窑炉及其分类
工业窑炉

烧成带—烧成过程:坯体借助燃料燃烧所释放出的热量, 烧成带 烧成过程:坯体借助燃料燃烧所释放出的热量,达 烧成过程 到所要求的烧成温度, 到所要求的烧成温度,完成坯体的烧成过程 。 950~1300℃:烧成和高温保温阶段:有固相反应和液相出 ~ ℃ 烧成和高温保温阶段: 现。最终产物为玻璃相、莫来石晶体和未融解的石英颗粒。 最终产物为玻璃相、莫来石晶体和未融解的石英颗粒。 冷却带—冷却过程: 高温烧成的制品进入冷却带, 冷却带 冷却过程: 高温烧成的制品进入冷却带,与从窑尾 冷却过程 鼓入的大量冷空气进行热交换 ,完成坯体的冷却过程 1)1300~700℃:急冷阶段。可以保持玻璃相,防止低价铁 ) ~ ℃ 急冷阶段。可以保持玻璃相, 被氧化,从而提高产品的光泽度、 半透明度和白度。 被氧化,从而提高产品的光泽度、 半透明度和白度。 2) 700~400℃ :慢冷阶段:进行慢冷以适应晶型转变,从 ~ ℃ 慢冷阶段:进行慢冷以适应晶型转变, 而防止因冷却速度过快而导致陶瓷产品的开裂。 而防止因冷却速度过快而导致陶瓷产品的开裂。 3)快冷阶段(400 ℃ ~室温 :快冷可以提高陶瓷产品的烧制 )快冷阶段 室温): 速度,从而缩短其烧制周期。 速度,从而缩短其烧制周期。
工业窑炉的概念

工业窑炉的概念工业窑炉是一种用于加热物体的设备,主要用于加热和处理金属、玻璃、陶瓷、石材等材料,以达到特定的物理、化学或材料学要求。
窑炉的概念涉及到其结构、工作原理、应用领域和分类等多方面内容。
下面将从这些方面详细介绍工业窑炉的概念。
窑炉的结构一般由加热室、加热元件、控制系统和排放系统组成。
加热室一般是一个封闭的空间,用于容纳待加热物体。
加热元件通常是在加热室中产生并传递热量的部件,常见的有电加热元件、气体燃烧器和燃油喷油器等。
控制系统主要负责控制加热温度、时间和其他参数,以保证加热过程的稳定和可靠性。
排放系统则用于排除燃烧产生的废气和废渣。
窑炉的工作原理主要是通过加热元件产生的热量传递给待加热物体,使其温度升高并实现特定的物质变化。
加热室中的空气和燃料在燃烧过程中产生高温气体,这些高温气体通过对流和辐射等方式传递给待加热物体。
在炉内,待加热物体接受到热量后,其内部分子开始运动,产生应力、形变或化学反应,从而实现物质的热处理、熔化或变形等目的。
工业窑炉的应用领域十分广泛,包括冶金、玻璃、陶瓷、石材、塑料、纤维和电子等行业。
在冶金行业,窑炉主要用于金属的熔炼、锻造、淬火和退火等工艺。
在玻璃行业,窑炉则主要用于玻璃的熔化、成型和退火等处理。
在陶瓷行业,窑炉被用来烧制陶瓷制品,如陶瓷器皿、砖瓦和瓷砖等。
在石材行业,窑炉用于石材的烧结、热处理和表面修饰等工艺。
此外,窑炉在塑料加工、纤维制造和电子组装等领域也有广泛应用。
根据不同的加热原理和使用目的,工业窑炉可以分为多个不同的类型。
常见的窑炉类型包括电阻加热窑炉、感应加热窑炉、燃气窑炉、燃油窑炉、煤炭窑炉和太阳能窑炉等。
在电阻加热窑炉中,通过通电的加热元件直接产生热量;在感应加热窑炉中,则利用交变电磁感应产生加热效应。
而燃气窑炉、燃油窑炉和煤炭窑炉则是通过燃料燃烧产生热能。
太阳能窑炉则是利用太阳能对待加热物体进行加热。
不同类型的窑炉适用于不同的加热需求,选择适合的窑炉类型可以提高加热效率和质量。
