磨削
磨削加工中的磨削方式

磨削加工中的磨削方式磨削加工是一种精密的金属加工方法,不仅可以用于加工金属材料,还可以用于加工陶瓷、玻璃等非金属材料。
它的基本原理是在切削工具与工件之间施加外力,并且在介质中进行磨磨擦削,以达到加工的目的。
磨削加工中的磨削方式有很多种,下面将对其进行一一介绍。
1. 平面磨削平面磨削是一种磨削工艺,主要用于加工平面及其上的孔和槽。
这种加工方式通过旋转磨削轮,使其与工件表面接触,施加相应的压力和剪切力来进行磨削。
平面磨削的加工精度高,工件表面质量好,适用于加工超精密配件。
2. 内圆磨削内圆磨削是一种在工作件内部进行磨削的加工方式,主要用于加工内径大小不同的圆柱体。
这种加工方式的主要设备是内圆磨床,通过不断旋转工作件和磨削轮,结合适当的压力、速度等参数,来进行磨削加工。
3. 外圆磨削外圆磨削是一种在工作件外部进行磨削的加工方式,主要用于加工外径大小不同的圆柱体。
这种加工方式的主要设备是外圆磨床,通过不断旋转工作件和磨削轮,结合适当的压力、速度等参数,来进行磨削加工。
4. 中心磨削中心磨削是一种在两个中心点之间进行磨削加工的方式,主要用于加工圆锥体、圆柱锥体等形状的工件。
这种加工方式的主要设备是中心磨床,在加工过程中,需要较高的精度控制及对磨削力的稳定性要求。
5. 轮廓磨削轮廓磨削是一种根据工件轮廓进行磨削的加工方式,主要用于加工各种不规则形状的工件。
这种加工方式的主要设备是数控磨床,通过对工件进行高精度的三维扫描和轮廓学习,来得到工件的三维形状。
随后,根据得到的轮廓数据进行加工。
6. 微型磨削微型磨削是一种在微米尺度下进行磨削的加工方式,主要用于加工高精度、超细的微件。
这种加工方式的设备应具有高精度、高速度、低摩擦等特点,常用于制造高端光学元件、半导体芯片等高端应用领域。
总之,磨削加工中的磨削方式有很多种,不同的加工方式适用于不同的工件加工需求,需要精确控制加工参数,以保证加工效果。
随着技术的不断进步,相信未来还会涌现更多更精密的磨削加工方式,为各行各业的高精度加工需求提供更多的选择。
磨盘的不同磨削方式及其应用
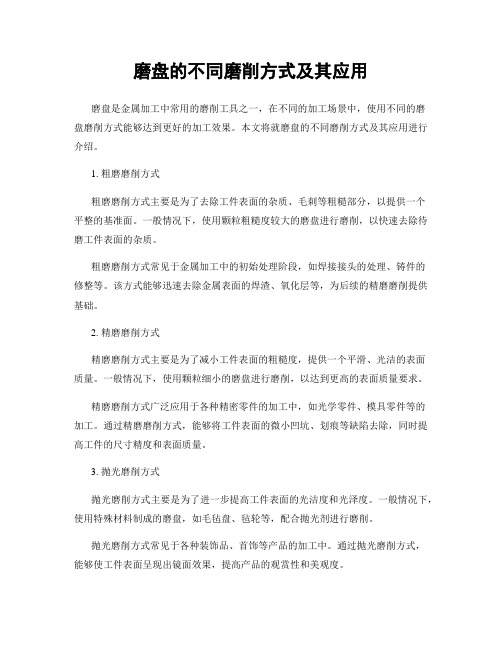
磨盘的不同磨削方式及其应用磨盘是金属加工中常用的磨削工具之一,在不同的加工场景中,使用不同的磨盘磨削方式能够达到更好的加工效果。
本文将就磨盘的不同磨削方式及其应用进行介绍。
1. 粗磨磨削方式粗磨磨削方式主要是为了去除工件表面的杂质、毛刺等粗糙部分,以提供一个平整的基准面。
一般情况下,使用颗粒粗糙度较大的磨盘进行磨削,以快速去除待磨工件表面的杂质。
粗磨磨削方式常见于金属加工中的初始处理阶段,如焊接接头的处理、铸件的修整等。
该方式能够迅速去除金属表面的焊渣、氧化层等,为后续的精磨磨削提供基础。
2. 精磨磨削方式精磨磨削方式主要是为了减小工件表面的粗糙度,提供一个平滑、光洁的表面质量。
一般情况下,使用颗粒细小的磨盘进行磨削,以达到更高的表面质量要求。
精磨磨削方式广泛应用于各种精密零件的加工中,如光学零件、模具零件等的加工。
通过精磨磨削方式,能够将工件表面的微小凹坑、划痕等缺陷去除,同时提高工件的尺寸精度和表面质量。
