炼钢车间T转炉三次除尘技术办法
莱钢120t转炉干法除尘系统优化改造实践

5 煤气 回收率较低。电场不稳定 , ) 煤气含尘量
波动 、 气 冷 却 系统 降 温 能力 不够 、 统泄 爆 安全 煤 系 隐患较大 等导致煤 气不能安 全 回收。
2 除尘系统优 化改造
图 1 干 法 除 尘 系 统 工 艺 流 程
干法 除尘 系统 主要 由蒸 发 冷却 器 、 筒 电除尘 圆
技术 、 备件 国产化技术等 对系统进行优化 改造 , 大大 提高 了系统运 行安全 , 设备故 障率为零 , 煤气含尘量 稳定在 8 以 m 下, 降低生产成本 4 rt Y , _ 年直接经济效益达 1 0 万元 。  ̄ 0 7 关键词 : 转炉干法除尘系统 ; 优化改造 ; 静电除尘器 ; 泄爆 中图分类号 : 7 7 X 5 文献标识码 : B 文章 编号 : 0 - 6 0 2 0 )6 0 2 — 2 1 4 4 2 (0 80 — 0 5 0 0
11 。静电除尘器泄爆频 繁造成 电场 阴极线断 0次 线、 阳极 板 变 形 和 内部件 损 坏 , 响 电场 运行 稳 定 影
并造 成烟 气 ( 煤气 ) 尘量 波动 (0~ 0 / , 含 1 30mg )严 m
收稿 日期 :0 8 0 — 0 修 回日期 :0 8 1- 6 20 - 6 1 ; 2 0 — 1 2
经过 分 析 发现 , 生 泄爆 现 象 的 主要 原 因 为 : 产 1开 吹 2mi ) n内碳 氧 反应 剧烈 , 力波 动大 ;) 压 2 吹氧 操作 不 规 范 , 气 压力 波 动 大 , 成过 量 氧气 进 入 氧 造 静 电 除尘 器 , 到爆 炸 条 件 ;) 吹泄 爆 的原 因是 达 3点 终 点碳控 制过高 , 造成拉碳 时碳 氧反应 剧烈 。 鉴 于这些 情 况 , 通过 多次 对冶炼 情况 的统 计 与 分析 , 建立 了转 炉开 吹氧压 表 , 总管压 力 、 座转 为 每 炉 的开 吹氧 压 、 门开度 等参数 建立 了曲线对 应关 阀 系, 总结 出 了 自动 开 吹 氧压 控制 模 型 , 现 了 在各 实
轧钢工程废气的净化

轧钢工程废气的净化轧钢工程废气的净化轧钢产品多种多样,伴随不同处理工艺会产生造成环境污染的有害废气,这些废气既对人体健康造成伤害,又对设备和产品质量造成不良影响。
下而整理了关于轧钢工程废气净化的文章,欢迎大家阅读!轧钢工程废气净化技术应用随着国家对大气污染物排放标准和环境卫生标准的提高,公众环境保护意识及对能源消耗问题认识的增强,以及轧钢工艺变化和设备运转速度的提高,如何解决轧钢环境污染问题日益被更多人所关注。
钢铁企业在轧钢废气治理方而增加了投资,没有废气净化系统的加设净化系统,停滞废弃的废气净化系统重新改造。
这一切给环保工作带来了商机,同时也提出了更高的要求。
这就使得废气净化系统设计不但要满足环保要求,而且要根据各个工程的不同特点和客户的需要,在节约投资、节省能耗、系统安全可靠三方面综合平衡,找出最佳方案。
♦专有烟气捕集罩废气净化系统中捕集罩是废气净化的核心设备,事关重要。
由于轧机周围情况复杂,设计烟气捕集罩困难较大。
设计好烟气捕集罩的指导思想就是既要最大限度地满足收集烟气作用,不使废气从烟罩中溢出,又要方便轧钢工艺操作,并且为了节省投资,罩子要尽量小。
