等离子燃烧技术
大型机组等离子点火及稳燃技术的应用

摘要:结合山西省某扩建电厂(2×200 MW)工程初步设计,对锅炉启动点火、锅炉低负荷助燃的方式进行了探讨和分析,得出了采用等离子点火系统及低负荷稳燃技术节能效果明显的结论。
关键词:等离子点火;稳燃技术;节油节约和替代燃料油,对缓解石油供需矛盾,保障国家经济安全具有重大的战略意义。
国家电力公司制定了节油规划,在规划中明确提出“要加大力度重点抓好等离子点火技术的完善和推广应用,这是火电厂实现大幅度节油的重大技术措施”。
世界上许多国家都在致力于研究等离子点火燃烧器,以期减少火力发电机组的油耗。
目前,等离子点火及稳燃技术已成功应用于近100台电站煤粉锅炉中。
等离子点火在新建机组上应用,节油效果特别明显。
例如内蒙古托克托发电厂600MW机组投产中采用等离子点火,从首次点火至1号机组“168h满负荷试运”完成,等离子点火装置共累计运行超过540h,各项设备均性能稳定、工作正常,初期投入等离子点火系统时,锅炉燃烧效率达95以上。
由于应用了等离子点火系统,在1号机组试运期间为电厂节约燃油达2000多t。
1 等离子点火技术基本原理1.1 等离子点火机理等离子点火装置是利用直流电流在介质气压0.004 MPa~0.03 MPa的条件下接触引弧,并在强磁场控制下获得稳定功率的直流空气等离子体,该等离子体在专门设计的燃烧器中心燃烧筒中形成温度T>5000K的、温度梯度极大的局部高温区,煤粉颗粒通过该等离子“火核”受到高温作用,并在1×10-3s内迅速释放出挥发物,使煤粉颗粒破裂粉碎,从而迅速燃烧,也有助于加速煤粉的燃烧,这样就大大地减少点燃煤粉所需要的引燃能量。
等离子体内含有大量化学活性粒子,如原子(C,H,O)、原子团(OH,H2,O2)、离子(O2-,H2-,OH-,O-,H+)和电子等,可加速热化学转换,促进燃料完全燃烧。
1.2 等离子点火系统等离子点火系统由等离子燃烧器及其输粉系统,直流供电及控制系统,辅助系统和热工监控系统组成。
等离子点火器工作原理

等离子点火器工作原理
等离子点火器是一种常用于点燃燃料的装置,它利用高压电场产生的等离子体来点燃燃料混合物。
其工作原理主要包括等离子体产生、传输和点火三个步骤。
首先,等离子点火器通过高压放电产生等离子体。
当高压电场加在两个电极之间时,电场强度超过气体击穿电压,气体中的自由电子被加速,与气体原子或分子碰撞,将其电离形成等离子体。
这种等离子体具有高能量和高温度,可以用来点燃燃料混合物。
其次,等离子体被传输到燃料混合物中。
等离子体产生后,需要将其传输到燃料混合物中,以点燃燃料。
传输等离子体的方法通常有两种,一种是通过电极直接将等离子体引入燃料混合物中,另一种是利用等离子体的电磁辐射来点燃燃料。
最后,等离子体点燃燃料混合物。
一旦等离子体传输到燃料混合物中,它会引发燃料的燃烧反应。
燃料混合物中的燃料和氧气在高温和高能量的作用下发生燃烧,释放出大量的热能和光能。
这样就完成了等离子点火器的工作,燃料开始燃烧,驱动发动机或其他设备运转。
总的来说,等离子点火器是一种利用高压电场产生等离子体来点燃燃料混合物的装置。
它通过产生、传输和点火三个步骤来完成点火过程。
等离子点火器在内燃机、火花塞点火系统等领域有着广泛的应用,是现代化工、交通运输等领域不可或缺的关键设备。
锅炉等离子点火技术介绍 - 副本
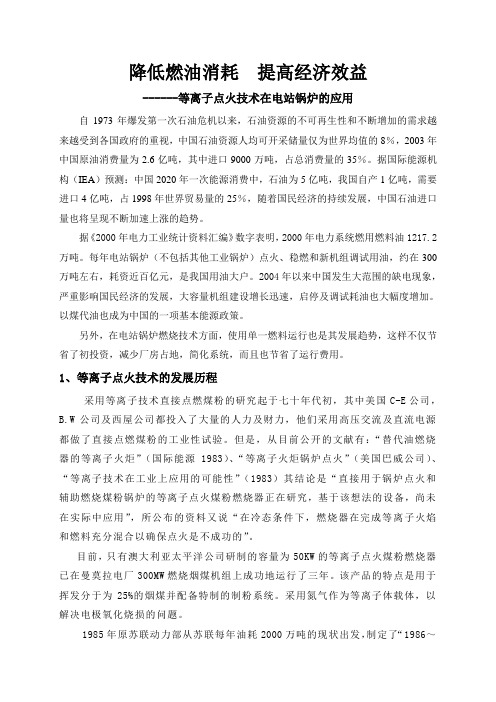
