涡流缺陷检测
涡流检测

涡流检测适用于导电材料探伤,常见的金属材料可分为两大类:非铁磁性材料和铁磁性材料。
后者为铜、铝、钛及其合金和奥氏体不锈钢;前者为钢、铁及其合金。
它们的本质差别是材质磁导率μ约为1或远大于1 。
在发电厂,除復水器等少量管道使用铜、钛、奥氏体不锈钢非铁磁性材料外,大量管道都采用钢管等铁磁性材料,典型的应用有省煤器、水冷壁等。
常规涡流探伤应用于非铁磁性管子,已是非常成熟的技术,它不单能探测出缺陷,并可以利用阻抗平面技术分析出缺陷所在的位置与深度。
然而,将它简单地应用于铁磁性材料的钢管,却得不到预期的结果,其原因何在?这是由于铁磁性材料μ>>1,根据涡流标准渗透公式:δ=503.3/√fμrσ可知在这种情况下,涡流只能集中在表面,无法渗透到材料的内部。
除此以外,铁磁性材料的磁畴结构,将对涡流检测信号产生极大的干扰,足以把缺陷信号完全淹没,而无法得到有用的信息。
克服铁磁性金属磁导率对探伤影响的方法有两种:其一,采用远场涡流检测方法;其二,对钢管进行饱和磁化后再探伤。
前一种方法需要更新仪器,后一种方法只需在原有常规仪器的基础上增加磁饱和装置即可对钢管等进行探伤,具有投资少的优点。
经过磁饱和处理后的铁磁性材料可以以非铁磁材料对待。
通常钢管涡流探伤采用通过式磁饱和器。
它是由通有直流电的线圈来产生稳恒强磁场,并借助于导套等高导磁部件将磁场疏导到被检测钢管的探伤部位,使之达到磁饱和状态。
为了充分利用线圈产生的磁场,装置一般都有由铁磁性材料(如纯铁)制作的外壳。
由于纯铁的μ值很大,磁阻很小,泄漏在空间中的磁力线会被铁壳收集,也被疏导到钢管的检测部位。
由于强大的磁化电流通过磁饱和器线圈,会使线圈发热,因此要有良好导热措施,以防线圈烧毁。
磁饱和装置除了用来产生强大的直流磁场外,检测线圈也常常用它来夹持,所以磁饱和装置的结构与检测线圈的外形有着密切关系。
在穿过式涡流探伤中,磁饱和装置中的导套与检测线圈必须保持同心,否则会造成较大的周向灵敏度差,导致漏检和误检。
涡流检测的实施步骤包括

涡流检测的实施步骤包括1. 准备工作在进行涡流检测之前,需要进行一些准备工作。
具体步骤如下:•确定被测物体:首先需要确定被测物体,即需要进行涡流检测的工件或部件。
可以是金属、合金等导电材料。
•检查设备:检查涡流检测设备是否完好,并且确保设备具备足够的能力来检测出所需的缺陷。
•清洁表面:确保被测物体的表面干净,并且没有任何影响检测结果的物质,如污垢、油脂等。
2. 设置参数在进行涡流检测之前,需要根据被测物体的特征和检测要求来设置合适的参数。
具体步骤如下:•选择探头:根据被测物体的几何形状和尺寸,选择合适的涡流探头。
探头的尺寸和形状会影响到检测的灵敏度和分辨率。
•设置频率:选择合适的涡流频率,一般根据被测物体的导电性和检测要求来确定。
高频率可以提高灵敏度,但对深层缺陷的探测能力较弱,低频率则相反。
•设置灵敏度:根据被测物体的厚度、材质和检测要求来设置灵敏度。
灵敏度越高,对于小缺陷的探测能力越强,但可能出现误报现象。
