七大浪费培训
7大浪费培训
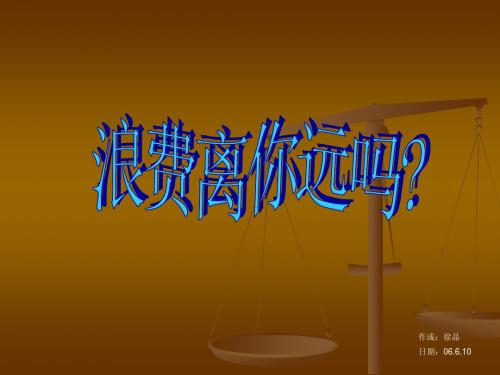
业务内容检讨
-----现在的业务都必要吗? -----现在的业务都必要吗? -----现在是按要求做的吗? -----现在是按要求做的吗? -----现在这样做有价值吗? -----现在这样做有价值吗? -----不做可以吗? -----不做可以吗?
作成:徐晶 日期:06.6.10
本课程目的
了解什么是浪费及常见的浪费现象
解析你的工作
消减工作中的浪费 提升效率/ 提升效率/效果
认识浪费
过程中的每一步骤 都可能存在浪费
输入
过程
输出
有附加值作业 无附加值作业—浪费
1.客户不会对此作业支付任何报酬, 甚至对其存在产生抱怨 2.作业内容重复
1.客户情愿为其支付报酬, 2.该作业能使产品或服务有所变化 3.该作业和任何作业不重复
业务流程检讨
----流程明确吗? ----流程明确吗? ----可简化吗? ----可简化吗? ----作业者真的清楚吗? ----作业者真的清楚吗? ----按流程做会有什么价值? ----按流程做会有什么价值?
个人业务检讨
----业务内容清楚吗? ----业务内容清楚吗? ----业务安排有计划吗? ----业务安排有计划吗?
运输和传送
指移动产品的次数或距离超过作业需要的次数或距离,如:
★同一原料或半成品存在两个以上存贮地点 ★将原料或半成品移动至不适当的存贮位置
等待
等待不会产生任何附加值,如:
★等待批准 ★等待出荷 ★等待原材料 ★等待设备维修 ★由生产线平衡效率低造成的某些工位的等待
移动
指作业人员在完成作业动作时额外的移动,如:
精益生产七大浪费基础知识培训

精益生产七大浪费基础知识培训1. 引言精益生产是一种以降低浪费为核心的管理方法,通过优化生产流程,提高生产效率和质量。
七大浪费是精益生产的基础概念,每个环节中的所有浪费都需要被尽可能地减少或消除。
本培训旨在帮助员工了解精益生产的七大浪费和如何识别并消除这些浪费。
2. 七大浪费及其定义以下是精益生产的七大浪费及其定义:2.1 过产量 (Overproduction)过产量是指在没有顾客需要的情况下生产过多的产品或提供过多的服务。
这会造成库存的增加和材料的浪费。
2.2 在等待 (Waiting)在等待是指在生产过程中,由于某些环节的停顿或延迟而导致的浪费。
这可能是由于设备故障、缺乏原材料或工人等原因引起的。
2.3 运输 (Transportation)运输是指将产品或材料从一个地方转移到另一个地方的过程中出现的浪费。
过多的运输可能增加产品的损坏风险并导致时间和资源的浪费。
2.4 不必要的库存 (Inventory)不必要的库存是指超过正常需求量而存放的产品或材料。
这会造成资金的浪费,并可能导致产品质量下降和过期等问题。
2.5 不必要的运动 (Motion)不必要的运动是指工人在生产过程中进行不必要的移动和动作所造成的浪费。
这可能是由于工作场所不合理的布局或操作不合理引起的。
