第6章拉深工艺与拉深模具
合集下载
凸缘矩形件的拉深工艺分析与模具设计

定了落料拉 深复合成 形的工 艺方案 ,缩短 了复 杂零件成 形模具 “ 试错”的过程 ,减 少了对设 计经验 的依 赖程度 ,提高 了模 具设计的准 确性和可 靠性 ,对 同类 零件的冲压 模具设计 具有 一 定的参考价值。介绍了模具结构及工作过程 ,对设计注意事项进行了分析 、归纳和总结 。 关键词 :凸缘矩形件 ;D Y N A F O R M;落料拉深复合成形 ;模具结构 中图分类号 :T G3 8 6 . 2 ;T G3 8 5 . 2 文献标识码 :B 文章编号 :1 0 0 9 — 0 1 3 4 ( 2 0 1 3 ) 0 3 ( 上) 一 0 0 3 8 —0 3
式 来 应 用 , 采 用 传 统 的 方 法 来 设 计 该 产 品 的 模
1 拉深 工艺分析
矩 形 件 是 一种 非 轴 对称 的零 件 , 它 的筒 壁 是
由直 边 部 分 和 圆 角部 分 构 成 ,拉 深 变 形 时 应 力 、 应 变 在 变 形 区 内沿 周边 的分 布 很 不 均 匀 ,因 而 在 拉深 过程 中变 形过 程较 为 复杂n 】 。 如图l 所 示 零件 属 于矩 形 件 的一种 类 型 ,但 是 和大 多数 设 计 参 考 资 料 上 所提 供 的矩 形 件 又 有 较 大 区别 。该 零 件 不 属 于 直 壁 式矩 形 件 , 同时 还 带 有 凸缘 , 因 此该 零 件 的 拉 深 工艺 比一 般 的矩 形 件
D o i : 1 0 . 3 9 6 9 / J . i s s n . 1 0 0 9 -0 1 3 4 . 2 0 1 3 . 0 3 (E) . 1 2
0 引言
如 图1 所 示 零 件是 某 家 电产 品上 的结 构件 ,材 料 采 用DC 0 3 冷轧 板 ,厚 度 1 n l l l l 。该结 构件 虽 然尺 寸精 度要求不高 ( I T1 a m ),但 是 属于 较 复 杂 的 拉 深件 , 成 形 过程 中存 在起 皱 、破 裂 的可 能 性 , 在 确 定 毛 坯 的 形 状 和 尺 寸 时 ,缺 少恰 当 的经 验 公
拉伸工艺及拉伸模具设计

凹模洞口的最大拉应力和凸缘最外边的最大压应力。 2.筒壁传力区的受力分析
(1)压边力 引起的摩擦力
FQ 该摩擦应力为:
M
2uFQ
dt
18
(2)材料流过凹模圆角半径产生弯曲变形的阻力 可
根据弯曲时内力和外力所作功相等的条件按下式计算:
W
1 4
b
rd
t t
2
(3)材料流过凹模圆角后又被拉直成筒壁的反向弯
ቤተ መጻሕፍቲ ባይዱ曲力仍按式上式进行计算:
'W
W
1 4
b
rd
t t
2
拉深初期凸模圆角处的弯曲应力也按上式计算,即:
''W
1 4
b
rp
t t
2
19
(4)材料流过凹模圆角时的摩擦阻力 通讨凸模圆角处危险断面传递的径向拉应力即为:
p
1max
M
2 w
'' w
eμα
p
1.1 m
ln
Rt r
2FQ dt
b
t 2rd t
侧壁上变成了间距相等的垂线,如图4.1.3所示,以前的扇形 毛坯网格变成了拉深后的矩形网格。
9
10
11
4.1.2拉深过程中变形毛坯各部分的应力与应变状态
拉深过程中某一瞬时毛坯变形和应力情况(如图4.1.5)
1.平面凸缘部分
主要变形区
2.凹模圆角区
过渡区
3.筒壁部分
传力区
4.凸模圆角部分
过渡区
5.圆筒底部分
有凸缘筒形件的拉深系数
m d
1
D (dt / d ) 4h / d 3.44r / d
(1)压边力 引起的摩擦力
FQ 该摩擦应力为:
M
2uFQ
dt
18
(2)材料流过凹模圆角半径产生弯曲变形的阻力 可
根据弯曲时内力和外力所作功相等的条件按下式计算:
W
1 4
b
rd
t t
2
(3)材料流过凹模圆角后又被拉直成筒壁的反向弯
ቤተ መጻሕፍቲ ባይዱ曲力仍按式上式进行计算:
'W
W
1 4
b
rd
t t
2
