双工位钻孔攻丝组合机床地PLC改造设计
基于PLC的钻孔组合机床控制系统设计

基于PLC的钻孔组合机床控制系统设计摘要:钻孔组合机床是一种常用的加工设备,其控制系统对于机床的工作效率和加工质量有着重要的影响。
本文基于PLC(可编程逻辑控制器)技术,设计了一种钻孔组合机床控制系统,并对系统进行了仿真和实验验证。
实验结果表明,该控制系统能够稳定可靠地控制钻孔组合机床的工作,并且具有较高的精度和效率。
关键词:PLC;钻孔组合机床;控制系统;仿真;实验验证一、引言钻孔组合机床是一种常用的加工设备,广泛应用于各行各业。
传统的钻孔组合机床控制系统多采用电磁继电器和电路控制的方式,具有控制精度低、可靠性差等缺点。
而PLC技术具有编程灵活、控制精度高、可靠性好等优点,因此在钻孔组合机床控制系统中得到了广泛应用。
本文基于PLC技术,设计了一种钻孔组合机床控制系统,并对系统进行了仿真和实验验证。
二、PLC钻孔组合机床控制系统的设计1.控制系统硬件设计PLC钻孔组合机床控制系统的硬件部分包括PLC主控模块、人机界面模块、执行机构模块等。
PLC主控模块实现对整个控制系统各部分的控制指令的解码和执行;人机界面模块为操作员提供了直观的控制界面;执行机构模块负责实际的加工操作。
2.控制系统软件设计PLC钻孔组合机床控制系统的软件部分主要包括控制程序的编写和参数设置。
控制程序的编写是整个软件设计的核心,包括自动控制程序、手动控制程序、故障检测程序等。
参数设置是根据具体的机床和工件进行的,包括钻孔深度、钻孔速度等参数的设置。
三、PLC钻孔组合机床控制系统的仿真为了验证设计的控制系统的正确性和可行性,本文进行了系统的仿真。
仿真结果表明,控制系统能够稳定可靠地控制钻孔组合机床的工作,并且具有较高的精度和效率。
四、PLC钻孔组合机床控制系统的实验验证根据仿真结果,设计了实验验证方案,并进行了实验。
实验结果表明,控制系统能够稳定可靠地控制钻孔组合机床的工作,实现了钻孔深度和钻孔速度的准确控制。
五、总结通过本文的研究,基于PLC的钻孔组合机床控制系统设计得到了较好的结果。
双面二工位铣钻组合机床PLC与组态控制系统设计毕业设计(论文)
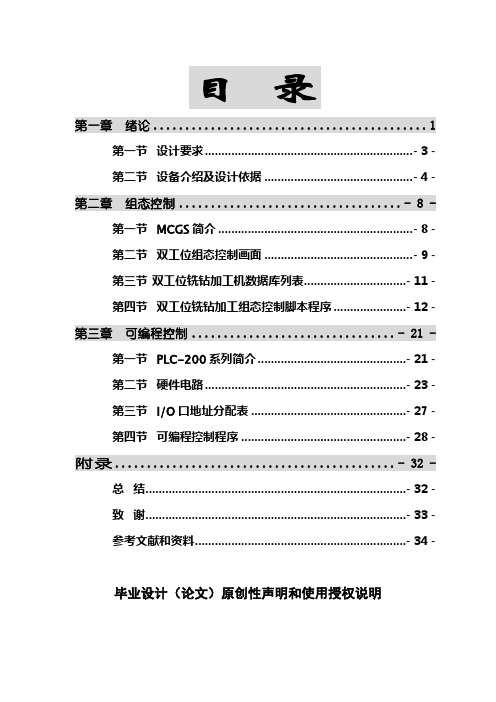
目录第一章绪论 (1)第一节设计要求 (3)第二节设备介绍及设计依据 (4)第二章组态控制................................... - 8 -第一节MCGS简介 . (8)第二节双工位组态控制画面 (9)第三节双工位铣钻加工机数据库列表 (11)第四节双工位铣钻加工组态控制脚本程序 (12)第三章可编程控制................................ - 20 -第一节PLC-200系列简介 (20)第二节硬件电路 (22)第三节I/O口地址分配表 (26)第四节可编程控制程序 (27)附录............................................ - 31 -总结 (31)致谢 (32)参考文献和资料 (33)毕业设计(论文)原创性声明和使用授权说明原创性声明本人郑重承诺:所呈交的毕业设计(论文),是我个人在指导教师的指导下进行的研究工作及取得的成果。
