七大浪费培训教材 精 完整版
合集下载
7大浪费及IE基础内训教材

□ 价值
□ 价值
□ 价值
□ 浪费
⑤ 组合PCB
□ 浪费
⑧ 更换箱子
□ 浪费
□ 价值
□ 价值
□ 价值
□ 浪费
□ 浪费
□ 浪费
⑥ 把螺丝刀拿过来
⑨ 挑选出不良产品
Ⅰ. 对浪费的认识
4) 工作和活动
产生净附加价值的动作
• 组装 • 焊接 • 粉刷 • 加工
产生低附加价值的动作
[人] 手工拧紧 KNOW-HOW 工作 追加工作(设计变更) 不良生产
□ 因“生产过剩”而发生的浪费种类。 ● 过早消耗材料和零件。(即过早生产就会加重利息负担。) ● 增加材料、产品的货盘和箱子。 ● 增加台车等搬运小车。 ● 在不知不觉中增加许多费用。(工资、折旧费、管理费等) ● 由于隐藏浪费问题,使工作者无法认识到需要改善。生产过剩可谓是“最大恶”。
Ⅰ. 对浪费的认识
用力组装
□ 单纯动作 □ 附带动作 □ 附加价值(非效率性) □ 附加价值(效率性)
按电钮
□ 单纯动作 □ 附带动作 □ 附加价值(非效率性) □ 附加价值(效率性)
Ⅰ. 对浪费的认识
----?
搞不好会 败家的!
了解工作(Work)和活动(Move) ( 工作 ≠ 活动 )
一, 二,三。。
嘿呦 嘿呦
问题发现
改善方法
1. 抓、放动作导致的浪费 - 将零件和工具抓或放的动
作必定带来浪费。 2. 不可取的方法
1. 不使用零件和工具 - 即使不使用工具或零件,
也要能够进行工作。
- 将零件和工具放在工作 者的后面。
2. 动作经济原则
- 需要动脚。
-应把零件和工具放在容易 使用或放回的场所。
七大浪费教材

个别效率与整体效率
能力需求:100件/H
项目 能力 达成率 奖金 效率
工序1 100件/H 100% 标准产量奖金 个别效率合格
工序2 125件/H 125% 125%奖金 个别效率高
举例:交 通 PSK-QSC, SL, ’02_Nov
工序3 80件/H 80% 0 个别效率低
工序4 100件/H 80% 0 个别效率低
13
13
Cell Promotion 库(III存) – 的從雁浪行费理論看 Cell Operation
库存的浪费有哪些?
1.产生不必要的搬运,堆积,放置,防护处理, 寻找等浪费
当库存增加时,搬运量将增加,需要 增加堆积和放置的场所,需要增加防护 措施,日常管理和领用时需要增加额外 时间等,甚至盘点的时间都要增加,这 些都是浪费。
地下工厂
过量生产的浪费
不良/再作业的浪费
5 %
搬运的浪费
企业每生产一件产品就 在制造一份浪费。伴随企业运 营中各业务环节不被察觉或不
动作 的浪
附加 值
浪费 / 非附 加值
被重视的浪费,日本企业管理
库存的浪费
界将之形象地比喻为“地下工 厂”。
费
等待的浪费 加工其本身的浪费 某国外管理专家:
在我的眼里,中国企业地上铺的都是黄金!
认识浪费
VA:价值
• 在必要的时间,生产必要数量的产品
NVA:无价值
• 任何非必要的动作和等待都是无价值的
NVA 浪费
NVA1
第一类浪费:无价值的,但是可以 通过快速的改善动作立即消除
NVA2
第二类浪费:无价值的,并且短期
内无法采取措施消除 PSK-QSC, SL, ’02_Nov
能力需求:100件/H
项目 能力 达成率 奖金 效率
工序1 100件/H 100% 标准产量奖金 个别效率合格
工序2 125件/H 125% 125%奖金 个别效率高
举例:交 通 PSK-QSC, SL, ’02_Nov
工序3 80件/H 80% 0 个别效率低
工序4 100件/H 80% 0 个别效率低
13
13
Cell Promotion 库(III存) – 的從雁浪行费理論看 Cell Operation
库存的浪费有哪些?
