磨削原理
机械制造中的磨削工艺工作原理
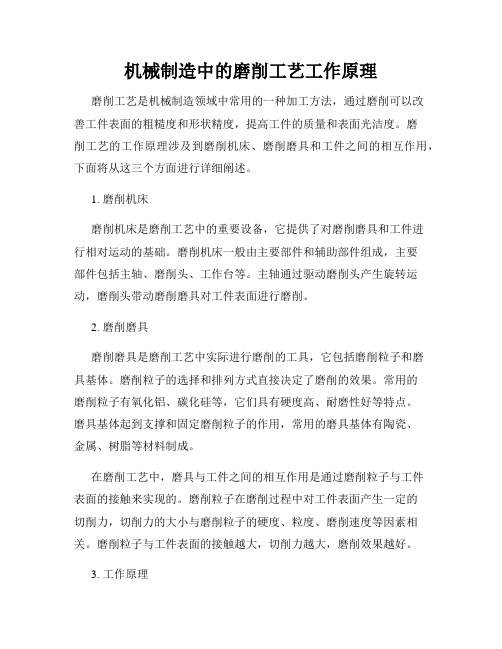
机械制造中的磨削工艺工作原理磨削工艺是机械制造领域中常用的一种加工方法,通过磨削可以改善工件表面的粗糙度和形状精度,提高工件的质量和表面光洁度。
磨削工艺的工作原理涉及到磨削机床、磨削磨具和工件之间的相互作用,下面将从这三个方面进行详细阐述。
1. 磨削机床磨削机床是磨削工艺中的重要设备,它提供了对磨削磨具和工件进行相对运动的基础。
磨削机床一般由主要部件和辅助部件组成,主要部件包括主轴、磨削头、工作台等。
主轴通过驱动磨削头产生旋转运动,磨削头带动磨削磨具对工件表面进行磨削。
2. 磨削磨具磨削磨具是磨削工艺中实际进行磨削的工具,它包括磨削粒子和磨具基体。
磨削粒子的选择和排列方式直接决定了磨削的效果。
常用的磨削粒子有氧化铝、碳化硅等,它们具有硬度高、耐磨性好等特点。
磨具基体起到支撑和固定磨削粒子的作用,常用的磨具基体有陶瓷、金属、树脂等材料制成。
在磨削工艺中,磨具与工件之间的相互作用是通过磨削粒子与工件表面的接触来实现的。
磨削粒子在磨削过程中对工件表面产生一定的切削力,切削力的大小与磨削粒子的硬度、粒度、磨削速度等因素相关。
磨削粒子与工件表面的接触越大,切削力越大,磨削效果越好。
3. 工作原理磨削工艺的工作原理可以概括为磨削磨具与工件表面的相互研磨作用。
当磨削工艺开始时,磨削磨具接触到工件表面,磨削粒子通过切削力对工件表面进行破坏和剥离,同时产生磨渣和切削热。
磨渣被磨削磨具和工作台带走,切削热则通过磨削磨具和冷却液排出。
磨削工艺的工作原理中还存在磨削力和磨削温度的问题。
在磨削过程中,磨削力对工件表面产生一定的切削和热变形,而磨削温度则会影响磨削粒子与工件表面的接触。
过高的磨削力和磨削温度会导致工件表面的质量下降和工具的损坏。
为了提高磨削工艺的效果,需要采取适当的磨削参数和技术手段。
磨削参数包括磨削速度、进给量等,它们的选择需要考虑到工件材料、磨削粒度和切削力等因素。
技术手段包括冷却液的使用、磨削液的选用等,它们可以有效降低磨削温度和防止损伤。
磨削原理
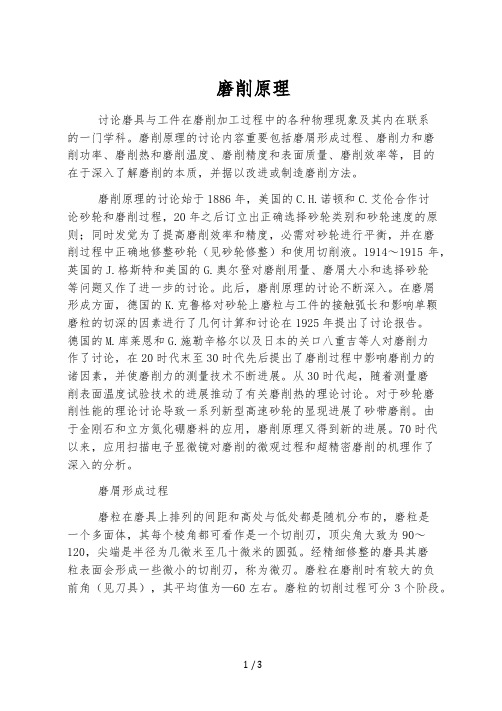
磨削原理讨论磨具与工件在磨削加工过程中的各种物理现象及其内在联系的一门学科。
磨削原理的讨论内容重要包括磨屑形成过程、磨削力和磨削功率、磨削热和磨削温度、磨削精度和表面质量、磨削效率等,目的在于深入了解磨削的本质,并据以改进或制造磨削方法。
磨削原理的讨论始于1886年,美国的C.H.诺顿和C.艾伦合作讨论砂轮和磨削过程,20年之后订立出正确选择砂轮类别和砂轮速度的原则;同时发觉为了提高磨削效率和精度,必需对砂轮进行平衡,并在磨削过程中正确地修整砂轮(见砂轮修整)和使用切削液。
