难加工材料
机械行业难加工材料与结构的加工技术(ppt 80页)

外型面难加工结构件主要有:薄壁件、叶片、涡轮盘 、微小微细零件外型面及其它特殊复杂的型面。
内型面难加工结构主要有:蜂窝结构、阵列孔、有特 殊要求的小孔、窄缝及其它特殊复杂的形腔结构。
南京航空航天大学机电学院052系
难加工材料的加工技术
南京航空航天大学机电学院052系
难加工材料与结构概述-分类
(4)低温性能好 钛合金在低温和超低温下能保 持力学性能。
(5)化学活性大 钛的化学活性大,与大气中的 O2、N2、H2、CO、CO2、水蒸气、氨气等均产 生剧烈的化学反应。
(6)导热性差 钛的导热系数低,约为Ni的1/4, Fe的1/5,Al的1/14
(1)钛合金具有密度小、强度高、能耐各种酸、碱、 海水、大气等介质的腐蚀等一系列优良的力学、物理 性能,因此在航空、航天、核能、船舶、化工、冶金 、医疗器械等工业中得到了越来越广泛的应用。
南京航空航天大学机电学院052系
难加工材料与结构概述-应用
1.钛合金
记忆钛合金镜架
钛合金刀具
南京航空航天大学机电学院052系
2.主要内容:
1)难加工材料
1)难加工材料的分类
2)难加工材料的应用
2) 难加工结构
南京航空航天大学机电学院052系
难加工材料与结构概述-分类
1.钛合金 2.高温合金 3.不锈钢 4.高强度钢与超高强度钢 5.复合材料 6.硬脆性材料
南京航空航天大学机电学院052系
难加工材料与结构概述-应用
2.高温合金
低膨胀、恒弹性、高弹 性高温合金
精密合金高温合金不锈钢棒
南京航空航天大学机电学院052系
难加工材料有哪些

难加工材料有哪些难加工材料是指那些在加工过程中难以获得理想加工表面质量和形状精度,以及难以获得较高的加工效率的材料。
这些材料通常具有高硬度、高强度、高熔点、高塑性变形抗力、高切削温度等特点。
难加工材料的加工难度主要表现在切削加工、磨削加工和电火花加工等方面。
下面将介绍一些常见的难加工材料。
1. 高硬度合金钢。
高硬度合金钢是一种具有较高硬度和强度的金属材料,通常用于制造刀具、模具等工具。
由于其硬度高,切削加工时易导致刀具磨损严重,加工表面质量难以保证。
2. 耐磨铸铁。
耐磨铸铁是一种具有较高硬度和耐磨性能的铸铁材料,常用于制造耐磨零件。
在磨削加工过程中,由于其硬度高、磨损性能好,磨削难度大,加工效率低。
3. 钛合金。
钛合金是一种具有优良的耐腐蚀性能和高强度重量比的金属材料,广泛应用于航空航天、航空发动机、航空航天器等领域。
由于其熔点高、塑性变形抗力大,切削加工难度大,易引起刀具磨损严重。
4. 陶瓷材料。
陶瓷材料具有优良的耐磨、耐腐蚀性能,常用于制造高温零部件、切削工具等。
然而,由于其脆性大、导热性差,磨削加工难度大,易导致加工表面裂纹和破损。
5. 难加工不锈钢。
难加工不锈钢是一种具有较高硬度和耐腐蚀性能的不锈钢材料,常用于制造化工设备、食品加工设备等。
由于其切削性能差,易导致刀具磨损,加工难度大。
6. 高硬度陶瓷。
高硬度陶瓷是一种具有极高硬度和耐磨性能的材料,常用于制造切削工具、轴承零件等。
然而,由于其脆性大、导热性差,磨削加工难度大,加工效率低。
