ProCAST 熔模铸造过程数值模拟
数值模拟技术在机器人铸件熔模铸造工艺中的应用
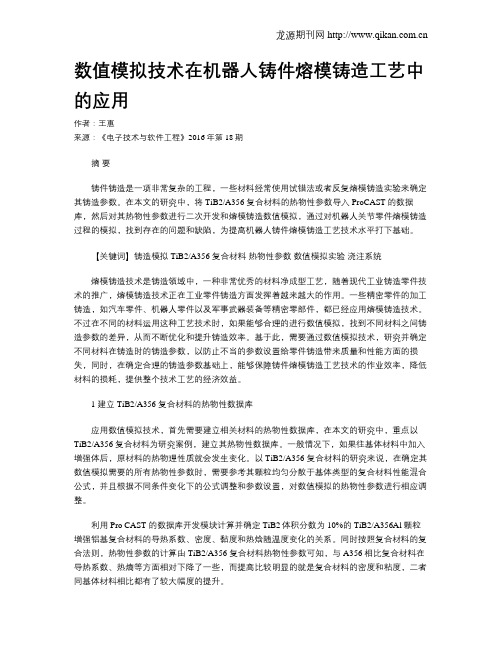
数值模拟技术在机器人铸件熔模铸造工艺中的应用作者:王惠来源:《电子技术与软件工程》2016年第18期摘要铸件铸造是一项非常复杂的工程,一些材料经常使用试错法或者反复熔模铸造实验来确定其铸造参数。
在本文的研究中,将TiB2/A356 复合材料的热物性参数导入ProCAST的数据库,然后对其热物性参数进行二次开发和熔模铸造数值模拟,通过对机器人关节零件熔模铸造过程的模拟,找到存在的问题和缺陷,为提高机器人铸件熔模铸造工艺技术水平打下基础。
【关键词】铸造模拟 TiB2/A356 复合材料热物性参数数值模拟实验浇注系统熔模铸造技术是铸造领域中,一种非常优秀的材料净成型工艺,随着现代工业铸造零件技术的推广,熔模铸造技术正在工业零件铸造方面发挥着越来越大的作用。
一些精密零件的加工铸造,如汽车零件、机器人零件以及军事武器装备等精密零部件,都已经应用熔模铸造技术。
不过在不同的材料运用这种工艺技术时,如果能够合理的进行数值模拟,找到不同材料之间铸造参数的差异,从而不断优化和提升铸造效率。
基于此,需要通过数值模拟技术,研究并确定不同材料在铸造时的铸造参数,以防止不当的参数设置给零件铸造带来质量和性能方面的损失,同时,在确定合理的铸造参数基础上,能够保障铸件熔模铸造工艺技术的作业效率,降低材料的损耗,提供整个技术工艺的经济效益。
1 建立TiB2/A356 复合材料的热物性数据库应用数值模拟技术,首先需要建立相关材料的热物性数据库,在本文的研究中,重点以TiB2/A356 复合材料为研究案例,建立其热物性数据库。
一般情况下,如果往基体材料中加入增强体后,原材料的热物理性质就会发生变化。
以 TiB2/A356 复合材料的研究来说,在确定其数值模拟需要的所有热物性参数时,需要参考其颗粒均匀分散于基体类型的复合材料性能混合公式,并且根据不同条件变化下的公式调整和参数设置,对数值模拟的热物性参数进行相应调整。
利用 Pro CAST 的数据库开发模块计算并确定 TiB2体积分数为 10%的 TiB2/A356Al 颗粒增强铝基复合材料的导热系数、密度、黏度和热焓随温度变化的关系。
Procast
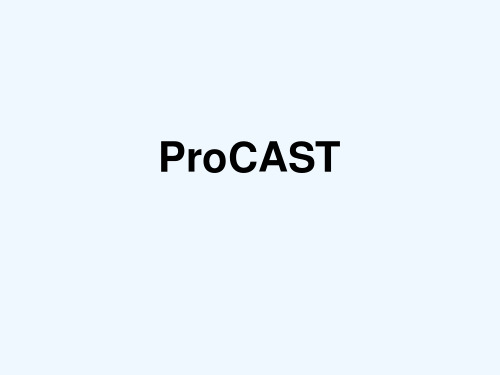
如果几何体没问题
删除细节以提高网格质量
几何体 • ProCAST • Iges • Step • Parasolid • Stl
如果有未划分网格的面
• 检查几何体 • 修复几何体 • 调整几何体 • 保存 prefix.gmrst 文件 • 划分面网格 • 检查网格 • 修复网格 • 保存 prefix.sm 文件 • 划分体网格 • 检查网格质量 • 修复网格质量 • 平滑处理 • 优化处理 • 保存 prefix.mesh 文件
辐射分析模块
本模块大大加强了基本模块中关于辐射计算的功 能。专门用于精确处理单晶铸造、熔模铸造过程 热辐射的计算。特别适用于高温合金例如铁基或 镍基合金。此模块被广泛用于涡轮叶片的生产模 拟。该模块采用最新的“灰体净辐射法”计算热辐 射自动计算视角因子、考虑阴影效应等,并提供 了能够考虑单晶铸造移动边界问题的功能。此模 块还可以用来处理连续性铸造的热辐射,工件在 热处理炉中的加热以及焊接等方面的问题。
