橡胶与金属的粘合是橡胶制品制造过程中的重要环节
橡胶与金属粘接后剥离 残余面积百分比

橡胶与金属粘接后剥离残余面积百分比在工程学和材料科学领域,橡胶与金属的粘接问题一直备受关注。
橡胶与金属之间的粘合强度对于许多应用来说至关重要,例如汽车轮胎、密封件和电缆等。
然而,橡胶与金属粘接后的剥离现象,特别是剥离时残余面积百分比的变化,一直是研究的热点之一。
要了解橡胶与金属粘接后的剥离过程,我们需要先了解橡胶与金属之间的界面现象。
橡胶与金属粘接的关键在于界面的化学键和物理键。
橡胶表面上的官能团与金属表面形成的化学键,以及物理键如机械锁和吸附力等,都会增强橡胶与金属的粘合强度。
这样的粘合强度对于橡胶制品的性能和寿命至关重要。
然而,橡胶与金属粘接后的剥离现象可能导致粘合强度的降低,这对于工程应用来说是一个主要的问题。
为了研究橡胶与金属粘接剥离时的残余面积百分比变化,研究人员通常采用剥离试验来评估粘合强度。
在剥离试验中,橡胶样品被黏附在金属表面上,然后通过施加剪切力将其剥离。
此过程中,可以测量橡胶与金属分离的力和剥离面积,由此得到粘合强度和残余面积百分比的数据。
研究表明,橡胶与金属粘接后的剥离现象受到多种因素的影响。
界面的表面粗糙度会影响粘接强度和剥离行为。
金属表面的粗糙度可以增加机械锁效应,从而提高粘合强度。
橡胶与金属之间的化学反应也对粘合强度起着重要作用。
一些化学键的形成可以增强粘接强度,而其他化学反应可能导致剥离时的残余面积百分比降低。
温度和湿度等环境条件也会对粘接剥离性能产生影响。
在实际应用中,人们通常希望橡胶与金属粘接后的剥离残余面积百分比尽可能小。
一个较小的残余面积百分比意味着粘接强度较高,耐久性较好。
研究人员一直在努力开发新的粘接技术和材料来改善橡胶与金属的粘接性能。
改变橡胶表面的化学组成、使用新型粘接剂和表面处理剂等都是改善橡胶与金属粘接性能的常用方法。
橡胶与金属粘接后的剥离残余面积百分比是评估粘接性能的重要参数之一。
研究橡胶与金属的粘接问题,深入了解界面的化学键和物理键,对改善橡胶制品的性能和寿命具有重要意义。
增粘剂Ricobond1756HS在氢化丁腈橡胶骨架油封中的应用
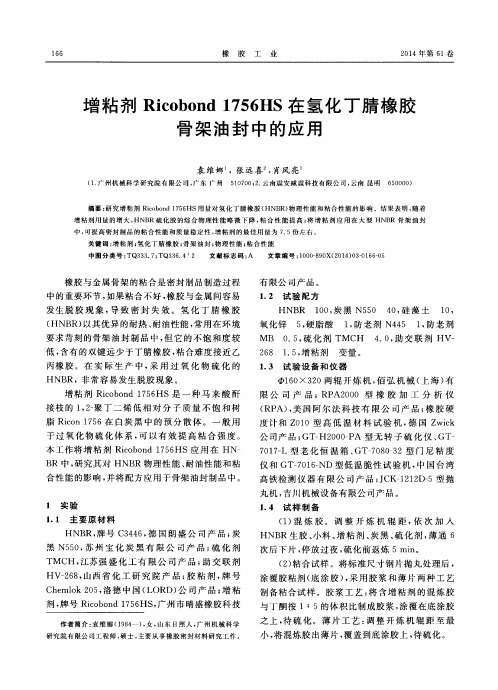
摘 要 :研 究 增 粘剂 Ricobond 1756HS用 量 对氢 化 丁腈 橡 胶 (HNBR)物 理 性 能 和 粘 合 性 能 的影 响 。结 果 表 明 :随 着 增 粘 剂 用 量 的 增 大 ,HNBR 硫 化 胶 的综 合 物 理 性 能 略 微 下 降 ,粘 合 性 能 提 高 ;将 增 粘 剂 应 用 在 大 型 HNBR 骨 架 油 封 中 ,可 提 高 密 封 制 品 的 粘合 性 能 和质 量 稳 定 性 ,增 粘 剂 的 最 佳用 量 为 7.5份 左 右 。
1 实 验 1.1 主 要 原 材 料
HNBR,牌 号 C3446,德 国 朗盛 公 司 产 品 ;炭 黑 N550,苏 州 宝 化 炭 黑 有 限 公 司 产 品 ;硫 化 剂 TMCH,江 苏强 盛 化 工 有 限 公 司产 品 ;助 交 联 剂 HV一268,山西 省 化 工 研 究 院产 品 ;胶 粘 剂 ,牌 号 Chemlok 205,洛 德 中 国 (LORD)公 司 产 品 ;增 粘 剂 ,牌号 Ricobond 1756HS,广 州市 晴盛 橡胶 科技