1.产生不必要的搬运,堆积,放置,防护处理, 寻找等浪费
当库存增加时,搬运量将增加,需要 增加堆积和放置的场所,需要增加防护 措施,日常管理和领用时需要增加额外 时间等,甚至盘点的时间都要增加,这 些都是浪费。
地下工厂
过量生产的浪费
不良/再作业的浪费
5 %
搬运的浪费
企业每生产一件产品就 在制造一份浪费。伴随企业运 营中各业务环节不被察觉或不
动作 的浪
附加 值
浪费 / 非附 加值
被重视的浪费,日本企业管理
库存的浪费
界将之形象地比喻为“地下工 厂”。
费
等待的浪费 加工其本身的浪费 某国外管理专家:
在我的眼里,中国企业地上铺的都是黄金!
认识浪费
VA:价值
• 在必要的时间,生产必要数量的产品
NVA:无价值
• 任何非必要的动作和等待都是无价值的
NVA 浪费
NVA1
第一类浪费:无价值的,但是可以 通过快速的改善动作立即消除
NVA2
第二类浪费:无价值的,并且短期
内无法采取措施消除 PSK-QSC, SL, ’02_Nov
七大浪费与现场改善培训讲义(ppt 55页)
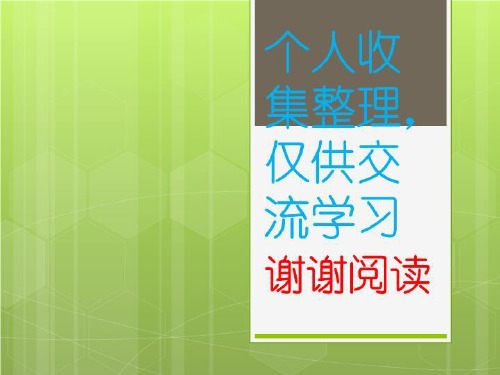
丰田汽车公司对企业增值与非增值活动的界定:
制造过 程
增值 (<5%)
非增值
必要非增值 (约60% )
非必要非增值(浪费) (约35%)
问题:搬运是属于那类活动呢?
15
用增值和非增值来分析企业制造过程
原料生产
运输 W aitin g
运输 T ran sp o rtatio n
存放 g in g
混合
检验 n sp ectio n
包装 P a c k a g i库n g存
S e t-u p
原料 Raw
时间 Tim e
= 有附加值的时间
=无 附 加 值 的 时 间 ( 浪 费 ) ue
成品
16
用增值和非增值来分析企业制造过程
提高传统生产的结果
$
$
时间 me
时间
精益生产后的m结e 果
节约少量的时间
非计划停线时间
物流供应 17%
内部供应 2%
29%
检验操作 1%
55%
生产时间统计过程:2月26日——3月5日 组织生产时间:67h 在线返修 总装工作时间:36.67h 44% 计划停线时间:19.45h 非计划停线时间:1788分钟
停线效率损失:45% 停线次数:134次
供应商质量 12%
七种浪费 过度库存浪费
过量生产浪费 不合理运输浪费 纠正错误浪费 过度加工浪费 多余动作浪费 等待浪费
20
一、过度库存的浪费
定义:各工序之间的库存或由原材料库存超过必需要的量。
库存给企业带来哪些成本?