国内石灰窑常见类型及选择节能减排窑型的原则
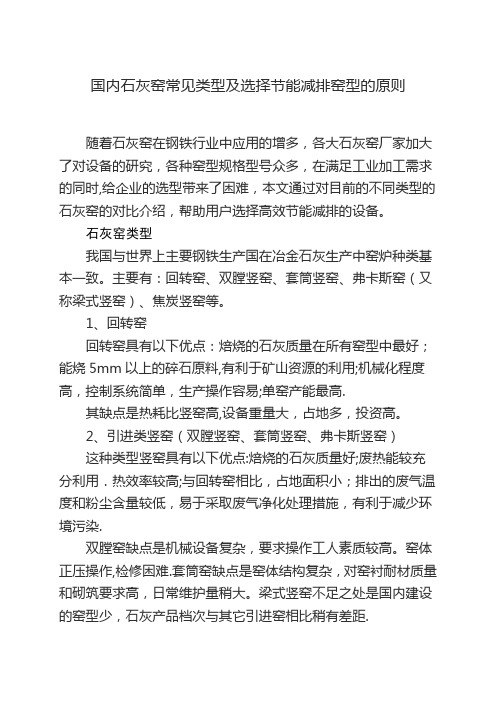
国内石灰窑常见类型及选择节能减排窑型的原则随着石灰窑在钢铁行业中应用的增多,各大石灰窑厂家加大了对设备的研究,各种窑型规格型号众多,在满足工业加工需求的同时,给企业的选型带来了困难,本文通过对目前的不同类型的石灰窑的对比介绍,帮助用户选择高效节能减排的设备。
石灰窑类型我国与世界上主要钢铁生产国在冶金石灰生产中窑炉种类基本一致。
主要有:回转窑、双膛竖窑、套筒竖窑、弗卡斯窑(又称梁式竖窑)、焦炭竖窑等。
1、回转窑回转窑具有以下优点:焙烧的石灰质量在所有窑型中最好;能烧5mm以上的碎石原料,有利于矿山资源的利用;机械化程度高,控制系统简单,生产操作容易;单窑产能最高.其缺点是热耗比竖窑高,设备重量大,占地多,投资高。
2、引进类竖窑(双膛竖窑、套筒竖窑、弗卡斯竖窑)这种类型竖窑具有以下优点:焙烧的石灰质量好;废热能较充分利用.热效率较高;与回转窑相比,占地面积小;排出的废气温度和粉尘含量较低,易于采取废气净化处理措施,有利于减少环境污染.双膛窑缺点是机械设备复杂,要求操作工人素质较高。
窑体正压操作,检修困难.套筒窑缺点是窑体结构复杂,对窑衬耐材质量和砌筑要求高,日常维护量稍大。
梁式竖窑不足之处是国内建设的窑型少,石灰产品档次与其它引进窑相比稍有差距.3、国产气烧竖窑该窑型是国内开发的传统窑型。
石灰质量适中,在活性石灰窑型中建设投资最低.由于采用煤气为燃料,石灰质量在原燃料条件满足要求时,可达到活性石灰标准的下线。
不足之处是窑顶废气温度高,热效率低,单窑产量低。
窑型选择原则由于以上不同窑型,特点各异;不同企业、不同时期,选择窑型时各项特点的权重也有所不同.但大部分需要遵循以下原则:1、资源综合利用效率传统的竖窑焙烧原料块度要求应大于40mm,而石灰石矿山开采,其原矿块度组成一般小于4Omm的占到总量的1/3左右。
考虑综合利用因素,回转窑具有很大的优势(10mm以上),双膛竖窑可以焙烧20mm以上的石灰石原料,因此从资源综合利用角度看,回转窑和双膛竖窑有利于提高资源综合利用率。
瓷器制作工艺中的窑炉设计优化研究
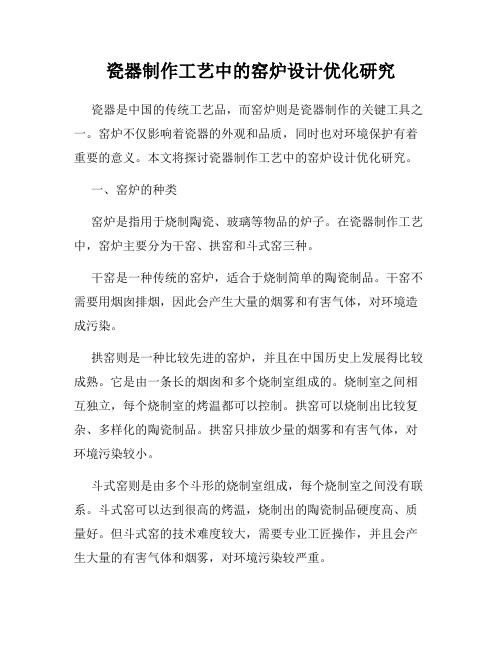
瓷器制作工艺中的窑炉设计优化研究瓷器是中国的传统工艺品,而窑炉则是瓷器制作的关键工具之一。
窑炉不仅影响着瓷器的外观和品质,同时也对环境保护有着重要的意义。
本文将探讨瓷器制作工艺中的窑炉设计优化研究。
一、窑炉的种类窑炉是指用于烧制陶瓷、玻璃等物品的炉子。
在瓷器制作工艺中,窑炉主要分为干窑、拱窑和斗式窑三种。
干窑是一种传统的窑炉,适合于烧制简单的陶瓷制品。
干窑不需要用烟囱排烟,因此会产生大量的烟雾和有害气体,对环境造成污染。
拱窑则是一种比较先进的窑炉,并且在中国历史上发展得比较成熟。
它是由一条长的烟囱和多个烧制室组成的。
烧制室之间相互独立,每个烧制室的烤温都可以控制。
拱窑可以烧制出比较复杂、多样化的陶瓷制品。
拱窑只排放少量的烟雾和有害气体,对环境污染较小。
斗式窑则是由多个斗形的烧制室组成,每个烧制室之间没有联系。
斗式窑可以达到很高的烤温,烧制出的陶瓷制品硬度高、质量好。