作 者 简 介 :袁 维 娜 (1984一 ),女 ,山 东 日照 人 ,广 州 机 械 科 学 研 究 院 有 限 公 司 工程 师 ,硕 士 ,主要 从 事 橡 胶 密 封 材 料 研 究 工作 。
有 限 公 司 产 品 。 1.2 试 验 配 方
HNBR 1OO,炭黑 N550 40,硅 藻 土 10, 氧化锌 5,硬脂 酸 1,防老 剂 N445 1,防 老 剂 MB 0.5,硫 化 剂 TMCH 4.0,助 交 联 剂 HV一 268 1.5,增 粘剂 变 量 。 1.3 试 验 设 备 和 仪 器
增粘 剂 Ricobond 1756HS是 一 种 马来 酸 酐 接枝 的 1,2一聚 丁 二 烯 低 相 对 分 子 质 量 不 饱 和 树 脂 Ricon 1756在 白炭 黑 中 的预 分 散 体 。一 般 用 于 过 氧 化 物 硫 化 体 系 ,可 以 有 效 提 高 粘 合 强 度 。 本 工作将 增 粘 剂 Ricobond 1756HS应 用 在 HN BR 中 ,研究 其对 HNBR物理 性能 、耐油 性能 和粘 合性 能 的影 响 ,并将 配方 应用 于骨 架油封 制 品 中。
橡胶工艺学试题库简答题

橡胶工艺学试题库简答题一、简答题(共60小题)1、常用热氧老化防老剂的作用机理是什么?(举三类分别说明)。
正确答案:链终止型防老剂:其作用主要是与链增长自由基R·或RO2·反应,以终止链增长过程来减缓氧化反应。
破坏氢化过氧化物性防老剂:机理是破坏氢过氧化物,使它们不生成活性游离基,延缓自动催化的引发过程,一般不单独使用,而是与酚类等抗氧剂并用,称为辅助防老剂。
金属离子钝化剂:主要是酰胺类、醛胺缩合物等,他们能与酚类和胺类防老剂有效地并用。
主要是铜抑制剂和铁抑制剂,可有效降低金属离子的浓度。
2、混炼操作开始前,需进行哪些准备工作?正确答案:各种原材料与配合剂的质量检验:配合剂的检验包括纯度、粒度及其分布、机械杂质、灰分及挥发分、酸碱度等;生胶的检验包括化学成分、门尼粘度、物理机械性能。
对某些配合剂尽心补充加工:固体配合剂的粉碎、干燥和筛选;低熔点固体配合剂的融化和过滤;液体配合剂的加温和过滤;粉状配合剂的干燥和筛选。
油膏与母炼胶的制造:为防止粉状物料的分散、损失及环境污染,有时候将某些配合剂、促进剂等事先以较大比例与液体软化剂混合制成膏状使用;而母炼胶是某些配合剂与生胶单独混合制成的物料。
称量配合操作:即按配方规定的原材料品种和用量比例,以适当的衡器进行称量搭配。
3、什么是液体橡胶?与普通橡胶相比有什么优缺点?(15分)正确答案:指室温下为粘稠状可流动的液体,经适当的化学反应后可形成三维网状结构,成为具有与普通橡胶类似性能的材料。
优点:易于实现机械化、自动化、连续化生产,不需用溶剂、水等分散介质便看实现液体状态下的加工。
缺点:扩链后的强度及耐挠曲性不如固体橡胶,加工需另建系统,现有设备不适用,材料成本高。
4、什么是压延效应?其原因是什么?正确答案:压延效应是指压延后的胶片在平行和垂直于压延方向上出现性能各向异性的现象。
原因:橡胶大分子链的拉伸取向;形状不对称的配合剂粒子沿压延方向的取向。
硫化橡胶 金属 标准
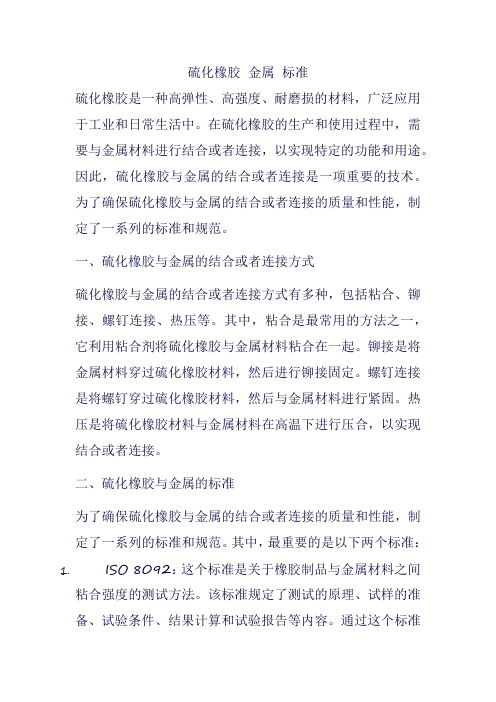
