超微细纳米研磨技术在纳米科技上应用与研讨
微纳米制造技术的研究与应用
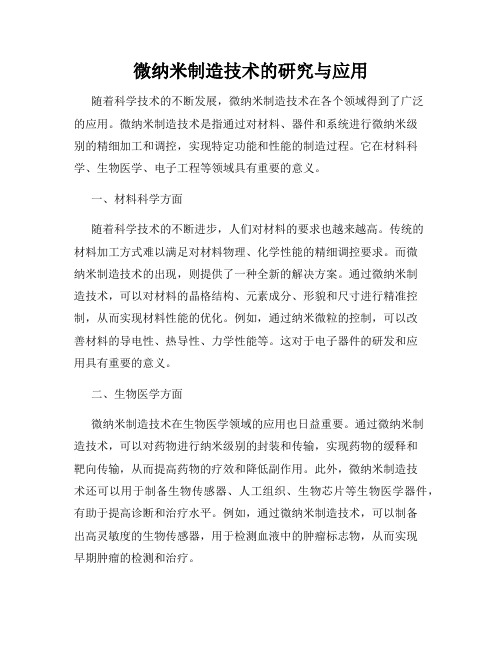
微纳米制造技术的研究与应用随着科学技术的不断发展,微纳米制造技术在各个领域得到了广泛的应用。
微纳米制造技术是指通过对材料、器件和系统进行微纳米级别的精细加工和调控,实现特定功能和性能的制造过程。
它在材料科学、生物医学、电子工程等领域具有重要的意义。
一、材料科学方面随着科学技术的不断进步,人们对材料的要求也越来越高。
传统的材料加工方式难以满足对材料物理、化学性能的精细调控要求。
而微纳米制造技术的出现,则提供了一种全新的解决方案。
通过微纳米制造技术,可以对材料的晶格结构、元素成分、形貌和尺寸进行精准控制,从而实现材料性能的优化。
例如,通过纳米微粒的控制,可以改善材料的导电性、热导性、力学性能等。
这对于电子器件的研发和应用具有重要的意义。
二、生物医学方面微纳米制造技术在生物医学领域的应用也日益重要。
通过微纳米制造技术,可以对药物进行纳米级别的封装和传输,实现药物的缓释和靶向传输,从而提高药物的疗效和降低副作用。
此外,微纳米制造技术还可以用于制备生物传感器、人工组织、生物芯片等生物医学器件,有助于提高诊断和治疗水平。
例如,通过微纳米制造技术,可以制备出高灵敏度的生物传感器,用于检测血液中的肿瘤标志物,从而实现早期肿瘤的检测和治疗。
三、电子工程方面微纳米制造技术对电子工程领域的发展也有重要的促进作用。
随着电子元器件越来越小型化,传统的制造技术已经难以满足要求。
而微纳米制造技术则可以在纳米尺度下进行电子元器件的精细加工和组装。
通过微纳米制造技术,可以制备出高性能的纳米传感器、纳米电池、纳米存储器等电子器件,有助于提高电子产品的性能和功能。
例如,微纳米制造技术可以制备出纳米传感器,用于实时监测环境中的温度、湿度、压力等参数,为智能电子设备的发展提供了新的思路和技术支持。
微纳米制造技术的研究与应用还面临着一些挑战。
首先,微纳米制造技术需要高精度的设备和工艺流程支持,因此,对设备和工艺的研发和改进也是必不可少的。
微纳米制造技术的研究和应用

微纳米制造技术的研究和应用随着科学技术的不断进步和发展,微纳米制造技术越来越成为人们关注的焦点。
微纳米制造技术是指通过微米或纳米级别的加工制造出微小的器件、元器件或系统,具有高度集成、高效能、高精度和高可靠性等特点。
该技术可以广泛应用于光电信息、能源储存、复合材料、生物医学等领域,在实现人类物质文明和提升人类生活质量方面具有重要作用。
一、微纳米制造技术的分类及发展状况微纳米制造技术根据加工的物质不同可分为纳米制造技术和微制造技术。
纳米制造技术主要是基于物理或化学原理制造出尺寸在10^-9米以下的纳米级别的结构或功能元件。
微制造技术则是利用微机电系统技术,通过薄膜加工、等离子体刻蚀等技术制造结构尺寸在10^-6米到10^-9米之间的微系统、微器件、微结构和微元器件。
目前,微纳米制造技术的发展状况处于飞速发展的阶段。
从另一个维度来看,虽然微纳米领域相对来说还处于比较早期的阶段,但是在材料、制造、模拟与设计、测试及应用等方面已经具备了相对完整的产业链,取得了快速发展和成熟。
其中,谷歌的“针尖技术”、三星电子的可戴式技术、苹果公司的3D相机技术等都是微纳米制造技术应用的体现。
