汽轮机#1轴承振动大分析及处理方法
汽轮机参数

三、汽轮机主要技术规范(一)汽轮机铭牌主要技术参数汽轮机型号 C12-3.43/0.981型式抽汽凝汽式汽轮机主汽门前蒸汽压力额定3.43(+0.2)MPa(a)-0.3最高3.63MPa(a)(可长期连续运行)主汽门前蒸汽温度额定435(+5)℃-15最高445℃(可长期连续运行)额定进汽量 87t/h最大进汽量 127t/h(可长期连续运行)额定抽汽量 50t/h最大抽汽量 80t/h额定抽汽压力 0.981MPa(G)抽汽压力范围 0.785~1.275MPa(G)额定抽汽温度317.2 ℃抽汽温度范围 250~330℃额定功率 12 MW汽轮机铭牌功率 12 MW最大功率 15 MW汽轮机转向(机头向机尾看)顺时针方向汽轮机额定转速 3000r/min汽轮机一发电机轴系临界转速 1735r/min汽轮机单个转子的临界转速 1470r/min汽轮机轴承座允许最大振动 0.03mm(双振幅值)过临界转速时轴承座允许最大振动 0.10mm(双振幅值)允许电频率变化范围50±0.5Hz汽轮机中心高(距运转平台) 750mm汽轮机本体总重 57t汽轮机上半总重(连同隔板上半等) 15t汽轮机下半重(包括隔板下半等) 19t汽轮机转子总重 7.83t汽轮机本体最大尺寸(长×宽×高)mm 6021×3590×3635(二)汽轮机技术要求;本汽轮机实际运行条件:进汽量为72 t/h,最大进汽量83 t/h;额定抽汽量45 t/h;无高加、除氧器回热抽汽;循环水温度≤33℃。
锅炉正常运行时,保证C12机组纯凝工况下发电量能达到12MW并长期稳定运行。
并考虑两台锅炉运行时,其中一台汽机故障时另一台汽机在保证供汽条件下,抽凝状态运行能达到15MW。
12MW抽凝式汽轮发电机组的实际运行工况:型式抽汽凝汽式汽轮机)MPa(a)主汽门前蒸汽压力额定3.43(+0.2-0.3最高3.63MPa(a)(可长期连续运行))℃主汽门前蒸汽温度额定435(+5-15最高445℃(可长期连续运行)额定进汽量 71t/h最大进汽量 83t/h(可长期连续运行)额定抽汽量 35t/h最大抽汽量 45t/h额定抽汽压力 0.981MPa(G)抽汽压力范围 0.785~1.275MPa(G)额定抽汽温度317.2 ℃抽汽温度范围 250~330℃四、发电机技术规范(一)发电机参数型号 QFW-15-2A额定功率15MW额定功率因数 0.8额定电压10.5kV额定转速 3000r/min频率 50Hz相数 3极数 2定子线圈接法 Y效率不低于 97%短路比 0.48顶值电压 1.8 倍额定励磁电压电压响应比 1 倍额定励磁电压/秒允许强励持续时间 10 s定、转子线圈绝缘等级/使用等级 F级/ F级空冷器进水量 100t/h交流无刷励磁机型号 TFLW80-3000A功率 80 kW直流输出电压 250V直流输出电流 320A接法 Y相数 3频率 150 