3. 抛光磨削方式抛光磨削方式主要是为了进一步提高工件表面的光洁度和光泽度。
一般情况下,使用特殊材料制成的磨盘,如毛毡盘、毡轮等,配合抛光剂进行磨削。
抛光磨削方式常见于各种装饰品、首饰等产品的加工中。
通过抛光磨削方式,能够使工件表面呈现出镜面效果,提高产品的观赏性和美观度。
4. 切割磨削方式切割磨削方式主要是为了通过磨削将工件切割成所需的形状和尺寸。
一般情况下,使用带有切割刃的磨盘进行磨削。
切割磨削方式常见于金属加工中的切割操作,如管材、板材等的切割。
通过切割磨削方式,能够实现高效、精确的切割操作,并具有较好的切割平整度和切割质量。
总结起来,磨盘的不同磨削方式在金属加工中起到了举足轻重的作用。
粗磨磨削方式去除工件粗糙部分,精磨磨削方式提供更高的表面质量,抛光磨削方式提升光洁度和光泽度,切割磨削方式实现快速、精确的切割操作。
这些磨削方式能够满足不同加工场景的需求,并在金属加工领域发挥重要作用。
磨削的工艺特点及应用范围

磨削的工艺特点及应用范围磨削是一种通过将磨料与工件接触并相对运动,以去除工件表面的材料来达到加工目的的工艺。
它是机械加工中常用的一种精密加工工艺,具有以下几个特点和应用范围。
首先,磨削具有高精度的特点。
由于磨削采用磨料的物理磨损作用,能够在工件表面形成较高的精度和光洁度。
这使得磨削可以在高要求的部件上进行加工,如模具、精密仪器零部件等。
其次,磨削具有高表面质量的优势。
由于磨削可产生微细破碎和位移切削,所以能够在工件表面形成比较光滑及均匀的表面。
磨削加工可将工件表面粗糙度控制在很低的范围内,以满足高精度零部件的要求。
第三,磨削可以加工各种材料。
由于磨料多种多样,几乎可以加工所有的工程材料,如钢、铸铁、有色金属、陶瓷、石材等。
而且磨削还可以加工硬度高、韧性好的材料,如硬质合金、高速钢等。
因此,磨削具有广泛的应用范围。
第四,磨削是一种高效率的加工方法。
尽管磨削是一种相对慢速的金属切削方式,但具有高的切削效率。
这是由于磨削通过很薄的材料去除率来实现加工,而它的单位材料去除率比其他加工方法要高得多。
此外,磨削可以实现连续加工,大大提高了生产效率。
第五,磨削可以加工各种形状的工件,如平面、曲面、孔等。
通过不同形状的磨具和磨料,可以加工出各种不同形状和精度要求的工件。
并且,由于磨削是一种柔性的加工方法,它可以根据加工需要进行不同的修整,以满足不同的要求。
最后,磨削还可以改善材料的机械性能和表面质量。
通过磨削可以降低材料的表面硬度和残余应力,从而提高材料的疲劳寿命和抗腐蚀性能。
此外,磨削还可以消除工件的加工硬化层,提高工件的尺寸精度和表面质量。
总之,磨削是一种高精度、高效率、多功能的加工方法。
它在航空航天、汽车、机床制造、电子仪器、模具制造等领域广泛应用。
在未来,随着科学技术的不断发展,磨削将更加趋向智能化,更好地满足不同领域对于精密加工的需求。
磨削加工原理
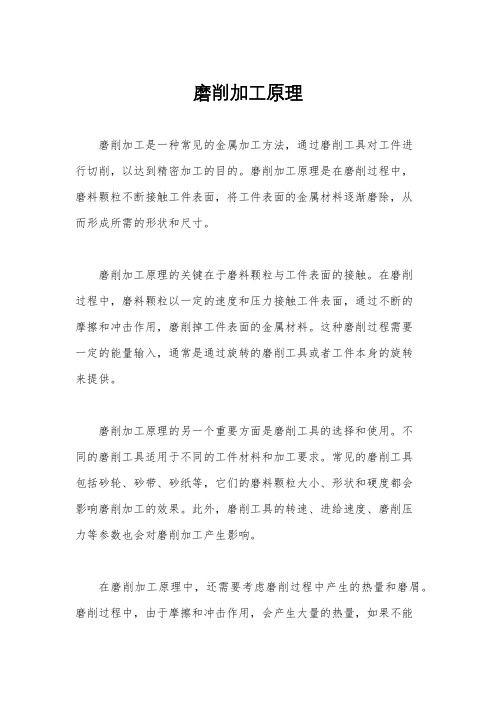
磨削加工原理
磨削加工是一种常见的金属加工方法,通过磨削工具对工件进
行切削,以达到精密加工的目的。
磨削加工原理是在磨削过程中,
磨料颗粒不断接触工件表面,将工件表面的金属材料逐渐磨除,从
