AP1000核电厂的安全壳设计
AP1000非能动安全系统
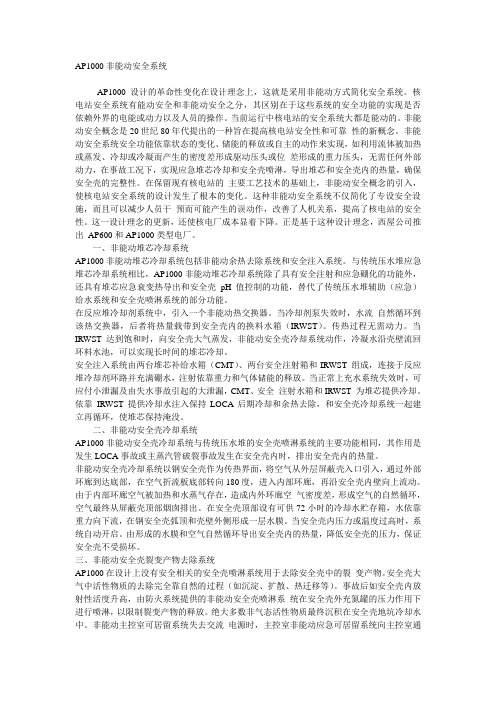
AP1000非能动安全系统AP1000 设计的革命性变化在设计理念上,这就是采用非能动方式简化安全系统。
核电站安全系统有能动安全和非能动安全之分,其区别在于这些系统的安全功能的实现是否依赖外界的电能或动力以及人员的操作。
当前运行中核电站的安全系统大都是能动的。
非能动安全概念是20世纪80年代提出的一种旨在提高核电站安全性和可靠性的新概念。
非能动安全系统安全功能依靠状态的变化、储能的释放或自主的动作来实现,如利用流体被加热或蒸发、冷却或冷凝而产生的密度差形成驱动压头或位差形成的重力压头,无需任何外部动力,在事故工况下,实现应急堆芯冷却和安全壳喷淋,导出堆芯和安全壳内的热量,确保安全壳的完整性。
在保留现有核电站的主要工艺技术的基础上,非能动安全概念的引入,使核电站安全系统的设计发生了根本的变化。
这种非能动安全系统不仅简化了专设安全设施,而且可以减少人员干预而可能产生的误动作,改善了人机关系,提高了核电站的安全性。
这一设计理念的更新,还使核电厂成本显着下降。
正是基于这种设计理念,西屋公司推出AP600和AP1000类型电厂。
一、非能动堆芯冷却系统AP1000非能动堆芯冷却系统包括非能动余热去除系统和安全注入系统。
与传统压水堆应急堆芯冷却系统相比,AP1000非能动堆芯冷却系统除了具有安全注射和应急硼化的功能外,还具有堆芯应急衰变热导出和安全壳pH 值控制的功能,替代了传统压水堆辅助(应急)给水系统和安全壳喷淋系统的部分功能。
在反应堆冷却剂系统中,引入一个非能动热交换器。
当冷却剂泵失效时,水流自然循环到该热交换器,后者将热量载带到安全壳内的换料水箱(IRWST)。
传热过程无需动力。
当IRWST达到饱和时,向安全壳大气蒸发,非能动安全壳冷却系统动作,冷凝水沿壳壁流回环料水池,可以实现长时间的堆芯冷却。
安全注入系统由两台堆芯补给水箱(CMT)、两台安全注射箱和IRWST 组成,连接于反应堆冷却剂环路并充满硼水,注射依靠重力和气体储能的释放。
AP1000钢制安全壳埋弧横焊工艺应用研究
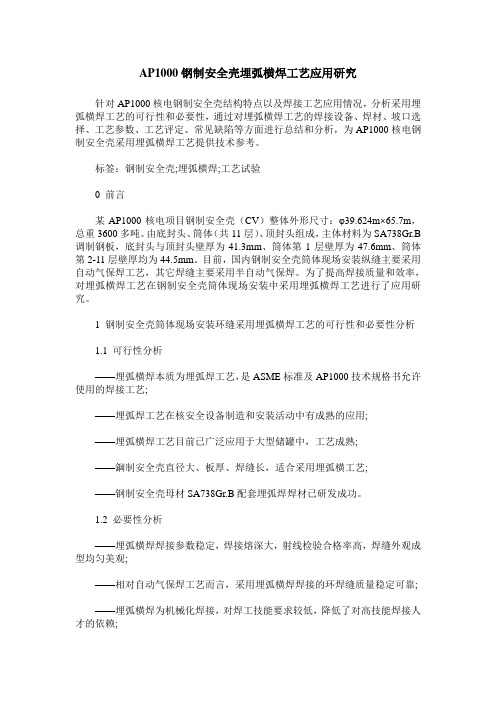
AP1000钢制安全壳埋弧横焊工艺应用研究针对AP1000核电钢制安全壳结构特点以及焊接工艺应用情况,分析采用埋弧横焊工艺的可行性和必要性,通过对埋弧横焊工艺的焊接设备、焊材、坡口选择、工艺参数、工艺评定、常见缺陷等方面进行总结和分析,为AP1000核电钢制安全壳采用埋弧横焊工艺提供技术参考。
标签:钢制安全壳;埋弧横焊;工艺试验0 前言某AP1000核电项目钢制安全壳(CV)整体外形尺寸:φ39.624m×65.7m,总重3600多吨。
由底封头、筒体(共11层)、顶封头组成,主体材料为SA738Gr.B 调制钢板,底封头与顶封头壁厚为41.3mm、筒体第1层壁厚为47.6mm、筒体第2-11层壁厚均为44.5mm。
目前,国内钢制安全壳筒体现场安装纵缝主要采用自动气保焊工艺,其它焊缝主要采用半自动气保焊。
为了提高焊接质量和效率,对埋弧横焊工艺在钢制安全壳筒体现场安装中采用埋弧横焊工艺进行了应用研究。
