磨削及磨削机理
3第三章 磨削机理

α= β=
4td D 2 + dD 4tD d 2 + Dd
所以 sinα+sinβ=α β β=α+β α β=α
= 4 td D
2
+ dD
+
4 tD d
2
+ dD
= 2 t(
1 1 + ) D d
Vw 1 1 g = 2a t( + ) VS D d
磨粒的最大切入深度 的指导意义 : 增大, 减少时, 将增大 单颗磨粒的切削力也增大, 将增大。 ⅰ 当VW增大,VS减少时,g将增大。单颗磨粒的切削力也增大, 对于软砂轮而言,会引起磨粒脱落加快,或对于硬砂轮来说, 对于软砂轮而言,会引起磨粒脱落加快,或对于硬砂轮来说,则会 加快磨粒的钝化速度,从而使磨具的寿命减少。 加快磨粒的钝化速度,从而使磨具的寿命减少。 最大切屑厚度与连续切刃间隔a成正比 成正比。 ⅱ 最大切屑厚度与连续切刃间隔 成正比。粒度粗而硬度低的 砂轮其a值较大 值较大, 也就较大 也就较大。 砂轮其 值较大,g也就较大。 砂轮和工件的尺寸也影响着g的大小 的大小, ⅲ 砂轮和工件的尺寸也影响着 的大小,当使用小直径的砂轮磨 削大直径的工件时, 将变大 削大直径的工件时 g将变大
NP ×
π
6
d o = V g × 1× d o
3
Vg是砂轮的组织,即磨粒 是砂轮的组织, 体积率。一般值0.4 0.4~ 体积率。一般值0.4~0.5
NP =
6V g
πd o 2
w =
'
1 NP
=
d o =(1.14~1.15)d 0 6V g
π
砂轮表面上平均 的切刃间隔大约 为平均粒径的 1.5~2倍 ~ 倍
磨削加工基础知识

磨削加工基础知识磨削加工是一种高精度的加工方法,具有高效、精度高、表面质量好等优点,被广泛应用于机械制造、航空航天、光学、电子、仪器仪表、医疗器械等领域。
磨削加工的基础知识对于理解磨削加工的工艺特点和实现高精度、高效加工具有重要意义。
第一、磨削加工的原理与工艺特点磨削加工是利用磨削工具对工件进行高速旋转运动和相对移动,通过对工件表面的撞击和摩擦作用,使工件表面物质逐渐脱落,同时形成较高的表面质量。
磨削工具是一个至关重要的部分,其轮廓、材料、粒度、硬度等参数会直接影响磨削效果。
同时,磨削加工具有高效、高精度、表面质量好的特点。
磨削加工时,磨削工具旋转高速,加工效率非常高。
同时,由于磨削加工的切削深度非常小,可以实现高精度加工。
此外,通过加工工艺优化,还可以获得高精度的工件表面质量。
第二、磨削加工的工具与磨削方法磨削工具是磨削加工的核心之一。
常用的磨削工具有磨石、磨轮、砂布轮、抛光布轮等,它们由不同的材料和制造工艺制成,具有不同的加工能力。
常见的磨削方法有平面磨削、圆柱磨削、内圆磨削、外圆磨削、表面磨削等。
通过选择合适的磨削工具和磨削方法,可以实现不同形状和精度要求的工件加工。
第三、磨削加工的加工参数在进行磨削加工时,需要设置一系列加工参数,包括磨削工具的转速、磨削深度、进给量、磨削液的类型和流量等。
这些参数直接影响着工件的加工效果和工具的使用寿命。
例如,在选择磨削工具的时候,需要考虑工件的材料、精度和表面质量要求等因素,选择合适的材料、形状、粒度磨削工具。