而形成所需的形状和尺寸。
磨削加工原理的关键在于磨料颗粒与工件表面的接触。
在磨削
过程中,磨料颗粒以一定的速度和压力接触工件表面,通过不断的
摩擦和冲击作用,磨削掉工件表面的金属材料。
这种磨削过程需要
一定的能量输入,通常是通过旋转的磨削工具或者工件本身的旋转
来提供。
磨削加工原理的另一个重要方面是磨削工具的选择和使用。
不
同的磨削工具适用于不同的工件材料和加工要求。
常见的磨削工具
包括砂轮、砂带、砂纸等,它们的磨料颗粒大小、形状和硬度都会
影响磨削加工的效果。
此外,磨削工具的转速、进给速度、磨削压
力等参数也会对磨削加工产生影响。
在磨削加工原理中,还需要考虑磨削过程中产生的热量和磨屑。
磨削过程中,由于摩擦和冲击作用,会产生大量的热量,如果不能
及时散去,会对工件和磨削工具造成损坏。
同时,磨削过程中产生的磨屑也需要及时清除,以免对加工质量产生影响。
总的来说,磨削加工原理是通过磨料颗粒不断接触工件表面,将工件表面的金属材料逐渐磨除,从而实现精密加工的目的。
在实际应用中,需要根据工件材料和加工要求选择合适的磨削工具和加工参数,同时要注意散热和清屑,以确保磨削加工的效果和质量。
磨削安全操作规程

磨削安全操作规程磨削是一种常见的金属加工工艺,它可以为工件提供必要的尺寸与表面精度。
然而,由于磨削过程中涉及到高速旋转的磨削工具,存在着一定的安全风险。
为了确保操作人员的人身安全以及提高工作效率,有必要制定磨削安全操作规程。
下面是一份关于磨削安全操作规程的示例,供参考。
一、操作前准备1.磨削操作应由经过培训的操作人员进行,操作人员应具备相关工艺知识和安全意识。
2.操作人员应穿戴个人防护装备,包括安全鞋、手套、护目镜和耳塞等。
长发应及时束起,松散衣物应固定好。
3.确认磨削设备工作状态正常,磨削工具安装牢固。
4.操作环境应通风良好,避免存在可燃和易爆物质。
5.操作面积应保持整洁,避免杂物和障碍物干扰操作。
二、安全操作程序1.磨削前应检查工件和磨削工具,确认无损坏或异常现象。
2.根据工件材质和形状,选择合适的磨削工艺和磨削工具。
3.将工件固定在磨床上,确保稳固可靠。
4.开启磨削装置前,应确保操作人员和周围人员都远离磨削区域。
5.启动磨削装置时,应逐渐增加转速,确保无异响和明显振动。
6.磨削过程中,操作人员应保持专注,及时调整磨削工具和工件的相对位置,以获得理想的磨削效果。
7.严禁使用磨损过度或损坏的磨削工具,一旦发现异常应立即停机进行更换。
8.磨削过程中,不得随意触摸磨削工具,避免发生意外伤害。
9.禁止超过磨削工具的额定负荷进行操作,避免设备过载。
10.磨削过程中,不得随意更改磨削参数,避免引发事故。
三、应急措施1.一旦发生磨削工具脱离或破损,操作人员应立即停机,确保人身安全。
2.磨削过程中如有异味、异响或明显振动等异常情况,应停机检查并排除故障后方可继续操作。
3.磨削过程中如发生火灾或其它紧急情况,应立即停机,并按照应急预案进行处理。
四、操作后注意事项1.停机后,应关闭磨削装置,并清除磨削区域的废料和杂物。
2.及时清洗和维护磨削工具,保持其良好的工作状态。
3.将操作台面恢复整洁,归位工具和配件。