SolStar SOLIDA 华铸CAE
英国 日本 中国
FVM DFDM FDM
—— —— 软件不限制
各种铸造 多数铸造 各种铸造
ProCAST分析模块
• • • • • • • • 有限元网格划分 MeshCAST 传热分析及前后处理 Base License 流动分析 Fluid flow 应力分析 Stress 热辐射分析 Rediation 显微组织分析 Micromodel 电磁感应分析 Electromagnetics 反向求解 Inverse
重力定义
1. 单击Process/Gravity, 弹出重力定义窗口 2.用左键单击X、 Y、Z来选择重力 大小和方向
3.单击Apply
基于PROCAST消失模铸造过程数值模拟分析的前处理

J o u na r l o f C h e n g d u T e x t i l e C o l l e g e
第 30卷 第 4期 (总第 1 1 0期 ) 2 01 3年 1 0月
文章编号: 1 0 0 8—5 5 8 0 ( 2 0 1 3 ) 0 4—0 0 6— 0 4
图 1 衬 板零 件 图
1 . 2 有 限元 网格 的划分
网格 划分是计 算机 数值模 拟不可缺少 的前处
析模块 和后处 理模块 。功 能模块包 括流 动分析模 块、 应 力分析 模 块 和辐 射 分析 模块 。高级 模 块包 括 晶粒 结构分 析模块 、 微观组 织分析 模块 、 电磁 分 析 模块 和射 芯流动分 析模块 。工具模 块包 括 网格 生 成模 块 、 反 向求解模 块 。P R O C A s T铸 造 充型 过 程模 拟流程 如 图 2所 示 。 本 文 以矿 山设 备 上 的 耐磨 件板 锤 为 例 , 详 细
9
模样 占据 型腔 , 消 失 模 的 充 型过 程 实 际 上是 高温 金 属液 体取代 泡沫 模样 的过 程 。而这 一过程 中极 为重要 的几个 参数 有 : 真空度、 泡 沫模样 与金 属液
体 之 间的换热 系数 、 气 隙的大 小 、 泡沫模 样 的气化
率。
5 ; 气化 率 为 G A S F R A C, 默认 为 0 . 1 。其 中 , 单 位
消失 模铸 造是一 种新型 的铸造方 式 。我国是 铸 造大 国 , 许 多生产厂 家尤其是 冶金 、 矿山、 煤炭 、 建材等行业, 采 用 消 失模 铸 造 群 铸 生 产 磨球 、 衬 板、 锤 头等 耐 磨件 , 在一 个 砂箱 内串 、 并联 很 多相 同或不 同 的消 失模 模 型 而进 行 一次 浇 注 成形 , 其 生 产效 率和经 济效益 比传统砂 型铸造 高 。 近 年来 , 随着计 算 机技 术 和有 限元 技术 的飞 速 发展 , 基 于知 识 的成 形 铸造 工 艺模 拟 仿 真发 展 越来 越 成熟 。模 拟 仿 真 可保 证零 部 件 的 品质 、 优 化 过程设 计 、 缩 短研制 周期 , 从而给铸 造工业 带来 效 益 。柳 百成 指 出采 用铸造过 程计算 机模 拟仿真
Procast熔模铸造模拟分析案例.