二、微纳米制造技术的重要应用领域1.电子信息领域微纳米制造技术在电子信息领域的应用主要表现在微电子元器件和微电子器件的制造以及集成电路的生产等方面。
通过微纳米制造技术,现已发展出了很多新型元器件和器件,如场效应管、晶体管、电容器、电阻器等。
2.能源领域微纳米制造技术在能源领域的应用范围较广,主要涉及到太阳能电池、燃料电池、微观传感器等。
采用微纳米制造技术制造的电池具有体积小、功率密度高、充电时间短和寿命长等优点。
3.生物医学领域微纳米制造技术在生物医学领域的应用主要包括组织工程和细胞培养等。
通过微纳米制造技术,可以制造出高精度、高密度、高复杂度、高度的组织结构,用于生物医药领域的研究和应用。
4.环保领域微纳米制造技术在环保领域的应用主要涉及到水处理、空气净化和危险废弃物处理等方面。
纳米科技和纳米材料的研究和应用
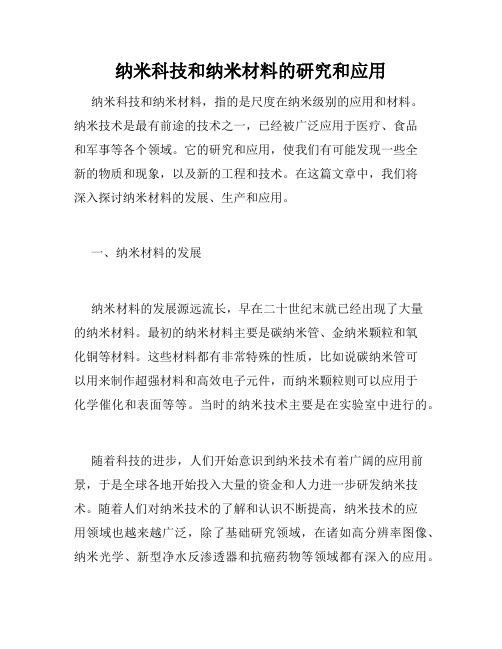
纳米科技和纳米材料的研究和应用纳米科技和纳米材料,指的是尺度在纳米级别的应用和材料。
纳米技术是最有前途的技术之一,已经被广泛应用于医疗、食品和军事等各个领域。
它的研究和应用,使我们有可能发现一些全新的物质和现象,以及新的工程和技术。
在这篇文章中,我们将深入探讨纳米材料的发展、生产和应用。
一、纳米材料的发展纳米材料的发展源远流长,早在二十世纪末就已经出现了大量的纳米材料。
最初的纳米材料主要是碳纳米管、金纳米颗粒和氧化铜等材料。
这些材料都有非常特殊的性质,比如说碳纳米管可以用来制作超强材料和高效电子元件,而纳米颗粒则可以应用于化学催化和表面等等。
当时的纳米技术主要是在实验室中进行的。
随着科技的进步,人们开始意识到纳米技术有着广阔的应用前景,于是全球各地开始投入大量的资金和人力进一步研发纳米技术。
随着人们对纳米技术的了解和认识不断提高,纳米技术的应用领域也越来越广泛,除了基础研究领域,在诸如高分辨率图像、纳米光学、新型净水反渗透器和抗癌药物等领域都有深入的应用。
二、纳米材料的制备纳米材料的制备,是伴随着纳米技术发展起来的。
传统的材料制备方法,相比之下它的发展还比较复杂。
制备纳米材料,需要优选适合其制备工艺的原材料,并在制备过程中,需要仔细控制制备条件,避免分子聚合度过高或分子化程度过低,同时还需要采用一些特殊的技术和工艺。
其中一项极为关键的技术就是纳米制备方法。
一般而言,纳米材料的制备方法可以分为几类:1. 物理制备法。
物理制备法主要是通过物理方式来制备纳米材料。
例如通过机械制备,火箭推进器的特种合金,还有在医学电子学中被广泛应用于电子元件的半导体器件等等都属于这种制备方法。
2. 化学制备法。
化学制备法主要是通过化学反应来制备纳米材料,该方法的优点在于制备工艺简单,可以制备出高质量的纳米材料,但缺点在于分散性和聚合性较大,必须经过处理才能性能良好。
其中较为常用的是溶胶-凝胶法,溶液法、共沉淀法等等。
3. 生物制备法。
超细粉磨技术

超细粉磨技术
摘要:
一、超细粉磨技术的定义与背景
二、超细粉磨技术的应用领域
三、超细粉磨技术的优势与挑战
四、我国超细粉磨技术的发展现状
五、未来发展趋势与展望
正文:
超细粉磨技术是指利用现代粉碎技术,将物料粉碎到纳米级细度的过程。
