新型陶瓷成型方法
陶瓷成型技术

陶瓷成型技术摘要: 成型技术是制备陶瓷材料的一个重要环节。
陶瓷制造经历数千年历史,直到20世纪中叶因为烧结理论的创立获得了飞速发展。
上世纪七八十年代关于超细粉体制备和表征的发展,促使陶瓷工艺第二次大发展。
当前阻碍陶瓷材料进一步发展的关键之一是成型工艺技术没有突破.压力成型不能满足形状复杂性和密度均匀性的要求。
本文评述了国内外陶瓷现代成型技术,讨论了上述成型方法的基本原理和特点。
关键词:陶瓷, 成型, 技术,进展一引言成型工艺是陶瓷材料制备过程的重要环节之一,在很大程度上影响着材料的微观组织结构,决定了产品的性能、应用和价格[1]。
过去,陶瓷材料学家比较重视烧结工艺,而成型工艺一直是个薄弱环节,不被人们所重视。
现在,人们已经逐渐认识到在陶瓷材料的制备工艺过程中,除了烧结过程之外,成型过程也是一个重要环节。
在成型过程中形成的某些缺陷(如不均匀性等)仅靠烧结工艺的改进是难以克服的,成型工艺已经成为制备高性能陶瓷材料部件的关键技术,它对提高陶瓷材料的均匀性、重复性和成品率,降低陶瓷制造成本具有十分重要的意义。
本文简单回顾了陶瓷成型方法的发展及技术特点。
二成型方法1 胶态浇注成型[2]胶态浇注成型是将具有流动性的浆料制成可自我支撑形状的一种成型方法。
该法利用浆料的流动性,使物料干燥并固化后得到一定形状的成型体。
主要包括以下几种方法:①注浆成型(Slip Casting)是将浆料注入具有渗透性的多孔模具(如石膏)中,模具内部的形状即为所需要的素坯形状,利用多孔模具的毛细管力而使液体排除,从而固化。
注浆成型的模具要具有一定的强度,吸水性好,吸水速度适中。
注浆成型工艺成本低,过程简单,易于操作和控制,但成型形状粗糙,注浆时间较长,坯体密度、强度也不高。
80年代中期,人们在传统注浆成型的基础上,相继发展产生了新的压滤成型(Pressure Filtration)和离心注浆成型(Centrifugal Casting),借助于外加压力和离心力的作用,来提高素坯的密度和强度,而且几乎不需要使用有机添加剂,因而避免了注射成型中复杂的脱脂过程,但由于坯体均匀性差,因而不能满足制备高性能高可靠性陶瓷材料的要求②流延成型(Tape Casting)〔1-2〕也称带式浇注,或刀片法(Doctor-blade)。
高性能新型陶瓷材料的制备与研究

高性能新型陶瓷材料的制备与研究摘要:高性能陶瓷材料的使用温度一般为1400~1500℃,超高温的材料能够达到1800℃以上,主要包含过渡金属的硼化物、碳化物以及石墨、氮化硼等。
高温陶瓷材料主要的优势是熔点较高,具备超高温耐腐蚀性及超高温稳定性,在国防、航天以及容器保护中应用广泛。
目前加强了对Si—B—C—N超高温陶瓷材料的研究,主要应用于超高温涂层材料,制备工艺主要是有机前驱体法,但是因为对超高温稳定机理的理解还需要进一步的加深和研究,其操作严格、成本较高。
因此,加强对新的制备工艺技术的研究,深入探讨超高温稳定化机理将成为未来研究的重要方向和内容。
基于此,对高性能新型陶瓷材料的制备与研究进行研究,以供参考。
关键词:高性能新型陶瓷材料;制备工艺引言从1962年R.L.Coble首先研究并成功生产了高性能的氧化铝复合陶瓷开始,就为复合陶瓷技术开拓了崭新的应用领域。