2.6 不良品 (Defects)不良品是指在生产过程中产生的不符合质量标准的产品。
这会造成时间、人力和材料的浪费,并可能影响公司的声誉和客户满意度。
2.7 过度处理 (Overprocessing)过度处理是指在生产过程中为产品提供超出顾客要求的功能或品质。
这会导致资源的浪费和过程的低效。
3. 如何减少或消除七大浪费减少或消除七大浪费是精益生产的核心目标之一。
以下是一些常见的方法和技巧:3.1 价值流图 (Value Stream Mapping)价值流图是一种用于分析和改进价值流程的工具。
通过绘制当前状态和未来状态的价值流图,可以识别出浪费和瓶颈,并采取相应的措施进行改进。
七大浪费培训感想范文
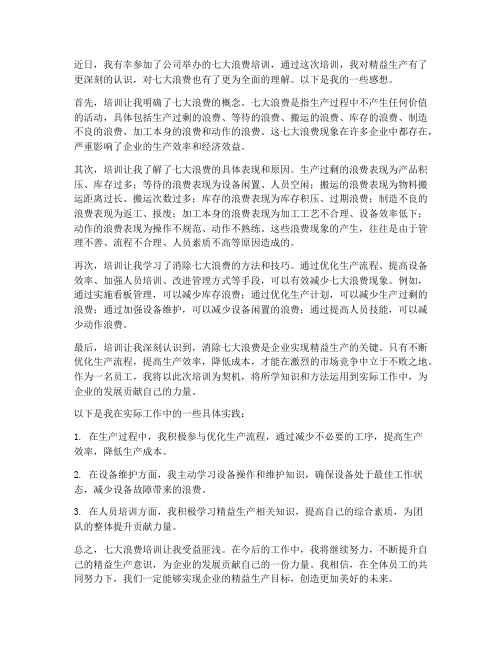
近日,我有幸参加了公司举办的七大浪费培训,通过这次培训,我对精益生产有了更深刻的认识,对七大浪费也有了更为全面的理解。
以下是我的一些感想。
首先,培训让我明确了七大浪费的概念。
七大浪费是指生产过程中不产生任何价值的活动,具体包括生产过剩的浪费、等待的浪费、搬运的浪费、库存的浪费、制造不良的浪费、加工本身的浪费和动作的浪费。
这七大浪费现象在许多企业中都存在,严重影响了企业的生产效率和经济效益。
其次,培训让我了解了七大浪费的具体表现和原因。
生产过剩的浪费表现为产品积压、库存过多;等待的浪费表现为设备闲置、人员空闲;搬运的浪费表现为物料搬运距离过长、搬运次数过多;库存的浪费表现为库存积压、过期浪费;制造不良的浪费表现为返工、报废;加工本身的浪费表现为加工工艺不合理、设备效率低下;动作的浪费表现为操作不规范、动作不熟练。
这些浪费现象的产生,往往是由于管理不善、流程不合理、人员素质不高等原因造成的。
再次,培训让我学习了消除七大浪费的方法和技巧。
通过优化生产流程、提高设备效率、加强人员培训、改进管理方式等手段,可以有效减少七大浪费现象。
例如,通过实施看板管理,可以减少库存浪费;通过优化生产计划,可以减少生产过剩的浪费;通过加强设备维护,可以减少设备闲置的浪费;通过提高人员技能,可以减少动作浪费。
最后,培训让我深刻认识到,消除七大浪费是企业实现精益生产的关键。
只有不断优化生产流程,提高生产效率,降低成本,才能在激烈的市场竞争中立于不败之地。
作为一名员工,我将以此次培训为契机,将所学知识和方法运用到实际工作中,为企业的发展贡献自己的力量。
以下是我在实际工作中的一些具体实践:1. 在生产过程中,我积极参与优化生产流程,通过减少不必要的工序,提高生产效率,降低生产成本。
2. 在设备维护方面,我主动学习设备操作和维护知识,确保设备处于最佳工作状态,减少设备故障带来的浪费。
3. 在人员培训方面,我积极学习精益生产相关知识,提高自己的综合素质,为团队的整体提升贡献力量。
7大浪费培训

每一种浪费对个人、公司的不良影响
3. 动作的浪费
对时间和体力上不必要的消耗
每一种浪费对个人、公司的不良影响
4. 搬运的浪费