综上所述,难加工材料主要包括高硬度合金钢、耐磨铸铁、钛合金、陶瓷材料、难加工不锈钢和高硬度陶瓷等。
这些材料在加工过程中具有较高的硬度、强度和耐磨性能,因此加工难度大,加工效率低。
针对这些材料的加工难题,需要采用合适的切削工艺、磨削工艺和电火花加工工艺,以提高加工质量和效率。
难加工材料的主要种类及应用领域
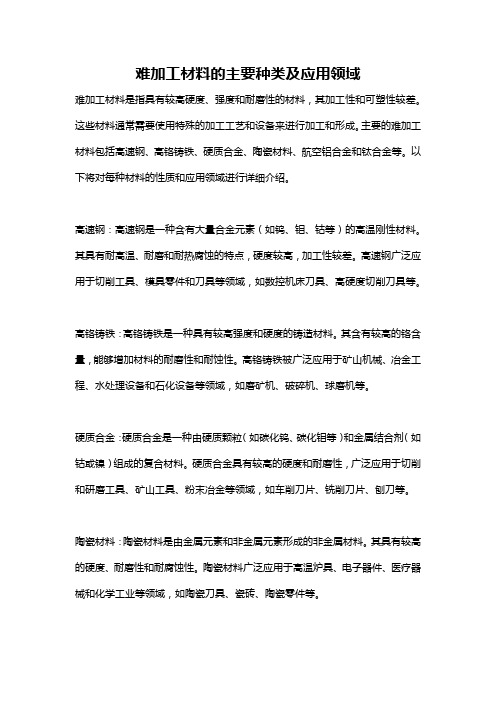
难加工材料的主要种类及应用领域难加工材料是指具有较高硬度、强度和耐磨性的材料,其加工性和可塑性较差。
这些材料通常需要使用特殊的加工工艺和设备来进行加工和形成。
主要的难加工材料包括高速钢、高铬铸铁、硬质合金、陶瓷材料、航空铝合金和钛合金等。
以下将对每种材料的性质和应用领域进行详细介绍。
高速钢:高速钢是一种含有大量合金元素(如钨、钼、钴等)的高温刚性材料。
其具有耐高温、耐磨和耐热腐蚀的特点,硬度较高,加工性较差。
高速钢广泛应用于切削工具、模具零件和刀具等领域,如数控机床刀具、高硬度切削刀具等。
高铬铸铁:高铬铸铁是一种具有较高强度和硬度的铸造材料。
其含有较高的铬含量,能够增加材料的耐磨性和耐蚀性。
高铬铸铁被广泛应用于矿山机械、冶金工程、水处理设备和石化设备等领域,如磨矿机、破碎机、球磨机等。
硬质合金:硬质合金是一种由硬质颗粒(如碳化钨、碳化钼等)和金属结合剂(如钴或镍)组成的复合材料。
硬质合金具有较高的硬度和耐磨性,广泛应用于切削和研磨工具、矿山工具、粉末冶金等领域,如车削刀片、铣削刀片、刨刀等。
陶瓷材料:陶瓷材料是由金属元素和非金属元素形成的非金属材料。
其具有较高的硬度、耐磨性和耐腐蚀性。
陶瓷材料广泛应用于高温炉具、电子器件、医疗器械和化学工业等领域,如陶瓷刀具、瓷砖、陶瓷零件等。
航空铝合金:航空铝合金是一种具有良好强度和轻质的金属材料。
其具有较高的硬度和耐磨性,加工难度较大。
航空铝合金广泛应用于航空航天工业和汽车工业的结构部件,如飞机主机壳、发动机部件、汽车车身等。
钛合金:钛合金是一种具有较高强度和轻质的金属材料。
其具有较高的硬度、耐腐蚀性和耐高温性,加工性较差。
钛合金被广泛应用于航空航天工业、化工设备和医疗器械等领域,如航空发动机零部件、化工反应容器、人工关节等。
综上所述,难加工材料主要包括高速钢、高铬铸铁、硬质合金、陶瓷材料、航空铝合金和钛合金等。
这些材料具有较高的硬度、强度和耐磨性,但加工性较差。
刀片材质分类

涂层CVD用途材质/ISO用分类代号特征P钢 T9005/ P05 - P10 钢加工用材质。
P钢 T9015/ P10 - P20 通过双桥效果可实现良好的覆盖抗剥落性。
采用专用基P钢 T9025/P20 - P30 及4种材质系列可应用到钢材车削加工的所有领域。
P钢 T9035/P30 - P40 T9005:在高速切削等要求耐磨损性的领域内,能发挥良好性能。
T9015:耐磨损性和抗崩刃性的平衡性合宽范围的切削条件。
T9025:在轻型~中等断续切削中,发挥良好的抗崩刃性。
T9035:具有极高抗崩刃性,更适用于强断续切削。
M不锈钢 T6020/M15 – M25 不锈钢加工用材质。
M不锈钢 T6030/M25 – M35 采用专用基体和高致密性涂层的组合,大幅度提高了抗极度磨损性和抗崩刃性。
