难切削材料
难加工材料有哪些

难加工材料有哪些难加工材料是指那些在加工过程中难以获得理想加工表面质量和形状精度,以及难以获得较高的加工效率的材料。
这些材料通常具有高硬度、高强度、高熔点、高塑性变形抗力、高切削温度等特点。
难加工材料的加工难度主要表现在切削加工、磨削加工和电火花加工等方面。
下面将介绍一些常见的难加工材料。
1. 高硬度合金钢。
高硬度合金钢是一种具有较高硬度和强度的金属材料,通常用于制造刀具、模具等工具。
由于其硬度高,切削加工时易导致刀具磨损严重,加工表面质量难以保证。
2. 耐磨铸铁。
耐磨铸铁是一种具有较高硬度和耐磨性能的铸铁材料,常用于制造耐磨零件。
在磨削加工过程中,由于其硬度高、磨损性能好,磨削难度大,加工效率低。
3. 钛合金。
钛合金是一种具有优良的耐腐蚀性能和高强度重量比的金属材料,广泛应用于航空航天、航空发动机、航空航天器等领域。
由于其熔点高、塑性变形抗力大,切削加工难度大,易引起刀具磨损严重。
4. 陶瓷材料。
陶瓷材料具有优良的耐磨、耐腐蚀性能,常用于制造高温零部件、切削工具等。
然而,由于其脆性大、导热性差,磨削加工难度大,易导致加工表面裂纹和破损。
5. 难加工不锈钢。
难加工不锈钢是一种具有较高硬度和耐腐蚀性能的不锈钢材料,常用于制造化工设备、食品加工设备等。
由于其切削性能差,易导致刀具磨损,加工难度大。
6. 高硬度陶瓷。
高硬度陶瓷是一种具有极高硬度和耐磨性能的材料,常用于制造切削工具、轴承零件等。
然而,由于其脆性大、导热性差,磨削加工难度大,加工效率低。
综上所述,难加工材料主要包括高硬度合金钢、耐磨铸铁、钛合金、陶瓷材料、难加工不锈钢和高硬度陶瓷等。
这些材料在加工过程中具有较高的硬度、强度和耐磨性能,因此加工难度大,加工效率低。
针对这些材料的加工难题,需要采用合适的切削工艺、磨削工艺和电火花加工工艺,以提高加工质量和效率。
常用材料的切削加工性能

ZT:常用材料的切削加工性能parti良好的切削加工性能:1 )刀具的寿命较高,或在一定的寿命下允许的切削速度较高2)在相同的切削条件下,切削力较小3)切削温度较低,容易获得较细的表面粗糙度,容易控制切削形状或者断屑§5-1工件材料和切削的加工性本章从工工件材料方面本分析影响生产率及表面质量的因素,以及提高它们的途径:从生产实际中了解到,有些材料容易切削(生产率高,表面质量好),而另一些材料却很切削;分析工件材料的机械物理性能以及化学成分如何影响切削加性,如何提高工件材料的切削加工性。
材料的切削加工性是指导某种材料进行切削加工性的难易程度,其易程度,一般与材料的化学成份,热处理状态、金相组织、物理力学性能以及切削条件有关。
一、衡量切削加工的指标工件材料的切削加工性,通常用下面的一个或数个指标衡量:1、刀具耐用度;2、一定刀具耐用度允许的切削速度;3、切削力;4、切削温度;5、加工表面粗糙度或表面质量。
目前,常用一定刀具耐用度下充许的切削速度V T作为衡量指标。
V T__-指刀具耐用度为T时,切削某种材料的允许的切削速度。