降低燃油消耗提高经济效益------等离子点火技术在电站锅炉的应用自1973年爆发第一次石油危机以来,石油资源的不可再生性和不断增加的需求越来越受到各国政府的重视,中国石油资源人均可开采储量仅为世界均值的8%,2003年中国原油消费量为2.6亿吨,其中进口9000万吨,占总消费量的35%。
据国际能源机构(IEA)预测:中国2020年一次能源消费中,石油为5亿吨,我国自产1亿吨,需要进口4亿吨,占1998年世界贸易量的25%,随着国民经济的持续发展,中国石油进口量也将呈现不断加速上涨的趋势。
据《2000年电力工业统计资料汇编》数字表明,2000年电力系统燃用燃料油1217.2万吨。
每年电站锅炉(不包括其他工业锅炉)点火、稳燃和新机组调试用油,约在300万吨左右,耗资近百亿元,是我国用油大户。
2004年以来中国发生大范围的缺电现象,严重影响国民经济的发展,大容量机组建设增长迅速,启停及调试耗油也大幅度增加。
以煤代油也成为中国的一项基本能源政策。
另外,在电站锅炉燃烧技术方面,使用单一燃料运行也是其发展趋势,这样不仅节省了初投资,减少厂房占地,简化系统,而且也节省了运行费用。
1、等离子点火技术的发展历程采用等离子技术直接点燃煤粉的研究起于七十年代初,其中美国C-E公司,B.W公司及西屋公司都投入了大量的人力及财力,他们采用高压交流及直流电源都做了直接点燃煤粉的工业性试验。
但是,从目前公开的文献有:“替代油燃烧器的等离子火炬”(国际能源1983)、“等离子火炬锅炉点火”(美国巴威公司)、“等离子技术在工业上应用的可能性”(1983)其结论是“直接用于锅炉点火和辅助燃烧煤粉锅炉的等离子点火煤粉燃烧器正在研究,基于该想法的设备,尚未在实际中应用”,所公布的资料又说“在冷态条件下,燃烧器在完成等离子火焰和燃料充分混合以确保点火是不成功的”。
目前,只有澳大利亚太平洋公司研制的容量为50KW的等离子点火煤粉燃烧器已在曼莫拉电厂300MW燃烧烟煤机组上成功地运行了三年。
等离子废气处理工艺原理介绍

等离子废气处理工艺原理介绍等离子体是一种由高温高能量电子和离子组成的气体。
它具有高活性和强氧化性,能够迅速分解和氧化废气中的污染物。
在等离子废气处理工艺中,通常会使用低温等离子体,即介于室温和200°C之间的等离子体。
这样既能减少对设备材料的腐蚀,又能保证良好的处理效果。
1.氧化反应:将废气中的有机物氧化为二氧化碳和水。
等离子能够提供足够的氧化能量,使废气中的有机物通过氧化反应迅速分解和燃烧。
这可以通过等离子中的电子和氧气分子发生碰撞并引发反应来实现。
2.中和反应:将废气中的氨气等碱性物质中和。
废气中常含有一些有机酸或酸性物质,而等离子废气处理工艺中的等离子能够提供丰富的电子和负离子,可以和废气中的酸性物质发生中和反应,将其转化为中性物质。
3.吸附除尘:过滤和除去废气中的固体颗粒物。
等离子废气处理工艺中,通常会设置过滤装置或静电电晕器等设备,以吸附和沉积废气中的固体颗粒物,从而净化废气。
除了上述主要步骤,等离子废气处理工艺还可以通过改变等离子体产生的活性物种种类和浓度来实现对不同污染物的处理。
例如,通过调整等离子体中氧气和水蒸气的浓度,可以降低NOx的浓度。
而通过增加氨气和水蒸气的浓度,可以降低SOx的浓度。
等离子废气处理工艺具有处理效率高、处理速度快、操作简便等优点。
同时,它还可以适用于不同类型的废气处理,如烟气脱硫、废气净化等。
然而,也需要注意到等离子废气处理工艺存在一些局限性,例如需要耗费一定的能源、对设备材料有一定的腐蚀性以及对处理后的废气排放标准的要求等。
总之,等离子废气处理工艺利用等离子体的化学反应和能量释放来对废气中的污染物进行分解和氧化,从而实现废气净化的目的。
它是一种高效、快速、简便的废气处理技术,适用于不同类型的废气处理。