尽我所知,除文中特别加以标注和致谢的地方外,不包含其他人或组织已经发表或公布过的研究成果,也不包含我为获得及其它教育机构的学位或学历而使用过的材料。
对本研究提供过帮助和做出过贡献的个人或集体,均已在文中作了明确的说明并表示了谢意。
作者签名:日期:指导教师签名:日期:使用授权说明本人完全了解大学关于收集、保存、使用毕业设计(论文)的规定,即:按照学校要求提交毕业设计(论文)的印刷本和电子版本;学校有权保存毕业设计(论文)的印刷本和电子版,并提供目录检索与阅览服务;学校可以采用影印、缩印、数字化或其它复制手段保存论文;在不以赢利为目的前提下,学校可以公布论文的部分或全部内容。
作者签名:日期:学位论文原创性声明本人郑重声明:所呈交的论文是本人在导师的指导下独立进行研究所取得的研究成果。
除了文中特别加以标注引用的内容外,本论文不包含任何其他个人或集体已经发表或撰写的成果作品。
项目3 双头钻床的PLC控制系统

项目3 双头钻床的PLC控制系统
教学目标
知识目标:
• 1.掌握选择性分支、并行分支流程程序的用法 • 2掌握设计选择性分支、并行分支流程状态转移图的 基本方法和技巧。
能力目标:
• 1.会根据实际控制要求设计PLC的外围电路 • 2. 会用状态转移图设计选择性分支、并行性分支流 程控制程序。
• 2.状态转移图 • 根据控制要求,电动机的正反转控制是一个具有 两个分支的选择性流程,分支转移的条件是正转 起动按钮Xl和反转起动按钮X2,汇合的条件是热 继电器X3或停止按钮X0,而初始状态S0可由初始 脉冲M8002来驱动。其状态转移图如图2-3-8(a) 所示。
可编程控制器应用技术
• 根据图 2-3-8(a)所示的状态转移图,其指令表如图23-8(b)所示。 LD M8002 STL S20
南北向 东西向
红灯亮30S 绿灯亮25S 绿灯闪3S 黄灯亮2S
绿灯亮25S
绿灯闪3S
黄灯亮2S
红灯亮30S
图2-3- 9交通灯自动运行的动作要求
可编程控制器应用技术
• 1.I/0分配
• 根据控制要求,分配I/O点并画出I/O接线图。其I/O分 配表如表2-3-2所示。I/O端口接线图如图2-3-10
可编程控制器应用技术
• 1.根据控制要求,分配输入输出端口,并画出 I/O接线图。I/O接线图见图2-3-14所示。
表2-9输入输出端口分配
序号 输入设备 输入点 序号 输出设备 输出 点
1
2 3 4 5 6 7
启动
工件夹紧 大钻头下限位开关 大钻头上限位开关 小钻头下限位开关 小钻头上限位开关 工件旋转到位
可编程控制器应用技术
如何用PLC改造组合机床
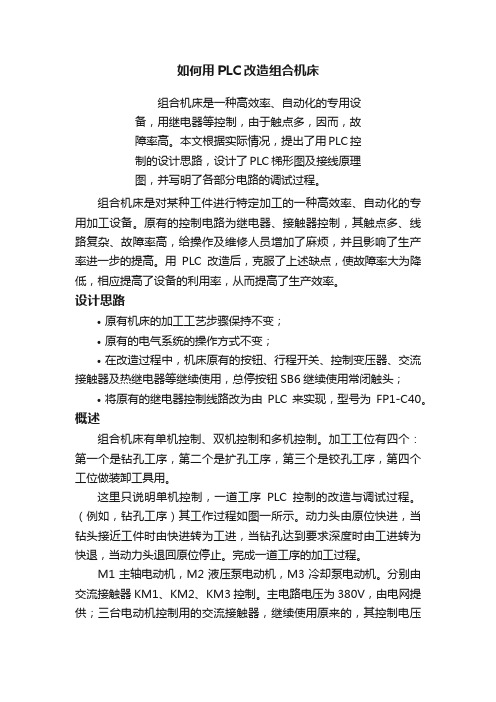
如何用PLC改造组合机床组合机床是一种高效率、自动化的专用设备,用继电器等控制,由于触点多,因而,故障率高。
