航空发动机压气机叶片设计
航空发动机涡轮叶片的优化设计与制造

航空发动机涡轮叶片的优化设计与制造航空发动机作为现代航空领域的核心装备,对其性能的要求越来越高。
而发动机的关键部件之一——涡轮叶片的优化设计与制造是影响发动机性能的重要因素之一。
本文将探讨航空发动机涡轮叶片优化设计与制造的相关问题,并分析目前的技术发展趋势。
一、涡轮叶片的功能及挑战作为航空发动机中转子部分的关键组成部分,涡轮叶片扮演着转化热能为动能的重要角色。
涡轮叶片必须具备良好的气动性能、耐高温、高强度和高疲劳寿命。
然而,由于涡轮叶片所处的高温高速环境,其设计与制造面临着一系列挑战。
首先,涡轮叶片需要具备较高的强度和刚度,以承受来自燃气的冲击和离心力。
同时,叶片还必须能够适应温度梯度造成的热应变,以防止由于热膨胀而导致的应力集中和热裂纹的产生。
其次,涡轮叶片在高速旋转过程中会遇到高速气流的冲击,这会导致叶片表面产生强烈的冲刷和磨损。
因此,在涡轮叶片的设计中,需要考虑气动阻力、流量损失和冲刷磨损的平衡。
最后,涡轮叶片的制造过程也是一个复杂而精细的工艺。
涡轮叶片的制造必须具备高精度、高可靠性和高一致性,以确保叶片的性能和质量。
二、涡轮叶片的优化设计为了克服涡轮叶片设计中的挑战,科学家和工程师采用了各种方法和技术进行优化设计。
首先,通过使用先进的材料和工艺,可以提高涡轮叶片的强度和耐热性能。
新材料如镍基合金和热喷涂技术等的应用,使得叶片能够在高温环境下保持相对稳定的性能。
其次,利用计算流体动力学(CFD)和计算机辅助设计(CAD)等先进技术,可以对涡轮叶片的气动性能进行精确的模拟和优化。
通过对流动分析和叶片表面形状的调整,可以减小气动阻力、提高流量效率,并减少叶片表面的冲刷磨损。
另外,采用拓扑优化和结构优化技术,可以在保证叶片强度的前提下,减轻叶片的质量。
通过在关键部位增加材料的厚度或者添加结构支撑,可以实现结构的优化和质量的降低。
这既可以提高叶片的振动特性,又能够延长叶片的寿命。
三、涡轮叶片的制造技术涡轮叶片的制造技术一直在不断发展和创新。
航空发动机设计手册第8册—压气机

航空发动机设计手册第8册—压气机航空发动机设计手册第8册—压气机导言航空发动机作为现代飞机的核心部件之一,其设计和性能直接关系到飞机的安全和效率。
而在整个发动机中,压气机作为将空气压缩的部分,具有非常重要的作用。
本文将从深度和广度两个方面对航空发动机设计手册第8册—压气机进行全面评估,并撰写一篇有价值的文章,以帮助读者更全面、深刻地理解这一主题。
一、压气机的作用和原理压气机是航空发动机中的一个重要部件,其主要作用是将从进气口吸入的空气进行压缩,以提高空气的密度和压力,为燃烧室提供更加理想的燃烧条件。
通过高效的压气机设计,可以有效提高发动机的功率输出和燃料效率,从而提高飞机的性能和经济性。
压气机的原理主要是通过旋转的叶片对空气进行不断的加速和压缩,使其内能转化为压缩空气的动能和静能。
二、压气机设计要点及技术挑战在航空发动机设计手册第8册中,对压气机的设计要点和技术挑战进行了详细的介绍。
压气机设计需要考虑叶片的气动性能和结构强度,以确保在高速旋转和高压力下的稳定运行。
压气机的叶片布局和数量、进气口的设计和进气量的控制等都是需要精密计算和优化的关键参数。
压气机在高速飞行状态下还需要考虑气动噪声和振动问题,以确保飞机在各种工况下都能够稳定、安全地运行。
三、压气机的发展趋势和展望随着航空发动机技术的不断进步和飞机性能的不断提高,压气机的设计也在不断发展和演进。
未来的压气机将更加注重高效、轻量化和智能化的设计,以满足飞机对燃料经济性、环保性和安全性的更高要求。
随着电力推进和混合动力技术的发展,压气机在这些新型动力系统中的应用也将得到更加广泛的关注和研究。
总结航空发动机设计手册第8册—压气机作为航空发动机设计的重要参考资料,全面系统地介绍了压气机的设计原理、计算方法和性能特点。
通过对压气机的深度和广度的探讨,我们可以更好地理解航空发动机的工作原理和设计要点,从而更好地应用于飞机研发和运行中。
压气机作为航空发动机的关键部件,其设计和性能对飞机的性能和经济性都具有重要影响,因此其发展趋势和展望也值得我们深入关注和研究。
基于EFFD参数化的风扇/压气机叶片一端壁一体化伴随优化设计