Hz功率因数 0.95每臂并联支路数 1个整流方式三相全波整流二极管参数 250A/1200V永磁副励磁机型号 TFY2.85-3000 C 容量 2.85kVA额定电压 190V额定电流 15A频率 400Hz相数单相功率因数 0.93.1干熄焦锅炉技术参数3.1.1 干熄焦锅炉型式:单汽包自然循环型室外式干熄焦锅炉3.1.2 干熄焦锅炉循环系统详见系统图3.1.3 锅炉入口烟气量:~210,000 Nm3/h 980℃(最大)~190,000 Nm3/h 960℃(正常) 3.1.4锅炉入口烟气温度: 900~980℃3.1.5 锅炉出口烟气温度: 160~180℃3.1.6循环气体成分见下表(供参考):循环气体成分表2锅炉入口含尘浓度:~10g/Nm33.1.7锅炉额定蒸发量:(红焦处理量140t/h) 83t/h(红焦处理量125t/h) 72.5t/h3.1.8汽包工作压力: 5.0MPa(G)3.1.9主蒸汽压力(二次过热器出口):4.5 MPa(G)(锅炉出口主蒸汽调节阀后): 4.2±0.2 MPa(G)3.1.10过热器出口蒸汽温度: 450±10℃锅炉出口参数在需方满足前提条件下,达到工况点对应参数:锅炉额定蒸发量:(红焦处理量140t/h) 83t/h正常蒸发量:(红焦处理量125t/h) 72.5t/h主蒸汽压力(二次过热器出口): 4.5MPa(G)(锅炉出口主蒸汽调节阀后): 4.2±0.2 MPa(G)过热器出口蒸汽温度: 450±10℃锅炉外表面温度:锅炉设备在正常运行条件下,当环境温度为25℃时,锅炉的炉墙外表温度不超过50℃,当环境温度大于25℃时,锅炉的炉墙外表温度不超过环境温度25℃,散热量不超过290W/M2。
汽轮机的功率计算公式

汽轮机的功率计算公式
汽轮机的功率计算公式
汽轮机功率的计算是一个最基本的汽轮机工程设计计算的步骤。
通常情况下,汽轮机功率的计算是按照热力学原理考虑,即计算机的输入功率和输出功率之差来求。
在计算汽轮机功率时,首先需要确定机组的参数,如汽轮机内燃机的蒸汽压力,汽轮机的汽温,转速,流量等;其次,需要计算汽轮机的发电效率,即输入功率与输出功率之比;最后,根据实际的发电效率及参数,可以计算出汽轮机的输出功率。
其计算公式如下:
P=(p1-p2)/e × m × hg
其中:
P 为汽轮机的输出功率;
P1 为蒸汽入口压力;
P2 为蒸汽出口压力;
E 为汽轮机的发电效率;
M 为汽轮机转速;
HG 为汽轮机的水头。
- 1 -。
汽轮机名词解释
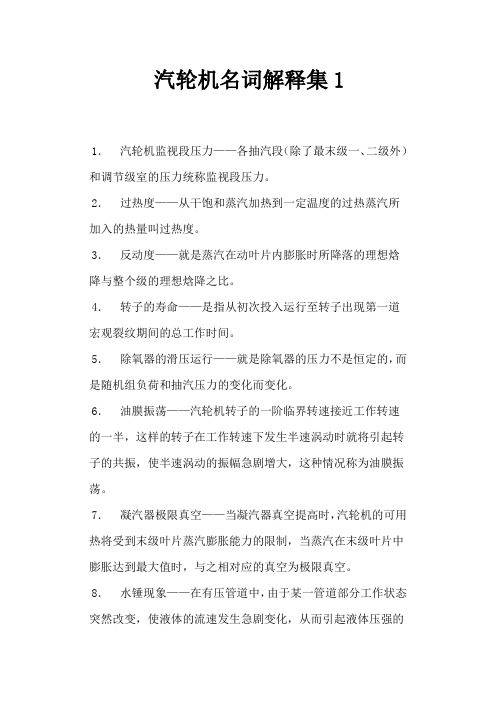
汽轮机名词解释集11.汽轮机监视段压力——各抽汽段(除了最末级一、二级外)和调节级室的压力统称监视段压力。
2.过热度——从干饱和蒸汽加热到一定温度的过热蒸汽所加入的热量叫过热度。
3.反动度——就是蒸汽在动叶片内膨胀时所降落的理想焓降与整个级的理想焓降之比。