该类材料不但具备较高的性能,而且耐腐蚀,可在高温高压下正常工作,还拥有其他金属材料所无可比拟的特性,如硬度较高、介电性能优异、低电导率、高温导性好等,从而逐步在照明科技、光学、特种仪表制作、无线电子科技和高温科技等领域得到越来越深入的运用。
1高性能陶瓷材料应用前景陶瓷材料是新材料中的重要分支,在能源、机械、冶金、汽车以及石油化工等各个行业发挥着重要作用,成为工业技术发展中不可或缺的关键材料。
随着社会经济市场的快速发展和国民经济水平的不断提升,工业企业的技术水平也在不断发展和提升,各个行业都迫切的需要大量的高性能陶瓷材料,因此市场前景较为广阔。
陶瓷材料一般情况下分为结构陶瓷、功能陶瓷,有的还分为陶瓷涂层以及陶瓷复合材料等。
目前使用较为广泛的主要是以结构陶瓷和功能陶瓷为主,其中结构陶瓷的优势是耐磨性较强、强度较高,在热机部件、耐磨部件等领域中具有较为广泛的应用。
陶瓷材料在多个领域中都得到了广泛应用,尤其是在高新技术领域,陶瓷材料在其中发挥着非常关键的作用。
多孔陶瓷

多孔陶瓷制备工艺1. 多孔陶瓷概述多孔陶瓷又被称为微孔陶瓷、泡沫陶瓷,是一种新型陶瓷材料,是由骨料、粘结剂和增孔剂等组分经过高温烧成的,具有三维立体网络骨架结构的陶瓷体。
多孔陶瓷是近30年来受到广泛关注的一种新型陶瓷材料,因其基体孔隙结构可实现多种功能特性,所以又称为气孔功能材料。
多孔陶瓷不仅具有良好的化学稳定性及热稳定性.而且还具有优异的透过性、高比表面积、极低的电导率及热导率等性能。
可用作过滤材料、催化剂载体、保温隔热材料、生物功能材料等,目前已经广泛应用于化工、能源、冶金、生物医药、环境保护、航空航天等诸多领域。
多孔陶瓷一般可按孔径大小分为3类:微孔陶瓷(孔径小于2nm)、介孔陶瓷(孔径为2~50nm)及宏孔陶瓷(孔径大于50nm)。
若按孔形结构及制备方法,其又可分为蜂窝陶瓷和泡沫陶瓷两类,后者有闭孔型、开孔型及半开孔型3种基本类型。
根据陶瓷基体材料种类,将其分为氧化铝基、氧化锆基、碳化硅基及二氧化硅基等。
需要指出的是,多孔陶瓷种类繁多,可以基于不同角度进行分类。
2. 多孔陶瓷的制备方法多孔陶瓷是由美国于1978年首先研制成功的。
他们利用氧化铝、高岭土等陶瓷材料制成多孔陶瓷用于铝合金铸造中的过滤,可以显著提高铸件质量,降低废品率,并在1980年4月美国铸造年会上发表了他们的研究成果。
此后,英、俄、德、日等国竞相开展了对多孔陶瓷的研究,已研制出多种材质、适合不同用途的多孔陶瓷,技术装备和生产工艺日益先进,产品已系列化和标准化,形成为一个新兴产业。
我国从20世纪80年代初开始研制多孔陶瓷。
多孔陶瓷首要特征是其多孔特性,制备的关键和难点是形成多孔结构。
根据使用目的和对材料性能的要求不同,近年逐渐开发出许多不同的制备技术。
其中应用比较成功,研究比较活跃的有:添加造孔剂工艺,颗粒堆积成型工艺,发泡工艺,有机泡沫浸渍工艺等传统制备工艺及孔梯度制备方法、离子交换法等新制备工艺。
2.1 多孔陶瓷的传统制备工艺2.1.1 添加造孔剂工艺该工艺通过在陶瓷配料中添加造孔剂,利用造孔剂在坯体中占据一定的空间,然后经过烧结,造孔剂离开基体而成气孔来制备多孔陶瓷。
陶瓷薄板生产工艺过程探讨
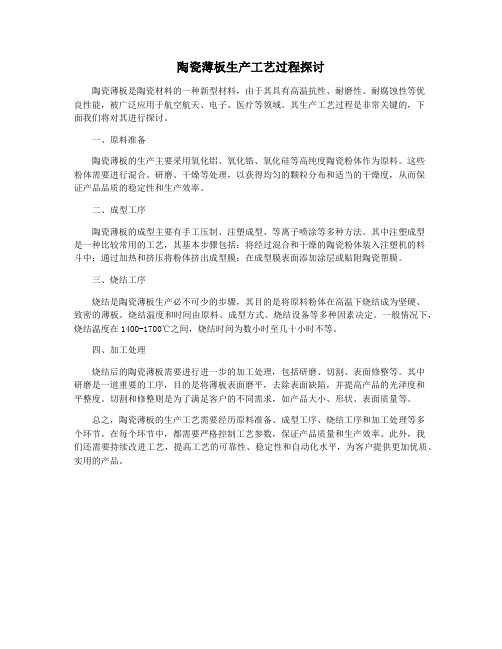
