催化剂汽提器内气固传质特性的研究(传质模型))
微通道内气液流动与传质特性的研究进展
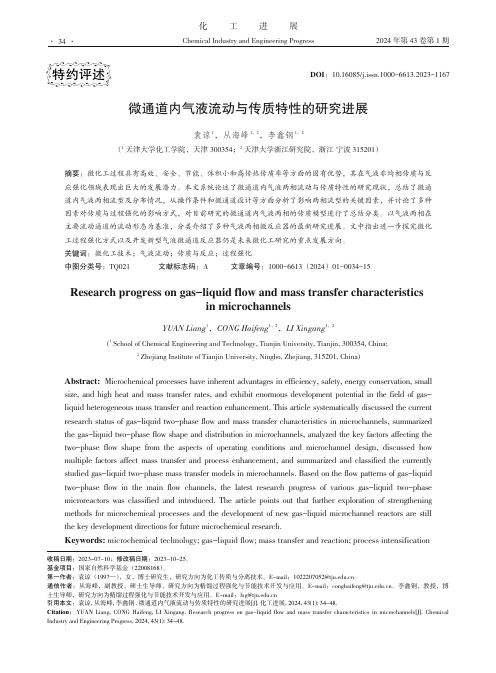
化工进展Chemical Industry and Engineering Progress2024 年第 43 卷第 1 期微通道内气液流动与传质特性的研究进展袁谅1,从海峰1,2,李鑫钢1,2(1 天津大学化工学院,天津 300354;2 天津大学浙江研究院,浙江 宁波 315201)摘要:微化工过程具有高效、安全、节能、体积小和高传热传质率等方面的固有优势,其在气液非均相传质与反应强化领域表现出巨大的发展潜力。
本文系统论述了微通道内气液两相流动与传质特性的研究现状,总结了微通道内气液两相流型及分布情况,从操作条件和微通道设计等方面分析了影响两相流型的关键因素,并讨论了多种因素对传质与过程强化的影响方式,对目前研究的微通道内气液两相的传质模型进行了总结分类。
以气液两相在主要流动通道的流动形态为基准,分类介绍了多种气液两相微反应器的最新研究进展。
文中指出进一步探究微化工过程强化方式以及开发新型气液微通道反应器仍是未来微化工研究的重点发展方向。
关键词:微化工技术;气液流动;传质与反应;过程强化中图分类号:TQ021 文献标志码:A 文章编号:1000-6613(2024)01-0034-15Research progress on gas-liquid flow and mass transfer characteristicsin microchannelsYUAN Liang 1,CONG Haifeng 1,2,LI Xingang 1,2(1 School of Chemical Engineering and Technology, Tianjin University, Tianjin, 300354, China;2Zhejiang Institute of Tianjin University, Ningbo, Zhejiang, 315201, China)Abstract: Microchemical processes have inherent advantages in efficiency, safety, energy conservation, small size, and high heat and mass transfer rates, and exhibit enormous development potential in the field of gas-liquid heterogeneous mass transfer and reaction enhancement. This article systematically discussed the currentresearch status of gas-liquid two-phase flow and mass transfer characteristics in microchannels, summarized the gas-liquid two-phase flow shape and distribution in microchannels, analyzed the key factors affecting the two-phase flow shape from the aspects of operating conditions and microchannel design, discussed how multiple factors affect mass transfer and process enhancement, and