柔性工装系统多点定位的自适应优化
柔性作业车间多目标动态调度

参考内容
引言
在制造业中,车间调度是一个关键问题,它影响着生产效率、生产成本和产品 质量。近年来,多目标柔性作业车间调度问题(MFOJSP)受到了广泛。 MFOJSP是指在作业车间中,同时考虑多个目标,如加工时间、成本、质量等, 并通过对这些目标的优化,实现车间调度的最优化。
模型建立
1、定义问题
2、鲁棒性要求:由于生产过程中的不确定性因素较多,算法需要具有一定的 鲁棒性,以应对各种异常情况。
3、优化目标多样性:多目标动态调度需要考虑多个不同的优化目标,例如生 产成本、交货期、设备利用率等。这需要算法具有处理多目标优化问题的能力。
4、求解难度:由于多目标动态调度的复杂性,求解难度较大,需要采用高效 的算法和优化技术。
三、现状与挑战
目前,针对柔性作业车间多目标动态调度问题,研究者们已经提出了一系列的 方法和算法。例如,遗传算法、粒子群优化算法、模拟退火算法等。这些算法 可以有效地解决单目标静态调度问题,但在多目标动态调度方面仍然存在一些 挑战。具体来说,以下几个方面的问题亟待解决:
1、实时性要求:多目标动态调度需要快速地响应生产过程中的变化,因此需 要算法具有实时性。
3、大数据分析与预测:利用大数据技术对生产数据进行挖掘和分析,以获得 更准确的生产预测和优化方案。
4、人机协同:将人类智慧和机器智能相结合,实现人机协同的调度系统。人 类智慧可以提供灵活性和创造性,而机器智能可以提供高效性和准确性。
5、绿色制造与可持续发展:在调度优化过程中考虑能源消耗、碳排放等因素, 以实现绿色制造和可持续发展。
一、柔性作业车间概述
柔性作业车间是一种灵活的生产组织形式,它可以根据市场需求的变化快速调 整生产计划,以满足客户的个性化需求。在柔性作业车间中,设备、人员和物 料等资源可以动态地配置和调整,以适应不同的生产任务。这种生产组织形式 的灵活性使得它在制造业中得到了广泛应用。
智能制造中柔性制造系统的设计与优化

智能制造中柔性制造系统的设计与优化一、引言随着科技的不断进步和信息技术的广泛应用,智能制造概念的兴起和推广,柔性制造系统作为一种高度自适应和灵活性强的生产系统模式,越来越受到制造业的重视和认可。
本文将详细探讨智能制造中柔性制造系统的设计与优化,从理论和实践的角度来分析其优势和应用。
二、柔性制造系统的概述柔性制造系统(Flexible Manufacturing System,FMS)是一种可以快速适应生产变化需求的自动化生产系统。
它利用计算机技术和先进的机电一体化技术,使得生产线能够快速调整和适应不同产品的制造要求。
柔性制造系统主要包括物料搬运系统、加工装备、控制系统和信息系统等组成部分,通过这些组成部分的协同工作,实现了对生产过程的灵活调度和管理。
三、柔性制造系统的设计与优化1. 柔性制造系统的设计原则柔性制造系统的设计需要考虑以下原则:(1)任务分配合理:根据产品的特点和生产要求,合理分配任务至多个加工单元,实现生产过程的灵活调度。
(2)模块化设计:采用模块化的设计思想,使得不同的任务可以独立进行,从而提高系统的可维护性和可扩展性。