3. 整备设备完成参数设置后,需要对涡流检测设备进行整备。
具体步骤如下:•连接设备:将涡流探头与检测设备连接,并进行牢固的固定,确保接触良好。
•校准设备:根据设备的要求,进行设备的校准工作。
校准的目的是保证设备的准确性和可靠性。
4. 进行涡流检测整备设备完成后,可以开始进行涡流检测。
具体步骤如下:•放置探头:将探头放置在被测物体的表面上,并确保与表面充分接触。
•移动探头:以适当的速度和方向移动探头,对被测物体的表面进行扫描。
应覆盖整个被测区域,确保不漏检。
•检测结果:根据设备的反馈,观察和记录涡流检测的结果。
发现任何缺陷或异常情况时,应及时采取进一步的措施。
5. 结果分析完成涡流检测后,需要对结果进行分析和评估。
具体步骤如下:•分析数据:将涡流检测的数据进行整理和分析。
根据数据,可以判断出是否存在缺陷,并对缺陷进行分类和定位。
•评估结果:根据检测结果和缺陷的性质,对被测物体的质量进行评估。
涡流检测—涡流检测基本原理(无损检测课件)

第2节 涡流检测的基本原理
原理
原理:当载有交变电流的线圈接近被检工件时,材料表面与近 表面会感应出涡流,其大小、相位和流动轨迹与被检工件的电 磁特性和缺陷等因素有关,涡流产生的磁场作用会使线圈阻抗 发生变化,测定线圈阻抗即可获得被检工件物理、结构和冶金 状态等信息。
第2节 涡流检测的基本原理
2. 涡流检测的特点
➢ (1ቤተ መጻሕፍቲ ባይዱ适用于各种导电材质的试件探伤。包括各种钢、钛、 镍、铝、铜及其合金。
➢ (2)可以检出表面和近表面缺陷。 ➢ (3)探测结果以电信号输出,容易实现自动化检测。 ➢ (4)由于采用非接触式检测,所以检测速度很快。 ➢ (5)不需接触工件也不用耦合介质,所以可以进行高温
在线检测。
2. 涡流检测的特点
➢ (6)形状复杂的试件很难应用。因此一般只用其检测管 材,板材等轧制型材。
➢ (7)不能显示出缺陷图形,因此无法从显示信号判断出 缺陷性质。
➢ (8)各种干扰检测的因素较多,容易引起杂乱信号。 ➢ (9)由于集肤效应,埋藏较深的缺陷无法检出 ➢ (10)不能用于不导电材料的检测。
涡流检测
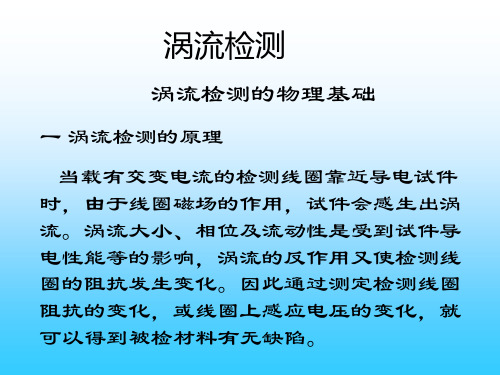
电导率
磁导率
测量金属试件的电磁参数; 金属热处理状态的鉴别; 金属材料的分选;
金属材料成分含量、杂质含量的 鉴别。
提离效应、厚度效 应、充填效应等
金属试件上涂、镀等膜层测量; 板材测厚; 位移、振动测量; 液面位置、压力等的监控; 试件尺寸、形状测量等。
1 1 f
2
渗透深度 与频率 f 的平方根成反比。
涡流检测的试验基础
将两个线圈固定在一起。在线圈Ⅰ上输 入交流电流,在线圈Ⅱ上接一个电压表, 同时把这两个线圈放在金属块上面。
线圈Ⅰ将激励出一个交变磁场。如果 线圈Ⅰ、线圈Ⅱ和金属块靠的很近,以 至于线圈Ⅰ所激励的磁场对线圈Ⅱ和金
属块都有感应,那么在金属块中就会产
阻抗,即线圈空载阻抗,X1L1 为空载的 感抗。
