高频感应加热的原理
高频加热炉的构造和原理

高频加热炉的构造和原理
高频加热炉是利用高频电磁感应的原理来加热物体的装置,其构造和原理如下:
1. 构造:
- 高频加热炉由一个主电源、电容器、电感线圈和工作盘组成。
- 主电源提供高频电源信号,一般为500 Hz到10 kHz之间的高频电流。
- 电容器用来存储电能,并使其在感应线圈中形成振荡电流。
- 电感线圈是通过电磁感应原理,将电能转化为磁能,并在工作盘中产生强大的电磁场。
- 工作盘是一个金属容器,可以容纳需要加热的物体。
2. 原理:
- 高频加热炉的原理基于高频电磁感应。
当高频电流通过电感线圈时,将形成一个高频交变磁场。
- 当金属物体置于炉盘内时,由于金属的导电性,磁场将穿过金属,并在金属内部引起涡流。
- 涡流在金属内部流动时,会遇到电阻而产生热量,从而将金属加热。
- 由于金属的电阻与导磁率有关,因此高频加热炉更适合加热具有较高电阻率的材料,如不锈钢、铜、铝等。
- 通过调节高频电源的频率和功率,可以控制加热炉的加热效果和温度。
高频加热炉具有加热速度快、效率高、加热均匀等优点,广泛应用于金属加热、
铸造、热处理、焊接等领域。
高频感应加热原理与应用

高频感应加热原理与应用您能想象的到,一根铁棒一二秒钟就可以被加热红起来吗?任何金属都可以被很快地加热到其熔化吗?这就是一种人类目前能够做到和掌握的最快捷的直接加热方法——高中频感应加热。
通常人们对物体的加热,一是利用煤、油、气等能源的燃烧产生热量;二是利用电炉等用电器将电能转换成热量。
这些热量只有通过热传递的方式(热传导、热对流、热辐射),才能传递到需要加热的物体上,也才能达到加热物体的目的。
由于这些加热方式,被加热的物体是通过吸收外部热量实现升温的。
因此,它们都属于间接加热方式。
我们知道,热量的自然传递规律是:热量只能从高温区向低温区,高温体向低温体,高温部分向低温部分自然的传递。
因此,只有当外部的热量、温度明显多于、高于被加热物体时,才能将其有效地加热。
这就需要用很多的能量来建立一个比被加热物体所需要的热量多的多、温度高的多的高温区。
如炉,烘箱等。
这样,不但这些热量中只有少部分能传达至被冷却体上,导致非常大的能源浪费。
而且冷却时间短,在冷却、冷却的过程中,还可以产生大量的有毒性物质和气体。
它们既可以对被冷却体导致腐蚀性的侵害,又可以对大气导致污染。
即便就是采用电炉等电能冷却方式,虽然无污染,但仍然存有着效率高、成本高、冷却速度慢等缺点。
科学的进步与发展,使我们今天无论是对金属物体加热还是对非金属物体加热,都可以采用高效、快速,且十分节能和环保的方式加热.这就是直接加热方式。
对于非金属物体,可以使用工作频率约240mhz及以上,能够并使其内部分子、原子每秒振动、摩擦上亿次之多的微波冷却。
也可以采用低频感应加热,如工频50hz等。
中频、高频感应器冷却,就是将工频(50hz)交流电转换成频率通常为1khz至上百khz,甚至频率更高的交流电,利用电磁感应原理,通过电感线圈转换成相同频率的磁场后,促进作用于处于该磁场中的金属体上。
利用涡流效应,在金属物体中分解成与磁场强度成正比的崔元孙转动电流(即为涡流)。
高频淬火原理