4.转子的寿命——是指从初次投入运行至转子出现第一道宏观裂纹期间的总工作时间。
5.除氧器的滑压运行——就是除氧器的压力不是恒定的,而是随机组负荷和抽汽压力的变化而变化。
6.油膜振荡——汽轮机转子的一阶临界转速接近工作转速的一半,这样的转子在工作转速下发生半速涡动时就将引起转子的共振,使半速涡动的振幅急剧增大,这种情况称为油膜振荡。
7.凝汽器极限真空——当凝汽器真空提高时,汽轮机的可用热将受到末级叶片蒸汽膨胀能力的限制,当蒸汽在末级叶片中膨胀达到最大值时,与之相对应的真空为极限真空。
8.水锤现象——在有压管道中,由于某一管道部分工作状态突然改变,使液体的流速发生急剧变化,从而引起液体压强的骤然大幅波动,这种现象叫水锤现象。
9.轴向位移——在汽轮机运行中,轴向推力作用于转子上,使之产生轴向窜动称为轴向位移。
10.余速损失——蒸汽离开动叶片时具有一定的余速,即具有一定的动能,这部分没被利用完的动能称余速损失。
11.转子惰走时间——发电机解列后,从汽轮机主汽门、调门关闭时起,到转子完全静止这段时间叫转子惰走时间。
12.死点——热膨胀时,纵销引导轴承座和汽缸沿轴向滑动,横销与纵销作用线的交点称为死点。
13.弹性变形——物体在受外力作用时,不论大小,均要发生变形,当外力停止作用后,如果物体能恢复到原来的形状和尺寸,则这种变形称物体的弹性变形。
14.塑性变形——物体受到外力的作用时,当外力增大到一定程度,即使停止外力作用,物体也不能恢复到原来的形状和尺寸,则这种变形称物体的塑性变形。
15.除氧器自生沸腾——指过量的热疏水进入除氧器时,其汽化出的蒸汽量已经满足或超过除氧器内的用汽需要,从而使除氧器内的给水不需要回热抽汽加热自己就沸腾,这种现象叫除氧器自生沸腾。
汽轮机名词解释
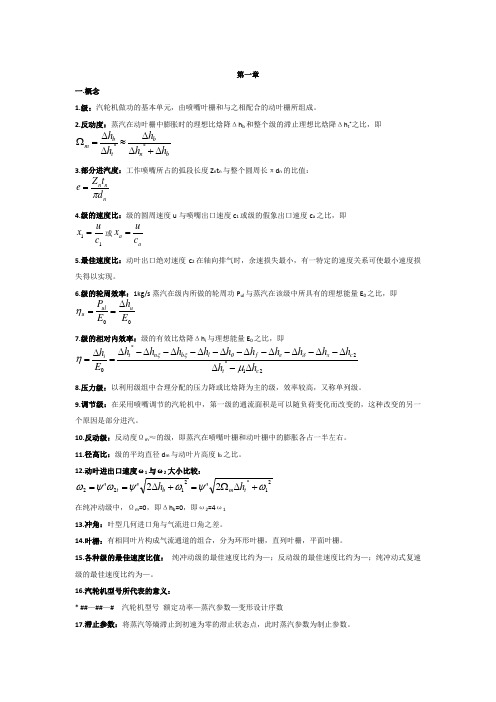
第一章一.概念1.级:汽轮机做功的基本单元,由喷嘴叶栅和与之相配合的动叶栅所组成。
2.反动度:蒸汽在动叶栅中膨胀时的理想比焓降Δh b 和整个级的滞止理想比焓降Δh t *之比,即b n b t b m h h h h h ∆+∆∆≈∆∆=Ω**3.部分进汽度:工作喷嘴所占的弧段长度Z n t n 与整个圆周长πd n 的比值:nnn d t Z e π= 4.级的速度比:级的圆周速度u 与喷嘴出口速度c 1或级的假象出口速度c a 之比,即 11c ux =或a a c u x =5.最佳速度比:动叶出口绝对速度c 2在轴向排气时,余速损失最小,有一特定的速度关系可使最小速度损失得以实现。
6.级的轮周效率:1kg/s 蒸汽在级内所做的轮周功P ul 与蒸汽在该级中所具有的理想能量E 0之比,即 00E h E P u ul u ∆==η 7.级的相对内效率:级的有效比焓降Δh i 与理想能量E 0之比,即 21*2*0c t c x e f l b n t i h h h h h h h h h h h h E h ∆-∆∆-∆-∆-∆-∆-∆-∆-∆-∆-∆=∆=μηδθξξ8.压力级:以利用级组中合理分配的压力降或比焓降为主的级,效率较高,又称单列级。
