聚氨酯发泡工艺简介
聚氨酯海绵发泡工艺
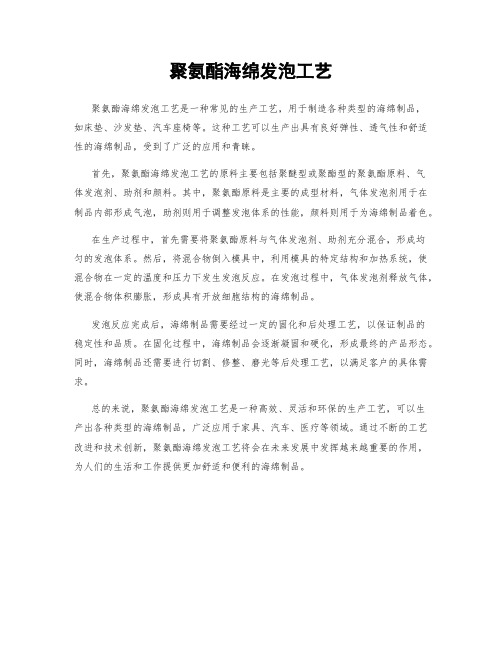
聚氨酯海绵发泡工艺
聚氨酯海绵发泡工艺是一种常见的生产工艺,用于制造各种类型的海绵制品,
如床垫、沙发垫、汽车座椅等。
这种工艺可以生产出具有良好弹性、透气性和舒适性的海绵制品,受到了广泛的应用和青睐。
首先,聚氨酯海绵发泡工艺的原料主要包括聚醚型或聚酯型的聚氨酯原料、气
体发泡剂、助剂和颜料。
其中,聚氨酯原料是主要的成型材料,气体发泡剂用于在制品内部形成气泡,助剂则用于调整发泡体系的性能,颜料则用于为海绵制品着色。
在生产过程中,首先需要将聚氨酯原料与气体发泡剂、助剂充分混合,形成均
匀的发泡体系。
然后,将混合物倒入模具中,利用模具的特定结构和加热系统,使混合物在一定的温度和压力下发生发泡反应。
在发泡过程中,气体发泡剂释放气体,使混合物体积膨胀,形成具有开放细胞结构的海绵制品。
发泡反应完成后,海绵制品需要经过一定的固化和后处理工艺,以保证制品的
稳定性和品质。
在固化过程中,海绵制品会逐渐凝固和硬化,形成最终的产品形态。
同时,海绵制品还需要进行切割、修整、磨光等后处理工艺,以满足客户的具体需求。
总的来说,聚氨酯海绵发泡工艺是一种高效、灵活和环保的生产工艺,可以生
产出各种类型的海绵制品,广泛应用于家具、汽车、医疗等领域。
通过不断的工艺改进和技术创新,聚氨酯海绵发泡工艺将会在未来发展中发挥越来越重要的作用,为人们的生活和工作提供更加舒适和便利的海绵制品。
PU发泡工艺介绍
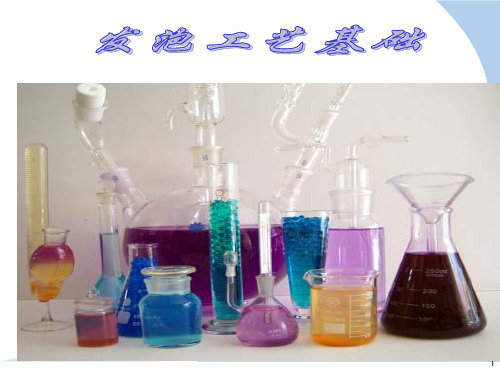
考量开孔和稳定性的重要指标。
9
聚氨酯原材料
聚氨酯原材料主要有ISO部分(又称黑料或 B料)和聚醚组合料部分(又称白料或A料) 组成。
ISO部分: TDI、TDI&MDI、 MDI。
聚醚组合料部分: 聚醚:聚醚多元醇和聚酯多元醇。
10
聚氨酯原材料
助剂:
催化剂:发泡胺催化剂和凝胶胺催化剂 泡沫稳定剂:有机硅油 发泡剂:H2O、F-11、F-12、二氯甲烷 阻燃剂:磷酸铵、氧化锑、含卤(烃、醇、酯、醚)、
撕裂强度:
通过规定形状的式样加撕裂力,来测定材料的抗撕裂性能。 试样尺寸为150*25*25mm(GB/T 10808),试样厚度方向为泡沫上升方向。
试样一端的中心部,沿厚度方向(泡沫上升方向)切一40mm长的切口, 沿试样厚度方向测量厚度,将试样张开夹在试验机夹具上,以 50~20mm/min的速度施加负荷,用刀片切割试样,保持刀口在中心位 置,记下试样断裂或撕裂50mm时的最大值。
• 料比: 产品硬度,物理性能和开孔性的重要控制 点;
17
聚氨酯原材料-聚醚组合料
• 聚醚多元醇和聚酯多元醇的未来发展趋势: • 高官能度的聚醚多元醇; • 高固含量和低粘度的聚合物多元醇; • 低挥发性; • 分子量高,分子量分布范围小; • 伯羟基含量进一步提高。
18
聚氨酯化学
两个主要反应方程式
• 将聚醚,水,催化剂和稳定剂按一定的比例配制后搅拌均匀的体系; 也称为A料
• 常见的配方:
22
工艺流程
• 原料检验
•
羟值,含水量,固含量,NCO含量等原材料性能;
