水泥回转窑煅烧过程中常见故障的成因及处理
水泥窑煅烧工艺异常情况原因分析及处理措施
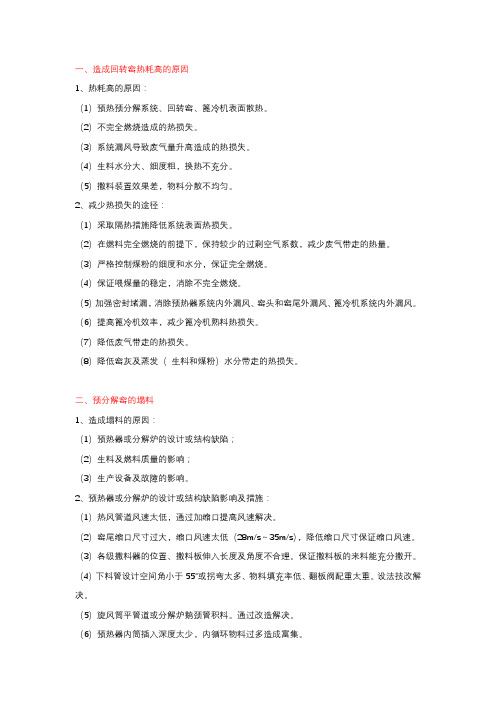
一、造成回转窑热耗高的原因1、热耗高的原因:(1)预热预分解系统、回转窑、篦冷机表面散热。
(2)不完全燃烧造成的热损失。
(3)系统漏风导致废气量升高造成的热损失。
(4)生料水分大、细度粗,换热不充分。
(5)撒料装置效果差,物料分散不均匀。
2、减少热损失的途径:(1)采取隔热措施降低系统表面热损失。
(2)在燃料完全燃烧的前提下,保持较少的过剩空气系数,减少废气带走的热量。
(3)严格控制煤粉的细度和水分,保证完全燃烧。
(4)保证喂煤量的稳定,消除不完全燃烧。
(5)加强密封堵漏,消除预热器系统内外漏风、窑头和窑尾外漏风、篦冷机系统内外漏风。
(6)提高篦冷机效率,减少篦冷机熟料热损失。
(7)降低废气带走的热损失。
(8)降低窑灰及蒸发(生料和煤粉)水分带走的热损失。
二、预分解窑的塌料1、造成塌料的原因:(1)预热器或分解炉的设计或结构缺陷;(2)生料及燃料质量的影响;(3)生产设备及故障的影响。
2、预热器或分解炉的设计或结构缺陷影响及措施:(1)热风管道风速太低,通过加缩口提高风速解决。
(2)窑尾缩口尺寸过大,缩口风速太低(28m/s~35m/s),降低缩口尺寸保证缩口风速。
(3)各级撒料器的位置、撒料板伸入长度及角度不合理。
保证撒料板的来料能充分撒开。
(4)下料管设计空间角小于55°或拐弯太多、物料填充率低、翻板阀配重太重。
设法技改解决。
(5)旋风筒平管道或分解炉鹅颈管积料。
通过改造解决。
(6)预热器内筒插入深度太少,内循环物料过多造成富集。
3、生料及燃料质量波动的影响及措施:有害成分碱、硫循环富集,物料易烧发粘、煤粉不完全燃烧等导致旋风筒内壁结皮或附着在旋风筒内壁的物料出现塌料。
通过配料及工艺操作调整解决。
4、生产操作及设备故障的影响及措施:(1)开窑时的低温、长火焰、低产量、慢窑速导致管道风速低,产生积料或在预热器内富集导致塌料。
采取快升温、加大料、提窑速的方法操作。
(2)窑、炉风量不平衡,窑内通风不足,缩口风速过低,导致塌料。
回转窑常见故障及其处理办法

弹簧板焊缝开裂
重新找正、补焊
传动小齿轮磨损严重,产生台阶。 更换小齿轮
基础地脚螺栓松动
紧固地脚螺栓
窑筒体振动引起
见前述,对症处理
窑筒体 开裂
表面温度太高或红窑烧损窑筒体, 窑筒体焊补,加固烧焊 强度和刚度削弱。
某档托轮顶力过大
正确调整托轮,减轻负荷。
窑筒体钢板材质有缺陷或接口焊缝 用金属探伤器检查内部缺
漏风严重 4)大小齿轮、托轮与轮带接触不良 5)主传动电机故障 6)托轮移位或托轮轴线与窑中心线不平行,造成内力过大。
7)在联锁的情况下,系统自动按照程序控制要求,进行跳 停保护,在此情况下,应做相应的处理: 首先立即停停止喂料,停止分解炉喂煤及窑头喂煤, 减风、减少冷却机冷却风量,防止太多的冷风入窑,造成 窑皮垮落,使窑内处于保温状态; 用辅助传动慢转窑,注意窑尾积料; 如果停窑时间较长,不能排出故障,应考虑全系统停车。
常见 故障
掉 砖 红 窑
产生原因
处理方法
窑衬及其镶砌质量不良或腐蚀后过 薄没有按期更换、导致掉砖红窑。
窑皮挂得不好
选用质量高的耐火砖,停窑 补换新砖,提高镶砌质量,