(3)信息化管理:通过信息系统实现对生产过程的追踪和控制,提高生产计划的准确性和实时性。
(4)资源共享:多个加工单元之间应该能够共享资源,如设备、工具和人力资源等,提高资源利用效率。
2. 柔性制造系统的优化方法针对柔性制造系统的优化,可以从以下几个方面进行考虑:(1)生产调度优化:通过算法模型和计算机软件优化生产调度,实现生产过程的高效运行和资源的合理利用。
(2)制造过程优化:分析柔性制造系统的每个环节,对生产过程进行优化,例如优化物料搬运路径和加工工艺等。
(3)质量控制优化:通过引入自动化检测和控制技术,提高产品的质量稳定性和一致性。
(4)资源管理优化:综合考虑设备利用率、能源消耗和人力需求等因素,对资源进行合理分配和规划,提高生产效率和资源利用效率。
四、柔性制造系统在智能制造中的应用1. 自动化生产柔性制造系统利用先进的机电一体化技术,能够实现生产过程的自动化控制和管理。
柔性模具成形的6大关键技术,不是只能做飞机蒙皮零件
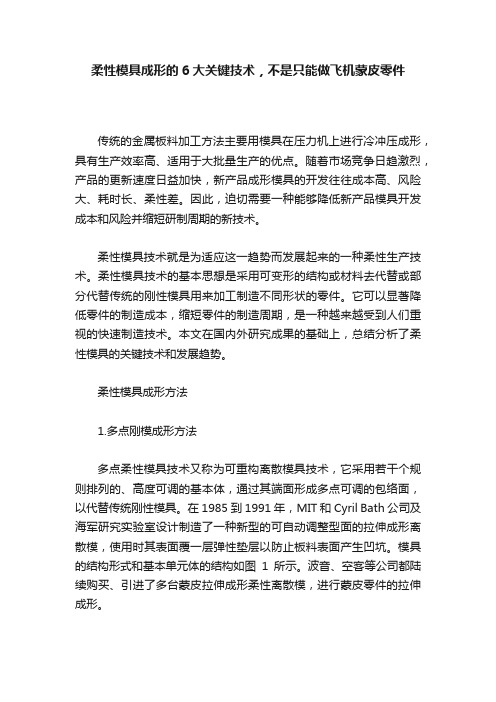
柔性模具成形的6大关键技术,不是只能做飞机蒙皮零件传统的金属板料加工方法主要用模具在压力机上进行冷冲压成形,具有生产效率高、适用于大批量生产的优点。
随着市场竞争日趋激烈,产品的更新速度日益加快,新产品成形模具的开发往往成本高、风险大、耗时长、柔性差。
因此,迫切需要一种能够降低新产品模具开发成本和风险并缩短研制周期的新技术。
柔性模具技术就是为适应这一趋势而发展起来的一种柔性生产技术。
柔性模具技术的基本思想是采用可变形的结构或材料去代替或部分代替传统的刚性模具用来加工制造不同形状的零件。
它可以显著降低零件的制造成本,缩短零件的制造周期,是一种越来越受到人们重视的快速制造技术。
本文在国内外研究成果的基础上,总结分析了柔性模具的关键技术和发展趋势。
柔性模具成形方法1.多点刚模成形方法多点柔性模具技术又称为可重构离散模具技术,它采用若干个规则排列的、高度可调的基本体,通过其端面形成多点可调的包络面,以代替传统刚性模具。
在1985到1991年,MIT和Cyril Bath公司及海军研究实验室设计制造了一种新型的可自动调整型面的拉伸成形离散模,使用时其表面覆一层弹性垫层以防止板料表面产生凹坑。
模具的结构形式和基本单元体的结构如图1所示。
波音、空客等公司都陆续购买、引进了多台蒙皮拉伸成形柔性离散模,进行蒙皮零件的拉伸成形。
国内北京航空制造工程研究所在现有柔性多点模具基础上,针对大型柔性多点模具,采用新型的调形驱动机构及伺服轴离合复用技术,实现与冲头驱动源分合,大大减少了驱动电机的数量,并开发出了具有价格竞争力的蒙皮拉伸成形多点模系统。
李明哲从90年代初期就开始进行离散模冲压技术的研究,开发了专用成形设备,取得了一系列的成果,在建筑结构件与装饰件、高速列车流线型车头覆盖件、船体外板及人脑颅骨修复体等产品的成形上发挥了重要作用。
图2(a)是利用片层式离散模进行的拉弯成形实验装置。
离散模应用拉弯成形时,由于型材拉弯零件截面复杂不同于板料拉形,因此需要模块化的结构。
工业机器人中的柔性夹具设计与优化

工业机器人中的柔性夹具设计与优化工业机器人作为现代制造业的重要装备,已经广泛应用于各个行业的生产线上。
