磨削技术理论与应用
平面双面研磨抛光

平面双面研磨抛光学校名称:重庆职业技术学院院系名称:电子工程系学生学号:20042348平面双面研磨抛光学科、专业:光电技术应用学生姓名:李士全指导老师姓名:王君重庆职业技术学院电子工程系摘要光学加工中,抛光就是研磨,是精磨以后的主要工序。
工件在精磨之后,虽然具有一定的光滑和规则的表面形状,但它还不完全透明而且表面形状也不是所要求的,需要经过抛光才能成为所要求的抛光表面。
研磨抛光是获得光学表面的最主要的工序。
平面双面研磨抛光顾名思义就是对大量平面零件上下两个表面同时加工进行高速抛光。
抛光中主要的是对磨盘的修正(修盘)、工艺参数、抛光液的浓度、PH值、机器的清洗等系列的掌握和理解。
抛光是零件加工中的最后工序,质量的要求很高,面对划痕、麻点、破边等系列的问题都有他的解决方法。
光学玻璃在抛光过程中及抛光下盘以后的腐蚀问题,长期以来一直影响着这些光学玻璃零件的加工质量和生产效率。
例如对化学稳定性差的光学玻璃抛光液中,添加适当的pH值调节剂,减少了一系列化学稳定性差的光学玻璃在抛光过程中的腐蚀问题,显著提高了抛光表面质量和合格率,并进一步提高了光学玻璃零件加工的效率和效益及其工艺技术水平。
在科技领先的现在,具有丰富的理论知识、实践经验、可操作技术才能进一步提高了光学冷加工的效率和效益及其工艺技术水平,在光学以后的发展进步中才有立足之地,。
关键词:修盘、PH值、疵病1平面双面研磨抛光目录引言 (1)一、抛光的基础 (2)二、平面双面抛光 (3)三、抛光常见问题及处理方法 (7)四、总结 (11)参考文献 (11)2重庆职业技术学院电子工程系引言如今我们不难发现,军用武器系统中几乎都装备有各种各样的光电传感器件,而在这些光电传感器件中,或多或少都采用了各种样式的光学零件。
从美国陆军所作的一项调查报告的材料中我们知道,1980~1990年美国军用激光和红外热成像产品所需要的各种光学零件就有114.77万块,其中球面光学零件为63.59万块,非球面光学零件为23.46万块,平面光学零件为18.1万块,多面体扫瞄镜为9.62万块。
外圆磨床设计说明书

外圆磨床设计说明书第1章绪论1.1磨床的类型与⽤途1.1.1 磨床的类型及其特点⽤磨料磨具(砂轮、砂带、油⽯和研磨料等)为⼯具进⾏切削加⼯的机床,统称为磨床(英⽂为Grinding machine),它们是因精加⼯和硬表⾯的需要⽽发展起来的[1]。
磨床种类很多,主要有:外圆磨床、内圆磨床、平⾯磨床、⼯具磨床和⽤来磨削特定表⾯和⼯件的专门化磨床,如花键轴磨床、凸轮轴磨床、曲轴磨床等[2]。
对外圆磨床来说,⼜可分为普通外圆磨床、万能外圆磨床、⽆⼼外圆磨床、宽砂轮外圆磨床、端⾯外圆磨床等以上均为使⽤砂轮作切削⼯具的磨床。
此外,还有以柔性砂带为切削⼯具的砂带磨床,以油⽯和研磨剂为切削⼯具的精磨磨床等。
磨床与其他机床相⽐,具有以下⼏个特点:1、磨床的磨具(砂轮)相对于⼯件做⾼速旋转运动(⼀般砂轮圆周线速度在35⽶/秒左右,⽬前已向200⽶/秒以上发展);2、它能加⼯表⾯硬度很⾼的⾦属和⾮⾦属材料的⼯件;3、它能使⼯件表⾯获得很⾼的精度和光洁度;4、易于实现⾃动化和⾃动线,进⾏⾼效率⽣产;5、磨床通常是电动机---油泵---发动部件,通过机械,电⽓,液压传动---传动部件带动⼯件和砂轮相对运动---⼯件部分组成[1]。
1.1.2 磨床的⽤途磨床可以加⼯各种表⾯,如内、外圆柱⾯和圆锥⾯、平⾯、渐开线齿廓⾯、螺旋⾯以及各种成形表⾯。
磨床可进⾏荒加⼯、粗加⼯、精加⼯和超精加⼯,可以进⾏各种⾼硬、超硬材料的加⼯,还可以刃磨⼑具和进⾏切断等,⼯艺范围⼗分⼴泛。
随着科学技术的发展,对机械零件的精度和表⾯质量要求越来越⾼,各种⾼硬度材料的应⽤⽇益增多。
精密铸造和精密锻造⼯艺的发展,使得有可能将⽑坯直接磨成成品。
⾼速磨削和强⼒磨削,进⼀步提⾼了磨削效率。
因此,磨床的使⽤范围⽇益扩⼤。
它在⾦属切削机床所占的⽐重不断上升。
⽬前在⼯业发达的国家中,磨床在机床总数中的⽐例已达30%----40%。