本文根据实际情况,提出了用PLC控制的设计思路,设计了PLC梯形图及接线原理图,并写明了各部分电路的调试过程。
组合机床是对某种工件进行特定加工的一种高效率、自动化的专用加工设备。
原有的控制电路为继电器、接触器控制,其触点多、线路复杂、故障率高,给操作及维修人员增加了麻烦,并且影响了生产率进一步的提高。
用PLC改造后,克服了上述缺点,使故障率大为降低,相应提高了设备的利用率,从而提高了生产效率。
设计思路•原有机床的加工工艺步骤保持不变;•原有的电气系统的操作方式不变;•在改造过程中,机床原有的按钮、行程开关、控制变压器、交流接触器及热继电器等继续使用,总停按钮SB6继续使用常闭触头;•将原有的继电器控制线路改为由PLC来实现,型号为FP1-C40。
概述组合机床有单机控制、双机控制和多机控制。
加工工位有四个:第一个是钻孔工序,第二个是扩孔工序,第三个是铰孔工序,第四个工位做装卸工具用。
这里只说明单机控制,一道工序PLC控制的改造与调试过程。
(例如,钻孔工序)其工作过程如图一所示。
动力头由原位快进,当钻头接近工件时由快进转为工进,当钻孔达到要求深度时由工进转为快退,当动力头退回原位停止。
完成一道工序的加工过程。
M1主轴电动机,M2液压泵电动机,M3冷却泵电动机。
分别由交流接触器KM1、KM2、KM3控制。
主电路电压为380V,由电网提供;三台电动机控制用的交流接触器,继续使用原来的,其控制电压为220V,仍然用原有的控制变压器提供;电磁阀的直流控制电压为24V,由原来的整流电路提供,PLC中也有24V输出,考虑到PLC的输出功率,所以不采用。
主电路部分不做改动,控制电路原理由梯形图体现,如图二所示,控制电路接线如图三所示。
调试过程1、主电路调试:原电路要求M1、M2电动机同时启动工作。
由复合开关SA3、SA4可控制M1与M2个之单独启动、停止(机床调试用);M3电动机在动力头工进时自动启动,也可以由按钮SB2单独控制。
PLC双钻孔钻床的设计
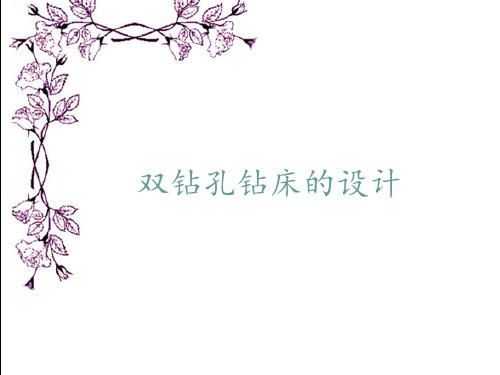
I0.1 Q0.4 Q0.2
I0.2
I0.3
I0.0 Q0.3 Q0.1
I0.4
I0.1 Q0.4 Q0.2
I0.2
I0.3
SM0.1
M0.0
R C0
I1.0.I0.0.I0.1 M0.1 Q0.0
I0.3
M0.2 Q0.1 I0.4
M0.3 Q0.1Q0.2 I0.2
M0.4 Q0.3 I0.0
Q0.0 I0.3
I0.0 Q0.3 Q0.1
I0.4
I0.1 Q0.4 Q0.2
I0.2
I0.3
I0.0 Q0.3 Q0.1
I0.4
I0.1 Q0.4 Q0.2
I0.2
I0.3
I0.0 Q0.3 Q0.1
I0.4
I0.1 Q0.4 Q0.2
I0.2
I0.3
I0.0 Q0.3 Q0.1
I0.4
M0.2 I0.2 M0.2 M0.4 M0.3
M0.3
M0.3无法通电的原因 是M0.2即是M0.3的 前级步.也是M0.3的
后续步.