在现代制造业中,柔性夹具作为一种重要的工具也得到了广泛的应用。
柔性夹具的设计与优化对于提高生产线效率,降低成本,提高产品质量都起到了至关重要的作用。
本文将针对工业机器人中的柔性夹具设计与优化进行探讨与分析。
首先,我们来了解什么是柔性夹具。
柔性夹具是一种可以根据工件形状和尺寸自动调整的夹具,其主要特点是具有良好的适应性和灵活性。
与传统的夹具相比,柔性夹具能够自适应各类工件形状,不需要频繁更换,提高了工作效率和生产线的稳定性。
在工业机器人中,柔性夹具的设计与优化需要考虑以下几个方面:首先,要考虑工件形状的适配性。
不同的工件形状需要设计相应的夹具结构来保持工件的稳定性和安全性。
柔性夹具设计时应该考虑工件的形状、尺寸以及表面特性等因素,调整夹具的形状和尺寸,确保夹具与工件之间的接触面积最大化,从而提高夹具的夹持力和稳定性。
其次,要考虑工件尺寸的适应性。
不同尺寸的工件需要设计不同尺寸的夹具来夹持。
柔性夹具应该具备自动调节夹持力的能力,可以根据工件尺寸的变化而自动调整夹持力大小,确保夹具与工件之间的紧密接触,从而提高夹持效果。
此外,夹具的材料选择也是关键。
夹具的材料应具备足够的强度和刚性,能够承受机器人的运动和重力负荷。
同时,夹具的材料还应具备较好的摩擦系数和抗磨损性能,从而提高夹持的稳定性和可靠性。
优化柔性夹具设计的关键在于提高其自适应性和智能化程度。
通过引入传感器和控制系统,可以实现对夹具尺寸、形状和夹持力的实时调整和监测。
例如,可以利用视觉传感器对工件形状进行扫描和分析,从而确定夹具的形状和尺寸。
同时,可以利用力传感器对夹具与工件之间的压力和接触状态进行监测,及时调整夹持力,避免工件变形或夹具滑脱。
另外,优化柔性夹具的设计还需要考虑生产线的整体效率和自动化程度。
柔性夹具与机器人之间的协同工作可以实现生产线的自动化和智能化。
智能制造中的柔性生产系统设计与优化研究

智能制造中的柔性生产系统设计与优化研究智能制造是当今制造业发展的重要方向,而柔性生产系统作为其中关键的组成部分,对于企业的生产效率和灵活性具有重要影响。
本文将对智能制造中柔性生产系统的设计与优化进行深入研究,探讨其在提高生产自动化程度、优化效率和降低成本方面的综合应用。
一、智能制造中柔性生产系统的设计原则柔性生产系统的设计是智能制造中重要的环节,它直接关系到制造业的生产效率和竞争力。
在设计柔性生产系统时,需要遵循以下原则:1. 模块化设计:将整个生产系统划分成若干个相对独立的模块,使得每个模块能够单独运作,并能够灵活组合。
这样可以提高生产系统的灵活性和适应性,便于对不同产品的生产进行调整。
2. 多功能性设计:每个模块应具备多种功能,能够适应不同产品的制造需求。
通过充分利用机器人、自动化设备和先进的控制系统,使得柔性生产系统能够自动完成多种工序,提高生产的效率和质量。
3. 信息化设计:在柔性生产系统中,信息的传输和处理是至关重要的。
通过建立先进的信息管理系统,实现对生产过程的实时监控和优化调整。
信息化设计还可以加强不同模块之间的协作和沟通,提高生产系统的整体效能。
二、智能制造中柔性生产系统的优化方法柔性生产系统的优化是智能制造中的重要任务之一。