1914~1915年,英国的J.格斯特和美国的G.奥尔登对磨削用量、磨屑大小和选择砂轮等问题又作了进一步的讨论。
此后,磨削原理的讨论不断深入。
在磨屑形成方面,德国的K.克鲁格对砂轮上磨粒与工件的接触弧长和影响单颗磨粒的切深的因素进行了几何计算和讨论在1925年提出了讨论报告。
德国的M.库莱恩和G.施勒辛格尔以及日本的关口八重吉等人对磨削力作了讨论,在20时代末至30时代先后提出了磨削过程中影响磨削力的诸因素,并使磨削力的测量技术不断进展。
从30时代起,随着测量磨削表面温度试验技术的进展推动了有关磨削热的理论讨论。
对于砂轮磨削性能的理论讨论导致一系列新型高速砂轮的显现进展了砂带磨削。
由于金刚石和立方氮化硼磨料的应用,磨削原理又得到新的进展。
70时代以来,应用扫描电子显微镜对磨削的微观过程和超精密磨削的机理作了深入的分析。
磨屑形成过程磨粒在磨具上排列的间距和高处与低处都是随机分布的,磨粒是一个多面体,其每个棱角都可看作是一个切削刃,顶尖角大致为90~120,尖端是半径为几微米至几十微米的圆弧。
经精细修整的磨具其磨粒表面会形成一些微小的切削刃,称为微刃。
磨粒在磨削时有较大的负前角(见刀具),其平均值为—60左右。
磨粒的切削过程可分3个阶段。
①滑擦阶段:磨粒开始挤入工件,滑擦而过,工件表面产生弹性变形而无切屑。
②耕犁阶段:磨粒挤入深度加大,工件产生塑性变形,耕犁成沟槽,磨粒两侧和前端堆高隆起;③切削阶段:切入深度连续增大,温度达到或超过工件材料的临界温度,工件材料明显地沿剪切面滑移而形成磨屑。
磨削原理
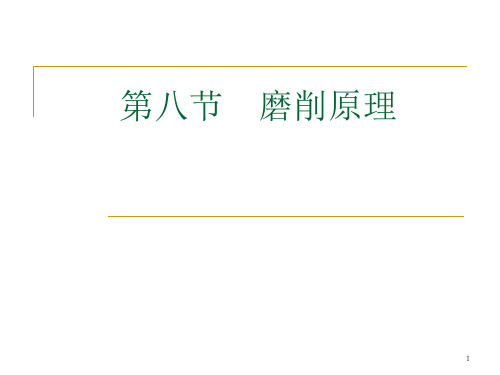
23
2.8.3磨削过程
切屑的形成过程
单颗磨粒的切削过程
磨削的切削厚度很薄只有0.005-0.05mm 磨削的切削厚度很薄只有 滑擦阶段 刻划阶段 切削阶段 磨削塑性材料时,形成带状切屑; 磨削塑性材料时,形成带状切屑; 磨削脆性材料时,形成挤裂切屑。 磨削脆性材料时,形成挤裂切屑。 在磨削过程中产生的高温作用下, 在磨削过程中产生的高温作用下,切屑熔化可成为球状 或灰烬形态
决定砂轮特性的要素:磨料、粒度、结合剂、 决定砂轮特性的要素:磨料、粒度、结合剂、硬 度、组织及尺寸形状
磨料: 磨料:其选择主要取决于工件材料的硬度 应具备的条件:硬度高、红硬性好; 应具备的条件:硬度高、红硬性好;有一定的强度和韧
性;有锋利的边刃
常用的磨料: 常用的磨料:
•氧化物系:主要成分是三氧化二铝 氧化物系: •碳化物系:通常以碳化硅、碳化硼等为肌体 碳化物系:通常以碳化硅、 •高硬磨料系:主要有人造金刚石和立方氮化硼 高硬磨料系:主要有人造金刚石和立方氮化硼(CBN)
耗的能量绝大部分转换为热量产生磨削热
磨削温度的概念: 磨削温度的概念:
工件平均温度:指磨削热传入工件引起的工件温升, 工件平均温度:指磨削热传入工件引起的工件温升,它影响工件的形
状和尺寸精度。在精磨时,为获得高尺寸精度, 状和尺寸精度。在精磨时,为获得高尺寸精度,要尽可能降低工件平均 温度并防止局部温度不均
7
2.8.1砂轮的特性和选择
决定砂轮特性的要素:磨料、粒度、结合剂、 决定砂轮特性的要素:磨料、粒度、结合剂、硬 度、组织及尺寸形状 结合剂:将磨粒粘合在一起,使砂轮具有一定的强度、 结合剂:将磨粒粘合在一起,使砂轮具有一定的强度、
气孔、硬度和抗腐蚀、 气孔、硬度和抗腐蚀、抗潮湿等性能 。它直接影响砂 轮的强度、 轮的强度、耐热性和耐用度 陶瓷结合剂(代号V) 陶瓷结合剂(代号 ) 树脂结合剂(代号B) 树脂结合剂(代号 ) 橡胶结合剂(代号R) 橡胶结合剂(代号 ) 金属结合剂(代号M) 金属结合剂(代号 )
磨削加工原理
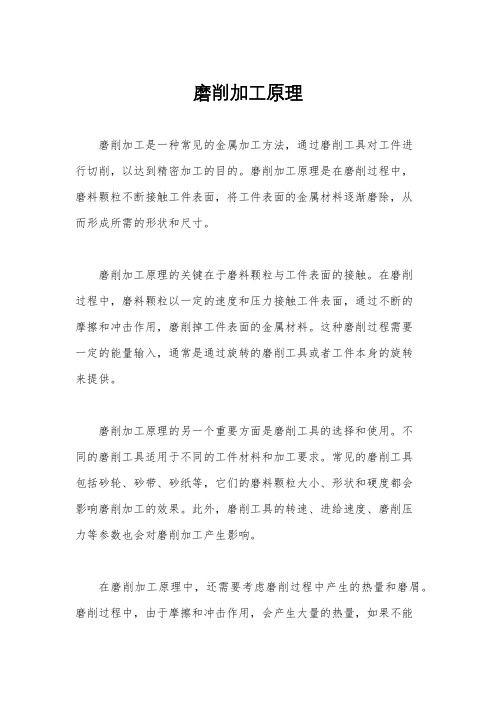
磨削加工原理
磨削加工是一种常见的金属加工方法,通过磨削工具对工件进
行切削,以达到精密加工的目的。
磨削加工原理是在磨削过程中,
磨料颗粒不断接触工件表面,将工件表面的金属材料逐渐磨除,从
而形成所需的形状和尺寸。
磨削加工原理的关键在于磨料颗粒与工件表面的接触。
在磨削
过程中,磨料颗粒以一定的速度和压力接触工件表面,通过不断的
摩擦和冲击作用,磨削掉工件表面的金属材料。
这种磨削过程需要
一定的能量输入,通常是通过旋转的磨削工具或者工件本身的旋转
来提供。
磨削加工原理的另一个重要方面是磨削工具的选择和使用。
不
同的磨削工具适用于不同的工件材料和加工要求。
常见的磨削工具
包括砂轮、砂带、砂纸等,它们的磨料颗粒大小、形状和硬度都会
影响磨削加工的效果。
此外,磨削工具的转速、进给速度、磨削压
力等参数也会对磨削加工产生影响。
在磨削加工原理中,还需要考虑磨削过程中产生的热量和磨屑。
磨削过程中,由于摩擦和冲击作用,会产生大量的热量,如果不能
及时散去,会对工件和磨削工具造成损坏。
同时,磨削过程中产生的磨屑也需要及时清除,以免对加工质量产生影响。
总的来说,磨削加工原理是通过磨料颗粒不断接触工件表面,将工件表面的金属材料逐渐磨除,从而实现精密加工的目的。
在实际应用中,需要根据工件材料和加工要求选择合适的磨削工具和加工参数,同时要注意散热和清屑,以确保磨削加工的效果和质量。
磨削过程及磨削原理