等离子点火

浅谈等离子点火摘要:通过对等离子点火的研究了解,等离子点火煤粉燃烧器的工作原理:首先设定输出电流,当阴极3前进同阳极2接触后,整个系统具有抗短路的能力且电流恒定不变,当阴极缓缓离开阳极时,电弧在线圈磁力的作用下拉出喷管外部,一定压力的空气在电弧的作用下,被电离为高温等离子体。
等离子点火系统的组成及压缩空气系统、冷却水系统、一次风系统的调试。
采用等离子点火,点火和稳燃与传统的燃油相比有经济、环保、高效、简单、安全,几大优点。
关键词:等离子点火原理组成调试优点1.等离子点火煤粉燃烧器的工作原理1.1点火机理等离子点火是利用直流电流(280~350a)在介质气压0.01~0.03mpa的条件下接触引弧,并在强磁场下获得稳定功率的直流空气等离子体,该等离子体在燃烧器的一次燃烧筒中形成t>5000k的梯度极大的局部高温区,煤粉颗粒通过该等离子“火核”受到高温作用,并在10~3秒内迅速释放出挥发物,并使煤粉颗粒破裂粉碎,从而迅速燃烧。
由于反应是在气相中进行,使混合物组分的粒级发生了变化。
因而使煤粉的燃烧速度加快,也有助于加速煤粉的燃烧,这样就大大地减少促使煤粉燃烧所需要的引燃能量e(e等=1/6e油)。
除此之外,等离子体对于煤粉的作用,可比通常情况下提高20%~80%的挥发份,即等离子体有再造挥发份的效应,这对于点燃低挥发份煤粉强化燃烧有特别的意义。
1.2等离子发生器工作原理等离子发生器为磁稳空气载体等离子发生器,它由线圈、阴极、阳极组成。
其中阴极材料采用高导电率的金属材料或非金属材料制成。
阳极由高导电率、高导热率及抗氧化的金属材料制成,它们均采用水冷方式,以承受电弧高温冲击。
线圈在高温250℃情况下具有抗2000v的直流电压击穿能力,电源采用全波整流并具有恒流性能。
其拉弧原理为:首先设定输出电流,当阴极3前进同阳极2接触后,整个系统具有抗短路的能力且电流恒定不变,当阴极缓缓离开阳极时,电弧在线圈磁力的作用下拉出喷管外部。
等离子点火器火焰温度

等离子点火器火焰温度等离子点火器是一种常用的点火设备,它利用高压电场产生的等离子体进行火焰点燃。
而火焰的温度则是等离子点火器的一个重要性能指标。
本文将介绍等离子点火器火焰温度的相关知识,帮助读者更好地了解这一设备的工作原理和应用特点。
一、等离子点火器的工作原理等离子点火器是通过产生高压电场,使空气分子发生电离,形成等离子体,从而实现火焰点燃的。
在等离子体形成的过程中,电子和正离子高速运动,产生了大量的能量。
这些能量转化为热能,使火焰温度升高。
二、等离子点火器火焰的特点1. 高温:等离子点火器产生的火焰温度通常可以达到上千摄氏度,甚至更高。
这种高温火焰可以在极短的时间内点燃燃料,提高点火效率。
2. 稳定:等离子点火器的火焰稳定性较好,不易受外界环境的影响。
即使在风力较大的情况下,火焰也能保持稳定。
3. 易于控制:等离子点火器的火焰温度可以通过调节电场强度和频率来控制。
这使得等离子点火器在不同的应用场景下,可以灵活地适应不同的需求。
三、等离子点火器火焰温度的影响因素等离子点火器火焰温度受多种因素影响,主要包括以下几个方面:1. 电场强度:电场强度越大,电子和正离子的能量越高,火焰温度也越高。
2. 电场频率:电场频率的变化会影响等离子体的形成和运动速度,从而影响火焰温度。
3. 燃料类型:不同的燃料有不同的燃烧特性,对火焰温度有一定的影响。
4. 氧气含量:氧气是燃料燃烧的必要条件,氧气含量越高,火焰温度也越高。
5. 点火距离:点火距离越近,火焰温度越高。
四、等离子点火器的应用领域等离子点火器在许多领域都有广泛的应用。
