海上油气田基本腐蚀机理及其影响因素讲解
海上油气田CO2/H2S腐蚀控制

溶解的 ls H ・ l/(gL ) 2 -
图 1 H S的 不 同溶 解 度 对碳 钢 腐 蚀 的 影 响 :
12 2 溶解 氧 的影 响 ..
的溶解 盐类 。在质 量浓 度低 的情 况下 , 这些 盐类 不
油气 田采 出水 中含 有 的氧一 般 由注入水 携带 。
和海底集输管道腐蚀 , 造成泵漏 、 管漏、 杆管断脱和 井下 工具 密封失 效 等 事 故 , 生 产 带来 极 大 危 害 , 给
且造 成重 大经济 损失 。
1 海 上油气 田腐 蚀现 状分 析 1 1 溶解盐 类 的影响 .
化学腐蚀产生氢 , 氢原子向钢铁 内部渗透 , 从而导 致 氢损伤 , 在很 低 的 拉 应力 下 就 可 能发 生 破 裂 , 因 此在 H s 腐蚀严重地区, 抽油杆断裂会更频繁。
张 强 李家锋 孙爱平
( 中国海洋石油能 源发展股 份有 限公 司 , 广东 湛江 54 5 ) 20 7
摘要: 根据 中国海 洋石油 南海 西部各油 气田的 实际情 况 , 结合水质特 点分析 了采 油平 台、 输油管 道、 水处理 系统和生产 管汇腐蚀的原 因以及影响 因素。阐述 了海上油气田腐蚀 机理 , 出了海上油气 提
田 开 采 的 防腐 蚀 措 施 。
关键词 : 海上油气 田
水质
C2 o 腐蚀
C :H S O / : 腐蚀
影 响因素
防护方法
中图分类号 :G 7 . T 126
文献标识码: A
文章编号 :17- 1X[0 0 0 00 0 10 05 2 1 )2- 0 1— 6 3
随着海上 油气 田注水 开 发 的深 入 , 大部 分地 区 进 入高 含水开 发期 , 由于其 水 质 矿 化 度较 高 、 蚀 腐 介 质质量 浓度 大 和注 海 水均 会 导 致 油 井 井 下设 备
海上油气田生产工艺系统内腐蚀控制及效果评价要求-概念解析以及定义

海上油气田生产工艺系统内腐蚀控制及效果评价要求-概述说明以及解释1.引言1.1 概述概述海上油气田生产工艺系统内的腐蚀控制是保证油气生产工艺系统正常运行和延长设备寿命的重要措施之一。
随着我国深海油气勘探和开发的不断深入,油气生产工艺系统内腐蚀控制的研究和实践显得尤为重要。
在海上油气田开发过程中,由于水分、氧气、电位和温度等因素的影响,生产工艺系统内普遍存在着腐蚀问题。
腐蚀不仅会导致设备损坏和效能下降,还可能造成环境污染和安全事故。
因此,加强对海上油气田生产工艺系统内腐蚀控制的研究,制定相应的评价要求和技术规范,具有重要的理论和实践意义。
本文首先介绍了海上油气田生产工艺系统内腐蚀控制的重要性,并概述了腐蚀控制方法的研究现状。
其次,本文详细探讨了海上油气田生产工艺系统内腐蚀控制方法,包括物理控制、化学控制和电化学控制等方面。
最后,本文提出了腐蚀控制的效果评价要求,以便对腐蚀控制方法的有效性进行评价和改进。
综上所述,海上油气田生产工艺系统内腐蚀控制及其效果评价要求的研究对于确保油气生产工艺系统的正常运行和设备的安全稳定具有重要意义。
通过本文的研究,有望为海上油气田的腐蚀控制提供理论指导和技术支持。