在总承包宁波钢铁有限公司1780mm热轧带钢精轧机除尘系统工程的设计过程中,中冶京诚的技术专家以一切为了用户满意为行动指南,与轧机操作人员就正常操作流程、操作习惯、运行故障监测、设备检修要求等问题进行反复探讨,并到现场实地测量,设置了便于机组人员观察机组运行情况和迅速排除小故障的快捷门,减少了停车时间,提高了生产效率。
此排烟罩获得2项国家实用新型专利证书。
该工程于2007年投产,极大地改善了车间内工作环境,系统运行正常,效果良好。
♦匹配不同净化设备设计各类废气净化系统具体包括板带热连轧机、连轧管轧机、冷连轧机、平整机和焊机烟气的净化系统,连续酸洗线、连退和镀锌机组清洗段、彩涂室的废气净化,以及拉矫破鳞机的除尘系统等。
这些生产线产生含有油雾、尘、酸气、碱气、有机溶剂挥发物等各类不同成份的废气。
300t转炉干法除尘设备维护实践

法 ) 首 钢京 唐公 司 3 0t 炉 干法 除 尘 技 术 从 西 门 , 0 转
子一 奥钢联 ( I ME AI 引 进 , 0 9年 5月 正 SE NS V ) 20 式 投产 使用 。3 0 t 炉 干 法 除 尘 系 统 的 工 艺 流 程 0 转
如 图 1所示 , 要辅 助设 备如 下 。 主 () 1 蒸发 冷却 器 ( C系统 ) 通过 喷 射 雾化 的水 E :
H a e nW i
( tema ig De at n ,Jn tn rn a d Se lUno mp n mi d,Ca i l r na d Se lC mp — S e l kn p rme t iga g Io n te in Co a y Li t e pt o n te o a aI
随着 氧气 转 炉炼 钢 生产 的发 展及炼 钢 工艺 的 日 趋完 善 , 相应 的 除尘 技 术 也 在 不 断 发展 和完 善 。 目 前, 氧气 转炉 炼钢 的净 化 回收 主要 有两 种方 法 , 即煤
气湿 法 ( G 法 ) 化 回收 系 统 和 煤 气 干 法 ( T法 ) O 净 L 净化 回收 系统 。 因 L T法 除尘 净 化 效 率 高 , 过 电 通
tm s g a al e l c y yse . I s a le n g sc e nng r c v r yse f r3 0 tc nv re .To e i r du ly r p a edby dr s tm ti ppi d i a l a i e o e y s tm o 0 o e tr t r b e si h q pm e so h ss se ,m e s r s ae m a e ou o r d c h r a do he p o l m n t e e ui nt fti y t m a u e r d tt e u e t e b e k wn,p r p r a tofs a e
新钢三炼钢转炉除尘系统的优化改造

L i —sa A i 1 a X o ho l a J n—w i Q in —m n Z A G N n —fn e lL g ig H N i a g eg
( o e p . P w rDet ,Xiy rna d SelC ,Ld. nu I n te o. t o Xn u,Ja g i3 8 0 ) iy in x 3 0 1
