汽车离合器用铜基金属陶瓷摩擦材料的研究进展
汽车刹车片用新型陶瓷基摩擦材料性能研究

汽车刹车片用新型陶瓷基摩擦材料性能研究钛酸钾晶须是当前一种新型的陶瓷基摩擦材料,属于增强体晶须,灵活利用其自身的性质,可以有效的应用在当前的汽车刹车片制作中,进而提升当前材料的硬度、密度以及抗拉强度,提升汽车刹车片的整体性能。
基于此,本文从当前的汽车刹车片的性能要求与材料入手,深入进行分析,进而明确其新型陶瓷基摩擦材料的性能,以供参考。
标签:汽车刹车片;新型陶瓷基;摩擦材料;性能分析0 引言随着时代不断发展,当前我国汽车工业逐渐繁荣,灵活应用当前先进的技术,促使现阶段的汽车制造逐渐向轻量化、高质量、高安全以及高寿命方向发展,进而对当前的汽车制动系统提出更高的要求,以保证其整体性能。
新型陶瓷基摩擦材料是当前全新的一种材料,其材料的引用可以提升汽车制动的安全性与稳定性,满足当前的需求。
1 新型陶瓷基摩擦材料概述在当前的汽车制动装置设计过程中,最理想的材料应具有满足所有制动要求的优点与优势,例如,具有良好的稳定性、磨损效率低、摩擦系数高、使用寿命长以及刹车噪音小等特点,以满足当前的需求。
对于摩擦材料来说,其由多方面的材料组成,有增强材料、基体材料、填料以及摩擦改性剂等组成,将当前的增强纤维作为骨架,提升摩擦片的整体摩擦性能。
以当前的钛基晶须材料为例,在实际的应用过程中,该材料自身具有较为优越的性能,化学性质稳定,物理性能良好,如硬度较低、耐磨、耐热、耐腐蚀,在实际的应用过程中,可以有效的促使当前的制动装置性能得到提升,以满足当前的需求[1]。
2 汽车刹车片用新型陶瓷基摩擦材料性能分析2.1 进行合理的摩擦材料制作实际上,当前的汽车制动器在进行制作过程中,其主要是利用当前的衬片功能进行发挥,其由当前的填料、增强纤维以及粘结剂组成,利用粘接剂自身的功能与优势,将相关的材料进行合理的融合,经过粘接、加热、固化等工序,促使其形成质量良好的摩擦材料,提升整体性能,满足当前的需求。
例如,作者通过合理的实验,对当前的汽车刹车片新型陶瓷基材料的性能进行分析,通过不同的粘结剂的不同体积分数明确其最优效果,进而选择出摩擦材料的最高强度与韧性,提升其整体性能。
陶瓷基复合材料与金属连接的研究进展

陶瓷基复合材料与金属连接的研究进展摘要陶瓷基复合材料是一种新兴的热结构材料,解决其自身及其与金属的连接工艺,是实现其推广应用的重要课题之一。
首先分析了陶瓷基复合材料自身连接及其与金属连接的难点,在此基础上从解决被连接材料的化学相容性与物理匹配性两方面出发,综述了陶瓷基复合材料自身及其与金属连接的研究进展,并介绍了几种典型的连接实例———活性金属钎焊、部分瞬间液相扩散连接以及宏观结构梯度中间层设计。
