线性尺寸链公差分析
尺寸链公差叠加分析

尺寸链公差叠加分析尺寸链公差叠加分析是在产品设计和制造过程中用于评估零部件尺寸公差叠加对整个产品尺寸的影响的一种方法。
通过尺寸链公差叠加分析,可以确定产品是否能够满足设计要求,并且能够预测零部件公差的贡献程度,从而指导制定合理的公差分配和调整。
尺寸链公差叠加分析是基于统计原理进行的,它假设零部件的公差服从正态分布。
在这种假设下,产品尺寸的公差可通过公差叠加计算得到。
公差叠加是指将零部件的公差传递到产品尺寸上,通过逐步累加的方式计算得到最终产品尺寸的公差。
1.确定产品的关键尺寸链:尺寸链是指产品上相关的零部件尺寸所构成的一个路径。
关键尺寸链是指对产品功能和性能影响最大的尺寸链。
2.确定零部件公差:通过对制造工艺和零部件的功能要求进行分析,确定零部件的公差范围。
3.进行公差叠加计算:利用数学模型和统计方法,将零部件公差逐步累加到产品尺寸上,得到产品尺寸的公差。
4.进行公差分析:根据产品的设计要求和公差要求,对产品尺寸的公差进行评估和分析,确定产品是否能够满足设计要求。
5.进行公差调整:根据公差分析的结果,对零部件的公差进行合理的调整,以满足产品的设计要求。
尺寸链公差叠加分析对产品设计和制造具有重要的意义。
它可以帮助设计人员选择合适的零部件公差,减小尺寸公差对产品性能和功能的影响。
同时,通过公差叠加分析,可以预测产品尺寸的变化范围,提前做好产品尺寸的控制和调整,从而减少制造成本。
尺寸链公差叠加分析有着广泛的应用。
在汽车制造、航空航天、机械制造等行业,尺寸链公差叠加分析被广泛应用于产品设计、制造和质量控制过程中。
通过合理的公差分配和调整,可以使产品达到更高的质量要求,提高产品的性能和可靠性。
总之,尺寸链公差叠加分析是一种对产品尺寸公差进行评估和分析的方法。
通过尺寸链公差叠加分析,可以预测零部件公差对产品尺寸的影响,指导合理的公差分配和调整,从而确保产品能够满足设计要求。
尺寸链及公差叠加分析讲解学习

尺寸链及公差叠加分析讲解学习尺寸链分析是指通过将不同零部件的尺寸相互关联,确定产品总尺寸的方法。
在设计产品时,往往需要包含多个零部件,这些零部件之间存在着一定的尺寸关系。
尺寸链分析可以帮助我们确定这些尺寸关系,以确保各个零部件能够正确地组装在一起,从而形成合适的总尺寸。
在尺寸链分析中,我们会将所有相关零部件的尺寸进行统一,并将它们按照设计要求进行组装。
通过对各个零部件之间的尺寸关系进行分析和计算,我们可以确定产品总尺寸的合理范围。
这样,在制造过程中,只要各个零部件的尺寸控制在合理的公差范围内,整个产品就能够达到设计要求。
公差叠加分析是指在尺寸链分析的基础上,进一步考虑产品制造和测量过程中的误差,将零部件的公差叠加到总尺寸上。
在产品制造和测量过程中,由于各种原因,零部件的尺寸往往会存在一定的误差。
这些误差可能来自于材料的不均匀性、制造设备的精度、操作人员的技术水平等。
为了确保产品能够满足设计要求,我们需要考虑这些误差对产品总尺寸的影响。
公差叠加分析可以帮助我们将各个零部件的公差叠加到产品总尺寸上,从而确定产品在制造和测量过程中所能容许的最大误差范围。
这样,我们在制造过程中就可以合理地控制零部件的尺寸,以确保产品能够达到设计要求。
尺寸链及公差叠加分析的学习对于产品设计和制造工程师来说是非常重要的。
它能够帮助我们更好地理解和把握产品尺寸的关系,从而设计出更优秀的产品。
同时,它也能够帮助我们在产品制造过程中合理地控制尺寸,从而提高产品的一致性和可重复性。
通过尺寸链及公差叠加分析,我们可以清楚地了解各个零部件之间的尺寸关系,从而更好地设计和优化产品。