A b t a t Th la ig r s l r o a i a tr o te ce nn y t m o o v re n N 3 Se l l n f n u Io n te . Ld. src e ce n n e u t a c n ts t fc oy t h la i g sse fc n e tri o. te a t y r n a d S e l s s P o Xi Co , t a d te d s c n e tai n o i h r ig fu a s hg , whc o lts t h n i n n . A c r i g t h s ee t , n n — c m b sin n h u t o c nr t fds a gn e g s i i h o c l ih p l e o te e v r me t c od n o te e d fc s o u o o ut o m t o s a o t o c n u t p i z t n r n v t n a d g o c n mi a d e v rn n a s l a e b e ba n d. e h d i d pe t o d c tmi i e o ai n o d e o o c n n i me tlr ut h v e n o ti e d o ao o o e s Ke wo d ce i g s se o o v re o tmi t n r n v t n d s ra m n y rs la n y tm c n e tr n f pi z i e o ai u tt t a o o e e t
转炉煤气干法净化回收技术

转炉煤气干法(LT)净化回收技术的国产化应用我国现有600多座转炉,年产钢超过4亿吨,节能减排潜力巨大。
目前我国绝大多数转炉的转炉煤气净化采用较为落后的湿法(以下简称老OG)除尘,耗水耗电量大,是钢铁工业节能减排的薄弱环节。
除了老OG除尘之外,近年来我国新建转炉采用了第四代湿法(以下简称新OG法),以及引进的千法(以下简称LT法):使转炉煤气净化技术取得了突破性进展。
在转炉煤气净化技术引进的同时,国内多家设计研究单位进行了吸收开发,目前转炉煤气净化的LT法、新OG法除引进少量关键技术和部件,大量的设备设计、系统设计立足于国内,甚至新OG法基本实现全国产化。
对我国转炉炼钢节能减排、实现负能炼钢起到了积极的推动作用。
但是我们仍清醒看到,转炉煤气净化发展到今天,这些技术包括引进技术都不同程度的存在一些问题、或有值得改之处,这是我国钢铁工业节能减排要追求和持续研究的新目标和新课题。
正是由于目前各种除尘方式的利弊所在,使新建转炉除尘设计选择LT法还是新OG法似乎难以确定。
本文就两种除尘方式进行比较,提出自己的建议。
1.国内外转炉烟气除尘技术的发展和现状当前,转炉烟气净化及煤气回收技术主要有两大类型:即日本的湿法系统(OG法)和德国的干法系统(LT法)。
1.1 湿法系统图1 OG法工艺流程OG法是以双级文氏管为主,抑制空气从转炉炉口流入,使转炉煤气保持不燃烧状态,经过冷却而回收的方法,因此也叫未燃法,又称湿法。
在湿法方面,日本从60年代起开发了OG法,这是世界上普遍采用的流程。
1962年,日本新日铁公司的转炉首次成功地应用该法对转炉烟气进行除尘并回收,合理地利用废气中的化学能和显能及含铁粉尘。
目前己成为世界上最广泛采用的转炉烟气处理方法,在保护环境、回收能源方面发挥了积极作用。
OG法装置主要由烟气冷却系统、烟气净化系统及附属设备组成(见图1)。
在冶炼中生成高一氧化碳浓度且含150~200mg/m3粉尘的煤气,温度达1600℃。