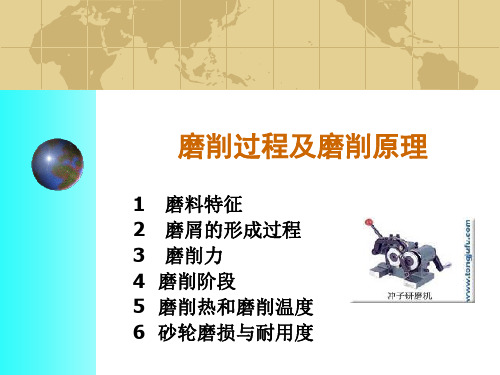
六、砂轮的磨损与耐用度
形态:磨耗磨损(A)、磨粒破碎(B-B) 和脱落磨损(C-C)。 砂轮耐用度:砂轮钝化、变形后加工 质量和效率降低。~用砂轮在两次修 整之间的实际磨削时间度时,工件将发 生颤振,表面粗糙度突然增大,或出 现表面烧伤现象。
由图可知,缩 短初磨阶段和稳定 阶段可提高生产效 率,而保持适当清 磨进给次数和清磨 时间可提高表面质 量。
五 磨削热和磨削温度
1. 磨削温度的基本概念 2. 影响磨削温度的主要因素
砂轮速度V: V ↑→θ↑ 工件速度Vw : Vw ↑→θ↓ 径向进给量fr: fr↑→θ↑ 工件材料: 导热性↓→θ↑ 砂轮硬度与粒度:硬度↓→θ↓ 磨粒大小↑→θ↓
二 磨屑的形成过程
滑擦阶段:磨粒切削厚度非常小,在 工件表面上滑擦而过,工件仅产生弹 性变形。
刻划阶段:工件材料开始产生塑性变 形,磨粒切入金属表面,磨粒的前方 及两侧出现表面隆起现象,在工件表 面刻划成沟纹。磨粒与工件间挤压摩 擦加剧,磨削热显著增加。
切削阶段:随着切削厚度的增加,在 达到临界值时,被磨粒推挤的金属明 显的滑移而形成切屑。
磨削过程及磨削原理
1 磨料特征 2 磨屑的形成过程 3 磨削力 4 磨削阶段 5 磨削热和磨削温度 6 砂轮磨损与耐用度
一 磨料特征
很不规则,大多数呈菱形八面体; 顶尖角大多数为90度~120度,以很大的负前角进行切 削; 磨粒切削刃几乎都存在切削刃钝圆半径; 在砂轮表面分布不均匀,高低也不同。
磨粒常见形状
三 磨削力
➢磨削力的的来源:工件材料产生变形时的抗力和 磨粒与工件间的摩擦力。
➢磨削力的特征: (1) 单位磨削力很大 (2) 径向分力很大---径向力虽不做工,但会使
工件产生水平方向的弯曲,直接影响加工精度。
磨削原理的说明

磨削原理的说明磨削是一种常见的机械加工工艺,用于去除工件中的金属材料,使其达到所需的精度和表面质量。
它通过将硬度较高的磨粒与工件表面相互作用,通过切割和破碎的方式来去除金属材料。
在磨削过程中,磨粒与工件之间产生的磨削力和热量是主要影响磨削效果的因素之一。
下面将从磨削原理的角度对其进行详细说明。
磨削原理的核心在于磨粒与工件之间的相互作用。
磨削时,磨料在磨具表面产生的磨削力将磨粒推向工件表面,磨粒与工件表面相互摩擦,同时切削进入工件中。
由于磨粒硬度高于工件材料,磨粒可以切入和切削工件材料,将其去除。
同时,磨削力也会产生剪切和破碎作用,进一步破碎和去除工件材料。
磨削力不仅包括切削力,还包括辊压力和摩擦力,这些力的作用使磨削过程更加复杂。
磨削过程中产生的热量也是一个重要的因素。
磨削时,磨削力和磨粒与工件间的摩擦产生热量,这些热量通过工件和磨具的传导和对流传递到周围。