我们可以通过调整零部件的尺寸关系来达到产品设计要求,避免因为尺寸不匹配而导致产品组装困难或功能失效的问题。
此外,公差叠加分析还可以帮助我们确定产品在制造和测量过程中所能容许的误差范围,从而提高产品的质量和性能。
在学习尺寸链及公差叠加分析时,我们需要深入了解产品设计和制造的相关知识,包括材料的性质和工艺、制造设备的精度和稳定性,以及测量技术和方法等。
公差分析和尺寸链计算

基准设计基准(在零件图上用以确定其它点、线、面位置的基准)工艺基准定位基准(在加工中用作定位的基准)测量基准(零件测量时所采用的基准,称为测量基准)装配基准(装配时用以确定零件在机器中位置的基准)基准分类和作用形位公差形位公差形状公差(单一要素,无基准)形状或位置公差(单一或关联要素,有或无基准)位置公差(关联要素,有基准)定向跳动定位平面度直线度圆度圆柱度线轮廓度面轮廓度垂直度角度平行度圆跳动全跳动位置度同心度对称度尺寸链的建立1. 形成封闭尺寸环2. 定义装配基准3. 设定GAP (即使干涉也可以假设)尺寸建立尺寸链草图的必要条件:a.各零件有详细的零件图纸。
b.各项目有详细的尺寸和公差,or定义公差表。
c.一个符合实际装配过程的装配图。
U ChannelPEG APEG CPEG BPEG BPEG CU Channel59.51 ±.3211.77±.569.29 ±.3714.24 ±0.29PEG APEG B PEG C如果要使用静态公差分析法RSS 分析所有尺寸组成能够装配,势必会有一个GAP ,Step1: 将所有尺寸组成偏向一边,形成gap ,一般情况下一个尺寸链只有一个gapRemark ,即使知道尺寸链会干涉,也请假设会有一个GAP ,如何确定GAP 是否干涉?U ChannelPEG APEG CPEG BPEG BPEG CGAPStep 2: 建立尺寸链,定义增环(+),减环(-)方向Start hereFinish here U ChannelPEG APEG CPEG BPEG BPEG CGAP(+)(-)Step 3: 将所有尺寸按减环方向开始列,注意尺寸链的连续性,不能断裂Step 4: 将所有尺寸公差平方和开根,得到所有尺寸累计公差和。
( 为简化计算,将极限偏差,修改为对称公差)如上计算结果,RSS 0.93> GAP nom 0.68, 因此结果是干涉的。
产品装配的尺寸链公差分析报告
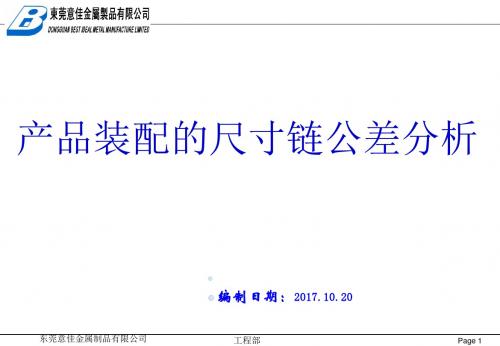
dGap = - 10.00 - 15.00 - 20.00 + 46.00 = 1.00
东莞意佳金属制品有限公司
工程部
n
计算公式: Ttot
Ti 2
i1
Ttot = 最大的预期间隙变量(对称公差) . N = 独立尺寸的堆叠数量. Ti = 第i个尺寸对称公差.
• 它的假设是每个尺寸的 Ppk 指标是1.33并且制程是在中心。
东莞意佳金属制品有限公司
工程部
Page 9
1. 确定组装要求
2. 建立封闭尺寸链图 3. 转换名义尺寸,将公差 转成对称公差 4. 按要求计算名义尺寸
n
Ttot Ti i 1
Ttot = 0.15 + 0.25 + 0.30 + 0.40 = 1.10
最小间隙 Xmin = dGap – Ttot = 1.00 – 1.10 = – 0.10 最大间隙 Xmax = dGap + Ttot = 1.00 + 1.10 = 2.10
[ 2] 吴巍, 袁洪印, 吴明 , 潘凤芝, 尺寸链在公差原则分析中的应用 . 《吉林 农业大学学报》 1999年S1期
[ 3] 杜官将, 薛小强, 尺寸链中形位公差的判别与解算 . 《机械工程与自动化》 2008( 6) : 164-168.