这种技术在我国得到了广泛的应用,为许多行业的发展提供了强大的支持。
超细粉磨技术的应用领域非常广泛,包括化工、医药、建材、冶金、能源等。
例如,在医药行业,超细粉磨技术可以用于制备药物微粒,提高药物的生物利用度和疗效;在建材行业,超细粉磨技术可以用于生产高性能的混凝土和陶瓷材料。
超细粉磨技术具有许多优势,例如提高物料的表面积,增加反应速率,提高产品的性能等。
然而,这种技术也面临着一些挑战,如粉碎过程中的能耗较高,设备磨损严重,以及粉碎产物的团聚等问题。
我国的超细粉磨技术经过多年的发展,已经取得了显著的进步。
不仅实现了设备的国产化,而且在粉碎工艺和应用研究方面也取得了重要突破。
目前,我国已经能够自主设计和制造各种类型的超细粉磨设备,满足了国内市场的需求。
展望未来,我国的超细粉磨技术将继续保持快速发展的势头。
微纳米加工制造技术的研究与应用
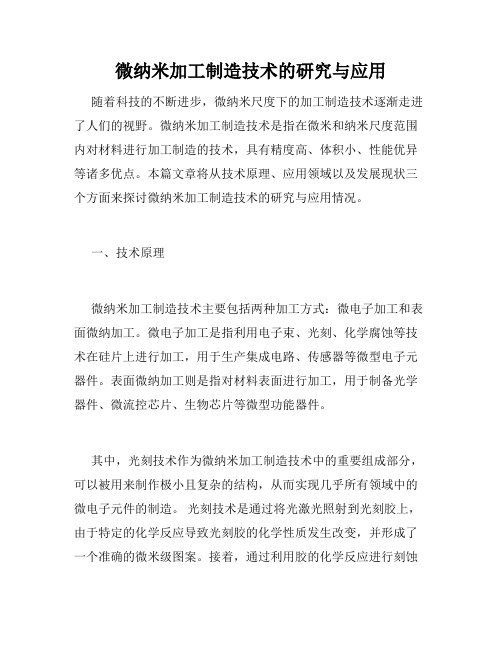
微纳米加工制造技术的研究与应用随着科技的不断进步,微纳米尺度下的加工制造技术逐渐走进了人们的视野。
微纳米加工制造技术是指在微米和纳米尺度范围内对材料进行加工制造的技术,具有精度高、体积小、性能优异等诸多优点。
本篇文章将从技术原理、应用领域以及发展现状三个方面来探讨微纳米加工制造技术的研究与应用情况。
一、技术原理微纳米加工制造技术主要包括两种加工方式:微电子加工和表面微纳加工。
微电子加工是指利用电子束、光刻、化学腐蚀等技术在硅片上进行加工,用于生产集成电路、传感器等微型电子元器件。
表面微纳加工则是指对材料表面进行加工,用于制备光学器件、微流控芯片、生物芯片等微型功能器件。
其中,光刻技术作为微纳米加工制造技术中的重要组成部分,可以被用来制作极小且复杂的结构,从而实现几乎所有领域中的微电子元件的制造。
光刻技术是通过将光激光照射到光刻胶上,由于特定的化学反应导致光刻胶的化学性质发生改变,并形成了一个准确的微米级图案。
接着,通过利用胶的化学反应进行刻蚀过程,在硅片上形成相应的微米级图案,最终得到期望的微电子元件。
二、应用领域微纳米加工制造技术的应用领域非常广泛,其中最为突出的是微电子元件的制造。
微电子元器件是现代电子技术的基础,能够被广泛应用在计算机芯片、手机、智能家居、医疗仪器等方面。
采用微纳米加工制造技术生产的微电子元器件,具有体积小、功耗低、性能稳定等优势,并能够满足各类电子设备对于小型、轻量化的要求,同时又提高了电子设备的集成度和性能。
除此之外,微纳米加工制造技术还可以被用于制备精密光学器件,如光纤通信器件、平面显示器件等,在制造过程中,可精确控制器件的微型化和性能改善。
同时,微纳米加工技术还可以用于生物芯片和生命科学领域,如DNA/蛋白质芯片、细胞芯片等的制备。
通过微纳米加工技术制造的生物芯片,能够实现对生命活动的微观探测,为生命科学研究提供了重要手段和技术支持。
三、发展现状随着微纳米加工制造技术的不断发展,相关技术也得到了迅速发展。
微纳米加工技术的研究及其应用

微纳米加工技术的研究及其应用随着先进制造业和电子产业的不断发展,越来越多的产品需要小型化和微型化,这引发了微纳米加工技术的研究和应用。
微纳米加工技术是一种用于制造微型器件的技术,利用先进的加工方法和设备在微米和纳米级别上进行加工。