一种不产生附加价值的动作,搬运的损失分为放置、堆积、 移动、整理等动作浪费。
1
5 3 2 4
7
6
怎样排产才能减少搬运
每一种浪费对个人、公司的不良影响
• • • 库存的浪费 过量生产造成的过量储存需要额外的成本来 运作维 持 过量储存也会掩盖住操作中的一些问题…
7大浪费
7大浪费
主讲:张万军
7大浪费内容
• 浪费的定义 • 7大浪费的种类 • 每一种浪费对个人、公司的不良影响
浪费的定义
在生产过程中 没有增加 产品附加价值的活动 就是浪费。
7大浪费种类
等 待 的 浪 多 浪 或 过 早 的 浪 费 费 浪 的 废 报 费 费 费 造 过 的 浪 费 费 、 • • 制 • 库 存 运 的 浪 浪 的 的 • 搬 • 动 作 工 修 理 • 加 • 不 良 -
生产计划不良 设定时 间过程 报废 机器停机 产能不平衡
不可靠的供货商
1)配片不及时是否库存有关系
2)库存的五金保管是否构成浪费
每一种浪费对个人、公司的不良影响
6. 制造过多或过早的浪费
超出下道工序所需求的数量及时间
前端部门 过早生产 台面上裁片饱满
做 50PCS
做 20PCS
1)生产计划与制造过多有否联系? 2)流水线的工序分配是否接近均衡?
每一种浪费对个人、公司的不良影响
7. 等待的浪费
缝纫机多次出故障 排产不均衡时 手工
需要 导致员工作业时空手等待 110秒 需要59 车位 秒
七大浪费-培训教材

七大浪费
1、过量生产的浪费 2、搬运的浪费 3、动作的浪费 4、等待的浪费
5、过程的浪费
6、库存的浪费
7、残次品的浪费
XXXX有限责任公司
32
七大浪费 之 过程的浪费
因技术(设计、加工)不足造成加工上的浪费 --原本不必要的工程或作业被当成必要; 又叫加工的浪费
多余的加工时间和辅助设备 用于加工多余的材料 过分精确的加工 过于昂贵设备 加工时去除多余材料
过剩设备 大LOT 生产 又大又快的机器, 接连着制造出的构造 追求高的设备稼动率 不能换线
20
七大浪费
1、过量生产的浪费
2、搬运的浪费
3、动作的浪费库存的浪费
7、残次品的浪费
XXXX有限责任公司
21
七大浪费之 搬运的浪费
物品的放置、堆积、移动、活性度的恶化等 叫做搬运的浪费
XXXX有限责任公司
23
七大浪费 之 搬运的浪费
➢说明
不必要的搬运,物品的移动 保管等,长距离与搬运的 流程,激化恶化性问题
搬运的浪费
➢内容
空间的过多使用, 生产性低下, 搬运工数的增减 搬运设备的增设 磕痕等外观不良的发生。
➢对策
U型设备布置 一个流生产流程 多能熟练工 立式作业
XXXX有限责任公司
•原材料 •在制品 •制成品 •供应品 •备件
生产问题
库 存
库存是万恶的根源
XXXX有限责任公司
36
七大浪费 之 库存的浪费
场所的浪费
•工厂越来越狭窄. •真正重要的物品没地方放
保管用具浪费
•货架,柜子过多使用 •卡板,搬运用具过多使用
异物/混入浪费
•相似的混用 •因异物进入要洗涤
精益生产认识之七大浪费培训