严禁压补。
加强配料工作,提高锻烧操 作水平。
轮带与垫板磨损严重,间隙过大, 严格控制烧成带附近的轮带
窑筒体径向变形增大。
与垫板间隙,间隙增大时要
3. 每班检查一次油位,如果低于油位下限时,必须立 即加油至其上限。
4. 发现漏油时,应立即采取措施止漏,若油漏到基础 上应及时清理,以免侵蚀基础,酿成隐患。
5. 窑经过长期停转后,若再启动,不宜直接使用主传 动,而应先用辅助传动转动1~2圈,然后再用主传动转动, 这时必须注意托轮轴承应预先润滑。
水泥窑常见工艺故障及处理

常见工艺故障及处理:1、预热器分解炉堵塞:现象:①锥体压力突然显示为零;②同时入口与下一级出口温度急升;③如C5堵,烟室、分解炉及C5出口温度急升。
原因判断:①煅烧温度过高造成结皮;②内部结皮塌料高温物料来不及排出而堵塞在缩口处;③拉风量不足,排风不流畅或拉风变化引起平台积料塌落;④预热器内部耐火材料或内筒脱落掉卡在锥体部位;⑤翻板阀失灵;⑥漏风严重引起结块;⑦煤粉燃烧不好,C5内仍有煤粉继续燃烧;⑧生料喂料波动过大。
处理措施:在发现锥体压力逐渐变小时,就应及时进行吹扫和加强捅堵,同时减料和调整操作参数。
当锥体压力为零时,应立刻止料停窑处理。
2、烟室结皮现象:①顶部缩口部位结皮:烟室负压降低,三次风分解炉出口负压增大,且负压波动很大。
②底部结皮:三次风、分解炉出口及烟室负压同时增大。
窑尾密封圈外部伴随有正压现象。
原因判断:①温度过高;②窑内通风不良;③火焰长,火点后移;④煤质差,硫含量高,煤粉燃烧不好;⑤生料成份波动大,KH忽高忽低;⑥生料中有害成份(硫、碱)高;⑦烟室斜坡耐火材料磨损不平整,造成拉料;⑧窑尾密封不严,掺入冷风。
处理措施:①窑运转时,要定时清理烟室结皮,可用空气炮清除,效果较为理想,如果结皮严重,空气炮难以起作用时,从壁孔人工清除,特别严重时,只能停窑清理。
②在操作中严格执行要求的操作参数,三班统一操作,稳定热工制度,防止还原气氛出现,确保煤粉完全燃烧。
当生料和煤粉波动较大时,更要特别注意必要时,可适当降低产量。
3、窑内结大蛋现象:①窑尾温度降低,负压增高且波动大;②三次风、分解炉出口负压增大;③窑功率高,且波动幅度大;④C5和分解炉出口温度低;⑤在筒体外面可听到有振动声响;⑥窑内通风不良,窑头火焰粗短,窑头时有正压。
原因判断:①配料不当,SM低IM低,液相量大,液相粘度低;②生料均化不理想,入窑生料化学成分波动大,导致用煤量不易稳定,热工制度不稳,此时易造成窑皮粘结与脱落,烧成带窑皮不易保持平整牢固,均易造成结大蛋;③喂料量不稳定;④煤粉燃烧不完全,煤粉到窑后烧,煤灰不均匀掺入物料;⑤火焰过长,火头后移,窑后局部高温;⑥分解炉温度过高,使入窑物料提前出现液相;⑦煤灰份高,细度粗;⑧原料中有害成份(碱、氯)高。
回转窑常见故障原因及排除
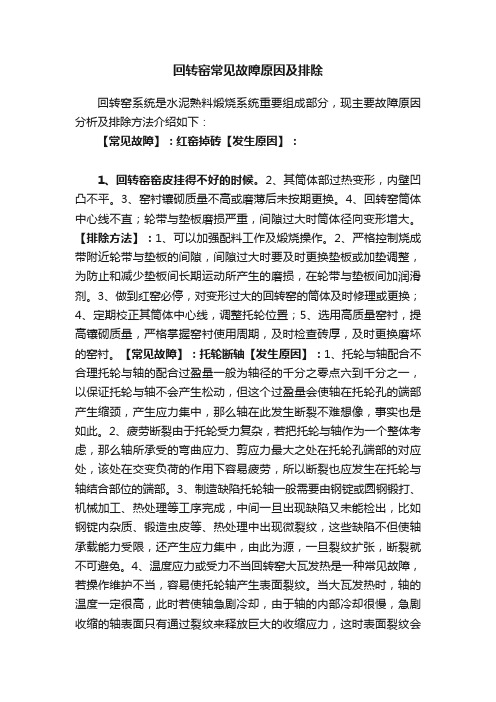
回转窑常见故障原因及排除回转窑系统是水泥熟料煅烧系统重要组成部分,现主要故障原因分析及排除方法介绍如下:【常见故障】:红窑掉砖【发生原因】:1、回转窑窑皮挂得不好的时候。
2、其筒体部过热变形,内壁凹凸不平。
3、窑衬镶砌质量不高或磨薄后未按期更换。
4、回转窑筒体中心线不直;轮带与垫板磨损严重,间隙过大时筒体径向变形增大。
【排除方法】:1、可以加强配料工作及煅烧操作。