据1997年欧洲机床展览会(EMO)的调查数据表明,25%的企业认为磨削是他们应⽤的最主要的加⼯技术,车削只占23%,钻削占22%,其它占8%;⽽磨床在企业中占机床的⽐例⾼达42%,车床占23%,铣床占22%,钻床占14%[3]。
微细加工技术概述及其应用

2011 年春季学期研究生课程考核(读书报告、研究报告)考核科目:微细超精密机械加工技术原理及系统设计学生所在院(系):机电工程学院学生所在学科:机械设计及理论学生姓名:杨嘉学号:10S008214学生类别:学术型考核结果阅卷人微细加工技术概述及其应用摘要微细加工原指加工尺度约在微米级范围的加工方法,现代微细加工技术已经不仅仅局限于纯机械加工方面,电、磁、声等多种手段已经被广泛应用于微细加工,从微细加工的发展来看,美国和德国在世界处于领先的地位,日本发展最快,中国有很大差距。
本文从用电火花加工方法加工微凹坑和用微铣削方法加工微小零件两方面描述了微细加工技术的实际应用。
关键词:微细加工;电火花;微铣削1微细加工技术简介及国内外研究成果1.1微细加工技术的概念微细加工原指加工尺度约在微米级范围的加工方法。
在微机械研究领域中,从尺寸角度,微机械可分为1mm~10mm的微小机械,1μm~1mm的微机械,1nm~1μm的纳米机械,微细加工则是微米级精细加工、亚微米级微细加工、纳米级微细加工的通称。
广义上的微细加工,其方式十分丰富,几乎涉及现代特种加工、微型精密切削加工等多种方式,微机械制造过程又往往是多种加工方法的组合。
从基本加工类型看,微细加工可大致分为四类:分离加工——将材料的某一部分分离出去的加工方式,如分解、蒸发、溅射、切削、破碎等;接合加工——同种或不同材料的附和加工或相互结合加工方式,如蒸镀、淀积、生长等;变形加工——使材料形状发生改变的加工方式,如塑性变形加工、流体变形加工等;材料处理或改性和热处理或表面改性等。
微细加工技术曾广泛用于大规模集成电路的加工制作,正是借助于微细加工技术才使得众多的微电子器件及相关技术和产业蓬勃兴起。
目前,微细加工技术已逐渐被赋予更广泛的内容和更高的要求,已在特种新型器件、电子零件和电子装置、机械零件和装置、表面分析、材料改性等方面发挥日益重要的作用,特别是微机械研究和制作方面,微细加工技术已成为必不可少的基本环节。
SABC碎磨流程的应用

半自磨与球磨设备 的规格及配套装机 功率的确定
芬兰Metso公司
实验室分批自磨试验
JuliusKruttschnitt矿物研究中心
JKTech落重试验
通过测定净功率和产品中-12.7mm 矿量 计算单位净功耗。设计时使用单位净功耗 乘以设计生产能力再乘以1.2的机械系数即 为选用的(半)自磨机功率。分批试验产 品的邦德球磨功指数和金属磨损指数可用 于后续球磨机选型计算和金属磨损预测。
优化手段: ①流程结构及设备配置的优化 ②半自磨磨矿介质的优化:钢球的选择应该以大直径的钢球为主,建议采用新型 “非球形多面体多元合金钢球”,取代传统的球形钢球,该钢球有20个六边形面, 能大大减少钢球与细粒矿石之间的研磨作用,增加钢球对大颗粒矿石的冲击磨削作 用,充分发挥半自磨机破碎和粗磨的优势。 ③半自磨设备及工艺参数的优化:钢球球径、装球率、介质充填率、排料格子板开 孔尺寸等 ④顽石处理系统的优化: • 采用预选设备选别后部分抛废(德国施德纳特公司生产的X射线分选机、 俄罗斯
虽然乌山一期SABC碎磨流程达产达标,但由于该工艺为国内大 型选矿厂首次应用,欠缺半自磨选型试验,设计流程参数、设备选型
等主要依据国内外类似流程推理计算,经过09年至14年5年的生产 实践,生产中出现了以下主要问题: • 半自磨机和球磨机安装功率不匹配; • 半自磨机功率闲置过大,衬板损坏严重,4个月需更换一次; • 球磨机作业负荷较大; • 顽石产率波动,顽石破碎机配制过大;
工作原理:筒体转动时,筒体内的研磨介质——钢球和矿块在摩擦力和离心力的作 用下,随着筒体回转被提升到一定高度,并按一定的线速度被抛落,矿石受到下落 钢球的撞击和钢球与钢球之间及钢球与磨机及矿块之间的附加压碎和磨剥作用而被 粉碎,并借助于水的冲力将被磨碎的合格物料送出筒体外。