一、微纳米加工技术的种类微纳米加工技术包括多种方法,例如光刻、离子束刻蚀、电子束刻蚀、激光切割和原子力显微镜刻蚀等。
光刻是一种利用光敏材料和紫外线曝光的方法,能制造出高精度的微型结构。
离子束刻蚀和电子束刻蚀则是利用离子束和电子束将材料刻蚀成所需的形状。
激光切割则是利用激光打孔或切割材料,制造微型结构。
原子力显微镜刻蚀是一种利用原子力显微镜在表面进行切割和刻蚀的方法。
二、微纳米加工技术的应用微纳米加工技术在各种领域中有广泛的应用,例如电子、光学、生物医学等。
在电子领域,微纳米加工技术被广泛应用于制造集成电路、传感器、微处理器等微型电子器件。
随着科技发展,其应用范围也越来越广泛,包括智能手机、平板电脑、计算机等各种电子设备。
光学领域是另一个微纳米加工技术的主要应用领域。
在光学器件的制造过程中,需要由微纳米加工技术加工制造折射、反射、衍射等微型结构,以达到所需的光学性能。
生物医学领域也是微纳米加工技术的一个主要应用领域。
微纳米加工技术可用于制造生物医学传感器、仿生芯片、微型结构和智能药物递送系统等。
通过微纳米加工技术制造出来的微型结构和组件可以准确高效地实现对生物体的检测、研究和治疗。
三、微纳米加工技术的未来发展微纳米加工技术的未来发展前景十分广阔。
随着对微型器件的需求不断增加和微纳米加工技术的不断提升,未来将有更多的微型器件和微型结构投入到生产制造中,从而带动整个产业的发展和经济的增长。
在科技发展的进程中,微纳米加工技术也将不断改进和完善,推动着科技进步的步伐。
未来,将会有更多的研究者加入到微纳米加工技术的研究和应用中,利用这一技术开发更多更先进的微型器件,为人类生产生活的方方面面提供更好的解决方案。
微纳米技术的研究和应用领域

微纳米技术的研究和应用领域微纳米技术是当代科技领域最为前沿的技术之一,以微米和纳米级别的物质和结构的制备和控制为基础,涉及领域非常广泛,包括材料科学、物理学、化学、生物学、机械工程等多个学科。
本文将介绍微纳米技术的研究和应用领域。
一、生物医学领域微纳米技术在生物医学领域得到广泛应用,它可以用于制备生物传感器、各种纳米药物载体、组织工程和医学成像等领域。
其中,纳米药物载体是微纳米技术的一个研究重点,研究人员用微纳米技术制备的纳米级药物可提高药物的生物利用度、可控性、靶向性和抗癌效果等,促进了临床治疗的进步。
同时,微纳米技术也可以用于组织工程,即在微观层面上重建生物组织。
组织工程主要涉及到生长的细胞、支撑材料和生物促进物(例如生长因子)对于生物组织的生长和修复起到重要作用。
微纳米技术可以在三维空间上精确地控制生物材料的形态和结构,并且其表面性质易于改变,可以提高细胞的黏附性和增加生物促进物的附着力,从而提高组织工程的效果。
二、光电子领域微纳米技术在光电子领域的应用十分广泛。
例如,微纳米结构可以制备出纳米激光器,随着纳米技术的不断发展,纳米激光器的性能也得到大幅度提升。
同时,微纳米技术也可以制备出多彩的微结构光学器件,例如微型透镜、反射器、线阵列和光子晶体等,可以被应用于激光周波同步、光电通讯、光存储和太阳能电池等领域。
此外,微纳米技术还可以用于制备人造光叶片,用于太阳能“捕捉”和酶催化的有机光化学反应,为未来的光合成和化学合成提供了可能性。
三、纳米器件领域微纳米技术在纳米器件领域的应用也十分广泛,例如纳米电子学、纳米机器人和纳米传感器等。