但斗式窑的技术难度较大,需要专业工匠操作,并且会产生大量的有害气体和烟雾,对环境污染较严重。
二、窑炉设计的问题在窑炉的设计中,有很多问题需要注意。
这些问题直接影响着烧制出的陶瓷制品的质量和环保程度。
首先,窑炉的加热方法应该掌握好。
不合理的加热方式会导致陶瓷制品变形、开裂等问题,影响制品的质量。
同时也会产生过多的烟雾和有害气体,对环境造成污染。
其次,窑炉的烟囱设计也是一个重要的问题。
烟囱的设计直接关系到排烟的效果,如果设计不合理会导致排烟不畅、二氧化碳和一氧化碳排放不完全等问题。
最后,窑炉的材料也需要注意选择。
窑炉内的材料应该具有一定的耐高温性能和化学稳定性。
如果材料不合格,会造成埋设热点位置不当,从而影响制品的质量和烧制效果。
三、窑炉设计优化研究在窑炉设计方面,优化研究是非常必要的。
通过对窑炉设计进行改进和优化,不仅可以提高烧制质量,同时也可以减少环境污染。
首先,可以从加热和排放方面入手,通过调整燃烧温度和烟囱高度等参数,提高排放效率和燃烧效率。
窑炉的分型

窑炉的分型本文档由杯子客 整理提供分享,供学习交流之用。
版权归著作公司所有,谢谢合作早在新石器时代,中国就已经发明了“穴窑”用来烧造陶器。
商周时期,又出现了升焰式的圆窑和方窑,但当时的瓷器与陶器同窑烧造,并无专门的瓷窑,像商周时期的原始瓷器与印纹硬陶即是同窑烧制。
随着制瓷业的不断发展,瓷窑才逐渐从陶窑中分离出来,成为专门烧造瓷器的窑炉。
按形制来分,窑炉有馒头窑(圆窑)、龙窑(长窑)、阶级窑、蛋形窑(景德镇窑)、葫芦形窑等多种.其中的馒头窑与龙窑是最为常见的,且沿用时间较长,北方的平原地区多使用馒头窑,而南方的山区、半山区则多依山建造龙窑;下面就谈一下这几种形制的窑炉。
馒头窑馒头窑又称“圆窑”,火膛与窑室合为一个馒头形的空间,故而得名。
馒头窑大约出现于西周晚期,一直沿用至今,它是北方地区流行的陶瓷窑炉形制,由窑门、火膛、窑室、烟囱等部分组成,多在生土层掏挖修制或以坯、砖砌筑而成。
馒头窑的特点是容易控制升温、降温的速度,保湿性较好,适用于焙烧胎体厚重、高温下釉黏度较大的瓷器;但由于它升温、降温都比较慢,烧成时间相对较长,且窑内温度前后、上下分布不够均匀,所以容易出次品。
馒头窑结构图龙窑又称长窑,多依山坡或土堆倾斜建筑,窑长多在30-80米之间,形似长龙,故称之龙窑。
龙窑结构分窑头、窑床、窑尾三部分。
龙窑出现于商代,这个时期的龙窑既烧制印纹硬陶,又烧制原始青瓷,即通常所说的“陶瓷同窑合烧”,至东汉晚期结束了陶瓷同窑合烧的状况,出现了专烧瓷器的龙窑。
此后,龙窑逐渐增长,各朝的倾斜度和结构也不断改进,使龙窑烧成效果不断完善,宋、元时期的龙窑出现了一种在窑室内砌筑多道挡火墙,将其分成若干小室,挡火墙下部设烟火孔,使室与室之间相通,即所谓的“分室龙窑”。
直至当今,南方有的地区仍然在使用龙窑烧制陶瓷器。
龙窑的特点是建筑方便,装烧量大,产量高,其升温、降温都很快,容易维持还原气氛,适合于焙烧胎体较薄、高温下釉黏度较小的石灰釉瓷器,所以有人说龙窑是青瓷的摇篮。
常见陶瓷窑炉名词解释

常見陶瓷窯爐名詞解釋窯爐陶瓷之燒成設備,陶瓷製作最後階段,坯體必須放入窯爐中以高溫燒成,使生坯轉變成為熟坯,而給予陶瓷必要之物理性質。
窯爐大致都有燃燒室,以產生熱量;有窯室以放置坯體;有煙道與煙囪,以排出廢氣。