以下是几个常见的应用领域:1. 燃气燃烧器:等离子点火器可以用于燃气燃烧器的点火,提高点火效率和稳定性。
2. 内燃机:等离子点火器可以用于内燃机的点火系统,提高燃烧效率和动力输出。
3. 工业加热:等离子点火器可以用于工业加热设备,提高加热效率和温度控制精度。
4. 焊接和切割:等离子点火器可以用于焊接和切割工艺中的火焰点燃,提高工艺效率和质量。
锅炉等离子点火技术和小油枪点火技
锅炉等离子点火技术和小油枪点火技术的比较锅炉等离子点火技术是由烟台龙源电力技术有限公司在总结前人工作的基础上,开发成功的锅炉点火及稳燃系统,为电厂节约燃油走出了一条新路子。
该项目2000年通过国家电力公司的鉴定,认为“DLZ-200型等离子点火装置在220t/h燃用贫煤锅炉上直接点火及稳燃是成功的。
该成果解决了多项技术关键问题,达到了世界领先水平”;2002年被科技部等国家五部委授予国家级重点新产品;2003年9月获得中国电力科学技术奖一等奖;2005年3月获得2004年度国家科技进步二等奖。
截至目前,等离子点火及稳燃技术已成功应用近300台电站煤粉锅炉,煤种:贫煤、劣质烟煤、烟煤和褐煤;机组容量等级:50MW、100MW、125MW、200MW、300MW和600MW;燃烧方式:切向燃烧直流燃烧器、墙式燃烧旋流燃烧器;制粉系统类型:钢球磨中储式、双进双出钢球磨直吹式、中速磨直吹式和风扇磨直吹式制粉系统。
小油枪点火技术是在利用等离子点火的某些技术而发明的另一种锅炉点火和稳燃技术,基本原理是用小油枪代替等离子发生器,并辅以煤粉燃烧器,用于锅炉点火和低负荷稳燃。
二者相比,比较如下:a、等离子点火是一个系统工程,与小油枪相比,该系统配置更合理,能满足电厂点火和低负荷稳燃的需要。
不管是等离子点火系统还是小油枪点火系统,都要有系统的概念,没有合理的系统配置,点火系统就不能发挥作用。
尤其是直吹式制粉系统的锅炉,要保证点火系统发挥作用,除了需要点火源(等离子发生器或小油枪)外,还需要设计合理的专用燃烧器、冷炉制粉系统、磨煤机出力控制措施等,否则,就可能出现点火初期磨煤机启动前大量用油烘炉或者升温升压速度快等问题。
烟台龙源公司在多年进行直吹式机组的等离子点火系统改造中,为保证锅炉冷炉启动的成功,采取了多项先进的技术措施。
如:为了保证磨煤机能够直接冷态启动,配套安装了锅炉冷炉制粉系统;为了保证锅炉启动满足升温升压曲线的需要,进行了磨煤机降出力改造;为了保证锅炉的等离子燃烧器能够满足锅炉正常运行的需要,设计了双筒压差平衡燃烧器。
等离子点火系统
等离子点火原理
等离子体 发生器
一级火焰
二级火焰
三级火焰
特制弯头
第三区为强化燃烧区,在一、二区 内挥发分基本燃尽,为提高疏松炭的燃 尽率采用提前补氧强化燃烧措施,提前 补氧的原因在于提高该区的热焓进而提 高喷管的初速达到加大火焰长度提高燃 尽度的目的,所采用的气膜冷却技术亦 达到了避免结焦的目的。 第四区为燃尽区,疏松碳的燃尽率, 决定于火焰的长度。随烟气的温升燃尽 率逐渐加大。
等离子点火燃烧器的优点:
1)经济:采用等离子点火运行和技术维护费仅是使用重 油点火时费用的15%~20%; 2)环保:由于点火时不燃用油品,电除尘装置可以在 点火初期投入,因此,减少了点火初期排放大量烟尘对环 境的污染;另外,电厂采用单一燃料后,减少了油品的运 输和储存环节,亦改善了电厂的环境;
3)高效:等离子体内含有大量化学活性的粒子,如原 子(C、H、O)、原子团(OH、H2、O2)、离子(O2- 、H2-、OH-、O-、H+)和电子等,可加速热化学转 换,促进燃料完全燃烧; 4)简单:电厂可以单一燃料运行,简化了系统,简化了 运行方式; 5)安全:取消炉前燃油系统,也自然避免了经常由于燃 油系统造成的各种事故