summarized and classified the currently studied gas-liquid two-phase mass transfer models in microchannels. Based on the flow patterns of gas-liquid two-phase flow in the main flow channels, the latest research progress of various gas-liquid two-phase microreactors was classified and introduced. The article points out that further exploration of strengtheningmethods for microchemical processes and the development of new gas-liquid microchannel reactors are still the key development directions for future microchemical research.Keywords: microchemical technology; gas-liquid flow; mass transfer and reaction; process intensification特约评述DOI :10.16085/j.issn.1000-6613.2023-1167收稿日期:2023-07-10;修改稿日期:2023-10-25。
催化裂化新型汽提器汽提蒸汽有效利用率的研究
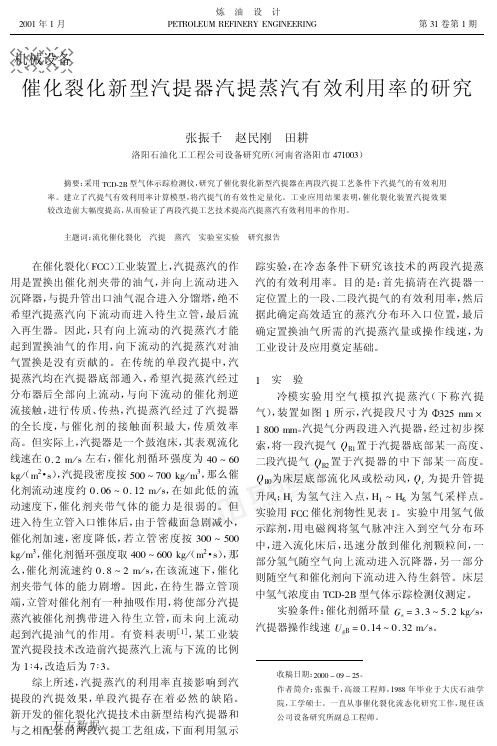
# ! 78, 78. .0* /#0 9: */ !.$ 11* % / (编辑 漆 萍)
段进入汽提器, 汽提线速在上述推荐范围内。改 造前后原料性质基本没有变化, 反"再系统操作条 件除汽提蒸汽量外, 维持以前的操作值, 工业试验 装置的汽提效果可从两个方面来分析: (#) 用焦炭中含氢量来衡量。汽提蒸汽用量 较改造前降低了 $ % & ’ ( ), 降低幅度为 #*+ , 焦炭 中氢含量由改造前的 ## % $+ (# , - 月平均值) 下 降至 - % &.+ ( / , ## 月平均值) , 氢含量最低达到 平均降低幅度 0! % &+ 。也就是说, 在汽提 0 % 1&+ , 蒸汽用量下降 #*+ 的情况下, 汽提段汽提效果提 高了 0! % &+ 。 (!) 从再生器再生温度和焦炭产率来判断, 改 造后再生温度为 -*.2 , 较改造前下降了 .2 , 焦炭 产率下降了 # % #1 个百分点。这充分说明汽提效 率提高后, 焦炭氢含量下降, 焦炭产率减少。 从上述两方面数据说明, 汽提段改造效果相 当显著, 从而也证明了冷模 试 验 结 果 的 正 确 性。
!"#$% &’ ())(*"+,(’(!! &) ’(- !".+//(. +’ )**#
9);<= 9)><?@;<, 9);A B@<=;<=, C@;< D><= ( 3#16,(7 , !"#$%&’() *’+’,-./ 0(+)$)#)’ 12 34!5 8’(,( 01#$$&) 01234563 C)> >EE>F’@G><>66 AE ’)> <>H 6’I@JJ>I @< 3447 H;6 K>’>I5@<>K L<K>I FA<K@’@A<6 AE ’HA"6’;=> 6’I@JJ@<= MN ’)> C4O"!M =;6 ’I;F@<= K>’>F’AI % P F;QFLQ;’@A< 5AK>Q EAI ’)> >EE>F’@G><>66 H;6 >6’;MQ@6)>K % 4A55>IF@;Q ;JJQ@F;" ’@A< 6)AH>K ’);’ ’)> >EE>F’@G><>66 AE ’)> 6’I@JJ>I @< 3447 H;6 =I>;’QN @5JIAG>K % 789:;4<2 EQL@K F;’;QN’@F FI;FR@<=, 6’I@JJ@<=, 6’>;5, Q;MAI;’AIN ’>6’, I>6>;IF) I>JAI