9.调节级:在采用喷嘴调节的汽轮机中,第一级的通流面积是可以随负荷变化而改变的,这种改变的另一个原因是部分进汽。
10.反动级:反动度Ωm ≈的级,即蒸汽在喷嘴叶栅和动叶栅中的膨胀各占一半左右。
11.径高比:级的平均直径d m 与动叶片高度l b 之比。
12.动叶进出口速度ω1与ω2大小比较:21*21222'2''ωψωψωψω+∆Ω=+∆==t m b t h h在纯冲动级中,Ωm =0,即Δh b =0,即ω2=4ω113.冲角:叶型几何进口角与气流进口角之差。
14.叶栅:有相同叶片构成气流通道的组合,分为环形叶栅,直列叶栅,平面叶栅。
汽轮机名词解释
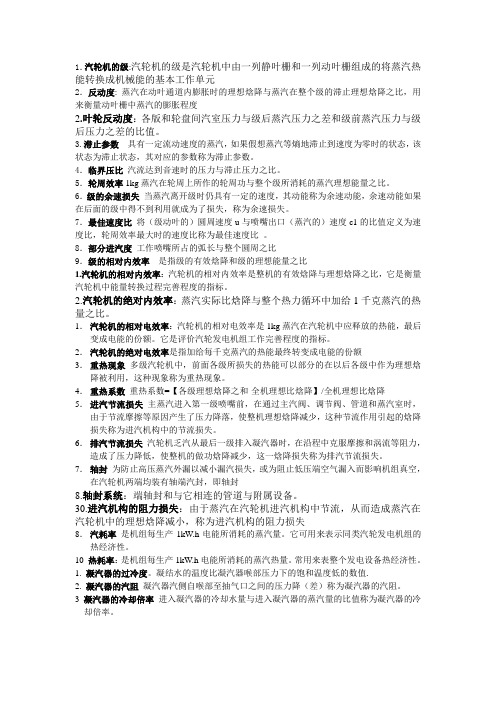
1.汽轮机的级:汽轮机的级是汽轮机中由一列静叶栅和一列动叶栅组成的将蒸汽热能转换成机械能的基本工作单元2.反动度: 蒸汽在动叶通道内膨胀时的理想焓降与蒸汽在整个级的滞止理想焓降之比,用来衡量动叶栅中蒸汽的膨胀程度2.叶轮反动度:各版和轮盘间汽室压力与级后蒸汽压力之差和级前蒸汽压力与级后压力之差的比值。
3.滞止参数具有一定流动速度的蒸汽,如果假想蒸汽等熵地滞止到速度为零时的状态,该状态为滞止状态,其对应的参数称为滞止参数。
4.临界压比汽流达到音速时的压力与滞止压力之比。
5.轮周效率1kg蒸汽在轮周上所作的轮周功与整个级所消耗的蒸汽理想能量之比。
6.级的余速损失当蒸汽离开级时仍具有一定的速度,其动能称为余速动能,余速动能如果在后面的级中得不到利用就成为了损失,称为余速损失。
7.最佳速度比将(级动叶的)圆周速度u与喷嘴出口(蒸汽的)速度c1的比值定义为速度比,轮周效率最大时的速度比称为最佳速度比。
8.部分进汽度工作喷嘴所占的弧长与整个圆周之比9.级的相对内效率是指级的有效焓降和级的理想能量之比1.汽轮机的相对内效率:汽轮机的相对内效率是整机的有效焓降与理想焓降之比,它是衡量汽轮机中能量转换过程完善程度的指标。
2.汽轮机的绝对内效率:蒸汽实际比焓降与整个热力循环中加给1千克蒸汽的热量之比。
1.汽轮机的相对电效率:汽轮机的相对电效率是1kg蒸汽在汽轮机中应释放的热能,最后变成电能的份额。
它是评价汽轮发电机组工作完善程度的指标。
2.汽轮机的绝对电效率是指加给每千克蒸汽的热能最终转变成电能的份额3.重热现象多级汽轮机中,前面各级所损失的热能可以部分的在以后各级中作为理想焓降被利用,这种现象称为重热现象。
4.重热系数重热系数=【各级理想焓降之和-全机理想比焓降】/全机理想比焓降5.进汽节流损失主蒸汽进入第一级喷嘴前,在通过主汽阀、调节阀、管道和蒸汽室时,由于节流摩擦等原因产生了压力降落,使整机理想焓降减少,这种节流作用引起的焓降损失称为进汽机构中的节流损失。
什么是汽轮机,汽轮机的组成部分有哪些?

