浅谈铸件缺陷――气孔
铸钢件气孔缺陷的分析及预防

铸钢件气孔缺陷的分析及预防摘要:在进行机械化生产的时候,铸钢件由于其精确度比较高,而且能够做到流水线生产,具有较好的重复性。
受到了人们的青睐,获得了广泛的应用,具体分析铸钢件的特点,对铸钢件在制造时容易产生的气孔缺陷进行分析,并且阐述铸钢件气孔出现缺陷的原理,分析如何预防铸钢件气孔缺陷,以供参考。
关键词:铸钢件气孔缺陷;制造;机械化引言由于铸钢件有易于进行大规模流水线生产的特点,在机械化生产的过程中获得了广泛的应用,在同一生产线上,不会限制铸钢件的形状大小和材料,铸钢件的特点在于铸钢件的外观和内部结构重复性好,而且尺寸精度较高,具有较好的表面光滑度以及平整性,不需要进行合箱取模,在操作的过程中工艺流程较为简单,。
在一定程度上,可以避免出现废品和铸造缺陷。
1铸钢件气孔缺陷的危害在铸钢产品当中气孔是一种主要的缺陷,对铸钢件的质量产生影响的一个重要因素。
气孔往往会导致铸件产生多种不利影响,会让铸件的有效截面积大幅度减少,还会导致铸钢件的强度降低,出现的一些多角形气孔和裂纹状气孔还会在一定程度上让铸件的块口敏感性增加,导致应力集中等问题的产生,逐步变成断裂缺陷的裂纹源。
另外,气孔还在一定程度上让铸件的抗拉强度和疲劳强度降低。
图1 铸钢件气孔2铸钢件气孔缺陷机理分析铸钢件当中常会出现一些气孔缺陷,这些缺陷会对铸钢件的硬度、强度以及弹性模量等相关性能产生较大影响,出现气孔的原因多种多样,生产工艺流程不当以及原材料质量不佳,都会导致铸钢件出现气孔缺陷。
合理的对铸钢件气孔缺陷进行分析,能够让气孔缺陷问题得到改善,让铸钢件的质量提高,让企业的效益增加。
导致顶盖报废的气孔当中,侵入性气孔是相对较为常见的,在箱体结构当中,顶盖属于密封型,在浇筑的过程中,高温钢液会让顶盖当中的一些石灰石成分分解,而出现一定量的二氧化碳,然后因为排气孔较小,造成分解的二氧化碳没有办法及时的向外排出,造成二氧化碳在分解的时候出现气压比钢液的表面阻力大等情况,二氧化碳就会在钢液当中渗入,二氧化碳与钢液是不相容的,与此同时二氧化碳具有较小的密度,会在钢液当中浮起,而从冒口处排出,一些二氧化碳无法排出,则会出现侵入性气孔在铸钢件的上表面滞留。
压铸件气孔产生的原因

压铸件气孔产生的原因产生气孔的原因有以下几点:一、氢气残留。
原材料里面还有氢气,坩埚及环境还有湿气,导致气体加热产生氢气夹裹在原材料里面,容易产生针状气孔。
二、压射室充满度不高。
压射室充满度不高会导致压射室内含空间过大,铝汤在压射前,出现回流撞击,产生涡流。
气泡是模具温度及铝温太高,容易产生气泡。
氢气,压射缸卷起,流道卷起,型腔内压力卷起,水蒸气产生气孔这些都是模具气孔的主因。
产生原因:1、金属液在压射室充满度过低(控制在45%~70%),易产生卷气,初压射速度过高。
2、模具浇注系统不合理,排气不良。
3、熔炼温度过高,含气量高,熔液未除气。
4、模具温度过高,留模时间不够,金属凝固时间不足,强度不够过早开模,受压气体膨胀起来。