Z 2 2 R 2 jL 2 R 2 j2 X 表示涡流环的自阻
抗,X2L2为涡流环的感抗。
Z 12 jX MjM 表示检测线圈与涡流环的
耦合阻抗,XMM称为耦合电抗。
➢反射阻抗与视在阻抗
反射阻抗: Z1' 1R' jX'
表示被测导体上的涡流场对检测线圈 的影响。
电压表读数随线圈与金属块之间 距离的变化而改变的现象,在涡流 检测中我们称为“提离”效应。应 用这个效应,我们就可以用涡流检 测法来测定金属材料表面上的绝缘 层的厚度。
涡流探伤法主要是用于检查金属表 面或近表面上的裂纹等缺陷。由于被 检零件一旦发生了裂纹等缺陷,那么 在零件的缺陷处不仅导电率或磁导率 发生了变化,而且零件的尺寸也发生 了相应的变化。所以涡流探伤法既应 用了导电率或导磁率效应,也应用了 尺寸效应。
第三节 涡流阻抗分析法
涡流检测原理
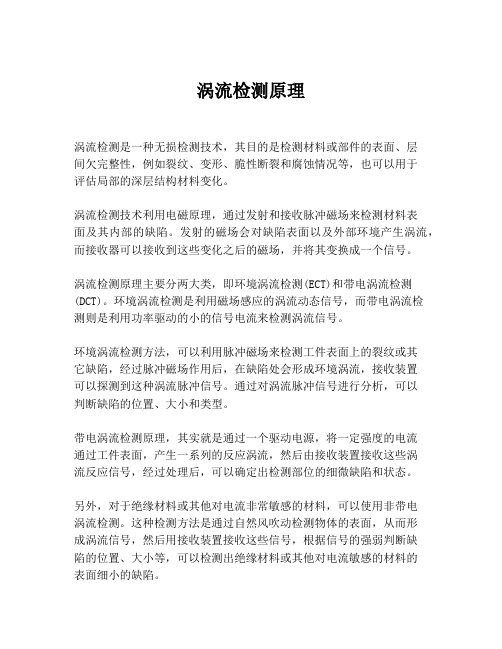
涡流检测原理涡流检测是一种无损检测技术,其目的是检测材料或部件的表面、层间欠完整性,例如裂纹、变形、脆性断裂和腐蚀情况等,也可以用于评估局部的深层结构材料变化。
涡流检测技术利用电磁原理,通过发射和接收脉冲磁场来检测材料表面及其内部的缺陷。
发射的磁场会对缺陷表面以及外部环境产生涡流,而接收器可以接收到这些变化之后的磁场,并将其变换成一个信号。
涡流检测原理主要分两大类,即环境涡流检测(ECT)和带电涡流检测(DCT)。
环境涡流检测是利用磁场感应的涡流动态信号,而带电涡流检测则是利用功率驱动的小的信号电流来检测涡流信号。
环境涡流检测方法,可以利用脉冲磁场来检测工件表面上的裂纹或其它缺陷,经过脉冲磁场作用后,在缺陷处会形成环境涡流,接收装置可以探测到这种涡流脉冲信号。
通过对涡流脉冲信号进行分析,可以判断缺陷的位置、大小和类型。
带电涡流检测原理,其实就是通过一个驱动电源,将一定强度的电流通过工件表面,产生一系列的反应涡流,然后由接收装置接收这些涡流反应信号,经过处理后,可以确定出检测部位的细微缺陷和状态。
另外,对于绝缘材料或其他对电流非常敏感的材料,可以使用非带电涡流检测。
这种检测方法是通过自然风吹动检测物体的表面,从而形成涡流信号,然后用接收装置接收这些信号,根据信号的强弱判断缺陷的位置、大小等,可以检测出绝缘材料或其他对电流敏感的材料的表面细小的缺陷。
总之,涡流检测是一种重要的无损检测技术,它利用电磁原理,利用脉冲磁场、驱动电源电流以及自然风吹动等多种方式,可以快速有效地检测出材料表面及其内部的裂纹、变形、脆性断裂和腐蚀情况等,为材料的质量检测提供了可靠的依据。
涡流检测技术
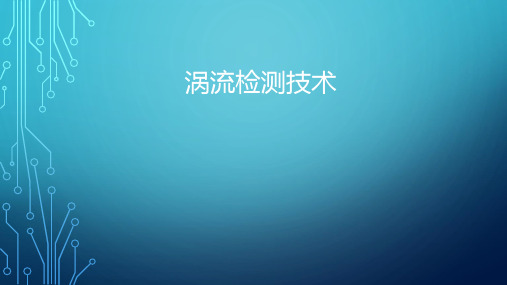
Thank you
涡流检测的主要用途及影响感生涡流的特性的主要因素
目的 探伤
材质试验
厚度及位移 等的测量
检测因素 试件中的裂纹、腐 蚀、凹坑、夹杂、 气泡等
电导率 磁导率
提离效应、厚度效 应、充填效应等
典型应用