• 配料
•
按配方配制聚醚组合料;
• 浇注
聚氨酯发泡技术

聚氨酯发泡技术
聚氨酯发泡技术是一种由聚氨酯原料,以及各种增塑剂、发泡剂、润湿剂、抗氧化剂、催化剂等复合而成的生产工艺。
它具有自主发泡性能,不需要外界加热即可实现空气及水分子体系中的渗透发泡,可得到有一定强度、密度和结构的发泡体,并可添加一些特殊功能性添加剂,使发泡材料具有抗水性、耐油性、耐酸碱性、抗紫外线老化性等特点,从而在保证发泡体结构稳定性的前提下具有良好的耐久性和耐用性。
聚氨酯发泡技术是一项先进的发泡技术,它的发泡过程采用的是自主发泡的原理,即聚氨酯原料在凝固时,由于其内部的发泡剂、催化剂等物质的作用,会形成小气泡,从而形成具有一定强度、密度和结构的发泡体,从而使发泡材料具有良好的抗水性、耐油性、耐酸碱性、抗紫外线老化性等特点,从而在保证发泡体结构稳定性的前提下具有良好的耐久性和耐用性。
聚氨酯发泡技术具有良好的发泡效果,可以生产出空心、多孔、可塑性好的发泡体,从而为实现结构密闭性、抗紫外线老化性、隔热性等特殊应用和要求提供有效的解决方案。
此外,聚氨酯发泡技术还具有良好的环保性,可以有效避免环境污染,符合相关的环境保护法规,被广泛应用于汽车、建筑、包装、冰箱、冷库等领域。
聚氨酯发泡技术的优点还有:发泡过程简单,可以节省大量的能源;发泡原料和发泡工艺可根据实际需要进行调整,生产出各种规格不同的发泡体;发泡体具有良好的机械性能,弹性大,耐受冲击;发泡过程中产生的CO2也可以有效利用,从而降低环境污染等。
总之,聚氨酯发泡技术具有发泡效果好、环保性强、耐用度高、可塑性良好等优点,广泛应用于汽车、建筑、包装、冰箱、冷库等领域,被认为是一种绿色环保的发泡技术。
聚氨酯海绵发泡工艺

聚氨酯海绵发泡工艺聚氨酯海绵是一种常见的海绵材料,具有良好的弹性、吸震、吸音、隔热等特性,在许多领域得到广泛应用,比如家具、汽车座椅、鞋垫等。
聚氨酯海绵的制作过程中,发泡工艺起着至关重要的作用。
下面将介绍聚氨酯海绵的发泡工艺及相关参考内容。
1. 聚氨酯海绵发泡工艺的基本步骤:(1) 原料准备:聚氨酯发泡材料主要包括聚醚多元醇、聚酯多元醇、异氰酸酯和增发剂等。
根据实际需要确定比例,并搅拌均匀。
(2) 模具准备:根据产品设计图纸,制作合适的模具,确保发泡后的聚氨酯海绵符合尺寸和形状要求。
(3) 发泡过程:将原料注入模具中,通过加热和加压的方式触发发泡反应。
发泡过程中,原料逐渐膨胀,填充整个模具空间。
(4) 固化和冷却:发泡完成后,聚氨酯材料需要经过固化和冷却,以保证海绵材料的稳定性和质量。
(5) 脱模和修整:待聚氨酯材料完全固化和冷却后,将其从模具中取出,并进行必要的修整和加工,如剪裁、打磨等。
2. 聚氨酯海绵发泡工艺的注意事项:(1) 原料配比:聚氨酯海绵的质量和性能与原料的配比关系密切。
需要根据产品的要求,确定合适的原料比例,以确保发泡后的海绵材料具有合适的硬度、弹性等特性。
(2) 发泡条件:发泡过程中的温度和压力对聚氨酯发泡效果有重要影响。
不同的发泡材料和产品要求,需要采用不同的发泡温度和压力,以获得最佳的发泡效果。
(3) 模具设计:模具的设计应符合产品的尺寸和形状要求。