5、脱模剂、注射头油用量过多。
6、喷涂后吹气时间过短,模具表面水未吹干。
解决压铸件气孔的办法:先分析出师什么原因导致的气孔,再来取相应的措施。
(1)干燥、干净的合金料。
(2)控制熔炼温度,避免过热,进行除气处理。
(3)合理选择压铸工艺参数,特别是压射速度。
调整高速切换起点。
(4)顺利填充有利于型腔气体排出,直浇道和横浇道有足够的长度(>50mm),有利于合金液平稳流动和气体有机会排出。
可改变浇口厚度、浇口方向、在形成气孔的位置设置溢流槽、排气槽。
溢流品截面积总和不能小于内浇口截面积总和的60%,否则排渣效果差。
(5)选择性能好的涂料及控制喷涂量。
预防措施:1、调整压铸工艺参数、压射速度和高压射速度的切换点。
2、修改模具浇道,增设溢流槽、排气槽。
3、降低缺陷区域模温,从而降低气体的压力作用。
4、调整熔炼工艺、5、延长留模时间,调整喷涂后吹气时间。
6、调整脱模剂、压射油用量。
气孔是压铸件中常见多发的缺陷之一。
气孔呈圆形或扁平椭圆形气泡状,直径为1mm至20mm不等,内表面光滑,覆有一层氧化层,通常分散在加工表面下。
一、气孔缺陷的成因01 金属杂质过多原材料或回收料中含有较多的氧化物和其他杂质,一些杂质(如氧化物、氢化物、油脂)在熔炼过程中会释放气体。
检测铸件气孔的方法

检测铸件气孔的方法一、引言在我国的铸造行业中,铸件气孔是一个常见的问题。
气孔的存在不仅影响铸件的外观质量,还会对其使用性能产生严重影响。
为了确保铸件的质量,对铸件气孔的检测至关重要。
本文将对铸件气孔的成因、危害以及常用的检测方法进行介绍,以帮助大家更好地了解和解决这一问题。
二、铸件气孔的成因及危害铸件气孔主要是由于铸造过程中,金属液与型砂、芯砂等固体粒子发生反应产生的气体在凝固过程中无法及时排出而在铸件内部形成的。
铸件气孔的存在会使铸件的强度、硬度、耐磨性等性能降低,同时还容易导致铸件在使用过程中出现裂纹、变形等现象。
三、检测铸件气孔的常用方法1.肉眼观察:通过肉眼直接观察铸件表面和断面,观察是否存在气孔。
这种方法适用于较大型的铸件,但对于微小气孔和内部气孔难以发现。
2.低倍显微镜检测:使用低倍显微镜观察铸件的表面和断面,可以较准确地检测到微小气孔。
但低倍显微镜检测仍然难以发现内部气孔。
3.超声波检测:利用超声波在铸件中的传播特性,检测铸件内部是否存在气孔。
这种方法无损检测,适用于各种类型的铸件,但对于形状复杂、厚度变化的铸件检测效果有所降低。
4.射线检测:通过射线对铸件进行透射,观察射线底片上是否存在气孔。
这种方法适用于厚壁、大型铸件的检测,但射线对人体有一定危害,需采取防护措施。
5.渗透检测:将渗透剂涂抹在铸件表面,通过检测气孔处渗透剂的扩散情况来判断气孔的存在。
这种方法适用于表面光滑、无油污的铸件,但对于内部气孔和微小气孔检测效果较差。
四、各种检测方法的优缺点对比1.肉眼观察和低倍显微镜检测:优点是操作简便、成本低,适用于大型铸件的表面气孔检测。
缺点是难以发现微小气孔和内部气孔。