转炉半干法一次除尘工艺操作规程
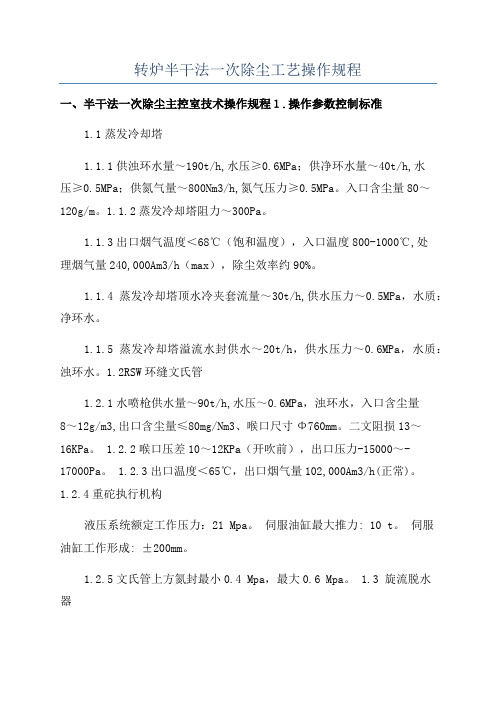
转炉半干法一次除尘工艺操作规程一、半干法一次除尘主控室技术操作规程1.操作参数控制标准1.1蒸发冷却塔1.1.1供浊环水量~190t/h,水压≥0.6MPa;供净环水量~40t/h,水压≥0.5MPa;供氮气量~800Nm3/h,氮气压力≥0.5MPa。
入口含尘量80~120g/m。
1.1.2蒸发冷却塔阻力~300Pa。
1.1.3出口烟气温度<68℃(饱和温度),入口温度800-1000℃,处理烟气量240,000Am3/h(max),除尘效率约90%。
1.1.4蒸发冷却塔顶水冷夹套流量~30t/h,供水压力~0.5MPa,水质:净环水。
1.1.5蒸发冷却塔溢流水封供水~20t/h,供水压力~0.6MPa,水质:浊环水。
1.2RSW环缝文氏管1.2.1水喷枪供水量~90t/h,水压~0.6MPa,浊环水,入口含尘量8~12g/m3,出口含尘量≤80mg/Nm3、喉口尺寸Φ760mm。
二文阻损13~16KPa。
1.2.2喉口压差10~12KPa(开吹前),出口压力-15000~-17000Pa。
1.2.3出口温度<65℃,出口烟气量102,000Am3/h(正常)。
1.2.4重砣执行机构液压系统额定工作压力:21 Mpa。
伺服油缸最大推力: 10 t。
伺服油缸工作形成: ±200mm。
1.2.5文氏管上方氮封最小0.4 Mpa,最大0.6 Mpa。
1.3 旋流脱水器1.3.1处理烟气量:102,000Am3/h(正常)1.3.2脱水方式:旋流脱水1.3.3脱水效率(机械水):>99%1.3.4出口烟气温度:不超过55℃1.3.5系统阻力:0.6KPa2.联锁条件2.1回收联锁2.1.1回收条件满足条件自动转回收,条件不满足自动转放散。
2.1.2三通阀转放散<15秒不到位,旁通阀开,水封逆止阀自动关闭。
2.1.3转回收水封逆止阀动作>15秒不到位,三同阀不动作。
2.1.4转回收三通阀>15秒不到位,旁通阀开,三通阀关,水封逆止关。
干法除尘的工艺流程及工作原理(精)

干法除尘的工艺流程及工作原理干法除尘的工艺流程及工作原理一、干法除尘的工艺流程:Ⅰ高温、未净化的转炉烟气Ⅱ高温未净化的转炉烟Ⅲ高温未净化的转炉烟气Ⅳ冷却后、粗净化的转粗灰Ⅴ冷却后、粗净化的转炉烟气Ⅵ冷却后、净化的转细灰不合格的转炉煤气二、干法除尘设备工作原理:1、干法除尘的设备组成:通过对干法除尘设备的功能来看,干法除尘的设备主要分成五大块,分别为转炉烟气的冷却设备(即EC系统)、转炉烟气的净化设备(即EP系统)、转炉烟气的动力设备(即ID风机)、转炉煤气的回收和排放设备(切换站和煤气冷却器)、粉尘排放设备(即EC粗输灰系统和EP细输灰系统)。
2、转炉烟气冷却设备(EC系统)转炉冶炼时,含有大量CO的高温烟气冷却后才能满足干法除尘系统的运行条件。
蒸发冷却器入口的烟气温度为800~1200C,出口温度的控制应根据静电式除尘器的入口温度而定,一般EC的出口温度控制在200~300C,才能达到静电除尘器的要求。
为此,EC系统采用14杆喷枪进行转炉烟气的冷却,喷枪通过双流喷嘴对蒸汽和冷却水进行混合,达到冷却水的雾化效果,提高冷却水与气流的接触面积,使得转炉烟气得到良好、均匀的冷却。
喷射水与转炉烟气在运行的过程中,水滴受烟气加热被蒸发,在汽化过程中吸收烟气的热量,从而降低烟气温度。