1 钢制安全壳筒体现场安装环缝采用埋弧横焊工艺的可行性和必要性分析1.1 可行性分析——埋弧横焊本质为埋弧焊工艺,是ASME标准及AP1000技术规格书允许使用的焊接工艺;——埋弧焊工艺在核安全设备制造和安装活动中有成熟的应用;——埋弧横焊工艺目前已广泛应用于大型储罐中,工艺成熟;——鋼制安全壳直径大、板厚、焊缝长,适合采用埋弧横工艺;——钢制安全壳母材SA738Gr.B配套埋弧焊焊材已研发成功。
1.2 必要性分析——埋弧横焊焊接参数稳定,焊接熔深大,射线检验合格率高,焊缝外观成型均匀美观;——相对自动气保焊工艺而言,采用埋弧横焊焊接的环焊缝质量稳定可靠;——埋弧横焊为机械化焊接,对焊工技能要求较低,降低了对高技能焊接人才的依赖;——埋弧横焊接操作工相比手工焊工培训周期大为缩短,节省大量焊工培训费用;——埋弧横焊的应用能有效提高焊接效率,从而提高经济效益。
2 焊接设备采用的埋弧横焊设备型号为YS-AGW-Ⅰ,主要包括焊接机头、焊接电源、控制器、操作箱、焊接行走机架、焊剂自动循环回收系统。
AP1000_资料介绍
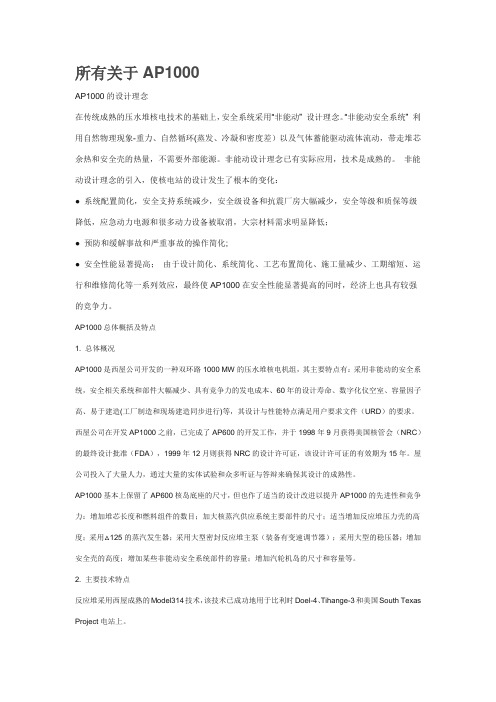
所有关于AP1000AP1000的设计理念在传统成熟的压水堆核电技术的基础上,安全系统采用“非能动” 设计理念。
“非能动安全系统” 利用自然物理现象-重力、自然循环(蒸发、冷凝和密度差)以及气体蓄能驱动流体流动,带走堆芯余热和安全壳的热量,不需要外部能源。
非能动设计理念已有实际应用,技术是成熟的。
非能动设计理念的引入,使核电站的设计发生了根本的变化:● 系统配置简化,安全支持系统减少,安全级设备和抗震厂房大幅减少,安全等级和质保等级降低,应急动力电源和很多动力设备被取消,大宗材料需求明显降低;● 预防和缓解事故和严重事故的操作简化;● 安全性能显著提高;由于设计简化、系统简化、工艺布置简化、施工量减少、工期缩短、运行和维修简化等一系列效应,最终使AP1000在安全性能显著提高的同时,经济上也具有较强的竞争力。
AP1000总体概括及特点1. 总体概况AP1000是西屋公司开发的一种双环路1000 MW的压水堆核电机组,其主要特点有:采用非能动的安全系统,安全相关系统和部件大幅减少、具有竞争力的发电成本、60年的设计寿命、数字化仪空室、容量因子高、易于建造(工厂制造和现场建造同步进行)等,其设计与性能特点满足用户要求文件(URD)的要求。
西屋公司在开发AP1000之前,已完成了AP600的开发工作,并于1998年9月获得美国核管会(NRC)的最终设计批准(FDA),1999年12月则获得NRC的设计许可证,该设计许可证的有效期为15年。
屋公司投入了大量人力,通过大量的实体试验和众多听证与答辩来确保其设计的成熟性。
AP1000基本上保留了AP600核岛底座的尺寸,但也作了适当的设计改进以提升AP1000的先进性和竞争力:增加堆芯长度和燃料组件的数目;加大核蒸汽供应系统主要部件的尺寸;适当增加反应堆压力壳的高度;采用△125的蒸汽发生器;采用大型密封反应堆主泵(装备有变速调节器);采用大型的稳压器;增加安全壳的高度;增加某些非能动安全系统部件的容量;增加汽轮机岛的尺寸和容量等。
AP1000核电站安全壳内氢气控制

AP1000核电站安全壳内氢气控制AP1000核电站作为第三代反应堆,在事故情况下安全壳内氢气控制上采取了能动和非能动相结合的方式控制厂房氢气浓度。
能动控制采用蓄电池供电的了氢气点火器,非能动控制则采用催化直接化学反应的非能动氢气复合器。
通过这两种方式的设计能够在设计基准事故时,安全壳总体氢气浓度应被限制在4%以内。
发生严重事故时,控制安全壳氢气的浓度水平应与规定要求相一致。