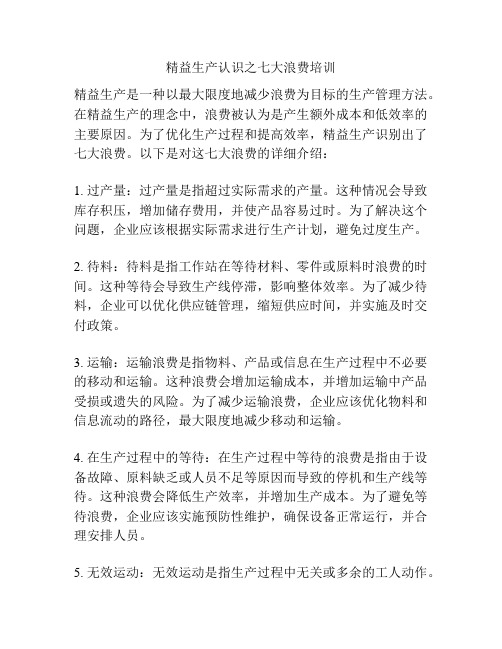
精益生产认识之七大浪费培训精益生产是一种以最大限度地减少浪费为目标的生产管理方法。
在精益生产的理念中,浪费被认为是产生额外成本和低效率的主要原因。
为了优化生产过程和提高效率,精益生产识别出了七大浪费。
以下是对这七大浪费的详细介绍:1. 过产量:过产量是指超过实际需求的产量。
这种情况会导致库存积压,增加储存费用,并使产品容易过时。
为了解决这个问题,企业应该根据实际需求进行生产计划,避免过度生产。
2. 待料:待料是指工作站在等待材料、零件或原料时浪费的时间。
这种等待会导致生产线停滞,影响整体效率。
为了减少待料,企业可以优化供应链管理,缩短供应时间,并实施及时交付政策。
3. 运输:运输浪费是指物料、产品或信息在生产过程中不必要的移动和运输。
这种浪费会增加运输成本,并增加运输中产品受损或遗失的风险。
为了减少运输浪费,企业应该优化物料和信息流动的路径,最大限度地减少移动和运输。
4. 在生产过程中的等待:在生产过程中等待的浪费是指由于设备故障、原料缺乏或人员不足等原因而导致的停机和生产线等待。
这种浪费会降低生产效率,并增加生产成本。
为了避免等待浪费,企业应该实施预防性维护,确保设备正常运行,并合理安排人员。
5. 无效运动:无效运动是指生产过程中无关或多余的工人动作。
这种浪费会造成不必要的体力消耗和生产时间延长。
为了减少无效运动浪费,企业应该优化工作站布局和工作流程,确保工人只进行必要的动作。
6. 过度加工:过度加工是指对产品进行超出要求的处理或处理步骤。
这种浪费会增加生产成本,同时也会延长生产周期。
为了避免过度加工浪费,企业应该对产品和工艺进行分析,找出不必要的加工步骤,并进行精简。
7. 库存:库存浪费是指过多或无用的库存。
这种浪费会增加资金占用和储存成本,并增加产品过时或损坏的风险。
为了减少库存浪费,企业应该实施准时生产和准时交付政策,并优化库存管理。
通过认识和理解这七大浪费,企业可以发现潜在的问题并采取相应的措施来减少浪费,提高生产效率和质量。
车间班组长7大浪费培训教材

七大浪费
5.库存的浪费 过多的库存会隐藏的问题点:
没有管理的紧张感,阻碍改善的活 性化 设备能力及人员需求的误判 对场地需求的判断错误 产品品质变差的可能性 容易出现呆滞物料 “怕出问题”的心态
5.库存的浪费
原因:
•视库存为当然 •设备配置不当或设备能力差 •大批量生产,重视稼动 •物流混乱,呆滞物品未及时处 理 •提早生产 •无计划生产
作业标准
7.做出不良的浪费
制造不良品所损失的浪费,越做损失越大
材料不良、加工不良、检查、市场不良、整修工件等
表现形式:
•因作业不熟练所造成的不良 •因不良而修整时所造成的浪费 •因不良造成人员及工程增多的浪费 •材料费增加
自动化、标准作业
防误装置
在工程内做出品质保 证
“三不政策”
一个流的生产方式
对策:
•库存意识的改革 •U型设备配置 •均衡化生产 •生产流程调整顺畅 •看板管理的贯彻 •快速换线换模 •生产计划安排考虑库存