拉深初期凸模圆角处的弯曲应力也按上式计算,即:
''W
1 4
b
rp
t t
2
19
(4)材料流过凹模圆角时的摩擦阻力 通讨凸模圆角处危险断面传递的径向拉应力即为:
p
1max
M
2 w
'' w
eμα
p
1.1 m
ln
Rt r
2FQ dt
b
t 2rd t
侧壁上变成了间距相等的垂线,如图4.1.3所示,以前的扇形 毛坯网格变成了拉深后的矩形网格。
9
10
11
4.1.2拉深过程中变形毛坯各部分的应力与应变状态
拉深过程中某一瞬时毛坯变形和应力情况(如图4.1.5)
1.平面凸缘部分
主要变形区
2.凹模圆角区
过渡区
3.筒壁部分
传力区
4.凸模圆角部分
过渡区
5.圆筒底部分
有凸缘筒形件的拉深系数
m d
1
D (dt / d ) 4h / d 3.44r / d
第一篇第六章车身覆盖件拉深工艺课件

第六章 汽车覆盖件拉深工艺
汽车覆盖件: 覆盖汽车发动机、底盘,构成驾驶室
和车身的薄钢板冲压件、内部覆盖件 。 载货汽车的车前钣金件和驾驶室、轿
车的车身等。 特点: 覆盖件具有材料薄、形状复杂 、
结构尺寸大、表面质量高 。 覆盖件材料:通常由0.7~1.2mm的08系
列冷轧薄钢板冲压而成。
1
8
(6) 覆盖件上的孔一般应在零件拉深成 形后冲出,以预防 发生变形。
(7) 覆盖件拉深的压料圈形状设计,应 保证压料面材料变形流动顺利、坯料定 位的稳定性、可靠性和送料、取件的方 便性、安全性。
9
(8) 充分考虑为后续翻边、修边等工序 提供良好的工艺条件,包括变形条件、 模具结构、零件定位、送料、取件等。
29
2.拉深筋(槛) (1) 拉深筋的作用 ① 增加进料阻力和刚度。 ② 调节材料的流动情况 。 ③ 扩大压料力的调节范围。 ④ 降低对压料面的加工光洁度的要求,
降低大型拉深模的制造工作量。 ⑤ 纠平材料不平整的缺陷。
30
(2) 拉深筋的种类。 ① 拉深筋。 ② 拉深槛。
图6-19 拉深筋
16
(3) 工艺补充部分尽量小。
图6-6 方案a是将翻边展开为 水平面,再加上工艺补充部 分,垂直修边。
方案b是将翻边展开为斜面, 再加上工艺补充部分,垂直
修边。
方案c是将翻边展开为垂直面, 再加上工艺补充部分,水平
修边。
以上三个方案中,方案a最好,
拉深深度浅,易成形,垂直图 6-6 某汽车前围拉深件工艺补充部分的三个方
思考:车门外板单动拉深模主要结构和 辅助结构有哪些?
排气孔,限位器和到位标志器的作用?
39
(2) 双动拉深模的典型结构。
汽车覆盖件: 覆盖汽车发动机、底盘,构成驾驶室
和车身的薄钢板冲压件、内部覆盖件 。 载货汽车的车前钣金件和驾驶室、轿
车的车身等。 特点: 覆盖件具有材料薄、形状复杂 、
结构尺寸大、表面质量高 。 覆盖件材料:通常由0.7~1.2mm的08系
列冷轧薄钢板冲压而成。
1
8
(6) 覆盖件上的孔一般应在零件拉深成 形后冲出,以预防 发生变形。
(7) 覆盖件拉深的压料圈形状设计,应 保证压料面材料变形流动顺利、坯料定 位的稳定性、可靠性和送料、取件的方 便性、安全性。
9
(8) 充分考虑为后续翻边、修边等工序 提供良好的工艺条件,包括变形条件、 模具结构、零件定位、送料、取件等。
29
2.拉深筋(槛) (1) 拉深筋的作用 ① 增加进料阻力和刚度。 ② 调节材料的流动情况 。 ③ 扩大压料力的调节范围。 ④ 降低对压料面的加工光洁度的要求,
降低大型拉深模的制造工作量。 ⑤ 纠平材料不平整的缺陷。
30
(2) 拉深筋的种类。 ① 拉深筋。 ② 拉深槛。
图6-19 拉深筋
16
(3) 工艺补充部分尽量小。
图6-6 方案a是将翻边展开为 水平面,再加上工艺补充部 分,垂直修边。
方案b是将翻边展开为斜面, 再加上工艺补充部分,垂直
修边。
方案c是将翻边展开为垂直面, 再加上工艺补充部分,水平
修边。
以上三个方案中,方案a最好,
拉深深度浅,易成形,垂直图 6-6 某汽车前围拉深件工艺补充部分的三个方
思考:车门外板单动拉深模主要结构和 辅助结构有哪些?