通过合理的优化方法,可以进一步提高生产效率和降低成本。
1. 生产任务调度优化:在柔性生产系统中,生产任务的调度对于提高生产效率至关重要。
利用优化算法,根据不同的生产任务和生产设备状况,合理安排任务的执行顺序和时间,实现资源的最优利用,减少生产时间和能耗。
2. 设备配置优化:柔性生产系统中的设备配置需要根据具体的生产需求进行合理调整。
通过对设备的排布和组合进行优化,能够减少工序之间的传送时间和能耗,提高生产效率。
3. 控制系统优化:柔性生产系统的控制系统是实现生产自动化的关键。
通过优化控制算法和系统参数的选择,可以减少设备之间的冲突和干扰,提高生产系统的稳定性和可靠性。
机械装备中的自适应控制与优化技术
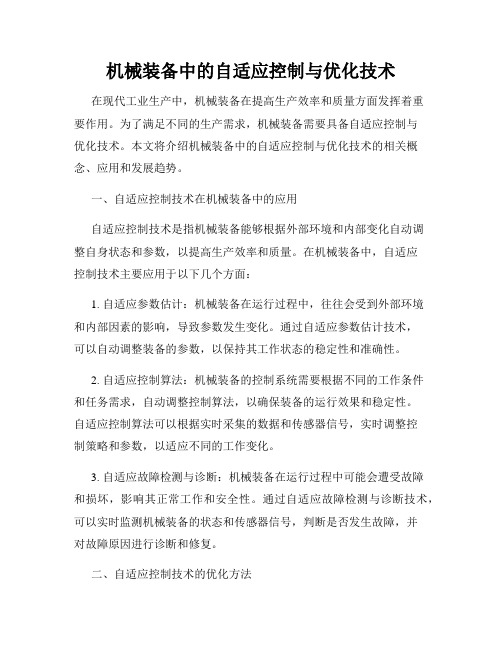
机械装备中的自适应控制与优化技术在现代工业生产中,机械装备在提高生产效率和质量方面发挥着重要作用。
为了满足不同的生产需求,机械装备需要具备自适应控制与优化技术。
本文将介绍机械装备中的自适应控制与优化技术的相关概念、应用和发展趋势。
一、自适应控制技术在机械装备中的应用自适应控制技术是指机械装备能够根据外部环境和内部变化自动调整自身状态和参数,以提高生产效率和质量。
在机械装备中,自适应控制技术主要应用于以下几个方面:1. 自适应参数估计:机械装备在运行过程中,往往会受到外部环境和内部因素的影响,导致参数发生变化。
通过自适应参数估计技术,可以自动调整装备的参数,以保持其工作状态的稳定性和准确性。
2. 自适应控制算法:机械装备的控制系统需要根据不同的工作条件和任务需求,自动调整控制算法,以确保装备的运行效果和稳定性。
自适应控制算法可以根据实时采集的数据和传感器信号,实时调整控制策略和参数,以适应不同的工作变化。
3. 自适应故障检测与诊断:机械装备在运行过程中可能会遭受故障和损坏,影响其正常工作和安全性。
通过自适应故障检测与诊断技术,可以实时监测机械装备的状态和传感器信号,判断是否发生故障,并对故障原因进行诊断和修复。
二、自适应控制技术的优化方法自适应控制技术的优化方法主要包括以下几个方面:1. 模型参数优化:通过分析机械装备的传感器信号和工作数据,建立合适的系统模型,并利用优化算法对模型参数进行优化,以提高系统的稳定性和响应性能。
2. 控制策略优化:根据机械装备的工作特点和任务需求,选择合适的控制策略,并利用优化算法调整控制参数,提高系统的控制精度和效率。
3. 故障诊断与修复优化:通过分析机械装备的故障数据和传感器信号,建立合适的故障诊断模型,并利用优化算法对故障诊断和修复过程进行优化,提高故障诊断的准确性和效率。
三、机械装备中自适应控制与优化技术的发展趋势随着科技的不断进步,机械装备中的自适应控制与优化技术也在不断发展。
薄壁件多点加工时定位点的优化选择
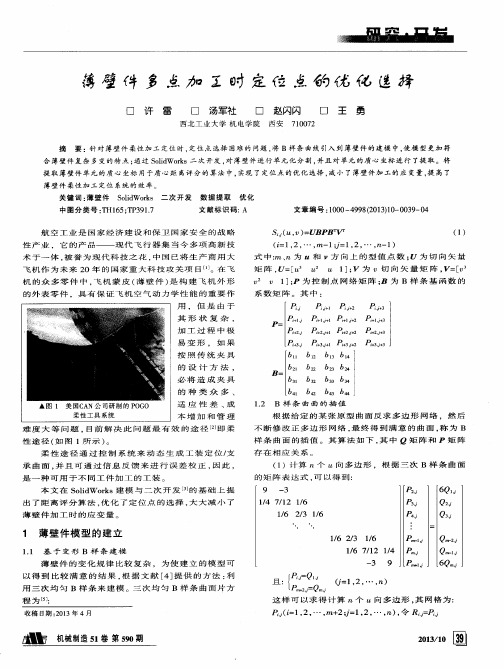
( 1 )
式 中: m、 / / , 为 u和 l , 方 向上 的型 值 点数 ; U 为 切 向 矢 量
矩阵 , =[
u u 1 ] ; V 为 切 向 矢 量 矩 阵 , =[ 口
的矩 阵表 达式 , 可 以得到 :