V T越高,说明该材料的切削加工性能好。
任何事情都是相对而言,那么对于材料的切削加工性,也要用相对加工性Kr表示。
它的基准是以切削抗拉强度& b = 0.735Gpa的45#钢,耐用度T=60min时的切削速度Vb60为基准。
相对加工性就是以该基准与切削其它材料时V60的比值。
即Kr=V60 / Vb60①当Kr>1时,说明该材料比45#钢易切削;切削加工性好;②当Kr<1时,该材料比45#钢难切削,切削加工性能差。
常用材料切削加工性,根据相对加工性Kr的大小切分为八级,见表 5 —1。
二、改善材料可切削性的途经1、改善材料的化学成份。
1*在黄铜中加入1 %〜3%的铅,在钢中加入0 .1%〜0.2 5%的铅。
铅可以球状粒子存在于材料的金相组织中,切削时能起很好润滑作用,减少摩擦,使刀具耐用度和表面质量得提咼。
六组材料特性及切削力
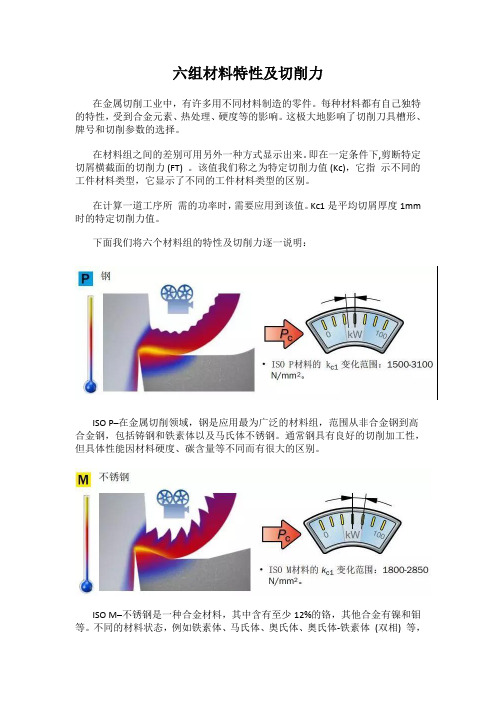
六组材料特性及切削力在金属切削工业中,有许多用不同材料制造的零件。
每种材料都有自己独特的特性,受到合金元素、热处理、硬度等的影响。
这极大地影响了切削刀具槽形、牌号和切削参数的选择。
在材料组之间的差别可用另外一种方式显示出来。
即在一定条件下,剪断特定切屑横截面的切削力 (FT) 。
该值我们称之为特定切削力值 (Kc),它指示不同的工件材料类型,它显示了不同的工件材料类型的区别。
在计算一道工序所需的功率时,需要应用到该值。
Kc1是平均切屑厚度1mm 时的特定切削力值。
下面我们将六个材料组的特性及切削力逐一说明:ISO P–在金属切削领域,钢是应用最为广泛的材料组,范围从非合金钢到高合金钢,包括铸钢和铁素体以及马氏体不锈钢。
通常钢具有良好的切削加工性,但具体性能因材料硬度、碳含量等不同而有很大的区别。
ISO M–不锈钢是一种合金材料,其中含有至少12%的铬,其他合金有镍和钼等。
不同的材料状态,例如铁素体、马氏体、奥氏体、奥氏体-铁素体(双相) 等,形成一个大的材料系列。
所有这类材料的共同点是,加工时切削刃会产生大量的热,易形成沟槽磨损和积屑瘤。
ISO K–与钢不同,铸铁是短切屑型材料。
灰口铸铁(GCI) 和可锻铸铁(MCI)非常容易加工,而球墨铸铁(NCI)、蠕墨铸铁(CGI) 和奥氏体铸铁(ADI) 就比较难加工。
所有铸铁都含有碳化硅(SiC),它会对切削刃造成严重磨损。
ISO S–耐热优质合金包括许多铁、镍、钴和钛基等高合金材料。
它们非常粘,极易形成积屑瘤,加工硬化严重,并产生大量的热量,非常类似于ISO M材料,但是更难以切削,导致切削刃的寿命更短。
ISO N–有色金属是软金属类型,例如铝、铜、黄铜等。
含硅(Si) 大于13%的铝合金对刀具具有非常强的磨料磨损性。
加工中通常应用具有锋利切削刃的刀片,一般可应用高切削速度并获得长刀具寿命。
ISO H–这一组包括硬度在HRc 45-65之间的钢材和硬度约为HB 400-600的冷硬铸铁。
为什么钛合金是一种难加工材料?