排气孔,限位器和到位标志器的作用?
39
(2) 双动拉深模的典型结构。
第六章 拉深工艺与拉深模具

2
上 海 应 用 技 术 学 院
拉深模: 拉深所使用的模具。
上 海 应 用 技 术 学 院
1-模柄 2 -上模座 3凸模固定板 4弹簧 5-压 边圈 6-定位 板 7-凹模 8-下模座 9 -卸料螺钉 10凸模
拉 深 模 结 构 图
拉深模特点:结构相对较简单,与冲裁模比较,工作部分有较 大的圆角,表面质量要求高,凸、凹模间隙略大 3 于板料厚度。
13
3.筒壁部分: 这是拉深时形成的侧壁部分,是已经结束了塑性变形阶段
的已变形区。这个区受单向拉应力作用,变形是拉伸变形。 是传力区。
4.凸模圆角部分:这是与凸缘圆角接触的部分,它从拉深开始一直承
受径向拉应力和切向拉应力的作用,并且受到凸模圆角的压力和弯曲作用, 因而这部分材料变薄最严重,尤其与侧壁相切的部位,所以此处最容易出 现拉裂,是拉深的“危险断面”。
5.筒底部分:这部分材料与凸模底面接触,在拉深开始时即被拉入凹
上 海 应 用 技 术 学 院
模,并在拉深的整个过程保持其平面形状。它受双向拉应力作用,变形是 双向拉伸变形。但这部分材料基本上不产生塑性变形或者只产生不大的塑 性变形。筒壁、底部圆角、筒底这三部分的作用是传递拉深力,把凸模的 作用力传递到变形区凸缘部分上,使之产生足以引起拉深变形的径向拉应 力,因而又叫传力区。
材料在拉深过程中产生塑性流动转
移了,使得拉深后工件高度增加了, 壁厚也略有增加。
8
(一)拉深成形时板料的受力分析 (二)拉深变形过程及特点 1.变形现象 平板圆形坯料的凸缘——弯曲绕过凹模圆角,
上 海 应 用 技 术 学 院
然后拉直——形成竖直筒壁。 变形区——凸缘; 已变形区——筒壁; 不变形区——底部。 底部和筒壁为传力区。
上 海 应 用 技 术 学 院
拉深模: 拉深所使用的模具。
上 海 应 用 技 术 学 院
1-模柄 2 -上模座 3凸模固定板 4弹簧 5-压 边圈 6-定位 板 7-凹模 8-下模座 9 -卸料螺钉 10凸模
拉 深 模 结 构 图
拉深模特点:结构相对较简单,与冲裁模比较,工作部分有较 大的圆角,表面质量要求高,凸、凹模间隙略大 3 于板料厚度。
13
3.筒壁部分: 这是拉深时形成的侧壁部分,是已经结束了塑性变形阶段
的已变形区。这个区受单向拉应力作用,变形是拉伸变形。 是传力区。
4.凸模圆角部分:这是与凸缘圆角接触的部分,它从拉深开始一直承
受径向拉应力和切向拉应力的作用,并且受到凸模圆角的压力和弯曲作用, 因而这部分材料变薄最严重,尤其与侧壁相切的部位,所以此处最容易出 现拉裂,是拉深的“危险断面”。
5.筒底部分:这部分材料与凸模底面接触,在拉深开始时即被拉入凹
上 海 应 用 技 术 学 院
模,并在拉深的整个过程保持其平面形状。它受双向拉应力作用,变形是 双向拉伸变形。但这部分材料基本上不产生塑性变形或者只产生不大的塑 性变形。筒壁、底部圆角、筒底这三部分的作用是传递拉深力,把凸模的 作用力传递到变形区凸缘部分上,使之产生足以引起拉深变形的径向拉应 力,因而又叫传力区。
材料在拉深过程中产生塑性流动转
移了,使得拉深后工件高度增加了, 壁厚也略有增加。
8
(一)拉深成形时板料的受力分析 (二)拉深变形过程及特点 1.变形现象 平板圆形坯料的凸缘——弯曲绕过凹模圆角,
上 海 应 用 技 术 学 院
然后拉直——形成竖直筒壁。 变形区——凸缘; 已变形区——筒壁; 不变形区——底部。 底部和筒壁为传力区。