等离子点火燃烧器故障处
等离子点火器断弧
(1)运行中发生突然熄弧时,重新拉弧即可,每次启弧间隔不得低于10s。 连续3次启弧不成功,若风压、水压、电流及电压参数均在正常值,仍难
以启弧时,则可能为阴极头烧坏;
(2)一般阴极头使用寿命超过50小时后,偶尔会出现掉弧现象,此时可以重 新启弧;超过80小时后需更换;
其拉弧原理为:首先设定输出电流, 当阴极前进同阳极接触后,整个系统具有 抗短路的能力且电流恒定不变,当阴极缓 缓离开阳极时,电弧在线圈磁力的作用下 拉出喷管外部。 一定压力的空气在电弧的作用下,被 电离为高温等离子体,其能量密度高达 105 ~ 106W/cm2,为点燃不同的煤种 创造了良好的条件。
等离子点火系统及注意事项探讨
等离子点火系统及注意事项探讨摘要:等离子点火技术的成功运用,燃煤火力发电厂大大减少启动燃油的消耗。
节能降耗是火电厂发展的趋势,本文主要介绍了崇信发电厂等离子体点火系统组成、构造、原理、维护注意事项。
关键词:等离子;点火系统;组成;注意事项崇信发电有限责任公司 1、2号锅炉为哈尔滨锅炉厂,采用HG-2145/25.4-YM12型超临界、一次中间再热、单炉膛、前后墙对冲燃烧方式、固态排渣、平衡通风、全钢构架、全悬吊结构Π型变压运行直流锅炉。
1、等离子体点火系统的组成1.1 点火系统有崇信电厂安装的等离子燃烧系统由点火系统和辅助系统两大部分组成。
点火系统由等离子燃烧器、等离子点火器、电源控制柜、隔离变压器、控制系统等组成1.2. 辅助系统有载体风系统、冷却水系统、图像火检系统、冷炉制粉系统、一次风在线监测系统、燃烧器壁温监测系统。
1.3 每台锅炉等离子点火系统共设计有五套等离子点火装置,分别对应A磨煤机五个煤粉燃烧器,系统控制是通过与DCS通讯联系方式,进行等离子点火系统的控制。
1.4 A磨煤机燃烧器在锅炉点火和稳燃期间,该燃烧器具有等离子点火和稳燃功能,可较大减少燃油量;在锅炉正常运行时,该燃烧器出力及燃烧工况与原来保持一致。
系统主要结构部件(图一)2、等离子发生器的构造及原理2.1、构造:点火器为磁稳空气载体等离子发生器,它主要由线圈组件(由导电管绕成的线圈、绝缘材料、进出水接头、导电接头、壳体)、阴极组件(由阴极头、外套管、内套管、驱动机构、进出水口、导电接头等构成)、阳极组件(由阳极、冷却水道、压缩空气载体风通道及壳体等构成)组成。
2.2、原理:首先设定输出电流,当阴极3前进同阳极2接触后,整个系统具有抗短路的能力且电流恒定不变,当阴极缓缓离开阳极时,电弧在线圈磁力的作用下拉出喷管外部。
一定压力的空气在电弧的作用下,被电离为高温等离子体,为点燃不同的煤种创造了良好的条件。
3、等离子系统组成3.1、等离子体点火机理:等离子体是指被电离的气体。
等离子点火器火焰温度
等离子点火器火焰温度等离子点火器是一种常用的点火设备,广泛应用于燃烧实验、工业生产以及火焰喷枪等领域。
作为一种高温点火源,等离子点火器的火焰温度非常高,能够达到数千摄氏度甚至更高。
等离子点火器的工作原理是通过电弧放电产生等离子体,这种高能离子体能够激发气体中的分子和原子,使其跃迁到高能级,然后再回落到低能级时释放出能量,形成火焰。
由于等离子点火器火焰的温度非常高,所以它具有很好的点火效果。
火焰温度是指火焰中燃烧物质的温度,通常用热力学温度来表示。
等离子点火器的火焰温度取决于许多因素,包括气体性质、气体流速、电源电压等。
一般来说,等离子点火器的火焰温度在3000摄氏度至8000摄氏度之间。