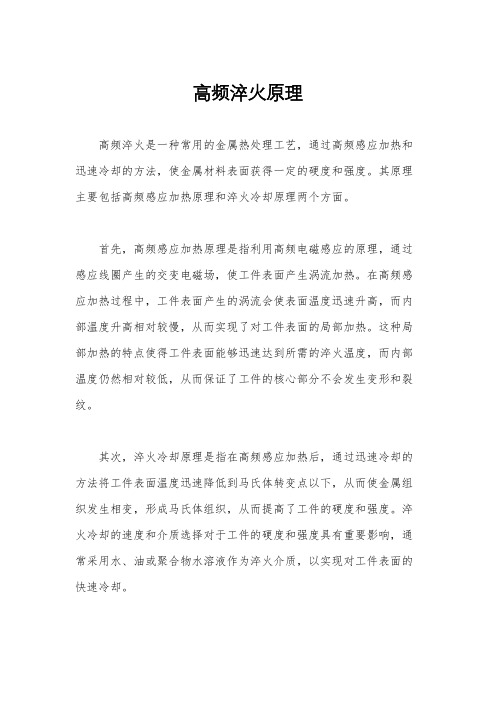
高频淬火原理
高频淬火是一种常用的金属热处理工艺,通过高频感应加热和迅速冷却的方法,使金属材料表面获得一定的硬度和强度。
其原理主要包括高频感应加热原理和淬火冷却原理两个方面。
首先,高频感应加热原理是指利用高频电磁感应的原理,通过感应线圈产生的交变电磁场,使工件表面产生涡流加热。
在高频感应加热过程中,工件表面产生的涡流会使表面温度迅速升高,而内部温度升高相对较慢,从而实现了对工件表面的局部加热。
这种局部加热的特点使得工件表面能够迅速达到所需的淬火温度,而内部温度仍然相对较低,从而保证了工件的核心部分不会发生变形和裂纹。
其次,淬火冷却原理是指在高频感应加热后,通过迅速冷却的方法将工件表面温度迅速降低到马氏体转变点以下,从而使金属组织发生相变,形成马氏体组织,从而提高了工件的硬度和强度。
淬火冷却的速度和介质选择对于工件的硬度和强度具有重要影响,通常采用水、油或聚合物水溶液作为淬火介质,以实现对工件表面的快速冷却。
高频淬火原理的应用范围广泛,可以用于各种金属材料的热处理,特别适用于对工件表面进行硬化处理,提高工件的耐磨性和使用寿命。
同时,高频淬火工艺具有加热速度快、热效率高、变形小等优点,因此在工业生产中得到了广泛的应用。
总之,高频淬火原理是一种通过高频感应加热和迅速冷却的方法,实现对金属材料表面硬化处理的工艺。
通过对高频感应加热原理和淬火冷却原理的深入理解和掌握,可以更好地应用于实际生产中,提高工件的性能和质量,满足不同工件的加工需求。
高频感应加热表面淬火-验证
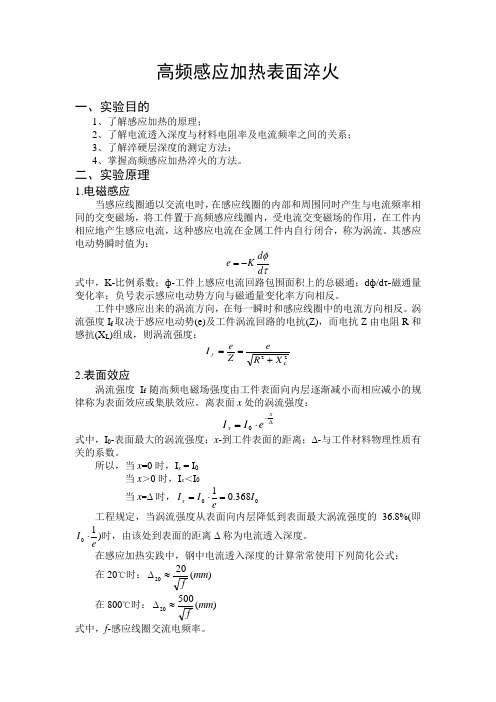
高频感应加热表面淬火一、实验目的1、了解感应加热的原理;2、了解电流透入深度与材料电阻率及电流频率之间的关系;3、了解淬硬层深度的测定方法;4、掌握高频感应加热淬火的方法。
二、实验原理1.电磁感应当感应线圈通以交流电时,在感应线圈的内部和周围同时产生与电流频率相同的交变磁场,将工件置于高频感应线圈内,受电流交变磁场的作用,在工件内相应地产生感应电流,这种感应电流在金属工件内自行闭合,称为涡流。
其感应电动势瞬时值为:τφd d K e -=式中,K-比例系数;ф-工件上感应电流回路包围面积上的总磁通;d ф/d τ-磁通量变化率;负号表示感应电动势方向与磁通量变化率方向相反。
工件中感应出来的涡流方向,在每一瞬时和感应线圈中的电流方向相反。
涡流强度I f 取决于感应电动势(e)及工件涡流回路的电抗(Z),而电抗Z 由电阻R 和感抗(X L )组成,则涡流强度:22Lf X R e Ze I +== 2.表面效应涡流强度I f 随高频电磁场强度由工件表面向内层逐渐减小而相应减小的规律称为表面效应或集肤效应。
离表面x 处的涡流强度:∆-⋅=x x e I I 0式中,I 0-表面最大的涡流强度;x -到工件表面的距离;Δ-与工件材料物理性质有关的系数。
所以,当x =0时,I x = I 0当x >0时,I x <I 0当x =Δ时,00368.01I eI I x =⋅= 工程规定,当涡流强度从表面向内层降低到表面最大涡流强度的36.8%(即eI 10⋅)时,由该处到表面的距离Δ称为电流透入深度。