2.超声波检测:优点是无需破坏铸件,可以检测到内部气孔。
缺点是对形状复杂、厚度变化的铸件检测效果有所降低,且对微小气孔检测效果较差。
3.射线检测:优点是适用于厚壁、大型铸件的检测,检测精度较高。
缺点是射线对人体有一定危害,需采取防护措施。
气孔类缺陷牲与防治方法
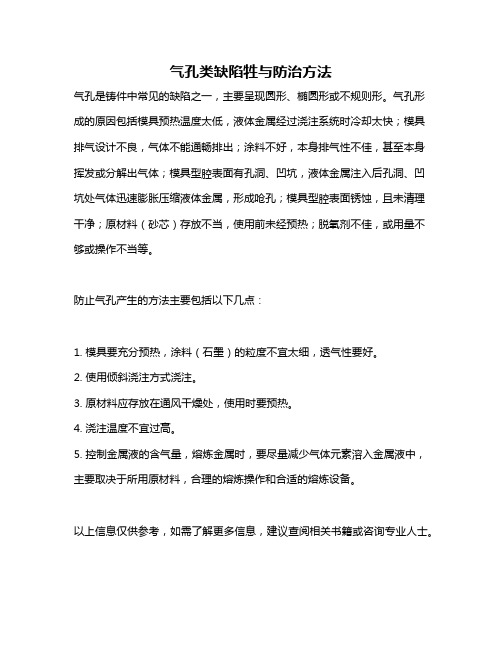
气孔类缺陷牲与防治方法
气孔是铸件中常见的缺陷之一,主要呈现圆形、椭圆形或不规则形。
气孔形成的原因包括模具预热温度太低,液体金属经过浇注系统时冷却太快;模具排气设计不良,气体不能通畅排出;涂料不好,本身排气性不佳,甚至本身挥发或分解出气体;模具型腔表面有孔洞、凹坑,液体金属注入后孔洞、凹坑处气体迅速膨胀压缩液体金属,形成呛孔;模具型腔表面锈蚀,且未清理干净;原材料(砂芯)存放不当,使用前未经预热;脱氧剂不佳,或用量不够或操作不当等。
防止气孔产生的方法主要包括以下几点:
1. 模具要充分预热,涂料(石墨)的粒度不宜太细,透气性要好。
2. 使用倾斜浇注方式浇注。
3. 原材料应存放在通风干燥处,使用时要预热。
4. 浇注温度不宜过高。
5. 控制金属液的含气量,熔炼金属时,要尽量减少气体元素溶入金属液中,主要取决于所用原材料,合理的熔炼操作和合适的熔炼设备。
以上信息仅供参考,如需了解更多信息,建议查阅相关书籍或咨询专业人士。
铸件气孔案例分析报告

铸件气孔案例分析报告1. 引言铸造是一种常见的金属加工方法,用于生产各种复杂形状的金属零件。
然而,在铸造过程中,气体存在的问题是一个常见的挑战。
气孔是铸件中最常见的缺陷之一,它们对铸件的力学性能和表面质量都会造成负面影响。
因此,对铸件气孔现象进行分析,并采取相应的措施来减少气孔产生,是提高铸件质量和性能的关键。
2. 气孔的成因气孔的形成是由于铸造过程中存在的气体无法完全逸出,而被困在铸件内部形成的。
气体在金属液态状态下溶解度较低,在凝固过程中会析出。
以下是几种常见的气孔成因:a) 液态金属中溶解的气体:液态金属中可溶解的气体,在固化过程中会分解,产生气体泡沫形成气孔。
b) 铸型气体:在铸造过程中,砂型或其他铸型材料中的挥发物会被加热并释放出气体,形成气孔。
c) 内部形成的气体:在凝固过程中,疏松的金属结构或其他元素的分解反应会生成气体,形成气孔。
3. 气孔的影响气孔对铸件性能和表面质量产生以下负面影响:a) 降低强度和韧性:气孔导致铸件内部存在弱点和孔洞,会降低铸件的强度和韧性。
b) 引起裂纹和漏洞:气孔是裂纹和漏洞形成的起点,它们可能在应力作用下扩展,导致铸件的损坏和失效。
c) 影响铸件外观:气孔会在铸件表面形成小孔或凹陷,影响铸件的外观质量,降低其市场竞争力。
4. 案例分析以下是一个关于铸件气孔案例的分析,以展示如何识别和解决气孔问题的过程:案例背景:一家汽车制造公司的铝合金发动机块铸件出现了气孔问题,导致部分铸件在测试中出现弯曲和断裂现象,严重影响了发动机的可靠性。
分析步骤:a) 气孔检测:使用X射线或CT扫描等非破坏性检测方法,对铸件进行全面的检测,确定气孔的位置和数量。