[ 4] 李仲辉, 鲁世红 , 考虑形位公差的装配公差分析 . 《机械工程与自动化》 2010 (3)105-107.
增加 0.10 达到最小间隙的要求 (dGap >0).
极值法求解尺寸链时,封闭环的公差

极值法求解尺寸链时,封闭环的公差尺寸链是指一组相关尺寸之间的依赖关系。
在设计和制造过程中,尺寸链的合理设计对产品的功能和质量起着至关重要的作用。
而要保证尺寸链的准确性和稳定性,我们需要进行封闭环的公差分析。
下面,我们将讨论如何通过极值法来求解尺寸链中的封闭环公差。
首先,什么是封闭环公差呢?封闭环公差是指在尺寸链中形成闭环的相关尺寸之间的公差分配。
封闭环公差的分析是为了确定每个尺寸的公差范围,以保证产品在各种工作条件下的功能和性能能够满足要求。
在进行封闭环公差分析之前,我们需要了解尺寸链的基本原理。
尺寸链是由一系列关联的尺寸组成的,其中有些尺寸是控制性尺寸,也就是需要保持高精度的尺寸;而其他尺寸则是受控尺寸,可以允许一定的变异。
尺寸链的目标是通过统一控制各个尺寸间的公差,实现整个产品的几何和功能要求。
极值法是一种常用的尺寸链公差分析方法。
其基本思想是在尺寸链中找到一条路径,使得路径上的各个尺寸间的公差和达到最大或最小值。
通过最大化或最小化的方式,可以有效地确定每个尺寸的公差范围,以满足整个尺寸链的要求。
具体来说,极值法的求解过程如下:首先,确定尺寸链中需要求解的尺寸;然后,对于每个尺寸,通过分析其上下游尺寸的公差影响,找出一个公差的最大值和最小值;接着,将最大值和最小值分别与上下游尺寸的公差进行比较,选择其中较小的一个作为当前尺寸的公差范围;最后,重复上述步骤,直到所有尺寸的公差范围都确定下来。
极值法的优点是简单易行、直观易懂,对于尺寸链的公差分析提供了一种有效的工具。
通过极值法求解尺寸链的封闭环公差,可以帮助工程师更好地把握尺寸链整体的精度控制,提高产品的质量和稳定性。
然而,极值法也有一些局限性。
首先,它要求尺寸链中的影响路径是明确的,而现实中的尺寸链可能非常复杂,存在多个影响路径,这就增加了公差分析的难度。
其次,极值法在求解尺寸链公差时只能考虑线性关系,而现实中的尺寸链往往存在非线性关系,这就需要其他方法和工具的辅助。
尺寸链计算方法-公差计算
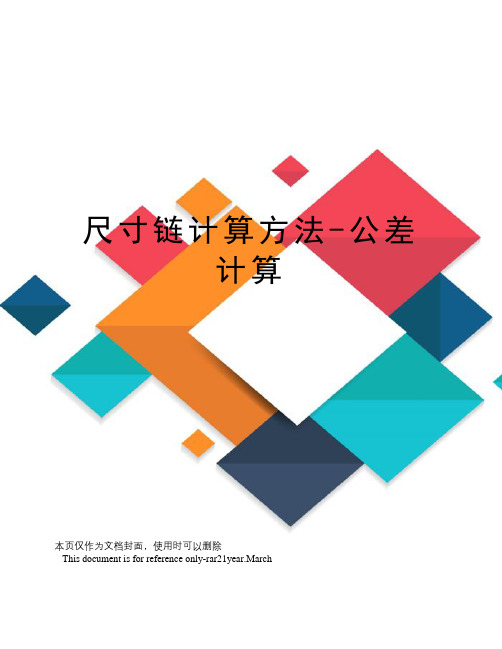
尺寸链计算方法-公差计算本页仅作为文档封面,使用时可以删除This document is for reference only-rar21year.March尺寸链计算一.基本概念尺寸链是一组构成封闭尺寸的组合。
尺寸链中的各个尺寸称为环。