4.及时上报设备异常和故障,确保设备的正常使用。
磨削加工参数-磨削加工的范围有哪些?

磨削加工参数-磨削加工的范围有哪些?磨削加工参数磨削加工是一种常用的精密加工方法,其加工参数对加工效果有着至关重要的影响。
以下是常用的磨削加工参数及其单位:1.磨削要素磨削速度v:砂轮旋转运动的线速度,单位为m/s。
工件速度vw:工件运动的线速度,单位为m/min。
轴向进给量fa:对平面磨削而言,指工作台每单行程或双行程后砂轮轴向移动量,单位为mm/单行程或mm/双行程,本“推荐表”采用mm/双行程为单位。
对外圆、内圆磨削而言,指工件每相对于砂轮的轴向移动量,单位为mm/r。
径向进给量fr:砂轮径向切入工件的深度,单位为mm。
Ra:以轮廓算术平均偏差评定的表面粗糙度参数,单位为μm。
B:砂轮宽度,单位为mm。
2.平面磨削平面磨削是一种常见的磨削加工方法。
下表列出了三种不同硬度的钢材在淬火状态下的平面磨削参数:XXX淬火状态(硬度:40~45HRC)类别 Ra fr(mm) fa(mm/双行程) v(m/s) vw(m/min)砂轮粗磨 1.6 0.02~0.04 0.3B 25~30 15~25WA46K 精磨 0.8 0.01~0.015 0.1B 20~25 10~15WA60KGCr15钢淬火状态(硬度:61~65HRC)类别 Ra fr(mm) fa(mm/双行程) v(m/s) vw(m/min)砂轮粗磨 1.6 0.015~0.03 0.3B 15~20 15~25WA46K 精磨 0.8 0.005~0.01 0.1B 15~20 15~25WA60KT10钢淬火状态(硬度:58~64HRC)类别 Ra fr(mm) fa(mm/双行程) v(m/s) vw(m/min)砂轮粗磨 1.6 0.02~0.03 0.3B 25~30 15~25WA46K 精磨 0.8 0.005~0.01 0.1B 20~25 10~15WA60K3.外圆磨削外圆磨削是一种将工件放置于旋转的工作台上,通过砂轮的切削作用来加工工件外圆的方法。
2.4磨削机理
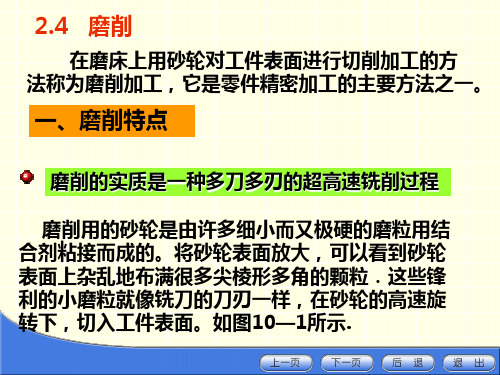
1)车削修整法
以单颗粒金刚石(或以细碎金刚石制成 的金刚笔、金刚石修整块) 作为刀具车 削砂轮是应用最普遍的修整方法。安装 在刀架上的金刚石刀具通常在垂直和水 平两个方向各倾斜约5°~15°;金刚 石与砂轮的接触点应低于砂轮轴线 0.5~2mm,修整时金刚石作均匀的低速 进给移动。要求磨削后的表面粗糙度越 小,则进给速度应越低,如要达到 Ra0.16~0.04µm的表面粗糙度,修整进 给速度应低于50mm/min。修整总量一般 为单面0.1mm左右,往复修整多次。粗 修的切深每次为0.01~0.03mm,精修则 小于0.01mm。
当砂轮硬度较低,修整较粗,磨削载荷较 重时。易出现脱落型。这时,砂轮廓形失真, 严重影响磨削表面质量及加工精度。 在磨削碳钢时由于切屑在磨削高温下发生 软化,嵌塞在砂轮空隙处,形成嵌入式堵塞, 在磨削钛合金时,由于切屑与磨粒的亲合力强, 使切屑熔结粘附于磨粒上,形成粘附式堵塞。 砂轮堵塞后即丧失切削能力,磨削力及温度剧 增,表面质量明显下降。