关键词: 陶瓷基复合材料化学相容性物理匹配性连接0前言陶瓷基复合材料(Ceramic Matrix Composites,以下简称CMCs)作为一种新兴的热结构材料,具有密度低、耐高温、抗氧化、热强度保持率高以及断裂韧性高等优点,在未来的高推重比航空发动机、卫星姿控发动机、超高声速冲压发动机、巡航导弹发动机、液体和固体火箭发动机等武器装备领域具有广阔的推广应用前景[ 1 ] ,在涡轮燃气电站和核能反应堆等民用领域的市场潜力更大[ 2, 3 ] 。
由德国工业设备公司( IABG)生产的C /SiC复合材料已经应用在光学领域(镜子和反射镜) 、燃烧室、热交换机、高性能车辆刹车盘、化学工业和国防领域[ 4 ] 。
连接是CMCs走向工程应用需要解决的关键技术之一。
一方面, CMCs复杂精密构件的低成本制造,需要实现CMCs之间的连接;另一方面,构件各部分不同的功能,需要实现其与金属之间的连接。
连接的目标是实现接头的高温使用,因此连接的金属对象为Nb合金[ 5~7 ] 、Ti合金[ 8~11 ] 、Ni基高温合金[ 12, 13 ]等难熔金属材料。
由于CMCs继承了陶瓷的化学性能以及高硬度、高模量(如C /SiC) 和低线膨胀系数(如SiC /SiC、C /SiC)等物理性能,即: CMCs - 金属连接与陶瓷- 金属连接在材料组配上有许多相似之处,两类接头的实现面临着一些基本的共性问题,这些问题在本质上可以归纳为两个方面:化学相容性与物理匹配性。
粉末冶金综述论文
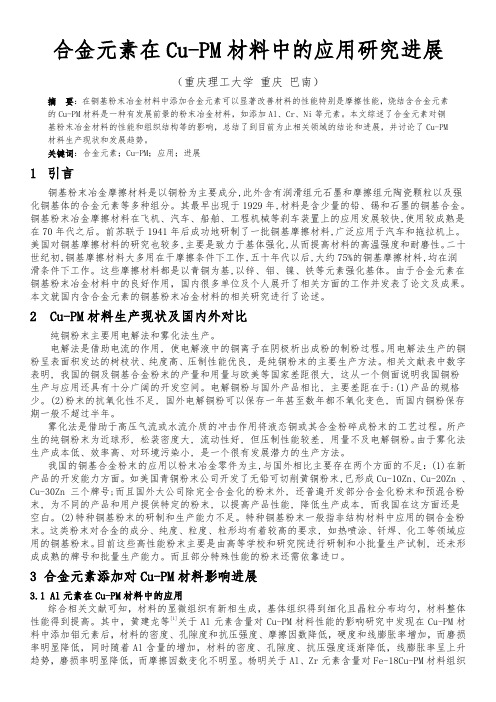
合金元素在Cu-PM材料中的应用研究进展(重庆理工大学重庆巴南)摘要:在铜基粉末冶金材料中添加合金元素可以显著改善材料的性能特别是摩擦性能,烧结含合金元素的Cu-PM材料是一种有发展前景的粉末冶金材料,如添加Al、Cr、Ni等元素。
本文综述了合金元素对铜基粉末冶金材料的性能和组织结构等的影响,总结了到目前为止相关领域的结论和进展,并讨论了Cu-PM 材料生产现状和发展趋势。
关键词:合金元素;Cu-PM;应用;进展1 引言铜基粉末冶金摩擦材料是以铜粉为主要成分,此外含有润滑组元石墨和摩擦组元陶瓷颗粒以及强化铜基体的合金元素等多种组分。
其最早出现于1929年,材料是含少量的铅、锡和石墨的铜基合金。
铜基粉末冶金摩擦材料在飞机、汽车、船舶、工程机械等刹车装置上的应用发展较快,使用较成熟是在70年代之后。
前苏联于1941年后成功地研制了一批铜基摩擦材料,广泛应用于汽车和拖拉机上。
美国对铜基摩擦材料的研究也较多,主要是致力于基体强化,从而提高材料的高温强度和耐磨性。
二十世纪初,铜基摩擦材料大多用在干摩擦条件下工作,五十年代以后,大约75%的铜基摩擦材料,均在润滑条件下工作。
这些摩擦材料都是以青铜为基,以锌、铝、镍、铁等元素强化基体。
由于合金元素在铜基粉末冶金材料中的良好作用,国内很多单位及个人展开了相关方面的工作并发表了论文及成果。
本文就国内含合金元素的铜基粉末冶金材料的相关研究进行了论述。
2 Cu-PM材料生产现状及国内外对比纯铜粉末主要用电解法和雾化法生产。