收稿日期:2021-07-12基金项目:国家自然科学基金(51406011)资助作者简介:李鑫(1992),男,博士。
引用格式:李鑫,张韬,李伟伟,等.基于EFFD 参数化的风扇/压气机叶片-端壁一体化伴随优化设计[J].航空发动机,2023,49(3):54-60.LI Xin ,ZHANG Tao ,LI Wei-wei ,et al.The coupled adjoint optimization of blade and endwall in fan/compressor based on EFFD parameterization method[J].Aeroen⁃gine ,2023,49(3):54-60.基于EFFD 参数化的风扇/压气机叶片-端壁一体化伴随优化设计李鑫1,张韬2,3,李伟伟1,周玲4,季路成1(清华大学航空发动机研究院1,车辆与运载学院2:北京100084;3.北京动力机械研究所,北京100024;4.北京理工大学宇航学院,北京100081)摘要:为解决传统扰动参数化方法的设计能力不足等问题,以拓展自由变形技术为基础开发相应参数化方法以改进伴随优化系统,并对典型跨声速风扇/压气机转子Rotor 67进行叶片-端壁一体化伴随优化。
结果表明:经过伴随优化,Rotor 67转子在流量、压比等工况约束变化较小的前提下效率提升了0.74%,且整体特性同样得到了大幅改进,而优化前后的几何与流动变化表明,端区几何调整及叶片吸力面变化引起的吸力面加速减弱、激波强度降低、角区分离涡结构改进等,均是性能提升的内在原因。
关键词:伴随优化;拓展自由变形;风扇/压气机;叶片-端壁一体化设计;航空发动机中图分类号:V232.4文献标识码:Adoi :10.13477/ki.aeroengine.2023.03.007The Coupled Adjoint Optimization of Blade and Endwall in Fan/Compressor Basedon EFFD Parameterization MethodLI Xin 1,ZHANG Tao 2,3,LI Wei-wei 1,ZHOU Ling 4,JI Lu-cheng 1(1.Institute for Aero Engine ,Tsinghua University ,Beijing 100084,China ;2.School of Vehicle and Mobility ,Tsinghua University ,Beijing 100084,China ;3.Beijing Institute of Power Machinery ,Beijing 100024,China ;4.School of Aerospace Engineering ,Beijing Institute of Technology ,Beijing 100081,China )Abstract :In order to solve the problem of insufficient design capability of traditional perturbation parameterization methods,a corre⁃sponding parameterization method was developed based on the Extended Free-Form Deformation (EFFD)technology to improve the cou⁃pled adjoint optimization system,and coupled adjoint optimization of blade and endwall was carried out for the typical transonic fan/com⁃pressor rotor of Rotor 67.The results show that,through coupled adjoint optimization,the efficiency of the optimized Rotor 67is increased by 0.74%under the premise of small changes in flow,pressure ratio and other operating conditions.The overall characteristics have also been greatly improved.The geometric and flow changes before and after the optimization show that the internal reasons for the performance improvements are the reduction of suction surface acceleration,the reduction of shock wave strength,and the improvement of corner sepa⁃rated vortex structure caused by the geometric adjustment of the end zone and the change of blade suction surface.Key words :coupled adjoint optimization;Extended Free-Form Deformation;fan/compressor;blade and endwall integrated design;aeroengine航空发动机Aeroengine0引言现代先进航空发动机的内部流动非线性程度高[1]、设计参数众多,完全依靠设计师凭经验进行手动设计已难以满足日益提高的发动机性能发展需求[2]。
航空发动机压气机叶片振动特征计算平台设计