在设置磨削深度和进给量时,需要根据工件材料是否易碎、磨削强度等因素进行综合考虑。
第四、磨削加工的提高磨削加工的加工精度和表面质量程度是衡量磨削加工质量的重要指标。
为了提高磨削加工的质量和效率,可以从以下方面进行优化。
首先是磨削工具的性能提升,如开发新型材料、制造工艺等。
其次是加工参数的优化,通过对加工深度、进给量和磨削液的改进,可以进一步提高加工效果和工具的使用寿命。
机械制造中的磨削工艺及其应用

机械制造中的磨削工艺及其应用磨削工艺在机械制造领域中具有广泛的应用,它是一种通过切削和磨擦来加工工件表面的方法。
磨削技术不仅可以改善工件表面的光洁度和精度,还可以提高工件的强度和耐磨性。
本文将详细介绍机械制造中的磨削工艺及其应用。
一、磨削工艺的基本原理磨削工艺是通过将磨料粒子与工件表面摩擦来消除工件表面的杂质并形成所需形状和尺寸的加工方法。
它的基本原理包括研磨机械的选择和研磨参数的控制。
1. 磨料的选择磨料是磨削工艺的核心材料,根据工件材料和磨削要求的不同,选择不同性能的磨料是非常重要的。
常见的磨料包括砂轮、研磨石、磨粉等。
砂轮通常由粘结剂和磨料颗粒组成,砂轮的种类繁多,可以根据不同的加工要求进行选择。
2. 研磨参数的控制研磨参数的控制对于磨削工艺的质量和效率有着重要影响。
常见的研磨参数包括磨削速度、进给量、磨削深度和磨削压力等。
合理地控制这些参数可以得到理想的磨削效果。
二、磨削工艺的分类根据磨料形态和研磨过程的不同,磨削工艺可以分为粒度磨削、方向磨削和超磨削等几种不同的分类。
1. 粒度磨削粒度磨削是最常见的磨削工艺,它通过利用磨料颗粒之间的相互作用来进行磨削。
根据磨削方式的不同,粒度磨削又可以分为砂轮磨削、磨粉磨削和研削磨削等几种不同的形式。
2. 方向磨削方向磨削是指沿工件表面某一方向进行磨削的方法。
根据方向的不同,方向磨削可以分为横向磨削、纵向磨削和斜向磨削等不同的形式。
方向磨削通常用于加工平面和外圆等形状的工件。
3. 超磨削超磨削是一种高精度加工方法,它通过利用超磨削工具和磨料颗粒进行磨削。
超磨削通常用于加工高精度的工件,如摄影镜头等。
三、磨削工艺的应用磨削工艺在机械制造中有着广泛的应用,下面将介绍几个常见的应用领域。
1. 表面精加工磨削工艺可以使工件表面获得较高的光洁度和精度,从而提高工件的质量和使用寿命。
它常被用于加工零件的表面,如汽车发动机缸体和曲轴等。
2. 零件修复在机械制造过程中,零件表面常常会出现一些缺陷或磨损。
磨削原理的说明

磨削原理的说明磨削是一种常见的机械加工工艺,用于去除工件中的金属材料,使其达到所需的精度和表面质量。
它通过将硬度较高的磨粒与工件表面相互作用,通过切割和破碎的方式来去除金属材料。
在磨削过程中,磨粒与工件之间产生的磨削力和热量是主要影响磨削效果的因素之一。
下面将从磨削原理的角度对其进行详细说明。
磨削原理的核心在于磨粒与工件之间的相互作用。
磨削时,磨料在磨具表面产生的磨削力将磨粒推向工件表面,磨粒与工件表面相互摩擦,同时切削进入工件中。