窯爐的分類法很多,依燒成火焰之走向不同,可分為直焰窯、橫焰窯、與倒焰窯;依所用燃料之不同,可分為薪柴窯、煤炭窯、重油窯、瓦斯窯、電窯等;依操作的連續性不同,可分為間歇式窯、半連續式窯與連續式窯等。
包仔窯傳統窯爐之一,在大陸稱為「饅頭窯」,在臺灣則依其外觀稱為「包仔窯」或「龜仔窯」。
在清代已經引入臺灣,專用於燒製磚瓦,也稱「瓦窯」。
包仔窯在臺灣分布的地方很廣,幾乎各地都有包仔窯的使用。
包仔窯外觀呈長橢圓形,高度可達五公尺以上。
有窯門可供裝窯與出窯,其後即為燃燒室,裝窯時,臨時以磚塊砌為擋火牆。
其後方即為窯室,後面為窯牆,下方留有通火口,後面接煙囪。
蛇窯蛇窯引進臺灣的歷史很早,在清朝時即隨著移民傳播而來。
這種窯爐是中國南方生產陶瓷器主要使用的窯爐,在大陸稱為龍窯,到臺灣之後則稱為「蛇窯」。
是臺灣早期陶業使用最普遍的窯爐,使用地區幾乎遍及全島。
蛇窯由窯頭的燃燒室、窯身、以及窯尾的煙囪等三大部分組成,窯身外並護以土臺。
通常依山而建,頭低尾高,外觀呈長條圓管形,全長可達百餘尺。
登窯登窯於日治時期引進臺灣。
在大陸又稱為「階級窯」或「串窯」;因其依地勢築窯,各窯室拾級而上,日本人稱為「登窯」;由於登窯有一間一間的窯室,故臺灣業者稱其為「目仔窯」,又稱為「坎仔窯」。
主要用於燒製陶瓷與紅磚,苗栗為使用最普遍之地方。
登窯通常選擇山坡地勢築窯,如建在平地時,則要把地基墊高成一斜坡,再行築窯。
目仔窯屬於半連續式的半倒焰窯爐,依山勢建築,由幾個窯室拾級而上,由七、八間到十五、六間都有,各窯室前後串連而成。
前為燃燒室,後端有煙囪之設計。
四角窯四角窯外觀呈四方形,又稱「角窯」,也稱為「四方窯」或「方窯」,因為以煤炭為主要燃料,所以也稱「煤炭窯」。
熔盐炉窑炉设备类型分类
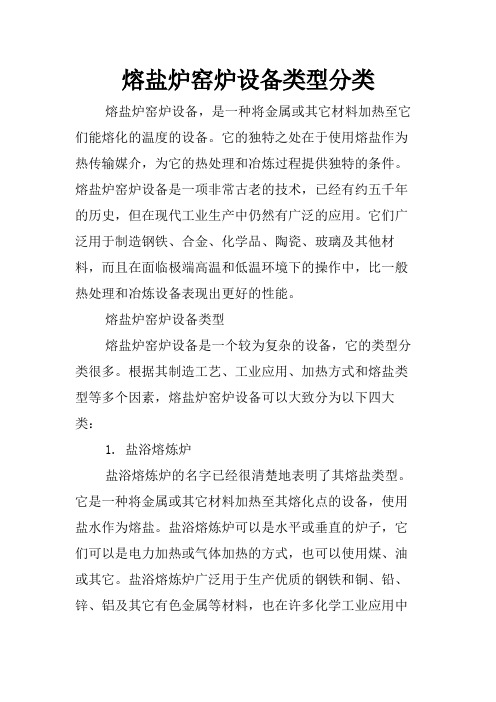
熔盐炉窑炉设备类型分类熔盐炉窑炉设备,是一种将金属或其它材料加热至它们能熔化的温度的设备。
它的独特之处在于使用熔盐作为热传输媒介,为它的热处理和冶炼过程提供独特的条件。
熔盐炉窑炉设备是一项非常古老的技术,已经有约五千年的历史,但在现代工业生产中仍然有广泛的应用。
它们广泛用于制造钢铁、合金、化学品、陶瓷、玻璃及其他材料,而且在面临极端高温和低温环境下的操作中,比一般热处理和冶炼设备表现出更好的性能。
熔盐炉窑炉设备类型熔盐炉窑炉设备是一个较为复杂的设备,它的类型分类很多。
根据其制造工艺、工业应用、加热方式和熔盐类型等多个因素,熔盐炉窑炉设备可以大致分为以下四大类:1. 盐浴熔炼炉盐浴熔炼炉的名字已经很清楚地表明了其熔盐类型。
它是一种将金属或其它材料加热至其熔化点的设备,使用盐水作为熔盐。
盐浴熔炼炉可以是水平或垂直的炉子,它们可以是电力加热或气体加热的方式,也可以使用煤、油或其它。
盐浴熔炼炉广泛用于生产优质的钢铁和铜、铅、锌、铝及其它有色金属等材料,也在许多化学工业应用中得到广泛的应用,比如溶剂回收,离子交换,工业炼油过程等等。
2. 熔盐浴炉熔盐浴炉是一种将金属或其它材料沉浸在熔融盐中加热的设备。
熔盐浴炉通常采用水平排列,使用动力供暖,可以采用煤气、燃油等不同的方式进行加热,也可以使用电加热器,是所有熔盐炉中最常见的一种。