电解法是借助电流的作用, 使电解液中的铜离子在阴极析出成粉的制粉过程。
用电解法生产的铜粉呈表面积发达的树枝状、纯度高、压制性能优良, 是纯铜粉末的主要生产方法。
相关文献表中数字表明, 我国的铜及铜基合金粉末的产量和用量与欧美等国家差距很大, 这从一个侧面说明我国铜粉生产与应用还具有十分广阔的开发空间。
电解铜粉与国外产品相比, 主要差距在于:(1)产品的规格少。
应用于汽车工业的特种陶瓷材料及其研究进展
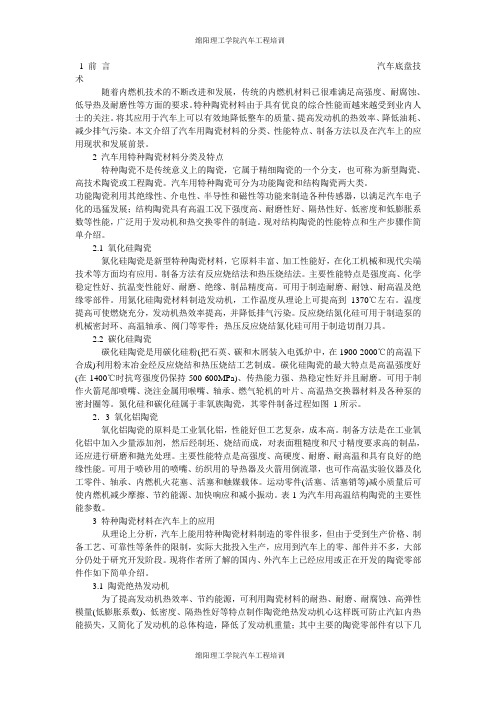
1 前言汽车底盘技术随着内燃机技术的不断改进和发展,传统的内燃机材料已很难满足高强度、耐腐蚀、低导热及耐磨性等方面的要求。
特种陶瓷材料由于具有优良的综合性能而越来越受到业内人士的关注。
将其应用于汽车上可以有效地降低整车的质量、提高发动机的热效率、降低油耗、减少排气污染。
本文介绍了汽车用陶瓷材料的分类、性能特点、制备方法以及在汽车上的应用现状和发展前景。
2 汽车用特种陶瓷材料分类及特点特种陶瓷不是传统意义上的陶瓷,它属于精细陶瓷的一个分支,也可称为新型陶瓷、高技术陶瓷或工程陶瓷。
汽车用特种陶瓷可分为功能陶瓷和结构陶瓷两大类。
功能陶瓷利用其绝缘性、介电性、半导性和磁性等功能来制造各种传感器,以满足汽车电子化的迅猛发展;结构陶瓷具有高温工况下强度高、耐磨性好、隔热性好、低密度和低膨胀系数等性能,广泛用于发动机和热交换零件的制造。
现对结构陶瓷的性能特点和生产步骤作简单介绍。
2.1 氧化硅陶瓷氮化硅陶瓷是新型特种陶瓷材料,它原料丰富、加工性能好,在化工机械和现代尖端技术等方面均有应用。
制备方法有反应烧结法和热压烧结法。
主要性能特点是强度高、化学稳定性好、抗温变性能好、耐磨、绝缘、制品精度高。
可用于制造耐磨、耐蚀、耐高温及绝缘零部件。
用氮化硅陶瓷材料制造发动机,工作温度从理论上可提高到1370℃左右。
温度提高可使燃烧充分,发动机热效率提高,并降低排气污染。
反应烧结氮化硅可用于制造泵的机械密封环、高温轴承、阀门等零件;热压反应烧结氮化硅可用于制造切削刀具。
2.2 碳化硅陶瓷碳化硅陶瓷是用碳化硅粉(把石英、碳和木屑装入电弧炉中,在1900-2000℃的高温下合成)利用粉末冶金经反应烧结和热压烧结工艺制成。
碳化硅陶瓷的最大特点是高温强度好(在1400℃时抗弯强度仍保持500-600MPa)、传热能力强、热稳定性好并且耐磨。
可用于制作火箭尾部喷嘴、浇注金属用喉嘴、轴承、燃气轮机的叶片、高温热交换器材料及各种泵的密封圈等。
陶瓷基板研究现状及新进展

其次,在新型制备技术方面,研究人员开发了一些新的制备方法,如静电纺丝 法、3D打印技术等,提高了陶瓷基板的制备效率和精度。例如,通过静电纺丝 法成功制备出了纳米级碳化硅陶瓷纤维,其具有优异的导热性和力学性能,有 望在高温封装领域得到广泛应用。