21
.(.....) 专业提供企管培训资料
过度库存的危害
七大浪费培训课程

§ § § § § § § § § § § § § § § § § § § § § § § § § § §
8/22
物的方面
必要时没有材料 作业用品的浪费使用多 材料取缔不好 有很多设计变更 设计有很多错误 很难看懂设计图 作业不够 不进行材料的检查 作业方法不好 没有做好作业改善 不知道作业方法 作业标准的修正很慢 作业不标准化 动力故障多 机器故障多 机器的修理不到位
29 机器的修理不到位
30 测定器具不够
31 测定器具的状态不好
32 没有准备好工具
33 准备作业做得不好
34 搬运方法没有计划性
35 搬运工具不足
36 讨厌换工程作业
37 没有安排好适合的工作
38 熟练者少
39 作业的训练不充分
40 不清楚工厂的纪律
41 不遵守厂规
42 监督指导不严
43 反复发生同样的事故
② 电话, 会议, 管理等的浪费 在电话的浪费中所有电话并不都是浪费. 重要的是怎么区别有益与浪费,虽然在这么多的浪费的因素中找出本质的 浪费的基准是很难的。扭转这种想法,去定义什么是对我们有益的,没有 利益的就判断为浪费
문제 발생 요인
4/22
2. 什么叫浪费 ?
※ 什么叫附加价值 ?
附加价值
参考资料 第一浪费
测定器具不够 测定器具的状态不好 没有准备好工具 作业准备不足 搬运方法没有计划性 搬运工具不足 反复发生同样的事故 负伤多 在工厂不进行事故发生的报告 没有安全卫生的规定 没有安全装备
3. 浪费的种类
2) 7大浪费 1.对于过度制造的浪费 2.库存的浪费 3.搬运的浪费 4.不良的浪费 5.作业本身的浪费 6.动作的浪费 7.待机的浪费
七大浪费培训教材(1)

二、七种浪费之二:搬运的浪费
在座的各位可能多数会认为搬运是必须 的动作,因为没有搬运,如何做下一个动作? 正因为如此,大多数人默认它的存在,而不 想方设法去消除它。其概念应理解为:不必 要的移动及把东西暂放在一旁[搬运的浪费若 分解开来,又包含放置、堆积、移动、整理 等动作的浪费。]
2.搬运的浪费
等待的浪费 搬运的浪费 不良品的浪费 动作的浪费 加工的浪费 库存的浪费 制造过多过早的浪费
1.等待的浪费
双手均未抓到及摸到东西的时间
材料、作业、搬运、检查之所有等待,以及宽放和监视作业
表现形式:
•自动机器操作中,人员的“闲视”等待 •作业充实度不够的等待 •设备故障、材料不良的等待 •生产安排不当的人员等待 •上下工序间未衍接好造成的工序间的等待
通过修整模具能够使修边更 容易,则可节省人力
5.加工上的浪费
表现形式:
•大家熟悉的月饼过度包装 •日本的电器
5.加工上的浪费
原因:
•思想理念上 •工程顺序设计上不足 •作业内容与工艺总体考虑 上不足 •模夹治具不良 •标准化不彻底
对策:
•工程设计修正
•作业内容的修正
•治具改善及自动化
•标准作业的贯彻
对策:
•自动化、标准作业 •防误装置
•一个流的生产方式 •品保制度的确立及运行 •定期的设备、模治具保养 •持续开展“5S活动”
注意:
•能回收重做的不良 •能修理的不良 •误判的不良
四、七种浪费之四:动作的浪费
要达到同样作业的目的,会有不同的动作,哪 些动作是不必要的呢?是不是要拿上、拿下如此频 繁?有没有必要有反转的动作、步行的动作、弯腰 的动作、对准的动作、直角转弯的动作等?若设计 得好,有很多动作皆可被省掉!在管理理论中,专 门有一种“动作研究”,但实施起来比较复杂,我 们完全可以用上述的基本思想,反思一下日常工作 中有哪些动作不合理?如何改进?