钛合金难加工原因钛合金热传导率低、加工硬化严重、与刀具的亲和性高、塑性变形小等4个特点是造成钛合金难以加工的本质原因。
其被切削指数只相当于易削钢的20%。
热传导率低钛合金热传导率大约只有45#钢的16%左右,加工中热量不能及时传导出去,造成切刃局部高温(加工中的刀尖温度是45#钢的1倍以上),容易引发刀具扩散磨损。
加工硬化严重钛合金加工硬化现象明显,表面硬化层相比不锈钢要严重,会给后续加工造成一定的困难,比如,刀具边界损伤增大。
与刀具的亲和性高与含钛的硬质合金粘结严重。
塑性变形小约为45钢的弹性模量的1/2,故弹性恢复大,摩擦严重。
同时,工件也容易发生装夹变形。
加工钛合金的工艺诀窍在理解钛合金加工机理的基础上,加上以往的经验,加工钛合金的主要工艺诀窍如下:(1)采用正角型几何形状的刀片,以减少切削力、切削热和工件的变形。
(2)保持恒定的进给以避免工件的硬化,在切削过程中刀具要始终处于进给状态,铣削时径向吃刀量ae应为半径的30%。
(3)采用高压大流量切削液,以保证加工过程的热稳定性,防止因温度过高导致工件表面变性和刀具损坏。
(4)保持刀片刃口锋利,钝的刀具是热集结和磨损的原因,容易导致刀具失效。
(5)尽可能在钛合金最软的状态加工,因为淬硬后材料变得更难加工,热处理提高了材料的强度并增加刀片的磨损。
(6)使用大的刀尖圆弧半径或倒角切入,尽可能把更多的刀刃进入切削。
这可以减少每一点的切削力和热量,防止局部破损。
在铣削钛合金时,各切削参数中切削速度对刀具寿命的影响最大,径向吃刀量(铣削深度)次之。
从刀片入手解决钛加工难题钛合金加工时出现的刀片沟槽磨损是后面和前面在沿切削深度方向上的局部磨损,它往往是由于前期加工留下的硬化层所造成的。
刀具与工件材料在加工温度超过800℃的化学反应和扩散,也是形成沟槽磨损的原因之一。
因为在加工过程中,工件的钛分子在刀片的前面积聚,在高压高温下“焊接”到刀刃上,形成积屑瘤。
难切削材料加工参数选择

1. 前角选择的原则:刀具材料的抗弯强度和韧性较高时,可选用大前角。
高速钢刀具的前角,在同样条件下,可比硬质合金刀具的前角大5-10°,而陶瓷的前角又要比硬质合金的小一些。
加工塑性材料宜选较大的前角,以减少金属变形和摩擦。
加工脆性材料时,应选5-15读的较小前角。
工件材料硬度、强度较低时,应选用较大前角,反之,选负前角或较小的正前角,以增强刀刃的强度和散热的体积。
粗加工取较小的前角,精加工取较大的前角,精密成型刀具取零度前角。
2. 倒棱选择原则:倒棱宽度和进给量有关。
倒棱宽度一般取(0.3~0.8)f 粗加工取大值。
进给量f<=0.2mm/r 的精加工刀具,不宜磨出负倒棱。
高速钢倒棱前角取-5~0°,硬质合金倒棱角去-15~-5。
另外也可以采用刃口钝圆形式代替倒棱,可以增强刃口强度,一般用于粗加工。
3. 后角选用原则:后角主要按照切削厚度来选择。
切削厚度小时,宜选用大后角,以减少刃口圆弧半径,使刃口锋利。
当f<=0.25mm/r 时,取后角为10~12°,反之,取后角为6~8°。
后角还依据材料强度和硬度选择,材料强度和硬度高,应取小的后角,相反则取大的后角,当工艺系统刚性差时,应选用小的后角或刃带宽=0.1mm~0.2mm,角度为0的刃带。