零件在加工或部件在装配过程中,最后得到的尺寸称为封闭环。
组成环又分为增环和减环,当尺寸链中某组成环的尺寸增大时,封闭环的尺寸也随之增大,则该组成环称为增环。
反之为减环。
补偿环:尺寸链中预先选定的某一组成环,可以通过改变其大小或位置,使封闭环达到规定要求。
传递系数ξ:表示各组成环对封闭环影响大小的系数。
增环ξ为正值,减环ξ为负值。
通常直线尺寸链的传递系数取+1或-1.尺寸链的主要特征:①.尺寸连接的封闭性;②.每个尺寸的变化(偏差)都会影响某一尺寸的精度。
二.尺寸链的分类1.按应用范围分工艺尺寸链:在零件加工过程中,几个相互联系的工艺尺寸形成的封闭链。
装配尺寸链:在设计或装配过程中,由几个相关零件的有关尺寸形成的封闭链。
2. 按构成尺寸链各环的空间位置分线性尺寸链:各环位于平行线上平面尺寸链:各环位于一个平面或相互平行的平面,各环不平行排列。
空间尺寸链:各环位于不平行的平面,需投影到三个座标平面上计算。
3.按尺寸链的形式分a)长度尺寸链和角度尺寸链b)装配尺寸链装、零件尺寸链和工艺尺寸链c)基本尺寸链与派生尺寸链基本尺寸链指全部组成环皆直接影响封闭环的尺寸链派生尺寸链指一个尺寸链的封闭环为另一个尺寸链组成环的尺寸链。
d)标量尺寸链和矢量尺寸链三. 基本尺寸的计算把每个基本尺寸看成构成尺寸链的各环,验算其封闭环是否符合设计要求。
是设计中尺寸链计算时首先应该进行的工作。
目前产品生产中经常出现错误的环节,大部分是基本尺寸链错误。
特别是测绘设计的产品。
由于原机的制造误差,测量系统的误差以及尺寸修约的误差,往往会使测绘设计与原设计产生很大的偏差,所以必须进行基本尺寸链的计算四.解尺寸链的主要方法根据零件尺寸的要求和相关标准确定零件尺寸公差,然后按照解尺寸链的最短途径原理的方法对尺寸公差进行验算和修正。
尺寸链计算及公差分析培训工程师ppt课件

尺寸链的计算(统计法)应用于生产批量大的自动化及半自动化生产方面, 或尺寸链的环数较多的场合.
为何要进行尺寸链分析
在我们加工工艺过程中, 治工具及工件的实际定位位置必然会与理想定位位 置有一定的差异,同时加工尺寸也会存在差异.需允许一定的误差存在,如何确定其 误差符合需求,则需引入尺寸链及公差的概念,并进行分析计算。
思考:客户RD图面定义的测量尺寸位置合理性?公差合理性?
让我们先看以下案例
➢侧墙高度变化对卡勾尺寸影响
T²= (0.4)²+(0.2)²+(0.05)²+(0.05)² T=0.45
尺寸链的计算(统计法)
➢ 计算封闭环的中间偏差 封闭环中间偏差等于所有增环中间偏差之和减去所有减环中间偏差之和。 注:中间偏差等于上下偏差代数和再除以2.