17809-冲压工艺与模具设计-电子教案-模块4
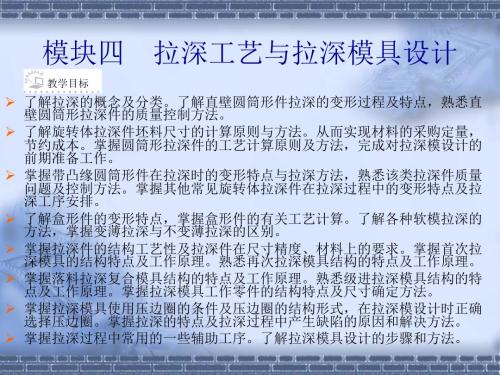
盒形件拉深时的应力分布
项目一 拉深工艺
低盒形件拉深件的毛坯
项目一 拉深工艺
高盒形件拉深件的毛坯
项目一 拉深工艺
任务八 其他拉深方法 变薄拉深件图
项目一 拉深工艺
液体凸模拉深的变形过程
项目一 拉深工艺
聚氨酯橡胶拉深模 强制润滑拉深
项目一 拉深工艺
变薄拉深
项目一 拉深工艺
项目二 拉深模具结构及工作原理
任务一 首次拉深模具的结构及工作原理
1. 无压边首次拉深模具
2. 有压边的首次拉深模具
项目二 拉深模具结构及工作原理
无压边装置的首次拉深模具 工作时,毛坯在定位圈3中 定位,拉深结束后,工件由 凹模底部的台阶完成脱模, 并由下模座底孔落下。由于 模具没有采用导向机构,故 模具安装时由校模圈2完成 凸、凹模的对中,保证间隙 均匀,工作时将校模圈移走。 该模具结构简单,制造方便, 通常用于材料塑性好、相对 厚度较大的零件拉深。由于 其凸模要深入凹模,所以只 适用于浅拉深。
项目二 拉深模具结构及工作原理
任务一 首次拉深模具的结构及工 作原理 任务二 再次拉深模具的结构及工 作原理
模块小结
项目一 拉深工艺
任务一 拉深概念及分类 典型拉深件
项目一 拉深工艺
拉深件的分类
项目一 拉深工艺
不变薄拉深
项目一 拉深工艺
变薄拉深
项目一 拉深工艺
任务二 直壁圆筒形件拉深的变形过程及特点 圆筒形拉深件
项目二 拉深模具结构及工作原理
无压边圈的再次拉深模具
项目二 拉深模具结构及工作原理
带弹性压边圈的再次拉深模具
项目二 拉深模具结构及工作原理
第六章拉深(5—7)
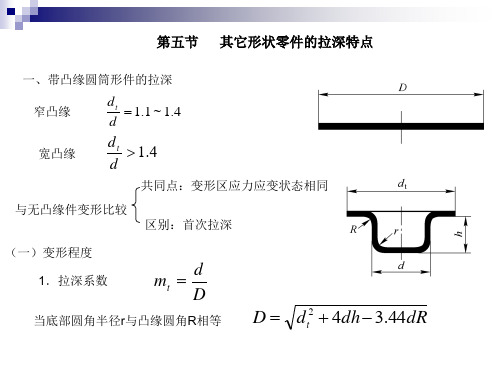
②变形情况:直边流入凹模的速度>圆角部分
∴直边对圆角的变形有带动作用,因此,可减少圆角的拉应力σL。 ③直边与圆角相互影响程度决定于r/B和H/B r/B↓→ 直边对圆角变形影响↑ H/B↑→ 直边对圆角变形影响↑
(二)盒形件毛坯形状与尺寸的确定 1、一次拉深成形的低盒形件坯料 作图法: (1)直边——按弯曲变形
不能用来作为判断依据
m
d d D 2d
2.三种成形方法
(1)
t 3% D
可不用压料圈,但行程终了要整形,
(2)
t 0.5% ~ 3% 采用压料装置拉深 D t 3% D
采用压料筋或反拉深方法
(3)
1. 带直壁 h (0.1 ~ 0.2)d 或带凸缘球形件 dt d (0.2 ~ 0.3)d 有利于球面成形(防皱) 2. 高度小于 r 的浅球形件 问题----------起皱、坯料偏移、回弹 (1)
di mi d i 1
(i=2,3,4…n)
以后各次拉深系数——其值与凸缘宽度及外形尺寸无关,可 查表5-11,与无凸缘拉深相同。
(二)拉深方法
1.小凸缘圆筒件拉深
前几道按无凸缘拉深→最后两道拉为带锥形凸缘件→再整形成平面凸缘。
2.宽凸缘圆筒件拉深方法
表面质量较差,需最后增加整形 工序,适用于薄、深、中小件 (dt<200mm)
查表5-14
ri——各次拉深后工序件口部圆角半径
(2)相对高度 当 r rd 也可用H/r表示 首次拉深查表5-13
拉深系数m大于表5-12或相对高度H/r小于表5-13可一次拉深成形。
(四)盒形件多工序的拉深方法及工序件尺寸的确定 盒形件多次拉深的变形特点: (与筒形件多次拉深不同;与盒形件首次拉深不同)
拉伸工艺与拉深模具设计
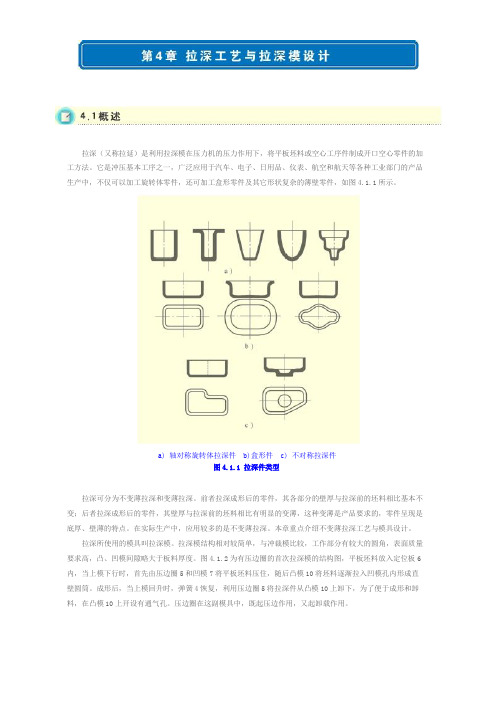