T6020:适用中速~高速领域,连续~轻型断续切削。
T6030:适用低速~中速领域,有极高抗崩刃性,连续~断续切削。
K铸铁 T5104/K05 – K15 铸铁、球墨铸铁材质。
K铸铁 T5115/K10 – K20 涂层采用比以往更精细更高硬度的柱状晶体Ti(K铸铁 T5125/K15 – K30 C,N)膜,大幅度提高了耐磨损性。
并且通过和高强度K铸铁 T5010/K05 –K15 专用微粒硬质合金基体的组合,使T5100系列3种材K铸铁 T5020/K10 – K25 质在FC.FCD车削加工的广泛领域内实现了卓越的性能。
T5105:可在高速,连续切削中发挥良好的耐磨损性和抗塑性变形性。
T5115:从连续切削到连断续,断续切削的广泛领域中,可实现稳定加工的通用材质。
T5125:适合强断续切削,较为强韧,很难出现突发性崩刃。
车螺纹专用 T313V 车螺纹专用。
采用抗塑性变形优良的基体和高致密性涂层的组合,可实现较高的加工面粗糙度和尺寸精度。
用途材质/ISO用分类代号特征P钢 T3030/P20 – P40 钢,不锈钢加工用材质。
难加工材料

难加工材料材料加工是指对原料进行加工改造,使其达到设计要求的一系列工艺。
在材料加工中,有些材料由于其特殊的性质,使得加工变得困难,需要采取一些特殊的加工方法。
下面就为大家介绍几种难加工材料及其加工方法。
首先,难加工材料之一是高温合金。
高温合金由于其高熔点和高硬度,使得加工变得困难。
在加工高温合金时,常用的加工方法包括电火花加工、激光加工和超音波加工等。
电火花加工是利用电火花放电腐蚀工件表面,使其形成所需轮廓的一种加工方法。
激光加工则是利用激光束将工件表面的材料熔融并挥发,从而获得所需形状。
超音波加工是利用超音波振动工具切割工件表面的一种加工方法。
其次,还有难加工材料是复合材料。
复合材料由于其由不同性质的材料组合而成,使得加工变得困难。
在加工复合材料时,常用的加工方法包括研磨加工、射出成型和压制成型等。
研磨加工是利用砂轮或研磨片对工件表面进行切削磨削的一种加工方法。
射出成型是将熔融的复合材料通过射出机加热喷射到模具中,并经冷却固化得到所需形状。
压制成型则是利用压力将熔融的复合材料填充到模具中,经冷却固化得到所需形状。
最后,还有难加工材料是硬质合金。
硬质合金由于其高硬度和脆性,使得加工变得困难。
在加工硬质合金时,常用的加工方法包括电火花加工、磨削加工和激光加工等。
电火花加工能够在硬质合金表面形成一层陶瓷膜,从而减小工件和工具的接触面积,降低切削力,从而使得加工更容易进行。
磨削加工则是利用砂轮或研磨片对硬质合金表面进行切削磨削的一种加工方法。
激光加工则是利用激光束将硬质合金表面的材料熔融并挥发,从而实现加工目的。
综上所述,对于难加工材料,我们需要结合其特殊性质采取相应的加工方法。
这些方法中包括电火花加工、激光加工、超音波加工、研磨加工、射出成型和压制成型等。
这些方法能够较好地克服难加工材料的特点,实现高质量、高效率的加工过程。
典型难加工零件工艺分析及编程
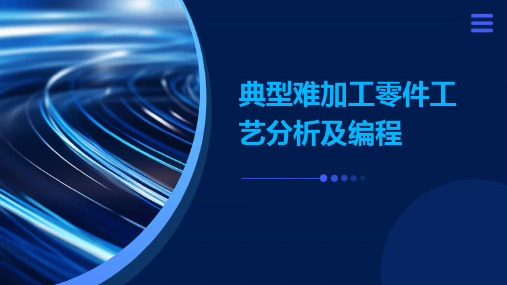