第四章 内部传递对气固相催化反应的影响
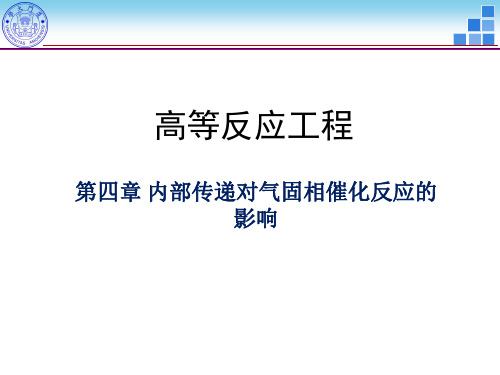
单根圆柱孔内气体扩散
1961年提出 “尘气模型”(Dusty gas model), 气体在圆 柱孔内的扩散是串联过程,总阻力是分子扩散与努 森扩散阻力之和。扩散传递通量为
J A D P dyA dCA D t dx RgT dx
综合扩散系数定义
D 1 (1 y A ) / DAB 1/ ( DK ) A
1
NB NA
2016/7/17
版权所有, By 曹志凯, 厦门大学化学工程与生物工程系
6
4.1.2 多孔催化剂中的气体有效扩散系数 比较两个模型,当曲节
Wheeler平行孔模型:
因子等于空隙率的倒数 D 时,两个模型统一 De
曲节因子由实验确定,Satterfield建议为4 随机孔模型:Wakao和Smith对双分散孔结构催化剂 提出,粒内空隙看成微粒间大孔和微粒 内小孔组成
2016/7/17
版权所有, By 曹志凯, 厦门大学化学工程与生物工程系
2
• 中压法聚乙烯催化剂的孔径与聚乙烯生成量 关系:抛物线形,孔径16nm时存在最大值
催化剂孔道内的扩散与活性组分负载量矛盾
• 混合二甲苯生产(甲苯歧化、甲苯与甲醇烷基化)
2C6H5CH3 C6H4 (CH3 )2 C6H6 C6H5CH3 CH3OH C6H4 (CH3 )2 H2O
高等反应工程
第四章 内部传递对气固相催化反应的 影响
粒内传递对反应影响是催化剂设计理论基础 催化剂配方、制备工艺 内扩散影响:粒径、粒内有效扩散系数(孔结 构和大小)
粒径降低,比表面积增加,内扩散阻力下降 ,固定床反应器压降增加 粒内微孔小,比表面积增加,负载的活性组 分多,但对扩散不利
南京工业大学反应工程题集-完全答案解析版

注:红色底色为需注意的题目;黄色为无答案的题目1.对于热效应不大,反应温度的允许变化范围又比较宽的情况,用单级反应器最方便。
2.气固催化平行反应,若主、副反应均为一级不可逆反应,且粒子等温,则内扩散不影响其选择性,在粒子内任意位置,反应速率之比均为速率常数之比。
选择题1.在V=100L/min流量下对三只反应器分别进行示踪实验,测得如下数据:反应器 A B C体积(L)1000 2000 3000σt2 (min)50 100 250则三只釜的反混大小顺序(B)A. A>B>CB. A>C>BC. C>B>AD. C>A>B2. 乙苯在催化剂上脱氢反应生成苯乙烯,经过一段时间反应后,苯乙烯生成量不再增加,但乙苯仍大量存在,表明这是一个(B)反应。
A.慢速B.可逆C.自催化D.不可逆3.反应器中等温进行着A→P(1)和A→R(2)两个反应,当降低A的浓度后,发现反应生成P 的量显著降低,而R 的生成量略降低,表明( A )A .反应(1)对A 的反应级数大于反应(2)B .反应(1)对A 的反应级数小于反应(2)C .反应(1)的活化能小于反应(2)D .反应(1)的反应速率常数大于反应(2)4.在间歇反应器中等温进行一级不可逆反应A →R ,当转化率达90%时,所需反应时间为2h 若反应改在管式反应器中进行,空时为2h ,其它条件同间歇反应器,则转化率为( B )A . 60% B. 90% C .45% D .75%☆两个等体积的全混流反应器进行串联操作,反应为一级不可逆,则第一釜的反应速率-rA1与第二釜的反应速率-rA2之间的关系为(A )。