硫化橡胶金属标准硫化橡胶是一种高弹性、高强度、耐磨损的材料,广泛应用于工业和日常生活中。
在硫化橡胶的生产和使用过程中,需要与金属材料进行结合或者连接,以实现特定的功能和用途。
因此,硫化橡胶与金属的结合或者连接是一项重要的技术。
为了确保硫化橡胶与金属的结合或者连接的质量和性能,制定了一系列的标准和规范。
一、硫化橡胶与金属的结合或者连接方式硫化橡胶与金属的结合或者连接方式有多种,包括粘合、铆接、螺钉连接、热压等。
其中,粘合是最常用的方法之一,它利用粘合剂将硫化橡胶与金属材料粘合在一起。
铆接是将金属材料穿过硫化橡胶材料,然后进行铆接固定。
螺钉连接是将螺钉穿过硫化橡胶材料,然后与金属材料进行紧固。
热压是将硫化橡胶材料与金属材料在高温下进行压合,以实现结合或者连接。
二、硫化橡胶与金属的标准为了确保硫化橡胶与金属的结合或者连接的质量和性能,制定了一系列的标准和规范。
其中,最重要的是以下两个标准:1.ISO 8092:这个标准是关于橡胶制品与金属材料之间粘合强度的测试方法。
该标准规定了测试的原理、试样的准备、试验条件、结果计算和试验报告等内容。
通过这个标准的测试,可以评估硫化橡胶与金属材料之间的粘合强度,以确保它们能够承受一定的外力和环境条件。
2.ASTM D 4169:这个标准是关于橡胶制品与金属材料之间粘合强度的测试方法。
该标准规定了测试的原理、试样的准备、试验条件、结果计算和试验报告等内容。
通过这个标准的测试,可以评估硫化橡胶与金属材料之间的粘合强度,以确保它们能够承受一定的外力和环境条件。
与ISO 8092类似,ASTM D 4169也是一项国际通用的标准,被广泛用于评估硫化橡胶与金属的结合或者连接的质量和性能。
除了以上两个重要的标准之外,还有一些其他的标准和技术规范,如GB/T 3512-2014《硫化橡胶或热塑性橡胶热空气加速老化和耐热试验》、GB/T 7762-2003《硫化橡胶或热塑性橡胶耐臭氧龟裂》、GB/T 3398.1-2008《硫化橡胶或热塑性橡胶硬度的测定第1部分:硬度计法》等。
橡胶制品常见问题及解决方法
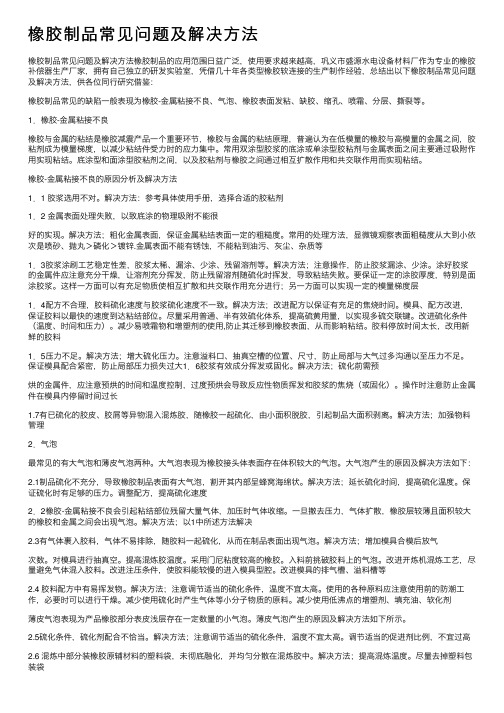
橡胶制品常见问题及解决⽅法橡胶制品常见问题及解决⽅法橡胶制品的应⽤范围⽇益⼴泛,使⽤要求越来越⾼,巩义市盛源⽔电设备材料⼚作为专业的橡胶补偿器⽣产⼚家,拥有⾃⼰独⽴的研发实验室,凭借⼏⼗年各类型橡胶软连接的⽣产制作经验,总结出以下橡胶制品常见问题及解决⽅法,供各位同⾏研究借鉴:橡胶制品常见的缺陷⼀般表现为橡胶-⾦属粘接不良、⽓泡、橡胶表⾯发粘、缺胶、缩孔、喷霜、分层、撕裂等。
1.橡胶-⾦属粘接不良橡胶与⾦属的粘结是橡胶减震产品⼀个重要环节,橡胶与⾦属的粘结原理,普遍认为在低模量的橡胶与⾼模量的⾦属之间,胶粘剂成为模量梯度,以减少粘结件受⼒时的应⼒集中。
常⽤双涂型胶浆的底涂或单涂型胶粘剂与⾦属表⾯之间主要通过吸附作⽤实现粘结。
底涂型和⾯涂型胶粘剂之间,以及胶粘剂与橡胶之间通过相互扩散作⽤和共交联作⽤⽽实现粘结。
橡胶-⾦属粘接不良的原因分析及解决⽅法1.1 胶浆选⽤不对。
解决⽅法:参考具体使⽤⼿册,选择合适的胶粘剂1.2 ⾦属表⾯处理失败,以致底涂的物理吸附不能很好的实现。
解决⽅法;粗化⾦属表⾯,保证⾦属粘结表⾯⼀定的粗糙度。
常⽤的处理⽅法,显微镜观察表⾯粗糙度从⼤到⼩依次是喷砂、抛丸>磷化>镀锌.⾦属表⾯不能有锈蚀,不能粘到油污、灰尘、杂质等1.3胶浆涂刷⼯艺稳定性差,胶浆太稀、漏涂、少涂、残留溶剂等。