由于磨粒硬度高于工件材料,磨粒可以切入和切削工件材料,将其去除。
同时,磨削力也会产生剪切和破碎作用,进一步破碎和去除工件材料。
磨削力不仅包括切削力,还包括辊压力和摩擦力,这些力的作用使磨削过程更加复杂。
磨削过程中产生的热量也是一个重要的因素。
磨削时,磨削力和磨粒与工件间的摩擦产生热量,这些热量通过工件和磨具的传导和对流传递到周围。
热量的积累会使工件表面温度升高,如果温度过高,可能导致工件变形或热裂纹的产生。
为了控制温度,常常使用冷却液或润滑剂来降低磨削过程中的摩擦和热量。
磨削原理中还有一些影响磨削效果的因素需要考虑。
首先是磨削速度和进给速度。
磨削速度是指磨具与工件的相对线速度,进给速度是指磨具与工件之间的相对位移速度。
适当的磨削速度和进给速度可以提高磨削效率和表面质量,但速度过高或过低都会影响加工效果。
其次是磨具的选择。
不同的工件材料和要求需要使用不同的磨具,例如砂轮、磨料带和研磨头等。
磨具的选择应考虑硬度、颗粒度、结构和绑定剂等因素。
最后是刀具与工件的角度和相对位置。
不同的磨削角度会对磨削效果产生影响,需要根据工件材料的特性来选择合适的角度。
总之,磨削是一种通过磨粒与工件表面的相互作用来去除金属材料的机械加工过程。
通过切削和破碎的方式来进行磨削,同时磨削力和热量的作用对磨削效果起到重要影响。
磨削过程中的磨削速度、进给速度、磨具选择和刀具角度等因素也需要合理调整和控制,以达到所需的加工精度和表面质量。
第七章 磨削加工

第七章磨削加工基本要求及重点:1、了解磨削特点和各种磨削方法与磨削运动。
2、明确砂轮的特性及其选择原则。
3、理解砂轮磨损及耐用度、磨削力及功率、磨削温度及烧伤等概念。
4、了解磨削过程,知道磨削表面缺陷产生的原因及解决办法。
5、了解高效率和高精度及小粗糙度磨削的方法。
§7-1 磨削概述及其原理一、概述磨削加工是用硬质磨粒作为切削工具对工件进行微细切削加工过程的统称。
它是一种精密加工方法。
1、磨削加工的优点及其应用与其他切削加工方法相比,磨削加工是一种多刀多刃的高速切削方法。
它是为适应传统金属材料的精加工及其淬硬表面加工的需要而发展起来的。
随着磨料磨具和高效磨削工艺(如高速磨削、强力磨削、重负荷磨削、砂带磨削等)的发展,以及磨床结构性能的不断改进,磨削加工效率和经济性在显著提高,磨削的应用已从精加工逐步扩大到粗加工领域。
同时,在当今的钛合金、高温合金、超高强度钢、不锈钢及高温结构陶瓷等难加工材料以及硬脆材料的加工中,磨削是一种非常有效的加工方法。
3、磨削加工机床分类磨床是用磨料或磨具(砂轮、砂带、油石或研磨料)作为工具对工件表面进行加工的机床。
为了适应磨削加工表面、结构形状和尺寸大小不同的各种工件的需要,满足不同生产批量的要求,需要的磨床种类很多。
按加工工件表面不同,分为如下几类:(1) 外圆磨床包括万能外圆磨床、外圆磨床及无心外圆磨床等。
(2) 内圆磨床包括内圆磨床,无心内圆磨床及行星式内圆磨床等。
(3) 平面磨床包括卧轴矩台平面磨床、立轴矩台平面磨床、卧轴圆台平面磨床及立轴圆台平面磨床等。