蒸发冷却器除了冷却烟气外,还可依靠气流的减速以及进口处水滴对烟尘的润湿将粗颗粒的烟尘分离出去,达到一次除尘的目的。
灰尘聚积在蒸发冷却器底部由链式输送机排出。
蒸发冷却器还有对烟气进行调节改善的功能,即在降低气体温度的同时提高其露点,改变粉尘比电阻,有利于在静电除尘器中将粉尘分离出来。
除了烟气冷却和调节以外,占烟气中灰尘总含量约15%的粗灰也在蒸发冷却器中进行收集、排放。
另外,通过对喷射水流量的控制(水调节阀),可控制EC的出口温度,使之达到静电式除尘器所需要的温度。
3、转炉烟气净化设备(EP系统)静电除尘器为圆筒形静电除尘器,它是转炉烟气干法除尘系统中的关键除尘设备,其主要技术特点为:①优异的极配形式。
除尘灰利用价值

除尘灰利用价值除尘灰利用价值西钢开发出用除尘灰制造泡沫渣新工艺日前,该厂在生产实践中,用废弃除尘灰制造泡沫渣一举获得了成功。
该工艺既使废弃物得以充分利用,也为公司降低了生产成本。
西钢二炼钢了解到公司炼铁厂除尘灰因含铁量较低,除烧结工艺可少量配用外,大量的除尘灰处于堆积状态。
他们决定由此入手,开辟除尘灰的新用途。
经过深入分析,他们发现该除尘灰含碳量很高,达到 40% ,含铁量达 30% ,其余的为氧化钙、二氧化硅等,用于电炉氧化期冶炼造泡沫渣比较合适。
于是,他们根据分析成分进行了冶炼配比试验,试验效果良好。
该除尘灰加入渣面后,碳和氧迅速发生化学反应,生成一氧化碳气泡,并穿越渣层形成良好的泡沫渣,可有效包裹住弧光,提高电弧热效率,同传统的焦粉造泡沫渣工艺相比,泡沫渣层厚,持续时间长,可完全替代焦粉,同时降低了生产成本,为电炉降本增效工作开辟了新的途径。
利用铁厂除尘灰作原料优化配料生产水泥熟料我厂粘土中铝含量较低,校正原料炉渣也是硅高铝低,熟料铝氧率一直上不去,为1.0 左右。
生料中粘土的配比也只有 7%左右,影响了生料的成球,我们曾试图用高炉矿渣配料,但由于土少使成球质量差。
1999 年 3 月份,我们发现铁厂原料烧结电除尘灰 (简称原料除尘灰 )和高炉布袋除尘灰 (简称高炉除尘灰 )往外大量排放,经化验,原料除尘灰含有较高的铁,可作为铁质校正原料;高炉除尘灰含有较高的 Al2O3,且 SiO2含量低,满足铝质校正原料要求。
我们以这两种除尘灰分别代替镍渣和炉渣,在Φ2.2m×8.5m机立窑上进行了 3个月的试生产,取得了较好的效果。
1 除尘灰的来源及性能原料除尘灰是铁精矿粉、萤石、石灰石、白云石、焦粉按一定比例配合后入烧结炉烧结,在出炉过程中通过电除尘器所收集的粉尘,其外观呈细颗粒状, 0.08mm 方孔筛筛余为25.8%,为暗红色。
高炉除尘灰是高炉在炼铁过程中由布袋除尘器所收集的粉尘,其外观呈粉状,刚清理出来时为深灰色,待放置一二天后变为白色,我们最终所利用的是白色粉尘,0.08mm 方孔筛筛余为 13.6%。
- 1、下载文档前请自行甄别文档内容的完整性,平台不提供额外的编辑、内容补充、找答案等附加服务。
- 2、"仅部分预览"的文档,不可在线预览部分如存在完整性等问题,可反馈申请退款(可完整预览的文档不适用该条件!)。
- 3、如文档侵犯您的权益,请联系客服反馈,我们会尽快为您处理(人工客服工作时间:9:00-18:30)。
秦皇岛宏兴钢铁有限公司炼钢车间2×60T转炉三次除尘项目技术方案张家口市宣化天洁环保科技有限公司2016年5月1.序言秦皇岛宏兴钢铁有限公司技改炼钢车间三次除尘项目尘源点包括2×60t转炉两座加料跨配顶吸罩,600T混铁炉一座配顶吸罩,散装料上料系统一套配集中除尘。