它由熔盐槽、保温层和隔离罩组成,可用于高温化学反应、高温电化学制程过程中的物质融解和萃取等多种应用。
3. 熔盐清洗炉熔盐清洗炉是一种将金属或其它材料浸泡在熔融盐中清洗的设备。
它采用熔盐在高温下形成惰性气氛的特性,可清洗去金属的表面氧化皮、锈蚀和化学树脂等杂质,达到优质的表面处理效果。
熔盐清洗炉主要由焙烧炉、盐池和加热器等组成,同时也可以进行化学加工和溶剂回收等化学反应,具有非常广泛的应用。
4. 熔盐固化炉熔盐固化炉是一种采用熔盐床的热处理设备。
熔盐床是一个熔盐浴,将金属零件放置在其中,然后将其加热至高温,从而使熔盐固化在金属表面形成一种防护层。
陶瓷窑炉的种类很多

陶瓷窑炉在工艺美术陶瓷生产中 同样发挥着重要作用,通过高温 烧成和艺术加工,使陶瓷制品具 有独特的艺术价值和收藏价值。
工艺美术陶瓷生产通常需要使用 多种窑炉类型,如电窑、燃气窑、 柴窑等,以满足不同工艺和艺术
创作的需求。
高技术陶瓷生产
高技术陶瓷是指具有优异性能和功能的 陶瓷材料,如高强度、高硬度、高耐腐
智能检测与诊断
利用传感器和智能检测技 术,实时监测陶瓷窑炉的 运行状态,及时发现和解 决故障,确保生产安全。
远程监控与管理
通过互联网和物联网技术, 实现对陶瓷窑炉的远程监 控和管理,方便远程操控 和维护。
绿色环保发展
节能减排
采用先进的节能技术和设备,降 低陶瓷窑炉的能耗和排放,减少
对环境的污染。
废弃物资源化利用
B
C
油窑
以油料为主要燃料,如柴油、重油等,燃烧 温度高且稳定,适用于烧制高品质陶瓷制品。
气窑
以气体燃料为主要燃料,如天然气、液化石 油气等,燃烧温度高且环保,是现代陶瓷工 业中常用的窑炉。
D
按照结构分类
01
龙窑
呈长条形,依山而建,形似龙身,因此得名。燃烧室和 烧成室为一体,温度均匀,适用于烧制日用陶瓷和艺术 陶瓷。
通过自动化控制系统,可以精确控制窑炉的温度、压力、气氛等关键参数,确保产 品的一致性和稳定性。
自动化程度高的陶瓷窑炉还能减少人工干预和操作失误,降低生产成本和产品质量 风险。
03 陶瓷窑炉的应用
日用陶瓷生产
日用陶瓷生产是陶瓷窑炉最广泛的应 用之一,主要涉及家庭和餐饮场所使 用的餐具、茶具、咖啡具等陶瓷制品 的生产。
蚀性等。
高技术陶瓷广泛应用于航空航天、机械 制造、电子信息等领域,作为结构材料
- 1、下载文档前请自行甄别文档内容的完整性,平台不提供额外的编辑、内容补充、找答案等附加服务。
- 2、"仅部分预览"的文档,不可在线预览部分如存在完整性等问题,可反馈申请退款(可完整预览的文档不适用该条件!)。
- 3、如文档侵犯您的权益,请联系客服反馈,我们会尽快为您处理(人工客服工作时间:9:00-18:30)。
窑炉及其分类英文名称:kiln;furnace;oven用耐火材料砌成的用以煅烧物料或烧成制品的设备。
其种类甚多:按煅烧物料品种可分为陶瓷用窑炉、水泥窑、玻璃窑、搪瓷窑等。
前者按操作方法可分为连续窑(隧道窑)、半连续窑和间歇窑。
按热原可分为火焰窑和电热窑。
按热源面向坯体状况可分为明焰窑、隔焰窑和半隔焰窑。
按坯体运载工具可分为有窑车窑、推板窑、辊底窑(辊道窑)、输送带窑,步进梁式窑和气垫窑等。
按通道数目可分为单通道窑、双通道窑和多通道窑。
一般大型窑炉燃料多为重油,轻柴油或煤气、天然气。
窑炉通常由窑室、燃烧设备、通风设备,输送设备等四部分组成。