消化
注意:
•库存是万恶之源 •管理点数削减降低安全库存 •消除生产风险降低安全库存
七大浪费
表现形式:
工作时的换手作业 未倒角之产品造成不易装配的浪费 小零件组合时,握持压住的浪费 动作顺序不当造成动作重复的浪费 寻找的浪费
•搬运距离很远的地方,小批量的运输 •主副线中的搬运 •出入库次数多的搬运 •破损、刮痕的发生
3.搬运的浪费
原因:
•生产线配置不当 •未均衡化生产 •坐姿作业 •设立了固定的半成品放置区 •生产计划安排不当
对策:
•U型设备配置 •一个流生产方式 •站立作业 •避免重新堆积、重新包装
注意:
七大浪费与现场改善培训讲义

七大浪费与现场改善培训讲义1. 引言本讲义旨在帮助企业了解并纠正常见的生产和运营中的七大浪费,以提高效率和降低成本。
通过现场改善培训,企业可以识别并消除浪费,实现生产流程的优化和持续改进。
2. 七大浪费概述2.1 传统的七大浪费概念传统的七大浪费包括:1.运输浪费:指产品或物料在生产过程中被多次搬运、移动或运输所造成的浪费。
2.库存浪费:指过多的存货或未使用的存货所造成的资金、空间和资源的浪费。
3.过程浪费:指生产过程中不必要的操作、等待或手续所导致的浪费。
4.过度生产:指生产过量或过早生产所造成的浪费。
5.等待浪费:指等待人员、物料或设备而导致的停工及时间的浪费。
6.过加工:指超过产品要求所必需的处理步骤或加工的浪费。
7.瑕疵品:指产品或物料的非正常损坏或不合格品所导致的浪费。
2.2 现场改善培训的目标现场改善培训通过对七大浪费的认知和分析,旨在帮助企业实施持续改进措施,提高效率和质量,并降低成本。
通过培训,员工将能够识别和消除浪费,提升团队合作和创新思维,从而促进企业的可持续发展。
3. 七大浪费详解3.1 运输浪费运输浪费是指产品或物料在生产过程中由于频繁搬运、移动或运输而导致的浪费。
它可能导致时间、能源和人力资源的浪费。
减少运输浪费的方法包括优化物料布局、减少搬运次数,并提高物流管理的效率。
3.2 库存浪费库存浪费是指过多的存货或未使用的存货导致的资金、空间和资源的浪费。
库存过剩可能导致资金的占用和财务成本的增加。
减少库存浪费的方法包括实施精益生产管理(Lean Production),采用精确物料需求计划(MRP)等。
3.3 过程浪费过程浪费是指生产过程中不必要的操作、等待或手续导致的浪费。
它可能包括重复工作、走动等不必要的动作。
通过精简工作流程、标准化操作和流程优化,可以减少过程浪费,并提高工作效率。
3.4 过度生产过度生产是指生产过量或过早生产导致的浪费。
它可能导致多余的库存、仓储和运输成本的增加。
- 1、下载文档前请自行甄别文档内容的完整性,平台不提供额外的编辑、内容补充、找答案等附加服务。
- 2、"仅部分预览"的文档,不可在线预览部分如存在完整性等问题,可反馈申请退款(可完整预览的文档不适用该条件!)。
- 3、如文档侵犯您的权益,请联系客服反馈,我们会尽快为您处理(人工客服工作时间:9:00-18:30)。