(4) 工具磨床 包括万能工具磨床(能刃磨各种常用刀具)、拉刀刃磨床、滚刀刃磨床等。
(5) 曲线磨床(6) 专用磨床 包括曲轴磨床、凸轮轴磨床,花键轴磨床、轧辊磨床、轴承套圈滚道磨床等。
(7) 坐标磨床(8) 锯磨机(9) 精磨机床 包括研磨机、珩磨机、抛光机、超精加工机床及砂轮机等。
二、磨削原理1、砂轮构造磨削时所用的砂轮是由磨粒、结合剂和气孔组成的,见图7-1。
最新磨削机理

磨削力分析
为便于分析问题,磨削力可为相互垂直的三个分力,即沿砂轮切 向的切向磨削力Ft,沿砂轮径向的法向磨削力Fn以及沿砂轮轴向的轴 向磨削力Fa。一般在磨削中,轴向力Fa较小,可忽略不计。
Fn称为法向磨削力 Ft称为切向磨削力 Fa称为轴向磨削力
F=Fn十Ft十Fa
磨削力
磨削力关系影响因素
一般情况,Fn>Ft>Fa,而法向磨削力与切向磨削力的比值Fn/Ft,称为磨削力比, 是加工中一个重要数据,它可间接地说明砂轮工作表面磨粒的锋利程度。因 为随着磨粒的钝化,将引起F的急剧增大,使砂轮磨损加快,系统振动增加, 噪声加大,工件表面粗糙度上升和表面质量恶化等。所以,它也可作为砂轮 耐用度的判断依据之一 。
若n=0, α=0,则0.5<γ<1,取ε=0.5, γ=0.5时,磨削力完全来源于摩擦,与磨削 变形无关。
在实际磨削中,不可能会出现单纯的摩擦和完全切削这两种情况。磨
削力由摩擦及切削变形两部分组成。那一部分占有主导地位,则取决于砂 轮、工件和磨削条件的综合情况。根据相关文献指导,概括多次试验结果, 指数的实际值出于下列范围: 0.1≤γ≤0.8;0.5 ≤ε ≤0.95。
NdFtg4NdFpap2sin
Fn NdFngNdFpap2si t na n
F 则可以得到单位磨削力的计算式: p
2Ndap1 2sin4Ft
tFann
其中 N d 为动态的有效磨刃数 ,Nd NtLsb, 为砂轮表面上的单位长度静态
L
有效磨刃数,削宽度。
砂轮接触面上的动态磨刃数的磨削力计算公式
ls
Fn, l Fp Aln Nd ldl
0
整个接触弧长度上的法向磨削力大小:
2 1
简述精密磨削机理
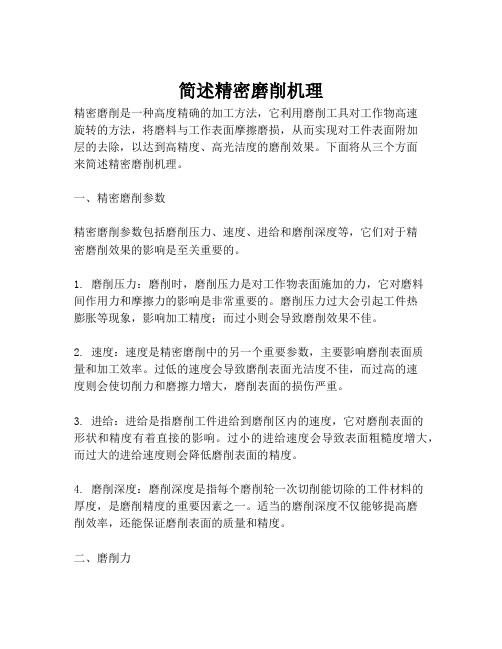
简述精密磨削机理精密磨削是一种高度精确的加工方法,它利用磨削工具对工作物高速旋转的方法,将磨料与工作表面摩擦磨损,从而实现对工件表面附加层的去除,以达到高精度、高光洁度的磨削效果。
下面将从三个方面来简述精密磨削机理。
一、精密磨削参数精密磨削参数包括磨削压力、速度、进给和磨削深度等,它们对于精密磨削效果的影响是至关重要的。
1. 磨削压力:磨削时,磨削压力是对工作物表面施加的力,它对磨料间作用力和摩擦力的影响是非常重要的。
磨削压力过大会引起工件热膨胀等现象,影响加工精度;而过小则会导致磨削效果不佳。
2. 速度:速度是精密磨削中的另一个重要参数,主要影响磨削表面质量和加工效率。
过低的速度会导致磨削表面光洁度不佳,而过高的速度则会使切削力和磨擦力增大,磨削表面的损伤严重。
3. 进给:进给是指磨削工件进给到磨削区内的速度,它对磨削表面的形状和精度有着直接的影响。