数控技术毕业论文(5篇)
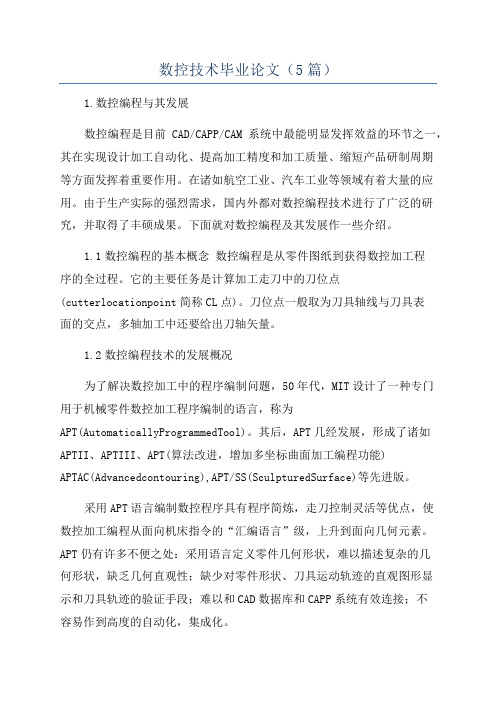
数控技术毕业论文(5篇)1.数控编程与其发展数控编程是目前CAD/CAPP/CAM系统中最能明显发挥效益的环节之一,其在实现设计加工自动化、提高加工精度和加工质量、缩短产品研制周期等方面发挥着重要作用。
在诸如航空工业、汽车工业等领域有着大量的应用。
由于生产实际的强烈需求,国内外都对数控编程技术进行了广泛的研究,并取得了丰硕成果。
下面就对数控编程及其发展作一些介绍。
1.1数控编程的基本概念数控编程是从零件图纸到获得数控加工程序的全过程。
它的主要任务是计算加工走刀中的刀位点(cutterlocationpoint简称CL点)。
刀位点一般取为刀具轴线与刀具表面的交点,多轴加工中还要给出刀轴矢量。
1.2数控编程技术的发展概况为了解决数控加工中的程序编制问题,50年代,MIT设计了一种专门用于机械零件数控加工程序编制的语言,称为APT(AutomaticallyProgrammedTool)。
其后,APT几经发展,形成了诸如APTII、APTIII、APT(算法改进,增加多坐标曲面加工编程功能)APTAC(Advancedcontouring),APT/SS(SculpturedSurface)等先进版。
采用APT语言编制数控程序具有程序简炼,走刀控制灵活等优点,使数控加工编程从面向机床指令的“汇编语言”级,上升到面向几何元素。
APT仍有许多不便之处:采用语言定义零件几何形状,难以描述复杂的几何形状,缺乏几何直观性;缺少对零件形状、刀具运动轨迹的直观图形显示和刀具轨迹的验证手段;难以和CAD数据库和CAPP系统有效连接;不容易作到高度的自动化,集成化。
针对APT语言的缺点,1978年,法国达索飞机公司开始开发集三维设计、分析、NC加工一体化的系统,称为为CATIA。
随后很快出现了象EUCLID,UGII,INTERGRAPH,Pro/Engineering,MasterCAM及NPU/GNCP 等系统,这些系统都有效的解决了几何造型、零件几何形状的显示,交互设计、修改及刀具轨迹生成,走刀过程的仿真显示、验证等问题,推动了CAD和CAM向一体化方向发展。
磨工高级理论知识试卷

职业技能鉴定国家题库 磨工高级理论知识试卷 注 意 事 项 1、本试卷依据2001年颁布的《磨工》国家职业标准命制, 考试时间:120分钟。
2、请在试卷标封处填写姓名、准考证号和所在单位的名称。
3、请仔细阅读答题要求,在规定位置填写答案。
一、单项选择题(第1题~第160题。
选择一个正确的答案,将相应的字母填入题内的括号中。
每题0.5分,满分80分。
) 1.在企业的经营活动中,下列选项中的( )不是职业道德功能的表现。
A 、激励作用 B 、决策能力 C 、规范行为 D 、遵纪守法 2.职业道德对企业起到( )的作用。
A 、增强员工独立意识 B 、模糊企业上级与员工关系 C 、使员工规规矩矩做事情 D 、增强企业凝聚力 3.正确阐述职业道德与人的事业的关系的选项是( )。
A 、没有职业道德的人不会获得成功 B 、要取得事业的成功,前提条件是要有职业道德 C 、事业成功的人往往并不需要较高的职业道德 D 、职业道德是人获得事业成功的重要条件 4.在商业活动中,不符合待人热情要求的是( )。
A 、严肃待客,表情冷漠 B 、主动服务,细致周到 C 、微笑大方,不厌其烦 D 、亲切友好,宾至如归 5.对待职业和岗位,( )并不是爱岗敬业所要求的。
A 、树立职业理想 B 、干一行爱一行专一行 C 、遵守企业的规章制度 D 、一职定终身,不改行 6.( )是企业诚实守信的内在要求。
A 、维护企业信誉 B 、增加职工福利 C 、注重经济效益 D 、开展员工培训 7.坚持办事公道,要努力做到( )。
A 、公私不分 B 、有求必应 C 、公正公平 D 、全面公开 8.下列关于勤劳节俭的论述中,正确的选项是( )。