电窑多半以电炉丝、硅碳棒或二硅化钼作为发热元件。
其结构较为简单,操作方便。
此外,还有多种气氛窑、电瓷窑炉等。
窑炉结构是否合理,选型是否正确,直接关系到产品的质量,产量和能量消耗的高低等,是陶瓷生产中的关键设备。
生产陶瓷的一个重要过程是烧成,烧成是在窑炉中进行的。
陶瓷生产的窑炉有连续式的(隧道窑)也有间隙式的(倒焰窑),不管是隧道窑还是倒焰窑,其热效率都比较低。
效率低的原因除了燃烧损失、散热损失等原因外,重要的一点是排烟损失。
烧成隧道窑废气带走的热量损失约占总热量的20%~40%,而倒焰窑废气带走的热量约占燃料消耗量的30%~50%。
因之回收窑尾废气的热量加以利用是提高窑炉效率的关键。
国内隧道窑排烟温度一般在200~300℃,也有高达400℃,个别倒焰窑的排烟温度可高达560℃。
一方面窑炉排烟带走大量余热,另一方面为了干燥坯件,一些工厂又另外建造窑炉或锅炉产生热风和蒸汽以满足烘干坯件的要求。
采用热管换热器来回收烟气中的余热加热空气作为烘干坯件的热源,可以取得较好的节能效果。
一、隧道窑烟道气余热利用隧道窑余热回收主要用以加热空气作为烘干坯件的热源,也可作为助燃空气以提高窑炉本身的热效率,两者的选择可依据各工厂具体情况而定。
二、电瓷厂隧道窑冷却带余热利用将电瓷厂隧道窑冷却带400℃~450℃的废气抽出通过热管换热器换热,烟气温度降至300℃,再返回窑炉中烧成带作为气氛膜风使用。
被加热的新鲜空气送入烘房,干燥电瓷坯件。
三、倒焰窑烟道气余热利用某厂倒焰窑排烟温度为564℃,实测该窑炉热效率仅为23%,由于坯件入窑前需要预热烘干,因之需再建一个烘干窑,以煤作为燃料,燃烧的烟气作为烘干热源。
根据计算,如将560℃烟气降到160℃排空,将新鲜空气加热到60~120℃,其热量足够烘干坯件所用。
•陶瓷窑炉污染分析•我国是陶瓷生产大国,日用瓷和建筑卫生陶瓷的产量均居世界第一。
据有关资料显示,2003年建筑陶瓷产量达30亿平方米,占全世界总产量的40%;卫生陶瓷6000万~6500万件,全国有陶瓷厂上万家,拥有大小窑炉几万条,消耗能源4000万~5000万吨标准煤。
然而,我国是一个能源资源相对贫乏的国家,人均能源可采储量2000年石油为2.6吨、天然气为1074立方米、煤炭为90吨,分别为世界平均值的11.1%、4.3%和55.4%,远远低于世界的平均水平。
而陶瓷行业是一个高能耗的行业,能耗占陶瓷生产成本的30%~40%,陶瓷的高能耗必然带来高污染,故全国迅猛发展的陶瓷业对我国的环境造成很大的污染,特别是陶瓷发展迅速的瓷区及周边地区更为严重。
广东省内除佛山地区外,其他地区,如深圳、东莞、清远、潮州等地及全国各主要瓷区已出现不少有关陶瓷厂烟囱废气污染而造成附近农民果树及农作物枯死失收等纠纷。
另外,窑炉废气易造成酸雨,广东每年因酸雨损失多达40亿元。
因此,节能降耗减少陶瓷窑炉污染是陶瓷生产的大势所趋,也是陶瓷工业可持续发展的重要条件。
窑炉结构不合理造成热污染据报道,我国共有建筑卫生陶瓷厂3000多家,有大小窑炉上万座,年耗标准煤近500万吨。
而能源的利用率仅是美国的一半,即28%~30%.这些窑炉中,很大部分仍是砖砌式窑墙结构,窑墙厚。
早期的隧道窑,窑墙厚达1~2米,由于大都是重质耐火砖,导热系数大,故窑墙外表面温度高,有的高达300~400℃,不但造成了热损失,降低了窑炉的热效率,还造成严重热污染。