过小的进给速度会导致表面粗糙度增大,而过大的进给速度则会降低磨削表面的精度。
4. 磨削深度:磨削深度是指每个磨削轮一次切削能切除的工件材料的厚度,是磨削精度的重要因素之一。
适当的磨削深度不仅能够提高磨削效率,还能保证磨削表面的质量和精度。
二、磨削力在精密磨削中,磨削力起着关键的作用。
磨削力包括切削力和法向力两个方向的力。
切削力是沿着工件表面的力,是磨削过程中摩擦力和切削力的总和。
法向力是垂直于工件表面的力,作用于磨削轮和工件之间的接触面。
法向力的大小和方向对于精密磨削过程中的磨削力影响极大。
三、磨削热在高速磨削过程中,由于磨削面与切削刃瞬间之间的摩擦和接触,会引起加工界面的热变形和变色。
因此,控制磨削热的积累是保证精密磨削效果的关键。
合适的工作液和降低磨削温度的措施(如降低表面温度、改善切削液的散热、提高磨削速度等)都可以在一定程度上减少磨削热对加工质量的影响。
总之,了解各种精密磨削参数与机理的相互关系,才能够更好地运用磨削工艺,提高精密磨削的效率和质量。
第2章磨削原理

2.2表征磨削过程的磨削要素
2.1.3磨粒的切削作用与磨削过程(2)
2.2表征磨削过程的磨削要素
2.1.3磨粒的切削作用与磨削过程(3)
2、 磨削的三个过程 根据上述模型可以看到磨削过程存在三个阶段. 第一阶段为 滑擦阶段 ,该阶段内切削刃与工件表面开始接触 ,工件系统仅仅发生弹性 变形 .随着切削刃切过工件表面 ,进一步发生变形,因而法向力稳定地上升,摩擦力用切向 力也同时稳定增加,即该阶段内,磨粒微刃不起切削作用,只是在工件表面滑擦。 第二阶段为 耕犁阶段 ,在滑擦阶段,摩擦逐渐加剧,越来越多的能量转变为热当金 属被加热到临界点,逐步增加的法向应力超过了随温度上升而下降的材料屈服应力时,切 削刃就被压入塑性基本体中。经塑性变形的金属被推向磨粒的侧面及前方,最终导致表面 的隆起。这就是磨削中的耕犁作用这种耕犁作用构成了磨削过程的第二个阶段。
磨削过程的第三个阶段即 切削屑形成阶段 。在滑擦和耕犁阶段中,磨粒并不产生磨 屑。由此可见,要产生磨屑及切下金属,存在着一个临界磨削深度。此外还可以看到,磨 粒切削刃推动于金属材料的流动,使前方隆起,两侧面形成沟壁,随后将有磨屑沿切浮点 刃前面滑出。
为了难验证磨粒磨削过程的三个阶段,R.S.Hahn和R.P.Lindsay曾通过单位磨削宽度法 高磨削力与切入进给量的关系进行了实验,从力的角度也清楚地说明了滑擦、耕和磨屑形 成过程。
N t C1k s a q p
- 1、下载文档前请自行甄别文档内容的完整性,平台不提供额外的编辑、内容补充、找答案等附加服务。
- 2、"仅部分预览"的文档,不可在线预览部分如存在完整性等问题,可反馈申请退款(可完整预览的文档不适用该条件!)。
- 3、如文档侵犯您的权益,请联系客服反馈,我们会尽快为您处理(人工客服工作时间:9:00-18:30)。
1.砂轮寿命及其判据