解决⽅法;注意操作,防⽌胶浆漏涂、少涂。
涂好胶浆的⾦属件应注意充分⼲燥,让溶剂充分挥发,防⽌残留溶剂随硫化时挥发,导致粘结失败。
要保证⼀定的涂胶厚度,特别是⾯涂胶浆。
这样⼀⽅⾯可以有充⾜物质使相互扩散和共交联作⽤充分进⾏;另⼀⽅⾯可以实现⼀定的模量梯度层1.4配⽅不合理,胶料硫化速度与胶浆硫化速度不⼀致。
解决⽅法;改进配⽅以保证有充⾜的焦烧时间。
模具、配⽅改进,保证胶料以最快的速度到达粘结部位。
尽量采⽤普通、半有效硫化体系,提⾼硫黄⽤量,以实现多硫交联键。
改进硫化条件(温度、时间和压⼒)。
减少易喷霜物和增塑剂的使⽤,防⽌其迁移到橡胶表⾯,从⽽影响粘结。
橡胶表面粘合力
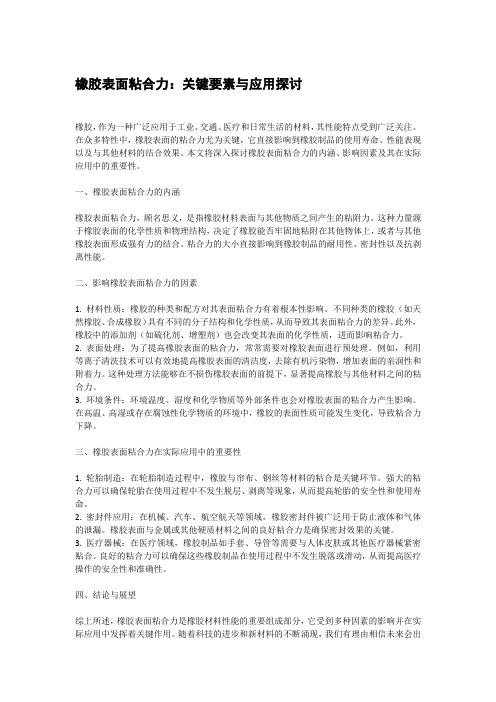
橡胶表面粘合力:关键要素与应用探讨橡胶,作为一种广泛应用于工业、交通、医疗和日常生活的材料,其性能特点受到广泛关注。
在众多特性中,橡胶表面的粘合力尤为关键,它直接影响到橡胶制品的使用寿命、性能表现以及与其他材料的结合效果。
本文将深入探讨橡胶表面粘合力的内涵、影响因素及其在实际应用中的重要性。
一、橡胶表面粘合力的内涵橡胶表面粘合力,顾名思义,是指橡胶材料表面与其他物质之间产生的粘附力。
这种力量源于橡胶表面的化学性质和物理结构,决定了橡胶能否牢固地粘附在其他物体上,或者与其他橡胶表面形成强有力的结合。
粘合力的大小直接影响到橡胶制品的耐用性、密封性以及抗剥离性能。
二、影响橡胶表面粘合力的因素1. 材料性质:橡胶的种类和配方对其表面粘合力有着根本性影响。
不同种类的橡胶(如天然橡胶、合成橡胶)具有不同的分子结构和化学性质,从而导致其表面粘合力的差异。
此外,橡胶中的添加剂(如硫化剂、增塑剂)也会改变其表面的化学性质,进而影响粘合力。
2. 表面处理:为了提高橡胶表面的粘合力,常常需要对橡胶表面进行预处理。
例如,利用等离子清洗技术可以有效地提高橡胶表面的清洁度,去除有机污染物,增加表面的亲润性和附着力。
这种处理方法能够在不损伤橡胶表面的前提下,显著提高橡胶与其他材料之间的粘合力。
3. 环境条件:环境温度、湿度和化学物质等外部条件也会对橡胶表面的粘合力产生影响。
在高温、高湿或存在腐蚀性化学物质的环境中,橡胶的表面性质可能发生变化,导致粘合力下降。
三、橡胶表面粘合力在实际应用中的重要性1. 轮胎制造:在轮胎制造过程中,橡胶与帘布、钢丝等材料的粘合是关键环节。
强大的粘合力可以确保轮胎在使用过程中不发生脱层、剥离等现象,从而提高轮胎的安全性和使用寿命。
2. 密封件应用:在机械、汽车、航空航天等领域,橡胶密封件被广泛用于防止液体和气体的泄漏。
橡胶表面与金属或其他硬质材料之间的良好粘合力是确保密封效果的关键。
3. 医疗器械:在医疗领域,橡胶制品如手套、导管等需要与人体皮肤或其他医疗器械紧密贴合。
橡胶和金属的粘结技术

橡胶和金属的粘结技术橡胶和金属是两种不同性质的材料,将两者很好地粘接可以制得具有不同构型和特性的复合件,这种复合体系在工业中有着广泛的用途,如汽车工业、机械制造工业、固体火箭发动机的柔性接头、桥梁的支撑缓冲垫等。
橡胶与金属之间化学结构和力学性能巨大的差异,使获得具有高强度的粘接有着很大的困难。
研制出高性能粘接和适用范围更广的新型胶粘剂始终是研究的热点。