我公司根据秦皇岛宏兴钢铁有限公司提供的资料,编制了本方案,其目的在于为该除尘提供成套的、优化的、建设性的解决方案,确保符合国家环保要求,达标排放的前提下降低投资及运行成本。
2.尘源点概述2.1需治理的扬尘点本方案治理的尘源点配套除尘罩范围如下:1)、2×60T转炉加料跨顶吸罩;2)、600T混铁炉兑铁口、出铁口工位除尘罩;3)、散装料地坑料仓卸料口除尘罩;4)、散装料皮带机机头、机尾除尘罩;5)、转运站皮带机头除尘罩、振动筛除尘罩;6)、通廊皮带机头、皮带机尾除尘罩;7)、高跨散装料仓皮带布料口除尘罩。
3.设计原则及依据3.1设计原则●达标排放,保证除尘效果;●不影响冶炼操作工艺;●最大限度地降低运行费用及一次投资;●利于维护管理,长期、有效、稳定地运行。
3.2设计依据●国家有关环保要求及环境指标:(获县以上环保部门的验收)排放浓度≤15mg/Nm3岗位粉尘浓度≤10mg/Nm3(扣除背景值)三次除尘捕集率≥95%(屋顶不冒黄烟),混铁炉捕捉率≥60%除尘效率≥99%。
●国家有关设计规范4.除尘工艺流程及设计说明4.1除尘工艺流程本套系统采用低阻、大流量系统工艺原则,其目的在于以最低的系统阻力,控制系统管道流速(18~20m/s),通过选取管道经济流速,尽量降低系统阻力损失从而能明显降低长期电耗。
换言之,追求的是在相同电机的情况下,最大限度地取得处理风量,提高捕集率。
在相同风量满足捕集效果的前提下,尽可能少地消耗电能,降低运行费,并合理组织烟气,使系统长期、可靠、稳定地运行在既不烧滤袋又不易于结露的中温状态。
烟气捕集是本系统的关键所在,设备其生产工艺不同、设备布置各异,因此,选用何种捕集罩型式成为本次方案的重点。
4.2除尘罩设计说明1)、2×60T转炉加料跨顶吸罩:60T转炉的烟尘基本处于持续产生过程,大量高温烟气受热膨胀和特抬升力影响从炉前二次除尘罩逃逸冲上加料跨车间顶部,由于现有车间全部密封,烟气淤积在车间顶部无法流通,必须在尘源上方利用现有厂房结构设置高悬伞形罩,捕集加料和兑铁水以及冶炼过程产生的三次烟气,被捕集的烟气通过系统管网汇合后进入低压脉冲除尘器进行过滤,最后满足排放达标的烟气通过引风机排入大气。
2)、600T混铁炉烟尘顶吸罩:600T混铁炉产生的烟气基本处于间断产生过程,主要是混铁炉兑铁水、出铁水及铁包倒罐工位产生的大量烟尘。
混铁炉是贮存从高炉运来供炼钢转炉用的铁水,当混铁炉兑铁水和混铁炉向铁水罐倒铁水时在一定温度下部分碳析成石墨粉尘,混杂着氧化铁粉末随热气流扩散到车间内,大量高温烟气受热膨胀和特抬升力影响从炉前二次除尘罩逃逸冲上加料跨车间顶部,由于现有车间全部密封,烟气淤积在车间顶部无法流通,必须在尘源上方利用现有厂房结构设置高悬伞形罩。
由于石墨粉尘非常轻,在随热气流上升的过程中就受到车间横向野风的影响飘散到车间各个角落,因此采取高悬伞形罩的形式捕捉此类粉尘的话想对转炉三次除尘顶吸罩效率较低。
建议应该在最靠近尘源点的位置设计低悬伞形罩或者尘源点侧吸罩进行有效捕捉才能明显提高集尘效果。
3)、散装料上料系统除尘罩散装料上料除尘系统主要包括地坑料仓下料除尘罩;皮带输送机头、机尾除尘罩;转运站振筛除尘罩以及转炉高位料仓皮带布料除尘罩几个部位。
此处烟气属于常温烟气必须采用封闭式除尘罩,尽量把尘源点烟气控制在最小范围内进行集中收集效果最佳。