同时由于采用了非能动设计,能够从根本上避免福岛核事故中安全壳氢气浓度控制失效而导致的氢气爆炸,保证放射性物质控制在安全壳内。
氢气控制系统主要包括3台氢气探测器,2台非能动氢气复合器和64个氢气点火器。
其中3台氢气探测器可以提供连续的安全壳氢气浓度监测和指示,为事故后监测和事故后缓解操作的运行评估提供输入信号。
一旦安全壳内氢气浓度有变化,在10秒内就能探测到氢气浓度变化的90%,在氢气浓度达到高值时在主控室和远方停堆工作站报警,提醒操纵员采取措施。
氢气探测器是非安全相关设备,由非1E级电源供电,主要用于在严重事故后,氢气浓度快速变化时,为操纵员提供及时的氢气浓度数据,探测器的工作范围是0-20%氢气浓度。
这个范围能够涵盖氢气爆燃、爆炸事故的所有氢气浓度范围。
非能动氢气复合器没有转动部件,不需要电源或其它任何支持系统,在有反应物(氢气和氧气)时自动启动。
非能动氢气复合器由一个不锈钢包壳构成,不锈钢包壳提供结构支撑,也为催化材料提供支撑。
包壳在底部和上部开口,并在催化层上部延伸而构成一个烟囱,这可产生额外的升力来增强效率和装置的通风能力。
催化材料被放置在网状加药箱内或在金属板酶催化材料上。
气体在加药箱和金属板之间的空间流动。
在运行期间,非能动氢气复合器内的气体在复合过程中被加热,通过自然对流上升。
当被加热的气体上升时,安全壳气体混合物被吸入非能动氢气复合器的底部,被加热的同时也产生水蒸气,通过安全壳大气混合处的烟囱排出。
由于在非能动氢气复合器内的反应是放热反应,催化剂的温度可能达到600℃甚至更高。
AP1000核电机组钢制安全壳底封头施工工艺探讨
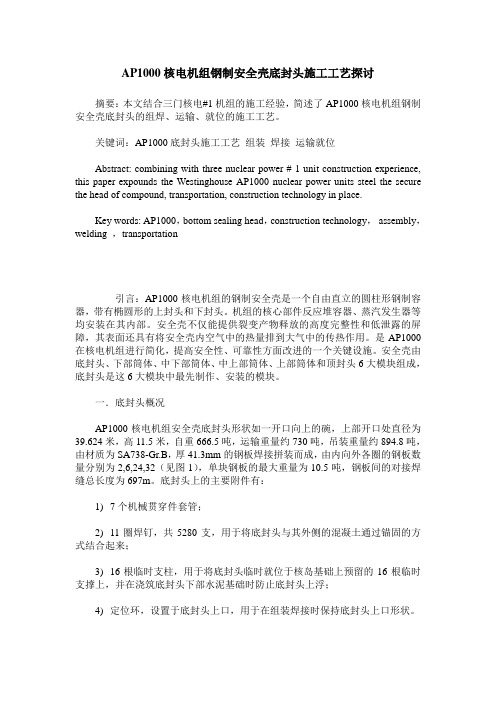
AP1000核电机组钢制安全壳底封头施工工艺探讨摘要:本文结合三门核电#1机组的施工经验,简述了AP1000核电机组钢制安全壳底封头的组焊、运输、就位的施工工艺。
关键词:AP1000底封头施工工艺组装焊接运输就位Abstract: combining with three nuclear power # 1 unit construction experience, this paper expounds the Westinghouse AP1000 nuclear power units steel the secure the head of compound, transportation, construction technology in place.Key words: AP1000,bottom sealing head,construction technology,assembly,welding ,transportation引言:AP1000核电机组的钢制安全壳是一个自由直立的圆柱形钢制容器,带有椭圆形的上封头和下封头。
机组的核心部件反应堆容器、蒸汽发生器等均安装在其内部。
安全壳不仅能提供裂变产物释放的高度完整性和低泄露的屏障,其表面还具有将安全壳内空气中的热量排到大气中的传热作用。
是AP1000在核电机组进行简化,提高安全性、可靠性方面改进的一个关键设施。
安全壳由底封头、下部筒体、中下部筒体、中上部筒体、上部筒体和顶封头6大模块组成,底封头是这6大模块中最先制作、安装的模块。