绿色制造的推广
要点一
环保材料
采用环保材料,如可回收材料、低毒材料等,减少对环境 的污染。
要点二
节能技术
采用节能技术,如高效加工技术、能源回收技术等,降低 能源消耗和排放。
THANKS
感谢观看
工艺分析的方法
工艺流程规划
根据零件的结构和加工要求,规划合理的加工流 程和顺序。
刀具与夹具选择
根据加工要求和零件结构,选择合适的刀具和夹 具,确保加工过程的稳定性和精度。
ABCD
加工参数确定
根据材料特性、刀具性能和加工条件,选择合适 的切削速度、进给速度和切削深度等参数。
工艺风险评估
对工艺流程和参数进行风险评估,确保加工过程 的安全性和可靠性。
编程技巧的应用
总结词
运用有效的编程技巧可以提高程序的可读性和执行效率。
详细描述
使用条件语句、循环语句和子程序等结构化编程技巧,可以简化复杂的加工过程。同时,利用优化算法和并行处 理技术可以提高程序的运行速度。
数控编程软件的使用
总结词
熟练掌握数控编程软件是实现高效编程的关键。
详细描述
常用的数控编程软件包括Mastercam、Fusion 360和SolidWorks等。这些软件提供了丰富的库函数 和工具,可以帮助程序员快速生成准确的数控代码。此外,程序员还需要了解如何设置工件坐标系、 选择合适的加工策略和刀具路径优化等技术。
降低生产成本
准确的工艺分析有助于减少 材料浪费、降低能耗和减少 刀具磨损,从而降低生产成 本。
提高产品质量
合理的工艺安排和参数选择 有助于减小加工误差,提高 零件的精度和一致性,从而 提高产品质量。
保障生产安全
正确的工艺分析可以避免因 不合理的加工方法和参数导 致的设备故障或生产事故, 保障生产安全。
工件切削加工性
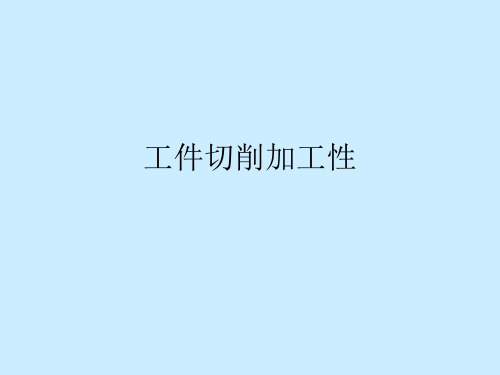
刃和刀尖的强度,一般取γ。=-4—0º,主偏角kr适当减小,刀
尖圆弧半径rε适当加大。
淬硬钢的组织为回火马氏体,硬度达HRC60以上,塑性
和导热系数都很低。其加工性及刀具材料、刀具几何参数的 选择基本上与冷硬铸铁同。对它们进行精加工,可采用CBN 刀具。
κr= 45° ~ 75°、λs= -10 °
6.钛合金切削加工性分析
1).钛合金特点和分类
a)密度小(约为 4.5g / cm3 ),比钢约小一倍。
b)强度极限高(可达σb=0.981~1.37GPa), 钛合金的比强度(单位重量强度)很高,尤其在高温下比强度仍 很高,这一点对航空、航天工业尤为重要。
工件切削加工性
表 7– 1 材料可加工性分级
分级
名称及种类
Kv
1 很容易切削材料 一般有色金属
> 3.0
2
易切削钢
容易切削材料
3
较易切削钢
2.5 ~ 3.0 1.6 ~ 2.5
4
一般钢及铸铁
1.0 ~ 1.6
普通材料
5
稍难切削材料 0.65 ~ 1.0
6
较难切削材料 0.5 ~ 0.65
7
难切削材料
理 ;对镍基高温合金可采用固溶处理(淬火)
b)、首选一足够的vc以保证加工质量,再选f 、ap
c)、选择合适的刀具材料和角度 连续切:YG6X、YW1 断续切:M42、501、B201
高速钢刀具:γo=15 ° ~20°、αo=12 ° 、κr=45 ° 硬质合金刀具:γo=5° ~ 10°、αo= 8° ~ 15° 、