砂轮两次修整之间的实际磨削时间称为砂轮寿命。判断砂轮寿命,一般 根据工作面磨损后所产生的现象目测判定。主要现象有:磨削过程出现 自激振动、工件表面出现再生振纹;磨削噪音增大;工件表面出现磨削 烧伤、磨削力急剧增大或减小;磨削精度下降;磨削表面粗糙度增大。 这些现象的产生主要是由于磨削温度过高使工件表面产生热损伤和由于 自激振动导致的粗糙度和精度下降。
返回目录
第14页
磨具特性的选择
一、磨具概述
磨具即指在加工工序中起磨削、研磨、抛光作用的工具。一般由磨料、 结合剂、气孔三大要素沟成,不过后又把浸渍剂列为第四要素,而超硬 磨具则把基体作为第四要素。其分类按磨料种类可分普通与超硬材料磨 具;按结合剂又分无机(陶瓷、菱苦土、硅酸钠结合剂磨具)、有机 (树脂和橡胶结合剂磨具)、金属结合剂;按磨料结合剂结合形式又可 分固结、涂附磨具及研磨膏。普通磨具的特征标记必须按顺包含下面8项 内容。例:PDT500*(10/16)*203-A/WA100L5V60m/s。依次序上例各数字 字母所代表含义为:
返回目录
第13页
修整砂轮的工具按修整器的几何形状和修整过程中运动形式可分两种: 静止型修整器和运动型修整器。普通的修整方法有三种:车削法、滚压 法和磨削法
我公司主要用金刚石笔的车削法修整和修整滚轮的磨削法。而对超硬磨 具的修整可分为整形和修锐:整形是对砂轮进行微量切削,使表面达到 所要求的几何形状;修锐是去除磨粒间的结合剂,使磨粒间有一定的溶 屑空间,并行成切削刃。对于陶瓷结合剂的疏松型的超硬砂轮(如金刚 石、CBN砂轮),整形和修锐可在同一工序进行。
Ft-------切向磨削力。直接影响磨削时有效功率的消耗 Fa-------轴向磨削力。总磨削力在砂轮轴线方向分力。
一般Fn >Ft>Fa。且Fn/ Ft可间接说明砂轮工作表面磨粒锋利程度,即
可 Ft=作λσ为′b砂ae 轮耐;用vvwsF度a=判σ′断ba依e 据之一vwv。•s2v。单a 从个上切式刃可的以分看力vv出公ws :式磨:削Fn各=σ分′ba力e 都与;磨
3.磨削主要运动参数:
磨削主运动即砂轮高速回转。不同类型的进给形式又有不同的运动参数。 外圆及内圆磨削除主运动外,还有径向进给(砂轮及工件沿其半径方向 的运动)运动、轴向进给(砂轮及工件沿其轴线方向)运动、圆周运动。 其中工件转速的选择原则:在保证工件表面粗糙度要求的前提下,应使 砂轮在单位时间内切下最多的磨屑而砂轮磨耗最少。一般取 υ砂:υ工 =80~160。 4.磨削加工的特点:
砂轮耐用度:表示砂轮两次修整间隔中金属磨除量
磨削比:磨除的工件体积(或质量)与砂轮的损耗体积(或质量)之比 叫磨削比。G=VWC/ VSC 磨削表面质量:指工件的粗糙度、表面精度及表面层质量等。
八、砂轮修整
砂轮在磨削过程中需要修整,其原因有二:一、由于磨粒磨损,棱角变 钝,气孔被切屑堵塞,从而失去切削能力;二、由于磨粒在砂轮中分布 不规则,切削刃的棱角锐利程度不同,磨削时形成自锐脱落不均匀,影 响工件表面质量。
目录
第6页
切屑弧长与接触弧长相等,则平均切断面积am=w2
vw vs
表示平均切刃间隔)
ae 1 1 (其中w ds dw
四、磨削力
1.磨削分力
磨削力是磨削过程中切削力和摩擦力的总和,由于磨削力大小方向不 断变化,所以一般将磨削力分解成三个力