A 、勤劳一定能使人致富B 、勤劳节俭有利于企业持续发展C 、新时代需要巧干,不需要勤劳D 、新时代需要创造,不需要节俭9.企业生产经营活动中,要求员工遵纪守法是( )。
考 生 答 题 不 准超过此 线A、约束人的体现B、保证经济活动正常进行所决定的C、领导者人为的规定D、追求利益的体现10.关于创新的论述,不正确的说法是()。
磨工考试题及答案
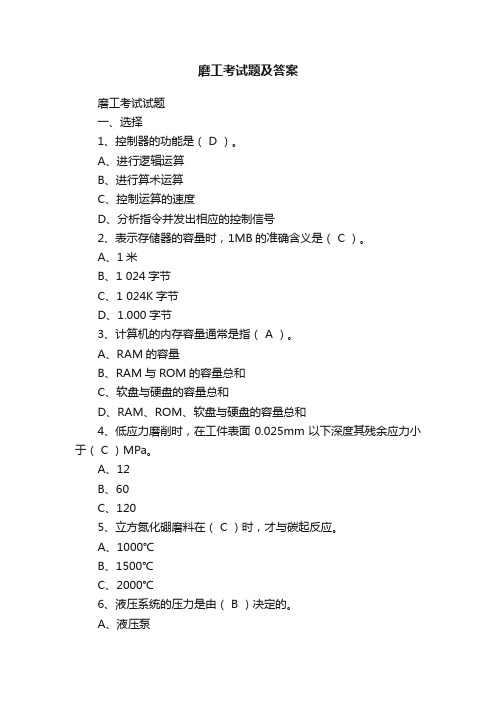
磨工考试题及答案磨工考试试题一、选择1、控制器的功能是( D )。
A、进行逻辑运算B、进行算术运算C、控制运算的速度D、分析指令并发出相应的控制信号2、表示存储器的容量时,1MB的准确含义是( C )。
A、1米B、1 024字节C、1 024K字节D、1.000字节3、计算机的内存容量通常是指( A )。
A、RAM的容量B、RAM与ROM的容量总和C、软盘与硬盘的容量总和D、RAM、ROM、软盘与硬盘的容量总和4、低应力磨削时,在工件表面0.025mm以下深度其残余应力小于( C )MPa。
A、12B、60C、1205、立方氮化硼磨料在( C )时,才与碳起反应。
A、1000℃B、1500℃C、2000℃6、液压系统的压力是由( B )决定的。
A、液压泵B、负载C、阀7、砂轮架主轴轴承的间隙冷态时应调整在( C )mm之间。
A、0.005-0.01B、0.01-0.015C、0.015-0.0208、静压轴承之所以能够承受载荷,关键在于液压泵在油缸之间有( B )。
A、减压阀B、节流阀C、整流器9、磨床运动部件从某一个位置运动到预期的另一个位置所达到的实际位置精度称为( B )精度。
A、工作B、定位C、几何D、运动10、磨床的( A )精度是保证加工精度的最基本条件。
A、几何B、传动C、定位11、磨削锥齿轮端面的夹具,应以齿轮的( C )作为定位基准。
A、外圆B、内孔C、分度圆12、浮标式气动量仪属于( C )式气动量仪。
A、压力B、流量C、流速13、对R Z值小于0.8μm的工件,需采用( C )来测量其表面粗糙度值。
A、工具显微镜B、光切显微镜C、干涉显微镜14、精磨细长轴时,工件一般圆周速度为( C )m/min。
A、60—80B、40—60C、20—4015、由于磨削压力引起的内应力,很容易使薄片工件产生(C )现象。
A、弯曲B、扭曲C、翘曲16、既硬又粘的材料磨削后,工件的( D )现象严重,表面发生烧伤等现象。
硬态切削技术的研究

摘要硬态切削工艺由于具有良好的加工环保性和加工柔韧性,该工艺已经逐步取代磨削工艺成为模具钢的精加工工艺,它是具有广泛应用前景的先进加工技术。
但硬态切削加工工艺中诸如刀具磨损、切削过程热流特性和已加工表面完整性等方面的理论与技术还存在诸多没有彻底揭示之处。
所以应该在上述方面展开深入研究,以便促进此新兴工艺在实际加工中的应用。
为揭示硬态切削过程已加工表面淬火效应,本文研究了不同升温速率下工件材料的相变点在切削状态下相变图谱位移情况;结合数值方法得到了不同刀具磨损情况下工件温度场分布情况,对已加工表面的变质层厚度进行了预测,并利用实验手段得到了已加工表面变质层受刀具磨损和切削速度的影响规律,同时也分析了淬火效应对已加工表面硬度的影响。
关键词:硬态切削、淬火、已加工表面AbstractHard cutting processing technology has gradually become a high strength steel finishing process and has replaced the grinding process in certain occasions as well,for its good processing environmental protection,flexible and precision.Thus,this technology is an advanced processing technology with wide application prospects.But many special cutting law of