管、棒、线、板材等的探伤; 机制件的探伤; 飞机维护及管道系统的维护检查; 疲劳裂纹的监视。
测量金属试件的电磁参数; 金属热处理状态的鉴别; 金属材料的分选; 金属材料成分含量、杂质含量的鉴 别。
金属试件上涂、镀等膜层测量; 板材测厚; 位移、振动测量; 液面位置、压力等的监控; 试件尺寸、形状测量等。
主要应用
• (1)能检测出材料和构件中的缺陷,例如裂纹、折叠、气孔和夹杂等。 • (2)能测量材料的电导率、磁导率、检测晶粒度、热处理状况、材料
的硬度和尺寸等。
• (3)金属材料或零件的混料分选。通过检查其成分、组织和物理性能
当探头从零件的中间部位移动到零件的边缘时,仪器所发生的报警现
象,是由于边缘效应所致,一般不是裂纹信号
当探头扫描移动到局部漆层脱落处,仪器所发出的报警现象,属间隙
效应引起,一般不是裂纹信号
当探头移动到受检部位的形状,或曲率发生变化的区域时,发出的报
警现象,一般不是裂纹信号
在对非磁性材料进行涡流检测过程中,如探头移动到磁性材料附近,
涡流检测的特点
• 优点: • (1)不需耦合剂,对管、棒、线材易于实现自动化。 • (2)对导电材料表面和近表面缺陷的检测灵敏度较高。 • (3)能在高温、高速下进行检测。 • (4)应用范围广,对影响感生涡流特性的各种物理和工艺因素均能实现检测。 • (5)工艺简单、操作容易、检测速度快。
涡流探伤检测的原理和应用

涡流探伤检测的原理和应用1. 原理介绍涡流探伤检测是一种无损检测技术,通过利用涡流感应原理来检测材料中的缺陷和表面裂纹。
涡流探伤检测主要适用于导电材料,如金属材料。
涡流探伤的原理基于法拉第电磁感应定律。
当交变电流通过线圈时,会在线圈周围产生交变磁场。
当磁场与导体相互作用时,会产生涡电流。
这些涡电流在导体中形成闭合回路,并且会导致磁场中的感应电动势。
涡流的大小和方向取决于导体的电导率和磁场的变化。
在涡流探伤中,线圈会在被检测的材料表面移动。
当线圈接近缺陷或表面裂纹时,由于局部磁场的变化,涡流的大小和分布会发生变化。
这种变化可以通过检测磁场中的感应电动势来识别和定位缺陷。
2. 涡流探伤的应用涡流探伤广泛应用于各个工业领域,主要用于以下几个方面:2.1 缺陷检测涡流探伤可用于检测材料中的缺陷,如裂纹、松动部分和孔洞等。
通过检测涡流的变化,可以判断缺陷的位置、形状和大小。
这对于确保材料的质量和安全性非常重要。
2.2 表面质量检查涡流探伤也可以用来检查材料表面的质量,如表面裂纹、划痕和氧化等。
通过对表面涡流的变化进行分析,可以快速发现表面缺陷,并及时采取修复措施。
2.3 零部件排序和分级在制造业中,涡流探伤可以用来对零部件进行排序和分级。
通过检测涡流的变化,可以判断零部件是否符合规格要求,并将其按照质量等级进行分类。
这有助于提高生产效率和产品质量。
2.4 腐蚀检测涡流探伤也可用于检测材料表面的腐蚀情况。
由于腐蚀会改变材料的电导率,涡流探测能够检测到这种电导率的变化,并通过分析涡流的特征来确定腐蚀的程度和位置。