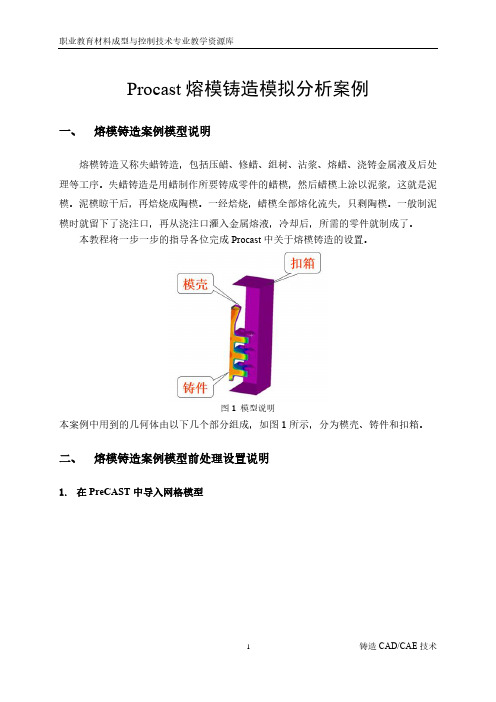
Procast熔模铸造模拟分析案例一、熔模铸造案例模型说明熔模铸造又称失蜡铸造,包括压蜡、修蜡、组树、沾浆、熔蜡、浇铸金属液及后处理等工序。
失蜡铸造是用蜡制作所要铸成零件的蜡模,然后蜡模上涂以泥浆,这就是泥模。
泥模晾干后,再焙烧成陶模。
一经焙烧,蜡模全部熔化流失,只剩陶模。
一般制泥模时就留下了浇注口,再从浇注口灌入金属熔液,冷却后,所需的零件就制成了。
本教程将一步一步的指导各位完成Procast中关于熔模铸造的设置。
图1 模型说明本案例中用到的几何体由以下几个部分组成,如图1所示,分为模壳、铸件和扣箱。
二、熔模铸造案例模型前处理设置说明1.在PreCAST中导入网格模型图2 网格导入说明如图2所示,在网格导入界面,选择网格所在的文件夹,然后在case中输入需要导入的计算模型名称,软件会自动根据路径和文件名称导入相应的几何网格信息。
读入后程序会自动显示模型、网格、节点信息。
(材料数,总的节点和单元数以及单位和轮廓尺寸),见图3所示。
注意,在辐射计算时存在一个扣箱。
图3 几何网格导入信息显示2.检查几何体网格导入后,PreCAST能够自动标示材料序号,总的结点和单元数。
也可以显示出单位和轮廓尺寸。
这些信息及各部件的体积都可以通过File menu->Check geometry 选项得到。
图4几何检查选项3.设置工件材料属性点选图5红色显示区域,再次点选相应材料牌号,点击assign最终设定,为铸件和模壳分别指定为铬镍铁合金718及一种壳材料。
图5材料定义4.创建并设置各部件之间界面换热面该步骤主要是对模型各个材料交接面设定界面换算系数,以确保材料各部分的准确换热。
图6换热界面及系数定义5.设置工艺边界条件该界面是定义铸造工艺边界条件,以实现不同的铸造工艺种类。
在熔模铸造中,需要通过该界面设置注入孔处的温度和浇注速度边界条件以及整个外扣箱的温度和辐射参数边界条件,具体见图7所示。
图7 边界条件定义6.设置重力该步骤是根据实际工艺重力方向来定义,见图8所示。
铸件缺陷形成的PROCAST数值模拟
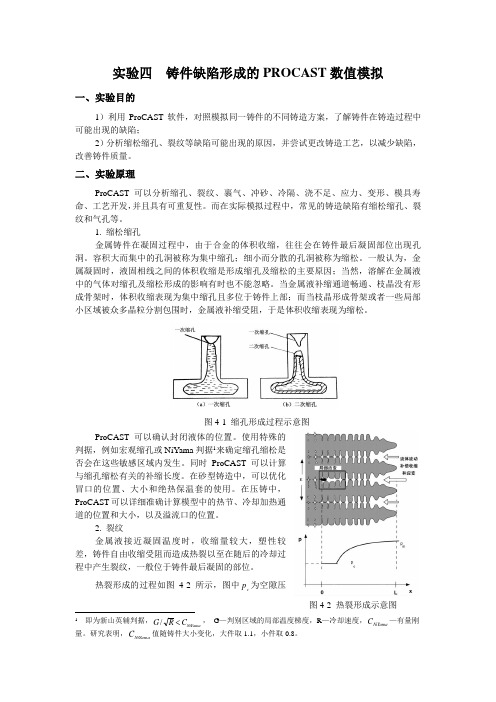
实验四 铸件缺陷形成的PROCAST 数值模拟一、实验目的1)利用ProCAST 软件,对照模拟同一铸件的不同铸造方案,了解铸件在铸造过程中可能出现的缺陷;2)分析缩松缩孔、裂纹等缺陷可能出现的原因,并尝试更改铸造工艺,以减少缺陷,改善铸件质量。
二、实验原理ProCAST 可以分析缩孔、裂纹、裹气、冲砂、冷隔、浇不足、应力、变形、模具寿命、工艺开发,并且具有可重复性。
而在实际模拟过程中,常见的铸造缺陷有缩松缩孔、裂纹和气孔等。
1. 缩松缩孔金属铸件在凝固过程中,由于合金的体积收缩,往往会在铸件最后凝固部位出现孔洞。
容积大而集中的孔洞被称为集中缩孔;细小而分散的孔洞被称为缩松。
一般认为,金属凝固时,液固相线之间的体积收缩是形成缩孔及缩松的主要原因;当然,溶解在金属液中的气体对缩孔及缩松形成的影响有时也不能忽略。
当金属液补缩通道畅通、枝晶没有形成骨架时,体积收缩表现为集中缩孔且多位于铸件上部;而当枝晶形成骨架或者一些局部小区域被众多晶粒分割包围时,金属液补缩受阻,于是体积收缩表现为缩松。
图4-1 缩孔形成过程示意图ProCAST 可以确认封闭液体的位置。
使用特殊的判据,例如宏观缩孔或NiYama 判据1来确定缩孔缩松是否会在这些敏感区域内发生。
同时ProCAST 可以计算与缩孔缩松有关的补缩长度。