一.底封头概况AP1000核电机组安全壳底封头形状如一开口向上的碗,上部开口处直径为39.624米,高11.5米,自重666.5吨,运输重量约730吨,吊装重量约894.8吨,由材质为SA738-Gr.B,厚41.3mm的钢板焊接拼装而成,由内向外各圈的钢板数量分别为2,6,24,32(见图1),单块钢板的最大重量为10.5吨,钢板间的对接焊缝总长度为697m。
AP1000安全壳空气过滤系统设计分析及改进
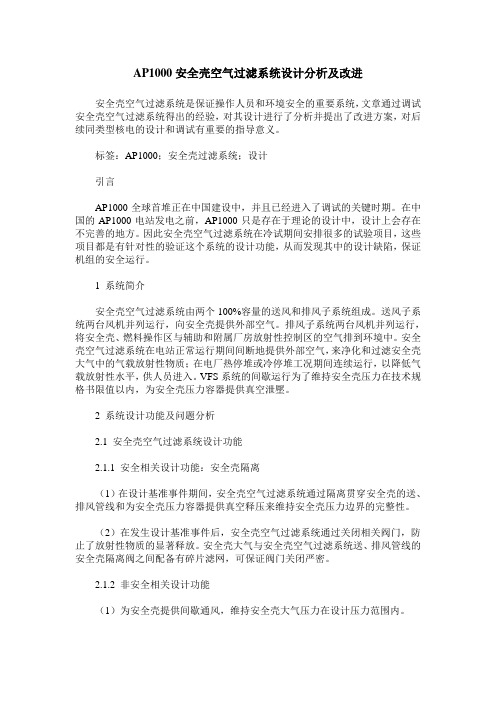
AP1000安全壳空气过滤系统设计分析及改进安全壳空气过滤系统是保证操作人员和环境安全的重要系统,文章通过调试安全壳空气过滤系统得出的经验,对其设计进行了分析并提出了改进方案,对后续同类型核电的设计和调试有重要的指导意义。
标签:AP1000;安全壳过滤系统;设计引言AP1000全球首堆正在中国建设中,并且已经进入了调试的关键时期。
在中国的AP1000电站发电之前,AP1000只是存在于理论的设计中,设计上会存在不完善的地方。
因此安全壳空气过滤系统在冷试期间安排很多的试验项目,这些项目都是有针对性的验证这个系统的设计功能,从而发现其中的设计缺陷,保证机组的安全运行。
1 系统简介安全壳空气过滤系统由两个100%容量的送风和排风子系统组成。
送风子系统两台风机并列运行,向安全壳提供外部空气。
排风子系统两台风机并列运行,将安全壳、燃料操作区与辅助和附属厂房放射性控制区的空气排到环境中。
安全壳空气过滤系统在电站正常运行期间间断地提供外部空气,来净化和过滤安全壳大气中的气载放射性物质;在电厂热停堆或冷停堆工况期间连续运行,以降低气载放射性水平,供人员进入。
VFS系统的间歇运行为了维持安全壳压力在技术规格书限值以内,为安全壳压力容器提供真空泄壓。
2 系统设计功能及问题分析2.1 安全壳空气过滤系统设计功能2.1.1 安全相关设计功能:安全壳隔离(1)在设计基准事件期间,安全壳空气过滤系统通过隔离贯穿安全壳的送、排风管线和为安全壳压力容器提供真空释压来维持安全壳压力边界的完整性。
(2)在发生设计基准事件后,安全壳空气过滤系统通过关闭相关阀门,防止了放射性物质的显著释放。
安全壳大气与安全壳空气过滤系统送、排风管线的安全壳隔离阀之间配备有碎片滤网,可保证阀门关闭严密。
2.1.2 非安全相关设计功能(1)为安全壳提供间歇通风,维持安全壳大气压力在设计压力范围内。
(2)调节安全壳送风湿度,降低安全壳冷却盘管上的冷凝。
(3)当监测到燃料操作区域和辅助/附属厂房辐射控制区(不包含保健物理和热机加工车间)正常排气放射性高时,处理以上区域的排气,并维持这些区域相对于邻近清洁区域的微负压。
第三代压水堆核电站AP1000简介1

1200MWe 电厂可利用率 1117MWe 堆芯熔化频率 3415MWt 大量早期释放频率
AP1000主要系统构成
反应堆和反应堆冷却剂系统 专设安全设施 反应堆辅助系统 蒸汽动力转换系统 电气系统 仪表控制系统
核蒸汽供应系统示意图
核电站是利用核裂变反 应产生的能量来发电。 它大体上可分为两部分: 一部分是利用核能产生 蒸汽的核岛,包括核反 应堆和一回路系统;另 一部分是利用蒸汽发电 的常规岛,包括汽轮发 电机系统。 由反应堆、一回路、 二回路实现着: 核能→热能→机械能 →电能的转换 核能以热能的形式释 放出来,被流经反应堆 的一回路高压冷却水带 走,水在堆芯中吸热, 温度升高后流出反应 堆,流经SG将热量传给 二次侧给水,降温后的 冷却水由主泵送入反应 堆不断地循环。SG二次 侧水受热后蒸发成饱和 蒸汽,通过主蒸汽管道 送往汽轮机,推动汽轮 机转动,带动发电机发 电。