3. 涡流探伤的优势涡流探伤具有以下几个优势:•无需接触被检测材料,非破坏性检测•可对复杂形状的零部件进行检测•检测速度快,可以实现自动化检测•检测结果直观易读,可进行定量化分析4. 涡流探伤的局限性涡流探伤也存在一些局限性:•只适用于导电材料,无法用于非导电材料的检测•线圈的质量和设计对检测结果有较大影响•检测深度有限,无法检测材料内部的缺陷•检测结果受材料的性质和表面状态影响较大5. 结论涡流探测作为一种非破坏性检测技术,具有广泛的应用前景。
涡流检测实验报告总结(3篇)
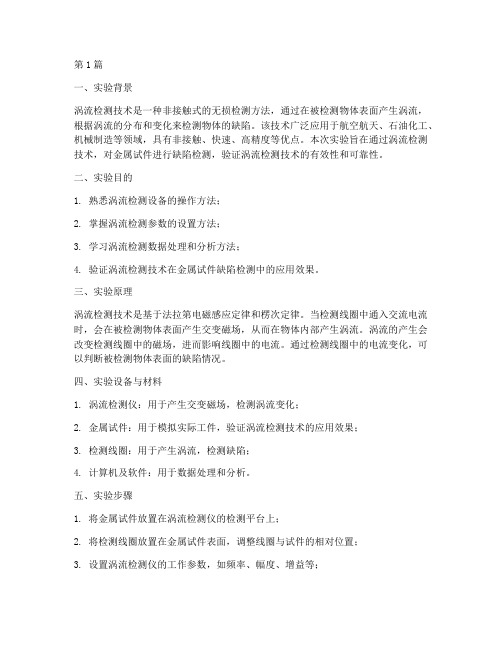
第1篇一、实验背景涡流检测技术是一种非接触式的无损检测方法,通过在被检测物体表面产生涡流,根据涡流的分布和变化来检测物体的缺陷。
该技术广泛应用于航空航天、石油化工、机械制造等领域,具有非接触、快速、高精度等优点。
本次实验旨在通过涡流检测技术,对金属试件进行缺陷检测,验证涡流检测技术的有效性和可靠性。
二、实验目的1. 熟悉涡流检测设备的操作方法;2. 掌握涡流检测参数的设置方法;3. 学习涡流检测数据处理和分析方法;4. 验证涡流检测技术在金属试件缺陷检测中的应用效果。
三、实验原理涡流检测技术是基于法拉第电磁感应定律和楞次定律。
当检测线圈中通入交流电流时,会在被检测物体表面产生交变磁场,从而在物体内部产生涡流。
涡流的产生会改变检测线圈中的磁场,进而影响线圈中的电流。
通过检测线圈中的电流变化,可以判断被检测物体表面的缺陷情况。
四、实验设备与材料1. 涡流检测仪:用于产生交变磁场,检测涡流变化;2. 金属试件:用于模拟实际工件,验证涡流检测技术的应用效果;3. 检测线圈:用于产生涡流,检测缺陷;4. 计算机及软件:用于数据处理和分析。
五、实验步骤1. 将金属试件放置在涡流检测仪的检测平台上;2. 将检测线圈放置在金属试件表面,调整线圈与试件的相对位置;3. 设置涡流检测仪的工作参数,如频率、幅度、增益等;4. 启动涡流检测仪,观察检测线圈中的电流变化;5. 分析电流变化,判断金属试件表面的缺陷情况;6. 改变检测参数,观察电流变化,验证参数对检测结果的影响;7. 记录实验数据,进行数据处理和分析。
六、实验结果与分析1. 在实验过程中,发现金属试件表面存在明显的缺陷,涡流检测仪能够准确检测出缺陷的位置和大小;2. 通过调整涡流检测仪的工作参数,发现参数对检测结果有显著影响。
适当调整参数,可以提高检测精度和灵敏度;3. 实验结果表明,涡流检测技术在金属试件缺陷检测中具有较好的应用效果,可以满足实际工程需求。
- 1、下载文档前请自行甄别文档内容的完整性,平台不提供额外的编辑、内容补充、找答案等附加服务。
- 2、"仅部分预览"的文档,不可在线预览部分如存在完整性等问题,可反馈申请退款(可完整预览的文档不适用该条件!)。
- 3、如文档侵犯您的权益,请联系客服反馈,我们会尽快为您处理(人工客服工作时间:9:00-18:30)。
我们只是知道,可以采用涡流检测的方式,对工程组件进行探伤,这也是比较常用的方式。