现场七大浪费培训教材-如何控制库存(PPT 26页)

具體措施一
正确确定库存物料: 对一般性的企业来说,其所经营的产品少则几十种,多则成千上万种,并且 在大多数的情况下,不需要也不可能对所有的产品都准备库存。所以企业的 首要任务就是正确确定库存和非库存的物料。 一般来说,企业的库存管理模式可以分为拉动式(反应式)和推动式(计划 式),前者是基于需求(生产或客户的订单),仅在需要时才生产或采购的 库存管理模式, JIT 和看板管理系统就是属于这种方式。这种模式所适用的 产品通常有以下的特点: 1 〃产品大多数为客户订制,或者说产品的标准化程度较低; 2 〃产品的单价较高,这种产品如果备大量的库存对企业的资金流动会造成 巨大的压力; 3 〃产品生产或采购的前置时间可以满足客户订单的交货要求,这种情况下 企业通常没有必要准备库存; 4 〃产品的流动性较慢;
待
續
占用厂房空间,造成多余的工场、仓库
建设投资的浪费
当库存增加时,就需要额外增加放置场所。 另外,因库存所造成的无形损失,绝不亚于上述 的有形损失,精益生产方式认为库存会隐藏问题点, 而“问题”在精益生产方式中被认为是宝藏,问题 如果能不断地被发现解决,则利益便会不断地产生。 库存隐藏问题点,造成下列后果:
由于库存量的存在,设备能力不帄衡时也看不出(库存越 多,越不容易看出来)。人员是否过剩,也无法了解。由于有 较多的库存,供应部门需要增加人员,制造一线需要更多的人 员来生产产品用于补充库存,需要增添设备来保证生产库存所 需要的设备能力,从而形成新一轮的浪费
如何控制庫存
库存按其存在形态又可分为原材料、在制品包括半 成品、产成品、维修备件、在途库存、寄售库存。不同 形态下的库存其管理方式和目标是不完全一样的。例如 原材料库存的管理强调的是生产计划的准确、原材料计 划的及时、供应商交货的快速和稳定,降低原材料库存 也应相应从这些方面来入手。而在制品或者是半成品的 库存量控制则需要通过制定合理的生产线工作节拍、使 物料在生产线上连续而均匀地流动、减少在制品的等待 时间、合理布置生产线的位置以物料在生产过程中的转 移距离等措施来实现.
《七大浪费分析与改善》培训教材共80页

Thank you
Hale Waihona Puke 45、法律的制定是为了保证每一个人 自由发 挥自己 的才能 ,而不 是为了 束缚他 的才能 。—— 罗伯斯 庇尔
6、最大的骄傲于最大的自卑都表示心灵的最软弱无力。——斯宾诺莎 7、自知之明是最难得的知识。——西班牙 8、勇气通往天堂,怯懦通往地狱。——塞内加 9、有时候读书是一种巧妙地避开思考的方法。——赫尔普斯 10、阅读一切好书如同和过去最杰出的人谈话。——笛卡儿
《七大浪费分析与改善》培 训教材
41、实际上,我们想要的不是针对犯 罪的法 律,而 是针对 疯狂的 法律。 ——马 克·吐温 42、法律的力量应当跟随着公民,就 像影子 跟随着 身体一 样。— —贝卡 利亚 43、法律和制度必须跟上人类思想进 步。— —杰弗 逊 44、人类受制于法律,法律受制于情 理。— —托·富 勒
Hale Waihona Puke 45、法律的制定是为了保证每一个人 自由发 挥自己 的才能 ,而不 是为了 束缚他 的才能 。—— 罗伯斯 庇尔
6、最大的骄傲于最大的自卑都表示心灵的最软弱无力。——斯宾诺莎 7、自知之明是最难得的知识。——西班牙 8、勇气通往天堂,怯懦通往地狱。——塞内加 9、有时候读书是一种巧妙地避开思考的方法。——赫尔普斯 10、阅读一切好书如同和过去最杰出的人谈话。——笛卡儿
