异. 统计制程管制 (SPC) 它可用统计管制图及时监督与控制线场作业 . . 它可用统计计算制程能力及规格 . . 它可防止制程的偏差去影响产品的良率与品质 / 可靠性. . 它可消除非机率原因的变异来改善制程. SPC 就是依据 统计 的逻辑 来判断 制程 是否正常 及应否采取改善对策的一套 控制系统 ? 对的问题比对的答案更重要
spc统计制程管制(SPC)

6
變異的來源
機遇原因
來自於潛在的自然變異 消除它們的成本很昂貴
可歸屬原因
反應製程的不穩定 統計製程管制最主要的目的就是要快速的偵測出 製程中的可歸屬原因或是偏移的發生
7
管制圖
為一種特殊的趨勢圖,它可以表現出產品特 性的變化情形
管制圖由三部份組成---管制界限(control limit)、中心線(center line)與樣本點
p Chart ; Mean:.168000 Sigma:.037387 n:100
.280160
.168000
12
4
6
8
妓セ絪腹
.055840 10
ぃ▆计
24
建立管制圖的步驟
步驟一:選擇品質特性 步驟二:選取合理樣本 步驟三:蒐集數據 步驟四:決定試用管制界限 步驟五:建立修正後的管制界限 步驟六:管制圖延續使用
分為計數值管制圖與計量值管制圖兩種類型。
8
管制圖的例子
妓セ翴 恨
いみ絬 恨
恨
1
5
10
15
20
25
妓セ
9
計數值管制圖
優點
計算簡單
能夠同時對不同的品質特性做整體性的控 制
種類
p管制圖 np管制圖 c管制圖 u管制圖
10
p 管制圖
ぃ▆瞯
0.07 0.06 0.05 0.04 0.03 0.02 0.01 0.00
說
明
中抽取 n 個產品,而發 現不良品個數為 x 的機
良焊點數 x 出現的機率 將會服從卜瓦松分配的
鐘,最主要的特徵是大 多數的數據會集中在平
率將會服從二項分配的 形態。
均數附近,而極大與及
SPC控制管理规定
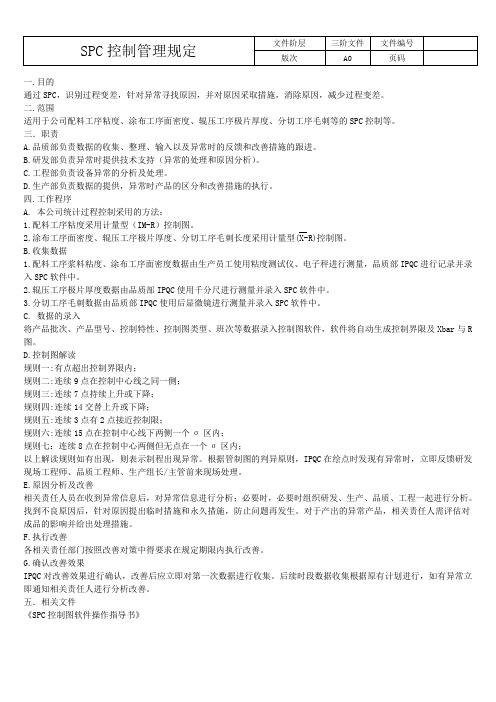
一.目的通过SPC,识别过程变差,针对异常寻找原因,并对原因采取措施,消除原因,减少过程变差。
二.范围适用于公司配料工序粘度、涂布工序面密度、辊压工序极片厚度、分切工序毛刺等的SPC控制等。
三.职责A.品质部负责数据的收集、整理、输入以及异常时的反馈和改善措施的跟进。
B.研发部负责异常时提供技术支持(异常的处理和原因分析)。
C.工程部负责设备异常的分析及处理。
D.生产部负责数据的提供,异常时产品的区分和改善措施的执行。
四.工作程序A. 本公司统计过程控制采用的方法:1.配料工序粘度采用计量型(IM-R)控制图。
2.涂布工序面密度、辊压工序极片厚度、分切工序毛刺长度采用计量型(X-R)控制图。
B.收集数据1.配料工序浆料粘度、涂布工序面密度数据由生产员工使用粘度测试仪、电子秤进行测量,品质部IPQC进行记录并录入SPC软件中。
2.辊压工序极片厚度数据由品质部IPQC使用千分尺进行测量并录入SPC软件中。
3.分切工序毛刺数据由品质部IPQC使用后显微镜进行测量并录入SPC软件中。
C. 数据的录入将产品批次、产品型号、控制特性、控制图类型、班次等数据录入控制图软件,软件将自动生成控制界限及Xbar与R 图。