在自动机床或自动生产线上,常常以切屑
难加工材料

加工高温合金、不锈钢材料时,刀具切削用量的选用一、高温合金的切削特点1.性能特征高温合金是一种多组元、激活能很高的高熔点,金属元素含量很多的复杂合金化材料。
有极好的热稳定性及热强性。
热稳定是高温下抗氧化、抗腐蚀的能力。
热强性是指高温下抵抗塑性变形和断裂的能力。
如以45号钢的切削加工性为100%,则高温合金的相对切削加工性为5%—20%。
可以说高温合金是各种各种难加工材料中最难切削的材料。
2.切削特点⑴切削力大:由于高温合金出众的高熔点、激活能大的组元,原子结合十分稳定。
切削时要使其原子脱离平衡位置,所需的能量很大,变形抗力大大上升。
合金中沉淀的硬化相对会增大塑性变形抗力,而塑性变形抗力使晶格严重扭曲,硬度大大提高,使变形抗力加大。
所以切削高温合金时,切削力比一般钢大2-3倍。
⑵切削温度高:由于切削时巨大的塑性变形,刀具与工件,切屑之间存在着强烈的摩擦,产生大量的切削热。
高温合金的导热系数很低,致使变形区的切削热高度集中于极小的切削区域内,使刀具切削刃及刀尖处的温度非常高。
在高温下会加剧刀具的扩散磨损和氧化磨损。
⑶加工硬化现象严重:高温中,高温合金的强化系数大,并且在切削过程中,合金中的强化相从固液中分解出来,弥散分布,使强化能力增加,加大了硬化程度。
切削高温合金时,已加工表面硬度要比基体硬度高的多约50%—100%。
⑷刀具易磨损:由于高温合金中的各种强化相和加工硬化现象,在切削过程中给刀具造成了巨大的摩擦,发生磨料磨损。
在高温高压条件下,刀具材料与被加工材料之间的亲和作用而造成粘附,使切屑与刀具之间出现粘结现象,造成粘结磨损。
在切削高温合金时,刀具除出现一般的正常磨损外,还会出现边界磨损及沟纹磨损。
主要原因是加工过程中高温合金的加工硬化所造成。
3.刀具的选用根据前面的了解,高温合金的切削加工性的确很差,导致刀具的耐用度低。
因此,应当寻求各种提高刀具的耐用度的措施。
⑴从刀具材料的选择着手:切削高温合金的刀具,要具备有高温硬度,高的耐磨性,强度和冲击韧性,良好的导热性,抗粘性及抗氧化性。
- 1、下载文档前请自行甄别文档内容的完整性,平台不提供额外的编辑、内容补充、找答案等附加服务。
- 2、"仅部分预览"的文档,不可在线预览部分如存在完整性等问题,可反馈申请退款(可完整预览的文档不适用该条件!)。
- 3、如文档侵犯您的权益,请联系客服反馈,我们会尽快为您处理(人工客服工作时间:9:00-18:30)。
摘要:阐述了难加工材料的特点,重点介绍了对难加工材料进行车削加工时应采取的措施,列举了几种不同材料车削时应选取的参数。
引言
在压缩机的生产过程中,经常会接触到一些难加工的材料,如制造压缩机叶轮的材
料有一种含有Cr、Ni、Mo等合金元素的高强度结构钢,这种钢材一经调质处理达
到一定的硬度时,很难车削。
钦合金叶轮因为钦合金元素的存在给车削带来诸多麻
烦,大型硬齿面齿轮,渗碳淬火的过程会造成一些需要加工的表面过硬而难以车削
加工;还有一些运输机械常用紫铜等纯金属制造的套类零件也给车削带来相当大的
麻烦。
为了解决这些难加工材料的车削加工问题,需要对难加工材料的特性有足够