因此需要对送料皮带加设导料槽进行封闭,振动筛需要从新加设软密封措施确保振动筛本体漏风率满足除尘要求,皮带机头部分采用半封闭顶吸罩同合理的风量设计,选取恰当的控制风速,保证皮带机头半封闭罩的烟气捕捉率。
高位料仓受现场因素影响应采取整体封闭形式,在整体封闭罩安装检修门及除尘管道接入口,每个接口管道安装电动阀门,通过布料车移动限位信号控制每个料仓位接口管道的开启和关闭。
5.除尘系统风量设计及划分5.1除尘工艺划分的原则按工艺设备在车间内就近布置的原则,优先考虑以上设备除尘系统的合建;优先考虑生产作业的周期性比较一致的设备合建为一套除尘系统;考虑将烟尘特性(成分、温度、粒径等)接近的扬尘点合建为一套除尘系统;综合均衡一套大系统和多套小系统在工艺、投资及管理上各自的优缺点,确定系统划分。
5.2除尘点风量设计(表1-1)5.3风量设计说明1)、表1-1中加料跨每个尘源点均加设电动蝶阀控制开/关(3个),其中加料跨2台转炉顶吸罩以及1台混铁炉顶吸罩同阀门切换实现加料跨始终有2个顶吸罩开启,通过岗位工作台上增设电动蝶阀开/关按钮,实现3个阀门之间开关/切换。
2)、表1-1中散装料高位料仓及散装料地坑下料口每个尘源点均加设电动蝶阀控制开/关(16+6=22个),其它尘源点均加设手动阀门(7个),用于调节系统阻力平衡。
6.除尘设计方案6.1方案一分析除尘总设计风量780000m3/h,系统风压6500Pa,加料跨尘源点和散装料尘源点共用一台除尘器,此方案投资费用较小。
由于散装料地坑下料以及1#转运站尘源点还在渣跨西南侧10~20m处,而除尘器位置在钢坯精整跨北侧靠东部位置,管线布置太远,阻力平衡基本无法实现控制,即风机满负荷状态下,加料跨2个顶吸罩打开后,远端散装料地坑下料以及1#转运站尘源点除尘风量会明显降低,因此我方建议把加料跨除尘系统和散装料除尘系统分开新建两套除尘系统较为合理。
6.2方案二分析加料跨除尘系统总设计风量600000m3/h,系统风压5500Pa;散装料除尘系统总设计风量180000m3/h,系统风压5500Pa;此方案可以保证两套除尘系统每个尘源点的除尘风量,其中加料跨除尘系统风机常开满负荷运行;而散装料除尘系统风机通过变频调速控制,实现工况满负荷和低速运行两种状态。
6.3两个方案对比分析此方案相对方案一投资费用相对较高,需要新建2套除尘系统,单对散装料系统除尘效果会明显高于方案一的设计方式。
我方建议贵方采用方案二。
7.主要设备选型7.1除尘器选型1)、加料跨除尘系统所述风量计算:600000m3/h根据系统总风量及系统烟气粉尘特性,除尘器选用我公司成熟的LCMD-12000低压脉冲布袋除尘器。
(技术参数表见附表1-2)2)、散装料除尘系统要所述风量计算:180000m3/h根据系统总风量及系统烟气粉尘特性,除尘器选用我公司成熟的LCMD-3800低压脉冲布袋除尘器。
(技术参数表见附表1-3)8.设备工作原理及结构介绍8.1工作原理LCM-D型离线清灰低压脉冲袋式除尘器的气体净化方式为外滤式,含尘气体由导流管进入各单元过滤室并通过设备于灰斗中的烟气导流装置;由于设计中袋底离进风口上口垂直距离有足够、合理的净空,气流通过适当导流和自然流向分布,达到整个过滤室内气流分布均匀;含尘气体中的颗粒粉尘通过自然沉降分离后直接落入灰斗、其余粉尘在导流系统的引导下,随气流进入中箱体过滤区,吸附在滤袋外表面。
过滤后的洁净气体透过滤袋经上箱体,经过离线蝶阀由排风管排出。