根据条件不同,磨粒的切削过程的3个阶段可以全部存 在,也可以部分存在 。
典型磨屑有带状、挤裂状、 球状及灰烬等(图10— 7).
三、磨削力及磨削功率 尽管单个磨粒切除的材料很少,但一个砂轮表层 有大量磨粒同时工作,而且磨粒的工作角度很不合理, 因此总的磨削力相当大。总磨削力可分解为三个分力: Rz——主磨削力(切向磨削力);
根据表面颜色,可以推断磨削温度及烧伤程度。如淡黄色 约为400℃~500℃,烧伤深度较浅;紫色为800℃~900℃, 烧伤层较深。 5、磨削表面裂纹 磨削过程中,当形成的残余拉应力超过工件材料的强 度极限时,工件表面就会出现裂纹。 磨削裂纹极浅,呈网状或垂直于磨削方向。有时不在表层, 而存在于表层之下。有时在研磨或使用过程中,由于去除 了表面极薄金属层后,残余应力失去平衡,形成微细裂纹。 这些微小裂纹,在交变载荷作用下,会迅速扩展,并造成 工件的破坏。
磨削速度计算公式

磨削速度计算公式
磨削速度是指磨削工件表面单位时间内被磨削掉的长度,是研磨过程中的一个重要参数。
磨削速度的计算公式一般可以根据不同的磨削方式和材料进行推导,下面将介绍几种常见的磨削速度计算公式。
(1)直径式磨削公式:
V=π×D×n
其中,V为磨削速度,D为工件直径,n为主轴转速。
(2)周速式磨削公式:
V=π×D×n÷60
其中,V为磨削速度,D为工件直径,n为主轴转速。
(1)线速度公式:
V=π×D×n
其中,V为磨削速度,D为砂轮直径,n为主轴转速。
(1)平均线速度公式:
V=π×D×n÷60
其中,V为磨削速度,D为砂轮直径,n为主轴转速。
(1)直径式磨削公式:
V=π×D×n
其中,V为磨削速度,D为刀具直径,n为主轴转速。
(2)周速式磨削公式:
V=π×D×n÷60
其中,V为磨削速度,D为刀具直径,n为主轴转速。
需要注意的是,以上公式中的单位需要保持一致,通常磨削速度的单位为m/s或m/min,直径和砂轮直径的单位为mm,主轴转速的单位为
r/min。
此外,还有一些专用的磨削速度计算公式,如球面磨削、内外棒材磨削等。
这些公式的推导较为复杂,需要根据具体情况进行推导。
总之,磨削速度计算公式的应用可以帮助工程师合理调整磨削参数,提高磨削效率和质量,在工程实践中具有重要意义。
- 1、下载文档前请自行甄别文档内容的完整性,平台不提供额外的编辑、内容补充、找答案等附加服务。
- 2、"仅部分预览"的文档,不可在线预览部分如存在完整性等问题,可反馈申请退款(可完整预览的文档不适用该条件!)。
- 3、如文档侵犯您的权益,请联系客服反馈,我们会尽快为您处理(人工客服工作时间:9:00-18:30)。
• Merchat在1945年推导出经典的成屑理论 Merchat在1945年推导出经典的成屑理论 模型, 模型,并开始推广应用于各种金属材料 的切削过程。由Merchat的理论,当切屑 的切削过程。 Merchat的理论, 的理论 沿前刀面滑动时会产生极薄的剪切区, 沿前刀面滑动时会产生极薄的剪切区, 一般切削条件下剪切消耗成屑能的75 75% 一般切削条件下剪切消耗成屑能的75% 左右,而刀具与切屑的摩擦耗去了25 25%。 左右,而刀具与切屑的摩擦耗去了25%。 尽管人们也观察到了其它的一些效应, 尽管人们也观察到了其它的一些效应, 但这个模型始终可给出成屑的准确描述。 但这个模型始终可给出成屑的准确描述。