1.2文章结构2. 正文2.1 腐蚀控制的重要性2.2 海上油气田生产工艺系统内腐蚀控制方法2.3 腐蚀控制的效果评价要求在本文的第一章引言中,我们已经对海上油气田生产工艺系统内腐蚀控制及效果评价要求的主题进行了概述和目的的介绍。
在本章节中,我们将详细探讨海上油气田生产工艺系统内腐蚀控制及效果评价要求的具体内容。
本节将首先分析腐蚀控制的重要性。
海上油气田的生产工艺系统常常受到海水、盐雾、高温、高压等恶劣环境的侵蚀,腐蚀现象会对系统的安全运行和产能造成重大影响。
因此,有效的腐蚀控制至关重要。
我们将深入探讨腐蚀控制的原理和方法,包括物理措施、化学措施以及材料选择等方面的内容。
接下来,我们将介绍海上油气田生产工艺系统内腐蚀控制的具体方法。
油气田的腐蚀与防护 ppt课件

(a)
(b)
图2.1 P110试样表面腐蚀产物膜结构和特征。(a)呈现蜂窝状腐 蚀,(b)口小底大烧瓶型
ppt课件
16
5. 温度对二氧化碳腐蚀机理的影响
低温,腐蚀产物膜 中 温 , 100oC 左 右 ,高 温 , 约 大 于
少,均匀腐蚀
膜局部破裂,局部 150oC , 膜 致 密 ,
ppt课件
13
3.二氧化碳腐蚀常见形态
– 国际研究普遍认为:
CO2局部腐蚀有以下三种典型机理 – 台地状腐蚀 – 蜗旋状腐蚀 – 点状腐蚀 – 我们研究发现,腐蚀后试样表面呈现为图2.1所示的蜂窝状和 底 大口小的烧瓶型点状腐蚀
ppt课件
14
ppt课件
15
4.微观腐蚀形态
(a)
闭塞电池效应很强:外大阴极,
(1-1)
ppt课件
10
几种典型腐蚀介质的腐蚀速率对比图
ppt课件
11
三 二氧化碳腐蚀简介
1. 反应机理: 阳极反应机理 Fe=Fe2+ +2e
Fe + HCO3-=FeCO3 +2e+H+ Fe+CO32-=FeCO3 +2e 也有认为初始腐蚀产物为Fe(OH)2,或Fe(HCO3)2 Cr+ 3OH- =Cr(OH)3+ 3e
» —— 高温和/或高压环境
» —— H2S、CO2、O2、Cl-和水分是主要腐蚀物质
» H2S、CO2、O2 是 腐蚀剂
» 水
是 载体
» Cl-
是 催化剂
– 就H2S、CO2和O2三种腐蚀剂来说,其腐蚀速率相对
油田注水系统腐蚀原因及对策
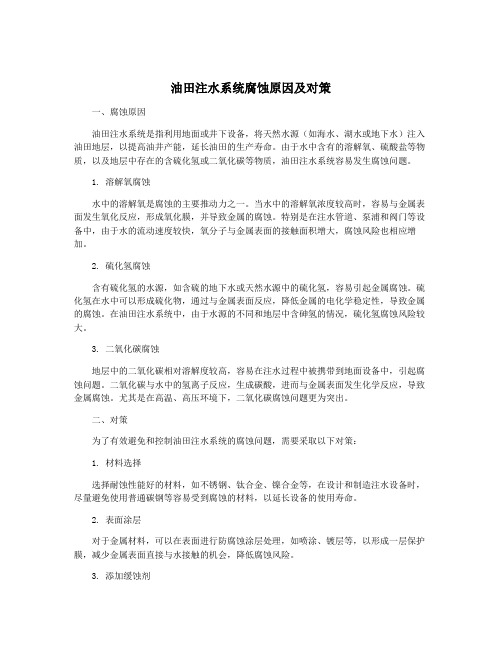
油田注水系统腐蚀原因及对策一、腐蚀原因油田注水系统是指利用地面或井下设备,将天然水源(如海水、湖水或地下水)注入油田地层,以提高油井产能,延长油田的生产寿命。
由于水中含有的溶解氧、硫酸盐等物质,以及地层中存在的含硫化氢或二氧化碳等物质,油田注水系统容易发生腐蚀问题。
1. 溶解氧腐蚀水中的溶解氧是腐蚀的主要推动力之一。
当水中的溶解氧浓度较高时,容易与金属表面发生氧化反应,形成氧化膜,并导致金属的腐蚀。
特别是在注水管道、泵浦和阀门等设备中,由于水的流动速度较快,氧分子与金属表面的接触面积增大,腐蚀风险也相应增加。
2. 硫化氢腐蚀含有硫化氢的水源,如含硫的地下水或天然水源中的硫化氢,容易引起金属腐蚀。
硫化氢在水中可以形成硫化物,通过与金属表面反应,降低金属的电化学稳定性,导致金属的腐蚀。
在油田注水系统中,由于水源的不同和地层中含砷氢的情况,硫化氢腐蚀风险较大。
3. 二氧化碳腐蚀地层中的二氧化碳相对溶解度较高,容易在注水过程中被携带到地面设备中,引起腐蚀问题。