这个温度范围非常高,足以使大多数物质燃烧起来。
等离子点火器火焰的高温有许多应用。
首先,它可以用于点燃燃料,如煤气、液化气等。
等离子点火器的高温火焰能够快速点燃燃料,提高燃烧效率,减少污染物的产生。
其次,等离子点火器火焰的高温还可以用于焊接和切割金属。
等离子点火器产生的高温火焰能够将金属加热至熔化点,实现金属的焊接和切割。
此外,等离子点火器的高温火焰还可以用于杀菌消毒、药物合成等领域。
然而,等离子点火器的高温火焰也存在一些问题。
首先,高温火焰会产生辐射热,可能对周围环境造成热辐射损害。
因此,在使用等离子点火器时需要注意安全防护措施,避免热辐射对人身和设备的伤害。
其次,高温火焰还会产生烟雾和有害气体,对环境造成污染。
因此,在使用等离子点火器时也需要注意排放和处理有害气体。
等离子点火器火焰的温度非常高,能够达到数千摄氏度甚至更高。
这种高温火焰具有很好的点火效果,广泛应用于燃烧实验、工业生产以及火焰喷枪等领域。
然而,高温火焰也存在一些问题,需要注意安全防护和环境保护。
合理使用等离子点火器火焰,能够发挥其优势,提高生产效率,保护环境。
- 1、下载文档前请自行甄别文档内容的完整性,平台不提供额外的编辑、内容补充、找答案等附加服务。
- 2、"仅部分预览"的文档,不可在线预览部分如存在完整性等问题,可反馈申请退款(可完整预览的文档不适用该条件!)。
- 3、如文档侵犯您的权益,请联系客服反馈,我们会尽快为您处理(人工客服工作时间:9:00-18:30)。
等离子燃烧技术在泰州电厂2*1000MW超超临界燃煤机组中的应用 泰州电厂 蒋德勇 摘要:本文介绍了等离子燃烧技术的原理,结合泰州电厂选用的设备,从运行的角度介绍了等离子燃烧技术在煤粉锅炉中的应用情况。 关键词:等离子 燃煤机组 超临界 等离子燃烧技术是采用空气等离子体作为点火源,在电弧的作用下,将一定压力的空气电离为高温等离子体,从而点燃煤粉的一种新型燃烧技术。它的出现改变了大型煤粉锅炉点火和稳燃依靠重油、轻油或天然气等燃料来实现的历史。近年来能源紧张,燃油价格不断上涨,为等离子燃烧技术的应用提供了契机。泰州电厂作为国内首批1000MW机组,成功的将等离子燃烧技术应用到实践,实现了锅炉的无油或少油启动,既节约了电厂的成本,又改善了电厂的生态环境。 等离子燃烧器利用直流电流在介质气压0.01~0.03MPa的条件下接触引弧,并在强磁场下获得稳定功率的直流空气等离子体,该等离子体在燃烧器的一次燃烧筒中形成T>5000K的梯度极大的局部高温区。煤粉颗粒通过该等离子“火核”受到高温作用,并在 10-3秒内迅速释放出挥发物,并使煤粉颗粒破裂粉碎,从而迅速燃烧。由于反应是在气相中进行,使混合物组分的粒级发生了变化。因而使煤粉的燃烧速度加快,也有助于煤粉的燃烧。为保护等离子装置本身,需用水冷却阴、阳极和线圈。所需冷却水采用闭式循环水,水压在0.6MPa左右,经等离子冷却水泵加压后进入等离子装置。 等离子点火装置的结构和组成及原理如图1~2所示:
等离子体(2)阴极(5)直线电机(3)线圈(1)阳极(4)可更换阴极头
(9)出水口电弧放电腔
(6)电源
(7)压缩空气进口
(8)进水口