封闭环中间偏差= (-0.2+0.2)/2-(-0.1+0.1)/2-(-0.05/2)-(0.05/2) =0-0+0.025-0.025 =0
3D设计值图示
实际卡勾尺寸
➢卡勾后退模拟分析
D件卡勾平移后退0.10mm模拟进行分析,如图所示: 结论:模拟后理论卡合量0.41mm,实际卡合量0.51mm, CD件卡勾间隙0.061mm
D件卡勾平移后退0.1mm图示
➢卡勾后退模拟分析
D件卡勾平移后退0.20mm模拟进行分析,如图所示: 结论:模拟后理论卡合量0.33mm,实际卡合量0.41mm, CD件卡勾间隙0.016mm
尺寸链公差计算

一.尺寸链公差计算
“公差的计算公式:尺寸公差δ=最大极限尺寸D(d)max-最小极限尺寸
D(d)min=ES(es)-EI(ei)。
公差就是零件尺寸允许的变动范围,合理分配零件的公差,优化产品设计,可以以最小的成本和最高的质量制造产品。
公差的计算方法:1、极值法这种方法是在考虑零件尺寸最不利的情况下,通过尺寸链中尺寸的最大值或最小值来计算目标尺寸的值。
2、均方根法这种方法是一种统计分析法,其实就是把尺寸链中的各个尺寸公差的平方之和再开根而得到目标尺寸的值。
尺寸链(dimensional chain ),是分析和技术工序尺寸的有效工具,在制订机械加工工艺过程和保证装配精度中都起着很重要的作用。
在零件加工或机器装配过程中,由互相联系的尺寸按一定顺序首尾相接排列而成的封闭尺寸组。
组成尺寸链的各个尺寸称为尺寸链的环。
其中,在装配或加工过程最终被间接保证精度的尺寸称为封闭环,其余尺寸称为组成环。
组成环可根据其对封闭环的影响性质分为增环和减环。
若其他尺寸不变,那些本身增大而封闭环也增大的尺寸称为增环,那些本身增大而封闭环减小的尺寸则称为减环。
- 1、下载文档前请自行甄别文档内容的完整性,平台不提供额外的编辑、内容补充、找答案等附加服务。
- 2、"仅部分预览"的文档,不可在线预览部分如存在完整性等问题,可反馈申请退款(可完整预览的文档不适用该条件!)。
- 3、如文档侵犯您的权益,请联系客服反馈,我们会尽快为您处理(人工客服工作时间:9:00-18:30)。
線性尺寸鏈公差分析. 程序設計用于(1D)線性尺寸鏈公差分析。程序解決以下問題: 公差分析,使用算術法"WC"(最差條件worst case)綜合和最優化尺寸鏈,也可以使用統計學計算"RSS"(Root Sum Squares)。 溫度變化引起的尺寸鏈變形分析。 使用"6 Sigma"的方法拓展尺寸鏈統計分析。 選擇裝配的尺寸鏈公差分析,包含組裝零件數的最優化。 所有完成的任務允許在額定公差值內運行,包括尺寸鏈的設計和最優化。 計算中包含了ANSI, ISO, DIN以及其他的專業文獻的 數據,方法,算法和信息。標准參考表: ANSI B4.1, ISO 286, ISO 2768, DIN 7186
計算的控制,結構及語法。 計算的控制與語法可以在此鏈接中找到相關信息 "計算的控制,結構與語法". 項目信息。 “項目信息”章節的目的,使用和控制可以在"項目信息"文檔裏找到. 理論-原理。 一個線性尺寸鏈是由一組獨立平行的尺寸形成的封閉環。他們可以是一個零件的相互位置尺寸(Fig.A)或是組裝單元中各個零件尺寸 (Fig. B).
一個尺寸鏈由分開的部分零件(輸入尺寸)和一個封閉零件(結果尺寸)組成。部分零件(A,B,C...)可以是圖面中的直接尺寸或者是按照先前的加工工藝,組裝方式。 所給尺寸中的封閉零件(Z)表現爲加工工藝或組裝尺寸的結果,結果綜合了部分零件的加工尺寸,組裝間隙或零件的幹涉。結果尺寸的大小,公差和極限直接取決于部分尺寸的大小和公差,取決于部分零件的變化對封閉零件變化的作用大小,在尺寸鏈中分爲兩類零件: - 增加零件 - 部分零件,該零件的增加導致封閉零件的尺寸增加 - 減少零件 - 部分零件,封閉零件尺寸隨著該零件的尺寸增加而減小 在解決尺寸鏈公差關系的時候,會出現兩類問題: 公差分析- 直接任務,控制 使用所有已知極限偏差的部分零件,封閉零件的極限偏差被設置。直接任務在計算中是明確的同時通常用于在給定圖面下檢查零件的組裝與加工。 公差合成- 間接任務,設計 出于功能需要使用封閉零件的極限偏差,來設計部分零件的極限偏差。間接任務用來解決設計功能組及組裝。 公差計算方法的選擇以及尺寸鏈零件的極限偏差影響組裝精度和零件的組裝互換性。因此,産品的經濟性和運轉性取決于此。在尺寸鏈中解決公差關系,工程實踐使用三個基本方法: • 算數計算法 • 統計學計算法 • 成組交替性計算方法