2、严格控制烧成带附近轮带与垫板的间隙,间隙过大时要及时更换垫板或加垫调整,为防止和减少垫板间长期运动所产生的磨损,在轮带与垫板间加润滑剂。
3、做到红窑必停,对变形过大的回转窑的筒体及时修理或更换;4、定期校正其筒体中心线,调整托轮位置;5、选用高质量窑衬,提高镶砌质量,严格掌握窑衬使用周期,及时检查砖厚,及时更换磨坏的窑衬。
【常见故障】:托轮断轴【发生原因】:1、托轮与轴配合不合理托轮与轴的配合过盈量一般为轴径的千分之零点六到千分之一,以保证托轮与轴不会产生松动,但这个过盈量会使轴在托轮孔的端部产生缩颈,产生应力集中,那么轴在此发生断裂不难想像,事实也是如此。
2、疲劳断裂由于托轮受力复杂,若把托轮与轴作为一个整体考虑,那么轴所承受的弯曲应力、剪应力最大之处在托轮孔端部的对应处,该处在交变负荷的作用下容易疲劳,所以断裂也应发生在托轮与轴结合部位的端部。
3、制造缺陷托轮轴一般需要由钢锭或圆钢锻打、机械加工、热处理等工序完成,中间一旦出现缺陷又未能检出,比如钢锭内杂质、锻造虫皮等、热处理中出现微裂纹,这些缺陷不但使轴承载能力受限,还产生应力集中,由此为源,一旦裂纹扩张,断裂就不可避免。
4、温度应力或受力不当回转窑大瓦发热是一种常见故障,若操作维护不当,容易使托轮轴产生表面裂纹。
当大瓦发热时,轴的温度一定很高,此时若使轴急剧冷却,由于轴的内部冷却很慢,急剧收缩的轴表面只有通过裂纹来释放巨大的收缩应力,这时表面裂纹会产生应力集中,在交变应力的作用下,裂纹一旦出现环向扩张,且达到一定程度就会发生断裂。
回转窑内结圈结球的原因及处理方法

各种类型的水泥回转窑都遇到过结圈问题。
结圈使窑该处的横断面积显著减少,严重影响窑内通风,阻碍物料运动,对回转窑的产量、质量、安全运转、煤耗、电耗均有一定影响。
尤其频繁结圈的回转窑,不仅破坏了窑内正常热工制度,而且损害操作人员的身体健康,给生产造成经济损失。
Eg2jexl 引起回转窑结圈的因素很多,它与原料性质、生料成分、燃料的灰分和细度、窑型、窑内还原气氛及热工制度等有关。
在实际生产过程中,煅烧硅酸率高的熟料时,对减少结圈有好处,但是烧硅酸率很高的白水泥熟料也结圈。
至于说煤灰的影响,但所有烧油的水泥回转窑同样也结圈。
所以结圈问题比较复杂。
现结合生产中的体会和认识,谈谈水泥回转窑结圈的预防和处理。
t%k`)p7O1 结圈的形成 LtKR15h,回转窑内形成结圈的因素很多,但液相的产生和固化是结圈的主要形成过程。
而衬料温度、物料温度、煤灰和生料组成又是决定液相的生成和固化的主要因素。
在熟料煅烧过程中,生料在1200℃左右出现液相,在1250℃左右液相粘度开始变小,液相量增加,由于料层覆盖温度突降,加之筒体表面散热,液相在窑壁上凝固下来,形成窑皮。
窑继续运转,窑皮又暴露在高温中而被熔掉下来,再次被物料覆盖,液相又凝固下来,如此周而复始。
如果粘挂上去的多,掉下来的小,窑皮就增厚,反之就变薄。
在正常情况下,窑皮可保持在200mm左右的厚度。
该温度条件及区域内若熔化和固化的过程达到平衡,窑皮就不会增厚。
当熔化的少固化的多,其厚度增长到一定程度,即形成圈。
当衬料与物料的温差大时,在足够液相的条件下,圈体越结越厚。
ma) + G!1.1 前结圈的形成 Gb"kl .j前结圈(又称窑口圈),是结在回转窑烧成带末端部位的圈。