9 —3
难 度 大 等 问题 , 目前 解 决 此 问 题 最 有 效 的 途 径 l 2 即 柔
性途 径 ( 如 图 l所 示 ) 。
柔 性 途 径 通 过 控 制 系统 来 动 态 生 成 工 装 定 - 5 2/  ̄ :
承曲面 , 并 且 可 通 过信 息 反 馈 来 进 行误 差 校 正 , 因此 , 是 一 种 可 用 于 不 同工 件 加 工 的 工 装 。 本 文在 S o l i d Wo r k s建 模 与 二 次 开 发 的 基 础 上 提
出 了距离 评分 算 法 , 优 化 了定 位 点 的 选 择 , 大 大 减 小 了 薄壁 件加 工 时 的应变 量 。
尸2 J P3 √ P4 J
●
6 Q1 J
Q2 J
1 , 4 7/ 1 2 1 / 6 1 / 6 2/ 3 l / 6
Q3 J Q Q—t
必 将 造 成 夹 具
b 3 1 b 3 2 b 3 3 6 3 4 I
b 4 l 6 4 2 6 4 3 6 “
的种 类 众 多 、
▲ 图 1 美 国C A N公 司研 f 『 P O G 0
柔性 工 具 系 统
适 应 性 差 、 成 本 增 加 和 管 理
机 的众 多 零 件 中 , 飞 机蒙 皮 ( 薄 壁件 ) 是 构 建 飞 机 外 形 的外 表 零 件 。具 有 保 证 飞 机 空 气 动 力 学 性 能 的 重 要 作
柔性制造系统的性能评价与改进
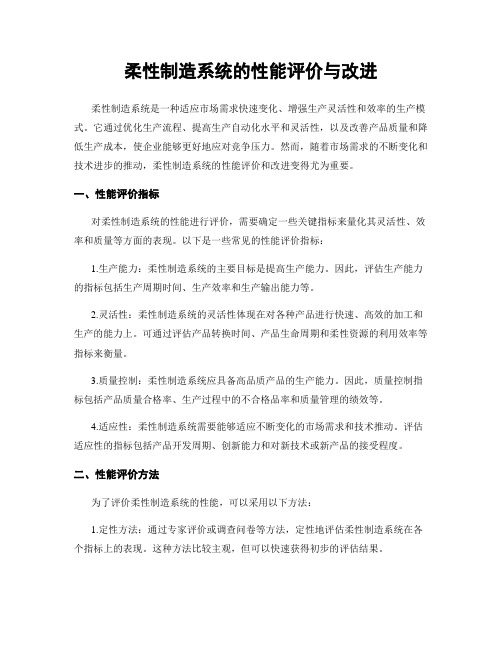
柔性制造系统的性能评价与改进柔性制造系统是一种适应市场需求快速变化、增强生产灵活性和效率的生产模式。
它通过优化生产流程、提高生产自动化水平和灵活性,以及改善产品质量和降低生产成本,使企业能够更好地应对竞争压力。
然而,随着市场需求的不断变化和技术进步的推动,柔性制造系统的性能评价和改进变得尤为重要。
一、性能评价指标对柔性制造系统的性能进行评价,需要确定一些关键指标来量化其灵活性、效率和质量等方面的表现。
以下是一些常见的性能评价指标:1.生产能力:柔性制造系统的主要目标是提高生产能力。
因此,评估生产能力的指标包括生产周期时间、生产效率和生产输出能力等。
2.灵活性:柔性制造系统的灵活性体现在对各种产品进行快速、高效的加工和生产的能力上。
可通过评估产品转换时间、产品生命周期和柔性资源的利用效率等指标来衡量。
3.质量控制:柔性制造系统应具备高品质产品的生产能力。
因此,质量控制指标包括产品质量合格率、生产过程中的不合格品率和质量管理的绩效等。
4.适应性:柔性制造系统需要能够适应不断变化的市场需求和技术推动。
评估适应性的指标包括产品开发周期、创新能力和对新技术或新产品的接受程度。
二、性能评价方法为了评价柔性制造系统的性能,可以采用以下方法:1.定性方法:通过专家评价或调查问卷等方法,定性地评估柔性制造系统在各个指标上的表现。
这种方法比较主观,但可以快速获得初步的评估结果。
2.定量方法:采用各种数据收集和分析方法,量化评估柔性制造系统在各个指标上的表现。
例如,可以通过收集生产数据、质量数据和设备运行数据等,使用统计分析方法来获得更准确的评价结果。