系统可靠性 操纵员可不干预时间
AP1000主要特点---简化
厂房、设备布置简化--缩短建造周期
●
第二代核电站的安全系统是能动系统,它包括数量较多的泵、 安全级阀门以及相应的管道,应急柴油机,换料水箱,安全级 支持系统(通风系统、设备冷却水系统)等组成。大部分设备 都布置在安全壳外的辅助厂房内。
●
第三代AP1000核电站的安全系统是非能动系统,它仅由5只水 箱以及相关的安全阀门和管道组成。全部设备都布置在安全壳 内。
前言
固有安全性主要体现在:
① 自然的安全性:自然科学法则,事故时能控制反应性或自动终止裂 变,确保堆芯不熔化。 ② 非能动安全性:建立在惯性原理、重力法则、热传递法则等基础上 的非能动设备(无源设备)的安全性,既安全功能的实现毋需依赖 外来的动力。 ③ 后备的安全性:由冗余系统的可靠度或阻止放射性物质释放的多重 屏障提供的安全性保证。
AP1000核电站钢制安全壳
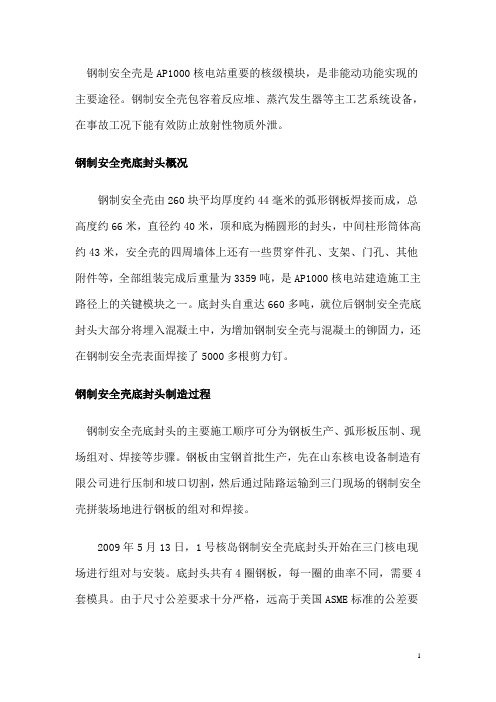
钢制安全壳是AP1000核电站重要的核级模块,是非能动功能实现的主要途径。
钢制安全壳包容着反应堆、蒸汽发生器等主工艺系统设备,在事故工况下能有效防止放射性物质外泄。
钢制安全壳底封头概况钢制安全壳由260块平均厚度约44毫米的弧形钢板焊接而成,总高度约66米,直径约40米,顶和底为椭圆形的封头,中间柱形筒体高约43米,安全壳的四周墙体上还有一些贯穿件孔、支架、门孔、其他附件等,全部组装完成后重量为3359吨,是AP1000核电站建造施工主路径上的关键模块之一。
底封头自重达660多吨,就位后钢制安全壳底封头大部分将埋入混凝土中,为增加钢制安全壳与混凝土的铆固力,还在钢制安全壳表面焊接了5000多根剪力钉。
钢制安全壳底封头制造过程钢制安全壳底封头的主要施工顺序可分为钢板生产、弧形板压制、现场组对、焊接等步骤。
钢板由宝钢首批生产,先在山东核电设备制造有限公司进行压制和坡口切割,然后通过陆路运输到三门现场的钢制安全壳拼装场地进行钢板的组对和焊接。
2009年5月13日,1号核岛钢制安全壳底封头开始在三门核电现场进行组对与安装。
底封头共有4圈钢板,每一圈的曲率不同,需要4套模具。
由于尺寸公差要求十分严格,远高于美国ASME标准的公差要求,对钢板轧制工艺提出了挑战。
工程技术人员进行了一系列试验,反复修模达10多次,验证了压制工艺,完成了技术攻关任务。
焊接作业于09年7月11日开始,底封头共有66条焊缝,焊缝总长697米。
焊前需要对钢板进行预热,预热温度100℃-200℃,同时进行正反两面焊接。
焊接时变形控制是关键,业主组织各方力量,在施工过程当中安装了一系列的卡具,并及时进行整体尺寸测量,严格依据相关标准、法规以及设计要求进行质量控制,保障了焊接工作的顺利进行。
10月7日,底封头主焊缝全部焊接完成,共无损检测RT拍片1400余张。
10月26日,1号机组钢制安全壳底封头通过了国家核安全局的检查。
底封头现场制造工作全部完成,具备吊装条件。
- 1、下载文档前请自行甄别文档内容的完整性,平台不提供额外的编辑、内容补充、找答案等附加服务。
- 2、"仅部分预览"的文档,不可在线预览部分如存在完整性等问题,可反馈申请退款(可完整预览的文档不适用该条件!)。
- 3、如文档侵犯您的权益,请联系客服反馈,我们会尽快为您处理(人工客服工作时间:9:00-18:30)。
核电厂的安全壳设计1 引言为了在电厂简化、安全性、可靠性、投资保护和电厂成本方面提供重大的、可度量的改进,AP1000采用非能动安全系统。