图 1 等离子装置的结构和组成 图2 等离子点火原理图 泰州电厂选用的是哈锅在日本三菱公司技术支持下设计制造的超超临界变压运行直流锅炉。本锅炉采用三菱重工(MHI)开发的低NOx的改进型PM主燃烧器和MACT燃烧技术。燃烧器采用无分隔墙的八角双火焰中心切圆燃烧大风箱结构。全摆动式燃烧器,共设六层三菱低NOx PM一次风喷口,三层油风室,一层燃烬风室、十层辅助风室和四层附加风室(Addition Air)。等离子燃烧器布置在A层燃烧器中,在锅炉点火及稳燃期间,可以替代油枪起到点火和稳燃的作用。在锅炉正常运行中,具有主燃烧器的功能,其出力及燃烧工况与其他层燃烧器一致。由于安装等离子燃烧器,在燃烧器摆角改变时,A层燃烧器不参与摆动,但这并不影响燃烧器摆角对过热器及再热器及过热器的调节。 燃烧器的结构布置如图3所示: 图3 燃烧器的结构布置图 泰州电厂采用沈阳重型机械集团有限责任公司生产的MPS280型中速磨煤机,带有出口分离器,可以在运行中调节煤粉细度。磨的启动采用带载启动,即在启动前先往磨煤机内铺入3~5T的煤,以防止磨煤机在启动过程中产生振动。直接用等离子助燃就牵涉到冷炉时,制粉系统如何启动的问题。为等离子燃烧器提供满足细度、浓度和湿度要求的煤粉是锅炉实现冷态等离子点火启动的必要条件。对于中速磨制粉系统,必须解决锅炉冷态启动时煤粉的来源,可以利用A层一次风煤粉主燃烧器对应的磨煤机制备等离子点火所需的煤粉。我厂燃用烟煤,启动磨煤机的热风温度不高,当燃用校核煤种和设计煤种时,磨煤机入口热风温度为153~220℃即可满足磨煤机启动条件,采用蒸汽加热器加热冷风方式来实现冷炉制粉。加热蒸汽采用辅助蒸汽,压力为:0.7MPa,温度300℃。蒸汽加热器的汽侧和风侧的系统如图4所示:
图4 蒸汽加热器的汽侧和风侧的系统图 下面结合我厂调试及商业运行一段时间以来的情况,谈谈等离子点火技术在电站锅炉中的应用:新建锅炉为了除去过热器及再热器内部的杂物,往往采用吹管的方法,吹管期间,锅炉处于低负荷运行阶段,因此就需要助燃及稳燃。若采用油助燃,将使得吹管成本大幅提高,泰州电厂#1炉吹管及调试期间,由于A磨煤机出现一些问题导致等离子不能投运,采用的是油枪助燃,#2炉则是直接用等离子助燃,没有使用油枪,实现吹管及调试的零用油。从调试及后来的起、停机过程中等离子的应用情况来看,直接用等离子点火,煤粉能较好着火,足以证明等离子能够起到点火源的作用,稳燃的效果也毋庸置疑。等离子装置的拉弧应在通一次风的情况下进行,虽然厂家建议可以在不通风的情况下拉弧10分钟,但从泰州电厂的运行结果来看,不提倡这种做法。等离子运行期间,虽然也出现过一些问题,但解决问题的同时,我们也积累了宝贵的运行经验。 既然采用等离子作为点火源,就必然考虑到等离子点火的安全性,防止锅炉的灭火放炮。对A磨而言,存在两种运行模式,等离子模式及正常模式。正常模式就是采用油枪作为点火源的情况,灭火保护采用的是传统的逻辑。对于等离子模式而言,等离子有自身的火检,此时判断等离子的拉弧情况,作为点火允许,需要八个角同时拉弧成功才允许点火。在等离子模式下运行时,考虑到等离子阴、阳极的寿命等原因引起的灭弧现象,当出现一个角断弧时,为了保证锅炉的安全性,需要对应角的油枪自动投入,若30s内对应角油枪未能投入,则跳闸A磨,锅炉MFT,若出现两个角同时断弧,则直接MFT。从运行的情况来看,出现第一种情况时,锅炉着火还是比较稳定的,没有出现燃烧不稳的情况,可以认为这样的设计是成功的。调试阶段曾经出现过在500MW以上出现一个角断弧,油枪联投的情况,考虑到此时已经不需要稳燃,故后来在等离子的逻辑中与上了负荷条件,即负荷在350MW以上时,等离子断弧不影响A磨的运行。这样的逻辑不仅要求等离子装置具有很高的可靠性,对油枪的性能也提出了要求。在采用等离子点火时,油枪的良好备用是安全稳定的保证。从安全角度出发,等离子模式与正常模式之间的切换时机最好选择在两台磨运行以后,为防止断弧时,油枪不能及时投运而造成灭火采用的在A磨启动后几分中进行切换存在一定的风险。 