在正常煅烧条件下,物料温度为1350~1450℃,液相量约为24%,其粘度较大。
当熟料离开烧成带时,液相开始冷却,进入冷却带的液相已基本固化。
在烧成带和冷却带的交界处存在着较大的温差,窑口物料温度高于窑皮温度。
回转窑常见故障及方案

回转窑常见故障及处理方法一.掉转红窑:1.窑衬及其镶砌质量不良或腐蚀后过薄没有按时更换,导致掉转红窑?方法:选用质量高的耐火砖,停窑补换新砖,提高镶砌质量,严禁补压。
2.窑皮挂的不好?方法:加强配料工作,提高煅烧操作水平。
3.轮带与垫板磨损严重,间隙过大,窑筒体径向变形增大?方法:严格控制烧成带附近的轮带与垫板间隙,间隙增大时要及时更换垫板或加垫调整。
4.窑体中心线不直?方法:定期校正窑体中心线。
5.窑筒体局部过热变形,内壁凹凸不平?方法:红窑必停,对变形过大的窑筒体及时整修或更换。
二.窑筒体振动:1.窑筒体受热不匀,弯曲变形过大,托轮脱空?方法:正确调整托轮。
2.大小齿轮齿合间隙过大或过小?方法:调整大小齿轮的齿合间隙。
3.大齿圈接口螺栓松动或断落?方法:紧固或更换螺栓。
4.弹簧板焊缝开裂?方法:重新找正焊补。
5.传动小齿轮磨损严重,产生台阶?方法:更换小齿轮。
6.基础地脚螺栓松动?方法:紧固地脚螺栓。
三.窑筒体开裂:1.表面温度太高或红窑烧损窑筒体,强度和刚度削弱? 方法:窑筒体补焊,加固烧焊。
2.某档托轮顶力太大?方法:正确调整托轮,减轻负荷。
3.窑筒体钢板材质有缺陷或接口焊缝质量差?方法:探伤检查内部缺陷四.窑筒体弯曲偏斜:1.突然停窑,长时间没有转动?方法:将窑弯出做一记号,等窑转到上面停窑数分钟使其复原。
2.窑墩基础下沉,托轮位置发生移动?方法:根据测量数据调整托轮位置五.托瓦衬瓦过热:1.窑中心线不直,衬瓦受力过大?方法:校正中心线,调整托轮受力情况。
2.托轮不正确歪斜,轴承推力过大?方法:调整托轮位置。
3.轴承内冷却水管漏水,用油不当或润滑油变质,以及油内混有其他杂物?方法:换油,修理水管,清洗衬瓦。
4.带油勺发生故障或油盘油沟堵塞?方法:清理油勺,修复带油勺。
六.电动机振动:1.地脚螺栓松动?方法:紧固地脚螺栓。
2.电动机与联轴器中心线不同心? 方法:校正中心线。
3.轴承损坏?方法:更换轴承,检查,调整间隙。
回转窑的常见故障及处理措施
回转窑的常见故障及处理措施一、温度指示误差大故障原因:1.热电偶被物料糊住;2.热电偶被烧断。
处理措施:1.清理积料;2.更换热电偶。
二、压力指示偏低故障原因:1.测压管被粉尘堵塞;2.旋风筒积料。
处理措施:1.用压缩空气吹扫测压管;2.用压缩空气吹扫旋风筒锥部。
三、跑生料故障原因:1.窑尾温度下降过大,喂煤量过少;2.预热器塌料,生料涌入烧成带,窜出窑头;3.火头被生料压缩,窑头温度下降,窑头负压波动,窑电流下降,窑内发浑,篦下温度高,窑头、冷却机冒灰。
处理措施:1.减喂料,减窑速;2.当出现跑生料预兆时或跑生料前期,可适当加煤。
当跑生料已成事实,窑头温度下降较大,宜适当减少喂料喂煤。
待电流及烧成带温度呈上升趋势时,即可加料,提高窑速,加料幅度不宜过大。
四、清理结皮故障原因:1.窑头正压太大;2.跑生料;3.冷却机堆雪人。
处理措施:1.放慢篦床速度,加大窑头抽风;2.减料、减煤、减风,大慢车;3.见冷却机“堆雪人”故障处理。