二氧化碳与水中的氢离子反应,生成碳酸,进而与金属表面发生化学反应,导致金属腐蚀。
尤其是在高温、高压环境下,二氧化碳腐蚀问题更为突出。
二、对策为了有效避免和控制油田注水系统的腐蚀问题,需要采取以下对策:1. 材料选择选择耐蚀性能好的材料,如不锈钢、钛合金、镍合金等,在设计和制造注水设备时,尽量避免使用普通碳钢等容易受到腐蚀的材料,以延长设备的使用寿命。
2. 表面涂层对于金属材料,可以在表面进行防腐蚀涂层处理,如喷涂、镀层等,以形成一层保护膜,减少金属表面直接与水接触的机会,降低腐蚀风险。
3. 添加缓蚀剂在注水系统中添加合适的缓蚀剂,可以有效减少腐蚀的发生。
缓蚀剂可以形成一层保护膜,阻断金属与水接触,减缓腐蚀的速度。
4. 控制水质定期监测和改善注水水源的水质,合理控制含氧量、硫化氢含量、二氧化碳含量等指标,降低腐蚀的风险。
5. 优化运行合理设计注水系统的运行参数,如流速、压力等,避免过高的流速和压力对金属构件造成冲刷和损伤,降低腐蚀风险。
海洋油气管道腐蚀的影响及对策

海洋油气管道腐蚀的影响及对策目录一、内容概述 (2)1.1 海洋油气管道的重要性 (3)1.2 管道腐蚀问题的严峻性 (4)二、海洋油气管道腐蚀的主要影响因素 (4)2.1 自然环境因素 (5)2.1.1 水文条件 (7)2.1.2 气候条件 (7)2.1.3 地质条件 (8)2.2 人为因素 (9)2.2.1 管道材料选择 (10)2.2.2 管道施工质量 (11)2.2.3 管道维护管理 (12)2.3 设备与工艺因素 (13)2.3.2 管道工艺 (16)三、海洋油气管道腐蚀的主要影响 (17)3.1 对管道结构的影响 (19)3.2 对管道安全性的影响 (20)3.3 对周边环境的影响 (21)四、海洋油气管道腐蚀的对策 (22)4.1 加强管道材料选择与研发 (23)4.2 提高管道施工质量 (24)4.3 完善管道维护管理体系 (25)4.4 优化管道设备与工艺设计 (26)五、案例分析 (27)5.1 某海洋油气田管道腐蚀案例分析 (29)5.2 防腐对策在案例中的应用与效果 (30)六、结论与展望 (31)6.2 对未来研究的展望 (33)一、内容概述本文档深入探讨了海洋油气管道腐蚀的严重后果及其应对策略,旨在为海洋工程领域提供关于管道腐蚀问题的全面理解,并为防止和减轻腐蚀提供实用的建议。
在当今全球能源需求不断增长的大背景下,海洋油气管道作为连接海上油气资源与陆地加工厂的重要通道,其作用日益凸显。
海洋环境的复杂性和油气管道长期运营所面临的多种挑战,使得管道腐蚀问题成为威胁管道安全、影响原油生产的关键因素。
腐蚀不仅导致管道材料性能下降,还可能引起管道结构的破坏,进而引发泄漏事故,造成环境污染和经济损失。
系统研究海洋油气管道的腐蚀情况,评估腐蚀风险,并采取有效的防护措施,对于保障石油工业的可持续发展具有重要意义。
本文档将详细分析海洋油气管道腐蚀的影响,包括对管道结构、原油运输安全以及环境保护等方面的影响。
油田集输管线的腐蚀原因及防腐对策

油田集输管线的腐蚀原因及防腐对策油田集输管线是将油井注入的原油和天然气输送至处理场或加工厂的管道系统。
由于长时间暴露在高温、高压和含有腐蚀性物质的环境下,油田集输管线容易发生腐蚀。
腐蚀是指金属材料与环境中的化学物质产生物理或化学反应导致其性能的损失,进而影响管线的安全运行。