然而,涡流检测具体能够对工程组件的哪些区域、哪些部位进行检测,我们也许并不是很清楚。
下面,我们就来看看涡流缺陷检测的应用范围。
1、裂纹和缺陷探伤
涡流探伤技术非常适用于查找金属部件的表面裂缝和缺陷,探伤效率极高。
在受到交变磁场诱导后,待探伤制品内将产生涡流流动,如果这些涡流被表面裂缝或者缺陷中断,涡流探头和仪器将会探测出涡流的变化并将该存有裂缝的制品标记为失效产品。
涡流探伤对于裂缝和缺陷来说,是一种非常干净、快速且探伤结果可重复的好方法,而且很容易被整合到生产过程中,用于探伤一些利用肉眼难以察觉的缺陷。
所用的探伤探针可以根据需求进行定制以有针对性的适应一些面积较小、难以触及的关键区域。
此外,有了阵列探测器和材料处理系统的辅助还能够实现对一些大型或者复杂产品的表面区域进行探伤。
可以利用涡流探伤技术探伤缺陷的产品主要有:车轮轴承、滚子轴承、小齿轮、轴、传动齿轮、活塞、紧固件、管道系统以及钢轨等。
2、热处理和材料结构验证
涡流探伤还能通过与已知结构的完好组件进行对比,进而验证待测试件是否具有完好的材料结构。
热处理过程中的变化以及所使用合金种类的不同都会导致材料结构的差异。
这些差异会导致测试件表面硬度和硬化层深度的变化。
涡流探伤技术能够通过材料电导率和磁导率的变化探伤出这些差异,因此,该技术有助于验证测试件的结构完整性和耐久性。
涡流探伤对于热处理和材料结构验证方面,属于一种快速、干净的探伤方法;对产品的探伤结果通常可以清晰的显示出“通过”或“不合格”。
可以利用涡流探伤技术进行热处理过程和材料结构验证的产品主要有:车轮轴承、滚子轴承、轴杆、小齿轮、球钉、金属粉末烧结产品、插销、紧固件、传动齿轮、传动系组件以及医疗器件等。
3、螺纹、功能件和装配件验证
类似于上述结构测试,涡流探伤技术还能够用于验证螺纹的质量问题、组件的功能验证、或者验证某个装配件是否被正确地组装在一起。
对螺纹进行涡流探伤有助于识别出螺纹是否出现局部受损、尺寸是否过大或者过小、设计是否合理等信息。
可以利用涡流探伤进行功能验证的组件主要包括:门凹槽、齿条等。
装配件的验证测试主要包括:轴承座圈上球轴承的安装、轴承内的夹杂物、活塞环的取向以及阀门和管件的组装等。
南京博克纳自动化系统有限公司总部位于美丽的中国古都南京,是国内专业研制无损检测仪器及设备的高科技企业。
公司致力于涡流、漏磁和超声波仪
器及各种非标设备的研制,已拥有自主研发的多项国家专利。
产品被广泛应用
于航天航空、军工、汽车、电力、铁路、冶金机械等行业。
产品出口:美国、
俄罗斯、德国、新加坡、泰国、印度、香港、南非、台湾、越南、哈萨克斯坦、伊朗、日本、韩国、巴西。
博克纳科技作为无损检测仪器及设备、传感器开发的公司,一直是研发和
制造高质量、高性能无损检测仪器及设备的创新厂家。
我们以客户为中心提供
设计服务,以满足用户的不同应用需求。
公司与国内有名的院校、科研所组成了社会化科研协作网络,具有强大的
研发、生产能力。
保证了公司的工业无损检测技术国内、国际过硬的技术地位。