五、预热器塌料故障原因:1.总排风量突然下降;2.锥体负压突然降低;3.窑尾温度下降幅度很大;4.窑头负压减小,呈正压。
处理措施:大塌料按跑生料故障处理,小塌料可适当增加窑头喂煤,或不作处理。
六、窑筒体温度低故障原因:窑皮太厚。
处理措施:1.窑打快车;2.改变入窑生料率值,提高硅值,降低铝率。
七、窑体温度高故障原因:1.掉窑皮;2.耐火砖薄;3.烧成带温度高;4.入窑生料率值不当,窑皮难挂;5.烧成带掉砖引起红窑。
处理措施:1.移动冷却风机,冷却高温区;2.调节喷煤管内外风改变火点,如筒体温度高于400℃还有上升趋势,停窑换砖;3.保证生料分解率,减轻窑头压力;4.提高铝率,提高烧成带温度,窑速、喂料量低一些;5.停窑补砖。
八、预热器锥体堵塞故障原因:1.下料翻板阀长期窜风,下锥体结皮;2.分解炉煤粉未充分燃烧,物料粘性增大,逐步积于锥体,未及时清堵;3.锥体负压急剧减少,下料温度下降,出口温度上升。
水泥窑煅烧异常情况分析及操作
1、熟料中的f-CaO偏高A、原因:生料成份偏高(KH高,n过高,熔剂矿物过低),生料不均匀,生料细度过粗,煤发热量不均匀,分解率偏低,头煤使用过少等。
B、措施与办法(1)将投料量及窑速适当降低些,先稳住质量。
(2)如火焰细长,窑烧成温度不足,可将火焰调节粗大,提高火焰温度。
(3)若分解率偏低,将分解率适当提高(分解炉出口温度提高)。
(4)若因烟室负压偏低,导致f-CaO偏高时,则检查烟室缩口处结皮情况,及时清除。
(5)若头煤过少,易结大蛋,中部生烧,将头煤使用量增加些。
(6)若因掉窑皮而导致f-CaO偏高,则将窑皮挂平整些,杜绝掉窑皮,稳定头温和炉温。
(7)若因煤粉燃烧不完全时,是将中心风开大些,旋流风开大些。
(8)窑内通风不畅时,将三次风阀关小些。
(9)火焰不顺畅,出现还原气氛时,将总风拉大些(开大高温风机液耦)(10)若因料层过厚结粒过大导致f-CaO偏高,则将窑速开大些。
(11)若煤粉细度、水分较高时,则适当降低。
(12)头煤使用量过多时,减少头煤。
(13)熔剂矿物较高,结粒较大时,将分解炉温度降低些,窑速提高些。
(14)若饱和比料高,结粒细小,则窑速适当降低,投料量降低,分解炉温度升高些。
但如果饱和比过高,就不能过分追求f-CaO合格把炉温控制过高,既要努力降低f-CaO,又要防止出现预热器堵塞等问题。
C、以上原因及措施不能单一而论,f-CaO偏高可能是多种原因共同产生的,或一种诱因引起多种现象,并相互作用形成恶性循环造成f-CaO不能控制,因此对问题要深入分析,找出根本原因,有针对性地采取措施才能解决。
另外可采取的措施有多种,也要认真分析并充分预计各种措施达到的效果,根据情况决定采取的方法。
2、高温风机跳停(以及其它原因引起的窑尾、预热器系统突然出现无负压的情况)。
由于电气或机械原因,高温风机突然出现停机、跳闸的现象或余热发电控制的窑尾、窑头主管道阀门突然关闭的现象,对人员及窑的安全有严重影响。
回转窑窑况的原因及处理
回转窑窑况的原因及处理大倾角皮带因预热器溢料而造成破损故障现象:预热器入口处溢料,导致皮带停止运转而电机正常运转,皮带与头、尾轮产生磨擦。
原因分析:1.预热器料位计上限位故障。
2.设备保护系统失灵。
3.岗位工与中控工责任心不强。
预防及解决措施:1.岗位工与中控工要勤沟通,掌握当班生产计划及每次上料所需的时间。