另外后角的选择与刀具的运动轨迹有关。
副后角选择原则与主后角相似。
4. 主偏角选择原则:在工艺系统和工艺要求允许的情况下,主偏角宜选的小一些。
工艺系统刚性好、切深小和工件硬度高时,如对冷硬铸铁和淬火钢的加工,取10~30°,工艺系统差可取75~93°。
粗加工时为了增加刀尖强度,改善散热条件,应取较小主偏角。
5. 副偏角的选择原则:在工艺系统刚性较好的情况下,副偏角不宜取得太大,精加工时取5~10°,粗加工时取10~15°。
切断刀或切槽刀为了增强刀头强度,取1~2°。
金属难加工材料切削及刀具磨损虚拟仿真报告(一)
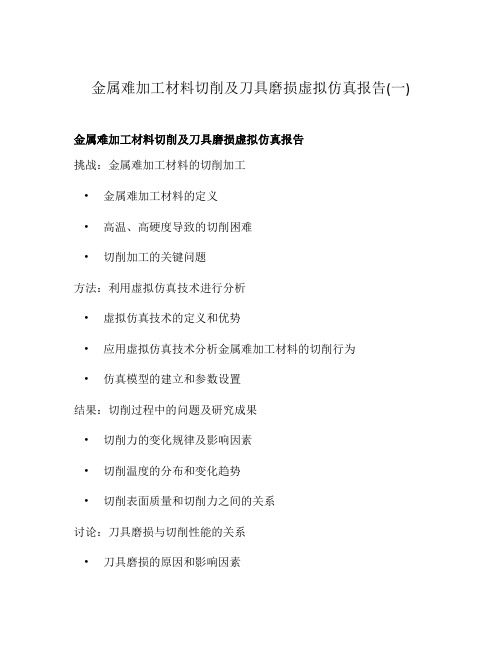
金属难加工材料切削及刀具磨损虚拟仿真报告(一)金属难加工材料切削及刀具磨损虚拟仿真报告挑战:金属难加工材料的切削加工•金属难加工材料的定义•高温、高硬度导致的切削困难•切削加工的关键问题方法:利用虚拟仿真技术进行分析•虚拟仿真技术的定义和优势•应用虚拟仿真技术分析金属难加工材料的切削行为•仿真模型的建立和参数设置结果:切削过程中的问题及研究成果•切削力的变化规律及影响因素•切削温度的分布和变化趋势•切削表面质量和切削力之间的关系讨论:刀具磨损与切削性能的关系•刀具磨损的原因和影响因素•切削力和刀具磨损的关系•如何通过优化切削参数延缓刀具磨损总结:虚拟仿真技术在切削加工中的应用前景•虚拟仿真技术的优势和局限性•未来发展方向和研究重点•为实际切削加工提供参考和决策依据金属难加工材料切削及刀具磨损虚拟仿真报告挑战:金属难加工材料的切削加工•金属难加工材料的定义–金属难加工材料是指具有高硬度、高强度和高耐磨性的金属材料,如钛合金、高速钢等。
•高温、高硬度导致的切削困难–由于金属难加工材料的硬度较高,切削时需要更大的切削力。
–高温会导致材料软化和脆性增加,使刀具损耗加剧。
•切削加工的关键问题–如何降低切削力和温度,提高切削效率和加工质量。
方法:利用虚拟仿真技术进行分析•虚拟仿真技术的定义和优势–虚拟仿真技术利用计算机模拟真实物理过程,可以减少实验成本、提高研究效率。
–通过虚拟仿真可以提前预测切削加工过程中的各种参数和结果。
•应用虚拟仿真技术分析金属难加工材料的切削行为–通过建立切削仿真模型,可以模拟金属难加工材料在切削过程中的变形、热力分布等行为。
–利用仿真结果可以分析切削力、切削温度和切削表面质量等参数的变化趋势。
•仿真模型的建立和参数设置–建立金属难加工材料的切削仿真模型。
–设置切削参数,如切削速度、进给速度和切削用量。
–调整模型和参数以获得准确的仿真结果。
结果:切削过程中的问题及研究成果•切削力的变化规律及影响因素–切削力随着切削速度的增加而增加,随着进给速度的增加先增加后减小。
不锈钢材料切削加工的难点分析与解决方法

…
…
一
不锈钢材料切 削加工 的难 点分析 与解 决方法
江 苏省 自动化研 究所 吴从好 于宏辉
【 摘要 】新产品的不断涌现对零件的材料提 出了更 高的要 求,所 需材 料有时必须满足高硬度、高耐磨性、 高韧性等特 殊要求 ,由此产生 了一批难加工材料 ,对 加
工工 艺提 出了更高的要求。本文 以不锈钢等难加 工材料为对象 ,结合我所加工遇到的实际问题,分析不锈钢 的加工难 点,并提 出了切实有效的解决方法。 【 关键词 】不锈钢 ;切削加工;加工方法