在砂型铸造中,可以优化冒口的位置、大小和绝热保温套的使用。
在压铸中,ProCAST 可以详细准确计算模型中的热节、冷却加热通道的位置和大小,以及溢流口的位置。
2. 裂纹金属液接近凝固温度时,收缩量较大,塑性较差,铸件自由收缩受阻而造成热裂以至在随后的冷却过程中产生裂纹,一般位于铸件最后凝固的部位。
热裂形成的过程如图4-2所示,图中c p 为空隙压1即为新山英辅判据,NiYam a C R G /, G —判别区域的局部温度梯度,R —冷却速度,NiYama C —有量刚量。
研究表明,NiYama C 值随铸件大小变化,大件取1.1,小件取0.8。
ProCAST模拟分析
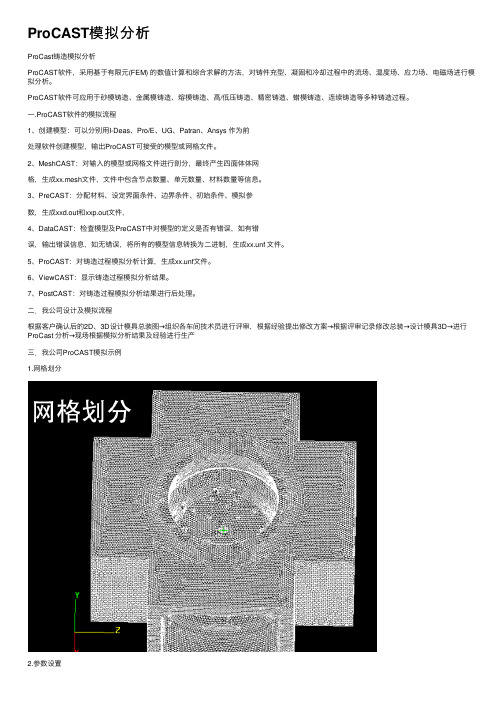
ProCAST模拟分析ProCast铸造模拟分析ProCAST软件,采⽤基于有限元(FEM) 的数值计算和综合求解的⽅法,对铸件充型、凝固和冷却过程中的流场、温度场、应⼒场、电磁场进⾏模拟分析。
ProCAST软件可应⽤于砂模铸造、⾦属模铸造、熔模铸造、⾼/低压铸造、精密铸造、蜡模铸造、连续铸造等多种铸造过程。
⼀.ProCAST软件的模拟流程1、创建模型:可以分别⽤I-Deas、Pro/E、UG、Patran、Ansys 作为前处理软件创建模型,输出ProCAST可接受的模型或⽹格⽂件。
2、MeshCAST:对输⼊的模型或⽹格⽂件进⾏剖分,最终产⽣四⾯体体⽹格,⽣成xx.mesh⽂件,⽂件中包含节点数量、单元数量、材料数量等信息。
3、PreCAST:分配材料、设定界⾯条件、边界条件、初始条件、模拟参数,⽣成xxd.out和xxp.out⽂件,4、DataCAST:检查模型及PreCAST中对模型的定义是否有错误,如有错误,输出错误信息,如⽆错误,将所有的模型信息转换为⼆进制,⽣成xx.unf ⽂件。
5、ProCAST:对铸造过程模拟分析计算,⽣成xx.unf⽂件。
6、ViewCAST:显⽰铸造过程模拟分析结果。
7、PostCAST:对铸造过程模拟分析结果进⾏后处理。
⼆.我公司设计及模拟流程根据客户确认后的2D、3D设计模具总装图→组织各车间技术员进⾏评审,根据经验提出修改⽅案→根据评审记录修改总装→设计模具3D→进⾏ProCast 分析→现场根据模拟分析结果及经验进⾏⽣产三.我公司ProCAST模拟⽰例1.⽹格划分2.参数设置3.后处理流场动态显⽰温度场动态显⽰最后凝固及补缩不⾜部位铸造缺陷位置有效应⼒热裂指⽰4.结论:根据模拟结果显⽰,铸造过程中按照顺序凝固原理,其铸造缺陷在可接受范围内。
在⽣产实际中可根据实际情况对⼯艺参数经⾏调整,来保证车轮铸造质量。
PROCAST-换热器壳体的虚拟熔模铸造

从虚拟到真实——换热器壳体的虚拟熔模铸造计算机技术特别是图形、图象处理技术的快速发展,使现实世界中的许多过程、现象和形象都能在计算机中再现出来,这就是所谓‘虚拟’。
例如,虚拟驾驶、虚拟人物,三维动画和游戏、甚至虚拟的节目主持人等等。
计算机数值模拟和可视化技术的发展,使虚拟铸造变成现实。
当然,这是建立在科学基础上的(以经典传热学、流体力学和弹塑性力学为理论基础)的虚拟,而不是基于艺术创作的虚拟。
从世界范围看铸造过程数值模拟技术的发展大体经历了三个发展阶段:①20世纪60年代是尝试阶段,开始开展以导热偏微分方程为基础的铸件凝固温度场数值模拟。
②20世纪70年代和80年代前期是以温度场数值模拟为主要内容的基础研究(材料热物理性能参数、界面条件、潜热处理等)及缩孔、缩松等缺陷判据与质量预测预报,同时开展对流场、应力场的研究。