借助于胶粘剂在硫化过程中将橡胶与金属粘接起来是目前采用的基本方法之一。
本文将就其进展进行综述。
1金属-橡胶粘接体系发展现状橡胶与金属之间的粘接已有很久的历史,可以追溯到1850年,目前采用的粘接方法可分为直接粘接法、硬质橡胶法、镀黄铜法和胶粘剂粘接法。
直接粘接法工艺简单,操作方便,将粘接材料表面进行适当处理后直接在加热加压过程中实现粘接。
可通过在橡胶中加入一些组分、在胶料表面涂偶联剂或对对橡胶进行环化处理等来提高橡胶与金属的粘接性能。
尹寿琳、陈日生等在天然橡胶中加入多硫化合物粘合剂B和酸性化合物助剂C,用此粘合A3钢板作挖泥泵耐磨衬里,挖泥1000h以上未发现橡胶与金属脱开。
此法不足的是,处理的金属件要尽快与胶料粘接,以免金属表面深层氧化;在胶料中添加一些多价金属的有机盐和无机盐,虽可提高粘接效果,但会改变橡胶材料原先的物理机械性能,且造成出模困难。
硬质橡胶法是最古老的粘接体系,在金属表面贴一层硫磺含量较高的硬质胶料或一层硬质胶浆,通过硫化使橡胶与金属粘接起来,硬质橡胶法粘接力较强,工艺简便,适于粘接大型制件,但是不耐冲击和震动,60℃以上粘接强度发生显著下降。
镀黄铜法较硬质橡胶法有较好的耐高温性,黄铜或表面镀黄铜金属件不同胶粘剂,借助于被粘橡胶中的硫磺扩散到金属表面与CuO、ZnO结合形成界面粘接层与橡胶产生牢固粘合,至今在轮胎工业中钢丝圈的粘接、钢丝帘线与帘布层胶的粘接、内胎气门嘴的制造中仍采用此法。
胶粘剂法是目前应用最广和最有效的方法,已经历了酚醛树脂、多异氰酸酯、卤化橡胶、特种硫化剂的卤化橡胶、硅橡胶和水基胶粘剂等不同的发展阶段。
橡胶制品的生产流程

橡胶制品的生产流程橡胶制品是指通过橡胶材料加工而成的各种物品,比如轮胎、橡胶管、橡胶制品等。
橡胶制品的生产流程经过多个环节,下面我们就来详细介绍一下。
首先,橡胶制品的生产需要准备原材料。
橡胶制品的原材料主要是橡胶乳和橡胶粉。
橡胶乳是橡胶树割皮后流出的白色胶液,它是橡胶制品生产中最重要的原料之一。
橡胶粉则是指将橡胶乳加热干燥后得到的粉末状物质。
接下来,将橡胶乳和橡胶粉混合制备成制品所需的橡胶胶料。
在混合的过程中,通常会加入一些辅助原料,如硫化剂、促进剂、防老剂等,以提高胶料的性能。
混合的设备通常是橡胶开炼机,通过机械切割和滚压的方式将橡胶乳和橡胶粉充分混合在一起,形成均匀的橡胶胶料。
然后,将橡胶胶料放入模具中进行成型。
模具的种类有很多,根据制品的不同而有所差异。
例如,制造轮胎的模具是由一对对称的金属模具组成,用来成型胎面、胎侧等部位。
模具的尺寸和形状决定了最终制品的外形和尺寸。
橡胶胶料通过加热软化后,被挤压到模具中,经过一定的时间形成所需的形状。
成型过程中需要控制好温度、时间和压力等因素,以保证制品的质量。
成型完成后,橡胶制品需要经过硫化处理。
硫化是指橡胶胶料中的硫化剂与橡胶中的双键发生化学反应,使胶料变得硬化、耐磨、耐高温等。
硫化的方法有很多种,常用的包括热硫化、冷硫化、热风硫化等。
热硫化是指将成型好的橡胶制品放入硫化罐中,通过加热使硫化剂与橡胶发生反应。
硫化时间通常在几分钟到几个小时之间,具体时间根据橡胶制品的种类和厚度而定。
最后,经过硫化处理的橡胶制品需要进行清洗和修整。
清洗是将橡胶制品表面的杂质和残留物清除,以保证表面的光洁度。
修整是对制品进行切割、打磨等处理,以使制品达到所需的尺寸和外观效果。