“起皱”和筒壁传力区的“拉裂”是拉深工艺能否顺利进行的主要障碍。为此,必须了解起 皱和拉裂的原因,在拉深工艺和拉深模设计等方面采取适当的措施,保证拉深工艺的顺利进行,提高拉深件的 质量。
1.凸缘变形区的起皱 拉深过程中,凸缘区变形区的材料在切向压应力 σ 的作用下,可能会产生失稳起皱,如图 4.2.6 所示。 凸缘区会不会起皱,主要决定于两个方面:一方面是切向压应力 σ 的大小,越大越容易失稳起皱;另一方面 是凸缘区板料本身的抵抗失 稳的能力,凸缘宽度越大,厚度越薄,材料弹性模量和硬化模量越小,抵抗失稳 能力越小。这类似于材料力学中的压杆稳定问题。压杆是否稳定不仅 取决于压力而且取决于压杆的粗细。在 拉深过程中 是随着拉深的进行而增加的,但凸缘变形区的相对厚度 也在增大。这说明拉深过程中失稳起皱的 因素在增加而抗失稳起皱的能力也在增加。
图 4.2.4
在厚度方向,由于压料圈的作用,产生压应力 ,通常 和 的绝对值比 大得多。厚度方向上材料的的变形 情况取决于径向拉应力 和切向压应力 之间比例关系,一般在材料产生切向压缩和径向伸长的同时,厚度有所 增厚,越接近于外缘,板料增厚越多。如果不压料( =0),或压料力较小( 小),这时板料增厚比较大。当 拉深变形程度较大,板料又比较薄时,则在坯料的凸缘部分,特别是外缘部分,在切向压应力 作用下可能失 稳而拱起,产生起皱现象。
此外,影响极限拉深系数的因素还有拉深方法、拉深次数、拉深速度、拉深件的形状等。 采用反拉深、软模拉深等可以降低极限拉深系数;首次拉深极限拉深系数比后次拉深极限拉深 系数小;拉深速度慢,有利于拉深工作的正常进行,盒形件角部拉深系数比相应的圆筒形件的
拉深系数小。 3.极限拉深系数的确定 由于影响极限拉深系数的因素很多,目前仍难采用理论计算方法准确确定极限拉深系数。
1.凸缘变形区的起皱 拉深过程中,凸缘区变形区的材料在切向压应力 σ 的作用下,可能会产生失稳起皱,如图 4.2.6 所示。 凸缘区会不会起皱,主要决定于两个方面:一方面是切向压应力 σ 的大小,越大越容易失稳起皱;另一方面 是凸缘区板料本身的抵抗失 稳的能力,凸缘宽度越大,厚度越薄,材料弹性模量和硬化模量越小,抵抗失稳 能力越小。这类似于材料力学中的压杆稳定问题。压杆是否稳定不仅 取决于压力而且取决于压杆的粗细。在 拉深过程中 是随着拉深的进行而增加的,但凸缘变形区的相对厚度 也在增大。这说明拉深过程中失稳起皱的 因素在增加而抗失稳起皱的能力也在增加。
图 4.2.4
在厚度方向,由于压料圈的作用,产生压应力 ,通常 和 的绝对值比 大得多。厚度方向上材料的的变形 情况取决于径向拉应力 和切向压应力 之间比例关系,一般在材料产生切向压缩和径向伸长的同时,厚度有所 增厚,越接近于外缘,板料增厚越多。如果不压料( =0),或压料力较小( 小),这时板料增厚比较大。当 拉深变形程度较大,板料又比较薄时,则在坯料的凸缘部分,特别是外缘部分,在切向压应力 作用下可能失 稳而拱起,产生起皱现象。
此外,影响极限拉深系数的因素还有拉深方法、拉深次数、拉深速度、拉深件的形状等。 采用反拉深、软模拉深等可以降低极限拉深系数;首次拉深极限拉深系数比后次拉深极限拉深 系数小;拉深速度慢,有利于拉深工作的正常进行,盒形件角部拉深系数比相应的圆筒形件的
拉深系数小。 3.极限拉深系数的确定 由于影响极限拉深系数的因素很多,目前仍难采用理论计算方法准确确定极限拉深系数。
5-6 拉深工艺设计
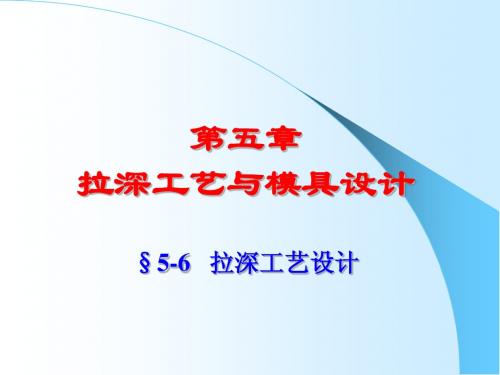