• • •
平面切入磨削中砂轮的法向力和切向力 金属材料 非金属材料
• 在上图及其它类似发现的基础上,可以将磨削 在上图及其它类似发现的基础上, 力和比磨削能认为是由切削和滑擦两个部分引 起的。图中磨削力和纵轴A 起的。图中磨削力和纵轴A=0处的交点与切削 部分有关,而超出这个截距的磨削力值则与滑 部分有关, 擦有关。因此有: 擦有关。因此有:
P u= Qw
• 上式中分子是磨削功率;分母是去除的工件材 上式中分子是磨削功率; 料体积,与磨削参数有关。 料体积,与磨削参数有关。由于
Qw = v w ab = πd w v f b Ft vs Ft vs u= 或u = vw ab πd w v f b
• 此处b指磨削宽度。比磨削能的重要意义在于 此处b指磨削宽度。 它可反映磨粒与工件的干涉机理和干涉程度, 它可反映磨粒与工件的干涉机理和干涉程度, 另外还可反映出加工过程参数, 另外还可反映出加工过程参数,而且对机床功 率需求估计也有重要作用。采用国际单位, 率需求估计也有重要作用。采用国际单位,比 磨削能可表示为“ 磨削能可表示为“Joul/mm3”(J/ mm3),此时去 (J/ 除率单位为“ /s”,功率为“瓦特” 除率单位为“mm3/s ,功率为“瓦特”;
5
磨削机理
• 5.1 引言 • 磨削中工件材料的去除是磨粒和工件材 料干涉的结果。 料干涉的结果。磨粒切刃与工件的干涉 与砂轮地貌、 与砂轮地貌、砂轮与工件的几何以及运 动关系有关。 动关系有关。本章将讨论磨粒与工件的 干涉机理。 干涉机理。
• 已有很多不同的方法来收集证据研究磨粒与工 件的干涉。 件的干涉。一种方法是研究磨屑以获得其产生 的理由,因此扫描电镜是一个非常重要的工具。 的理由,因此扫描电镜是一个非常重要的工具。 另一个方法是测量不同条件下的磨削力和磨削 功率,这里一个重要的参数就是比磨削能, 功率,这里一个重要的参数就是比磨削能,它 是指去除单位体积工件材料所消耗的能量。 是指去除单位体积工件材料所消耗的能量。这 个参数的重要性在于各种磨粒- 个参数的重要性在于各种磨粒-工件的干涉机 理必须满足能量守恒定理, 理必须满足能量守恒定理,比磨削能取决于不 同的磨削条件。 同的磨削条件。更直接地观察二者的干涉是用 单颗磨粒或类似磨粒的刀具作切削试验。当然 单颗磨粒或类似磨粒的刀具作切削试验。 这些结果只有在试验条件能准确地模拟砂轮磨 粒状况下才是有效的。 粒状况下才是有效的。
• 5.4
普通磨粒砂轮磨削机理
• 5.4.1 尺寸效应及其能量 • 系统地测量磨削力和比磨削能始于20世纪50年 20世纪50年 系统地测量磨削力和比磨削能始于20世纪50 代初, 代初,当时发现比磨削能比其它切削方式要大 得多, 得多,而且降低 vw 和 a 以减小未变形切屑厚 度时比磨削能更大。 度时比磨削能更大。 • 所谓比磨削能是指磨除单位体积工件材料所需 要的能量。 要的能量。