同时,模具的材料要具有良好的耐热性和抗粘性,以便顺利脱模和修整。
(4) 固化和冷却时间:发泡后的聚氨酯海绵需要经过一定时间的固化和冷却,以确保材料内部结构的稳定性和材料性能的发挥。
固化和冷却时间的长短将直接影响到产品的质量。
以上是聚氨酯海绵发泡工艺及相关参考内容的简要介绍。
发泡工艺对于聚氨酯海绵的制作至关重要,不同的产品和要求将对发泡工艺提出不同的要求。
通过合理配比原料、控制发泡条件、优化模具设计以及适当的固化和冷却时间,可以生产出具有高质量和性能的聚氨酯海绵产品。
聚氨酯发泡生产工艺

聚氨酯发泡生产工艺
聚氨酯发泡是一种广泛应用于建筑、汽车、航空航天、电子、家具等行业的发泡材料,其生产工艺大致可分为原材料准备、混合反应、模具注射和固化四个步骤。
首先,进行原材料准备。
聚氨酯发泡生产所需的原材料主要有聚醚、聚酯、催化剂、气体发生剂等。
这些原材料需要严格按照配比准备,并且保持干燥和洁净。
其次,进行混合反应。
将事先准备好的聚醚、聚酯等原材料加入混合机中进行搅拌和混合。
加入的催化剂和气体发生剂可以控制发泡材料的反应速度和发泡性能。
然后,进行模具注射。
混合反应后的聚氨酯液体会在模具中注射,模具形状可以根据产品的要求进行设计和制造。
模具中的空腔会被聚氨酯液体填充,同时发生泡沫扩张,形成发泡材料的形状。
最后,进行固化。
注射完成后,发泡材料需要在模具中进行固化。
根据产品的要求,可以通过加热、冷却等方式对发泡材料进行固化,使其达到所需的硬度和强度。
在整个聚氨酯发泡的生产过程中,需要注意一些关键环节。
首先,原材料的选择和准备非常重要,不同的原材料和配比会对产品的质量产生影响。
其次,混合反应的时间和温度需要控制好,以保证反应的充分和均匀。
注射过程中,模具的设计和制造也需要精确,以确保产品形状的准确性和一致性。
最后,固
化的温度和时间也需要根据产品的要求进行调整,以获得最佳的固化效果。
总之,聚氨酯发泡生产工艺需要进行原材料准备、混合反应、模具注射和固化等步骤。
通过严格控制每个环节,可以获得高质量的发泡产品。
PU发泡工艺介绍
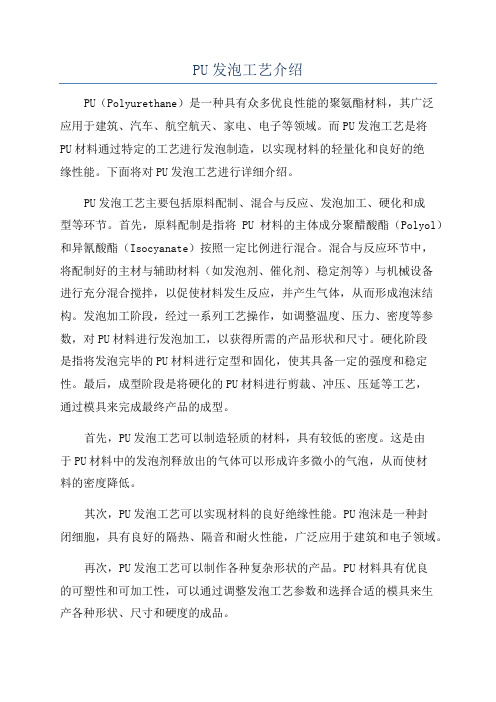
PU发泡工艺介绍PU(Polyurethane)是一种具有众多优良性能的聚氨酯材料,其广泛应用于建筑、汽车、航空航天、家电、电子等领域。
而PU发泡工艺是将PU材料通过特定的工艺进行发泡制造,以实现材料的轻量化和良好的绝缘性能。
下面将对PU发泡工艺进行详细介绍。
PU发泡工艺主要包括原料配制、混合与反应、发泡加工、硬化和成型等环节。
首先,原料配制是指将PU材料的主体成分聚醋酸酯(Polyol)和异氰酸酯(Isocyanate)按照一定比例进行混合。
混合与反应环节中,将配制好的主材与辅助材料(如发泡剂、催化剂、稳定剂等)与机械设备进行充分混合搅拌,以促使材料发生反应,并产生气体,从而形成泡沫结构。
发泡加工阶段,经过一系列工艺操作,如调整温度、压力、密度等参数,对PU材料进行发泡加工,以获得所需的产品形状和尺寸。
硬化阶段是指将发泡完毕的PU材料进行定型和固化,使其具备一定的强度和稳定性。