其中,纳米机器人与纳米传感器的结合已成为一种新的研究方向,例如可以制备出由生物蛋白质组成的纳米机器人,可以应用于药物输送和疾病诊断等领域。
同时,微纳米技术的非常规性能可以用来制备出纳米级传感器,可以检测微量物质的存在和性质,为环境监测和生物监测等领域提供了新的可能性。
超微粉碎技术在中药领域中的研究概况

超微粉碎技术在中药领域中的研究概况随着生产技术和检验科技的不断提升,提高药物的吸收、利用和治疗效果已成为药物研发的重要方向。
超微粉碎技术是一种利用高速旋转和冷却的方法将物质粉碎为微米级粒子的技术。
由于其具有高精度、高效率和高稳定性等特点,在中药领域中得到了广泛的应用和研究。
本文将从超微粉碎技术的原理、中药领域的应用和研究进展三个方面进行综述。
超微粉碎技术原理超微粉碎技术是一种利用高速旋转和冷却的方法将物质粉碎为微米级粒子的技术。
具体过程为:将物质加入粉碎室,通过高速旋转的刀片碾磨并冷却加入的物质,从而达到超微粉碎的目的。
因此,在不同的粉碎条件下,超微粉碎技术能够制备出不同粒度大小的物质,从而满足不同领域的需求。
超微粉碎技术在中药领域中的应用对提高中药活性成分的利用率有重要意义中药中的活性成分通常分布不均,而且很小一部分才具有治疗作用。
通过超微粉碎技术,能够将其它成分过滤掉,提取出小分子活性成分,并将其制成超微粉末,以达到更高的吸收率。
对难溶性中药成分颗粒化有利中药中的一些成分难溶于水,难于溶解和吞咽。
通过超微粉碎技术,能够将这些难溶的成分制成微粒,提高水溶性和生物利用度。
对药物的口服途径和制剂形式有重要意义通过超微粉碎技术,制成的超微粉末可以更好地吸附在肠胃道上,避免被肠道吸收,从而增加药物的口服途径。
同时,由于超微粉末的表面积大,可以直接制成片剂、胶囊等制剂形式,从而减少加工过程和药品的管理成本。
超微粉碎技术在中药领域中的研究进展实现浸出液中提取柿温内酯的纳米级分散柿温内酯是一种新型的抗癌活性成分。
通过超微粉碎技术,将其制成纳米粉末,利用纳米分散剂制成纳米颗粒溶液,可以实现浸出液中柿温内酯的提取和分散,从而提高药效。
制备黄芩黄酮水分散粉末的研究黄芩黄酮是一种重要的药用成分。
通过超微粉碎技术,将其制成水分散粉末,可以提高水溶性和生物利用度,从而增加药效。
利用超微粉碎技术提取黄杨苷黄杨苷是一种抗肿瘤活性成分。
- 1、下载文档前请自行甄别文档内容的完整性,平台不提供额外的编辑、内容补充、找答案等附加服务。
- 2、"仅部分预览"的文档,不可在线预览部分如存在完整性等问题,可反馈申请退款(可完整预览的文档不适用该条件!)。
- 3、如文档侵犯您的权益,请联系客服反馈,我们会尽快为您处理(人工客服工作时间:9:00-18:30)。
超微细纳米研磨技术在纳米科技上应用与研讨传统型之研磨机因受限于研磨室内之热交换只靠研磨室表面之热夹套层来做热交换,因此当研磨室之大小从实验型放大到量产型时,热交换面积之放大比例因无法与研磨室体积之放大比例均一,导致无法将实验型研磨机所得到之结果等比例地放大到量产型之机台。
同时,对于对温度较敏感或纳米级材料之应用,往往因热交换面积无法随研磨室之体积等比例放大,导致其量产型研磨机之产能无法等比例放大,甚至质量因研磨室内所承受之动力密度不够而无法达到要求。