造成油田集输管线腐蚀的主要原因有以下几种:1. 氧化腐蚀:当管线内的金属表面暴露在氧气中时,金属表面会氧化,进而起到腐蚀的作用。
2. 硫化物腐蚀:油田集输管线中的环境中往往存在硫化物,当管线表面与硫化物接触时,会引发硫化物腐蚀,加速金属表面的腐蚀速度。
3. 酸性腐蚀:油田集输管线中的部分油井中含有酸性物质,如硫酸和盐酸等,当这些物质接触到金属表面时,会加速腐蚀过程。
为了解决油田集输管线腐蚀带来的安全隐患,需要采取相应的防腐对策。
以下是几种常用的防腐对策:1. 表面涂覆防腐剂:通过对油田集输管线进行外部涂覆防腐,可使金属管道表面与外部环境隔绝,减少与腐蚀物质的接触,从而延缓腐蚀过程。
2. 阴极保护:在油田集输管线中通过向管道施加负电位,使其成为阴极,从而减少金属管道表面的电子流动,降低金属的电化学反应,延缓腐蚀速度。
3. 油田环境监测:及时对油田集输管线周围的环境进行监测,了解环境中的腐蚀性物质浓度和变化情况,及时采取相应的措施进行防腐。
4. 材料选择:选择耐腐蚀性能好的金属材料作为油田集输管线的构造材料,如钢材中的耐腐蚀不锈钢等。
5. 定期检测和维护:对油田集输管线进行定期的内外部检测和维护,发现腐蚀问题及时修复,可防止腐蚀扩散,延长管线的使用寿命。
油田集输管线腐蚀的原因主要包括氧化腐蚀、硫化物腐蚀和酸性腐蚀等,采取的对策包括表面涂覆防腐剂、阴极保护、油田环境监测、材料选择以及定期检测和维护。
这些对策可以有效地减缓油田集输管线的腐蚀速度,保障管线的安全运行。
油田注水系统腐蚀原因及对策

油田注水系统腐蚀原因及对策随着全球能源需求的不断增长,油田开采工作也越来越受到关注。
在油田开采过程中,为了提高产量和延长油井寿命,经常需要进行注水作业。
油田注水系统在使用过程中常常会出现腐蚀现象,这给油田注水系统的正常运行带来了很大的困扰。
本文将从腐蚀原因和对策两方面来探讨油田注水系统腐蚀问题,并提出相应的解决方案。
一、腐蚀原因1. 水中杂质:油田注水系统中的水中往往含有各种杂质,如氯离子、硫酸盐等,这些杂质会直接影响到金属材料的腐蚀速度。
特别是在海水注水系统中,盐分的存在更会加剧金属材料的腐蚀。
2. 流体速度:注水系统中的流体速度对金属材料的腐蚀也有很大的影响。
如果流速过大,会导致流体中的氧气对金属表面产生氧化反应,从而加速金属腐蚀的速度。
3. 温度:油田注水系统中的温度变化也会对金属材料的腐蚀产生影响。
当温度过高时,金属表面的保护膜容易失效,使金属材料更容易受到腐蚀。
4. 金属选择:在注水系统中使用的金属材料选择也会直接影响腐蚀的程度。
不同的金属对不同的腐蚀环境的适应能力不同,要根据实际情况选择合适的金属材料。
二、对策1. 优化水质:注水前需要对水质进行充分净化处理,尽量降低水中的杂质含量,可以采用逆渗透、离子交换等方法进行水质处理,从源头上减少腐蚀的可能性。
2. 控制流速:控制注水系统中的流体速度,避免过高的流速导致金属材料腐蚀加速。
可以通过调节管道尺寸、增加阀门等方式来降低流速。
3. 温度控制:加强对注水系统中的温度变化进行监测和控制,避免过高温度导致金属腐蚀。
可以通过安装冷却装置或者保温材料来控制温度。
5. 防腐涂层:对于容易发生腐蚀的金属部件,可以采用防腐涂层来延长其使用寿命,如喷涂耐蚀涂料、电镀防腐层等。