1978年美国精铸年会上J.Hockin (Electronicast Inc.)发表的“Factors Affecting The Solidification 0f Inv estment casting”、和Arizona大学G.H.Geiger教授的“Fundamentals of Solidification”长达100页的长篇论文“The Thermal Conductivity of Shell Investment Materials ”,为建立熔模铸造充型-凝固过程数值模拟数据库奠定了坚实的基础。
③20世纪80年代后期和90年代是实用化和研究工作进一步深化的阶段。
事实上,美国UES公司开发的ProCAST铸造过程仿真软件早在1988年就开发成功。
90年代中期,美、德、法、英、日等国一大批功能强大、性能完备的商品软件已投放市场,对铸造新产品的研制、开发和生产发挥出越来越大的作用。
在众多铸造过程模拟软件中,已有许多可用于熔模铸造,ProCAST就是其中的代表。
它最初是以工程工作站/Unix为开发平台,现在也有微机/Windows版本。
procast指导书_实验五实验六

43铸造过程数值模拟综合实验前言一、铸造过程数值模拟的来源、内容和意义为了生产出合格的铸件,就要对影响其形成的因素进行有效的控制。
铸件的形成主要经历了充型和凝固两个阶段,宏观上主要涉及到液态金属充型流动、金属凝固和冷却收缩、高温金属冷却和收缩3种物理现象。
在充型过程中,流场、温度场和浓度场同时变化,凝固时伴随着温度场的变化的同时存在着枝晶间对流和收缩现象;收缩则导致应力场的变化。
与流动相关的主要缺陷有:浇不足、冷隔、气孔、夹渣;充型中形成的温度场分布直接关系到后续的凝固冷却过程;充型中形成的浓度场分布与后续的冷却凝固形成的偏析和组织不均匀有关。
凝固过程的温度场变化及收缩是导致缩孔缩松的主要原因,枝晶间对流和枝晶收缩是微观缩松的直接原因,热裂冷裂的形成归因于应力场的变化。
可见,客观地反映不同阶段的场的变化,并加以有效的控制,是获得合格铸件的充要条件。
传统的铸件生产因其不同于冷加工的特殊性,只能对铸件的形成过程进行粗糙的基于经验和一般理论基础上的控制,形成的控制系统——铸造工艺的局限性表现在:1)只是定性分析;2)要反复试制才能确定工艺。
铸造过程数值模拟的目的就是要对铸件形成过程各个阶段的场的变化进行数值解析以获得合理的铸件形成的控制参数,其内容主要包括温度场、流场、浓度场、应力场等的计算模拟。
二、铸造过程数值模拟原理铸造过程数值模拟技术的实质是对铸件成型系统(包括铸件—型芯—铸型等)进行几何上的有限离散,在物理模型的支持下,通过数值计算来分析铸造过程有关物理场的变化特点,并结合铸造缺陷的形成判据来预测铸件质量。
数值解法的一般步骤是:1)汇集给定问题的单值性条件,即研究对象的几何条件、物理条件、初始条件和边界条件等。
2)将物理过程所涉及的区域在空间上和时间上进行离散化处理。
3)建立内部节点(或单元)和边界节点(或单元)的数值方程。
4)选用适当的计算方法求解线性代数方程组。
5)编程计算。
其中,核心部分是数值方程的建立。
- 1、下载文档前请自行甄别文档内容的完整性,平台不提供额外的编辑、内容补充、找答案等附加服务。
- 2、"仅部分预览"的文档,不可在线预览部分如存在完整性等问题,可反馈申请退款(可完整预览的文档不适用该条件!)。
- 3、如文档侵犯您的权益,请联系客服反馈,我们会尽快为您处理(人工客服工作时间:9:00-18:30)。