热量的积累会使工件表面温度升高,如果温度过高,可能导致工件变形或热裂纹的产生。
为了控制温度,常常使用冷却液或润滑剂来降低磨削过程中的摩擦和热量。
磨削原理中还有一些影响磨削效果的因素需要考虑。
首先是磨削速度和进给速度。
磨削速度是指磨具与工件的相对线速度,进给速度是指磨具与工件之间的相对位移速度。
适当的磨削速度和进给速度可以提高磨削效率和表面质量,但速度过高或过低都会影响加工效果。
其次是磨具的选择。
不同的工件材料和要求需要使用不同的磨具,例如砂轮、磨料带和研磨头等。
磨具的选择应考虑硬度、颗粒度、结构和绑定剂等因素。
最后是刀具与工件的角度和相对位置。
不同的磨削角度会对磨削效果产生影响,需要根据工件材料的特性来选择合适的角度。
总之,磨削是一种通过磨粒与工件表面的相互作用来去除金属材料的机械加工过程。
通过切削和破碎的方式来进行磨削,同时磨削力和热量的作用对磨削效果起到重要影响。
磨削过程中的磨削速度、进给速度、磨具选择和刀具角度等因素也需要合理调整和控制,以达到所需的加工精度和表面质量。
机制技术(3-3)磨削原理
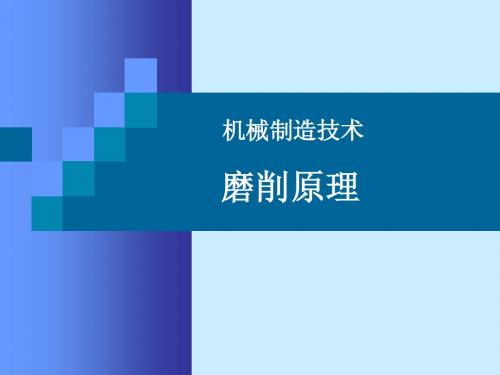
四、磨削原理
㈢、砂轮特性及选择 2、选择砂轮特性的一般原则
⑴、选择砂轮的磨料
2.碳化物系(主要成份碳化硅、碳化硼)
① 黑色碳化硅(C)韧性低、硬度高,磨铸铁、黄铜等脆材 ②绿色碳化硅(GC)韧性差、更硬,磨Y合金、陶瓷、玻璃等 3.超硬磨料 人造金刚石(D)、立方氮化硼(CBN)
四、磨削原理
㈢、砂轮特性及选择 2、选择砂轮特性的一般原则
㈤、高效磨削方法简介 3、砂带磨削
机械制造技术
磨削原理
四、磨削原理
㈠、磨削过程及切屑形成机理 磨粒微小切削刃不规则,磨 削过程复杂磨粒形状、大小各异, 一般都有钝圆半径,磨粒以较大 的负前角(通常刃口前角为-60~ -85°)进行切削。 磨粒切削刃几何形状不确定 磨粒及切削刃随机分布磨削厚 度小(<几μ m),磨削速度高,磨 削点瞬时温度高(达1000℃以上)
vc=π dono/1000
2、工件进给运动
磨削内外圆时:工件旋转运动vw;
磨削平面时:工作台直线运动ntab。
3、轴向进给量fa
4、径向进给量fr
四、磨削原理
㈤、高效磨削方法简介 1、高速磨削
2、强力磨削
3、砂带磨削
四、磨削原理
㈤、高效磨削方法简介 1、高速磨削
2、强力磨削
3、砂带磨削
四、磨削原理
⑴、选择砂轮的磨料
四、磨削原理
㈢、砂轮特性及选择 2、选择砂轮特性的一般原则 ⑵、选择砂轮的硬度