如车间窑炉旁温度高达几十摄氏度,造成车间环境恶劣,严重影响窑炉操作工人的身体健康。
现在很多辊道窑,辊棒日夜辊动,使填塞的保温棉辊成孔洞漏热,特别是正压操作,火焰从孔洞两边喷出,辊棒附近温度高达300~400℃,对周围环境造成严重热污染。
还有便是大多数的梭式窑,由于结构及烟气的排出没有经过余热回收,大多数的梭式窑尾气在600~860℃,不但大量的热从不锈钢板所弯制的烟囱排出,而且由于烟囱外壁的辐射对流把大量的热散失在车间周围引发热污染。
由于热耗增加,故要多消耗大量的燃料,燃料在燃烧过程中会产生更多的废气,污染环境。
保温材料和保温方式不合理不同的窑墙结构、保温材料,其保温效果完全不同,窑墙外表面的温度也不同。
利用轻质保温材料或陶瓷纤维,可大大地增强保温性能,使窑外壁的散热量大大减少,原因是纤维的导热系数一般只有传统耐火砖的1/6,容重在100~600千克/立方米,是传统耐火砖的1/25,而蓄热量仅为砖砌式炉衬的1/30~1/10,如实用温度在1300~1500℃的新型SX系列电阻炉,使用莫来石纤维,不但可以减少炉壁厚度,大大减轻窑炉重量,加快窑炉升温速度,空炉升温至1500℃,升温时间仅为传统电炉的1/18,即少于20分钟即可。
大大减少窑外壁的散热量,节能率可达30%左右。
在连续式窑炉高温部位粘贴莫来石纤维,节油率达28.7%.全纤维5立方米梭式窑每窑次耗气量为170千克左右,比原砖混结构窑炉,每次可节气60千克左右。
故现代的轻质窑墙或全纤维质窑墙保温性能都很好,窑外壁温度可降到30~60℃,大大提高了窑炉的热效率,减少窑墙的热污染。
同时,由于保温性能好,减少热损失,从而减少燃料的损耗,实际上是减少了废气污染。
燃料和燃烧方式不同形成的污染物不同(一)以煤为燃料我国是煤炭储量大国,同时也是世界上最大的煤炭消费国,耗煤量占世界总耗煤量的1/4,2000年煤产量达14.5亿吨,这么多煤炭,大部分都作为燃料烧掉,故煤炭作为燃料直接燃烧是我国大气污染的主要根源。
目前我国大气中90%的SO2、85%的CO2、80%的ROx(粉尘)和50%的NOx均来自煤的燃烧,其中煤炭燃烧后排放出的温室气体CO2占我国全部矿物燃料燃烧排放出的CO2的85%,而我国每年的CO2的排放量已排名世界第二位(13.6%)。
陶瓷窑炉使用燃料多种多样,而煤占燃料总消耗量的2/3,由于燃煤窑炉建造费用和燃料成本低,煤炭资源丰富,分布广泛,可就地取材,所以对大、中、小陶瓷企业,特别是乡镇企业,仍有很大的吸引力。
据资料统计,目前仅在日用陶瓷、建筑卫生陶瓷生产企业中就有3000余座燃煤窑炉,达到窑炉总数的70%.据计算,烧天然气的CO2排放量比烧煤炭少45%左右,烧石油比烧煤炭少15%左右。
燃烧产生的大量CO2促使地球大气层产生温室效应,造成地球表面温度逐年升高,使人类生态环境受到极大的威胁,人类文明进程中所产生的温室气体的负面作用正威胁着人类本身的生存和发展,国际上已提出“大气污染防治重点在亚洲,而亚洲的关键在中国”。
各国为了减轻温室效应给人们带来的严重后果,采取各种积极措施,如丹麦、荷兰、瑞典、芬兰4国已开始向企业征收CO2排放税,多数国家征收煤炭税,即用税收政策来控制CO2的排放量。