最后,成型阶段是将硬化的PU材料进行剪裁、冲压、压延等工艺,通过模具来完成最终产品的成型。
首先,PU发泡工艺可以制造轻质的材料,具有较低的密度。
这是由于PU材料中的发泡剂释放出的气体可以形成许多微小的气泡,从而使材料的密度降低。
其次,PU发泡工艺可以实现材料的良好绝缘性能。
PU泡沫是一种封闭细胞,具有良好的隔热、隔音和耐火性能,广泛应用于建筑和电子领域。
再次,PU发泡工艺可以制作各种复杂形状的产品。
PU材料具有优良的可塑性和可加工性,可以通过调整发泡工艺参数和选择合适的模具来生产各种形状、尺寸和硬度的成品。
此外,PU发泡工艺还具有可持续发展的优势。
PU材料可以通过循环利用和再生利用来降低对环境的影响。
同时,PU发泡工艺可以有效减少材料的使用量,从而实现资源节约。
在应用方面,PU发泡工艺广泛应用于建筑、汽车、航空航天、家电、电子等领域。
在建筑领域,PU发泡材料可用于墙体隔热、屋顶保温、地板隔音等。
在汽车行业,PU发泡材料可用于制造汽车座椅、车门内饰等零部件。
pu发泡工艺技术

pu发泡工艺技术PU发泡工艺技术是一种利用聚氨酯材料进行发泡制作的技术。
该技术可以使用于各种行业和领域,如建筑、汽车、家具、电子等。
在PU发泡工艺技术中,聚氨酯材料是通过化学反应组成的,形成一个具有轻质孔隙结构的发泡体。
PU发泡工艺技术主要包括材料准备、混合、注塑、发泡、固化等步骤。
首先,需要准备好聚氨酯材料,通常是由两种液体材料混合而成的。
然后,将这两种液体材料按一定比例混合,使其达到适合发泡的状态。
接下来,将混合的材料注入模具中。
模具可以根据需要制作成任何形状,以满足产品的要求。
在注塑过程中,材料开始发生变化,逐渐充满整个模具,并形成一个密闭的空腔。
在发泡阶段,注塑的材料会发生化学反应,产生气体,使整个空腔膨胀。
这样,PU发泡材料就形成了一个轻质、高强度的聚氨酯泡沫。
最后,通过固化工艺,使聚氨酯泡沫发泡体完全固化。
固化的时间和温度取决于具体的产品要求和材料性质。
完成固化后,就可以将PU发泡制品取出模具,得到成品。
PU发泡工艺技术具有许多优点。
首先,PU发泡材料具有优良的绝缘性能,可以在电子领域中广泛应用。
其次,由于聚氨酯材料的性质可调,可以制作出各种不同硬度、厚度和形状的产品。
另外,PU发泡材料重量轻、强度高,可以减少产品的重量和成本。
PU发泡工艺技术的应用范围很广。
在建筑领域,可以用来制作隔热材料、隔音材料和防水材料等。
在汽车领域,可以用于制作车座、车门和车顶等。
在家具领域,可以用于制作床垫、沙发和椅子等。
此外,PU发泡材料还可以用于制作包装材料、运动器材和医疗器械等。
总之,PU发泡工艺技术是一种十分重要且具有广泛应用的技术。
它通过化学反应和物理变化,将聚氨酯材料转化为轻质、高强度的泡沫制品。
这种技术不仅可以满足各种行业和领域的需求,同时也具有良好的环保性能。
随着科学技术的不断进步,PU发泡工艺技术将在更多领域中发挥作用,为人们的生活带来更多便利和舒适。
聚氨酯发泡工艺范文
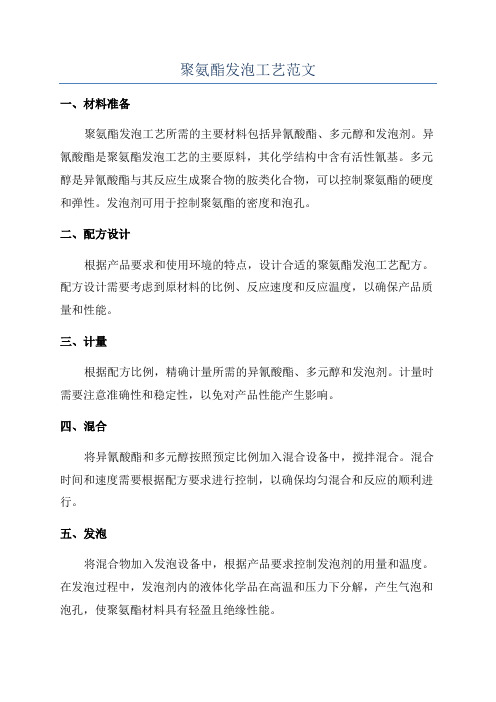