下列3种工艺方案:
方案1
(1)落料 (2)首次拉深 (3)二次拉深 (4)三次拉深
方案2
方案3
(1)落料、首次拉深复合 (1)落料 (2)二次拉深 (2)正、反拉深 (3)三次拉深
三种方案比较 : 模具结构简单, 压力机吨位可 较小,生产率 低,适于批量 不大的生产。
正、反拉深模具 复合工序的模具 结构较复杂,这 较复杂,且压力 时需要采用双动 机吨位要求较大, 压力机、生产力 生 产 率 比 方 案 1 率高,适宜于批 高,适宜于批量 量大而且具备双 动压力机的情况。 1)多道工序的拉深成形工序设计时,每一道工序完成一 定的加工任务,使先行工序不妨碍后续工序的完成; (2)每道拉深工序的最大变形程度不能超过其极限值; (3)已成形部分和待成形部分之间,不应再发生材料的转 移。 (4)在大批量生产中,若凸凹模的模壁强度允许,应采用 落料、拉深复合工艺。
查表取修边余量为10mm, 则零件高度为570mm, 因而可求得毛坯直径D≈965mm。 357.5 零件的总拉深系数 m Σ = = 0.37 965 t/D=2.5/965=0.25%
查表需分3次拉深,拉深系数分别为: m1=0.58 m2=0.79 m3=0.81 故 d1=m1D=0.58×965mm≈560mm d2=m2d1=0.79×560mm≈442mm d3=m3d2=0.81×442mm≈357.5mm
第五章 拉深工艺与模具设计
§5-6 拉深工艺设计
一、拉深件的工艺性
1.拉深件结构形状的要求 拉深件结构形状的要求
拉深后材料各部位的厚度变化:底部厚度基本 不变,底部圆角部分变薄,凸缘部分变厚。 在设计拉深件时,尺寸应明确标注的是外形尺 寸还是内形尺寸,不能同时标注内、外形尺寸。
- 1、下载文档前请自行甄别文档内容的完整性,平台不提供额外的编辑、内容补充、找答案等附加服务。
- 2、"仅部分预览"的文档,不可在线预览部分如存在完整性等问题,可反馈申请退款(可完整预览的文档不适用该条件!)。
- 3、如文档侵犯您的权益,请联系客服反馈,我们会尽快为您处理(人工客服工作时间:9:00-18:30)。
按图得:
4
D2
a1 a2
a3+a4+a5
ai
故
D
4
ai
a1
4
(d
2 4
d32 )
a2
2
r1d3
4r1
a3 d2h
a4
2
r2 d1
4r2
整理后可得坯料直径为:
a5
d12
4
D
d12
4d2h
2r(d1
d2
)
4r 2
d
2 4
d32
d
2 4
4d 2 H
3.44rd 2
常用旋转体拉深件毛坯直径计算公式见表6-5
m
dn D
d1 D
d2 d1
d3 d2
d n1 d n2
dn d n1
m1m2 m3 mn1mn
如果m取得过小,会使拉深件起皱、断裂或严重变薄超差。
因此拉深系数减小有一个客观的界限
极限拉深系数 mmin
从工艺的角度来看,mmin越小越有利于减少工序数。
20
(二)影响极限拉深系数的因素
29
(3)确定拉深次数 先判断能否一次拉出
计算总拉深系数
m总=
d D
20 78
0.256
查表6-8取:m1=0.55 m2=0.75
由于m总<< m1,,所以一次拉不出。
计算法: n 1 lg 20 1g(0.55 78)=3.65
lg 0.75
查表法: 由表6-9查得n=4
取n=4
推算法: 由表6-6查得m1=0.5 m2=0.75 m3=0.78 m4=0.8 m5=0.82
d1=m1D;d2=m2d1;…;dn=mndn-1; 3)当dn≤d时,计算的次数即为拉深次数。