算術計算方法 - WC method (Worst Case). 最常使用的方法,有時叫做最大-最小計算方法。它用于在任何部分零件的實際尺寸的任意組合下保證封閉零件的所需極限偏差,也就是最大和最小極限尺寸。 這個方法保證了零件的完全裝配和工作交替性。但是,由于封閉零件的高精度要求,導致部分零件的公差值太極限,因此帶來高的加工成本。因此WC方法主要適合用于計算小數量零件尺寸鏈或結果尺寸的公差是可以接受的 情況。最常用于單間或小批量生産。 WC 方法計算得出的結果尺寸是部分尺寸的算術和。因此封閉零件的尺寸決定于其中心值:
和總的公差: 封閉零件的邊界尺寸關系: 含義:i -第i個零件的中心值
Ti - 第i個零件的公差 n - 部分零件數 i=1,..,k - 增加零件尺寸 i=k,..,n - 減少零件尺寸
統計學計算方法 -統計計算方法- RSS, 6 西格碼 方法 尺寸鏈的統計學計算方法依據概率運算法。這些方法假定選擇隨機零件組裝,部分零件的偏差極限值出現的幾率很小,由于是組合的概率。每個零件的各個加工尺寸的偏差極限出現的事件概率很小。預選一些零件的廢品的風險,尺寸鏈中的部分零件公差可以增加。 統計方法僅僅保證部件裝配的互換性,不良狀況(損壞)的低比率。考慮使用局部零件較大公差,但是,這會導致生産成本的降低。通常用于大量生存,節省制造成本重于由零件不完整互配性裝配帶來的組裝和工作費用。 封閉零件的尺寸顯示來自公差區域平均值的變化。各個尺寸的發生概率按數理統計計算同時大多數情況下完全符合正態分布。分布以概率密度的高斯曲線描述,“x"尺寸的事件概率按下面公式計算: 高斯曲線的形狀由兩個參數描述,中心值µ定義結果尺寸出現最高頻率的位置;標准差σ定義了曲線“細長比”
標准差σ變化值的高斯曲線
高斯曲線和定義的封閉零件的極限尺寸的交集爲制程目標良率。超出允許區間的爲制程不良。 中心和非中心設計的制程良率
通常工程領域,制造制程常常設置滿足有效等級3σ。意味著結果尺寸的上限UL和下限 LL在中心值µ的3σ以內。在高斯曲線的上下限以內等于總集合的99.73%,這個區域的産品符合規格要求。超出的部分比率爲 0.27% ,爲尺寸超出的産品。
封閉零件公差的可變寬度所代表的良率
Limit sizes極限尺寸 Process yield 制程良率[%] Number of rejects per million components produced百萬個零件中不良品數 ± 1 68.2 317310
± 2 95.4 45500
± 3 99.73 2700
± 3.5 99.95 465 ± 4 99.994 63
± 4.5 99.9993 6.8
± 5 99.99994 0.6
± 6 99.9999998 0.002
和的平方根方法 這個計算方法也是和尺寸鏈統計計算方法一樣的最普遍的傳統計算方法。RSS方法依據假設各個局部零件在3σ制程能力(品質)下制造。
極限值由此符合容許空間µ+/-3σ,標准差設置如下: 封閉零件尺寸爲平均值
以及標准差: 含義: i - 第i個零件標准差
i - 第i個零件的中心值
Ti - 第i個零件的公差 n - 總局部零件數 i=1,..,k - 遞增零件數 i=k,..,n - 遞減零件數
6 西格碼”方法 通常工程領域,制造制程常常傳統地設置滿足有效等級3σ。大約百萬個産品中2700個不良。盡管這些超出地産品起初看起來非常良好,但在一些産品領域,越發不足。除此之外,從長期來看幾乎不可能保證制程特性曲線地中心值完全在容許範圍地中心。以防大批量生産時的制程曲線的中心值隨著時間的推移而偏移,由于變化因數的影響(錯誤的組裝,工具和夾具的磨損,溫度變化等等。)1.5σ的偏移是典型的,對于接近3σ等級的制程能力,表現爲超出公差的比率爲百萬分之67000。