两釜反应温度相同。
A .-rA1 > -rA2B .-rA1 = -rA2C .-rA1 < -rA2 D.不能确定何者为大5.四只相同体积的全混釜串联操作,其无因次停留时间分布的方差值2θσ为( B )A . 1.0 B. 0.25 C .0.50 D .06.对一平行—连串反应RA QP A −→−−→−−→−)3()2()1( ,P 为目的产物,若活化能次序为:E 2<E 1<E 3,为了目的产物的收率最大,则最佳操作温度序列为( B )。
(6)气固催化反应器
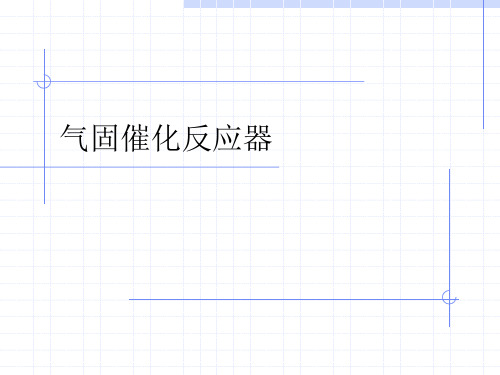
固定床反应器的代表:
固定床反应器的优缺点
床层内流体流动接近 PFR,返混小,所以 rA↑,xA↑,较小容 积,较大生产能力; 催化剂不易磨损而可 长期使用; 易控制,如停留时间 可严格控制,温度分 布调节。 传热较差,催化剂属 导热不良物质,反应 结果对温度的依赖性 又很强,所以对于热 效应大的反应过程, 传热和控温是技术难 点和关键所在; 催化剂更换必须停产, 所以必须要有足够长 寿命;催化剂粒子不 能太小。
反应器的热稳定性和参数灵敏性
化学反应器内的传热问题与一般的加热、冷却或换热 过程中的传热问题有一个重要的区别,就是反应器内 的反应过程和传热过程之间相互交联作用。 对于放热反应过程,可能出现如下的恶性循环:
反应温度上升 反应加快 反应放热速率增大
当然,这种恶性循环是吸热反应所没有的,也是一般 换热过程中所不存在的一类特殊现象。这种现象的存 在对传热和反应器的操作、控制都提出了特殊的要求。
绝热式反应器
结构简单,床内没有传热装置,预热到适当温度的反应物 料,在绝热条件下进行反应,对于热效应不大,反应温度 允许变化范围又较宽的情况最为适用,又分为单段和多段。 单段--绝热条件下只反应一次; 多段--反应一次后经换热满足所需温度条件,再次 进行绝热反应,一次称为一段,如催化重整 多段绝热式反应器,按段间换热方式的不同又可分为:
参数灵敏性
所谓参数灵敏性指的是各有关参数如流量、进口温度 和冷却介质温度等作微小调整时,反应器内温度或反 应结果将会有多大变化? 如果反应器的参数灵敏性过高,那末对参数的调整就 会有过高的精度要求,使反应器的操作变得十分困难。 因此,在反应器的设计中,确定设备尺寸和工艺条件 时必需设法避免过高的参数灵敏性。
化学反应气固两相流传质传热研究进展分析

化学反应气固两相流传质传热研究进展分析气固两相流是一种重要的多相流动状态,广泛应用于化工、冶金、环境保护等领域中。
在这种流动状态下,气体相与固体相之间发生着传质与传热的过程,研究气固两相流的传质传热行为对于实现高效、节能、环保的化工过程具有重要意义。
本文将就化学反应气固两相流传质传热研究进展进行分析。
在化学反应气固两相流传质传热的研究中,研究者们主要关注以下几个方面:传质传热机理、数值模拟与实验研究、传质传热特性、传质传热过程的优化与增强。
首先,传质传热机理是研究气固两相流行为的基础。
在气固两相流中,固体颗粒上的次级蒸发、亚细胞内传质、气体颗粒的边界层传质等过程是传质传热机理的关键。
研究者们通过理论分析、模型建立和实验验证等方法,深入探究了这些机理,并提出了相应的传质传热模型。
其次,数值模拟与实验研究是研究气固两相流传质传热的重要手段。
通过数值模拟可以对气固两相流的传质传热行为进行分析和预测,为优化和设计工艺提供理论依据。
与此同时,实验研究可以验证数值模拟结果的准确性,并获取实际工艺中的传质传热数据。
这两种方法相互辅助,为气固两相流传质传热研究提供了可靠的数据支持。