D.控制图解读规则一:有点超出控制界限内;规则二:连续9点在控制中心线之同一侧;规则三:连续7点持续上升或下降;规则四:连续14交替上升或下降;规则五:连续3点有2点接近控制限;规则六:连续15点在控制中心线下两侧一个σ区内;规则七:连续8点在控制中心两侧但无点在一个σ区内;以上解读规则如有出现,则表示制程出现异常。
根据管制图的判异原则,IPQC在绘点时发现有异常时,立即反馈研发现场工程师、品质工程师、生产组长/主管前来现场处理。
E.原因分析及改善相关责任人员在收到异常信息后,对异常信息进行分析;必要时,必要时组织研发、生产、品质、工程一起进行分析。
找到不良原因后,针对原因提出临时措施和永久措施,防止问题再发生。
FQ-TS-SPC-005制程控制统计分析程序
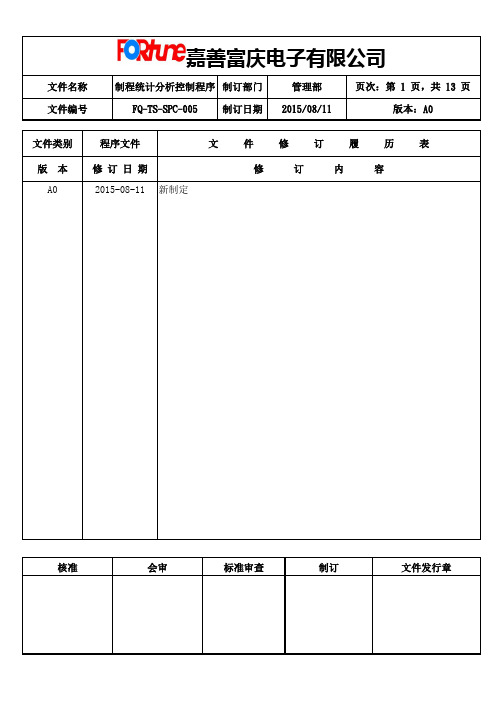
制程统计分析控制程序制程统计分析控制程序1 目的为了解和改善过程,通过对过程能力的分析/评估使其有量化资料,为设计、制造过程的改进,选择材料,操作人员及作业方法,提供依据和参考。
2 范围本程序适用于富庆有限公司顾客要求和需做统计过程控制(PP K、CPK、CmK 、PPM)的所有产品。
3 引用文件《文件和资料控制程序》《开发设计管理程序》《过程控制程序》《失效模式及后果分析程序》《质量管理体系程序》《控制计划管理程序》《质量记录控制程序》《生产件批准程序》4 术语和定义SPC:指统计过程控制。
CpK:稳定过程的能力指数。
它是一项有关过程的指数,计算时需同时考虑过程数的趋势及该趋势接近于规格界限的程度。
PpK:初期过程的能力指数。
它是一项类似于CPK的指数,但计算时是以新产品的初期过程性能研究所得的数据为基础。
Ca:过程准确度。
指从生产过程中所获得的资料,其实际平均值与规格中心值之间偏差的程度。
Cp:过程精密度。
指从生产过程中全数抽样或随机抽样(一般样本在50个以上)所计算出来的样本标准差(σ×),以推定实际群体的标准差(σ)用3个标准差(3σ)与规格容许差比较。
PPM:质量水准,即每百万个零件不合格数。
指一种根据实际的缺陷材料来反映过程能力的一种方法。
PPM数据常用来优先制定纠正措施。
Cmk:设备能力指数:是反映机械设备在受控条件下,当其人/料/法不变时的生产能力大小。
5 职责品质部负责统计过程控制的监督、管理工作。
制程统计分析控制程序工程部门、生产部门、品质部门负责统计过程控制的数据搜集和分析。
6 工作流程和内容制程统计分析控制程序制程统计分析控制程序制程统计分析控制程序7 附件附件一: PPM、Cp、Cpk、Pp、Ppk过程能力计算及评价方法附件二:控制图的判定方法附件三:抽样检验作业指导书附件四:机械和工装设备能力计算作业规范附件一:PPM、Cp、Cpk、Pp、Ppk过程能力计算及评价方法1.质量水准PPM的过程能力计算及评值方法:当产品和/或过程特性的数据为计数值时,制造过程能力的计算及等级评价方法如下:(1)计算公式:不良品数PPM = × 1000000检验总数(2)等级评价及处理方法:制程统计分析控制程序2.