其有中密F切n-关---系--法。向磨削力。三分力最大,与砂轮和磨粒抗压强度及系统刚性
1.连续切刃间隔:
通常把实际参加切削的切刃示为有效切削刃,它不仅跟砂轮表面几何参 数有关,它也随υ砂、υ工或a厚的变化而变化。
返回目录
第5页
2.磨粒最大切入深度:指单颗磨粒最大切入深度对磨削加工的力和热有着
直接影响,进而影响整个加工质量、砂轮耐用度、磨削效率及磨削能的 消耗。单颗磨粒最大切入深度g为:
返回目录
第4页
参与磨削的磨粒数极多;起切削作用的磨粒数具有特殊性质;磨粒具有 一定的脆性及热稳定性;磨粒切削刃形状不规则,单颗粒切入深度小; 磨具具有较好的自锐性;比磨削能大;可获得高精度低粗糙度表面。
二、磨削过程
在磨粒切削刃与工件接触的全过程中,存在三个明显不同特征的区域, 即弹性滑擦区、塑性耕犁区和切削区。而磨粒进入切削区域的过程中, 磨粒切刃与工件之间的干涉深度从零开始逐渐加深。正是由于磨削过程 中存在弹塑性变形,才使得磨粒在切削过程中与工件的表面生成曲线、 理论干涉曲线、实际干涉曲线不重合,从而导致磨削残留余量、降低磨 削精度。
削宽度、砂轮切入深度、工件速度成比例增加,与砂轮速度成比例
返回目录
第7页
减小。在实际磨削中,严格解析磨削力是困难的,在工程上常简化其公
式,如Ft=k0 vs vw ae (其中k0为磨削系数)
2.比磨削能
指磨除工件上单位体积的金属所消耗的能量叫比磨削能。U=W/V=
。
它对估算磨Ft削vs 力和功率消耗有重要意义。
返回目录
第10页
其中油溶性磨削液主要成分多为矿物油。普通矿物油是在低黏度或中 黏度矿物油中加防锈添加剂。如在机械油、轻质柴油、煤油中加脂肪酸 以增强润滑作用。另外在磨削液中加入硫、氯、磷等元素的极压添加剂 形成极压油,其渗透能力和润滑能力会更佳适宜表面粗糙度要求低的工 序加工使用。油溶性磨削液有较好的附着性,能隔绝空气,防止磨削区 氧化和水解等不良的化学反应。如CBN砂轮易高温下与水发生反应,所 以使用CBN高速磨削时应采用油性磨削液。水溶性磨削液主要成分是水, 再配加其它添加剂而成。其具有很好的冷却效果,且配制方便、成本低 廉、不易污染。
bvwae
五、磨削热
金属切削时绝大部分能量转化为热能,这些热能传散在切屑、刀具、工 件上。其中车削、铣削等普通切削方式,热量都是被切屑带走,而对与 磨削来说由于切削的金属层非常薄所以大约60%~90%的热量都传入工件, 这些热量来不及导入工件更深处所以在局部形成高温,并在表层形成极 大的温度梯度。当这些局部温度达到一定临界值时,就会在工件表面形 成热损伤(如表面氧化、烧伤、残余应力、裂纹等),也影响工件尺寸 精度。所以控制磨削热非常关紧。
返回目录
第16页
磨料种类 代号
主要特点
主要应用范围
棕刚玉
棕褐色,抗破碎能力强,抗氧 适于磨削抗张强度大的金属
A 化、抗腐蚀,韧性强
材料,如普通碳素钢等
白刚玉 WA 铬刚玉 PA 微晶刚玉 MA 单晶刚玉 SA 锆刚玉 ZA
洁 白 的 刚 玉 晶 体 , 有 微 刃 结 构 ,主要用于淬火钢、合金钢的 硬度比棕刚玉高,但脆性大, 细磨精磨,及磨螺纹及齿轮 韧性低,切削能力强