第三,传质传热特性是研究气固两相流的重要内容之一。
研究者们通过实验和模拟手段研究了在不同气体流速、固体颗粒尺寸和形状、气体成分等条件下的传质传热特性。
发现了某些气固体系的传质传热特性与物料性质、流动状态等密切相关的规律,并提出了相应的数学模型来描述这种关系。
最后,传质传热的优化与增强是研究气固两相流的重要目标之一。
通过改变气体流速、固体颗粒尺寸和形状、操作条件等因素,可以提高气固两相流传质传热效率,减少能量消耗和环境污染。
研究者们利用优化理论和方法,通过模拟和实验探索了传质传热过程的优化与增强方法,并取得了一定的成果。
综上所述,化学反应气固两相流传质传热研究在很大程度上推动了化工过程的高效、节能、环保。
对于气固两相流传质传热机理的研究相信会有更深入的理解和认识,数值模拟与实验研究将会更加精确和可靠,传质传热特性的探索将会更加全面和准确,传质传热的优化与增强将会更加高效和定量。
气固传质过程中的质量传输机理研究及反应器设计
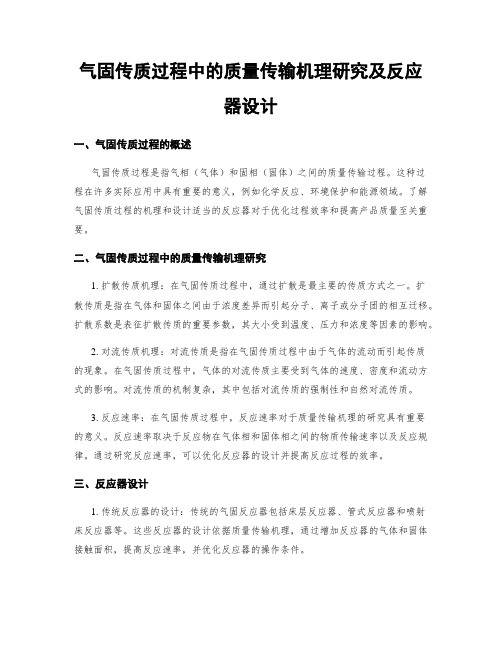
气固传质过程中的质量传输机理研究及反应器设计一、气固传质过程的概述气固传质过程是指气相(气体)和固相(固体)之间的质量传输过程。
这种过程在许多实际应用中具有重要的意义,例如化学反应、环境保护和能源领域。
了解气固传质过程的机理和设计适当的反应器对于优化过程效率和提高产品质量至关重要。
二、气固传质过程中的质量传输机理研究1. 扩散传质机理:在气固传质过程中,通过扩散是最主要的传质方式之一。
扩散传质是指在气体和固体之间由于浓度差异而引起分子、离子或分子团的相互迁移。
扩散系数是表征扩散传质的重要参数,其大小受到温度、压力和浓度等因素的影响。
2. 对流传质机理:对流传质是指在气固传质过程中由于气体的流动而引起传质的现象。
在气固传质过程中,气体的对流传质主要受到气体的速度、密度和流动方式的影响。
对流传质的机制复杂,其中包括对流传质的强制性和自然对流传质。
3. 反应速率:在气固传质过程中,反应速率对于质量传输机理的研究具有重要的意义。
反应速率取决于反应物在气体相和固体相之间的物质传输速率以及反应规律。
通过研究反应速率,可以优化反应器的设计并提高反应过程的效率。
三、反应器设计1. 传统反应器的设计:传统的气固反应器包括床层反应器、管式反应器和喷射床反应器等。
这些反应器的设计依据质量传输机理,通过增加反应器的气体和固体接触面积,提高反应速率,并优化反应器的操作条件。
2. 高效反应器的设计:为了提高气固传质过程的效率,研究人员提出了许多新型的高效反应器设计。
例如,流化床反应器采用气体通过固体床层的方式进行反应,具有较高的传质速率和较好的混合性能。
旋转床反应器通过固体颗粒的旋转运动实现气体和固体的充分接触,从而提高反应速率。
这些高效反应器的设计可以进一步提高气固传质过程的效率和产品质量。
3. 数值模拟方法:随着计算机技术的发展,数值模拟方法成为研究气固传质过程和反应器设计的重要手段之一。
通过建立适当的数学模型,使用计算流体力学(CFD)和计算传质学(CTD)等方法进行数值模拟,可以对气固传质过程进行深入的研究,并优化反应器的设计。
化学反应工程-21-第六章-气固相催化反应固定床反应器

同样可写出:
C0,n1 C0,n
R A aV 1 B 4 E r l 2 C1,n C0,n l 8 u r u
T
R
0
2rdr 2 T 2 2 R R
R
0
Trdr
说明: 2rdr E t dt,即分布密度函数。 R 2
CA
R
0
2rdr 2 CA 2 2 R R
R
0
C A rdr
二、数学模型求解