6. 定期检测:对注水系统中的金属部件进行定期检测,及时发现腐蚀现象,及时进行维护和更换,以保证系统的正常运行。
油田注水系统的腐蚀问题是一个复杂的系统工程问题,需要结合水质处理、流速控制、温度控制、金属保护等多种手段来解决。
浅析油田集输管线的腐蚀原因及防腐措施
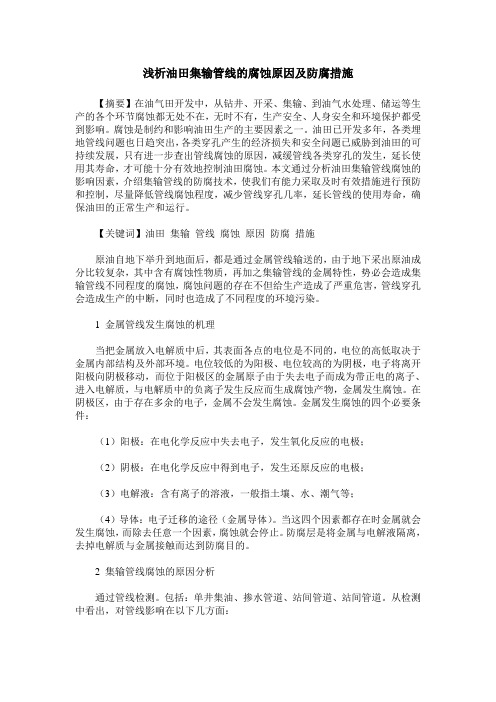
浅析油田集输管线的腐蚀原因及防腐措施【摘要】在油气田开发中,从钻井、开采、集输、到油气水处理、储运等生产的各个环节腐蚀都无处不在,无时不有,生产安全、人身安全和环境保护都受到影响。
腐蚀是制约和影响油田生产的主要因素之一。
油田已开发多年,各类埋地管线问题也日趋突出,各类穿孔产生的经济损失和安全问题已威胁到油田的可持续发展,只有进一步查出管线腐蚀的原因,减缓管线各类穿孔的发生,延长使用其寿命,才可能十分有效地控制油田腐蚀。
本文通过分析油田集输管线腐蚀的影响因素,介绍集输管线的防腐技术,使我们有能力采取及时有效措施进行预防和控制,尽量降低管线腐蚀程度,减少管线穿孔几率,延长管线的使用寿命,确保油田的正常生产和运行。
【关键词】油田集输管线腐蚀原因防腐措施原油自地下举升到地面后,都是通过金属管线输送的,由于地下采出原油成分比较复杂,其中含有腐蚀性物质,再加之集输管线的金属特性,势必会造成集输管线不同程度的腐蚀,腐蚀问题的存在不但给生产造成了严重危害,管线穿孔会造成生产的中断,同时也造成了不同程度的环境污染。
1 金属管线发生腐蚀的机理当把金属放入电解质中后,其表面各点的电位是不同的,电位的高低取决于金属内部结构及外部环境。
电位较低的为阳极、电位较高的为阴极,电子将离开阳极向阴极移动,而位于阳极区的金属原子由于失去电子而成为带正电的离子、进入电解质,与电解质中的负离子发生反应而生成腐蚀产物,金属发生腐蚀。
在阴极区,由于存在多余的电子,金属不会发生腐蚀。
金属发生腐蚀的四个必要条件:(1)阳极:在电化学反应中失去电子,发生氧化反应的电极;(2)阴极:在电化学反应中得到电子,发生还原反应的电极;(3)电解液:含有离子的溶液,一般指土壤、水、潮气等;(4)导体:电子迁移的途径(金属导体)。
当这四个因素都存在时金属就会发生腐蚀,而除去任意一个因素,腐蚀就会停止。
防腐层是将金属与电解液隔离,去掉电解质与金属接触而达到防腐目的。
- 1、下载文档前请自行甄别文档内容的完整性,平台不提供额外的编辑、内容补充、找答案等附加服务。
- 2、"仅部分预览"的文档,不可在线预览部分如存在完整性等问题,可反馈申请退款(可完整预览的文档不适用该条件!)。
- 3、如文档侵犯您的权益,请联系客服反馈,我们会尽快为您处理(人工客服工作时间:9:00-18:30)。
第二节海上油气田基本腐蚀机理及其影响因素一、二氧化碳腐蚀机理多年来,二氧化碳的腐蚀机理一直是研究的热点。
干燥的CO2气体本身是没有腐蚀性的。
CO2较容易溶解在水中,而在碳氢化合物(如原油)中的溶解度则更高,气体CO2与碳氢化合物的体积比可以达到3比1。
当CO2溶解在水中时,会促进钢铁发生电化学腐蚀。
根据CO2腐蚀的不同腐蚀破坏形态,能提出不同的腐蚀机理。
以CO2对钢铁和含铬钢的腐蚀为例,有全面腐蚀,也有局部腐蚀。