b) 气孔成因分析:通过对铸造工艺参数、金属合金成分和砂型材料等进行分析,确定气孔产生的可能原因。
c) 工艺优化:针对气孔成因,通过调整铸造温度、压力和保温时间等工艺参数,优化铸造过程,减少气孔的形成。
d) 砂型改进:对砂型材料进行优化,选择低挥发性和低含气量的材料,减少砂型气体的释放。
铸件气孔 -回复
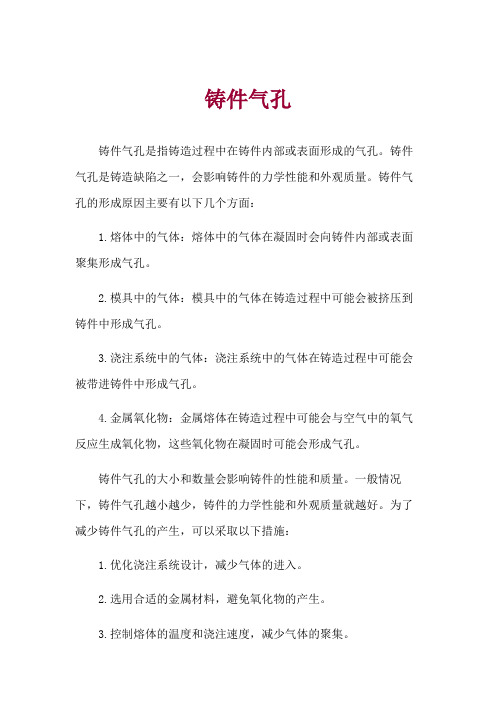
铸件气孔
铸件气孔是指铸造过程中在铸件内部或表面形成的气孔。
铸件气孔是铸造缺陷之一,会影响铸件的力学性能和外观质量。
铸件气孔的形成原因主要有以下几个方面:
1.熔体中的气体:熔体中的气体在凝固时会向铸件内部或表面聚集形成气孔。
2.模具中的气体:模具中的气体在铸造过程中可能会被挤压到铸件中形成气孔。
3.浇注系统中的气体:浇注系统中的气体在铸造过程中可能会被带进铸件中形成气孔。
4.金属氧化物:金属熔体在铸造过程中可能会与空气中的氧气反应生成氧化物,这些氧化物在凝固时可能会形成气孔。
铸件气孔的大小和数量会影响铸件的性能和质量。
一般情况下,铸件气孔越小越少,铸件的力学性能和外观质量就越好。
为了减少铸件气孔的产生,可以采取以下措施:
1.优化浇注系统设计,减少气体的进入。
2.选用合适的金属材料,避免氧化物的产生。
3.控制熔体的温度和浇注速度,减少气体的聚集。
4.采用真空铸造或压力铸造等先进工艺,减少气体的产生。
铸件气孔的检测方法包括目视检查、X射线检测、超声波检测等。
一旦发现铸件气孔,需要进行修补或重新铸造。
铸件气孔分析及解决措施的建议
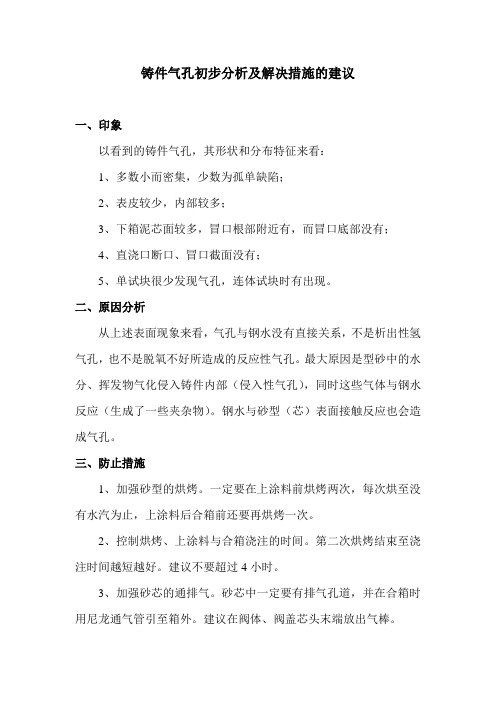
铸件气孔初步分析及解决措施的建议一、印象以看到的铸件气孔,其形状和分布特征来看:1、多数小而密集,少数为孤单缺陷;2、表皮较少,内部较多;3、下箱泥芯面较多,冒口根部附近有,而冒口底部没有;4、直浇口断口、冒口截面没有;5、单试块很少发现气孔,连体试块时有出现。
二、原因分析从上述表面现象来看,气孔与钢水没有直接关系,不是析出性氢气孔,也不是脱氧不好所造成的反应性气孔。
最大原因是型砂中的水分、挥发物气化侵入铸件内部(侵入性气孔),同时这些气体与钢水反应(生成了一些夹杂物)。
钢水与砂型(芯)表面接触反应也会造成气孔。
三、防止措施1、加强砂型的烘烤。
一定要在上涂料前烘烤两次,每次烘至没有水汽为止,上涂料后合箱前还要再烘烤一次。
2、控制烘烤、上涂料与合箱浇注的时间。
第二次烘烤结束至浇注时间越短越好。
建议不要超过4小时。
3、加强砂芯的通排气。
砂芯中一定要有排气孔道,并在合箱时用尼龙通气管引至箱外。
建议在阀体、阀盖芯头末端放出气棒。
4、浇注坑内潮湿的砂要清理掉,换成破碎机清除出来的陶口管碎屑。
5、改变浇口位置,如自封密式闸阀阀体中通道端有气孔在此处增加底注浇口。
6、树脂固化剂厂家的对比试验,某一时期固定用一家厂的树脂、固化剂,统计对比出现气孔的概率。