1、显式差分法 上述方程组(3)、(4)没有解析解,只能求其数值解: 方程的自变量为r、l,其定义域就是整个反应器,即是圆柱形 的反应床,为求得定义域上因变量CA、T的分布规律,数值 解的基本思路是:
2点:气流主体由l+dl面离开微元体带出的热量:
g u 2rdr C P Tl dl,J s 1
3点:由轴向热传导自l面而传入微元体的热量:
T 1 eZ 2rdr,J s l l
4点:由轴向热传导自l+dl面离开而传出的热量:
T 1 eZ 2rdr,J s l l dl
6点:A自r+dr面由径向扩散而离开微元体的量:
C Er A 2 r dr dl, s 1 mol r r dr
2 mol s 1 7点:微元体中A的反应量: R A 1 B r dr dl r dl , 2
R A aV 1 B H rA
g uCP
l 1 2 Tm1,n 2Tm,n Tm1,n Tm 1,n Tm,n g uCP r m l 5
- 1、下载文档前请自行甄别文档内容的完整性,平台不提供额外的编辑、内容补充、找答案等附加服务。
- 2、"仅部分预览"的文档,不可在线预览部分如存在完整性等问题,可反馈申请退款(可完整预览的文档不适用该条件!)。
- 3、如文档侵犯您的权益,请联系客服反馈,我们会尽快为您处理(人工客服工作时间:9:00-18:30)。
Mass balance of infinitesimal element
取催化剂密相料面为 z 轴零点,令气泡相内油气的浓度 (即体积分率)为 y,而乳化相内油气的浓度 为 x,单位时间内由于催化剂夹带,而向床层内带入油气体积为 Qe,可用下面的公式表示: 1 1 Qe = wp − (1) ρmf ρp 定义 ve=Qe / Aa,称为油气下行表观线速,则 1 1 ve = Gp − (2) ρ mf ρ p 将气泡相的总流量 Qb 除以汽提段的横截面积 A a 定义为气泡相表观气速 ub , 根据流化床两相理论, 气泡相的表观气速 ub ub = ug − umf 得如下公式: 整理后可得: ub dy = −ve dx 由假设 6 可知微元体内单位时间内的总传质体积 dG 可用下式表示: dG = N Aα Aa dz = K ( x − y )α Aa dz 由于床层处于稳态操作,因此 dG = ub Aa dy = −ve Aa dx 油气浓度存在如下关系: ub ( x0 − y ) = ve ( x0 − x ) (u − v ) x + v x y= b e 0 e ub 将式(9)和(7)代入到式(6)中可得 v −ve Aa dx = K 1 − e ( x − x0 ) α Aa dz ub (8) (9) (10) (7) 假定汽提段稀密相界面处油气的浓度为 x0 ,按照质量守恒原理,则在任一高度上气泡和乳化相内 (6) (5) ub Aa ( y + dy ) − ub Aa y = ve Aa ( x + dx ) − ve Aa x (3) 取汽提段一个体积微元体,如图 1 所示。由于床层操作处于稳态过程,对微元体进行质量衡算可
张永民, 卢春喜, 时铭显
(石油大学, 北京 102249)
摘 要: 采用氧气示踪的方法在 φ 486 ×8000mm 的有机玻璃床内对普通流化床汽提器和盘环形挡板汽提器进行了系
统的气固相传质冷态模拟实验,得出了不同汽提线速和催化剂质量流率下上述两种催化剂汽提器内油气浓度轴向分 布的变化规律。根据其油气浓度轴向分布的特点,结合鼓泡流化床两相理论以及一系列的假设,提出了针对这两种 汽提器的一维传质模型。由实验结果待定了一维传质模型的模型参数,获得了计算两种汽提器轴向油气浓度分布的 半经验的指数关联式。该关联式和实验数据比较吻合,相对误差均在 10 %以内。由该关联式可进一步计算出汽提器 的汽提效率,可以为工业汽提器工艺参数的优化以及工程设计提供参考。 关键词:汽提器; 传质模型; 催化裂化; 流态化 中图分类号:TQ052; TQ021.4 文献标识码:A