在感应加热实践中,钢中电流透入深度的计算常常使用下列简化公式:在20℃时:)(2020mm f ≈∆在800℃时:)(50020mm f≈∆式中,f -感应线圈交流电频率。
3.淬硬层深度工件经感应加热淬火后的金相组织与加热温度沿截面分布有关,一般可分为淬硬层、过渡层及心部组织三部分。
还与钢的化学成分、淬火规范、工件尺寸等因素有关;如果加热层较深,在淬硬层中存在马氏体+贝氏体或马氏体+贝氏体+屈氏体+少量铁素体混合组织。
高频电磁加热原理

高频电磁加热原理
高频电磁加热原理是指利用高频电磁场对物体进行加热的一种方法。
高频电磁加热主要依靠电磁场对物体内部的自由电荷进行激发和振动,从而使其产生热量。
高频电磁加热原理主要包括以下几个方面:
1. 电磁感应:高频交变电流通过线圈产生变化的磁场,在物体中引发感应电流。
根据法拉第电磁感应定律,感应电流会形成闭合回路,产生磁场能量并加热物体。
2. 导体损耗:高频电磁场中的电磁波通过导体时,会引发导体内部电荷的欧姆损耗。
这是由于导体内部电荷在电场和磁场作用下发生摩擦,产生热量,使导体加热。
3. 界面效应:高频电磁场作用在物体表面时,会引发物体表面的电荷分布变化。
这种变化使电荷在物体表面发生摩擦,并由于内阻发热。
这种效应在涂料干燥、胶水固化等工艺中广泛应用。
4. 电磁波温差加热:高频电场通过物体时,会产生温差效应。
当电磁波在物体中传播时,由于物体不同部分电阻的差异,会引起温度的差异。
这种温差效应可以对物体进行局部加热或控制温度分布。
总之,高频电磁加热原理通过电磁场的感应、导体损耗、界面效应以及温差效应对物体进行加热。
这种加热方式具有快速、
高效、均匀的特点,被广泛应用于工业生产、医疗器械和烹饪等领域。
高频感应加热焊接实验

高频感应加热焊接实验高频感应加热焊接实验一、实验目的(一)了解高频感应加热焊接方法,并实际施焊。
(二)熟悉高频感应焊接头的焊缝及焊接热影响区组织变化规律,金相观察和分析。
二、实验内容1.高频感应加热焊接工艺试验。
2.高频感应加热焊接规范参数调节和采集。
3.高频感应焊接接头金相组织观察。
三、实验装置及实验材料1.国产感应加热焊接系统2.焊接试样、辅助材料3.粗、细金相砂纸、玻璃平板、机械抛光机、抛光粉4.无水乙醇、4%硝酸酒精溶液、氢氧化钠水溶液、王水、吹风机、脱脂棉5.金相显微镜,计算机图像处理系统四、实验原理感应加热的原理:工件放到感应器内,高频大电流流向被绕制成环状或其它形状的加热线圈(通常是用紫铜管制作)。
由此在线圈内产生极性瞬间变化的强磁束,将金属等被加热物体放置在线圈内,磁束就会贯通整个被加热物体,在被加热物体的内部与加热电流相反的方向,便会产生相对应的很大涡电流。
由于被加热物体内存在着电阻,所以会产生很多的焦耳热,使物体自身的温度迅速上升。
达到对所有金属材料加热的目的。
感应器一般是输入中频或高频交流电(300-300000Hz或更高)的空心铜管。
产生交变磁场在工件中产生出同频率的感应电流,这种感应电流在工件的分布是不均匀的,在表面强,而在内部很弱,到心部接近于0,利用这个集肤效应,可使工件表面迅速加热,在几秒钟内表面温度上升到800-1000oC,而心部温度升高很小。