1、生产过剩的浪费
1)表现形式: ・过多的设备、过多的人员 ・库存堆积、在制品增加 ・产品积压造成不合格品发生 ・资金回转率低 ・额外的仓库 、额外的人员需求 产生新的浪费: ・材料、零部件、能源的过早消耗 ・托盘、物料箱的占用 ・铲车、物料车的占用
2)生产过剩的原因: ・ 对开工率的错误认识 ・ 停线是不可以的错误想法 ・ 可以对付设备故障、不合格品、缺勤等问题 ・ 对付生产负荷的不均衡 ・ 生产能力不稳定 ・ 生产计划不协调,缺乏交流(内部、外部)
石子(问题点)
三
3)库存的浪费的改善着眼点:
浪费的种类
• 首先要明确各工序生产能力 • 从开始到最后,要考虑全体的流程
• 不要追求部分的效率
• 设备能力、大小要和生产线构想合在一起考虑 • 缩短准备时间
• 要把生产线外的在制品进行定量并要有管理规定
11
三
浪费的种类
定义:对物料的任何移动 2)产生的原因: •生产计划没有均衡化
19
三
浪费的种类
定义:对产品进行检查,返工等补救措施 2)产生的原因: •生产能力不稳定 •过度依靠人力来发现错误 •员工缺乏培训
7、返工的浪费
1)表现形式:
•额外的时间和人工进行检查,返 工等工作 •由此而引起的无法准时交货
•企业的运作是补救式的,而非预 防式的(救火队方式的运作)
3)改善着眼点: • 产品制造的质量需通过工序本身 来自我保证 • 用5个为什么来彻底追查不合格 品发生的原因 • 通过纵向生产、用缩短工期来降 低不合格品
20
四
消除浪费的步骤
第一步: 了解什么是浪费
第二步: 识别工序中哪里存在浪费
第四步: 实施持续改进措施,
第三步:
使用合适的工具来消除
已识别的特定浪费
21
重复实施上述步骤
谢谢!
22
七大浪费培训
1
一
消除浪费的目的 浪费的定义 浪费的种类 消除浪费的步骤
目录
二
三
四
2
一
消除浪费的目的
1、 实 施 成 本 递 减 , 增 加 利 润
① ②
售价=成本+利润 ……需求>供给 …… 成本主义 利润=售价-成本 ……需求<供给 …… 成本递减
利润 成本
售价 成本
利润 售价
成本主义
成本递减
作业员进行其他多余的操作,等待时间明显化后再进 行改善
9
三
浪费的种类
定义:任何超过客户或者后工序作业需求的供应
2、库存的浪费
1)表现形式: •需要额外的进货区域 •停滞不前的物料流动 •发现问题后需要进行大量返工 •需要额外资源进行物料搬运(人员, 场地,货架,车辆等等) •对客户要求的变化不能及时反应
2)产生的原因: •工艺更改和工序更改没有协调 •随意引进不必要的先进技术 •由不正确的人来作决定 •没有平衡各个工艺的要求 •没有正确了解客户的要求
6、加工本身的浪费
1)表现形式:
•没有清晰的产品/技术标准
•无穷无尽的精益求精 •需要多余的作业时间和辅助设备
3)改善着眼点: • 通过工序确认来分出真正必要的 工作和浪费,由此将浪费显现化以及 对策(对于新产品特别重要) • 加工条件的最适合化? • 工序安排是否合适?