陶瓷薄板生产工艺过程探讨陶瓷薄板是陶瓷材料的一种新型材料,由于其具有高温抗性、耐磨性、耐腐蚀性等优良性能,被广泛应用于航空航天、电子、医疗等领域。
其生产工艺过程是非常关键的,下面我们将对其进行探讨。
一、原料准备陶瓷薄板的生产主要采用氧化铝、氧化锆、氧化硅等高纯度陶瓷粉体作为原料。
这些粉体需要进行混合、研磨、干燥等处理,以获得均匀的颗粒分布和适当的干燥度,从而保证产品品质的稳定性和生产效率。
二、成型工序陶瓷薄板的成型主要有手工压制、注塑成型、等离子喷涂等多种方法。
其中注塑成型是一种比较常用的工艺,其基本步骤包括:将经过混合和干燥的陶瓷粉体装入注塑机的料斗中;通过加热和挤压将粉体挤出成型膜;在成型膜表面添加涂层或贴附陶瓷帮膜。
三、烧结工序烧结是陶瓷薄板生产必不可少的步骤,其目的是将原料粉体在高温下烧结成为坚硬、致密的薄板。
烧结温度和时间由原料、成型方式、烧结设备等多种因素决定。
一般情况下,烧结温度在1400-1700℃之间,烧结时间为数小时至几十小时不等。
四、加工处理烧结后的陶瓷薄板需要进行进一步的加工处理,包括研磨、切割、表面修整等。
其中研磨是一道重要的工序,目的是将薄板表面磨平,去除表面缺陷,并提高产品的光泽度和平整度。
切割和修整则是为了满足客户的不同需求,如产品大小、形状、表面质量等。
总之,陶瓷薄板的生产工艺需要经历原料准备、成型工序、烧结工序和加工处理等多个环节。
在每个环节中,都需要严格控制工艺参数,保证产品质量和生产效率。
此外,我们还需要持续改进工艺,提高工艺的可靠性、稳定性和自动化水平,为客户提供更加优质、实用的产品。
第二章特种陶瓷成型工艺思考题及答案
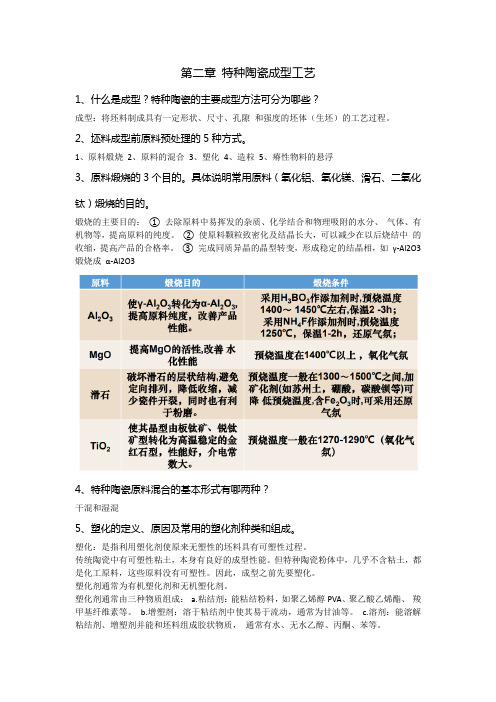
第二章特种陶瓷成型工艺1、什么是成型?特种陶瓷的主要成型方法可分为哪些?成型:将坯料制成具有一定形状、尺寸、孔隙和强度的坯体(生坯)的工艺过程。
2、坯料成型前原料预处理的5种方式。
1、原料煅烧2、原料的混合3、塑化4、造粒5、瘠性物料的悬浮3、原料煅烧的3个目的。
具体说明常用原料(氧化铝、氧化镁、滑石、二氧化钛)煅烧的目的。
煅烧的主要目的:① 去除原料中易挥发的杂质、化学结合和物理吸附的水分、气体、有机物等,提高原料的纯度。
② 使原料颗粒致密化及结晶长大,可以减少在以后烧结中的收缩,提高产品的合格率。
③ 完成同质异晶的晶型转变,形成稳定的结晶相,如γ-Al2O3煅烧成α-Al2O34、特种陶瓷原料混合的基本形式有哪两种?干混和湿混5、塑化的定义、原因及常用的塑化剂种类和组成。
塑化:是指利用塑化剂使原来无塑性的坯料具有可塑性过程。
传统陶瓷中有可塑性粘土,本身有良好的成型性能。
但特种陶瓷粉体中,几乎不含粘土,都是化工原料,这些原料没有可塑性。
因此,成型之前先要塑化。
塑化剂通常为有机塑化剂和无机塑化剂。
塑化剂通常由三种物质组成:a.粘结剂:能粘结粉料,如聚乙烯醇PVA、聚乙酸乙烯酯、羧甲基纤维素等。
b.增塑剂:溶于粘结剂中使其易于流动,通常为甘油等。
c.溶剂:能溶解粘结剂、增塑剂并能和坯料组成胶状物质,通常有水、无水乙醇、丙酮、苯等。
6、塑化剂对坯体性能的影响。
(1)还原作用的影响:将会同坯体中某些成分发生作用,导致还原反应,使制品的性能变坏,特别是易还原的TiO2和钛酸盐。