感应加热的芯部温度是通过一定的时间渗透进去的,因此在选用感应加热设备时,必须考虑温度渗透时间,选用合适的感应加热频率。
感应加热多数用于工业金属零件表面淬火、金属熔炼、棒料透热等多个领域,是使工件表面产生一定的感应电流,迅速加热零件表面,达到表面迅速加热,甚至透热融化的效果。
感应加热是遵循电磁感应、集肤效应、热传导三个基本原则。
实验原理:用一个模拟的单匝短路次级线圈来说明。
以圆柱体加热的方式为例,工件和感应器的组合可以看做是一台具有多匝初级线圈(感应器线圈)和单匝短路次级线圈(圆柱体工件)的变压器,初级线圈和次级线圈彼此间由较小的空气间隙隔开。
高频感应炉原理
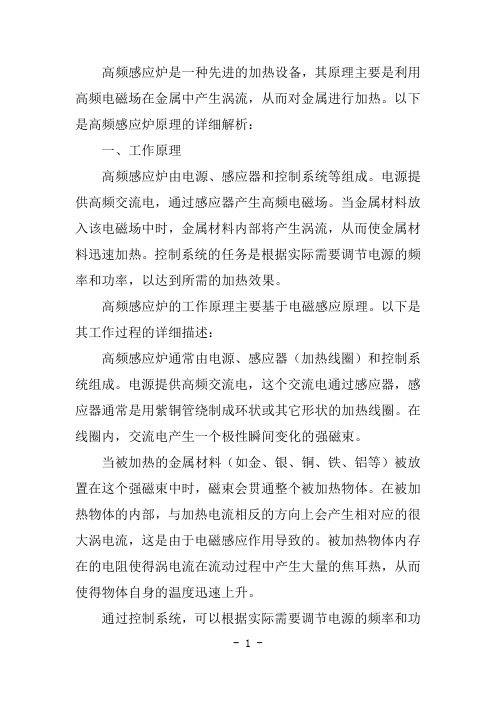
高频感应炉是一种先进的加热设备,其原理主要是利用高频电磁场在金属中产生涡流,从而对金属进行加热。
以下是高频感应炉原理的详细解析:一、工作原理高频感应炉由电源、感应器和控制系统等组成。
电源提供高频交流电,通过感应器产生高频电磁场。
当金属材料放入该电磁场中时,金属材料内部将产生涡流,从而使金属材料迅速加热。
控制系统的任务是根据实际需要调节电源的频率和功率,以达到所需的加热效果。
高频感应炉的工作原理主要基于电磁感应原理。
以下是其工作过程的详细描述:高频感应炉通常由电源、感应器(加热线圈)和控制系统组成。
电源提供高频交流电,这个交流电通过感应器,感应器通常是用紫铜管绕制成环状或其它形状的加热线圈。
在线圈内,交流电产生一个极性瞬间变化的强磁束。
当被加热的金属材料(如金、银、铜、铁、铝等)被放置在这个强磁束中时,磁束会贯通整个被加热物体。
在被加热物体的内部,与加热电流相反的方向上会产生相对应的很大涡电流,这是由于电磁感应作用导致的。
被加热物体内存在的电阻使得涡电流在流动过程中产生大量的焦耳热,从而使得物体自身的温度迅速上升。
通过控制系统,可以根据实际需要调节电源的频率和功率,以达到所需的加热效果。
高频感应炉的加热方式具有高效、快速、非接触式加热等优点,因此在金属熔炼、焊接、表面淬火等加工和热处理过程中得到广泛应用。
在热处理过程中,高频感应炉可用于各种金属的局部或整体淬火、退火、回火、透热等处理。
在热成型过程中,可用于整件锻打、局部锻打、热镦、热轧等操作。
在焊接过程中,可用于各种金属制品的钎焊、刀具刀片、锯片锯齿的焊接以及同种或异种金属的焊接。
在金属熔炼过程中,高频感应炉可用于金、银、铜、铁、铝等金属的熔炼和铸造。
总的来说,高频感应炉通过电磁感应原理实现对金属材料的快速、高效、非接触式加热,是一种理想的加热工艺设备。
二、优点高效节能:由于高频感应炉采用电磁场直接加热金属,避免了传统热传导方式中的热量散失,因此能源利用率极高,可达到90%以上。
感应加热原理(中频高频)

用感应电流使工件局部加热的表面热处理工艺。
这种热处理工艺常用於表面淬火﹐也可用於局部退火或回火﹐有时也用於整体淬火和回火。
20世纪30年代初﹐美国﹑苏联先后开始应用感应加热方法对零件进行表面淬火。
随著工业的发展﹐感应加热热处理技术不断改进﹐应用范围也不断扩大。