通过非线性拟合的方式,就可以待定 出模型参数 C 和 KC,进而可求解出 K′。 对实验数据拟合发现,在汽提器结构 一定的情况下, C 是汽提气表观气速 ug 的函数,而 K′是汽提气表观气速 ug 和催 化剂质量流率 GP 两个操作参数的函数。 将 C 与 ug 关联, K′与 ug 和 GP 关联,就 得到 C 和 K′的关联式,如方程(13)(14)。 将两个关联式代入到公式 (11)中,就可以 得到普通流化床汽提器轴向氧浓度的分 布规律(平均相对误差<10%)。 C = −224.92ug 2 + 21.81ug + 8.3182 (13)
(
)
(12)
10 9 Oxygen concentration / % 8 7 6 5 4 0 图3 500 1000 1500 2000 Distance from gas distributor / mm 不同质量流率下普通流化床汽提器轴向氧浓度分布的 实验值与模型计算结果的对比 Fig.3 Comparison of axial oxygen concentration of general fluidized bed stripper between model formula and experimental results under different catalyst fluxes ◆ Gp=26.73 kg⋅(m2⋅s)−1 ■ Gp=55.10 kg⋅(m2⋅s) −1 ▲ Gp=60.99 kg⋅(m2⋅s) −1 ug=0.10 m⋅s−1, computational result
第 18 卷第 4 期
张永民等: 催化剂汽提器内气固传质特性的研究
411
3
3.1
பைடு நூலகம்
实验验证与分析
实验装置及方法[6] 实验方法和文献[7] 中的介绍的基本相同,
Oxygen concentration / %
14 12 10 8 6 4 2 0 0 500 1000 1500 2000 Distance from gas distributor / mm 图2 不同表观气速下普通流化床汽提器轴向氧浓度分布的实验值 与模型计算结果的对比 Fig.2 Comparison of axial oxygen concentration of general fluidized bed stripper between model formula and experimental results under different stripping velocities ◆ ug=0.05m⋅s−1 ■ ug =0.10 m⋅s−1 ▲ ug =0.15 m⋅s−1 × ug =0.20 m⋅s−1 Gp=26.73kg.(m2⋅s) −1 computational result
即采用氧示踪的模拟方式,以进入汽提段的催 化剂内夹带的氧气来模拟工业装置中的油气, 以工业液氮气化后的氮气作为汽提段的汽提 气,根据不同位置处所检测到的氧气浓度分布 来模拟汽提段不同位置的油气浓度。通过对实 验数据的分析,确定汽提器的传质特性 。 实验在一套 φ486 ×8000mm 的大型冷模两 器循环实验装置上进行,实验装置模拟工业催 化裂化基本流程, 装置简图如参考文献[6]中图 2 所示。实验中采用的汽提器为一外径 φ486, 内径 φ160 的环形结构,密相料位高度为 2.3m , 其中盘环形挡板汽提器按照工业装置设计,内 外挡板坡角 45°,共设 8 层挡板。
K' = ( 0.065ug + 0.0306) ( 0.065Gp − 0.375) (14)