修整过程中需要注意操作技巧,以防止制品表面被刮伤或损坏。
综上所述,橡胶制品的生产流程包括准备原材料、混合制备橡胶胶料、模具成型、硫化处理、清洗和修整等环节。
每个环节都需要严格控制各种因素,以保证制品的质量和性能。
- 1、下载文档前请自行甄别文档内容的完整性,平台不提供额外的编辑、内容补充、找答案等附加服务。
- 2、"仅部分预览"的文档,不可在线预览部分如存在完整性等问题,可反馈申请退款(可完整预览的文档不适用该条件!)。
- 3、如文档侵犯您的权益,请联系客服反馈,我们会尽快为您处理(人工客服工作时间:9:00-18:30)。
橡胶与金属的粘合是橡胶制品制造过程中的重要环节,如果粘合不良或无法粘合,一些橡胶制品如轮胎、钢丝输送带、橡胶软管,橡胶骨架油封、汽门油封,橡胶金属组合垫圈、组合胶套等橡胶金属复合制品就无法制作。
就橡胶密封制品而言,上世纪80年代初,青岛密封件厂协同青岛化工厂研制成功了RM-1粘合剂,替代日本TD870成功生产出与国外同等水平的骨架油封,使引进的国外技术得以消化吸收,开辟了骨架油封制作的新工艺。
上世纪90年代,由于汽车工业的发展,不少厂家要求用氟橡胶制作骨架油封、汽车油封,但是粘合问题不好解决,严重的制约了该产品的开发,当时青岛双星集团密封件厂成功的研制了FG-1氟橡胶与黑色金属的热硫化粘合剂,使氟橡胶与金属骨架牢牢的粘合成一体,顺理成章的研发成功斯太尔发动机曲轴前后油封和气门油封替代了进口,满足了配套需要,该粘合剂一直使用至今。
因此橡胶与金属粘合是极其重要的应用技术,应引起生产企业的高度重视。
1 金属骨架的表面处理) 骨架表面无油污、无锈蚀,有一定粗糙度的新鲜表面才能有效的与金属粘合,因此骨架必须进行表面处理,处理大体有两种方法:一是机械法处理。
如采用履带式的抛丸清理机326或滚筒式的抛丸清理机Q3110,将粒径0.5mm的钢砂喷射到骨架表面,将表面的锈蚀等有害物料喷掉,使表面新鲜并增大表面积,加大骨架与胶粘剂间的接触面;二是化学法。
即酸洗处理,磷化钝化处理,其工艺过程是碱液去油,酸液去锈,磷化上磷化膜,然后进行钝化烘干,碱液是有多种材料如苛性钠、硅酸钠(表面湿润剂)、焦磷酸钠(阴离子表面活性剂)、烷基磺酸钠组成的水溶液,清洗温度80-90℃,时间视表面的油污多少而有差异,一般是5min左右。
去油污的骨架经流动的自来水冲洗后,进行酸洗处理,而不同的金属去锈时对酸的品种是有选择性的。
例如,铁件要用盐酸清洗处理。
铜件和不锈钢骨架采用硫酸、硝酸混合液协同去锈。
铝件用硫酸、铬酸混合液进行处理。
要求对周围环境不产生或少产生腐蚀时,而金属骨架锈蚀较轻的骨架,可采用以草酸为主,掺用少量硫酸和加入缓钝剂的水溶液进行处理。
磷化是黑色金属表面处理的重要方法。
磷化液的品种很多,如常温磷化液,采用的是铁系磷化液,骨架经酸洗后进行表调,放入常温磷化液中(温度30℃左右)处理5-6min;中温磷化是采用锌系或锌钙系的磷化液,骨架在65-75℃下处理6min左右;高温磷化液是锰系磷化液,骨架在80-90℃下处理3-4min,目前采用中温磷化液较好,因常温磷化表面磷化膜磷化后停放时容易造成再生锈,高温磷化的骨架表面磷化膜粗糙而且较厚,易造成脱落,中温磷化,磷化膜细致而牢固有利于粘合。
磷化后的骨架要进行钝化处理,主要是通过钝化液的表面处理,封闭骨架表面的易氧化离子,防止骨架再生锈。