因此,焙烧工艺要特别注意。
(2)对电性能的影响:由于塑化剂挥发时产生一定的气孔,也会影响到制品的绝缘性能。
粘结剂越多,气孔越多,击穿电压越低。
(3)对机械强度的影响:塑化剂挥发是否完全、塑化剂用量的大小,会影响到产生气孔的多少,从而将影响到坯体的机械强度。
(4)塑化剂用量的影响一般塑化剂的含量越少越好,但塑化剂过低,坯体达不到致密化,也容易产生分层。
工业陶瓷及其成型
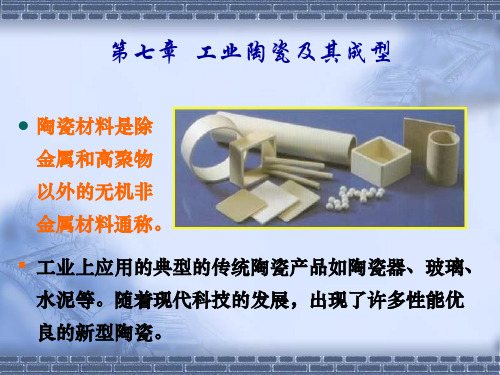
① 氮化硅的制备与烧结工艺
工业硅直接氮化:3Si+2N2→Si3N4 二氧化硅还原氮化:3SiO2+6C+2N2→Si3N4+6CO 烧结工艺 优点 缺点
反应烧结 烧结时几乎没有收缩,能 密度低,强度低,耐蚀
得到复杂的形状 性差 只能制造简单形状,烧 热压烧结 用较少的助剂就能致密化, 强度、耐蚀性最好 结助剂使高温强度降低
1)悬浮料浆的制备。 料浆是陶瓷原料粉体和水组成的悬浮 液。料浆应具有良好的流动性,足够小的粘度,尽可能少 的含水量,弱的触变性(静止时粘度变化小),良好的稳定性 (悬浮性)及良好的渗透(水)性等性能。
2)注浆方法。
实心注浆 如后图a所示。料浆注入模型后,料浆中的 水分同时被模型的两个工作面吸收,注件在两模之间形成, 没有多余料浆排出。 空心注浆如后图a所示。料浆注入模型后,由模型单面 吸浆,当注件达到要求的厚度时,排出多余料浆而形成空 心注件。
氧化锆拉线轮
氧化锆油泵
氧化柱塞
氧化锆球阀
7.2 工业陶瓷的生产过程
工业陶瓷的生产过程主要包括坯体成形前的坯料准备、坯 体成形、烧结、烧结及坯体的后续加工等内容。 1.坯体成形前的准备 首先是利用物理、化学等方法对粉料进行处理获得所 需要规格的粉体;然后按照瓷料的成分,将各种原料进行 称量配料,配料后根据不同的成形方法,混合制备成不同 形式的坯料。 2.坯体成形 成形是将坯料制成具有一定形状和规格的坯体。可采 用的方法有:湿塑成型、注浆成型、模压成型、注射成型、 热压铸成型、等静压成型、塑性成型、带式成型等。
1.按用途的不同分类 1)日用陶瓷:如茶具、缸,坛、盆、罐、盘、碟、碗等。 2)艺术(工艺)陶瓷:如花瓶、雕塑品、器皿、 陈设品等。 3)工业陶瓷:指应用于各种工业的陶瓷制品。又分以下方面: ①建筑一卫生陶瓷: 如砖瓦,排水管、面砖,外墙砖, 卫生洁具等; ②化工(化学)陶瓷: 用于各种化学工业的耐酸容器、 管道,塔、泵、阀以及搪砌反应锅的耐酸砖、灰等; ③电瓷: 用于电力工业高低压输电线路上的绝缘子。电 机用套管,支柱绝缘子、低压电器和照明用绝缘子,以及电 讯用绝缘子,无线电用绝缘子等; ④特种陶瓷: 用于各种现代工业和尖端科学技术的特种 陶瓷制品,有高铝氧质瓷、镁石质瓷、钛镁石质瓷、锆英石 质瓷、锂质瓷、以及磁性瓷、金属陶瓷等。
特种陶瓷概述

特种陶瓷概述摘要本文主要叙述了国内特种陶瓷市场发展和生产现状,讲述了相关的制备方法和最新的相关技术前沿工艺,最后展望了特种陶瓷未来的发展趋势。
关键词特种陶瓷;市场现状;制备工艺;发展规模前言特种陶瓷也称为先进陶瓷、新型陶瓷、高性能陶瓷等,突破了传统陶瓷以黏土为主要原料的界限,主要以氧化物、炭化物、氮化物、硅化物等为主要原料,有时还可以与金属进行复合形成陶瓷金属复合材料,是一种采用现代材料工艺制备的,具有独特和优异性能的陶瓷材料。