改进方法
M0.1
I0.1
=1 M1.0
M0.2 I0.2
I0.3 M0.3
M0.4
M0.2=(M0.1*I0.1+M1.0*1+M0.2)*M0.3
M0.3=(M0.2*I0.2+M0.3)*(M0.4+M1.0)
2
5
7
e
f
3
6
g X8=(X4.j+X6.i+X7.g+X8).X0
h
i
X2=(X1.b+X2).X3
多工位组合机床的PLC控制系统设计毕业设计
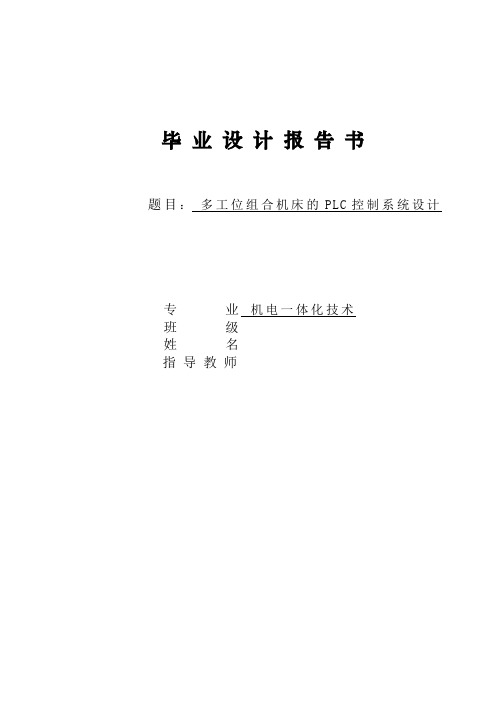
毕业设计报告书题目:多工位组合机床的PLC控制系统设计专业机电一体化技术班级姓名指导教师目录第一部分设计任务与调研 (1)第二部分设计说明 (4)第三部分设计成果 (10)第四部分结束语 (25)第五部分致谢 (26)第六部分参考文献 (27)第一部分设计任务与调研1.毕业设计的主要任务组合机床是针对特定工件,进行特定加工而设计的一种高效率自动化专用加工设备,这类设备大多能多刀同时工作,并且具有自动循环的功能。
组合机床是随着机械工业的不断发展,由通用机床、专用机床发展起来的。
通用机床一般用一把刀具进行加工,自动化程度低、辅助时间长、生产效率低,但通用机床能够重新调整,以适应加工对象的变化。
专用机床可以实现的多刀切削,自动化程度较高,结构较简单,生产效率也较高。
但是,专用机床的设计,制造周期长,造价高,工作可靠性也较差。
专用机床是针对某工件的一定工序设计的,当产品进行改进,工件的结构,尺寸稍有变化时,它就不能继续使用。
在综合了通用机床、专用机床优点的基础上产生了组合机床。
组合机床通常由标准通用部件和加工专用部件组合构成,动力部件采用电动机驱动或采用液压系统驱动,由电气系统进行工作自动循环的控制,是典型的机电或机电液一体化的自动加工设备。
常见的组合机床,标准通用部件有动力滑台各种加工动力头以及回转工作台等,可用电动机驱动,也可用液压驱动。
各标准通用动力部件组合构成一台组合机床时,该机床的控制电路可由各动力部件的控制电路通过一定的连接电路组合构成。
多动力部件构成的组合机床,其控制通常有三方面的工作要求:第一方面是动力部件的点动和复位控制。
第二方面是动力部件的半自动循环控制。
第三方面是整批全自动工作循环控制。
本文所用组合机床为四工位组合机床,该机床由四个滑台,各载一个加工动力头,组成四个加工工位,除了四个加工工位外,还有夹具,上下料机械手和进料器,四个辅助装置以及冷却和液压系统共14个部分。
机床的四个加工动力头同时对一个零件的四个端面以及中心孔进行加工,一次加工完成一个零件,由上料机械手自动上料,下料机械手自动取走加工完成的零件,零件每小时可加工80件。
PLC在两工位钻孔攻丝组合机床的应用

毕业论文(设计)PLC在两工位钻孔攻丝组合机床的应用目录摘要 (I)第一章前言 (1)1.1研究目的和意义 (1)1.2国外研究现状 (2)1.3研究容和方法 (3)第二章 PLC在组合机床中的应用 (4)2.1 组合机床的简介 (4)2.2 可编程控制器的简介 (5)2.3 PLC的简介……………………………………………………………………第三章两工位钻孔攻丝组合机床的设计……………………………………………3.1 两工位钻孔攻丝组合机床示意图……………………………………………3.2 两工位钻孔攻丝组合机床的控制要求………………………………………3.3 I/O分配………………………………………………………………………3.4 硬件接线图设计………………………………………………………………3.5 软件系统设计…………………………………………………………………第四章结论和建议……………………………………………………………………总结………………………………………………………………………………………致谢………………………………………………………………………………………参考文献…………………………………………………………………………………附录………………………………………………………………………………………摘要正文:本课题主要研究的是用PLC控制两工位钻孔攻丝组合机床的运作。