什么是汽轮机,汽轮机的组成部分有哪些?汽轮机是一种将热能转化为机械能的热力机械,它利用高温高压蒸汽对叶轮产生冲击力,从而驱动叶轮旋转,达到转动机械的目的。
汽轮机的组成部分主要包括以下几个方面。
蒸汽系统蒸汽系统是汽轮机的核心部件,主要包括锅炉、汽轮机本体和凝汽器三部分。
其中,锅炉是汽轮机的热源,将火力、燃气或核能等其它能源释放的热能转化为蒸汽,向汽轮机中输送高温高压的蒸汽。
汽轮机本体是蒸汽动力机的核心,它将高温高压的蒸汽能转化为机械能,驱动发电机旋转,把热能转化为电能。
凝汽器则是汽轮机发电的必备附件,它能够将汽轮机排出的低温低压蒸汽冷却至凝冻状态,回收其中所含的热能,提高汽轮机的热效率。
叶轮机组叶轮机组包括高压缸、中压缸、低压缸和转子,其中,高压缸的叶轮转速最快,它注入的蒸汽温度最高,能够承载最大的工作压力;中压缸的叶轮转速次之,它接收高压缸排出的蒸汽,供低压缸进一步扩张利用;低压缸的叶轮转速最慢,它是整个汽轮机中体积最大的部件,也是其中最后一个转动的叶轮。
转子则是一系列叶轮的集合,它们直接承受蒸汽的能量,产生旋转并驱动发电。
控制和保护系统控制和保护系统是汽轮机重要的配套系统,它可以对蒸汽供应、发电机负载、汽轮机温度等多个因素进行监测和控制,保证汽轮机的安全、稳定运行。
其中,汽轮机控制系统包括液压、电气、机械三种控制方式;汽轮机保护系统则包括行程开关、超温保护、高低液位保护等多个保护装置,它能够对突发事故进行及时报警。
以上是汽轮机的主要组成部分和结构特点,我们可以看出,汽轮机在工业生产和生活中都扮演着十分重要的角色。
在今后的生产和发展中,汽轮机的组成和特点会不断地发生变化,它将更加智能化,自动化,高效化,为我们的工作和生活带来更多便利。
汽轮机生产工艺

汽轮机生产工艺
汽轮机是一种将燃气燃料转化为动力能源的设备,广泛应用于电力和工业领域。
汽轮机的生产工艺主要包括以下几个步骤。
首先是材料准备阶段,汽轮机的主要材料包括高温合金和钢材。
这些材料需要经过原材料选择、加工和质检等步骤,以保证其质量和性能符合要求。
接下来是焊接工艺。
汽轮机的组装和制造涉及到大量的焊接工艺,包括气体保护焊、电弧焊和激光焊等。
焊接工艺需要根据不同的部件和要求选择合适的焊接方法,并严格控制焊接参数,以确保焊接质量达到标准。
然后是机械加工阶段。
汽轮机的零部件需要经过数控机床、车床和磨床等机械加工设备的加工。
机械加工工艺包括车削、铣削、钻孔和磨削等,通过这些工艺可以使零部件达到规定的尺寸和形状要求。
再者是热处理工艺。
汽轮机的部分零部件需要进行热处理,以提高其硬度和强度。
热处理工艺包括退火、正火、淬火和固溶处理等,通过这些工艺可以改变材料的组织结构和性能。
最后是装配和调试阶段。
完成所有零部件的加工和热处理后,需要进行总装和调试。
总装包括零部件的组装和连接,调试包括机械调试和电气调试。
通过装配和调试可以确保汽轮机的各项指标和功能符合设计要求。
总之,汽轮机的生产工艺涉及到材料准备、焊接、机械加工、热处理、装配和调试等多个环节。
每个环节都需要严格控制和操作,以确保最终产品的质量和性能。
汽轮机--简单提纲

- 1、下载文档前请自行甄别文档内容的完整性,平台不提供额外的编辑、内容补充、找答案等附加服务。
- 2、"仅部分预览"的文档,不可在线预览部分如存在完整性等问题,可反馈申请退款(可完整预览的文档不适用该条件!)。
- 3、如文档侵犯您的权益,请联系客服反馈,我们会尽快为您处理(人工客服工作时间:9:00-18:30)。
汽轮机#1轴承振动大分析及处理方法
顾崇廉,谈立春
(北京太阳宫燃气热电有限公司,北京 100028)
摘要:针对汽轮机#1轴承振动偏大,特别是机组带大负荷时振动迅速增加,同时出现半频振动,且半频分量的比重较大。