好 、 耐 磨 性 高 、与 不锈 钢 亲 和 作 用 小 的 工对 象 的 塑 性 变 形 , 也 能 够 降低 切 削 温 与 优 质 碳 素 结 构 钢 相 比 ,不 锈 钢 材 特 点 。 度 和 切 削力 , 同时减 少 硬 化层 的 产生 。 料 加 入 了c 、N 、N N 、M 等 合 金 元 r i 、 b o 3 1 1高速 钢 .. 2 )后 角 n : 增 加 后 角 将 减 小 加 工 素 。这 些 合 金 元 素 的增 加 , 不 仅 提 高 了 高速 钢 是 加 入w o C 、V 0 、M 、 r 、G 等 表 面 与后 刀 面 的摩 擦 , 但 切 削 刃 的散 热 钢 的耐 蚀 性 ,对 不 锈 钢 的 机 械 性 能 也有 合 金 元 素 的 高 合 金 工 具 钢 ,具 有 较 好 的 能 力 和 强 度 也 随 之 降 低 。 后 角 的大 小 取 定 影 响 。 如 马 氏体 不锈 钢 4 r 3 5 C 1 与4 号 工 艺 性 能 ,强 度 和 韧 性 配 合 好 ,抗 冲 击 决 于 切 削 厚 度 ,切 削 厚 度 大 时 , 宜 选 较 中碳 钢 相 比 ,具 有 相 同 的 含 碳 量 ,但 相 振 动 的 能 力 较 强 。在 高 速 切 削产 生 高 热 小后 角 。
钛合金薄壁腰形深窄槽数控铣削加工方法

01序言钛合金强度高、密度小、耐热性好,同时还具有较高的疲劳寿命和优良的耐腐蚀性能,是航空发动机风扇、压气机、轮盘和叶片等重要零部件的首选材料。
钛合金材料的切削加工性能只有普通钢的20%~30%[1],是一种典型的难切削材料。
一种新型钛合金航空发动机薄壁复杂扩压器机匣需要加工16个宽约9.2mm、深54.5mm、弧长约80mm 的深槽(见图1),相邻两处腰形槽最小壁厚约2.2mm。
鉴于深窄槽结构的特殊性,加工时只能选用直径小、悬伸长的铣刀,切削加工时易产生振刀、崩刃现象,同时刀尖冷却效果差、排屑难,切削温度高,产生让刀和表面加工硬化现象,存在切削效率低、刀具寿命短以及尺寸难以加工合格等问题,是目前加工制造中的难题之一。
图1薄壁扩压器深槽结构示意02工艺方案试验腰形深窄槽数量多,材料去除量大,加工时须保证较高的加工效率,经过分析,排除摆线铣和动态铣加工方案,制定了插铣法和分层铣削法两种主要加工方案,两种方案都先采用⎫8mm钻头钻通,然后用⎫8mm合金铣刀进行铣削,根据铣削方式、切削参数的不同,分别进行工艺试验。
2.1插铣法试验插铣法,又称为Z轴铣削法,是实现高切除率金属切削的最有效加工方法之一。
其加工原理是:刀具沿轴向连续地上下进刀,主要作用力为轴向切削力,大大降低了作用于机床的径向切削力,即使刀具悬伸长度较大,仍具有较高的加工刚性,能够减小零件变形,保证加工稳定性[2]。
插铣法的加工效率远高于常规的端面铣削方法。
试验中虽然缺少专用的插铣刀,但是鉴于插铣法在深槽加工方面的优势,采用普通合金铣刀对腰形槽进行了插铣加工工艺试验,其切削参数和试验效果见表1。
表1插铣切削参数和试验效果分析表1可知,切削宽度较大时,效率高,但加工振动大,刀具易崩断;减小切削宽度后,效率有所降低,刀具磨损较快,同时零件振动较大,存在一定的质量和安全隐患。