稳定过程的能力指数Cp、Cpk计算及评价方法:(1)计算公式:A)Ca = (x-U) / (T / 2)×100%注: U = 规格中心值T = 公差 = SU - SL = 规格上限值–规格下限值σ= 产品和/或过程特性之数据分配的群体标准差的估计值x = 产品和/或过程特性之数据分配的平均值B)Cp = T / 6σ(当产品和/或过程特性为双边规格时)或CPU(上稳定过程的能力指数)= (SU-x)/ 3σ(当产品和/或过程特性为单边规格时)CPL(下稳定过程的能力指数)= (x-SL)/ 3σ(当产品和/或过程特性为单边规格时)Z1 = 3Cp(1+Ca)……根据Z1数值查常(正)态分配表得P1%;Z2 = 3Cp(1-Ca)……根据Z2数值查常(正)态分配表得P2%不合格率P% = P1% + P2%注:σ = R / d2( R 为全距之平均值,d2为系数,与抽样的样本大小n有关,当n = 4时,d2=2.059;当n = 5时,d2= 2.3267)C)Cpk = (1-∣Ca∣)× Cp当Ca = 0时,Cpk = Cp。
SPC管理控制程序
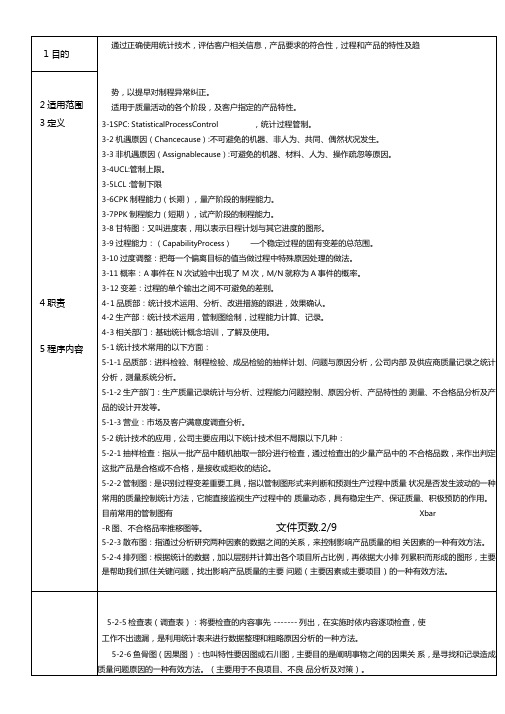
---计算管制界限UCLR LCLR UCLXbar LCLXbarUC.=D4 RLCL R=D3 RUCL X=X+A RLCL X=X-A2R---画管制界限于管制图上⑷.R管制图分析:---超出管制界限点,需分析异常;---趋势:7点于平均值一边,或连续7点持续升高或降低,需分析异常;---非随机分布点:2/3点分布于一标准差区域,其余1/3点分布于2到3标准差区域,需分析异常;---发现异常及分析原因,可使用排列图及鱼骨图分析异常原因;---重新计算管制界限•将超出管制界限之点去除后,重新计算管制界限。
(5).Xbar管制图分析:---超出管制界限点,需分析异常;---趋势:7点于平均值一边,或连续7点持续升高或降低,需分析异常;---非随机分布点:2/3点分布于一标准差区域,其余1/3点分布于2到3标准差区域,需分析异常;---发现异常及分析原因,可使用柏拉图及鱼骨图分析异常原因;---重新计算管制界限.将超出管制界限之点去除后,重新计算管制界限。
(6).重新制定量产管制界限=R/d 2R new= d2UCL R=D4 R newLCL R=D3 R neW-CL R=D3 R new(2).组数至少25组以上。
(3).计算每一组的不良品数(np),并记录于“ CONTROLCHARTFORATTRIBUTEDA检验报告内)。
(4).将每一数值画于p管制图上。
(5).计算制程平均不良品比率。
n?P2 …“K P Kp = n2... n K(6).计算UCL及LCLo(7).将Pbar画实线,UCL及LCL画虚线于p管制图上。
消除其影响。
监控可以充分体现出SPC预防控制的作用。
5-5SPC作业流程5-5-1决定管制项目(1).对客户明确要求的管制项目,生产制造过程中必须进行管控。
(2).由品质部、生产部门、营业课共同识别过程关键参数,选择管制项目5-5-2决定管制标准(1).客户明确要求的管制标准,生产制造过程中必须达到。
SPC规则及操作程序

SPC规则及操作程序第 001 版文件编号:发布日期: 2007 年 6 月 27 日实施日期: 2007 年 6 月 27 日目录 (03)1. 目的 (04)2. 适用范围 (04)3. 名词解释 (04)4. 成员及职责 (04)5. SPC control scope ……………………………………………………………………056. SPC chart naming rule (05)7. SPC committee and review procedure………………………………………………051. 目的规范公司SPC system基本设置和操作规则。