SO2虽不是温室气体,但却是很有害的气体,它与空气中的水蒸汽结合生成的亚硫酸和硫酸对森林植被、农作物、建筑物、文物古迹、牲畜等一切生物及人类本身都有很大的危害。
据统计,陶瓷工业窑炉的节能问题,始终制约着陶瓷行业的发展。
此前,据对一些企业能耗的调查,结果显示卫生陶瓷烧成能耗指标最高与最低相比,有的可达到几倍。
进入21世纪以来,国际能源市场供应形势发生了许多变化,令人不得不更加关注陶瓷行业的节能。
可以说,将来陶瓷业的竞争首先是降低能耗型的先进烧成技术的竞争。
现代建筑卫生陶瓷行业使用的窑炉,具有许多先进的工艺技术特点。
具体分析其特点,有:使用了洁净的能源种类与采用了全自动化控制高速喷嘴;新型节能型窑炉大量采用了轻质□热的耐火材料;窑炉设计为宽断面明焰裸烧型结构;节能型窑炉更能够适宜流行的低温快烧生产方式。
1.洁净能源与全自动化高速喷嘴大多数陶瓷窑炉由于采用了高效喷嘴,清洁高热效能源已成为陶瓷烧成燃料的主流。
纵观陶瓷发展史,适宜于陶瓷烧成的能源种类很多,有固体燃料、液体燃料及气体燃料等。
它们有木柴、煤炭、重油、轻质油、电力、天然气、液化石油气等等。
随着历史前进,烧成技术不断提高,有的能源地位上升,有的则被淘汰出局。
例如,用于传统陶瓷制品烧成的木柴与煤炭等固体燃料,由于热效低及对环境污染严重等原因,在建筑卫生陶瓷生产方面已经基本完成了其历史使命。
重油与液化石油气热值高,便于低温快速烧成,尤其是液化石油气在新兴建筑卫生陶瓷行业成为最受青睐的能源种类。
由于液化石油气热值高,燃气内杂质含量少,且容易快速升温与降温,非常方便于陶瓷的低温快烧工艺。
随着等温高效均匀燃烧喷嘴的革新与推广,将极大地降低能源消耗。
新型全自动化控制高速喷嘴由于强力的喷燃系统,可以降低窑内温差,迅速提高窑温,实现快速等温烧成效率。
因此,陶瓷窑炉的节能今后将取决于新型全自动化控制高速喷嘴的不断改进。
2.明焰裸烧方式从陶瓷烧成的发展历史看,陶瓷工业窑炉的烧成方式分为明焰装匣烧(传统煤烧隧道窑)、□焰露烧(马氟窑)及明焰裸烧(辊道窑、梭式窑、电窑)等多种方法。
2.1明焰装匣烧成方法此类烧成方式采用了木柴或煤炭作为能源。
产品装匣的目的:一是为了避免木灰或煤渣的污染;二是为了增加产品的装载量。
由于制品是先放入匣钵内,再组装成匣钵柱入窑烧成,产品不是直接受热,大量的能源消耗在窑具上,因此明焰装匣烧成方法能耗非常高,窑内上下温差大而且烧成周期很长。
此种烧成方法造成产品废品率高,经济效益低,长期以来制约了国内陶瓷工业的发展。
2.2□焰露烧方法马氟窑是□焰露烧方法的代表性窑型。
□焰露烧方式可以部分解决窑内温差的问题,但由于产品的烧成仍然为□焰受热方式,大量的能源消耗在厚厚的耐火材料□壁上,而且□焰露烧使用的窑炉窑型小,不能形成大规模生产批量。
2.3明焰裸烧方法明焰裸烧方法是20世纪70年代以来陶瓷烧成最引人注目的成果。
明焰裸烧方法作为最先进的烧成方法在窑温的均匀性、窑容积、生产强度和单位耗能方面均表现出最佳效果,成为现代建筑卫生陶瓷烧成的首选窑型,因此能在很短的时间内推广普及。
明焰裸烧方式窑温均匀性高,这是由于此种烧成方式的产品垛阻力小、窑内压力降低、预热带负压低,因此漏入冷空气少。
由于烧嘴的喷射作用,窑炉内的气流强烈循环、热焰剧烈扰动,对于均匀和平衡窑内温度非常有利。