《七大浪费分析与改善》培 训教材
41、实际上,我们想要的不是针对犯 罪的法 律,而 是针对 疯狂的 法律。 ——马 克·吐温 42、法律的力量应当跟随着公民,就 像影子 跟随着 身体一 样。— —贝卡 利亚 43、法律和制度必须跟上人类思想进 步。— —杰弗 逊 44、人类受制于法律,法律受制于情 理。— —托·富 勒
七大浪费培训资料讲解
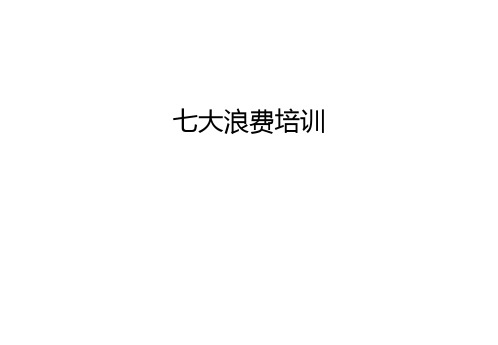
1)表现形式: •人等机器 •机器等人 •人等人 •有人过于忙乱 •非计划的停机
浪费的种类
定义:人员以及设备等资源的空闲 2)产生的原因: •生产线能力不平衡 •生产换型时间长 •人员和设备的效率低 •设备维护不到位 •物料供应不及时
14
三
浪费的种类
3)等待的浪费的改善着眼点:
• 进行时间测定,要将操作等待时间明确化 (要明显看见的操作等待很少) • 1人作业的场合,应缩短瓶颈工序的时间和
16
三
3)动作的浪费的改善着眼点:
浪费的种类
动作经济的八个基本原则
☆ 双手并用——两手同时使用 ☆ 伸手可及——动作距离最短 ☆ 容易取放——动作轻松、容易 ☆ 利用夹具——动作单元力最少 ☆ 重心不变——不做弯腰动作 ☆ 方向不变——不转身进行操作 ☆ 位置不变——不移动作业 ☆ 借用重力——使物体从高处自
•设备和物料距离过大引起的走动
•人员及设备的效率低
•人或机器“特别忙”
•没有考虑人机工序学
12种动作上的浪费
•工作方法不统一
1.两手空闲
7.转身角度太大
2.单手空闲
8.动作之间没有配合好
3.作业动作停止
9.不了解作业技巧
4.作业动作太大
10.伸背动作
5.拿的动作交替
11.弯腰动作
6.步行
12.重复动作
6
三
浪费的种类
等待的浪费
库存的浪费
动作的浪费
次 返品 工、 的返浪工费浪费
搬运的浪费
加加工工本的身浪的费浪费
制生产造过过剩剩的的浪浪费费
7
三
浪费的种类
1、生产过剩的浪费
定义:生产多于需求或生产快于需求 (最大的浪费)
浪费的种类
定义:人员以及设备等资源的空闲 2)产生的原因: •生产线能力不平衡 •生产换型时间长 •人员和设备的效率低 •设备维护不到位 •物料供应不及时
14
三
浪费的种类
3)等待的浪费的改善着眼点:
• 进行时间测定,要将操作等待时间明确化 (要明显看见的操作等待很少) • 1人作业的场合,应缩短瓶颈工序的时间和
16
三
3)动作的浪费的改善着眼点:
浪费的种类
动作经济的八个基本原则
☆ 双手并用——两手同时使用 ☆ 伸手可及——动作距离最短 ☆ 容易取放——动作轻松、容易 ☆ 利用夹具——动作单元力最少 ☆ 重心不变——不做弯腰动作 ☆ 方向不变——不转身进行操作 ☆ 位置不变——不移动作业 ☆ 借用重力——使物体从高处自
•设备和物料距离过大引起的走动
•人员及设备的效率低
•人或机器“特别忙”
•没有考虑人机工序学
12种动作上的浪费
•工作方法不统一
1.两手空闲
7.转身角度太大
2.单手空闲
8.动作之间没有配合好
3.作业动作停止
9.不了解作业技巧
4.作业动作太大
10.伸背动作
5.拿的动作交替
11.弯腰动作
6.步行
12.重复动作
6
三
浪费的种类
等待的浪费
库存的浪费
动作的浪费
次 返品 工、 的返浪工费浪费
搬运的浪费
加加工工本的身浪的费浪费
制生产造过过剩剩的的浪浪费费
7
三
浪费的种类
1、生产过剩的浪费
定义:生产多于需求或生产快于需求 (最大的浪费)