2. 适用范围公司所有已经release的flow,产品,机台的inline monitor, offline monitor 以及产品WAT monitor所做的统计过程控制。
3. 名词解释SPC: Statistical Process Control,即统计制程管控。
Module PE: 技术部门制程工程师,包括薄膜,光刻,刻蚀,扩散的制程工程师。
Module EE: 设备部门设备工程师,包括薄膜,光刻,刻蚀,扩散的制程工程师。
PIE:技术部门工艺整合工程师。
QE:质量部门质量工程师YE:技术部门良率工程师PDE:产品工程师SPC Committee: 负责review SPC performance的委员会,由QE, PIE, PDE,YE, Module PE/EE组成。
4.成员及职责委员会主席:质量部部长。
委员会委员:PIE,QE,Module PE的课长(含)以上级别。
QE:SPC committee coordinator,参与SPC review。
负责监控SPC chart,定期summary 需要review的SPC chart作为SPC committee review的材料,负责召开SPC 例行会议,汇报某时间段的FAB SPC performance,对不符合要求的SPC chart进行highlight,协助调查root cause, 并监督committee得出的相关action的执行。
- 1、下载文档前请自行甄别文档内容的完整性,平台不提供额外的编辑、内容补充、找答案等附加服务。
- 2、"仅部分预览"的文档,不可在线预览部分如存在完整性等问题,可反馈申请退款(可完整预览的文档不适用该条件!)。
- 3、如文档侵犯您的权益,请联系客服反馈,我们会尽快为您处理(人工客服工作时间:9:00-18:30)。
文件类别 文件名称 版次
程序文件 统计制程控制程序
2.0
核 准 审 核 制 作 持有单位 发行章
表单编号:00040001-01
2
文件修订履历表
发布日期
制
定、修
发行 发行 修订 修订 版次 页次 版次 页次
订
记
录
修订内容重点
表单编号:00040002-01
1、 目的 规定有关统计过程控制及过程能力分析的方法。
统计制程控制程序
4.4 技术部监督并验证过程纠正预防措施的实施。 4.5 正常生产过程中,确保每半年对关键、重要特性(可收集计量型数据的)进行一次 Cpk
值研究。当顾客有特殊要求时,执行顾客要求。 5、工作内容及控制方法
5.1 设备能力的测算 5.1.1 确定所研究的对象分析和加工零件的待测特性及规范公差,测量方法和测量工具。 5.1.2 样本数:最小样本为 50 件。 5.1.3 研究时机:新零件、新设备/模具、公差带压缩、设备大修、设备更新、机器搬迁、 长期停产等。 5.1.4 采集样本的时机 在做完测量系统分析并合格后,按规定的样本数连续采集数据并记录。 5.1.5 计算公式 X =∑Xi/n S= ∑(Xi-X)2 (n-1) Cm=(USL-LSL)/6S Cmk=min{(USL-X)/3S,(X-LSL)/3S } S——过程变差的平方根 n——采集的样本数 Xi——样本的测量值 X——样本的平均值 USL——公差的上限 LSL——公差的下限 5.1.6 设备能力的评价