由于该零件为新型号研制件,工艺准备条件有限,本次工艺试验采用了组合夹具和普通铣刀,零件装夹刚度一般,且机匣最小壁厚仅为2.1mm,插铣过程中易振刀,同时普通合金铣刀插铣加工寿命低,最终导致了插铣加工试验效果不够理想。
- 1、下载文档前请自行甄别文档内容的完整性,平台不提供额外的编辑、内容补充、找答案等附加服务。
- 2、"仅部分预览"的文档,不可在线预览部分如存在完整性等问题,可反馈申请退款(可完整预览的文档不适用该条件!)。
- 3、如文档侵犯您的权益,请联系客服反馈,我们会尽快为您处理(人工客服工作时间:9:00-18:30)。
难切削材料(不锈钢、钛合金、高温合金及淬火高硬钢)的切削难题。
悬赏分:0 - 共有0个答案 - 已经结束
一、瑞士FRAISA高速切削刀具——解决难切削材料(不锈钢、钛合金、高温合金及淬火高硬钢)的切削难题。
FRAISA是瑞士著名的刀具厂商,专业研发设计生产高速钢、硬质合金的高速铣刀、高速超硬钻咀、高速丝攻、螺纹检具以及整体硬质合金工具等; 瑞士fraisa高速切削铣刀能为客户:提高切削效率,解决切削难题,优化切削方案,降低加工成本。
◆具有耐高温、耐磨损、耐黏附、高精度的fraisa切削刀具特别适用于 20000-60000 转的高速切削加工。
为客户在高速切削中拥有更高的表面光洁度及精度,减少许多的后续加工,为高效率、高精度、高品质的加工提供更多的帮助。
◆独特的unicut-CELLERO自润滑铜铝涂层兼具优良的耐磨度及提高高粘性材料加工速度,铝件薄壁可加工至0.1mm,完成出色完美的高速切削铜铝及非铁金属材料。
◆ DURO-S超硬涂层的耐磨损性及高度的热稳定性可高速铣削难切削硬度高达HRC70度以下淬硬钢材料。
◆特有的TRIBO-N涂层拥有极高的耐粘性,非常适合于高速切削钛合金、镍合金及强韧的不锈钢。
◆ DIAMANT石墨涂层有极高的耐磨性专用于长寿命高速切削石墨炭晶加工;
◆ MICRO超小径涂层20倍D直径的超长颈细小刀具,直径0.2mm可高速切削HRC25-62度高硬度金属材料及非铁金属材料。
◆最新开发的POLYCHROM涂层有极高的耐磨性耐热性专用于长寿命高速切削各种模具材料加工。
瑞士FRAISA还采用非常先进的刀具涂层和制造设计工艺。
并在高要求的各金属加工行业中广泛应用,如:航天航空,汽车制造,模具和电子等制造行业得到了全球金属加工业的认可采购。
-诚征各省市区域分销商,面向同行经销商批发销售。
二、德国ELEMENT高效精密铣刀
德国ELEMENT是著名的精密铣刀品牌,专业针对各种模具金属材料加工的各类型刀具,刀具规格齐全:平底铣刀,球头铣刀,圆鼻铣刀,深沟长颈型铣刀,微小径铣刀等各种类型的铣刀,并有为适合加工各种不同有色金属,特别针对压铸铝、镁合金材料而设计的多种刀具可供选择,可满足客户的各种加工需求。
注:德国ELEMENT--诚征中国地区各工业省市区域代理或区域分销商。
欢迎您的来电洽谈合作:
达海精密刀具有限公司
电话:+86-769 8788 2889 8791 7998
传真:+86-769 8791 1920 8794 1165
电邮:dahaimj@
网站:/ ; QQ: 1034944410 800020131。