聚氨酯发泡工艺范文一、材料准备聚氨酯发泡工艺所需的主要材料包括异氰酸酯、多元醇和发泡剂。
异氰酸酯是聚氨酯发泡工艺的主要原料,其化学结构中含有活性氰基。
多元醇是异氰酸酯与其反应生成聚合物的胺类化合物,可以控制聚氨酯的硬度和弹性。
发泡剂可用于控制聚氨酯的密度和泡孔。
二、配方设计根据产品要求和使用环境的特点,设计合适的聚氨酯发泡工艺配方。
配方设计需要考虑到原材料的比例、反应速度和反应温度,以确保产品质量和性能。
三、计量根据配方比例,精确计量所需的异氰酸酯、多元醇和发泡剂。
计量时需要注意准确性和稳定性,以免对产品性能产生影响。
四、混合将异氰酸酯和多元醇按照预定比例加入混合设备中,搅拌混合。
混合时间和速度需要根据配方要求进行控制,以确保均匀混合和反应的顺利进行。
五、发泡将混合物加入发泡设备中,根据产品要求控制发泡剂的用量和温度。
在发泡过程中,发泡剂内的液体化学品在高温和压力下分解,产生气泡和泡孔,使聚氨酯材料具有轻盈且绝缘性能。
六、固化发泡后的聚氨酯材料需要进行固化处理,以加强产品的机械性能和稳定性。
固化时间和温度需要根据具体配方和产品要求进行控制。
七、加工固化后的聚氨酯材料可以进行各种加工操作,如切割、打磨和装配。
根据产品设计和使用要求,对聚氨酯材料进行相应的加工处理。
八、质量检验对最终的聚氨酯发泡产品进行质量检验,检测产品的物理性能、化学性能和外观质量,以确保产品符合设计要求和标准。
总结:聚氨酯发泡工艺是一种常用的材料加工工艺,通过控制配方比例、发泡参数和固化条件,可以制造出具有特定硬度和密度的聚氨酯材料。
在实施聚氨酯发泡工艺时,需要精确计量原材料、合理控制温度和压力,并进行适当的质量检验,以确保产品达到预期要求。
- 1、下载文档前请自行甄别文档内容的完整性,平台不提供额外的编辑、内容补充、找答案等附加服务。
- 2、"仅部分预览"的文档,不可在线预览部分如存在完整性等问题,可反馈申请退款(可完整预览的文档不适用该条件!)。
- 3、如文档侵犯您的权益,请联系客服反馈,我们会尽快为您处理(人工客服工作时间:9:00-18:30)。
聚氨酯发泡工艺简介聚氨酯硬泡生产工艺硬泡成型工艺聚氨酯硬泡的基本生产方法聚氨酯硬泡一般为室温发泡,成型工艺比较简单。
按施工机械化程度可分为手工发泡和机械发泡。
根据发泡时的压力,可分为高压发泡和低压发泡。
按成型方式可分为浇注发泡和喷涂发泡。
浇注发泡按具体应用领域、制品形状又可分为块状发泡、模塑发泡、保温壳体浇注等。
根据发泡体系可发为HCFC 发泡体系、戊烷发泡体系和水发泡体系等,不同的发泡体系对设备的要求不一样。
按是否连续化生产可分为间歇法和连续法。
间歇法适合于小批量生产。
连续法适合于大规模生产,采用流水线生产方法,效率高。
按操作步骤中是否需预聚可分为一步法和预聚法(或半预聚法)。
1.手工发泡及机械发泡在不具备发泡机、模具数量少和泡沫制品的需要量不大时可采用手工浇注的方法成型。
手工发泡劳动生产率低,原料利用率低,有不少原料粘附在容器壁上。
成品率也较低。
开发新配方,以及生产之前对原料体系进行例行检测和配方调试,一般需先在实验室进行小试,即进行手工发泡试验。
在生产中,这种方法只适用于小规模现场临时施工、生产少量不定型产品或制作一些泡沫塑料样品。