安全壳是实现上述改进的一个关键设施。
它不仅提供了防止裂变产物释放的高度完整、低泄漏率的屏障,其表面还承担将安全壳空气中的热量排到大气中去的传热功能。
安全壳内部结构连同非能动堆芯冷却系统(PXS)和严重事故缓解设施一起设计。
本文介绍了API000安全壳容器设计、建造、事故后特征和严重事故性能。
此外,本文也讨论了放射性释放模式,假设条件以及安全壳短期和长期性能。
2 AP1000 安全壳设计概述AP1000安全壳是一个自由直立的圆柱形钢制容器,带有椭球形的上封头和下封头。
钢制安全壳容器被完全包容在一个混凝土屏蔽体中,该厂房提供了对外部危害(如飞射物)的防护,并限制中子、γ射线、散射照射对电厂工作人员和公众的辐照。
如图l 所示,API000设计保留了和AP600相同的直径,但其高度比AP600增加了7.8 m ,从而增加了自由空间。
此外,与AP600相比,AP1000通过增加容器壁的厚度和使用SA738型B 级材料提高了安全壳的设计压力。
AP1000安全壳容器的一些重要参数与AP600的比较见表l。
如表中所示,圆柱形容器大部分的钢壁标称厚度是4.445cm,局部位置较厚,如设备闸门处。
最低一层圈柱形壳体的壁厚增加到4.762 cm,以便为预埋件过渡段中的腐蚀情况留有裕度。
封头是椭球形的,厚度为4.127cm,主直径为39.624m,而高度为11.468m。
安全壳容器由5个主要结构模块组装建造而成,每个模块都由预先成型的、喷好漆的钢板制成。
为了进一步减少安全壳内的组装活动,这些模块包含环形加强筋、吊环梁、设备闸门、人员空气闸门、贯穿件组件和其它附件,其中包括非能动安全壳冷却系统(PCS)空气挡板的支撑和水分配溢流口的固定板。
安全壳容器的设计使其能支撑环吊及其载荷,并考虑了蒸汽发生器的更换。
表1 AP1000/AP600 安全壳参数比较2.1 设备和人员闸门安全壳有2个设备闸门,其内径为4.877 m。
1个设备闸门在操作平台高度,标高为41.5 m,另1个在标高32.9 m处,它可以使设备从路线通道进入安全壳。
设备闸门由带有球形凸向的圆柱形套管拴接在安全壳容器内侧的压力密封的盘形封头组成。
2 个设备闸门中的每1个都带有1台电动绞车和1个自备电源,自备电源可以从其存放位置移动闸门并安装在闸门通道中。
人员空气闸门有2个,它们分别置于2个设备闸门附近。
每个空气闸门有2个串列布置的门,这2个门在机械上联锁,以防止2个门同时打开,在1个门打开之前,另1个门完全关闭。
可以使用专门的工具和规程将联锁旁路。
设备闸门的设计能使安全壳内部升高的压力作用在闸门的球形凸面上,而封头处于承压状态。
通过1个环形空间为每个闸门提供双重密封,该环形空间能承接密封泄漏试验的压力。
设备闸门和空气闸门的通道周围是钢制圆柱体,该通道通过屏蔽厂房从安全壳容器径向延伸到辅助厂房,安全壳容器支撑这些闸门组件。
2.2 贯穿件机械贯穿件包括燃料输送贯穿件和机械管道贯穿件。
这些贯穿件的总体设计特点与它们的工作状态相一致。
例如,主蒸汽管道和给水管道包含有尽量减小作用于安全壳容器管道载荷的波动管,以及保护波动管并防止刚好在压力容器外面发生管道破裂时使安全壳环形空间过度升压的保护管道。
较小的启动给水和蒸汽发生器排污管线贯穿件不要求装波纹管,但要求包含保护管道。
典型的管道贯穿件使用1个与工艺管道连在一起的波纹端头,它被焊接到安全壳贯穿件套管上,焊缝对于在役检查是可达的。