熔模铸造过程数值模拟—国外精铸技术进展述评北京航空航天大学陈冰20世纪90年代以来,国外一大批商业化铸造过程数值模拟软件的出现,标志着此项技术已完全成熟并进入实用化阶段,有相当一部分已成功地用于熔模铸造。
其中,A FSolid (3D)(美国), PASSAGF/POWERCAST(美国)、MAGMA(德国)、PAM-CAST(法国)、ProCAST(美国)等最具代表性。
尤其值得一提的是由美国UES公司开发的ProCAST,和美国铸造师协会(American Foundrymen's Society)开发的 AFSolid(3D),它们代表了二种不同类型的软件系统。
一. 熔模精密铸造过程数值模拟的佼佼者——ProCAST早在1985年,美国UES Software Co.便以工程工作站/Unix为开发平台,着手开发ProCAST[1]。
为了保证模拟结果的准确性,ProCAST一开始就采用有限元方法(FEM)作为模拟的核心技术。
自1987年起,开发用于熔模铸造(精铸)的专业模块。
1990年后,位于瑞士洛桑的Calcom SA和瑞士联邦科技研究院也参加ProCAST部分模块的开发工作。
2002年,UES Software和Calcom SA先后加盟ESI 集团(法国)。
通过联合,ESI集团在虚拟制造领域的领先地位进一步增强。
现在,ProCAST也有微机/Windows或Windows NT版本。
三维几何造型模块支持IGES、STEP、STL 或Parasolids等标准的CAD文件格式。
Meshcast模块能自动生成有限元网格。
它的凝固分析模块可以准确计算和显示合金液在凝固过程的温度场、凝固时间,以及固相率变化,同时,从孤立液相区、缩孔/缩松体积分数、缩孔/缩松Nyiama (新山英辅)判据等三方面,帮助铸造工程师分析判断缩孔/缩松产生的可能性和具体位置(见图1) [2]。
针对熔模铸造热壳浇注的特点,ProCAST传热分析模块考虑到热辐射对温度场和铸件凝固过程的影响, 这对于经常需要处理热辐射问题的熔模铸造而言特别重要。
例如,对不锈钢人体植入物的凝固过程进行模拟时,发现位于模组中部的铸件由于接收到的辐射热比周边铸件多,因而温度偏高,不利于铸件顺序凝固,容易产生缩孔、缩松[1]。
特别值得一提的是,ProCAST特有的辐射分析模块,计及辐射线入射角和遮挡物的影响,模拟对象一旦因相互运动导致辐射线入射角改变或产生遮挡, 该软件将重新自动进行计算,特别适用于定向凝固和单晶铸造。
a) 孤立液相区b) 缩孔/缩松体积分数c) Nyiama (新山英辅)判据图1 ProCAST缩孔/缩松判据图2 热辐射对模组温度场的影响图3 流场与温度场耦合计算自1992年起,ProCAST的流动分析模块便能通过Navier-Stocks流动方程进行流场计算,同时与传热过程耦合(图3) [2]。
不仅模拟金属液的充型过程和状态,同时还将温度场变化显示出来,预测冷隔和浇不到等铸造缺陷(图4) [2]。
此外,它还可以模拟流体通过多孔介质(例如陶瓷过滤器)的流动状态,预测放置过滤器后可能出现的倒流、噎流等现象(图5)。
此外,流动分析模块中,可以对诸如精铸模料在内的非牛顿流体的充型行为进行模拟,是该软件的又一特色(图6) [1]。
图4 浇不足缺陷预测 图5 由于过滤器使用不当造成噎流图6空心叶片蜡模充型过程模拟结果(左) 与实验结果(右)比较图7 铝-镁合金晶间疏松模拟结果(右) 与实验结果(左)比较图8 整铸涡轮残留应力模拟(左)和裂纹预测(右)1994年美国国家航空航天总局(NASA)在调查评估的基础上推荐该软件为美国航空航天领域铸造过程CAE的首选软件。