• 另一个限制传统成屑理论应用于磨削过程的原 因是其比磨削能太大。 因是其比磨削能太大。几乎所有的能量均转化 为热,由于高切速和大应变,磨削成屑很快, 为热,由于高切速和大应变,磨削成屑很快, 整个过程金属是绝热的,这意味着没有足够的 整个过程金属是绝热的, 时间把塑性流动产生的大量热在变形过程中传 导出去。 导出去。在绝热条件下单位体积的塑性变形能 应限制在可将其从一般条件下转化为熔融态的 情况之内。 情况之内。单位体积熔融能可从手册液态熔点 到室温的焓查出。 到室温的焓查出。
• 从显微镜下可以看出磨屑与切屑非常近似。第 从显微镜下可以看出磨屑与切屑非常近似。 一张图片是普碳钢磨屑的SEM照片, SEM照片 一张图片是普碳钢磨屑的SEM照片,卷曲的磨 屑与车削和铣削的切屑非常相似, 屑与车削和铣削的切屑非常相似,只是由于切 刃形状和干涉深度差异造成磨屑的尺寸和形状 不很规则。 不很规则。磨屑有与其它加工方式相同的很细 的节状结构。 的节状结构。节状切屑是因局部热塑性变形引 起材料剪切抗力减小形成的。 起材料剪切抗力减小形成的。第二张图片是其 放大图,节间距约为0.5μm 0.5μm, 放大图,节间距约为0.5μm,比车削切屑稍细 一些,这是因为磨削是典型的负前角加工,另 一些,这是因为磨削是典型的负前角加工, 外由于磨削速度很快, 外由于磨削速度很快,造成磨削的成屑变形更 接近于绝热剪切。 接近于绝热剪切。
Ft = Ft ,c + Ft , sl
Fn = Fn ,c + Fn , sl
• 这里 Ft ,c 和Fn ,c 是由于切削引起的切向力和法向 力,Ft , sl 和Fn , sl 是由于滑擦引起的切向力和法向 作为一个典型磨粒的情况如下图所示。 力。作为一个典型磨粒的情况如下图所示。
• 对于钢工件而言滑擦力和磨粒磨损面积 成正比关系, 成正比关系,这表明工件与磨粒磨损平 面间平均接触压力和摩擦系数µ的关系: 面间平均接触压力和摩擦系数µ的关系:
• 5.2 磨屑 • 一般认为金属磨削过程类似于车削和铣削,其 一般认为金属磨削过程类似于车削和铣削, 金属材料是通过剪切过程去除的。 金属材料是通过剪切过程去除的。这个提法是 基于70年前人们在显微镜下观察到了类似切屑 基于 年前人们在显微镜下观察到了类似切屑 以下是磨削AISI1065钢的 钢的SEM 的磨削碎片 。以下是磨削 钢的 照片。 照片。
Ft = Ft ,c + µpb(d e a ) A
12
Fn = Fn ,c + pb(d e a ) A
12
• 在这个模型框架下可估计表征磨损平面和工件 接触关系的两个特征量µ 接触关系的两个特征量 µ 和 p , 综合上述公 式可得到: 式可得到:
Ft = Ft ,c + µpAa Fn = Fn ,c + pAa
• 这里 Aa 是工件和磨损平面的实际接触面 可表为磨削区面积(接触弧长× 积,可表为磨削区面积(接触弧长×磨 削宽度b 削宽度b)和砂轮磨损表面积比 A 的乘 积,即
Aa=b ⋅ lc ⋅ A = bA(ad e )1/ 2
• 由此可得磨削力公式为