the hard cutting processing technology still need to explore,especially cutting tool wear in cutting,surface quenching effect,processing surface integrity and other aspects of the theory and technology need a systemic research,which could further promote the advanced technology.In order to reveal the die steel Cr12MoV already processing surface quenching effect mechanism,this paper studied the workpiece material phase transition point in different heating rate and the phase diagram of displacement in different cutting state;Combining with numerical method to get the workpiece temperature field distribution in the different tool wear condition,and predicating the thickness of already processing surface metamorphic layer,beside,by using experimental method to get the influence mechanism of the tool wear and cutting speed to finished surface metamorphic layer.At the same time,the paper also evaluated how quenching effect influence the processing surface hardness.Key words:Hard cutting;Quenaching;Already processing surface;目录摘要 (I)Abstract ................................................................................................................ I I 第1章绪论.. (4)1.1 硬态切削的研究目的和意义 (4)1.2 硬态切削 (4)1.3 高强度钢硬态切削的特征及优势 (4)1.4 已加按工表面变质层 (5)1.5 硬态切削技术的发展趋势 (6)第2章硬态切削已加工表面变质层的产生的因素分析 (7)2.1 变质层的研究现状 (7)2.2 变质层的形态 (7)2.2.1 变质层的形成条件 (8)2.3 变质层的形成机制 (8)2.3.1 硬态切削过程中被加工表面的变质层 (11)2.3.2 变质层体积的变化 (12)2.3.3 变质层的晶粒细化 (13)第3章影响变质层产生的因素分析 (14)3.1 影响变质层形成的主要因素 (14)第4章变质层产生的临界条件判定 (17)4.1 变质层产生临界条件的判定 (17)4.2 急剧温升条件下Cr12MoV相变点变化的研究 (17)第5章硬态切削过程温度场分布 (20)第6章已加工表面变质层的生成机制 (22)6.1 切削速度对变质层生成的影响 (22)6.2 后刀面磨损对表面变质层产生的影响 (24)第7章模具钢已加工表面淬硬机制 (26)7.1 加工硬化的评价方法 (26)7.2 6.2 高强度钢加工硬化试验 (26)参考文献 (28)第1章绪论1.1硬态切削的研究目的和意义硬态切削是当今最富生气的切削技术之一。