最后,在应用推广方面,陶瓷基板已经在高速铁路、汽车、航空航天、半导体 照明等领域得到了广泛应用,并不断拓展其应用领域。例如,近期研究发现, 陶瓷基板在太阳能光伏领域也展现出了良好的应用前景,有望成为未来太阳能 电池封装的重要材料之一。
针对这些关键问题,可以采取以下解决途径和方法:首先,加强基础研究,深 入了解陶瓷基板材料的性能和特点,发现新的物理和化学效应,为材料设计和 优化提供理论依据。其次,加强技术研发,不断改进和优化制备工艺,提高制 备效率和产品质量。最后,加强应用研究和市场推广,积极探索陶瓷基板的新 的应用领域和市场机会,提高其应用范围和市场份额。
然而,目前陶瓷基板研究还存在一些问题。首先,在材料性能方面,虽然现有 的陶瓷基板材料已经具有很多优点,但仍需要进行针对性地优化和改进,以满 足不同领域对封取得了一定的成果,但仍存在一些不足之处,如生产效率低、制造成本高 等。
最后,在应用推广方面,尽管陶瓷基板在某些领域已经得到了广泛应用,但仍 需要进一步拓展其应用领域,提高其应用范围和市场份额。
陶瓷基板研究现状及新进展
目录
01 一、陶瓷基板研究现 状
03
三、关键问题及解决 途径
02
二、陶瓷基板研究新 进展
陶瓷基板是一种以陶瓷为基体,经过精密加工和烧结而成的电子封装材料。由 于其具有高导热性、高绝缘性、耐高温、耐腐蚀等优点,被广泛应用于高可靠 性、高集成度的电子设备中。本次演示将综述陶瓷基板的研究现状和最新进展, 以期为相关领域的研究人员提供参考。
Ti(C,N)基金属陶瓷强韧化技术的研究进展
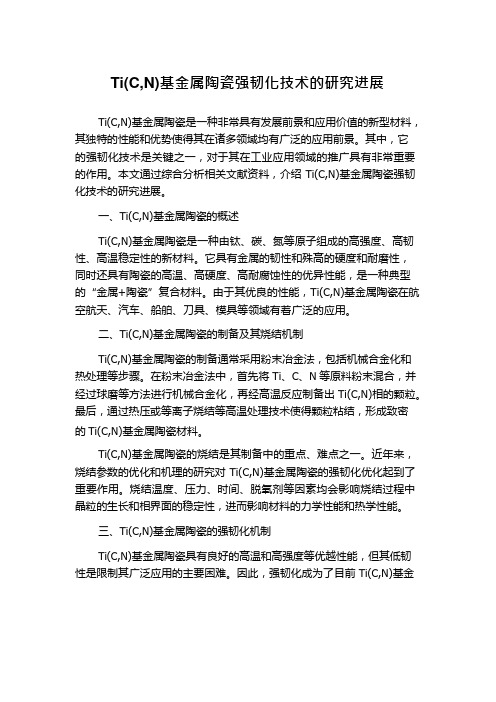
Ti(C,N)基金属陶瓷强韧化技术的研究进展Ti(C,N)基金属陶瓷是一种非常具有发展前景和应用价值的新型材料,其独特的性能和优势使得其在诸多领域均有广泛的应用前景。
其中,它的强韧化技术是关键之一,对于其在工业应用领域的推广具有非常重要的作用。
本文通过综合分析相关文献资料,介绍Ti(C,N)基金属陶瓷强韧化技术的研究进展。
一、Ti(C,N)基金属陶瓷的概述Ti(C,N)基金属陶瓷是一种由钛、碳、氮等原子组成的高强度、高韧性、高温稳定性的新材料。
它具有金属的韧性和殊高的硬度和耐磨性,同时还具有陶瓷的高温、高硬度、高耐腐蚀性的优异性能,是一种典型的“金属+陶瓷”复合材料。
由于其优良的性能,Ti(C,N)基金属陶瓷在航空航天、汽车、船舶、刀具、模具等领域有着广泛的应用。
二、Ti(C,N)基金属陶瓷的制备及其烧结机制Ti(C,N)基金属陶瓷的制备通常采用粉末冶金法,包括机械合金化和热处理等步骤。
在粉末冶金法中,首先将Ti、C、N 等原料粉末混合,并经过球磨等方法进行机械合金化,再经高温反应制备出Ti(C,N)相的颗粒。
最后,通过热压或等离子烧结等高温处理技术使得颗粒粘结,形成致密的Ti(C,N)基金属陶瓷材料。
Ti(C,N)基金属陶瓷的烧结是其制备中的重点、难点之一。
近年来,烧结参数的优化和机理的研究对Ti(C,N)基金属陶瓷的强韧化优化起到了重要作用。