短缩瓶颈工序的时间和增加生产线外的作业
• 操作设备台数的增加
15
三
浪费的种类
定义:对产品不产生价值的任何人员和设备的动作 2)产生的原因: •生产场地和设备规划不合理
5、动作的浪费
1)表现形式:
•人找工具 •大量的弯腰,抬头和取物
•工作场地没有组织
•人员及设备的效率低 •没有考虑人机工序学
•设备和物料距离过大引起的走动
13
三
浪费的种类
定义:人员以及设备等资源的空闲 2)产生的原因:
4、等待的浪费
1)表现形式: •人等机器
•生产线能力不平衡 •生产换型时间长 •人员和设备的效率低
•机器等人
•人等人 •有人过于忙乱 •非计划的停机
•设备维护不到位
•物料供应不及时
14
三
3)等待的浪费的改善着眼点:
浪费的种类
• 进行时间测定,要将操作等待时间明确化 (要明显看见的操作等待很少) • 1人作业的场合,应缩短瓶颈工序的时间和 增加生产线外的辅助作业 • 2人以上作业的场合,应纠正作业的顺序,
最适合作业区域
适合作业区域
手臂运动范围
17
三
浪费的种类
三角形原理
作业点
作业过程中,作业点、
手持工具 工具和零部件三个位置构 成三角形关系。此三角形
小零件
越小,作业效率越高。
18
三
浪费的种类
定义:亦称为“过分加工的浪费”,一是指多余的加 工;另一方面是指超过顾客要求以上的精密加工,造 成资源的浪费
3、搬运的浪费
1)表现形式:
•需要额外的运输工具 •需要额外的储存场所
•工作场地缺乏组织
•场地规划不合理 •大量的库存和堆场
•需要额外的生产场地
•大量的盘点工作 •产品在搬运中损坏
12
三
浪费的种类
3)改善的着眼点: • 通过生产布局的修整,消除搬运,缩短距离 • 通过逐步流水生产线化来消除物品暂放的浪费 • 通过流水生产线来消除工决于制造的方法 成本的构成
其他 能源 劳务费 材料费 部件购 入费 各公司相同费用 浪费——因各公司制造方法不同 而产生差异的费用
各公司的成本价格没有很大差异, 因制造方法的差异(浪费)
产生的成本不同
4
一
2、 可 以 简 化 作 业, 使 工 作 更 轻 松 且 安 全 地 完 成
•人或机器“特别忙”
12种动作上的浪费 1.两手空闲 7.转身角度太大
•工作方法不统一
2.单手空闲
3.作业动作停止 4.作业动作太大
8.动作之间没有配合好
9.不了解作业技巧 10.伸背动作
5.拿的动作交替
6.步行
11.弯腰动作
12.重复动作 16
三
3)动作的浪费的改善着眼点:
浪费的种类
动作经济的八个基本原则 ☆ ☆ ☆ ☆ ☆ ☆ ☆ ☆ 双手并用——两手同时使用 伸手可及——动作距离最短 容易取放——动作轻松、容易 利用夹具——动作单元力最少 重心不变——不做弯腰动作 方向不变——不转身进行操作 位置不变——不移动作业 借用重力——使物体从高处自 动落下
消除浪费的目的
危险呀! 返修(手修理)作业增加・・・
机械故障
今天又要加班哦・・・
彻底排除所有的浪费 使作业更简化、轻松、安全 物美价廉的产品
5
二
浪费的定义
浪费是指不增加附加价值,使成本增加的一系列活动。
对于JIT来讲,凡是超出增加产品价值所绝对必须的最
少量的物料、设备、人力、场地和时间的部分都是浪费。
水量(库存)
不合格品 发生 设备故障 部品错漏 装 计划未完
2)产生的原因:
•生产能力不稳定
•不必要的停机 •生产换型时间长 •生产计划不协调 •市场调查不准确 •错误的想法: 因为有库存和在制品,
生产计划就好安排了„
这种库存品一定会卖掉,所以没关系! 因为有地方,所以即使有库存也没关系!
10
问题点
1、不增加价值的活 动,是浪费
这里有 两层含义
2、尽管是增加价 值的活动﹐但所用 的资源超过了“绝 对最少”的界限﹐ 也是浪费
6
三
浪费的种类
库存的浪费
等待的浪费
动作的浪费 次品、返工浪费 返工的浪费
加工本身的浪费 加工的浪费 搬运的浪费
生产过剩的浪费 制造过剩的浪费
7
三
浪费的种类
定义:生产多于需求或生产快于需求 (最大的浪费)
生产过剩的后果:
难以判断什么时间什么地 方会发生问题
8
三
3)生产过剩的改善着眼点:
浪费的种类
• 首先要明确各工序生产能力,进行平衡作业 • 从开始到结束的生产连接以及整个流程的考虑 • 不要追求部分效率 • 设备能力、运行方法要和生产线的构想合在一起考虑
• 有操作等待时间的时候,为了明确此种情况,首先不要让