年计算一次。
5.2.12.3 过程能力测算由技术部保存,期限三年。初始过程能力测算表提交先期质量策划小
组。
6、形成文件和记录
控制图
表单编号:00040004-01
0.67<Cpk≤1.00
三级
1.分析产生不足的原因,采取措施加以改进; 不足
2.加强检验,实行全数检验或考虑放宽标准范围。
Cpk<0.67
四级
严重 1.停止加工,立即追查原因; 不足 2.采取措施,实行全数检验加以筛选。
5.2.12.1 评价过程能力:(批量生产阶段进行)
5.2.12.2 初始过程能力只在过程刚刚建立或改变时分析计算,批量生产产品过程能力每半
5.2.11 生产现场品检人员制作控制用控制图:
5.2.11.1 将初始过程满足质量要求所到的控制中心线与上、下控制限画在控制图上。
5.2.11.2 按初始过程能力研究确定的子组大小收集样本,记录过程事件。
5.2.11.3 计算每组样本的均制和极差,并在控制图上描点。
5.2.11.4 分析控制图上的点是否随机分布(方法同 5.1.8)
5.2.8 分析控制图是否随即分布:
a. 点:出现超出控制线的点;
b. 链:产生连续七点上升/下降/在平均值的一侧的点;
c. 明显的非随机图形:显著多于(或少于)2/3 的点落在离均值很近之处。
表单编号:00040004-01
统计制程控制程序
若有上述非随机分布现象,则:
①去除非随机点,Байду номын сангаас新计算控制界限,再次分析控制图;
②如需采取纠正措施,改进过程,则应在纠正措施实施有效后重新收集数据,制作控制图
并重新进行分析。
5.2.9 计算初始过程能力指数:(试生产阶段进行或过程改变)
Pp=(USL-LSL)/6σs 式中:USL:规范的公差上限
LSL:规范的公差下限
σs:总体样本标准差 在过程有偏移的情况下
Ppk=min{(USL-X)/3σs s , (X-LSL)/3σs s }
>1.67
特级
1.可以考虑放宽对特性波动的控制 理想
2.收缩标准范围,提高质量要求
1.33<Cpk≤1.67
一级
1.关键特性不变,非关键特性可降低对波动的限制; 正常
2.简化检验,换全检为抽检或减少抽检频次。
1.00<Cpk≤1.33
二级
略显 不足
1.当为 1.33 时,处于正常状态; 2.当接近 1 时,应加强管理; 3.一般不能简化检验。
5.2.12 计算过程能力指数
Cp=(USL-LSL)/ 6σR/d2 Cpk=min{(USL-X)/ 3σR/d2 ,(X-LSL)/ 3σR/d2} 其中σR/d2= R /d2 ,式中 d2 根据子组容量查表得出
表单编号:00040004-01
统计制程控制程序
Cpk
过程等级 评价 处理原则
2、 使用范围 本规定适用于设备能力、初始过程能力和长期过程能力的研究。