的了解,然后采取有针对性的措施才能予以解决。
1 难加工材料的加工特点
1.何谓难加工材料
所谓难加工材料,主要是指切削加工性能差的材料。
金属材料切削加工性的好坏,
主要是从切削时的刀具耐用度、已加工表面的质量及切屑形成和排除的难易程度3
个方面来衡量。
只要上述这3个方面有一项明显的差,就可认为是难加工材料。
常
见的难加工材料有高强度钢、不锈钢、高温合金、钦合金、高锰钢和纯金属(如紫铜)
等。
2.难加工材料的切削特点
a.车削温度:在切削难加工材料时,切削温度一般都比较高,主要原因有以下
两方面。
i.导热系数低:难加工材料的导热系数一般都比较低(纯金属紫铜等除
外),在切削时切削热不易传散,而且易集中在刀尖处。
ii.热强度高:如镍基合金等高温合金在500一800℃时抗拉强度达到最高值。
因此在车削这类合金时,车刀的车削速度不宜过高,一般不宜超过10m/min,否则刀具切人工件的切削阻力将会增大。
b.切削变形系数和加工硬化:难加工材料中的高温合金和不锈钢等,这些材料
的变形系数都比较大。
在较小的切削速度开始,变形系数就随着车削速度的增大而增大,在切削速度大约达到6m/min的情况下,切屑的变形系数将达到最大值。
由于车削过程中形成切屑时的塑性变形,金属产生硬化和强化,使切削阻力增大,刀具磨损加快,甚至产生崩刃。
如高温合金、高锰钢和奥氏体不锈钢奥氏体组织,其硬化的严重程度和深度都很大,要比4 5钢大好几倍。
难加工材料由于硬化程度严重,切屑的温度和硬度高,韧性好,以及切削温度高(强韧切屑),如果这样的切屑流经前刀面,就容易产生粘结和熔焊等粘刀现象,粘刀不利于切屑的排除,使容屑糟堵塞,容易造成打刀。
粘刀还容易使刀具产生粘结磨损和崩刃。
另外,强韧的切屑呈锯齿形,容易损坏刀具刃口。
c.切削力:难加工材料一般强度较高,尤其是高温强度要比一般钢材大得多,
再加上塑性变形大和加工硬化程度严重,因此车削难加工材料的切削力一般都比车削普通碳钢时大得多。
d.磨损限度与耐用度:由于难加工材料的温度高、热强度高、塑性大、切削温
度高和加工硬化严重,有些材料还有较强的化学亲和力和粘刀现象,所以车刀的磨损速度也较快。
车削硬化现象严重的材料,车刀后刀面的磨损限度值不宜过大。
硬质合金车刀粗车时的磨损限度为0.9~1.0mm ,精车为0.4~0.6mm 。
难加工材料的刀具耐用度对于不锈钢而言为90~150min。
对高温合金和钦合金等材料来说,刀具的耐用度时间还要短。
车刀的耐用度与选择合理的车削速度和车刀材料及车刀类型都有一定的关系。
2 车削时应采取的措施
1.选择刀具材料
车削难加工材料,应根据材料的特性来选择合理的切削性能好的刀具材料。
如对于
高温状态下硬度较高的材料的车削应选择硬度和高温硬度均较好的含钻高速钢以及
钨钻类及钨钻钦类通用硬质合金。
对于钦合金材料及含钦不锈钢材料的车削应避开
对钨钻钦类硬质合金的使用。
2.选择合理的车刀几何参数
如对硬度低、塑性好的材料应采用较大的前角和后角;对于高温合金材料应采用较大
的刃倾角。
3.选用合适的切削液
用高速钢车削高温合金一般选用水溶性切削液;用硬质合金车刀车削时则应选用油