其后,包括美国Howmet、Pratt & Whitney、PPC、GEAE以及英国Rolls-Royce 等世界著名的航空航天精铸企业纷纷选择ProCAST作为铸造工艺分析和新产品开发的重要工具。
图8所示为ProCAST新近发布的对整铸涡轮残留应力模拟和裂纹预测结果[3]。
ProCAST 2004公布的对铝-镁合金晶间疏松(图7) [4]、整铸涡轮铸造晶粒结构模拟(图9)[3],和空心单晶叶片晶体生长过程的模拟结果(图10)[3],标志着该软件已经将铸造晶粒组织和微观结构模拟提升到一个新水平。
图9 整铸涡轮铸造晶粒结构模拟 图10 单晶铸造空心叶片单晶生长过程模拟二.充型-凝固过程模拟和浇道优化设计一步完成[5]AFSolid开发始于1985年,它最初是以微机/DOS 为平台的一套二维系统,1993年后升级为三维。
三维几何造型模块支持AutoCAD以及IGES、STL和DXF等几何图形文件格式。
计算方法采用有限差分法,流动和传热计算进行了适当的简化处理,可以说是一种简化版的模拟软件,适用于包括砂型、熔模、金属型、压力铸造等在内的多种铸造方法。
其功能虽不能和ProCAST等高档软件相提并论,但价格便宜,目前在全球40多个国家拥有410多家用户,其销售量号称世界之最,用户大多为生产商业铸件的中小型精铸厂。
近来,美国Finite Solutions Co.与美国铸造师协会合作,将多变量优化运算软件链接到AFSolid凝固模拟软件中,使凝固过程模拟与工艺优化一步完成,使计算机模拟的效率大为提高。
众所周知,仅仅通过一模拟,其结果往往很难令人满意,所以工程技术人员就必须根据自身的经验和知识对首次模拟结果进行分析,修改工艺方案和设计,再进行下一次模拟,经过反复多次模拟和修改,最终才能获得满意的工艺方案或参数。
可见,这种方法其实是用计算机试错法来代替生产现场的试错法。
当然效率明显提高,也降低了成本。
但是,计算机反复试错,也需要耗费较多的机时。
针对这一问题,美国Finite Solutions Co. 提出将多变量优化运算软件链接到AFSolid凝固模拟软件中,进行二次开发,使模拟与优化一步完成,从而使计算机模拟的效率大为提高。
目前已经有不少现成的商业软件可用来进行工程问题的优化运算。
Finite Solutions Co.从中选择了当前流行于汽车零部件和结构设计的HyperOpt (开发商:Altair Engineering Inc.)。
优化运算通常要求有三个前提: 即设计变量、约束条件和目标函数。
设计变量是指具体的设计特征,可以是几何特征,如冒口直径、高度,横浇道和内浇道尺寸等,也可以是工艺参数,如浇注温度、型壳焙烧温度等。
设定设计变量时需要给出最大、最小和正常值。
约束条件是指工艺条件的上限和下限。
约束可被指定为一个最小值(所得的最终结果数值应等于或大于给定的约束值)或最大值(所得的最终结果数值应等于或小于给定的约束值)。
每一次优化运算,可以指定一个或多个约束,例如约束可以是允许存在的最大的疏松级别或可以接受的最低的工艺出品率等。
目标函数是指预期目标。
用户只能选择一个目标函数并指定该函数的最佳值(最大或最小值)。
例如如果以缩孔缩松程度为目标函数,此时最小值为最佳;如果选择工艺出品率作为目标函数,当然最大值最佳。
值得强调指出的是,每一次优化运算,只能指定一个目标函数。