3.多指标综合评价:将多个评价指标综合考虑,建立评价模型来评估柔性制造系统的综合性能。
可以采用模糊综合评价法、层次分析法或主成分分析法等方法来进行综合评价。
三、性能改进措施基于性能评价结果,针对柔性制造系统的不足之处,可以采取一些改进措施来提高其性能。
以下是一些常见的改进措施:1.优化生产流程:通过优化生产流程,深入分析并找出瓶颈环节和低效操作,以提高生产效率和降低生产成本。
- 1、下载文档前请自行甄别文档内容的完整性,平台不提供额外的编辑、内容补充、找答案等附加服务。
- 2、"仅部分预览"的文档,不可在线预览部分如存在完整性等问题,可反馈申请退款(可完整预览的文档不适用该条件!)。
- 3、如文档侵犯您的权益,请联系客服反馈,我们会尽快为您处理(人工客服工作时间:9:00-18:30)。
在现代 大型飞行 器 中 , 承力 骨 架贴 合 的是厚 度 与
控制 等手段 动态生 成所需 的定位/ 支承 曲面 , 如此 一种
很薄 的大尺度 合金 或复合材 料蒙皮 , 刚度 非 常差 , 其 加
工过程 中很容 易发生 变形 。对于该 类大型 薄壁 曲面零 件, 生产 厂家一 般采用 “ 加工 后成 型 ” 艺 。先对 平 先 工 板 材加工 周边轮廓 、 窗 、 开 开孔 , 后将 平 面半成 品进 之
功 能部 件 Fcnl u Us n n
柔・ 装 系统 多 点定位 的 自适应 优 化 I 生工
陆俊 百 周 凯
( 华大学精 密仪器 与机械 学系 , 清 北京 1 0 8 ) 0 0 4 摘 要 : 针对飞行 器大型 薄壁件 ; - 的技术 难点 。  ̄r n 开发 了基 于机器 人操作 的智能 柔性工 艺装备 系统。通 过分 析 系统 结构 和运 行原理 , 建立 了数学模 型 , 出 了多点定 位 的 自适应 优 化方 法。 该方 法根 据 给定 的 提 加 工轨迹 , 自适 应地调整 柔性 工装 系统 的定位/ 支承 分布 , 证总体 加工变 形趋近 最小 。实例验证 表 保 明, 该方 法可 以使柔性工 装 系统 的支承 分布处 于最优 状态 , 实现对 系统资 源的最佳 利用 , 满足飞行 器 大 型薄壁 件的高 速高精 度J - 需求 。 jr n
js ct n sp o r yo f xbet l gss m acrig oseie ut gpt a at e .E — ut l a o/u pr ar f eil o i yt codn p c dctn a d pi l x so i t a l on e t i f i h vy
L u b i HOU Ka U J n a ,Z i
( s g u nvr t, e ig1 0 8 , H Ti h aU i sy B in 0 0 4 C N) n ei j