手工发泡大致分几步:(1) 确定配方,计算制品的体积,根据密度计算用料量,根据制品总用料量一般要求过量5%~15%。
(2) 清理模具、涂脱模剂、模具预热。
(3) 称料,搅拌混合,浇注,熟化,脱模。
手工浇注的混合步骤为:将各种原料精确称量后,将多元醇及助剂预混合,多元醇预混物及多异氰酸酯分别置于不同的容器中,然后将这些原料混合均匀,立即注入模具或需要充填泡沫塑料的空间中去,经化学反应并发泡后即得到泡沫塑料。
在我国,一些中小型工厂中手工发泡仍占有重要的地位。
手工浇注也是机械浇注的基础。
但在批量大、模具多的情况下手工浇注是不合适的。
批量生产、规模化施工,一般采用发泡机机械化操作,效率高。
2.一步法及预聚法目前,硬质聚氨酯泡沫塑料都是用一步法生产的,也就是各种原料进行混合后发泡成型。
为了生产的方便,目前不少厂家把聚醚多元醇或(及)其它多元醇、催化剂、泡沫稳定剂、发泡剂等原料预混在一起,称之为“ 白料”,使用时与粗MDI(俗称“ 黑料” )以双组分形式混合发泡,仍属于“ 一步法”,因为在混合发泡之前没有发生化学反应。
早期的聚氨酯硬泡采用预聚法生产。
这是因为当时所用的多异氰酸酯原料为TDI-80。
由于TDI 粘度小,与多元醇的粘度不匹配;TDI 在高温下挥发性大;且与多元醇、水等反应放热量大,若用一步法生产操作困难,故当时多用预聚法。
若把全部TDI 和多元醇反应,制得的端异氰酸酯基预聚体粘度很高,使用不便。
硬泡生产中所指的预聚法实际上是“ 半预聚法”。
即首先TDI与部分多元醇反应,制成的预聚体中NCO 的质量分数一般为20%~25%。
由于TDI大大过量,预聚体的粘度较低。
预聚体再和聚酯或聚醚多元醇、发泡剂、表面活性剂、催化剂等混合,经过发泡反应而制得硬质泡沫塑料。
预聚法优点是:发泡缓和,泡沫中心温度低,适合于模制品;缺点是:步骤复杂、物料流动性差,对薄壁制品及形状复杂的制品不适用。
自从聚合MDI 开发成功后,TDI 已基本上不再用作硬质泡沫塑料的原料,一步法随之取代了预聚法。
浇注成型工艺浇注发泡是聚氨酯硬泡常用的成型方法,即就是将各种原料混合均匀后,注入模具或制件的空腔内发泡成型。
聚氨酯硬泡的浇注成型可采用手工发泡或机械发泡,机械发泡可采用间歇法及连续法发泡方式。
机械浇注发泡的原理和手工发泡的相似,差别在于手工发泡是将各种原料依次称入容器中,搅拌混合;而机械浇注发泡则是由计量泵按配方比例连续将原料输入发泡机的混合室快速混合。
硬泡浇注方式适用于生产块状硬泡、硬泡模塑制品,在制件的空腔内填充泡沫,以及其它的现场浇注泡沫。
块状硬泡及模塑发泡块状硬质泡沫塑料指尺寸较大的硬泡块坯,一般可用间隙式浇注或用连续发泡机生产。
块状硬泡切割后制成一定形状的制品。
模塑硬泡一般指在模具中直接浇注成型的硬泡制品。
块状硬泡的生产方法和连续法块状软泡及箱式发泡软泡相似。
原料中可加入一定量的固体粉状或糊状填料。
块状硬泡在模具顶上常装有一定重量的浮动盖板。
反应物料量按模具体积和所需泡沫塑料密度计算,另加3%~5%比较合适。
这种情况下,泡沫上升受到浮动盖板限制,结构更为均匀,各向异性程度减小。