从轴承自激振动、轴系负荷分配和汽流激振方面进行分析,利用检修期间,对#1轴振问题进行治理,使机组振动水平达到优秀范围内。
关键词:轴振;轴承自激振动;晃度;汽流激振;
一、前言
北京太阳宫电厂为燃气—蒸汽联合循环机组,汽轮机为LN275/CC154-11.49
/0.613/0.276/566/566型哈汽机组, 1、2#轴承为4瓦块可倾瓦轴承,振动保护监视系统TSI,监测1~6号轴承X、Y方向(分别为面向机头向后看垂直中分面左侧45°和右侧45°位置)转子相对振动以及垂直方向的轴承座振动。
二、机组振动特点
2010年10月机组检修之前,机组振动主要反映在#1轴承轴振动(特别是Y方向轴振)偏大,轴承座振动很小,通常不超过10μm 。
对振动数据进行分析,其#1轴承轴振具有如下特征:
(1)#1轴承轴振测点位置晃度值过大
根据该机组多次冷态启动过程数据,发现在低转速(通常400r/min左右)时#1轴承X、Y方向轴振动数据(即晃度值)分别高达75μm和90μm左右,严重超标。
但基频值分别只有25μm和30μm左右。
(2)带负荷后振动出现一定程度的爬升
机组带负荷后#1轴承轴振较空载时的数据明显增大(特别是Y方向轴振)。
表1列出的是不同工况下1、2号轴承轴振动数据,从中看出热态空载时#1轴承轴振较冷态空载时有一定的增大,223MW时的振动(Y方向轴振)进一步增大。
表1 不同工况下汽轮机1、2#轴承轴振基频和通频值(μm∠°/μm)
(3)额定负荷附近振动剧烈波动
当机组在较大负荷(220MW附近)运行时,#1轴承轴振就呈现一定的波动,波动主要来
自21.87Hz的低频分量,幅值5~50μm不等,而基频分量基本不变;当负荷超过240MW,振动大幅波动,见图1,波动仍是21.87Hz的低频分量为主,其最大波动到达103μm。
见图2
图1 DCS系统记录的#1轴承轴振随负荷变化
图2 TDM记录的250MW工况下#1轴承轴振频谱
三、振动原因分析
根据汽轮机振动的以上三个特点,下面进行相应的原因分析。
(1)晃度和测量位置问题分析
转子的晃度是由机械的、电磁的、材质的因素(例如被测轴段偏心、弯曲、转轴表面不圆度及局部缺陷、剩磁、材质不均匀、表层残余应力等)引起的非振动偏差。
GB/T 11348.2-2007标准规定各测点总的晃度值不应超过相应许可振动位移的25%,#1轴承X、Y 方向轴振测点处晃度高达75μm和90μm左右,远超过标准要求。
在采用电涡流传感器进行轴振动测量中,通常仪表上显示的轴振动测量数值是该振动测点的晃度值和实际的轴振动值的矢量之和。
由于#1轴承轴振测点处的晃度值偏大,使得二次仪表显示的振动值较实际振
动值大。
由于#1轴承X、Y方向轴振测点位置不在GB/T 11348.2-2007标准规定的轴承中央,而
在轴承中央外侧接近轴封处的前箱外油挡处,由于此处高温轴颈容易产生油渍,并且易污染,造成轴颈光洁度较差。
(2)带负荷振动的增大问题分析
由于带负荷(热态下)#1轴承轴振动明显比空载时振动要大,说明高中压转子存在一定的热变形,造成转子热态下平衡状态的恶化。
除转子本体热变形产生附加的不平衡振动外,还可能由于与高中压转子相连的主油泵小轴热态下摆度的增大引起,其通常在转子存在一定的热变形时更加明显。
(3)大负荷附近振动剧烈波动问题分析
在机组240MW负荷以上时,#1轴承轴振出现大幅波动,以21.87Hz的低频分量为主,振动成分中出现低频分量一般预示着该振动系统的稳定性较差。
引发低频振动的原因通常包括轴承自激振动和汽流激振。
轴承自激振动是润滑轴承油膜力激发的不稳定振动,其一般是由过大的轴承磨损或间隙、不合适的轴承设计、轴承承载过小、润滑油参数的改变等因素引起的。
在机组由冷态到带大负荷(热态)过程中,轴颈在轴承中的位置会出现一定的变化。