烧结温度、压力、时间、脱氧剂等因素均会影响烧结过程中晶粒的生长和相界面的稳定性,进而影响材料的力学性能和热学性能。
三、Ti(C,N)基金属陶瓷的强韧化机制Ti(C,N)基金属陶瓷具有良好的高温和高强度等优越性能,但其低韧性是限制其广泛应用的主要困难。
因此,强韧化成为了目前Ti(C,N)基金属陶瓷研究的主要方向之一。
主要强韧化机制为韧性增散机制和图案转化机制:(1)韧性增散机制韧性增散机制是指通过向Ti(C,N)基金属陶瓷中添加少量的可溶性增散相(如Ni、Fe、Co 等)以调节晶界能量,减缓晶粒生长速率,从而增加Ti(C,N)基金属陶瓷的韧性。
湿式离合器用纸基摩擦片的研究进展

湿式离合器用纸基摩擦片的研究进展纸基摩擦片是一种多孔湿式摩擦材料,因其具有良好的摩擦特性而广泛应用于车辆及工程机械的自动变速器和制动器中。
简要介绍了纸基摩擦片的摩擦磨损机理,综述了近年来通过改进原料配方、制备工艺和油槽结构提高纸基摩擦片性能的进展,并对纸基摩擦片的发展趋势进行了展望。
标签:纸基摩擦片;多孔;摩擦磨损机理;摩擦性能纸基摩擦材料出现于上世纪50年代末,至今经历了由早期的纤维素增强纸基,石棉增强纸基和高品质纸基摩擦材料的3代发展[1]。
该种材料已广泛应用于汽车、船舶、工程机械、矿山机械等领域的离合器、制动器中。
随着纸基摩擦片的应用从轻载车辆向重载车辆过渡,对纸基摩擦片性能的要求也有所提高。
GB/T 21955—2008《农林拖拉机和机械纸基摩擦片技术条件》对纸基摩擦片的摩擦性能作出了严格规定,要求动摩擦系数0.11~0.14,静摩擦系数0.12~0.17,磨损率小于5×10-8 cm3/J。
GB/T 13826—2008《湿式(非金属类)摩擦材料》规定:用于汽车、拖拉机和工程机械的纸基摩擦片的动摩擦系数0.15~0.19,静摩擦系数大于0.15,磨损率小于6×10-5 cm3/J,密度0.6~3.0 g/cm3,孔隙率25%~50%。
为了提高纸基摩擦材料的性能,保证机械的工作效率,研究者对纸基摩擦材料的摩擦机理进行了大量研究。
主要是通过原料配方、制备工艺和沟槽结构的改进来提高纸基摩擦片的摩擦磨损性能和力学性能。
1 摩擦磨损机理研究在车辆的自动变速装置中,纸基摩擦材料通过与对偶片的相互作用而达到能量传输的目的。
根据接合压力的不同,可以将纸基摩擦材料与对偶片的接合过程分为3个阶段:挤压段、混合表面接触段及压紧接触段。
随着纸基摩擦材料和对偶盘之间的润滑油被逐渐挤压出接触面,润滑状态由流体润滑过渡到混合接触润滑,最后形成边界润滑。
实际接触面积和润滑状态是影响纸基摩擦材料性能的重要因素。
陶瓷金属化研究现状及发展趋势
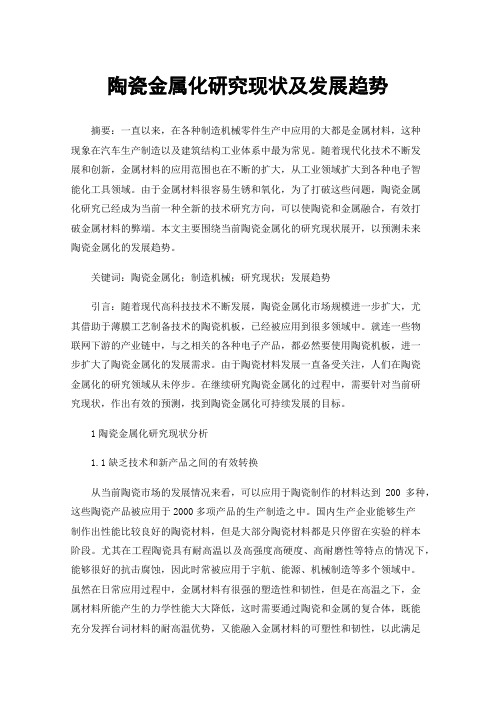
陶瓷金属化研究现状及发展趋势摘要:一直以来,在各种制造机械零件生产中应用的大都是金属材料,这种现象在汽车生产制造以及建筑结构工业体系中最为常见。