同一厂家的产品也要统计出现气孔的概率,看哪一家的产品好。
7、合金烘烤容易造成气孔的镍板、钼铁、金属铬等合金材料要脱氧,容易造成气孔的废钢,如不锈钢压块料要烘烤。
8、熔炼时不能用潮湿的造渣材料,吸了水的石灰一定不要用,熔炼后期加大渣量,减少功率,防止驼峰致使钢水外露吸气。
9、如有可能,弹性闸板砂芯试用水玻璃有机酯。
这种砂与碱酚醛砂不冲突,可以同时回用。
1.。
消失模工艺铸件气孔、渣孔缺陷,是怎么形成的?该如何防止?

消失模工艺铸件气孔、渣孔缺陷,是怎么形成的?该如何防止?本次疫情期间,罗通老师写了一篇关于铸件气孔、渣孔缺陷的文章,洲际铸造平台授权转载!许多消失模铸造厂在生产加工件时特别是碳钢不锈钢件,虽然抛丸后没有什么问题外观也比较理想,可是一加工就出现渣孔气孔,而产生的位置一般在产品的中上部及侧边和浇注系统的对面,夹渣是夹杂缺陷的铁液熔渣和模样残渣。
铸件上二者一般都呈黑色,大小不一,形状很不规则,有块状、片状、线条状等。
一般存在于铸件内部,多见于铸件上表面的皮下和拐角处。
那么泡沫模型气化分解生成大量的气体及残留物不能及时排出铸型,泡沫、涂料层填充干砂的干燥不良,在高温包围下,裂解出大量的氢气和氧气侵入铸件而形成气孔。
产生气孔渣孔的原因一般有以下几种:1,泡沫的水分干燥不透彻就去上涂料,涂料第一遍没干透就去上第二遍,在高温的液体浇注时产生的气孔,2,泡沫的密度过于太大使浇注时来不及气化而吐食泡沫产生的泡沫渣形成渣孔3,钢水脱氧不良、炉台、炉内、包内除渣不净,熔化铁水时,或多或少要产生熔渣,特别是炉料锈蚀严重或采用铁屑熔炼时,产生大量的金属熔渣。
在浇注时熔渣很容易随着铁水进入型腔,留在铸件内部,凝固后就形成黑色夹渣。
由于夹渣的密度比铁水小,一般要浮在铸件上面,铸件拐角处对熔渣有阻碍作用,熔渣上浮时易产生滞留,所以该部位也多见夹渣缺陷。
镇静时间过短,浇注过程中挡渣不力,浇注工艺不合理造成渣孔。
4,由于浇注系统设计不合理,大件小件混合搭配在一个砂型形成了纵横交错,钢水的充型速度大于泡沫气化退让及气体排出速度,造成充型前沿将气化残留物包夹在钢水中再次气化形成内壁烟黑色的分解气孔。
5,浇注温度低,充型前沿钢水不能使泡沫充分气化,未分解的残余物质来不及浮集到冒口而凝固在铸件中形成气孔。
5、内浇道开设位置不合理,充型时形成死角区,由于型腔内气体压力作用,使气化残留物积聚在死角处形成气孔,内浇道截面积过大,而且少使充型速度大于泡沫气化退让速度,吞食泡沫,在合金内部分解气化,而气体无法排出形成气孔。
- 1、下载文档前请自行甄别文档内容的完整性,平台不提供额外的编辑、内容补充、找答案等附加服务。
- 2、"仅部分预览"的文档,不可在线预览部分如存在完整性等问题,可反馈申请退款(可完整预览的文档不适用该条件!)。
- 3、如文档侵犯您的权益,请联系客服反馈,我们会尽快为您处理(人工客服工作时间:9:00-18:30)。
技师专业论文
工种:铸造工
浅谈铸件缺陷――气孔
姓名:
身份证号:
等级:
准考证号:
培训单位:
鉴定单位:
日期:
目录
一、引言 1
二、气孔分类 1 (一)侵入性气孔 1
1、特征 2
2、侵入性气孔的形成条件 2
3、防止侵入性气孔的主要方法和工艺措施 3 (二)析出性气孔 3
1、特征 3
2、析出性气孔的形成机理 4
3、防治析出性气孔的方法 4 (三)反应性气孔的形成机理 4
1、特征 5
2、反应性气孔的形成机理 5
3、防止反应性气孔的措施 5
三、结束语 6
摘要:材料的合理选用,正确的工艺操作过程,才能减少铸件气孔的产生。
关键词:气孔气孔的分类气孔的形成预防工艺措施
一、引言
从2007年3月份转为车间中间检验岗位工作。
在这十三年的实际操作及学习中,了解并懂得了一些粗浅的铸造知识。
现在结合我们公司的生产实际简单谈谈我对铸件缺陷——气孔的认知。
二、气孔的分类
根据调查统计资料,由于气孔所导致的铸件废品占废品总数的三分之一左右。
气孔是气体聚集在铸件表面、皮下和内部而形成的孔洞。
气孔的孔壁光滑,捎带氧化色彩,无一定形状、尺寸和位置,气孔有各种类型,其产生的原因各不相同,按照气体来源的不同一般将气孔分为三类:侵入性气孔、析出性气孔和反应性气孔。
(一)侵入性气孔
由于浇注过程中液态金属对铸型激烈的热作用,使型砂和芯砂中的发气物(如水份、粘结剂和附加物质等)气化、分解和燃烧,生成大量气体以及型腔中原有的气体侵入液态金属内部而不能逸出所产生的孔洞称为侵入性气孔
1、特征侵入性气孔尺寸较大,孔壁光滑,有光泽,稍带氧化色,
呈圆形或腰圆形,多数呈梨形,位于铸件表面或内部。
如下图所示:
2、侵入性气孔的形成条件由于浇注时型芯砂在金属液的高温作用下,产生大量气体,使金属液和砂型界面上的气体压力骤然增加,气体可能侵入金属液,也可能从砂型或排气孔中排出型外,只有满足下列条件的情况下,型砂中的气孔才会侵入金属液。
如下图所示:
P液
B
(a)(b)(c)
即P气>P液+P阻+P腔
公式中P气——金属液和砂型界面的气体压力。
P液——金属液静压力(P液=ρgh 其中ρ金属液的密度;g为重力加速度;h为金属液的高度)。
P阻——气体侵入金属液时,由于金属液表面张力而引
起的阻力。
P腔——型腔中金属液面上的气体压力。
3、防止侵入性气孔形成的主要方法和工艺措施(在我公司的铸件气孔缺陷中主要为侵入性气孔)
①选用粒度适宜含泥量少的原砂且保证新砂的烘干度,以及加大新砂的混制比例;控制粘上水分及附加物的加入量,保证型砂有良好的透气性。
②在不影响砂型强度的前提下,尽量减少树脂加入量及提高砂芯上涂后的烘干度,并及时使用烘干后的砂芯。
③适当增加铸型排气孔洞数量,保证铸型、砂芯排气孔洞的畅通。
④适当提高浇注温度,浇铸温度控制在1415℃――1430℃之间,使侵入的气体有充分的时间从金属液中上浮和排出。
⑤加快浇注速度,使浇铸速度控制在15秒――18秒,或增大直浇道的横截面积(即:采用使用双排内浇道),提高金属液的静压力。
⑥应设置平稳的浇注系统,防止气体卷入。
(二)析出性气孔
溶解在金属液中的气体,在冷却和凝固过程中,由于溶解度降低而析出形成的孔洞称为析出性气孔。