从表2所列的各工况下间隙电压变化数值,可以看出#1轴颈向上及Y方向浮动量过大,达0.385mm(根据振动传感器灵敏度可以换算成轴颈位置相对变化量),这会造成轴承在热态下承载下降,导致稳定性变差。
汽流激振通常是当转子在汽缸中出现偏心时作用在转子上的蒸汽力引起的自激振动,通常发生在高参数大容量机组的高中压转子上,往往是出现在较大负荷工况。
从机组运行中间隙电压的变化,发现轴颈在轴承中明显向Y方向偏斜(或转子在汽缸中偏斜),会产生较大的蒸汽激振力,造成振动失稳。
当然,机组运行中转子在汽缸中位置的偏斜,除与作用在转子上的蒸汽力大小和方向有关外,也与汽缸的不均匀膨胀有关。
如果存在汽缸跑偏现象,则也会造成转子在汽缸中相对位置的显著变化。
综上所述,#1轴承振动失稳是轴承自激振动和汽流激振共同作用的结果。
表2 汽轮机1、2号轴承间隙电压变化(V)
四、检修中解决振动问题采取的措施
(1)控制和减小#1轴振测点的晃度
在机组的大修中,检查发现#1轴振测量面的光洁度较差,不仅有油档齿磨出的划痕,还有疑似涡流探头头部保护塑料的融化物(图3方框内所示),在随后的检修工作中,通过对测量表面的车削打磨处理,同时又在轴颈附近位置增加了新的#1轴振测点,其晃度又明显小于老测点,如表3,并将新测点引入保护。
图3 原#1轴承轴振的测量面
图4 #1轴振新测点安装位置表3 检修前后,#1轴振测点的晃度变化(通频,单位:μm)
(2)调整轴承安装参数
由于转子运行中#1轴颈向Y方向偏移量过大,因此为保证运行中轴颈在轴承中相对中部,可调整轴承安装参数,以减小汽流激振力,进而降低不稳定的低频振动分量。
此外,对轴承安装参数进行调整也可增大Y方向油膜刚度,以减小热态下Y方向轴振。
现场优化轴承性能的方法有两种:一是标高调整;二是轴承间隙调整。
由于#1轴承位于轴系端部,理论计算结果和现场实践经验均表明#1轴承标高对其性能的影响十分有限,因此检修中主要对#1轴承间隙进行优化计算。
转子支撑力(G)主要包括轴承承载力(W)和蒸汽作用力(F),就高中压转子#1轴承侧的支撑而言,存在力平衡(如图4):
111
G W F
=+。
另外,#1轴承相关安装参数如表6所示。
图5 高中压转子#1轴承侧的受力示意图
采用有限元-差分法分别对如下两种假设条件下、安装间隙分别为0.63mm(检修前轴承间隙)和0.51mm(轴承安装标准的下限)的轴承性能进行计算分析,
(1)假设蒸汽对转子的托起力(
1
F)不变,即轴承承载力(
1
W)也不变由于轴承承载力不变,#1轴承在不同安装间隙下的油膜刚度和阻尼也不会有明显变化,但在机组定速3000r/min到230MW负荷过程中,轴颈浮起量将大幅减小,见表4,使转子在汽缸中位置的偏斜量减小,进而减小汽流激振力,从而最大限度地控制汽流激振。
表4 不同安装间隙下#1轴颈的浮起量
(2)假设转子的浮起量不变,即轴承偏心率不变
表5给出了不同直径安装间隙工况,在机组定速3000r/min到230MW负荷过程中,轴承油膜刚度和阻尼的变化。
可以看出随着轴承安装间隙的减小,轴承油膜刚度和阻尼逐渐增大。
表5 不同工况下#1轴承的性能参数
由以上计算分析来看,减小轴承间隙不仅能够增强油膜刚度和阻尼,增强轴承的稳定性,同时减小浮起量改善通流的同心度,降低机组振动。
因此在检修期间调整#1瓦下瓦块调整垫片,把#1轴承直径安装间隙左、右侧分别减小到0.52
mm、0.54mm。
(3)调整轴系负荷分配
调整#2瓦枕垫块,使#2瓦标高减小0.14mm,增加高中压轴系载荷,提高轴承稳定性,减小轴颈浮起量。
综上处理后,机组在254MW时,各轴振在优秀范围,其#1轴振Y向的频谱如图6。
图6 TDM记录的254MW工况下#1轴承轴振频谱
五、总结
检修前对振动问题的分析和检修期间的处理,随后又进行了现场动平衡,在检修后,机组带满负荷时#1轴承振动在优秀范围,同时半频分量很小。
验证了其方案的可行性。