随着现代化技术不断发展和创新,金属材料的应用范围也在不断的扩大,从工业领域扩大到各种电子智能化工具领域。
由于金属材料很容易生锈和氧化,为了打破这些问题,陶瓷金属化研究已经成为当前一种全新的技术研究方向,可以使陶瓷和金属融合,有效打破金属材料的弊端。
本文主要围绕当前陶瓷金属化的研究现状展开,以预测未来陶瓷金属化的发展趋势。
关键词:陶瓷金属化;制造机械;研究现状;发展趋势引言:随着现代高科技技术不断发展,陶瓷金属化市场规模进一步扩大,尤其借助于薄膜工艺制备技术的陶瓷机板,已经被应用到很多领域中。
就连一些物联网下游的产业链中,与之相关的各种电子产品,都必然要使用陶瓷机板,进一步扩大了陶瓷金属化的发展需求。
由于陶瓷材料发展一直备受关注,人们在陶瓷金属化的研究领域从未停步。
在继续研究陶瓷金属化的过程中,需要针对当前研究现状,作出有效的预测,找到陶瓷金属化可持续发展的目标。
1陶瓷金属化研究现状分析1.1缺乏技术和新产品之间的有效转换从当前陶瓷市场的发展情况来看,可以应用于陶瓷制作的材料达到200多种,这些陶瓷产品被应用于2000多项产品的生产制造之中。
国内生产企业能够生产制作出性能比较良好的陶瓷材料,但是大部分陶瓷材料都是只停留在实验的样本阶段。
尤其在工程陶瓷具有耐高温以及高强度高硬度、高耐磨性等特点的情况下,能够很好的抗击腐蚀,因此时常被应用于宇航、能源、机械制造等多个领域中。
虽然在日常应用过程中,金属材料有很强的塑造性和韧性,但是在高温之下,金属材料所能产生的力学性能大大降低,这时需要通过陶瓷和金属的复合体,既能充分发挥台词材料的耐高温优势,又能融入金属材料的可塑性和韧性,以此满足现在与工程的应用需求。
不过,陶瓷材料和金属材料具有不同的化学键结构,陶瓷本身有一定的特殊物理策略性,很难实现与金属的有效融合链接。
- 1、下载文档前请自行甄别文档内容的完整性,平台不提供额外的编辑、内容补充、找答案等附加服务。
- 2、"仅部分预览"的文档,不可在线预览部分如存在完整性等问题,可反馈申请退款(可完整预览的文档不适用该条件!)。
- 3、如文档侵犯您的权益,请联系客服反馈,我们会尽快为您处理(人工客服工作时间:9:00-18:30)。
—21— 新材料新装饰XINCAILIAOXINZHUANGSHI 2014年4期 汽车离合器用铜基金属
陶瓷摩擦材料的研究进展
冯超 徐吉波 魏子良 王琦 胡欢
(湖北汽车工业学院 材料科学与工程学院 十堰湖北 442002)
摘要:金属陶瓷摩擦材料具有吸能效率高、导热性好、摩擦系数高、耐高温、耐磨等特点,可用 于重型车、矿区用车、工程作业车、沙漠车等重载荷车辆以代替不抗热的有机摩擦片。
本文综述了铜基金属陶瓷摩擦材料的发展现状,展望了铜基金属陶瓷摩擦材料的发展前景。
关键词:金属陶瓷;铜基摩擦材料;研究进展
1前言 汽车离合器靠摩擦来传递动力。
当汽车行驶时,离合器的主动部件和从动盘相互压紧而一起旋转,但在起步、换档过程中,主、从动件之间相对摩擦,从动盘摩擦片发热并发生磨损。