两工位钻孔攻丝组合机床经系统通电后能自动完成工件的钻孔和攻丝加工,该机床主要由床身、移动工作台、夹具、钻孔滑台、钻孔动力头、攻丝滑台、攻丝动力头、滑台移动控制凸轮和液压系统组成。
工作台的移动包括左移和右移以及夹具的动作包括夹紧和放松,钻孔滑台的移动包括前移和后移,都由液压系统执行,其中钻孔滑台和攻丝滑台的移动是通过控制凸轮来控制滑台移动液压系统的液压阀实现的,电气系统不参与。
只需启动控制凸轮电机即可。
该系统通过PLC的控制,工作台和滑台的移动将严格的按规定的时序同步进行,使两种运动密切配合,生产效率大大提高。
双面钻孔组合机床PLC控制

景背题课 1.1
论绪 .1
论绪 1
计设程课合综
3
。泛广用使�业行个各等乐娱化文及 保环�输运通交�纺轻�车汽�造制械机�材建�力电�工化�油石�铁钢于用 应泛广已外内国在 CLP�前目。等装包�床磨�床机合组�机书订�机刷印�机 塑注如。线水流化动自及控群机多于用可也�制控的备设台单于用可既�制控序 顺�制控辑逻现实�路电器电继的统传代取它�制控辑逻的量关开于用的泛广最 本基最 CLP。的现实来统系制控气电或动气过通是能功些这�上统传在。集采据 数的量散离量大及 �制控的作动护保锁连行进系关辑逻照按并 �作动序顺行进件 条辑逻照按它�制控序顺量关开的量大�中程过产生业工在程历展发的 CLP
退快台滑 7.3
进工台滑机右→电得 01VY 阀磁电�电 失 8VY→关开程行束结进快台滑机右 6TS 到遇者或进工缸压液台滑机左→电得 7VY 阀磁电�电失 5VY→3TS 关开程行束结进快台滑机左到碰时束结进快当
进工台滑 6.3
理原作工床机合组孔钻面双 3 计设程课合综
9
Hale Waihona Puke 3.2I 2.2I 1.2I 0.2I 7.1I
图程流作工的床机合组孔钻面双 2.2
图理原路电主床机合组孔钻面双 1.2 图
。示所 1.2 图如路电主制控�动驱现实阀磁电过通缸压液由动移的台 滑右左而�动带机动电流交由别分�转旋的头钻右�左的床机合组孔钻面双
图理原路电主床机合组孔钻面双 1.2
述概制控床机合组孔钻面双 .2
述概床机合组孔钻面双 2
销位定拔 9.3
件工开松缸压液→电得 4VY 铁磁电→退快束结电失 6VY,9VY 铁磁电→时 8TS 关开程行束结退快台滑机右和 5TS 关开程行到遇束结退快台滑机左当
- 1、下载文档前请自行甄别文档内容的完整性,平台不提供额外的编辑、内容补充、找答案等附加服务。
- 2、"仅部分预览"的文档,不可在线预览部分如存在完整性等问题,可反馈申请退款(可完整预览的文档不适用该条件!)。
- 3、如文档侵犯您的权益,请联系客服反馈,我们会尽快为您处理(人工客服工作时间:9:00-18:30)。
专业综合设计与实践报告书2013 /2014第 2 学期专业电气工程及其自动化班级 10电Y1学号 10120731姓名叶翔专业综合设计与实践任务书二级学院(直属学部):电子信息与电气工程学院专业:电气工程及其自动化目录第一章机床的改造目的以及原因 (5)第二章工作原理 (6)2.1原理: (6)2.2机床加工顺序功能图 (7)第三章设计分析 (9)3.1 PLC 的选型 (9)3.2系统主回路设计 (9)3.3 I/O 分配 (11)3.4硬件接线图设计 (11)3.4 梯形图设计 (13)第四章系统调试 (15)小结 (16)参考文献 (17)附录 (18)1.主电路 (18)2.PLC接线图 (19)3.原图 (20)4 .梯形图 (21)第一章机床的改造目的以及原因两工位钻孔攻丝组合机床是一种广泛使用的给机械零件钻孔攻丝机床,是许多大型企业不可缺少的设备之一。