类极压切削液,如极压乳化液、硫化乳化油、氯化煤油等均可作为难加工材料的切
削液。
4.选择合理的车削用量
车削速度的选择主要受刀具耐用度的限制,而刀具耐用度又取决于刀具的磨损情况。
总的来说,由于难加工材料的切削抗力大、车削时温度易升高和热强度高等特点。
车削速度、进给量和走刀量等切削用量的值都应比车削普通钢材适当减小。
3 几种难加工材料的车削加工
1.高锰奥氏体钢的车削
高锰奥氏体钢的主要难加工特点:加工硬化程度严重、导热性差、切削温度高、冲
击韧性高和延伸率较大。
因此,切削这类材料应采用强度和韧性均较好的硬质合金。
刀具的前角一般较小(-5°~5°);后角应大些,一般为12°~18°;主偏角为45°~60°;
刃倾角一般在-5°左右。
为了降低硬化程度,刃口应磨得锋利些,车削速度一般在2
0m/min左右。
2.高强度钢的车削
车削高强度钢,由于切削力大,容易引起硬质合金刀齿的崩刃,一般多采用YT14、
YG6等牌号的硬质合金。
刀具的前角一般在-5°~20°;刃倾角为~10°左右为宜;主偏
角为45°~60°,车削速度为30~45m/min,并随工件材料硬度的提高,车削速度应
降低,最低车削速度在10m/min左右为宜;进给量在0.5~1mm/r为宜。
3.不锈钢的车削
由于不锈钢塑性好且加工硬化严重,车削时冲击和振动较严重,切屑不易卷曲和折
断。
因此,要求机床、夹具和刀具系统的刚性要好。
用硬质合金车刀,应采用YG
类通用性硬质合金。
硬质合金车刀的前角为5°~10°,前角上可磨出圆弧卷屑槽,
前角还可以适当加大,但刀刃上应留有0.05~0.20mm的刃带;后角应在5°一10°为
宜;还应该采用60°的主偏角和5°~10°的刃倾角。
采用硬质合金刀具的切削速度为1
00~150m/min,进给速度为30~100mm/min。
4.高温合金的车削
高温合金切削的主要特点:硬化严重、容易粘刀、导热性差和高温强度高。
因此应
该选择耐高温、高温硬度高和高温强度高的硬质合金刀具。
刀刃要锋利,后角要大
些并用正前角,并有一定的刃倾角,以利于切屑的排出。
车削速度不宜太高,一般
在20~50m/min,进给量在0.3~0.5mm/r为宜。
5.钛合金的车削
钛合金切削的主要特点:钛合金主要的化学成分是金属钛,在切削过程中与碳化钛
的亲和力强,易产生粘结,导热性差,其他特点与不锈钢比较接近。
应当选用钨钻
类硬质合金车刀车削,车刀前角要小,一般为0°~5°,后角为4°~10°,主偏角为
45°~75°,刀尖圆弧半径为0.5~1mm ,切削速度为15~55m/min,切削时应大量
使用切削液,最好是采用极压乳化液。
6.紫铜的车削
车削紫铜的车刀,其材料以高速钢为主,也可以采用钨钻类硬质合金。
紫铜塑性大、
切削变形大、易粘刀,因此车刀的刃口一定要锋利,前刀面最好为大圆弧卷屑槽,
前后刀面表面粗糙度精度要高,高速钢车刀前角要大,一般为20°~35°,后角为1
0°~25°,主偏角为45°~90°,副偏角也要大些,要用钨钻类硬质合金车刀前角应
略小些。
选用的切削速度应大,可在50~100m/min,若用硬质合金车刀,切削速
度可达200m/min,切削时可选用润滑性好的极压乳化液,充分冲注,以提高表面
粗糙度精度。