离合器的使用寿命主要取决于其从动盘摩擦片的耐磨性。
通常汽车离合器从动盘摩擦片采用树脂基石棉材料做成。
在160℃以上树脂片自身及其对偶件的磨损量都急剧增大,而金属陶瓷片在250℃以上仍保持很好的耐磨性,其对偶的磨损也很小。
另一方面,金属陶瓷摩擦材料对铸铁的摩擦系数要比树脂石棉片对铸铁的摩擦系数高一些,因此用金属陶瓷摩擦片的离合器在同一夹紧载荷下,能比采用树脂片的离合器提供更大的摩擦力矩,亦即在保证相同的扭矩容量下所用的夹紧载荷减小,从而使离合器接合更柔和,在相同夹紧力下扭矩得到提高[1,2]。
2 铜基金属陶瓷摩擦材料的应用
从20世纪50年代起,国外就在拖拉机、工程机械及载货汽车上开始使用金属陶瓷磨擦材料作为离合从动盘的磨擦面片。
由于金属陶瓷磨擦面片的磨擦系数高于有机石棉片,采用金属陶瓷磨擦面片的离合器与采用石棉片的离合器相比,在同一夹紧载荷下可提供更大的磨擦力矩,即离合器扭矩容量较大;而在同样大小的扭矩容量下,所用夹紧载荷较小,使离合器接合更平稳、柔和。
此外,金属陶瓷材料比有机材料更耐高温,对于起步换挡频繁、离合器工作温度较高的汽车来说,用金属陶瓷材料更耐磨。
据有关资料介绍,在温度160℃以下有机片的耐磨性还是比较好,但当温度更高时,其耐磨性急剧下降;而金属陶瓷材料则在接近300℃的高温下仍有较好的耐磨性。
显然,对于使用条件恶劣的车辆来说,其离合器从动盘磨擦面的工作温度高,只有用耐高温的金属陶瓷材料才能保证足够长的使用寿命。
据有关资料介绍,采用金属陶瓷片的离合器使用寿命比有机片的长75%。
3 国内外研究现状 金属陶瓷磨擦材料是由金属基体、陶瓷成份和润滑剂组成的一种多元复合材料。
金属基体的主要作用是以机械结合的方式将陶瓷成份和润滑剂保持于其中,形成具有一定机械强度的整体;陶瓷成份主要起磨擦剂作用;而润滑剂成份则主要起提高材料抗咬合性和抗粘接性的润滑作用,特别有利于降低对偶材料的磨损,并使磨擦副工作平稳。
润滑剂组分和陶瓷组分共同形成金属陶瓷磨擦磨损性能的调节剂。
基体作为摩擦材料的主要组元,其作用主要是以机械结合方式将摩擦颗粒和润滑剂保持于其中,形成具有一定力学性能的整体。
基体的强度是摩擦材料承载能力的反应,在很大程度上取决于基体的成分、结构和物理一力学性能。
目前改善材料基体结构和强度主要从两个方面入手[3-4]:一是添加合金元素来强化基体。
二是在较软的基体中添加强度较高的金属纤维或其它增强纤维。
基体的组织结构、物理化学性质
在很大程度上决定了粉末冶金摩擦材料的力学性能、摩擦磨损性能、
热稳定性和导热性等整体性能的发挥。
摩擦材料要求基体具有足够高
的熔点,高的耐热强度和热稳定性,工作温度内有较高的塑性变形抗
力,高的耐磨性。
开展对基体成分及性能的研究至关重要,对提高铜
基金属陶瓷摩擦材料摩擦性能提供有益的指导。