(3)查表法
表6-9 根据毛坯相对厚度t/D与零件的相对高度h/d查取拉 深次数。
表6-10 根据毛坯相对厚度t/D与总拉深系数查取拉深次数。
26
四、筒形件各次拉深件的半成品尺寸计算
1. 各次半成品的直径确定
第六章 拉深工艺与拉深模具
拉深是基本冲压成形工序之一
第一节 拉深过程分析 第二节 筒形件拉深的工艺计算 第三节 筒形件在以后各次拉深时的特点及其方法 第四节 拉深力与压边力的计算 第五节 拉深模工作部分结构参数的确定 第六节 拉深模的典型结构 第七节 其它形状零件的拉深特点
1
拉深:
又称拉延,是利用拉深模在压力机的压力作用下,将平板坯 料或空心工序件制成各种开口空心零件的加工方法。
3)压料圈的压料力 压料力增大了筒壁传力区的拉应力,压料力太大,可能导致 拉裂。 必须正确调整压料力,即应在保证不起皱的前堤下,尽量减 少压料力,提高工艺的稳定性。 4. 拉深方法、拉深次数、拉深速度、拉深件的形状等
23
(三)极限拉深系数的确定 由于影响极限拉深系数的因素很多,目前仍难采用理论计
算方法准确确定极限拉深系数。在实际生产中,极限拉深系 数值一般是在一定的拉深条件下用实验方法得出的。
1. 材料的力学性能
s/ b越小
减小拉深系数
越大 r越大
减小拉深系数 减小拉深系数
2. 板料的相对厚度 t / D
t/D
mmin
21
3. 拉深工作条件
1)模具的几何参数
r凸太小,增大了板料绕凸模弯曲的拉应力,降低了危险断面的 抗拉强度,降低极限变形程度; r凹过小,拉深过程中由于绕凹模圆角弯曲和校直,增大了筒壁 的拉应力,减小了极限拉深系数。
表6-6和表6-7是圆筒形件在不同条件下各次拉深的极限拉深系数。 表6-8是各种材料的极限拉深系数。
在实际生产中,并不是在所有情况下都采用极限拉深系
数。为了提高工艺稳定性和零件质量,适宜采用稍大于
极限拉深系数mmin的值。
24
三、拉深次数的确定
1.拉深次数的确定方法 当m总>mmin时,拉深件可一次拉成,否则需要多次拉深。
9
三、拉深件的起皱与拉裂
拉深过程中的质量问题:
主要是凸缘变形区的起皱和筒壁传力区的拉裂。
凸缘区起皱:
由于切向压应力引起板料失去稳定而产生弯曲;
传力区拉裂:
由于拉应力超过抗拉强度引起板料断裂。
10
1.凸缘变形区的起皱
主要决定于:
一方面是切向压应力的大小,越大越容易失稳起皱;
另一方面是凸缘区板料本身的抵抗失稳的能力。
按图得:
4
D2
A1
A2+A3
Ai
故
D
4
Ai
A1 d (H r)
A2
4
2r(d 2r) 8r 2
A3
4
(d
2r)2
整理后可得坯料直径为:
D (d 2r)2 4d (H r) 2r(d 2r) 8r 2
d 2 4dH 1.72dr 0.56r 2
16
带凸缘筒形件的毛坯直径计算
d1 0.53 78mm 41mm d3 0.79 31mm 24.5mm
d2 0.76 41mm 31mm d4 0.82 24.5mm 20mm
各次半成品底部圆角半径取: r1=5mm,r2=4.5mm,r3=4mmr4=3.5mm
各次半成品高度为
h1
0.25
782 41
凸缘宽度越大,厚度越薄,材料弹性模 量和硬化模量越小,抵抗失稳能力越小。 最易起皱的位置: 凸缘边缘区域
起皱最强烈的时刻: 在Rt=(0.7~0.9)R0时 防止起皱: 压边
11
2.筒壁的拉裂
主要取决于:
一方面是筒壁传力区中的拉应力;
另一方面是筒壁传力区的抗拉强度。
当筒壁拉应力超过筒壁材料的抗拉强度时,拉深件就 会在底部圆角与筒壁相切处——“危险断面”产生破 防止裂拉。裂:
凸、凹模间隙太小,板料受 到太大的挤压作用和摩擦阻 力,增大拉深力;太大会影 响拉深件的精度,拉深件锥 度和回弹较大。
22
2)摩擦润滑
凹模和压料圈与板料接触的表面润滑条件好,可以减 少摩擦阻力和筒壁传力区的拉应力。
凸模表面不宜太光滑,也不宜润滑,以减小由于凸模 与材料的相对滑动而使危险断面变薄破裂的危险。
不变薄拉深
拉深 变薄拉深
拉深工艺特点: 拉深时金属有较大的流动。
拉深模: 拉深所使用的模具。
拉深模特点: 与冲裁模比较,凹凸模无锋利的刃口,有较大的
圆角半径,较大的间隙。
2
拉深件类型:
直壁旋转件
圆筒形零件
非直壁旋转件 直壁非旋转件
各种曲面形零件 盒形零件
非旋转件曲面形状零件
不规则形状的零件
变形力学特点不同 变形区的位置,变形特点,受力情况,成形机理。
是否采用压料装置主要看拉深过程中是否可能发生起皱,在实际
生产中可按表6-12来判断拉深过程中是否起皱和采用压料装置。
33
压料装置产生的压料力FQ大小应适当: 在保证变形区不起皱的前提下,尽量选用小的压料力。
理想的压料力是随起皱可能性变化而变化。 任何形状的拉深件:FQ=Ap
相似原则: 拉深前坯料的形状与冲件断面形状相似。
但坯料的周边必须是光滑的曲线连接。 形状复杂的拉深件:
需多次试压,反复修改,才能最终确定坯料形状。
13
拉深件的模具设计顺序: 先设计拉深模,坯料形状尺寸确定后再设计冲裁模。
切边工序: 拉深件口部不整齐,需留切边余量。
切边余量可参考表6-2和表6-3。
确定拉深次数以后,由表查得各次拉深的极限拉深系数,
适当放大,并加以调整,其原则是:
1)保证
m1m2 mn
d D
2)使 m1 m2 mn
最后按调整后的拉深系数计算各次工序件直径:
d1=m1D d2=m2d1 …
dn=mndn-1
27
2. 各次半成品的高度计算
根据拉深后工序件表面积与坯料表面积相等的原则,可得
拉深系数m是以拉深后的直径d与拉深前的坯料D(工序件dn)直
径之比表示。
第一次拉深系数:
m1
d1 D
第二次拉深系数:m2
d2 d1
第n次拉深系数:
mn
dn d n1
19
拉深系数m表示拉深前后坯料(工序件)直径的变化率。
m愈小,说明拉深变形程度愈大,相反,变形程度愈小。
拉深件的总拉深系数等于各次拉深系数的乘积,即
17
(三)复杂形状的旋转体拉深件
久里金法则求其表面积:
任何形状的母线绕轴旋转一周所得到的旋转体面积,等于 该母线的长度与其重心绕该轴线旋转所得周长的乘积。 如右图所示,旋转体表面积为
A 2Rx L
因拉深前后面积相等,故坯料直径D:
D 2
4
2Rx L
D 8Rx L
18二Biblioteka 拉深系数(一)拉深系数m的概念
一方面要通过改善材料的力学性能,提高筒壁抗拉强度;
另一方面通过正确制定拉深工艺和设计模具,降低筒壁所 受拉应力。
12
第二节 筒形件拉深的工艺计算
一、旋转体拉深件毛坯尺寸的计算 (一)确定毛坯形状与尺寸的依据
体积不变原则: 若拉深前后料厚不变,拉深前坯料表面积与
拉深后冲件表面积近似相等,得到坯料尺寸。
d1 0.50 78mm 39mm d2 0.75 39mm 29.3mm d3 0.78 29.3mm 22.8mm d4 0.80 22.8mm 18.3mm
由于d4<d,,所以4次可以拉出。
30
(4)确定各次拉深半成品尺寸
经调整后的各次拉深系数为:
m1=0.53,m2=0.76,m3=0.79,m4=0.82 各次半成品直径为
3
第一节 圆筒形件拉深过程分析