Ab t a t n elg n e i l o l g s se ma i u ae y r b t s d v l p d t ov r b e n ar rf ag — s r c :I t l e tf x b e to i y t m n p lt d b o o si e eo e o sl e p o lms i icatlr e— i l n saeti c l hn-walwo k ic c i i g l r p e e ma h n n .Ad p ie o t z t n o l —p i tl c t n i r s n e y d — a t p i ai fmu t on o a i s p e e td b e v mi o i o s rb n y t m tu t r n r rn il c ii g s se sr cu e a d wo k p i cp e,t e sa ls t e t a de .Th s meh d a — h n we e tb ih ma h mai lmo 1 c i t o d
为 了克服这一 问题 , 先成 型 后加 工 ” 艺发 展 了 “ 工 起 来 。然 而 , 型后 的半 成 品 为刚 度极 差 的弹性 薄 壁 成
发 了基 于机器 人操作 的智 能柔 性 工装 系 统 , 其基 本 结
关键 词 : 行器大 型薄壁 件 柔性工艺装 备 系统 多点定位 自适 应优化 飞
Ad p ie Opi z t n o l— on o a in i Fe il o l g Sy t m a t t v mia i fMut — itL c t n lxbe T oi se o ip o n
p rme t lr s lss o t a u p  ̄ d srb to a e o t z d t k e tu e o y tm e o r e e i n a e u t h w h ts p o iti u in c n b p i e o ma e b s s fs se r s u c s, mi wh c mp o e u lt n f ce c far rf a g —s a e t i ih i r v s q ai a d e in y o ic atlr e c l hn-walwo k ic c i i g y i l r p e e ma h n n . Ke ywo ds:Aic a r e- c l i r r r f La g s a e Thn-walW okpe e;Flxb e To l g S se ;Mu t—p i o ain;Ad pi e t l r ic e i l o i y tm n li ontL c to at v
问题 : 型工序 会使 已加 工 好 的零 件周 边 轮 廓 和窗 孔 成
本文将 介绍 在柔性 工装系统 中多点 定位 的 自适应优 化
方 面的研究成 果 。
部 位产生 很大变形 , 对飞 行器 的气 动性 能 和 隐身 性 能
均 造成很 大影 响 。
1 系 结 构
针 对飞行 器大 型薄 壁 曲 面零 件加 工 的特 殊 性 , 开
工装 可用 于不 同零 件 的加 工 , 幅度 提 高 制造 柔性 和 大
效率 。
为此 , 者 与企 业 合 作 对 以柔 性 途 径 实现 “ 成 笔 先
型后加 工 ” 艺 的有 关 方 法 和 实 现 技术 进 行 了研究 。 工
行 成型处 理 , 到 曲面 蒙皮 。这 一 方法 存 在 以下 严 重 得