钝化液的品种很多,如以铬酸盐类、硝酸盐类,三乙酸胺为代表的有机胺类,其中铬酸盐类钝,化效果好,表面的铬离子有利于与橡胶的粘合,但铬酸盐类环保控制较严格,需进行废液的处理,对于难粘合如不锈钢骨架除混合酸清冼后进行表面钝化后还需进行偶化处理,这有利于提高粘合强度。
如无锡威力达公司生产的全电脑控制双勾磷化处理线,温度、浸洗时间、烘干时间、停放滴水时间等全部自动控制,可有效的保证处理质量。
其工艺过程是碱液去锈(5℃×3min),吊起滴水(常温×1min)→自来水冲洗(常温×1min)→酸液去锈(常温×3min)→吊起滴液(常温×1min)→流动自来水冲洗(常温×0.5min)→磷化处理(65-70℃×5-6min)→吊起滴液(常温×1min)→流动自来水冲洗(常温×1min)→吊起滴液(常温×1min)→钝化(90℃×0.5min)→烘干备用。
2 粘合胶、胶料配方的设计要使橡胶与金属骨架产生良好的粘合强度,必须要在粘合剂与金属界面上和粘合剂与橡胶界面上,具有良好的扩散、湿润、吸附、渗透能力,大的分子间的引力(即范德华引力)和密集的化学键及良好的共硫化效应,要达到上述要求,除选择高活性的粘合剂、严格的金属骨架表面处理工艺和正确的配制浸涂、预固化粘合剂之外,橡胶配方是极其重要的因素,若胶料配方不当,其粘着强度低而且适应性也差。
丁腈橡胶与铁骨架浸涂酚类粘合剂,以进行热硫化为例,通过试验发现丁腈橡胶随着丙烯腈含量的增加,粘合强度随之提高(见表1)。
不同丙烯腈含量丁腈橡胶的粘合强度生胶品种国产丁腈橡胶40日本丁腈橡胶203S国产丁腈橡胶26、27-30日本丁腈橡胶N-41日本丁腈橡胶240S国产丁腈橡胶18丙烯腈含量/%36-3832-3426-3027-2822-2418-20粘着强度/MPa5.04.84.73.5光面光面试验配方:丁腈橡胶变量,氧化锌5;硬脂酸防老剂RD 2;MB 二辛酯15;炭黑95;硫黄0.5;TMTD 1;TETD 1份;DM 2.5。
从表1可看出不同品种的丁腈橡胶,粘着强度的差异很大,丁腈橡胶40最好,230尚可,中低丙烯腈含量的胶料粘着强度最差。
+ e k: S! A3 @7 _1 e本文来自:橡胶技术网2.5。
从表1可看出不同品种的丁腈橡胶,粘着强度的差异很大,丁腈橡胶40最好,230尚可,中低丙烯腈含量的胶料粘着强度最差。
试验中还发现丁腈橡胶的硫化体系对粘合强度有较大影响8不同硫化体系的丁腈胶与铁骨架的粘合强度硫化体系DCP+TMTD+DM+S2,1.5,1.5,0.3DCP+S+DM2,0.3,1.5S+DM1.5,1.5S+TMTD+DM0.5,2,3粘着强度/MPa>5.04.54.03.7试验配方组成:丁腈橡胶26 100;氧化锌5;硬脂酸1;炭黑90;二辛酪15;凡士林3;防老剂3。
骨架喷砂后,浸涂RM-1粘合剂经145℃预固化15min进行热硫化粘着。
从表2中看出过氧化物硫化体系的粘着强度>硫黄体系的粘着强度>低硫高促硫化体系的粘着强度。
在试验和生产实践中还发现,中低丙烯腈含量的生胶采用过氧化物硫化体系的胶料配方,其补强剂对粘着强度的影响也很大。
白炭黑胶料的粘着强度>白炭黑+喷雾炭黑(1:2)>喷雾炭黑+半补强,炭黑(1:1)。
在丁腈橡胶26中在硫黄1.5份,DM1.5份的配方中加入间甲白体系(即RS2,RH2.5,白炭黑15)的粘合强度较高,拉力机无法拉断,在白炭黑的胶料中加入凡土林有助于粘合,若加入适量的硅烷偶联剂可进一步提高粘合强度。