砂轮的硬度指砂轮工作时在磨削力作用下磨粒脱落的难 易程度。取决于结合剂的结合能力及所占比例,与磨料硬度 无关。硬度高,磨料不易脱落;硬度低,自锐性好。分7大 级(超软、软、中软、中、中硬、硬、超硬),16小级
中等组织适于一般磨削工作,如淬火钢、刀具刃磨等。
磨削有哪些原理特点
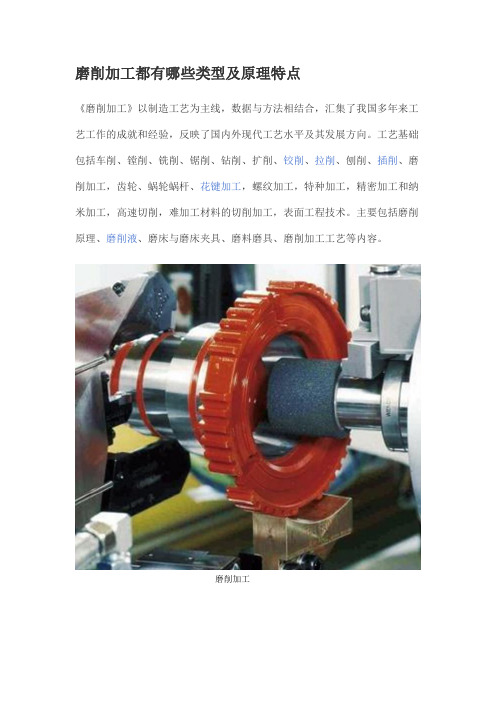
磨削加工都有哪些类型及原理特点《磨削加工》以制造工艺为主线,数据与方法相结合,汇集了我国多年来工艺工作的成就和经验,反映了国内外现代工艺水平及其发展方向。
工艺基础包括车削、镗削、铣削、锯削、钻削、扩削、铰削、拉削、刨削、插削、磨削加工,齿轮、蜗轮蜗杆、花键加工,螺纹加工,特种加工,精密加工和纳米加工,高速切削,难加工材料的切削加工,表面工程技术。
主要包括磨削原理、磨削液、磨床与磨床夹具、磨料磨具、磨削加工工艺等内容。
磨削加工磨削加工1、外圆磨削主要在外圆磨床上进行,用以磨削轴类工件的外圆柱、外圆锥和轴肩端面。
磨削时,工件低速旋转,如果工件同时作纵向往复移动并在纵向移动的每次单行程或双行程后砂轮相对工件作横向进给,称为纵向磨削法。
如果砂轮宽度大于被磨削表面的长度,则工件在磨削过程中不作纵向移动,而是砂轮相对工件连续进行横向进给,称为切入磨削法。
一般切入磨削法效率高于纵向磨削法。
如果将砂轮修整成成形面,切入磨削法可加工成形的外表面。
2、内圆磨削主要用于在内圆磨床、万能外圆磨床和坐标磨床上磨削工件的圆柱孔、圆锥孔和孔端面。
一般采用纵向磨削法。
磨削成形内表面时,可采用切入磨削法。
在坐标磨床上磨削内孔时,工件固定在工作台上,砂轮除作高速旋转外,还绕所磨孔的中心线作行星运动。
内圆磨削时,由于砂轮直径小,磨削速度常常低于30米/秒、耐磨性是普通砂轮的20-100倍,极大的减少了砂轮的修正及更换频率。
3、平面磨削主要用于在平面磨床上磨削平面、沟槽等。
平面磨削有两种:用砂轮外圆表面磨削的称为周边磨削,一般使用卧轴平面磨床,如用成形砂轮也可加工各种成形面;用砂轮端面磨削的称为端面磨削,一般使用立轴平面磨床。
4、无心磨削一般在无心磨床上进行,用以磨削工件外圆。
磨削时,工件不用顶尖定心和支承,而是放在砂轮与导轮之间,由其下方的托板支承,并由导轮带动旋转。
当导轮轴线与砂轮轴线调整成斜交1°~6°时,工件能边旋转边自动沿轴向作纵向进给运动,这称为贯穿磨削。
- 1、下载文档前请自行甄别文档内容的完整性,平台不提供额外的编辑、内容补充、找答案等附加服务。
- 2、"仅部分预览"的文档,不可在线预览部分如存在完整性等问题,可反馈申请退款(可完整预览的文档不适用该条件!)。
- 3、如文档侵犯您的权益,请联系客服反馈,我们会尽快为您处理(人工客服工作时间:9:00-18:30)。