本文所介绍之新一代双缸型设计之研磨机则将研磨室之体积缩小,并增加热交换面积且使其与研磨室之体积成固定比例,如此不管研磨室之体积大小为何,其热交换面积与研磨室大小成固定比例,可使单位研磨室体积之动力密度不受研磨室大小之影响,达到实验型研磨机之研发结果与量产型研磨机在同一品质下之产能等比例放大之目的,同时对于较难分散研磨或对温度较敏感之应用及纳米级材料之分散研磨皆能运用无碍。
关键词:传统型研磨机(Conventionalfullspaceagitationmills)、放大(Scale-up)、纳米级材料(Nano-sizematerial)、动力密度(Powerdensity)、新一代双缸型设计之研磨机(Doublecylindricalannulargapmills)引言随着3C产品之轻、薄、短小化及纳米尺度材料应用之白热化,如何将超威细研磨技术应用于纳米材料之制作及分散研磨已成为当下之重要课题。
传统产业所需之染料、涂料及油墨之产品粒径需求只到微米级,所需之分散研磨技术门坎较低,同时因为该产品之单价较低,所以研发较不受到重视。
但目前国内上述大部分之传统产业业者已逐渐将其产品从传统之微米级尺寸产品应用领域转型到高科技所需之之纳米级尺寸产品所需之材料,如薄膜型液晶显示器(TFTLCD)所需之彩色光阻(colorresist)、打印机所需之喷墨(jetinks)、被动组件、光电产业及生化产业所需之纳米级材料等,因上述高科技所需之纳米级尺寸之材料单价较高,每公斤约为数千到数万元,且不同产品或厂家所需之规格亦不同,所以研发便成为产业转型之重要课题。
但由于传统型设计之单缸型研磨机受限于热交换只来自于研磨室表面之热夹套层,故对于不同研磨室体积之研磨机之产能无法满足线性放大之需求。
相反地,本文所介绍之新一代双缸型设计之研磨机则将研磨室之体积缩小,并增加热交换面积且使其与研磨室之体积成固定比例,如此不管研磨室之体积大小为何,其热交换面积与研磨室大小成固定比例,可使单位研磨室体积之动力密度不受研磨室大小之影响,达到实验型研磨机之研发结果与量产型研磨机在同一质量下之产能等比例放大之目的,同时对于较难分散研磨或对温度较敏感之应用及纳米级材料之分散研磨皆能运用无碍,本文将详细地对上述之论点做一报告并以实例来说明之。
1.输入比能量(Massspecificenergyinput)与动力密度(powerdensity)之定义1.1输入之比能量:输入之比能量当以循环式操作(recirculationoperatingmode)时,比能量之计算为自启动研磨机后到停机时之总累积消耗之有效动力除以浆料之批次量,每单位时间之产能与该研磨室所承受之有效消耗动力成正比即由上可知,每单位时间之产能与该研磨室所承受之有效消耗动力成正比,但此关系只适用于当研磨机在合理的参数操作下方可成立。
限于篇幅,本文不再对此做更深一步探讨。
1.2研磨室所承受之动力密度(Powerdensityinthegrindingchamber):在分散及研磨的应用实例中,有很多应用的质量要求唯有在单位体积之研磨室在受到某一程度之动力强度时方可达到。
以定量来分析,若以Pv来表示单位体积研磨室所受到之动力消耗,即以Pv 来表示单位体积研磨室所受到之动力消耗例如下列针对纳米尺度材料之要求或温度很敏感或之应用,除非在高动力密度条件下来分散研磨,否则很困难达到所欲之质量要求。