• 对于铁,单位体积的熔化能为 10. 10.5 J/mm3 , 这个数值也适用于 钢 。 磨削钢的比磨削能一般为 20~ 20 ~ 60 J/mm3 。 更高的比磨削能 仅可能在精磨中出现。 仅可能在精磨中出现。在磨削中 如果塑性变形能高于熔化能则难 以令人信服。 以令人信服。
• 5.4.2 滑擦力和滑擦能 • 金属去除是通过成屑实现的,但更多的磨削能 金属去除是通过成屑实现的, 不是通过成屑消耗的。 不是通过成屑消耗的。磨粒磨钝的小平面在工 件表面滑动而不去除工件材料但消耗了能量。 件表面滑动而不去除工件材料但消耗了能量。 每个小平面最初是在磨削前的修整中得到的。 每个小平面最初是在磨削前的修整中得到的。 在磨削中小平面粘结部分金属而逐渐发出光亮 且通过磨耗磨损进一步扩大。 且通过磨耗磨损进一步扩大。下图示出磨钝平 面粘结金属的情况,许多磨粒还带着一些切屑。 面粘结金属的情况,许多磨粒还带着一些切屑。 扩大的砂轮磨损平面在一定程度上通过自锐或 磨粒从结合剂中脱落形成新切刃。 磨粒从结合剂中脱落形成新切刃。
• 5.3 磨削力、磨削功率和比磨削能 磨削力、 砂轮磨削工件就产生了磨削力。 砂轮磨削工件就产生了磨削力 。 对于切入磨削 无论是平面磨削或是外圆磨削) (无论是平面磨削或是外圆磨削),砂轮对工 件的总磨削力可分解为切向力 Ft 和径向力 Fn 两部分。 两部分 。 对于往复磨削还应附加上一个平行于 Fa 砂轮主轴的轴向磨削力分量 。 磨削功率P可表为: 磨削功率P可表为: P = Ft ⋅ (vs ± vw ) • 式中 “ + ” 号表示逆磨 , “ - ” 号表示 “ 顺 式中“ 号表示逆磨, 号表示“ 磨”。
• 磨削过程中磨损小平面产生的沿磨削方向的细 纹表明磨削能的一部分是由磨粒在工件上的滑 动消耗的, 动消耗的,二者的直接关系可由磨削力与砂轮 磨钝的程度表达出来。对于一定的机床结构, 磨钝的程度表达出来。 对于一定的机床结构, 如下图所示法向力和切向力随磨损面积A 如下图所示法向力和切向力随磨损面积 A 的增 加而增加。对于给定的工件材料, 加而增加。对于给定的工件材料,通过改变砂 轮硬度、修整条件、 轮硬度、修整条件、累积金属去除量来观察磨 削力和磨损平面的关系变化。对于钢工件( 削力和磨损平面的关系变化。对于钢工件(左 图),磨削力随磨损面积直线上升,当达到某 磨削力随磨损面积直线上升, 一临界点后,直线斜率产生突变, 一临界点后,直线斜率产生突变,工件出现了 烧伤;而对于非金属材料(右图) 烧伤;而对于非金属材料(右图)则未出现中 间直线斜率不一致的情况。 间直线斜率不一致的情况。
• 人们一直试图采用类似于其它的切削过 程模型来解释磨削的有关问题。 程模型来解释磨削的有关问题。对切刃 形状进行一些假设,估计成屑过程中的 形状进行一些假设, 塑性变形剪切应力, 塑性变形剪切应力,磨削流动应力。精磨中未 变形切屑厚度很小, 变形切屑厚度很小,由此计算出的高的 剪切应力意味着高的比磨削能。 剪切应力意味着高的比磨削能。
• 因一般情况下 简化为: 简化为:
vw 比 vs 小得多 , 所以功率可 小得多,
P = Ft ⋅ vs
• 对于多数磨削情况,上式关系均成立。与纵向 对于多数磨削情况,上式关系均成立。 进给速度和横向进给速度相关的功率部分一般 可不计。 可不计。