1、特征数量多,尺寸小,形状呈圆形、椭圆形或针状。
在
铸件断面呈大面积均匀分布。
同一炉次铸件大部分有气孔,主要是氢气孔和氮气孔,这是铝合金和钢铸件中常见的缺陷。
我公司所使用的灰铁铸件中出现此类缺陷的几率相对较少。
2、析出性气孔的形成金属具有吸附和溶解气体的能力(如氢、氧、氮等)。
尤其在液态时能溶解大量气体。
溶解在液态金属中的气体,在温度和外界压力降低时,就会从金属中析出,析出的方式有两种:一种是气体原子从金属内部扩散到金属表面,脱离吸附状态,另一种是气体原子在金属内部形成气体分子和气泡上浮排出。
3、防止析出性气孔的方法
①减少合金的吸气量。
清洁炉料,烘干炉衬和浇注工具,缩短熔炼时间,以避免液态金属和炉气的接触,减少熔炼吸气等。
②对金属液进行除气处理,可用加入元素除气法,吹入不溶性气体及真空除气法等。
③阻止气体的析出。
如提高铸件的冷却速度,正确设置浇冒系统,提高外界的压力等。
(三)反应性气孔
由于液态金属与铸型界面之间,液态金属与渣之间或液态金属内部某些元素之间发生了化学反应产生气体而形成的孔洞,成为反应性气孔。
1、特征这种气体孔一般均匀成群分布,且往往产生于铸件皮下。
又因为形状呈针头或细长腰圆形状,又称针孔。
此类气孔在
铸钢件、球墨铁中出现较多。
下面着重阐述球墨铸铁。
2、反应性气孔的形成机理皮下气孔的形成过程是一个复杂的物理、化学过程。
受各种因素的影响气体来源原子内部析出或外部的侵入。
铁液内部析出的气体有:镁的蒸气,硅铁和稀土合金中的氢气及铁液凝固时溶解度急剧降低而析出的气体;外部侵入的气体主要是铁液和铸型界面上产生某种化学反应所生成的气体。
如:铁液中逸出的镁或铁液表面的硫化镁与铸型中的水蒸气,发生如下反应:
Mg + H2O = MgO + H2
MgS + H2O =MgO + H2S
内部析出的气体受到铁液表面氧化膜的阻止不能尽快逸出液面,外部界面反应的气体凭较大的压力侵入有糊状凝固特性而表层较长时间内不能完全凝固的球墨铸铁液体中,待表面凝固后,滞留于铸件表皮下形成皮下气孔。
3、防止反应性气孔的措施
①在保证球化的前提下,尽量减少残留镁量,使镁的质量分数控制在0.03﹪-00.4﹪之间,并尽可能降低原铁液的含硫量。
②尽量控制型砂中的水份,水的质量分数:中压造型低于5﹪,高压造型低于4﹪。
③选择合适的原砂,尽可能降低型砂的强度,提高型砂的透气性。
④孕育硅铁要预热,烘烤。
⑤控制冷却速度,冷却凝固速度快或缓慢两种情况产生皮下气孔都会很少。
⑥在型砂中配入一定的煤粉(FS、MD粉),在金属--铸型界面上造成还原性气氛保护层,防止铁液氧化。
⑦尽可能提高浇注温度,温度控制在1415℃――1430℃。
⑧设置平稳的浇注系统,防止气体卷入及铁液飞溅搅动造成镁蒸气挥发和燃烧产生气体。
三、结束语
铸造缺陷――气孔对铸件质量和铸造生产有很大的危害。
要迅速有效地消除气孔,必须作系统地调查研究,准确地判断气孔地种类,查明产生地原因,经综合分析和实践验证,方可采取相应地防止措施。