对铜基金属陶瓷摩擦材料基体的研究,不能仅局限于基体本身,因为现代高性能粉末冶金摩擦材料大多是多组元的复合体,各个组元对材料性能的作用是相互影响的,因此研究基体的同时也应考虑其它组元加入后对基体的影响。
目前在基体方面的研究工作,大都是在摩擦材料三大组元都存在的情况下来研究的,主要涉及以下各个方面:基体的类型;基体的物理、机械性能对摩擦磨损性能的影响;合金元素(辅助组元)对基体性能的影响;基体组织、硬相和塑性相的分布、第二相的影响、摩擦过程中表层组织的变化;材料中非金属组分与金属基体的相互作用、基体夹持硬质点的能力、粘结问题的研究;改善基体的压制、烧结等工艺性能研究摩擦过程中表层元素扩散过程研
究;基体塑变能力对摩擦磨损性能的影响,孔隙度大小、分布对基体
性能的影响;改善基体耐热性、耐磨性的研究等诸多方面[5-6]。
4 发展现状
目前,随着重载汽车离合器片的发展,以及离合器结构设计的紧凑性要求,对铜基金属陶瓷摩擦材料的耐磨性和耐热性提出了更高要求,特别是高温制动的稳定性。
因此研究开发具有优异性能的新型铜基摩擦材料十分重要和迫切。
为提高铜基摩擦材料的耐热性和耐磨性,主要途径:添加合金元素来强化提高基体的耐磨性和耐热强度;通过改变材料的摩擦剂与润滑剂,调节材料的成分,如添加铁和石墨等耐高温、耐磨材料来提高摩擦材料的整体性能。
目前铜基纳米复合材料的研究成果表明:纳米氧化物作为弥散增强相所制备的弥散强化铜基复合材料,在保持铜本身高导热性能的同时还大幅度提高了强度及抗高温软化特性,具有其他强化方法无法比拟的优点。
因此,将纳米材料应用于铜基摩擦材料,为改善摩擦材料的摩擦学性能提供了新途径。
参考文献:
[1]黄建龙,王建吉,党兴武,陈生圣.铝含量对铜基粉末冶金材料性能的影响.润滑与密封,2013,38(1):56-60.
[2]邓海金,李明,龚敏.钢纤维对铜基金属陶瓷摩擦材料力学和摩擦学性能的影响.摩擦学报,2004,24(4):336-340.
[3]钟志刚,邓海金,李明,等.铁含量对铜基金属陶瓷摩擦磨损性能的影响.材料工程,2002,(8):17-19.
[4]王晔,燕青芝,张肖路,等.石墨对铜基粉末冶金闸片材料性能的影响.粉末冶金技术,2012,30(6):432-439.
[5]Xiong X,Sheng H C,Chen J,et al.Effects of sintering pressure and
temperature on microstructure and tribological characteristic of Cu-based
aircraft brake material.Transactions of nonferrous metals society of China,2007,17:669 -675. [6]湛永钟,张国定,曾建民,等.SiC 和石墨混杂增强铜基复合材料的高温摩擦磨损特性研究.摩擦学学报,2006,26(3):223-227. 基金项目:湖北汽车工业学院大学生创新性实验项目基金资助。