模拟-优化运算步骤下:首先建立一个初始的工艺设计,包括浇注补缩系统和铸件的三维几何模型和所有相关材料的数据;然后选择设计变量、约束和目标函数;再启动软件自动进行模拟-优化运算,计算机运行过程中不断按原先设定,自动更改设计变量,检查是否违反了约束条件,搜索并确定目标函数最佳值。
从缩短模拟计算时间的角度考虑,计算方法采用有限差分比有限元法更为有利。
而AFSolid的计算方法正是采用有限差分法,所以运算速度快。
例如对一个需要上百万甚至更多单元才能准确表达清楚的复杂铸件,在目前新型的个人电脑上进行一次模拟计算,运行时间还不到30min。
需要进行16次连续模拟的优化运算也只要一天就轻松地完成了。
而采用某些其它软件进行类似的工作往往需要几周时间。
应用实例——不锈钢精铸接头重13.2磅。
图11a所示为原始铸造方案。
由图11b所示凝固时间模拟结果可见,其顶部红色部位正处在横浇道下方,受横浇道高温区热辐射影响冷却慢,得不到有效地补缩,容易产生缩松。
图11 不锈钢精铸接头原始铸造方案及模拟结果a)铸造方案 b) 凝固时间模拟结果更改设计变量包括内浇道尺寸(只改动水平方向尺寸,图12上)和横浇道尺寸(水平和垂直方向尺寸同时改动,图12下),总共更改3个设计变量;以铸件材质密度最小值为健全铸件的99.8%作为约束条件(即疏松度最大值为0.2%);以工艺出品率最大为目标函数。
然后进行包含15次模拟(含充型分析)的模拟-优化运算。
在Pentium III-1GHz微机上运行只需1小时零7分钟。
每完成一次模拟,系统都会自动更改浇道尺寸,同时,进行网格剖分,建立新的型壳几何模型,应用热辐射观察因子计算型壳温度场。
采用经模拟-优化的工艺设计后(图13上),缩孔已从铸件中被排除到浇道中(图13下),缩松减少50%以上。
对比图11a和图13上,内浇道减小为原先的85%,而横浇道水平和垂直尺寸分别减小到为原先的53%和86%,浇注系统总重量减少了6.75kg,工艺出品率由30%增加到46%。
按每年生产铸件2500件计,每年节省金属材料费用37500美元,省电16500 kW·h。
三.当前推广应用计算机仿真技术存在的问题1.数据库数据匮乏数据库数据匮乏是当前熔模铸造过程仿真技术普遍存在的问题。
某些材料(例如特殊合金材料和某些型壳材料)的热物理性能数据,尤其是界面传热系数,很难寻觅。
国内情况就更为严重,各种合金和型壳材料的热物理性能数据几乎全部来自国外文献资料。
真正按照国内材料和工艺,由实验方法测出的数据可以说是一片空白,这不能不说是一个很大的缺憾。
对比国外,早在1978年,美国精铸年会上发表的题为“Factors Affecting The Solidification of Investment casting”、“Fundamentals of Solidification”和 Arizona大学长达100页的长篇论文“The Thermal Conductivity of Shell Investment Materials ”,为建立熔模铸造过程仿真所需的基础数据库奠定了坚实的基础。
而ProCAST 除内含基本的材料性能数据库外,还拥有独特的合金热力学数据库。
它以新兴的计算材料学为基础,由英国的ThermoTech公司开发。
利用这个独特的数据库,用户只需输入合金化学成分,计算机便可自动求算出液、固相线温度、凝固潜热、比热容和合金密度随温度的变化等热物理参数。
图12 更改设计变量(上——更改内浇道尺寸,下——更改横浇道尺寸)图13 更改后的工艺设计(上)和模拟结果(下)2.图形数据文件标准化和相互交流CAD数据文件的转换和标准化也是一个十分重要的问题。