磨削液常用加添加剂来改善磨削液性能,常用的有油性添加剂、极压添 加剂、防锈添加剂、抗泡沫添加剂以及乳化剂等。而常用的一些供液方 法有;浇注法、高压冷却、内冷供液法、超声波供液法和浸渍砂轮等方 法。
七、砂轮的磨损
返回目录
第11页
在磨削过程中,由于磨削力和磨削热的作用,砂轮工作表面磨粒会逐渐 磨钝,这将影响被加工的表面质量和几何精度,并引起振动、噪音、粗 糙度增大,产生裂纹、烧伤和残余应力等,因此砂轮要进行定期的修整。 磨粒的磨耗磨损形式主要有:磨料机械磨损、化学磨损、粘附磨损。
砂轮寿命终结形式:砂轮表面钝化——磨平状态(将增大磨削力及磨 削热);砂轮堵塞(易出现振动或噪音及至烧伤);砂轮轮廓破坏(影 响加工精度)
返回目录
第12页
2.评价砂轮磨削性能指标 磨削效率:实验时常用指标有磨除率(Z),指单位时间内磨除的工件
体积或质量;比磨除率(Z′),指磨具的单位宽度在单位时间所磨去的 工件体积。它表示在磨具耐用度期间内, 磨具平均宽度的磨除率。
2.磨削温度的分类和意义:
⑴.工件的平均温升θw: 它主要影响工件的尺寸和形状精度,它在磨削经过一 定时间后会稳定在某一范围内,其主要虽砂轮转速、切向力的增加而增 加,虽工件转速增加而降低。
⑵.接触面温度θ、θm: 即接触弧部分的表面温度,其主要与工件烧伤、裂纹、 内应力有密切关系。它可分平均温度θ和最高温度θm,一般θm=1.5θ, 其 接触面温度虽砂轮切入深度αe、砂轮速度、工件速度的增加而增高。
返回目录
第 8页
1.磨削热产生与传散
磨削热来源于磨削功率的消耗。磨削热量Q分配如下:
Q=QW+QS+QC+QO+QU (QW、QS、QC、QO、QU分别表示:传入工件 热量、传入砂轮热量、传入切屑热量、传入切削液热量、、辐射热量)。 热量的分配还跟工件、砂轮的导热性有关,如超硬磨具导热性好,所以 磨削热大部分被砂轮带走。
磨削及磨削机理
一、磨削概述
1.磨削:
指用磨具进行去除材料的加工方法。
2.分类:
按其加工对象可分六种基本类型:平面磨削、外圆磨削、内圆磨削、无 心磨削、自由磨削、环端面磨削。按砂轮与工件相对运动关系又可分往 复式、切入式及综合磨削。按工件与砂轮干涉处运动方向又可分顺磨和 逆磨两种方式。轴承行业采用无心夹具磨削轴承套圈,常用顺磨方式, 即砂轮与工件在切向处旋转方向相同。
g =2α ae 1 (1 其 中α-----连续切刃间隔;υs-----砂轮转速; υw--- ds dw
-工件转速;αe-----砂轮切深;ds、dw------砂轮直径、工件直径)
此公式虽近似而得,但对磨削加工却有重要指导意义。其中外圆磨 削取正,内圆磨削取负。
3.切削弧长:
一个切刃在一次切削中所产生的切屑,其未经变形的长度,又叫砂轮接 触弧长
PDT———磨具的形状代号(单面凸砂轮),现用新代号数字表示(38)
500———砂轮直径,mm(正规的还须标上环端直径)
10/16——砂轮厚度,mm。其中10mm为砂轮厚度,16mm为中孔加厚区厚度。
203———砂轮孔径,mm