基本原理将工件放入感应器(线圈)内(图1感应加热原理)﹐当感应器中通入一定频率的交变电流时﹐周围即產生交变磁场。
交变磁场的电磁感应作用使工件内產生封闭的感应电流──涡流。
感应电流在工件截面上的分布很不均匀﹐工件表层电流密度很高﹐向内逐渐减小(图2沿工件截面的电流密度分布)﹐这种现象称为集肤效应。
工件表层高密度电流的电能转变为热能﹐使表层的温度昇高﹐即实现表面加热。
电流频率越高﹐工件表层与内部的电流密度差则越大﹐加热层越薄。
在加热层温度超过钢的临界点温度后迅速冷却﹐即可实现表面淬火。
分类根据交变电流的频率高低﹐可将感应加热热处理分为超高频﹑高频﹑超音频﹑中频﹑工频5类。
①超高频感应加热热处理所用的电流频率高达27兆赫﹐加热层极薄﹐仅约0.15毫米﹐可用於圆盘锯等形状复杂工件的薄层表面淬火。
②高频感应加热热处理所用的电流频率通常为200~300千赫﹐加热层深度为0.5~2毫米﹐可用於齿轮﹑汽缸套﹑凸轮﹑轴等零件的表面淬火。
③超音频感应加热热处理所用的电流频率一般为20~30千赫﹐用超音频感应电流对小模数齿轮加热﹐加热层大致沿齿廓分布﹐粹火后使用性能较好。
④中频感应加热热处理所用的电流频率一般为2.5~10千赫﹐加热层深度为2~8毫米﹐多用於大模数齿轮﹑直径较大的轴类和冷轧辊等工件的表面淬火。
⑤工频感应加热热处理所用的电流频率为50~60赫﹐加热层深度为10~15毫米﹐可用於大型工件的表面淬火。
(见彩图差温炉淬火﹑600毫米直径冷轧辊工频感应加热淬火﹑大型铸钢件的热处理炉﹑真空淬火炉四、感应加热表面淬火(一)基本原理:将工件放在用空心铜管绕成的感应器内,通入中频或高频交流电后,在工件表面形成同频率的的感应电流,将零件表面迅速加热(几秒钟内即可升温800~1000度,心部仍接近室温)后立即喷水冷却(或浸油淬火),使工件表面层淬硬。
- 1、下载文档前请自行甄别文档内容的完整性,平台不提供额外的编辑、内容补充、找答案等附加服务。
- 2、"仅部分预览"的文档,不可在线预览部分如存在完整性等问题,可反馈申请退款(可完整预览的文档不适用该条件!)。
- 3、如文档侵犯您的权益,请联系客服反馈,我们会尽快为您处理(人工客服工作时间:9:00-18:30)。
高频感应加热的原理及设备一、高频感应加热的原理感应加热是利用导体在高频磁场作用下产生的感应电流(涡流损耗)以及导体内磁场的作用(磁滞损耗)引起导体自身发热而进行加热的。
【当金属导体处在一个高频交变电场中,根据法拉第电磁感应定律,将在金属导体内产生感应电动势,由于导体的电阻很小,从而产生强大的感应电流。
由焦耳—楞次定律可知,交变磁场将使导体中电流趋向导体表面流通,引起集肤效应,舜间电流的密度与频率成正比,频率越高,感应电流密度集中于导体的表面,即集肤效应就越严重,有效的导电面积减少,电阻增大,从而使导体迅速升温】【高频感应加热的原理:导体有电流通过时,在其周围就同时产生磁场,高频电流流向被绕制成环状或其它形状的电感线圈(通常是用紫铜管制作)。