3、 术语 3.1 变差:也称波动,指同一过程输出个体间的差异。 3.2 初始过程能力:是过程总变差的总范围(6σs)。 3.3 过程能力:某一稳定过程固有变差的总范围(6σR/d2)。 3.4 初始过程能力指数:不考虑过程有无偏移,定义为容差宽度除以过程能力,用以评价生 产过程准备情况。 3.5 过程能力指数:不考虑过程有无偏移,定义为容差宽度除以过程能力,用以评价某一稳 定过程的输出同规范要求(顾客要求)的关系。 3.6 Cmk(设备能力指数):衡量所使用的设备是否满足零件加工精度的要求的定量化指标。 3.7 统计过程控制:适用诸如控制图等统计技术来分析过程或其输出,以便采取适当的措施 来达到并保持统计控制状态,从而提高过程能力。 3.8 控制图:用来表示一个过程特性的图像,图上标有根据那个特性收集到的一些统计数据, 一条中心线,一条或两条控制限。它能减少Ⅰ类或Ⅱ类错误的净经济损失。它有两个基 本的用途:一是用来判定一个过程是否一直受统计控制;二是用来监控过程保持受控状 态。 控制图可分为计量型和计数型两大类。计量型的过程表现为得到的质量特性为可度量 的数值(如直径、长度等),计数型表现为只有两个数值(如合格/不合格,成功/失败…), 但他们可以被计数从而用来记录和分析。
σs=
n
∑(Xi- X)2/ ( n – 1 )
I=1
5.2.10 评价初始过程能力指数
Ppk≥1.67:满足要求,可以进入批量生产阶段。
Ppk<1.67:初始能力需改进
①减少特殊原因引起的变差,将过程均值调整到接近目标值。
②减少特殊原因引起的变差,减少单个过程特性值的变差。
③改变规范使之与过程能力一致。
Cmk≥1.67,设备有满足质量指标的加工能力,可使用于指定生产; Cmk<1.67,设备能力不足,应对该设备加工的所有零件进行 100%检验,并对设备进行检修,
检修后重新进行 Cmk 研究。 5.1.7 保存 设备能力测算表由生产部负责保存,期限长期。
表单编号:00040004-01
统计制程控制程序
k
R
=
∑
i=1
Ri式/K中:k:子组数
k
X
=
∑
i=1
Xi
/K
Ri:每一个子组的极差
Xi:每一个子组的均值 5.2.6 计算控制限
UCLr= D4R LCLr=D3 R UCLx=X + A2 R LCLx= X -A2 R
式中 A2,D3,D4 根据子组容量表查得出
5.2.7 按计算结果在均值图和极差图中画出控制限。
5.2 过程性能及过程能力研究 5.2.1 制定“Ppk、Cpk 计划” 5.2.2 绘制分析用控制图(X-R 图为例) 5.2.2.1 收集数据并记录在控制图上,同时与控制图下面记录过程相关事件。 5.2.2.2 计算每一子组的均值和极差,并记录在控制图上。
X=∑Xi/n , R=Xmax-Xmin n:子组中样品数量 Xi:子组中每一样品测量值 Xmax:子组中最大样品测量值 Xmin:子组中最小样品测量值 5.2.3 选定控制图的刻度 5.2.4 按平均值和极差值在控制图上描出对应点。 5.2.5 计算极差均值和过程均值 X,并按均值在控制图上画出中心线。
4、职责 4.1 新产品试制阶段,由产品质量先期策划小组依据产品/过程特殊特性,制定设备能力、 初始过程能力研究计划,并组织实施。
4.2 批量生产阶段,由技术部技术人员负责制定计划(或依特殊情况),收集数据及计算,并 正确评价。
4.3 若统计过程不受控,相关职能部门应制定过程纠正预防措施并实施。
表单编号:00040001-01