根据介质温度的不同,腐蚀的发生可以分为三类:在温度较低时,主要发生金属的活泼溶解,对碳钢主要发生金属的溶解,为全面腐蚀,而对于含铬钢可以形成腐蚀产物膜;在中间温度区间,两种金属由于腐蚀产物在金属表面的不均匀分布,主要发生局部腐蚀,如点蚀等;在高温时,无论碳钢和含铬钢,腐蚀产物可以较好地沉淀在金属表面,从而抑制金属的腐蚀。
1 二氧化碳全面腐蚀机理铁在CO2水溶液中的腐蚀基本过程的阳极反应为:Fe +OH-FeOH + eFeOH FeOH++ eFeOH+Fe2++ OH-亦即铁的阳极氧化过程G.Schmitt等的研究结果表明在腐蚀阴极主要有以下两种反应。
(下标ad代表吸附在钢铁表面上的物质,sol代表溶液中的物质)1.1非催化的氢离子阴极还原反应当PH < 4时H3O+ + e Had + H2OH2CO3H++ HCO3-HCO3-H++ CO32-当4<PH <6时H2CO3+ e Had + HCO3-当PH>6时2HCO3- +2e H2+ 2CO32-1.2表面吸附CO2,ad的氢离子催化还原反应CO2,sol CO2,adCO2,ad + H2O H2CO3,adH2CO3,ad + e + HCO3-,adH3O+ad + e Had + H2OH2CO3,ad + H3O+2CO3,ad + H2O两种阴极反应的实质都是由于CO2溶解后形成的HCO3-电离出的H+的还原过程。
总的腐蚀反应为:CO2+ H2O + Fe FeCO3+ H2O金属材料在CO2水溶液中的腐蚀,从本质上说是一种电化学腐蚀,符合一本的电化学腐蚀特征。
2 二氧化碳局部腐蚀机理二氧化碳的局部腐蚀现象主要包括点蚀、台地侵蚀、流动诱导局部腐蚀等等。
二氧化碳的腐蚀破坏往往是由局部腐蚀造成的,然而对局部腐蚀机理仍然缺少深入的研究。
总的来将,在含CO2的介质中,腐蚀产物FeCO3、垢CaCO3或其他的生成物膜在钢铁表面不同的区域覆盖度不同,这样,不同覆盖度的区域之间形成了具有很强自催化特性的腐蚀电偶或闭塞电池。
CO2的局部腐蚀就是这种腐蚀电偶作用的结果。
这一机理能够很好地解释电化学作用在发生及扩展过程中所起的作用。
2.1介质中H2S的含量对二氧化碳腐蚀的影响H2S、CO2是油气工业中主要的腐蚀性气体。
在无二氧化碳(sweet gas)油气介质中也难免存在少量硫化氢。
钢材设备上,硫化氢可形成FeS膜,引起局部腐蚀,导致氢鼓泡、硫化物应力腐蚀开裂(SSCC),并能和CO2共同引起应力腐蚀开裂(SCC)。
不同浓度的硫化氢对CO2的影响如表所示,其中H2S对CO2腐蚀的影响可以分为三类。
第一类:环境温度较低(60℃左右),H2S浓度低于3.3mg.kg-1,H2S通过加速腐蚀的阴极反应而加速腐蚀的进行。
第二类,温度在100℃左右,H2S浓度超过33mg.kg-1时,局部腐蚀降低但是均匀腐蚀速度增加。
当温度在150℃附近时,发生第三类腐蚀,金属表面会形成FeCO3或FeS保护膜,从而抑制腐蚀的进行。
表1-7不同浓度的H2S对CO2腐蚀的影响< 3.3< 33< 3302.2介质中O2的含量O2与CO2共存于水中会引起严重的腐蚀。