∙于分散研磨过程中,浆料温度不得超过40ºC,且需将颜料研磨到20-80nm 纳米级之粒径,以期达到最佳之透明度、色浓度或光泽之要求,如彩色光阻、喷墨,…。
∙于分散研磨过程中,浆料温度不得超过35-40ºC,且需将水性之颜料分散研磨并达到最大之色浓度。
∙于分散研磨过程中,浆料温度不得超过50ºC,且需将印刷油墨之色膏分散研磨到色片等级之色泽及透明度要求之油墨。
∙于分散研磨过程中,浆料温度不得超过40ºC,且需将碳黑分散研磨成色膏以应用于工业用或汽车用之表面漆,并达到最高之质量要求。
∙于分散研磨过程中,浆料温度不得超过45ºC之靠紫外线熟化型(UV-curing)之印刷油墨色膏。
2.传统型研磨机于不同研磨室尺寸放大时所遇到之困难2.1动力密度与研磨室大小之关系:如图一所示,传统型研磨机之原理为泵浦(pump)将浆料从研磨室之一端打入研磨室内,研磨室内之搅拌单元持续地打动磨球,使磨球在研磨室内均匀地运动,浆料于研磨室内的移动过程中,依流量或黏滞性(viscosity)大小不同而与磨球产生不同大小之剪切力以产生分散研磨之效果,当然为了避免磨球流出研磨室,在研磨室的另一端设计有滤网以避免磨球跑出研磨室。
传统之研磨机传统之研磨机中只能靠研磨室外层之热夹套层作热交换,通常此型之研磨机于研磨室体积较小时。
如实验型研磨机之研磨室1L,要达到对温度敏感且较难分散研磨之浆料要求,Pv=2kW/l.或许没有问题,但一旦欲将实验型研磨机之研磨机参数放大到量产机型时则产生问题,理由如下:理由由上可知,当研磨室体积放大10倍时,从式〔12〕可得知热交换面积只能放大102/3=4.6倍,为了避免浆料温度上升,动力密度必然只能增加4.6倍而非10倍。
原因如下:原因假设动力密度与研磨室热交换面积成正比,即由上可得知,传统型研磨机于放大时,其热交换面积并无法与动力密度等比例放大,而是与研磨室直径成反比。
所以当传统型研磨机欲将实验型研磨机之参数放大到量产型研磨机时,受限于热交换面积无法等比例随研磨室体积之增加而等比例增加,为了避免浆料温不过高,势必降低动力密度。
如此将导致产能降低,或研磨效果降低,甚至对此上述纳米尺寸材料之分散研磨或对温度较敏感之应用则无法胜任。
所以传统研磨机若欲从事大量生产,唯一方法为选购多部小型研磨机,如此虽可达到量的要求,但在设备数量及人员之营运成本上将大大提高,已无竞争力。
2.2研磨室体积放大(ScaleUp)之估算方法:从实验型研磨机可以得到欲达到某一质量要求所需之比能量Em值,若欲放大到量产之产能mprod(t/h)时,从公式〔2〕可计算出所需之有效动力消耗为:公式〔2〕可计算出所需之有效动力消耗3.新一代研磨机之设计–研磨室体积小、高效率、磨球在研磨室可依特定轨迹而循环(Small-volumehigh-performancemillswithadefinedinternalgrindingmed iacirculation)3.1研磨机产能依研磨室体积线性放大之条件:若欲使研磨机在高动力密度下,可以任意放大且维持浆料之温度不变下而得到一样的质量,唯一方法为需让研磨机之热交换面积与动力密度成固定比例。