燃料输送管焊接到贯穿件套管上,而安全壳边界是在换料通道端处有双垫圈的盲板。
膨胀波纹管提供换料操作期间的水密封,并调节安全壳容器、安全壳内部结构和换料厂房之间的移动差。
电气贯穿件一般通过直径为305mm或457mm的安全壳接管,而且这些贯穿件要安装得便于进行泄漏试验。
3 建造安全壳容器由3.65m×11.58m、预先成型的、喷好漆的钢板建成,这些钢板焊在一起制成5个大的结构模块:下封头,3个圆柱段和上封头。
这些结构模块在靠近核电厂核岛区的3个组装区制造。
多个组装区使得可以在3个模块上同时进行工作。
当模块制成时,将用重型起重机(如lampson1500 起重机)将每个安全壳模块吊起送到它的最终位置。
安全壳容器封头和3个圆柱环在堆厂房外现场组装具有总体上的优点,因为许多关键路径上的活动能不受干扰地同时进行。
每个结构模块都安装好附件、闸门、桥型远道、管道、孔道、支撑,甚至钢筋和模板,因而减少了在拥挤的安全壳区域内的活动。
其它的优点包括:a. 材料和设备的吊装搬运都在地面上进行;b. 工作站是固定的,并且很容易提供许多必要的对恶劣天气的防护;c. 大大改善了工作的进出通道和支持设施;d. 总体上减少了人力、施工时间和成本。
美国和日本的建造公司已经审查了安全壳的制造设计,并且已经确认安全壳容器的建造能较好地满足经论证的制造经验。
安全壳容器高度的增加影响很小,因为没有增加结构模块数量,最重的安全壳模块也没有大的改变。
容器圆柱段上部环形段保留了3 板层和环吊支撑(700 t) o AP1000要求现场组装焊缝数与AP600相比没有变化,都要求4个环状焊缝以连接5 个结构模块。
增加钢板厚度和用SA738钢代替SA537钢对焊接性能没有明显影响。
现在, SA738是建造商日常使用的常规材料。
4 事故后的性能AP1000安全壳的设计能包容任何假想的设计基准事件,包括反应堆冷却剂系统环路管道或主蒸汽管道发生双端剪切断裂时释放的质量和能量,并且不超过其设计压力。
此外,钢制安全壳体与非能动安全壳冷却系统一起发生作用,能在事故后限制和迅速降低安全壳的温度和压力。
该传热功能也能降低安全壳大气中的裂变产物浓度,而安全壳的钢壳及其贯穿件的高度完整性也阻挡了裂变产物向环境的释放。
4.1 降低压力和温度在假想的设计基准事件以后,由于大量的质量和能量释放到安全壳自由空间中,使得安全壳的压力和温度迅速增加。
钢制安全壳壳体被安全壳大气加热,通过冷凝蒸汽从安全壳大气移出热能,并将热能传送到安全壳外表面的PCS 冷却流体中(水和空气)。
因此,在事故后以及其它设计基准和停堆事件后,带有PCS系统的安全壳起着安全相关的最终热阱作用。
对于AP1000,最严重的安全壳压力设计基准事故是假想的冷段双端剪切断裂(DECLG)。
对于这个事故,计算得到的安全壳峰值压力是3.99bar(57.8 psi g),它出现在始发事件后的23 min。
通过安全壳壳体的传热也有效而迅速地降低安全壳内的压力和温度。
正如图2 和图3 所示,安全壳压力在5.5h 内降低到约1.65 bar(24 psi g)。
在24h 时安全壳压力约为1.52 bar(22 psi g),而安全壳温度是104℃。
安全壳内大气和外部环境压力差的迅速减小将有助于限制放射性物质向环境的释放,因为这时裂变产物从安全壳向外部环境泄漏的驱动力迅速减小。
要指出的是,图2 和图3 描述了安全分析评估的结果。