O2还是铁腐蚀反应中的主要阳极去极化剂之一,此外,O2在二氧化碳腐蚀的催化机制中起到了重大作用:当钢铁表面未生成保护膜时,O2含量的增加,使得碳钢腐蚀速率增加;如果在钢铁表面生成保护膜,则O2的存在几乎不会影响碳钢的腐蚀速率,因为此时CO2的存在也将会大大提高钢铁的腐蚀速率,因为此时CO2在腐蚀中起到催化剂的作用。
2.3介质水的含量无论在气相还是在液相中,CO2腐蚀的发生都离不开水对钢铁表面的浸湿作用。
因此,水在介质中的含量是影响CO2腐蚀的一个重要因素.当然,这种腐蚀和介质的流速以及流动状态密切相关.当有表面活性物质存在(如,油田注水过程中都会直接加入表面活性物质或加入强碱与油中和生成表面活性物质),油水混合介质在流动过程中会形成乳化液。
一般来说,当水中的含量小于30%(质量)时,会形成油包水(水/油)乳化液,水包含在油中,这时水对钢铁表面的浸湿将会受到抑制,发生二氧化碳腐蚀的倾向较小;当水的含量大于40%(质量)时,会形成水包油(油/水)乳液,油包含在水中,这时水相对钢铁表面发生浸湿而引起CO2腐蚀。
所以,30%(质量)的含水量是判断是否发生CO2腐蚀的一个经验判断。
相对来说这是一个不十分严格的标准,只有油水两相能形成乳液时方可采用。
随着含水量的增大,CO 2的腐蚀速度增大。
在含水率为45%(质量)左右,CO 2的腐蚀速度出现一个突越,这可能是因为介质从油包水乳化液向水包油乳化液转变的缘故。
2.4介质温度大量的研究结果显示,温度是CO 2腐蚀的重要参数;且很多研究结果表明:在60℃附近CO 2腐蚀在动力学上有质的变化。
FeCO 3溶解度具有负的温度系数,溶解度随温度升高而降低,即反常溶解现象。
因此在60~110℃之间,铁表面可能形成具有一定性的腐蚀产物—碳酸亚铁FeCO 3膜,使腐蚀速度出现过渡区,该温区内局部腐蚀较突出。
而低于60℃,材料表面不能形成保护性膜,钢的腐蚀速率出现一个极大值(含Mn 钢在40℃附近,含Cr 钢在60℃附近)。
在110℃或更高的温度范围,可以发生下列反应:3Fe + 4H 2O = Fe 3O 4 + 4H 2因而在110℃附近显示出钢的第二个腐蚀速率极大值。
表面产物层也由FeCO 3变成厚而疏松的无保护性的杂有Fe 3O 4的FeCO 3膜,并且随温度升高Fe 3O 4量增加甚至在膜中占主导地位。
对于含铬钢,在高温时主要转变为铬的氧化物。
根据温度对腐蚀的影响,铁的CO 2腐蚀可以分为以下四种情况(1) T<60℃,腐蚀产物为FeCO 3,软而无附着力,金属表面光滑,主要发生均匀腐蚀;(2) 60~110℃,钢铁表面可以生成具有一定保护性的腐蚀产物膜,局部腐蚀较突出;(3) 在110℃附近,均匀腐蚀速度高,局部腐蚀严重(深孔),腐蚀产物为厚而疏松的FeCO 3粗结晶;(4) 150℃以上,生成细致、紧密、附着力强的FeCO 3和Fe 3O 4膜,腐蚀速率较低。
上述讨论表明,温度是通过化学反应和腐蚀产物特征来影响钢的腐蚀行为,钢种的不同和环境介质参数的差异都会对腐蚀的温度规律产生影响,故需根据具体分析研究对象,才能得到有实际意义的结果。
2.5二氧化碳分压当温度低于60℃时,二氧化碳分压(2CO P )对碳钢和低合金钢腐蚀速率的影响可用Ward 等提出的经验公式表达:lg Vc = 0.67lg 2CO P + C式中Vc 为腐蚀速率,单位为mm.a -1; 2CO P 单位取Mpa ; C 为与T 有关常数。