由此在线圈内产生极性瞬间变化的强磁束,将被加热的金属物质放置在感应线圈内,磁束就会贯通整个被加热物质,在被加热物质内部与加热电流相反的方向产生很大的涡流,由于被加热金属物质的电阻产生焦耳热,使金属物质自身的温度迅速上升,从而完成对金属工件的加热】二、感应加热系统的构成感应加热系统由高频电源(高频发生器)、导线、变压器、感应器组成。
其工作步骤是①由高频电源把普通电源(220v/50hz)变成高压高频低电流输出,(其频率的高低根据加热对象而定,就其包材而言,一般频率应在480kHZ左右。
)②通过变压器把高压、高频低电流变成低压高频大电流。
③感应器通过低压高频大电流后在感应器周围形成较强的高频磁场。
一般电流越大,磁场强度越高。
全晶体管高频感应加热设备1、高频感应加热设备现状高频感应加热设备在我省已得到广泛应用,设各频率范围在200-450 kHz,高频功率最大可达400 kW。
我省的高频感应加热设备主要应用于金属热处理、’淬火、透热、熔炼、钎焊、直缝钢管焊接、电真空器件去气加热、半导体材料炼制、塑料热合、烘烤和提纯等。
现在我省使用的高频感应加热设备都是以大功率真空管(发射电子管)为核心构成单级自激振荡器,把高压直流电能量转换成高频交流电能量,它们的电子管板极转换效率一般在75环左右,设备的整机总效率一般在50绒以下,水和电能的消耗非常大。
自70年代中期后,对高频设备也进行了一系列改进,如:(1)用节能型牡钨烟丝电子管代替老式纯钨灯丝系列电子管,如FV-911代替FV-433 } FV-431,FV-89F管等;(2)采用高压硅堆整流代替充汞闸流管整流;(3)采用大功率双向可控硅结合微机调压代替原闸流管调压;(4)根据各自工艺条件重新更改振荡回路,选择合理的振荡频率。
这样,经过一系列改造后,使我省的频设备整机总电效率有一定的提高,在节能方面有一定的效果,但由于振荡电子管这个耗电最大的器件未改掉,所以在节能方面,并不是特别显著。
2、全晶体苍高频感应加热设备电子技术的发展,可谓日新月异。
80年代初,日本首先改进半导体生产工艺,开发生产出场控电力电子器件—大功率静电感应晶体管(SIT ) ,并设计制成换流桥式的,把直流电能量转换成高频电能量的全晶体管化高频感应加热设备,随后美国、西德等发达国家也迅速研制,使之很快就商品化了。
2. 1大功率静电感应晶体管(SIT)的特点大功率静电感应晶体管(SIT)是一种大功率电力电子器件,它的符号与三极管相同,作用也相似,但它主要用在大功率换流或导通的控制场合,它具有以下几个特点:(1)具有“正导通”特性,在正栅压为"0 V”时,SIT处于导通状态,而在加上负栅压时,则将处于关断状态;(2)开关速度快,可用于高频段;(3)是高输入阻抗的电压控制型器件,所以用较小的驱动功率就能控制较大的功率;(4)SIT元件是高耐压大电流型器件;(5)电流的负温度系数不会使电流集中,从而有利于并联驱动,因此可运用于大功率装置。
目前,静电感应晶体管(SIT)的单管功耗有1kW和3kW级的电力电子器件,供组装高频逆变设备.2. 2全晶体管高频感应加热设备主电路由静电感应晶体管SIT组装的高频感应加热设备主回路如附图所示,主电路由3部份组成: (1)直流电源部份:该部份是把工频三相交流电转换为直流电,并控制下面几部份。
该部份主要由三相晶闸管(SCR)可调电路和直流电抗器La与电解电容Ca组成的直流滤波器组成,调整三相晶闸管整流电路的直流输出电压,可调节该设备的输出功率。