其他通用性非极性橡胶与金属的粘合与丁腈橡胶相类似。
如天然橡胶与铜嘴的直接粘合配方(不涂粘合剂)采用高氧化锌40份、硫黄3.5-份,添加适量的增粘剂松焦油、黄油、氧化铁红可使酸液清洗后的铜嘴骨架直接进行热硫化粘着,其他通用型橡胶如丁苯橡胶、氯丁橡胶、三元乙丙橡胶、顺丁橡胶添加上述材料也可提高橡胶与金属的粘合强度。
粘合剂主要分五大类:(1)异氰酸酯类,如列克钠;(2)树脂类如RM-1、TD870,GN-1等:(3)卤化橡胶或环化橡胶类如开姆洛克220,开姆希尔211等;(4)硅烷类如3290、5150和GF-1等;(5)硅烷和树脂混合类如512、PC-22等。
目前市场销售较多的是美国开姆洛克系列粘合剂,德国汉高的开姆希尔系列粘合剂。
该系列粘合剂为开姆洛克新品,另外还有麦加母系列粘合剂,国内青岛化工厂的BM-1和青岛鲁中泰化工公司的GF-1和GN-1粘合剂等。
氟橡胶与金属的粘合可选择德国汉高公司开姆希尔512、保乐固PC-22、美加母3290和青岛鲁中泰的GF-1。
丁腈橡胶、ACM胶、聚氨酯橡胶可选择韩国产的TD870,青岛化工厂的RM-1,青岛鲁中泰公司的GN-1,无色制品可选择透明粘合剂PC-35。
其他通用类型的橡胶,如天然橡胶、丁苯,橡胶、顺丁橡胶、氯丁橡胶、三元乙丙橡胶等,可选择树脂类的粘合剂做底胶如开姆希尔211,麦加母的3270/3276,开姆洛克205然后再涂如开姆希尔225,美加母100、115,开姆洛克250、252。
硅橡胶与金属的粘合,可选择3290,过氧化硅烷VTPS 和GF-1进行热硫化粘合。
粘合剂的应用工艺也很重要,用于TD870粘合剂的溶剂和稀释剂必须用甲醇或乙醇做溶剂。
粘合剂与溶剂的配比,因金属骨架板材的料厚有所差别,料厚0.3-0.8mm的配比(粘合剂:溶剂)是1:8-1:12;料厚0.8-1.2mm配比是1:8-1:6);1.2以上的是1:6-1:4,512和PC-22必须用甲乙酮做溶剂配比是1:4-1:8。
3290必须,用无水乙醇做溶剂,配比是1:3-1:4。
橡胶类的粘合剂如开姆希尔411,开姆洛克250,麦加母14450,可用甲苯、二甲苯做稀释剂,用量20%左右,金属骨架浸涂粘合剂和浸涂后的预固化停放时间也很重要,一般树脂类、硅烷类、硅烷和树脂混合类的粘合剂,可将骨架全部浸到粘合剂溶剂溶液中进行离心浸涂,橡胶类粘合剂因粘度高,必须进行刷涂或喷涂,涂后的金属骨架必须进行常温停放,挥发掉溶剂后进行预固化。
如TD870、RM-1、GN-1粘合剂需径145±3℃×10min的预固化。
3290和GF-1粘合剂常温停放5min后,须经150℃×10min的预固化。
橡胶类的粘合剂可常温停放待溶剂挥发后,即可进行热硫化,预固化后的骨架要放置在于燥清洁场地,TD870的骨架可放置于3周左右,3290和GF-1骨架不宜超过5天。
1.金属骨架表面必须进行喷砂处理或化学处理,才能与金属进行热硫化粘着。
2.一般通用型橡胶如丁腈橡胶、丁苯橡胶等采用过氧化物硫化体系或硫黄硫化体系,有利于粘合,配方中加入适量的白炭黑、硅烷偶联剂、增粘树脂、氧化铁红等可提高粘合强度。
3.开姆希尔新品种粘合剂可应用于橡胶与金属的热硫化粘着。
粘合剂与溶剂的配比及其浸涂工艺、预固化工艺是热硫化粘着的重要工艺过程,必须严格控制。