很明顯在此等級的制程損壞是不可接受的。因此,最近“6西格碼”的方法越來越被廣泛使用在評估制程品質上。方法的概念是獲得制程特性的中心值是在距離兩個公差極限值6σ範圍內。在此有效制程條件下,即使1.5σ的偏移産生,也可保證百萬分之3.4的超出公差的比率。
“6σ”的方法相對較新,它變得廣泛而流行是在1980s和1990s。第一次是由Motorola公司運用于實際而主要在美國被使用。它適用于高品質的制造流程和制程曲線會偏移的大批量生産中。 “6σ”防範是標准“RSS”的修改同時引入兩個新的參數,(Cp, Cpk) ,被成爲制程能力指數。這些能力指數被
用于評估制造流程的品質。 Cp值用于對照傳統的3 σ制程能力而評估制造流程的品質。
對于容許空間µ+/-3σ,Cp等于1。對于高品質的制程,公差極限在距離中心值6σ的範圍內, Cp=2。
Cpk值是Cp在考慮制程偏移而修改的。 對于中心偏移因數k的範圍爲<0..1> 決定了一半公差區間內而産生的相應偏移值。對于典型的1.5σ制程特性偏移,“6σ”品質下的中心偏移因數將會是k=0.25 , Cpk=1.5。
有效的標准差評估如下:
在對尺寸鏈中所有局部零件運用能力指數後,封閉零件的尺寸可以類似于“RSS”方法而活和中心值µ以及標准差
同時:σei-第i個零件的有效標准差。 對于“6σ”方法,結果爲4.5σ的制程能力比率也是可接受的。
成組互換方法(選擇組配) 選擇組配方法用于大量制造的精確産品,並且在産品內不存在零件工作互換性的問題。産品組裝是通過挑選各個零件進入公差子集,零件的制造尺寸可以被指定爲較大公差。狹小的結果尺寸公差通過選擇的子集功能匹配(綜合)而得。爲了定義封閉零件得結果尺寸,上面定義得“WC”方法被使用,除了計算不包含局部零件得所有制造公差,但是,僅有狹小的公差適合選定的公差子集。 選擇組配方法是一個非常有效的解決尺寸鏈方法,允許局部零件的制造公差大幅度增長,同時明顯減小制造成本。另一方面,這個方法計算帶來了零件組配的要求提升,操作成本相應提升,通常需要更換所有組裝零件以防局部零件的磨損或破壞。 如果選擇裝配的方法是有效的,必須解決零件優化選擇(綜合)的問題。零件必須匹配,所以對于給定的制造零件的數目可以組裝最大可能性的零件數目從而獲得功能需求。這個任務可以分爲兩個部分:
1.任務設計部分 爲了使封閉零件符合功能需求,尋找局部零件各個子集的所有組合。此任務必須在生産之前解決,在設計尺寸鏈的過程中。適合組配的數目取決于局部零件的所有制造公差,同時也取決于所選的公差子集的數目。尺寸鏈一定被設計可接受的組裝組合的數目在有效極限範圍內。 對于一些較小數目的適合組合,可能沒有必要在組裝中使用所有制造零件。這就是爲什麽制程的組裝良率減小而生産成本增加了。當在這機過程中出現一些不可接受的子集,主要指數表現出來。 另一方面,較大數目的適合組合表現爲無效設計,尺寸鏈可能要被設計爲更優化的方式,局部零件公差放大或公差子集數目縮小。
2. 任務的技術部分 對于在各個公差子集中給定制造零件數目的組裝零件數目的最優化。 該任務必須在制造中被重複履行,在補充庫存之前,在組裝開始之前。任務的主要目的是爲了獲得組裝産品的最大可能性數目而決定最優化組裝流程。在解決問題時,我們必須從在組裝的可接受組合子集中選擇最優化組合設置,同時在各個使用的組合中決定組裝零件的數目。 通過從所選子集中取消零件而漸進各個産品的組裝,最優化的算法是以此爲基礎的。在最先階段,計算出組裝産品的最大和最小可能數目。其後,根據預選計劃從選擇的子集中縮小零件數。因此,組裝産品數目低估增加越來越快,上估減少越來越慢。 任務的方案通常不明確。不同的組裝流程帶來同樣的數目的組裝産品是經常發生的。這就是爲什麽使用的組裝組合數目被用作另一個優化准則的原因。使用組合數的最小化導致組裝的簡化和加速,也就是說,在制造費用的降低,在一些實際應用中,兩個標准同樣重要。
計算單位,標准公差。 本行用于調整計算的單位系統和選擇標准公差。 計算單位 In the list box, select the required system of units for calculation. After switching the units, all values will be automatically recalculated. 在表格中,選擇計算所需的單位系統,一旦改變單位,所有值將重新自動計算。