输入电压为工频3}p380V,最大直流电压可达500 V以上,输出直流可以100~100%连续可调。
(2)逆变部份:该部份把直流交换为高频交流,并控制后面部份,这部份由电压型单相全桥电路构成,使用1kW或3kW级功耗的SIT作为逆变桥的开关器件,使用同一级功耗的SIT 器件组成电路时,设备的功率越大,频率越高,每一桥臂上并联的SIT器件愈多;R- C。
和D.为缓冲电路,当SIT开始关断而产生浪涌电压,超过这些电路中的直流电压时,二级管D,导通,而电容器C。
吸收该浪涌能量,使逆变桥中的SIT器件安全运行。
SIT元件的导通或关断是由设备上所配备的微机和专用程序控制触发信号,控制其导通或关断。
(3)负载回路部份:该部份的功能是把高频功率输向被加热的金属工件上,负载回路是由谐振回路、电流互感器和加热线圈组成,该电路中的串联谐振回路构成了电压型逆变电路,电容器CT和电感LT两端各产生几干伏以上的高频电压。
高频变流器次级侧通常做成单匝,联接着加热线圈L},巨大的高频电流在L。
周围所产生,高频磁通使金属工件迅速急剧发热。
3、全晶体管化高频与电子管式高频比较全晶体管化高频感应加热设备在如下几个方面优于电子管式高频感应加热设备。
3. 1工作模式得到彻底改变电子管高频感应加热设备需将工频3}p380 V升高后,经高压整流器件变换成相应的直流高压才能供给电子管工作,电子管板极内阻大,有大量功率损耗在板极上发热,而且需要及时加水冷却,同时还需把一部份功率反馈到栅极,并且要较大的灯丝加热功率,这样就有大量的电能损耗在转换之中。
而晶体管高频中的SIT电力电子器件,只需较小的驱动功率来控制较大功率换流的产生,SIT元件正向导通压降很小,损耗不大,并且采用直流500 V的低压工作状态。
电子管板极转换效率最高为750o,SIT电力电子器件为9200;全晶体管高频省去了高压整流变压器、高压硅堆;如果多管并用,能使热量分散,只需加少量的水便可,30kW以下小功率高频可减去水冷却,晶体管高频整机总效率比电子管高频要高20000 3.2能源的节约电子管高频电压转换次数多,电压变化大,而全晶体管高频电压变化不大,在几百伏内变动,不需多次变换电能,所以全晶体管高频比同功率电子管高频节电3000.节水83沁,如输出为80 kW级(FV-911S)电子管高频,振荡工作时输入功率为158 kW,用水3 1/s,而同样的输出功为80 kW的全晶体管高频,振荡工作时,输入功率只需113 kW , 用水。
. 5 1/s,电子管还另需消耗 2. 2 kW的灯丝加热功率。
3.3设备一与维护全晶体管高频体积只有电子管高频的1/3,所以设备占地面积也只有1/3,晶体管高!p设备结构简单.工作非常稳定.故障少(据国内使用厂家介绍,使用2年多没有发现任何故障),维修费用低,省去了原电子管高'G} r1 r i;} " 1:需换的1 }?电r管(6',l loo kW高频为例),约7 000元,水套((2年更换1只)约 3 500元,每年1次的整流变压器检修、滤油费约} m>o 七.整个维修费1年最少可节约 1 万多元。