滤袋采用压缩空气进行喷吹清灰,清灰机构由气包、喷吹管和电磁脉冲控制阀等组成。
过滤室内每排滤袋出口顶部装配有一根喷吹管,喷吹管下侧正对滤袋中心设有喷吹口,每根喷吹管上均设有一个脉冲阀并与压缩空气气包相通。
清灰时,电磁阀打开脉冲阀,压缩空气经喷口喷向滤袋,与其引射的周围气体一起射入滤袋内部,引发滤袋全面抖动并形成由里向外的反吹气流作用,清除附着在滤袋外表面的粉尘,达到清灰的目的。
随着过滤工况的进行,当滤袋表面积尘达到一定量时,由清灰控制装置(差压或定时、手动控制)按设定程序打开电磁脉冲阀喷吹,压缩空气以极短促的时间顺序通过各个脉冲阀经喷吹管上的喷嘴诱导数倍于喷射气量的空气进入滤袋,形成空气波,使滤袋由袋口至底部产生急剧的膨胀和冲击振动,造成很强的清灰作用,抖落滤袋上的粉尘。
落入灰斗中的粉尘经由卸灰阀排出后,经由输灰系统输出。
除尘器配有先进的离线蝶阀,具有在线、离线二状态清灰功能和离线检修功能。
阻力减小,气流通畅。
除尘器设置有差压、料位等在线监测装置。
除尘器的控制(包括清灰控制等)采用PLC控制。
整套除尘系统的控制实行自动化无人值守控制,并可向工厂大系统反馈信息、接受工厂大系统远程控制。
所有的检修维护工作在除尘器净气室及机外执行,无须进入除尘器顶部。
8.2除尘器主要结构、特点①设计合理的灰斗导流技术解决了一般布袋除尘器常产生的各分室气流不均匀的现象。
②设计了特殊大储量的脉冲阀贮气包既可满足用户提供的高压(G型)气源时使用,亦可满足低压(D型)气源时使用。
③滤袋上端采用弹簧涨圈型式,不但密封性能好,而且在维修更换布袋时快捷简单,实现机外换袋。
④在袋笼上端的结构设计上可按不同工况有多种结构型式(八角型、圆型等)的选择,对袋笼的制造有严格的要求,本公司的袋笼是在引进国外技术合作生产的自动化生产线上加工,其各项指标较行业标准提高50%左右。
⑤袋笼标准长度6米,如用户场地有限,还可根据需要增长1-2米,从而在处理相同风量时,该设备较其它反吹风除尘器和常规脉冲除尘器占地面积最小,可节省30-50%,设备重量亦能减少40%左右。
⑥离线阀升降式提升阀结构,降低了设备阻力,使用出风顺畅。
9.LCM-D型长袋低压脉冲除尘器的制造技术9.1除尘器的阻力控制除尘器的阻力分为两部分。
本设备的设计总阻力为≤1500Pa。
除尘器的阻力一部分是设备的固有阻力(即原始阻力),这是由设备的各个烟气流通途径造成的。
除尘器进出风方式、进风管道各部位的尘气流速选择是否妥当;除尘器各仓室进风的均匀度;导流系统设计是否合理;进风口距离滤袋底部的水平高度导致的含尘气体稳流空间是否足够;滤袋直径和滤袋间距决定的滤袋间烟气抬升速度的合理性;出口管道风速的合理选定等都将影响除尘器的固有阻力值。
为此,我公司设计的布袋除尘器采用平进平出的进出风方式;进风总管和导流系统的设计保证各仓室进风不均匀度在5%以下;进风口距离滤袋底部的水平高度保证含尘气体获得稳流空间;滤袋直径采用160mm且滤袋间距的选定,保证过滤区内滤袋内的净气空间和滤袋外的含尘气体空间比,以保证滤袋间的尘气抬升。
从以往我公司设计生产的除尘器来看,设备的原始阻力都在350Pa左右。
第二部分是设备的运行阻力。
设备的运行阻力是由除尘器在运行过程中滤袋表面形成的挂灰层的厚度导致的一个循环值。
一般我们对这个值的上限设定在1000-1200Pa,在设备达到这个阻力值时,系统启动清灰,将设备阻力回复到原始阻力,进入下一个循环。