2.上料时岗位工要对所辖区域内的设备进行监护,防止预热器入口处溢料。
3.上岗时,岗位工与中控工一旦发现皮带机不转时,要立即停机,并及时通知调度室,以防止皮带与头、尾轮磨擦产生损坏,造成重大生产事故。
窑体弯曲出现刮、卡现象原因:1.在停窑初期,窑内温度较高未及时转窑。
2.烘窑时,遇到雨天或雪天,造成窑体受热不均。
3.停窑后长时间不转窑。
4.因停电,设备故障或不按操作规程进行操作导致回转窑突然停转,石灰石集中在下部,局部高温。
影响:1.窑位窜动,影响窑头、窑尾密封。
2.窑体受力不均,震动大易损坏传动机构。
3.易损坏托轮。
防止及处理方法:1.停电时,及时启动备用电源转窑(15min以内),防止回转窑停转时间过长。
2.烘窑时,如遇到雨天或雪天应立即启动辅传转窑,使窑筒体受热均匀。
3.通常弯曲的凸向部分在下。
如弯曲不大,可将窑筒体弯曲部分向上,稍停片刻加热弯曲部分的筒体。
温度较高时,需慢转窑几周后,再使弯曲的凸向部分停在上方。
如此反复进行,直至基本复原为止。
4.如果筒体弯曲较大,拖轮与轮带有较大间隙,电机无法启动,应考虑大修处理。
5.严格按操作规程进行标准化操作。
结圈原因:1.石灰石中小粒灰石比例大,杂质含量多(Sio2、FeO3、A1i2O3.粉尘)。
2.操作不当,工艺参数不合理,致火点后移、燃烧带伸长使液相过早出现。
3.高温状态下带料停窑。
4.窑温、窑速、给料量不匹配,造成物料在高温区域内停留时间过长。
5.煤气质量差、发热植低、压力波动大,煤气在窑内未充分燃烧,导致煤气在窑尾和预热仓室内继续燃烧。
回转窑掉砖红窑原因分析及处理措施
回转窑掉砖红窑原因分析及处理措施一、故障表现及故障分析回转窑内所有的耐火材料,要满足窑炉对它的一下要求:1、耐火度高;2、热膨胀及重烧线变化小;3、常温耐压强度及高温荷重变形温度高;4、抗热震性、抗渣性、耐磨性及抗震性好;5、尺寸准确、外形整齐等。
水泥回转窑用耐火转是根据回转窑系统各部位的使用条件,并注意选择不同品种的耐火材料进行合理匹配而砌筑在窑上的:A. 窑的卸料口使用硅莫砖以刚玉为骨料的耐火热混凝土,有时也使用碳化硅砖。
B. 窑的进料带一般使用AL2O3,含量为70%~80%的高铝砖、耐热震高铝砖、尖晶石转和镁铬砖。
C. 窑的烧成带普遍使用镁铬转质碱性耐火材料,也有的用高镁铝砖、聚磷酸钠结合镁砖、水玻璃结合镁砖等。
目前大部分使用镁铝尖晶石砖。
D. 过渡带使用以刚玉和50%~80%AL2O3的铝钒制成的高铝砖、直接结合镁铬砖、普通镁铬砖和尖晶石砖等。
E. 分解带(第二过渡带)使用粘土砖、高铝砖、煅烧成结合的轻质转或普通镁铬砖;在与过渡带相连的高磨损、高温度区域内,可采用含量50%~60%的高铝砖,普通鉻铬砖或尖晶石砖。
F. 预热带一段一般使用耐碱隔热粘土砖。
G. 预热器及分解炉的直筒、锥体部分以及连接管道内,采用耐碱粘土转及硅铝质耐磨转,并加隔热复合层,以及源砌筑;顶盖部分可采用火转挂顶,背衬矿棉,也可采用混凝土浇注;各处弯头多使用浇注料;窑尾上什管道等处使用结构致密的半硅质粘土砖。
H. 冷却机系统使用耐火转、轻质浇注料、隔热转、隔热板材等,下料喉部区域及高温区采用普通镁铬砖、高强高铝砖和普通高铝砖;中低温区域可采用粘土转等。
当具备下列情况之一时,回转窑就可能发生掉砖红窑现象而被迫停窑处理。