该机床的电气系统由主拖动和控制系统两部份组成。
主拖动系统可以概括为以下四类:晶闸管-直流电动机(SCR-D)模拟直流调速系统、JF-D 调速系统、全数字直流调速系统和交流变频调速系统。
控制系统有继电器逻辑控制系统和继电器与 PLC 结合的控制系统。
JF-D 调速系统是上世纪 60 年代在机床上广泛使用的调速系统,目前该系统在国有大中型企业仍然占有相当大的比重。
JF-D 主要由直流发电机、直流电动机和交磁放大机组成。
其工作原理为:通过交磁放大机控制直流发电机的励磁电压,后者控制直流发电机的输出电压,从而控制直流电动机的电枢电压,最终控制直流电动机的转速。
另外还有二台交流电动机和一台直流发电机为该系统服务,大的交流电动机是直流发电机的原动机,小的交流电动机是交磁放大机的原动机,直流发电机为直流电动机的励磁绕组提供励磁电压。
目前,JF-D 型的两工位攻丝床的电气系统存在下列问题:(1) 故障率高,可靠性差,维护检修工作量大。
(2) 电气系统的连线多,判明故障性质和查找故障困难,查找故障的时间较长。
(3) 工作台频繁地来回运动,继电器和接触器的触点容易损坏或接触不良。
(4) 机械方式实现的触点控制反应速度慢。
(5) 继电器的控制功能被固定在线路中,功能单一,灵活性差等。
(6) 调速系统占地面积大,噪音大,耗电量大,效率低。
(7) 惯性大,调速系统动态及静态性能均不理想。
根据前面的分析,改造两工位钻孔攻丝组合机床的主拖动部份一般采交流变频调速系统,控制部份采用PLC。
由于变频调速系统的各种运行状况和故障情况都可以通过显示器显示,因此得到电气设计人员和维护人员的推崇和喜爱。
所以在本设计中对电机的转速控制用交流变频调速技术。
第二章工作原理2.1原理:系统通电后,初始步S0激活,辅助继电器M01变为ON状态;进入S20步,自动启动液压泵电机M1并保持,当工作台在钻孔工位, 钻孔滑台在原位,攻丝滑台在原位,(即SQ1 、SQ2 、SQ3动作),并且液压系统压力正常,压力继电器PV动作时,进入S21步,原点指示灯HL1亮,将要加工的工件放到工作台上,同时按下启动按钮SB,进入S22步,夹紧电磁阀得电并保持,液压系统控制夹具将待加工工件夹紧在夹紧限位SQ4开始动作时即表明工件已经被夹紧,紧接着进入S23步,凸轮电机M2得电运转并保持,钻孔动力头电机M3启动并保持,冷却泵电机M5得电运转并保持,且由于凸轮电机M2运转使钻孔滑台前移,进行钻孔加工。
当SQ5动作时即表明钻孔滑台已达到终点,此时进入S24步,钻孔滑台将自动后退,到原位时停,M3同时复位停止。
等到钻孔滑台回到原位后,SQ2动作,进入S25步,电磁阀YV2得电,液压系统使工作台右移,当限位开关SQ6动作时表明工作台到攻丝工位,此时工作台应停止运动。
接着进入S26步,启动电机M4正转,攻丝滑台开始前移,进行攻丝加工,当攻终点限位SQ7动作时,进入S27步,制动电磁阀DL得电,攻丝动力头制动,同时计时器T1开始工作,0.3S后进入S28步,攻丝动力头电机M4反转,同时攻丝滑台将自动后退。