因用水量减少,水泵也可根据需要改用较小功率的。
4、国内外研制动态4. 1国外产品情况目前在世界上只有少数几个国家的大公司能制造全晶体管高频,如日本的岛田理化工业(株),富士电波机(株),电气兴业(株),美国的ENI公司,德国的FDF公司,EMA 公司等,产品规格已成系列化,如: 日本的:T系列20-}30 kHz 3}-50 kW七种规格,A系列200-}-300 kHz 2,5,10 kW 三种规格,SST系列20^" 200 kHz 2.0, 30, 40 kW三种规格,20~150 kHz 50~200 kW六种规格,20~100 kHz 300, 400 kW二种规格。
美国的:STATITRON系列50^-300 kHz 25一400 kW八种规格西德的:ELOMAT TGI系歹,j 50^-200 kHz 15^-240 kW 等规格,而且他们还在试制更高频,更大功率的高频设备,用途已不只是工业.如广播电台,军事通讯等。
4. 2国产化研制情况我国非常重视国际上这一电力电子器件技术的研究和应用,国家计委、科委、机电部已确定SIT元件和晶体管高频的研制为“八五”国家重点科技攻关项目,具体布署了SIT 器件及全晶体管化高频设备整机的同步攻关,目前我国有关科研单位已研制出小功率0. 1 kW级以下的SIT元件.大功率级的研制还在进行,整机的研制在辽宁电子设备厂进行,目前已研制并出产了几台输出功率为80 kW的全晶体管高频感应加热设备,并在1993年中国国际计算机设备展览会上演示了他们的产品;现在他们又在研制输出功率为10 kW级的全晶体管高频感应加热设备,估计到1996年研制出样机,输出在80 kW以下的高频感应加热设备频率可达300 kHz o 科学技术在不断进步,电子管高频被大功率晶体管代替是必然趋势,这个日子已不会很长,让我们迎接这个时代的到来,为我省的节能技术工作做出新贡献。
高频加热机全称“高频感应加热机”,又名高频感应加热设备、高频感应加热装置、高频加热电源、高频电源、高频焊接机、高周波感应加热机、高周波感应加热器(焊接器)等,另外还有中频感应加热设备、超高频感应加热设备,应用范围十分广泛。
高频大电流流向被绕制成环状或其它形状的加热线圈(通常是用紫铜管制作)。
由此在线圈内产生极性瞬间变化的强磁束,将金属等被加热物质放置在线圈内,磁束就会贯通整个被加热物质,在被加热物质内部与加热电流相反的方向产生很大的涡电流,由于被加热物质内的电阻产生焦耳热,使物质自身的温度迅速上升,这就是感应加热的原理。
感应加热设备就是利用电磁感应原理,使工件在交变磁场中产生感应电流,利用感应电流通过工件所产生的热效应.使工件表面、内孔、局部或整体加热的一种大功率电加热设备。
(一)锻造、轧制类1 、各种麻类的热轧2 、标准件、紧固件的执镦。
如高强度螺栓、螺帽等。
3 、钎钢、钎具的回火、锻造、挤压等的加热。
4 、不锈钢制品退火、退热。
(二)热处理类1、各种五金工具、手工工具的热处理。
如钳子、扳手、旋具、锤子、斧头等。
2、各种汽车配件、摩托车配件的高频淬火处理。
如:曲轴、连杆、活塞销、曲柄销、链轮、凸轮轴、气门、各种摇臂轴;变速箱内各种齿轮、花键思、传动半轴、各种拔叉叉等高频淬火处理。