已成为现代高性能复合材料的一个研究热点。
特种陶瓷于二十世纪发展起来,在近二、三十年内,新产品不断涌现,在现代工业技术,特别是在高技术、新技术领域中的地位日趋重要。
许多科学家预言:特种陶瓷在二十一世纪的科学技术发展中,必将占据十分重要的地位。
特种陶瓷不同的化学组成和组织结构决定了它不同的特殊性质和功能,可作为工程结构材料和功能材料应用于机械、电子、化工、冶炼、能源、医学、激光、核反应、宇航等领域。
一些经济发达国家,特别是日本、美国和西欧国家,为了加速新技术革命,为新型产业的发展奠定物质基础,投入大量人力、物力和财力研究开发特种陶瓷,因此,特种陶瓷的发展十分迅速,在技术上也有很大突破。
1.发展现状1.1市场情况:与20年前相比,目前我国特陶行业结构变化巨大,私营企业、外资企业的数量和比重迅猛增加,特别是外资企业增长势头迅猛,约占我国全部特陶企业的10%左右。
当前在电子陶瓷行业中,股份制和三资企业市场竞争力最强。
我国特陶市场的开放和市场规模的潜力,吸引许多国外企业纷纷进入,投资不断增加,规模逐步扩大,其投资模式已从最初的产品输入(经销产品)到生产输入(投资设厂),再到应用研究输入(设立实验室),对我国本土特陶企业带来巨大挑战。
1995年我国特种陶瓷产品销售额80亿元人民币(约合10亿美元),其中电子陶瓷约占70%,约56亿元;结构陶瓷占30%,约为24亿元。
相当于日本的1/9、美国的1/5,与欧洲的市场规模相当。
新型陶瓷材料课件

新型陶瓷材料的研发和生产技术难度较大,需要突破关键技术瓶颈, 实现规模化生产。
成本压力
高性能陶瓷材料的生产成本往往较高,难以满足市场需求。降低生 产成本,提高产品竞争力是新型陶瓷材料面临的挑战之一。
国际竞 争
在全球范围内,新型陶瓷材料领域的竞争日益激烈。国内企业需要提 高自身技术水平,拓展国际市场,以应对国际竞争压力。
谢谢您的聆听
THANKS
过滤材料等,应用于环保领域。
02
新型陶瓷材料的制备技术
原料选择与处理
原料选择
新型陶瓷材料的制备首先依赖于精选的原料,如高纯度的氧化物、碳酸盐、硅 酸盐等。这些原料需要具有高的化学纯度及良好的烧结活性。
原料处理
在原料准备阶段,一般需要进行粉碎、球磨、筛分等操作,以获得微细且粒度 分布均匀的粉体。此外,为了改善粉体的烧结活性,往往还需要进行预烧处理。
02
绿色环保趋势
随着环保意识的提高,新型陶瓷材料的环保性将成为重要的发展方向。
例如,研发生产无毒、低污染、可循环使用的陶瓷材料,以满足环保和
可持续发展的需求。
03
功能陶瓷拓展应用领域
功能陶瓷在电子、通讯、生物医疗等领域具有广泛应用。随着技术进步,
功能陶瓷的性能将不断提升,拓展其应用领域。
面临的挑战
烧结技术
无压烧结:无压烧结是在常 压下进行陶瓷坯体的烧结, 通过控制温度和时间,使坯 体发生致密化,达到所需的 物理和化学性能。无压烧结 具有设备简单、成本低等优 点。
热压烧结:热压烧结是在高 温高压下进行的烧结过程, 可以显著缩短烧结时间,提 高材料的致密度和性能。但 热压烧结设备成本高,操作 复杂。
新型陶瓷材料课件
CONTENTS