最大安全壳压力的计算中考虑了较大的保守性,其中包括:a. 保守假设的高衰变热水平;b. 保守假设的安全壳内低热阱;c. 保守假设的安全壳内表面和外表面上的低热传输;d. 保守假设的安全壳外部的PCS低的水流量和淋湿面积;e. 不考虑安全壳外冷却水的热去除作用;f. 假定外部水和空气温度保持在它们的最大的安全允许值不变:g. 保守假设RCS 大的质量和能量释放。
在事故后的长期阶段(几天后),安全壳压力将随着衰变热的减少而降低。
安全壳和安全壳内的安全设备在这些条件下运行将不存在问题。
表2给出了几个最严重的设计基准事故安全分析的概要结果。
通常事故后,即使大LOCA 事故后,释放到安全壳中的放射性剂量微乎其微。
然而,如果发生如PRA所考虑的多重失效,则有可能使堆芯损坏,以致有相当多的放射性释放到安全壳中。
在这种情况下,希望安全壳的压力降低到接近环境大气压力。
因为这种情况对应于一个PRA 系列,因此现实的分析假设是适合的。
类似预计的长期安全壳的压力也应用现实假设进行了计算,见表3 。
如果冷却水流量在72h 增加到PCS 最小流量22.7 m3/h 以上,也能够达到较低的压力。
这些低压力和低温度与在堆芯熔化事故后将电厂带到安全、稳定状态的目标是一致的。
表2 最严重设计基准事故下安全壳压力变化概要结果表3 双端剪切断裂LOCA后预计的安全壳压力变化同时需要指出的是,有几个非安全设施可用来进一步降低安全壳的压力和温度。
这些系统包括正常余热排出系统和安全壳风机冷却器。
因为这些设施不是安全相关设施,因此在设计基准安全分析中它们并没有被考虑。
AP1000 安全壳设计和PCS设计有几项显著的优点,包括:a. 安全壳冷却与堆芯冷却是相互独立的,因此不会发生可能引起堆芯熔化的共模失效;b. 安全壳冷却更加可靠。
PCS触发仅仅需要打开3个触发阀门中的1个,3个阀门中的2个是故障开启的气动阀,而另一个是电动阀。
该设计提供了3 重冗余性和2种多样性;c. 几种备用水掘通过管道供安全壳使用,包括除盐水和消防水。
一些临时水源,如消防车,也能方便地连接到安全壳;d. PCS仅仅通过空气冷却就能提供足够的热量排出能力,这可以防止安全壳超压事故,进一步降低放射性大量释放的可能性;e. 电厂设计大大简化,因为PCS运行不依靠复杂的电源网络(交流或直流)、冷却水系统或HVAC 系统;f. 与应用安全壳喷淋系统和安全壳外水循环系统冷却安全壳以缓解严重事故的核电厂相比,AP1000 放射性释放到环境的可能性大大降低。
这也是为什么EUR不允许严重事故工况下安全壳水在安全壳外循环的原因。
4.2 事故后泄漏控制设计基准剂量计算假定在事故期间从AP1000安全壳的泄漏率保持在最大安全允许的泄漏率值0.1%/d不变。
为了计算主控室和厂外的设计基准剂量,该泄漏假定直接进入环境大气。
这些假设是很保守的,因为:a. 安全壳壳体具有高度的完整性,坚固的钢容器有4.44 cm 厚。
连接钢板的焊缝按ASME 要求检查,保证其没有泄漏;b. 尽量减少了通过贯穿件泄漏的可能性。
AP1000的贯穿件比采用能动安全设施和轴密封泵的核电厂少得多(约50%)。
此外,根据运行经验仔细选择了隔离间。
最后,AP1000使用少很多的安全壳HVAC 吹扫管线和高度完整性的隔离阀,减少了泄漏的机会。
在现役核电厂中,吹扫管线的泄漏已成为一个问题;c. 非能动安全壳冷却系统的空气冷却仅仅用于安全壳操作平台标高以上的部分,这一段没有能直接泄漏到大气的贯穿件。
在操作平台以上有2个贯穿件:1个是设备闸门,另l个是人员闸门。