也可用自由发泡生产块状硬泡,即在没有顶盖的箱体内发泡,泡沫密度由配方决定。
小体积(体积小于0.5 m3,厚度不大于10cm)聚氨酯硬泡生产配方及工艺目前已经成熟,国内普遍采用。
大体积块状硬泡发泡工艺难度较大,国内生产厂家少。
在大体积聚氨酯硬泡生产中,应注意防止泡沫内部产生的热量积聚而引起烧芯。
一般需控制原料中的水分,不用水发泡以减少热量的产生,尽量采用物理发泡剂以吸收反应热,降低发泡原料的料温。
间隙式箱式发泡和模塑发泡,发泡过程大致是这样的:多元醇、发泡剂、催化剂等原料精确计量后置于一容器中预混合均匀,加入异氰酸酯后立即充分混合均匀,具有流动性的反应物料注入模具,经化学反应并发泡成型。
箱式块状发泡工艺的优点是投资少,灵活性大。
一个模具每小时一般可生产两块硬泡。
缺点是原料损耗大,劳动生产率低。
模塑发泡是在有一定强度的密闭模具(如密闭的箱体)内发泡,密度由配方用量和设定的模具体积来决定。
一般用于生产一些小型硬泡制品,如整皮硬泡、结构硬泡等。
模塑发泡的模具要求能承受一定的模内压力。
原料的过填充量根据要求的密度及整皮质量而定。
大体积块状泡沫一般需用发泡机混合与浇注物料。
高、低压发泡机均可。
机械发泡,发泡料的乳白时间远比搅拌式混合的短。
因此,生产大块泡沫塑料,最好选用大输出量发泡机。
连续法生产块状硬泡的过程与块状软泡的相似,所用发泡机,其原理和外观也与生产软泡的机器相似。
如Planibloc平顶发泡装置也适用于生产块状硬泡。
浇注成型中的注意事项浇注发泡成型的催化剂以胺类催化剂为主,可采用延迟性胺类催化剂延长乳白时间,满足对模具的填充要求,这类催化剂可提高原料体系的流动性,但不影响其固化性。
异氰酸酯指数稍大于100,如105。
浇注发泡成型过程中,原料温度与环境温度直接影响泡沫塑料制品的质量。
环境温度以20~30℃为宜,原料温度可控制在20~30℃或稍高一些。
温度过高或过低都不易得到高质量的制品。
对船舶、车辆等大型制品现场浇注成型,难以控制环境温度,则可适当控制原料温度并调节催化剂用量。
对模具的要求是结构合理,拆装方便,重量轻,耐一定压力,并且内表面还要有较好的光洁度。
同时还要根据模具的大小和不同的形状,在合适的位置钻多个排气孔。
制造模具的材质一般是铝合金,有时也用钢模。
模具温度的高低直接影响反应热移走的速度。
模温低,发泡倍率小,制品密度大,表皮厚;模温高则相反。
为制得高质量的泡沫塑料制品,一般将模温控制在40~50℃范围。
料温和模温较低时,化学反应进行缓慢,泡沫固化时间长;温度高,则固化时间短。
在注入模具内发泡时,应在脱模前将模具与制品一起放在较高温度环境下熟化,让化学反应进行完全。
若过早脱模,则熟化不充分,泡沫会变形。
原料品种与制件形状尺寸不同,所需的熟化时间和温度也不同。
一般模塑泡沫在模具中需固化10min 后才能脱模。
由于混合时间短,混合效率是需重视的因素。
手工浇注发泡,搅拌器应有足够的功率和转速。
混合得均匀,泡沫孔细而均匀,质量好;混合不好,泡孔粗而不均匀,甚至在局部范围内出现化学组成不符合配方要求的现象,大大影响制品质量。
聚氨酯硬泡喷涂成型聚氨酯硬泡喷涂发泡成型即是将双组分组合料迅速混合后直接喷射到物件表面而发泡成型。