(一)、回转窑所用的耐火砖质量很差,不具备工业窑炉对耐火砖的起码要求;或未按使用场合进行匹配与否的选择;(二)、窑衬的镶砌不规范,砌筑质量差;或者镶砌方法选择不当,如采用横向环砌法,方法虽简单,技术容易掌握、镶砌速度也快,但当砖缝超过一定范围时,就容易从环内掉转,严重时整环砖都有脱落的危险;(三)、窑衬砌筑质量尚可,但窑皮未挂好,对耐火砖没有保护好;(四)、回转窑煅烧操作不当,如窑点火后升温速度过快等;(五)、喂煤过多,喷煤燃烧器净风旋流风比例过高,致使局部高温也会导致掉砖红窑。
- 1、下载文档前请自行甄别文档内容的完整性,平台不提供额外的编辑、内容补充、找答案等附加服务。
- 2、"仅部分预览"的文档,不可在线预览部分如存在完整性等问题,可反馈申请退款(可完整预览的文档不适用该条件!)。
- 3、如文档侵犯您的权益,请联系客服反馈,我们会尽快为您处理(人工客服工作时间:9:00-18:30)。
水泥回转窑煅烧过程中常见故障的成因及处理(1)
摘要:回转窑煅烧过程中出现的结圈,堆雪人等故障,其成因是非常复杂的,要针对性的实
施处理方法。
关键词:回转窑煅烧故障处理
我公司5000t/d熟料水泥生产线于2010年10月投产以来,由于矿山不能正常投用,原材料收购民采,入窑生料成分波动太大,给生产带来诸多麻烦。
煅烧过程中结圈,堆雪人等时有发生。
为了适用厂里现状,满足生产需要,我们精心组织,认真分析调整。
本文主要介绍一下,回转窑煅烧过程中出现的结圈,堆雪人等故障的成因和处理。
一、回转窑煅烧过程中的一般故障成因、分析和防范措施
(一)原因:1.窑尾温度过高;2.熟料冷却过慢;3. 燃料在烧成带的不完全燃烧;4.
火焰过长;5. 氯含量高;6. 硫含量高;7. 碱含量高;8. 设备的限制。
(二)分析:1. 取样;2. 关注样品的温度,风量,水分的一致性;3. 关注样品的代
表性;4. 出现圈或雪人前后的操作记录对比
(三)措施:1. 调整原料及燃料;2. 控制氯,碱,硫含量的内循环。
A,安装旁路放风系统。
B,减少窑灰的入窑量(比如窑灰可作为水泥的混合材)。
C,确定循环周期。
3. 调整喷煤管(保证熟料的冷却,缩短烧成带的长度,保证燃料的完全燃烧,喷煤管位于窑中心位置。
);4. 提高窑速;5. 保持稳定的二次风温
二、二次风温与火焰以及窑圈的关系
在窑系统的操作中,我们对系统拉风,分解炉出口温度,窑速,窑电流,喷煤管的调整等都比较重视,而对篦冷机的操作:稳定的厚料层,稳定的二次风温,稳定的窑头罩负压重视不够,对篦冷机一段篦速,窑头排风机阀门的调整比较随意,其实回转窑出现的很多问题
都是因为二次风温波动引起的。
我们都知道气体体积随温度变化而变化,但我们在操作时却常常会忘记这种关系。
却说:“我并没有提高风量?”“火焰扫窑皮了,而昨天并不是这样,肯定有谁调喷煤管了?”。
其实这都是因为二次风温的变化引起了窑况变化的缘故。
当二次风温提高时,二次风量及风速也同时提高,高风速就可能把二次风和粉尘带到窑头罩的顶部,因此在窑头罩的底部才表现为负压。
同时当二次风温变化时,会造成火焰向上或向下的变化。
当然二次风温的提高有助于燃料的燃烧,但我们更应重视它对火焰形状的影响。
正常的二次风温能够保证较好的火焰形
状,此时的风温为1000度左右,风速为~5m/s。