等离子装置的可靠性是等离子成功运用的关键,但在如何使等离子的效果发挥的更加出色,也需要我们在运行中不断的摸索。从目前的运行情况来看,我们采用的是控制煤种、煤量、煤粉细度、一次风量,出口温度等方式。在加仓时,尽量给A仓加热量高,挥发份高的煤种,以利于释放出更多的挥发份;A磨等离子拉弧时,提高分离器转速以达到提高煤粉细度的目的,以利于煤粉的燃烧;出口粉温应在一次风温允许的条件下尽可能的高,以利于煤粉的着火。煤量应严格控制在燃烧器在等离子状态下的出力范围,防止燃烧器因为过负荷而造成结焦。风煤比控制到1:0.45左右,可以参考出口风速,一般在19m/s左右,风速不宜太高。在冷炉阶段,由启动锅炉供辅汽的情况下,由于启动锅炉主汽压力与温度的限制,使得磨煤机一次风速与出口温度总是存在矛盾。在这两者之间,个人认为应该把风速放在第一位。为防止制粉系统启动后,磨出口粉温的快速下降,需要进行充分暖磨,控制好暖磨风量及暖磨时间。 泰州电厂的磨煤机需要带载启动,虽然在冷炉启动时不会出现爆燃的现象,但若在热炉状态下,这一点就需要格外关注。由于磨煤机在存煤很比较少的情况下运行时,会产生振动,因此磨煤机停运后,是走不空的,在热炉条件下,若铺煤过多,或者在没有对磨充分吹扫的情况下开始等离子拉弧的工作,就可能引起爆燃。一直以来,我们很少遇到热炉启动,因此,对这一点也没有引起重视。即使在锅炉温度比较高的时候,由于锅炉容量比较大,而点火时风量又较大,故在局部爆燃的情况下,对炉膛负压的影响也比较小。直到在后来的一次起机过程中,由于点火风量较小(900多吨),在等离子拉弧后,虽然等离子运行情况良好,但是锅炉MFT,首触为风量低。从DCS历史记录中可以清楚的看出,在拉弧的瞬间,炉膛出现正压,虽然不大,但由于当时送风压力也就只有2KPa, 因此出现了上面的一目。这次事故虽然没有酿成严重的后果,但给我们的教训是深刻的。从之后的起机经验来看,控制点火风量在1400T/H左右是安全的,对A磨的吹扫也不容忽视。在热炉点火的情况下,烟气温度足够加热一次风达到等离子拉弧的条件,因此可以不用辅汽加热一次风。在冷炉情况下,当空预器出口一次风温达到暖风器出口风温差不多水平时,可以将热一次风倒到正常的方式,将暖风器停运。此时,暖风器没有冷却介质通过,若没有及时隔离,就存在爆炸的可能性。(某电厂就出现过此类事故。) 鉴于等离子装置固定安装在A层燃烧器中,因此在正常运行时,由于炉膛温度及风温较高,仍应加强对等离子装置壁温的监视,防止烧损及结焦。当A磨运行时,等离子装置有煤粉通过,可以得到充分的冷却,不会造成超温,从运行的情况来看,前后壁温最高值在270°C左右。若发现壁温升高,则需要注意等离子套筒的监视,很有可能是结焦的结果。当A磨停运时,没有煤粉及一次风通过,将使等离子壁温迅速升高,若A磨没有检修工作,可以采取磨煤机通风的措施来降低等离子壁温;若A磨有检修工作,不能通一次风,此时可以通过开大A层燃烧器二次风的措施来减缓壁温的升高。尽管如此等离子壁温的最高值还是达到480°C左右(800MW),随着负荷的上升,壁温将上升。目前壁温的控制值在560°C。因此在等离子装置完好的情况下,可以运行。 考虑到等离子装置配套系统的检修工作,在等离子不拉弧的情况下,等离子载体风机,等离子冷却水泵均可以停运,但等离子火检风机不能停运,否则会烧毁等离子火检。在冬季,还应注意冷却水系统的防冻工作。 以上是本人一些浅显的认识,由于1000MW机组在国内刚刚起步,没有成熟的运行经验,对等离子点火也缺乏深刻的认识,在以后的运行中肯定还会遇到其他问题。我相信只要在生产过程中不断摸索,必然会使等离子燃烧技术更好的运用在电站锅炉中。