喷涂是聚氨酯硬泡是一种重要的施工方法,可用于冷库、粮库、住宅及厂房屋顶、墙体、贮罐等领域的保温层施工,应用已逐渐普及。
喷涂发泡成型的优点是:不需要模具;无论是在水平面还是垂直面、顶面,无论是在形状简单的物体表面或者还是复杂的表面,都可通过喷涂方法形成硬质聚氨酯泡沫塑料保温层;劳动生产率高;喷涂发泡所得的硬质聚氨酯泡沫塑料无接缝,绝热效果好,兼具一定的防水功能。
低压及高压喷涂一般按喷涂设备压力分为低压喷涂和高压喷涂,高压喷涂发泡按提供压力的介质种类又分为气压型和液压型高压喷涂工艺。
低压喷涂发泡是靠柱塞泵将聚氨酯泡沫组合料“ 白料” (即组合聚醚)、“ 黑料” (即聚合MDI)这两种原料从原料桶内抽出并输送到喷枪枪嘴,然后靠压缩空气将黑白两种原料从喷枪嘴中吹出的同时使之混合发泡。
低压喷涂发泡的缺点是:原材料损耗大,污染环境;黑白两种原料容易互串而造成枪嘴、管道堵塞,每次停机都要手工清洗枪嘴;另外压缩空气压力不稳定,混合效果时好时坏,影响发泡质量,喷涂表面不光滑。
但低压喷涂发泡设备价格较高压机低。
低压喷涂发泡施工是一般先开空气压缩机,调节空气压力和流量到所需值,然后开动计量泵开始喷涂施工,枪口与被喷涂面距离300~500mm,以流量1~2 kg/min、喷枪移动速度0.5~0.8 s/m 为宜。
喷涂结束时先停泵,再停压缩空气,拆喷枪,用溶剂清洗之。
高压喷涂发泡,物料在空间很小的混合室内高速撞击并剧烈旋转剪切,混合非常充分。
高速运动的物料在喷枪口形成细雾状液滴,均匀地喷射到物件表面。
高压型喷涂发泡设备与低压型喷涂发泡设备相比,具有压力波动小、喷涂雾化效果好、属无气喷涂、原料浪费少、污染小、喷枪自清洁等一系列优点。
目前国内高压喷涂设备主要来自美国Glas-Craft公司、Graco 公司、Gusmer 等公司。
进口的高压喷涂机有的带可控加热器,可把黑白料加热(最高达70℃)。
为了方便施工,在主加热器与喷枪之间配备长管。
为防止两个发泡料组分在流经长管道时冷却降温,长管外面包有保温层,内有温度补偿加热器,以保证黑料、白料达到设定的温度。
选择合适的喷涂发泡设备,是控制硬质聚氨酯喷涂泡沫平整度及泡沫质量的关键之一。
高压喷涂发泡效果明显优于低压喷涂发泡。
喷涂发泡工艺对原料的要求①毒性小,喷涂发泡时,原料喷散成很细的液滴,为减少对环境的污染和操作人员的健康,除发泡剂外,其它原料中的低沸点成分应严加控制,臭味大的叔胺催化剂尽量少用。
特别是聚合MDI 中,易挥发低相对分子质量的异氰酸酯含量要控制在很低范围内。
②粘度小,有利于在极短时间内混合均匀。
③催化剂活性要大,因为喷涂发泡工艺要求反应速度较快,泡沫应很快固化,不流淌。
一般选用三亚乙基二胺、二月桂酸二丁基锡等催化剂。
具有催化作用的叔胺类多元醇,如由乙二胺与环氧丙烷反应制得的俗称“ 胺醚” 的多元醇,常常用于喷涂发泡。
组合料的固化速度应调节在适当的范围,如乳白时间3~5s,不粘时间10~20 s。
这样,能保证反应液混合后立即在喷射面固化,形成泡沫塑料。
这一点,对由下往上的顶部喷涂特别重要。
关于喷涂发泡的环境条件,有几点应注意。