二次风温降到800度左右,相应风速为~4m/s,火焰的头部就可能下垂,不再在窑的中心燃烧而冲击物料。
而如果喷煤管在第4象限更接近料面时,这种冲击会更加明显。
当二次风温升到1250度左右,相应风速为~7m /s,火焰就可能上升,此时烧成带温度会降低,窑电流下降,调整不及时就有窜生料的可能。
上述几个较极端的例子表明:保持恒定的二次风温比追求更高的二次风温更加重要。
通常我们会尝试达到更高的二次风温,却造成二次风温时高时低的循环,从而影响火焰形状的稳定及燃料的完全燃烧,熟料可能在缺氧下锻烧,熟料冷却慢,飞砂料增多,窑内形成圈。
同时应牢记两点:测得的二次风温往往因为熟料的辐射热而偏高,二次风温的变化常常是因
为一段篦速的调整而引起。
二次风温的波动是回转窑结圈的主要原因之一。
操作中必须保持喷煤管的位置及火焰的稳定。
结圈的位置随烧成带的长短变化,此处主要是已分解的生料,液相和固态生料组成,它们很容易形成浮窑皮,如果生料量,生料分解率,火焰形状或长度发生变化,很容易跨落。
这些浮窑皮的存在对熟料的烧结是有帮助的,它能提高此处的气体速度,有助于生料的混合,
阻止生料过快进入烧成带。
三、堆雪人的情况
生料配料不当造成飞沙了的现象是篦冷机堆雪人的根本原因,未完全燃烧的煤粉粒发生二次燃烧。
为了强化煅烧提高烧成温度,一般情况下会增加煤粉的用量,由于过多的煤粉用量,很容易造成煤粉燃烧不透被裹入熟料中,在窑内产生飞砂熟料结粒差不均匀的情况下,部分未燃烧的煤粉随熟料一起进入冷却机,在受大窑旋转和高速气流的影响与细颗粒“飞沙”料一起和结粒大的熟料颗粒发生离析,而堆积在蓖冷机前端的蓖板上,由于冷却机内风温高、氧气含量充足,未完全燃烧的煤粉颗粒发生二次燃烧,导致细颗粒熟料表面出现二次高温和液相出现,同时由于细颗粒之间的通风率差,蓖下风机不易吹透,细小颗粒无法尽快冷却,
使得熟料粘结在前端的蓖板
,产生堆雪人。
窜生料也会形成堆“雪人”现象,窜出的生料含有相当一部分未燃烧的煤粉,同样会产生大小颗粒的离析现象,在蓖冷机内因氧气密度大,温度高同样会产生二次燃烧,使熟料在蓖冷机内继续进行反应,导致细小熟料或为烧透的熟料颗粒表面产生液相,在风机无法吹透的情况下产生“堆雪人”现象。
四、预热器的结皮情况
首先是烟室的结皮,这同样是燃料的不完全燃烧,一氧化碳偏高,尾温偏高造成的。
如果漏风的话,还会造成碱,硫在此处的富集。
碱,硫在烧成带为气态,随着废气进入烟室,一般正常窑尾温度会使碱,硫继续保持为气态,如果温度降低(漏风)则变成液态形成结皮。
如果入窑生料的分解率偏高,也会造成C4AF的液相提前出现而结皮。
当喂料量大,烟室粉尘浓度高时,这些液相会附着在生料上,而不会在墙上结皮。
碱,硫在气态或固态都不会造成结皮,旁路放风就是利用这个原理,让抽出的废气快速冷却,使碱,硫直接从气态变成固态,而不至于在旁路放风的冷却室大量结皮。
一般旁路放风能收集0.5~2%的生料,20~25%的SO3,4.5~5%的K2O。
从而保证预热器系统的稳定运行。
从上面的分析我们可以看出:篦冷机料层不稳定,造成二次风温波动,从而引起火焰形状的变化,燃料的不完全燃烧,窑况不稳定,窑内结圈结球。
同时篦冷机料层过厚,熟料冷却慢,造成堆雪人,结窑口圈等现象。
当然,窑况的稳定是一项系统工程,只有各种条件和设备都处于比较优化的状态,才能达到比较理想的效果。