该式表明钢的腐蚀速率随2CO P 增加而增大。
在2CO P <0.2Mpa 、T<60℃且介质为层流状态时,由于腐蚀产物的影响,计算结果往往高于实测值。
因此该式只能用来估计没有膜的裸钢的最大腐蚀速度。
此外,该式不能反映出流动状态、合金元素等对腐蚀速率有重要影响的事实,从而限制了它的实际应用范围。
在一般情况下,由于CO 2不是一种理想的气体,常采用逸度f 来表示CO 2的真实分压P f = kP其中:k 为逸度系数。
由于k 的可变性,而且CO 2在水溶液中的溶解度也会受到溶液中离子强度的影响而发生变化,式中0.67也不是固定不变的。
N80钢在模拟轮南油田回注污水介质中腐蚀速度(Vc ,mm.a -1)和二氧化碳的分压(Pco 2,Mpa )的对数也呈线性关系,如下所示:lg Vc = 1.0058lg 2CO P —0.4095二氧化碳分压在判断CO 2腐蚀中起着重要的作用。
DNV 于1981年颁布的TNB111认为,当油气的相对湿度大于50%,二氧化碳超过1Mpa 、O 2分压超过100Pa 、H 2S 分压超过1Mpa 时,油气具有腐蚀性。
目前在油气工业中根据CO 2分压判断CO2腐蚀性的规律如下:表1-8在油气工业中CO2分压如此重要,那么如何确定油气工业设备中的二氧化碳分压呢?一般可以采用以下的计算方法:输油管线中CO 2分压 = 井口回压 × CO 2百分含量井口二氧化碳分压 = 井口油压 × CO 2百分含量井下CO 2分压 = 饱和压力(或流压)× CO 2百分含量2.6介质的pH 值pH 值的变化直接影响H 2CO 3在水溶液中的存在形式。
当pH 值小于4时,主要以H 2CO 3形式存在;当pH 值在4~10之间,主要以HCO 3-形式存在;当pH 值大于10时,主要以CO 32-存在。
一般来说,pH 值的增大,使H +含量减少,降低了原子氢还原反应速度,从而降低了腐蚀速度。
裸钢在pH 值低于3.8的含CO 2除O 2的水中,腐蚀速率随PH 降低而增加,表明此时CO 2对腐蚀的影响主要体现在pH 对腐蚀的影响。
这是因为钢铁在酸性介质中的腐蚀,主要是以氢离子为去极化剂的电化学反应,腐蚀速率受氢离子还原的阴极过程控制。
当pH 介于4~6之间时,电化学试验证明,在相同的pH 值情况下,裸钢在CO 2饱和溶液中的阴极电流密度高于N 2饱和的具有相同pH 值的阴极电流密度,即裸钢在CO 2饱和溶液中的腐蚀速率高于在不含CO 2的相同pH 溶液中的情况。
这表明CO 2对腐蚀的影响不仅体现在pH 值对腐蚀的影响,也体现在对裸钢CO 2腐蚀的催化作用。
pH 值不仅是2CO P 和T 的函数,也与水中Fe 2+及其他离子浓度有关。
在除O 2的水中,若无Fe 2+等离子,CO 2溶于水后可使pH 值显著降低,有很强腐蚀性。
在同样2CO P 与T 条件下,Fe 2+浓度增加30mg/L ,就使水的pH 从3.9增加到5.1。
这个作用相当于改变2CO P 几个大气压的效果。
pH 值升高会影响FeCO 3的溶解度,随着pH 值的增大,FeCO 3的溶解度降低。
因此,在局部高pH 的情况下,接近钢表面的Fe 2+便沉积为FeCO 3膜,从而引发了腐蚀的不均匀性。
pH 值的变化,也直接影响金属材料在含CO 2介质中腐蚀产物的形态、腐蚀电位等。