如此任何尺寸之研磨机之研磨效率将不受研磨机研磨室体积大小而影响,同时热交换效果亦将不受研磨室大小之变化而变化,即需满足下列之条件:满足条件3.2新一代研磨机之构造–动力密度之大小可以不受研磨室之大小而改变(Structureandfunctionofamultiple-zonePerlmillwithanonsize-dependentpowerdensit y)图二“ Puhler NANO Advantis ”新一代双缸型高效率研磨机之原理及构造图三PuhlerNANOAdvantis新一代量产型双缸型研磨机之外观图四新一代研磨机之转子(rotor)设计图五新一代实验型双缸型研磨机之外观如图二所示“PuhlerNANOAdvantis”型研磨机之设计即可满足上述动力密度之大小不受研磨室大小而改变。
Advantis之构造乃将一个中空之转子套在由二个静置之内外缸所形成之研磨室间,内外缸及转子皆有热夹套层设计以供热交换使用,浆料由研磨室上方进入研磨室后,将经过三个阶段的分散研磨而后利用离心力原理由滤网流出研磨室。
第一阶段为经由转子之转动而生强力涡流区以进行预分散效果,然后经由转子外层上之插梢与外缸上插梢撞击磨球所产生之强力之撞击及剪切力区来分散研磨浆料,最后浆料与磨球一起流经转动之转子之内层与静置之内缸所形成之间隙区产生之剪切力做最后一阶段之分散研磨。
磨球与浆料一起运动到内缸之上缘后,受到离心力作用之影响磨球将往外甩而由转子上设计之间隙(gap)跑回强力涡流区,即预分散区,然后随着浆料再进行第二阶段之研磨,如此在研磨室内循环,而浆料则受到离心力之影响往内甩,经由滤网而流出。
因磨球一直在研磨室内循环,所以可以避免因磨球挤压所产生之压力,此设计可以适用于大流量之应用。
一般对同一研磨室体积大小而言,PuhlerNANOAdvantis之流量可为传统型之10倍以上,且压力不致上升。
此设计于研磨室放大时,仅需将研磨室之直径与长度做等比例之放大即可。
故从实验型到量产型之各种机种皆可以任意放大,热交换面积与研磨室大小之比例将固定,不受研磨室之大小而改变。
由于本机型之热交换面积非常大(内缸、外缸、转子皆有热交换之夹套层设计),所以无论研磨室之大小为何,皆可以维持单位体积研磨室之动力密度为P/V=4kW/l,同时可确保从实验到量产之各机型之应用皆可以将产能等比例放大,质量亦可以均一。
3.3如何提高研磨之产能及质量之方法:本文以透明性颜料色膏应用为例,以循环式操作方式,采用量产型之研磨机台来比较在不同之转子转速下而产生之不同动力密度时对产品质量及产能所产生之影响做一探讨。
从图3.a之制作乃以动力密度为2.1kW/l时,定义所需色膏之透明之质量要求为Xstandard,其所需之研磨时间定义为tstandard,然后再利用提高转子之转速以提高不同之动力密度,于动力密度分别为3.0及3.3kW/l时,分别做出透明度与研磨时间之关系图,当然为了维持色膏质量不受浆料温度改变之影响,于不同之转子运速时,需调整冷却水之大小以维持相同之浆料温度。
由图3.a可以得知:∙当动力密度为2.1kW/l时,即使延长研磨时间,对质量之影响亦非常有限,如图所示当延长时间到100%时,透明度只增加到104%。
∙当动力密度提高到3kW/l时,仅需动力密度为2.1kW/l时之61%之时间即可达到质量要求Xstandard,若延长研磨时间,则仍可以继续提高透明度,如图所示,最后可提高27%之透明度。