攻丝滑台后退到原位SQ3动作,进入S29步,凸轮电机M2复位停止,冷却泵电机复位停止,同时计时器T2开始工作,3S后进入S30步,左移电磁阀YV3得电,工件台左移,同时加紧电磁阀复位,钻孔工位SQ1动作时左移停止,放松电磁阀得电后放松工件,放松限位动作后,停止放松。
原位指示灯亮时即可取下工件,整个加工过程到此完成。
2.2机床加工顺序功能图顺序功能图是一种易于构思,易于理解的程序设计工具,它既有流程图的直观,又有利于复杂的逻辑控制关系的分解与综合。
以下便是该设计的顺序功能图,见图4-2:第三章设计分析3.1 PLC 的选型PLC的电源应选择220VAC电源,与国内电源电压一致。
根据所需的 PLC 的输入/输出点数,并留有一定的余地。
选择PLC时,应该考虑性能价格比,输入输出点数对价格有直接的影响,每增加一块输入输出卡件就需要增加一定的费用,所以在估计和选择时应充分考虑这一点。
本次设计的机床所用的输入为10点,输出为13点,选择 PLC 的基本单元的型号为FX2N-32MR-001,输入输出点数总和为32,其中16点输入,16点输出,M是基本单元,R表示继电器输出,001表示适用于中国,选用该型号的PLC已足够。
3.2系统主回路设计在该控制系统中,根据工艺的要求,共选择电机五个,其中M1作为液压电机;M2为控制凸轮电机:M3为钻孔动立头电机;M4为攻丝动力头电机;M5作为冷却泵电机。
QS空气开关一个,KM交流接触器六个,FU熔断器二十一个,FR热继电器五个,变压器一台。
根据控制要求绘制出主回路电路原理图,如图3-1所示。
在图 3-1中,QS空气开关一般处于闭合状态,设备运行时合上空气开关,非工作时断开。
在该控制电路中旋转闭合手动开关SA,HL3指示灯亮,之后可进行手动操作,KA1常闭触点起保护作用;断开手动开关SA之后才能闭合SB,KA1线圈得电,完成自锁同时自动指示灯亮,系统自动对工件进行加工。
主电路图如下:3.3 I/O 分配I/O的分配有助于我们更好的理解题意,使编程过程不再复杂难懂。
I/O分配如表3.1所示:表3.2 I/O分配表3.4硬件接线图设计由组合机床加工工艺要求可知,其工艺过程为一顺序控制过程,所以可运用状态编程的思想,采用步进顺控指令对其进行控制。
虽然该控制为自动循环顺序控制,考虑到具体情况,需设置手动控制环节。
为减少输入点,简化程序,将按钮或转换开关接在驱动回路,可实现上述各工步的手动操作。
系统配置及I/O接线如图3.3所示。
图3.3 系统配置及I/O接线图3.4 梯形图设计梯形图的设计整体反映了编者的思想,使我们更清楚的理解程序的作用及用途,它是由状态图进一步转化而来,结合PLC控制将会使程序浅显易懂,以下便是该设计的梯形图,见图3.4图3.4 梯形图设计第四章系统调试PLC程序的调试可以分为模拟调试和现场调试两个调试过程,在此之前首先对PLC外部接线作仔细检查,这一个环节很重要。
外部接线一定要准确无误。
也可以用事先编写好的试验程序对外部接线做扫描通电检查来查找接线故障。
不过,为了安全考虑,最好将主电路断开。
当确认接线无误后再连接主电路,将模拟调试好的程序送入用户存储器进行调试,直到各部分的功能都正常,并能协调一致地完成整体的控制功能为止。
(1)程序的模拟调试将设计好的程序写入PLC后,首先逐条仔细检查,并改正写入时出现的错误。
用户程序一般先在实验室模拟调试,实际的输入信号可以用钮子开关和按钮来模拟,各输出量的通/断状态用PLC上有关的发光二极管来显示,一般不用接PLC 实际的负载(如接触器、电磁阀等)。
可以根据功能表图,在适当的时候用开关或按钮来模拟实际的反馈信号,如限位开关触点的接通和断开。
对于顺序控制程序,调试程序的主要任务是检查程序的运行是否符合功能表图的规定,即在某一转换条件实现时,是否发生步的活动状态的正确变化,即该转换所有的前级步是否变为不活动步,所有的后续步是否变为活动步,以及各步被驱动的负载是否发生相应的变化。