412
高
校
化
学
14
工
程
学
报
2004 年 8 月
实验数据表明,对于普通流化床汽提 器而言,在相同的汽提线速和催化剂质量 流率下,随着距离分布管高度的增加,汽 提段内油气含量呈指数增加;随着汽提线 速的增加,汽提器各处的油气含量明显下 降,而随着催化剂质量流率的增加,汽提 段各处的油气含量则略有增加。图 2 和图 3 分别给出了普通流化床汽提器在不同汽 提气表观线速下和不同催化剂质量流率 下轴向氧浓度分布的模型计算结果和实 验数据的对比图,可以看出实验数据和模 型计算结果基本吻合,误差分析表明,两 者之间的总体平均相对误差均小于 10%。 同样的方法应用于盘环形挡板汽提
图1 Fig.1 微元体的物料衡算
相之间的传质作用; 递,两者的传质速率相同,即同体积置换;
u y
v x x
u y +dy
v x +dx
度为 umf / ε mf ; 体积、大小分布一样,也即具有相同的传质表面积; 颗粒内孔夹带的油气不能被汽提,只能置换出颗粒之 间夹带的油气; 气 泡 和 乳 化 相 之 间 的 传 质 速 率 NA 与 气 泡 和 乳 化 相 内 气 体 的 浓 度 差 呈 线 性 关 系 , 即
[7]
实验中采用的颗粒同样为 FCC 平衡催化剂,颗粒物性参数如文献[7]中表 1 所示。 3.2 实验结果与分析 实验中汽提气表观线速共取四档(ug=0.05 m⋅ s−1 、0.10 m ⋅s−1 、0.15 m⋅ s−1 、0.2 m⋅ s−1),催化剂质量流 率取三档(Gp=26.73kg⋅ (m2⋅s)−1,50.10kg⋅ (m2⋅s) −1,60.99kg⋅(m2⋅s) −1)。 为了待定一维传质模型的模型参数 K′和 C 的值,本文采用如下方法: x0 取汽提段稀密相界面处氧气的浓度,umf 由 Leva 公式求得 umf = 0.0093 d p
1
背
景
催化剂汽提器在催化裂化装置中起着重要的作用。有资料显示[1],催化剂从提升管反应器出来经快 分分离后,会夹带一部分油气,这部分油气的量约占产品重量的 2%~4% ,如果可以完全汽提出这部分 油气,催化剂上的焦炭量将减少 20%~40% ,所以高效汽提器不仅可以提高轻质油收率,减少蒸汽用量, 而且还可以降低装置的再生外取热负荷,在节能增效和维护装置热平衡操作方面都能起到重要的作用。 长期以来,国内对汽提器的重要性认识不足,工业装置内汽提器的设计仅仅是参考一些极其有限 的经验数据。目前国内催化裂化装置中使用的汽提器主要是人字形挡板和盘环形挡板两种结构,这两 种型式的汽提器汽提效率普遍都比较低, 而且也存在着催化剂分布不匀、 局部失流态化等一系列问题。 因此很有必要对汽提器内气固相之间的传质规律进行系统的研究,以找出操作参数对汽提器汽提效率 的影响规律,为工业优化设计提供参考。 研究表明[2]:吸附或沉积在催化剂表面(包括内部微孔表面)上的有三种类型的物质: “软”焦炭(在 高温等苛刻条件下能被汽提的部分)、 “硬”焦炭(不可汽提的部分)以及吸附和夹带的易汽提的烃类。本 文的研究主要针对易汽提烃的汽提上,这一过程主要体现在两方面的作用:首先是水蒸汽向上的流动 吹扫出夹带在催化剂颗粒空隙间的油气,其次是利用水蒸汽具有的较强的竞争吸附性能,降低油气的 分压,从而达到置换一部分微孔内油气的目的。影响汽提效率的主要因素有汽提蒸汽用量、催化剂停 留时间、操作温度、催化剂物性和汽提器内部结构等。 催化裂化汽提段是典型的气固逆流密相流化床输送过程,夹带油气的催化剂呈密相状态向下流 动,汽提气体主要以气泡形式向上流动。在这个过程中,传质作用主要发生在气泡相和乳化相之间, 随着催化剂向下流动,乳化相中的油气浓度逐渐降低;同时随着气泡相的向上流动,气泡相中油气浓 度逐渐升高。