调试时应充分考虑各种可能的情况,对系统各种不同的工作方式、有选择序列的功能表图中的每一条支路、各种可能的进展路线,都应逐一检查,不能遗漏。
发现问题后应及时修改梯形图和PLC中的程序,直到在各种可能的情况下输入量与输出量之间的关系完全符合要求。
(2)程序的现场调试完成上述的工作后,将PLC安装在控制现场进行联机总调试,在调试过程中将暴露出系统中可能存在的传感器、执行器和硬接线等方面的问题,以及PLC的外部接线图和梯形图程序设计中的问题,应对出现的问题及时加以解决。
如果调试达不到指标要求,则对相应硬件和软件部分作适当调整,通常只需要修改程序就可能达到调整的目的。
全部调试通过后,系统就可以投入实际的运行了。
小结基于PLC的两工位钻孔攻丝组合机床控制系统的设计是在设备更新理论及基本原则的指导下,提出了用可编程控制器和变频调速技术对老式机床电气控制系统进行改造的思路,并重点研究了两项技术基本原理及其应用在机床电气系统改造中的大致过程及注意事项。
本文的主要工作和结论如下:(1) 对可编程控制器技术和变频调速技术进行了分析研究,并总结出两项技术的应用要点。
(2) 在上述研究的基础上,结合该机床的电气控制特性重点研究了可编程控制器技术及变频调速技术在电气改造中的应用方案及步骤,主要包括装置选型、主电路的设计、程序设计、调试等。
(3) 两项技术对两工位钻孔攻丝组合机床电气系统改造效果进行了对比分析。
分析表明两项技术的成功应用使电气故障率降低了很多,改造后机床运行稳定性大大提高,为企业创造了较好的经济效益。
(4) 用可编程控制技术和变频调速技术来对重型机床电气系统改造达到了理想的投入产出,并且具有对故障的自诊断能力,维修方便,值得在普通机床和一些电气控制中进行电气控制系统改造推广。
(5) 配线时要纵观全局,当接某一个点的线时要看下原理的其它地方有没有与该点相连的地方,如果有把它们一次性接在一起;否则,要拆掉重接,会造成很多麻烦和重复性的工作。
(6) 机床的调试是一项复杂的工作,一定要有耐心,且要根据机床的实际动作与设计要求进行对比。
对比后要分析是硬件的原因还是PLC程序的原因,得出结论后进行相应的更改。
不足之处:由于所掌握的知识有限,许多问题没有解决,以至于机床的加工范围受限;PLC的扩展部分也没有考虑等,不足之处有待今后进一步研究解决。
参考文献[1] 廖常初. PLC基础及应用. 北京:机械工业出版社,2005.4[2] 何衍庆. 可编程序控制器原理及应用技巧. 北京:化学工业出版社.2000[3] 高安邦等编. 新编机床电气与PLC控制技术. 北京:机械工业出版社,2008[4] 钟肇新.可编程序控制器原理及应用.北京:华南理工大学出版社2001[5] 贺家李. 电力系统继电保护原理. 北京:中国电力出版社,2010.6[6] 陶权. PLC控制系统设计、安装与调试. 北京:北京理工大学出版社,2011.7[7] 黄晓红. 工厂电气控制与可编程序控制器. 北京:中国科学出版社,2003.10[8] Troys, Dougalas. Development Environment for Batch Process Control Computers in Industry, 1996, 31(1): 61-84[9] 谢云敏,郭贵中,党保华主编.电气与可编程控制技术.上海:上海交通大学出版社,2012[10] 曾令宜主编.AutoCAD2008工程绘图技能训练教程.北京:高等教育出版社,2009.2附录1.主电路2.PLC接线图3.原图4 .梯形图。