航空发动机叶片的无损检测毕业设计说明书
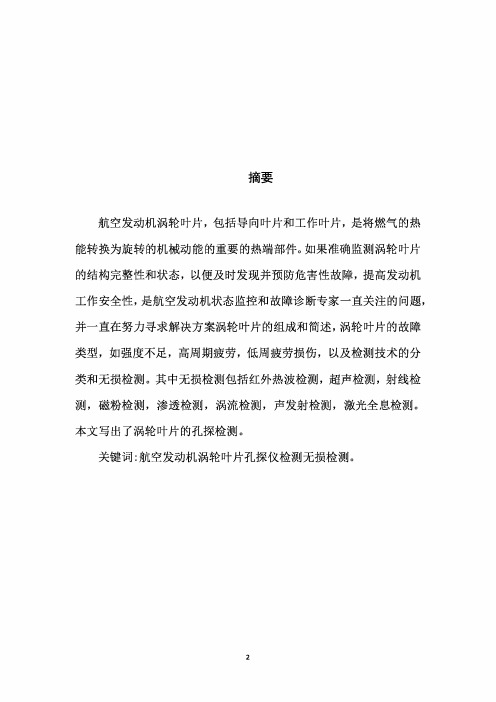
摘要航空发动机涡轮叶片,包括导向叶片和工作叶片,是将燃气的热能转换为旋转的机械动能的重要的热端部件。
如果准确监测涡轮叶片的结构完整性和状态,以便及时发现并预防危害性故障,提高发动机工作安全性,是航空发动机状态监控和故障诊断专家一直关注的问题,并一直在努力寻求解决方案涡轮叶片的组成和简述,涡轮叶片的故障类型,如强度不足,高周期疲劳,低周疲劳损伤,以及检测技术的分类和无损检测。
其中无损检测包括红外热波检测,超声检测,射线检测,磁粉检测,渗透检测,涡流检测,声发射检测,激光全息检测。
本文写出了涡轮叶片的孔探检测。
关键词:航空发动机涡轮叶片孔探仪检测无损检测。
目录摘要 (2)绪论 (1)第一章涡轮叶片的简述 (2)1.1涡轮的工作叶片 (2)1.2导向叶片 (2)第二章故障类型 (3)2.1强度不足及其故障模式 (3)2.2高周期疲劳损伤及其故障模式 (3)2.3低周疲劳损伤及故阵模式 (3)2.4涡轮叶片的常见故障及概率 (3)2.5注意事项 (5)第三章机上孔探检测 (6)3.1涡轮叶片的机上孔探检查 (6)3.2涡轮叶片的不同部位孔探检查 (6)3.3孔探技术的发展和实际应用的需求 (7)3.4修理车间检测前的清洗预处理 (7)3.5叶片完整性检查 (8)3.6探孔注意事项 (8)第四章涡轮叶片孔探案例分析 (9)4.1高压涡轮叶片断裂 (9)4.2典型案例分析 (10)4.3叶片断裂的原因 (11)4.4叶片修理与孔探检测 (13)4.5总结 (14)参考资料 (15)致谢 (16)航空发动机涡轮叶片无损检测技术绪论航空发动机涡轮叶片,包括导向叶片和工作叶片,是将燃气的热能转换为旋转的机械动能的重要的热端部件。
基于提高推重比和单位推力的需要,涡轮前燃气温度日益提高,目前国外新型的航空燃气涡轮发动机涡轮前的温度已达到1700K以上。
涡轮叶片在高压腐蚀性燃气的神击下高速旋转,除承受巨大的拉应力外,还承受频率、幅值变化都很大的交变拉应力和扭转应力,此外还存在高温氧化、热腐蚀和磨损问题。
压气机叶片服役稳定载荷

压气机叶片服役稳定载荷压气机叶片服役稳定载荷是一个在航空发动机领域非常重要的概念。
压气机叶片是航空发动机中的一个核心组件,起到压缩空气并将其送往燃烧室的作用。
在高速旋转的压气机中,叶片需要承受巨大的离心力和温度负荷,因此其设计和材料的选择至关重要,以确保在各种工况下的安全和可靠性。
1. 压气机叶片的设计与制造压气机叶片的设计需要考虑多个因素,包括空气动力学特性、材料的热特性、叶片流动特性等。
设计人员需要通过复杂的计算模型和仿真分析来确定合适的叶片几何形状和结构布局。
材料的选择也至关重要,常见的材料包括高温合金、钛合金等。
这些材料具有良好的耐高温、耐腐蚀和抗疲劳性能,能够满足叶片在高温、高速和高振动环境中的工作要求。
2. 叶片的受力分析压气机叶片在工作条件下承受多种受力,包括离心力、气动力、热应力等。
离心力是由于叶片的旋转而产生的,在叶片上形成一个向外的离心力矩。
气动力是由于空气流动而产生的,主要表现为压力和剪力。
热应力是由于叶片在高温环境中的热膨胀和冷却不均匀引起的。
在叶片的设计和制造过程中,需要进行受力分析并优化叶片的结构,以确保其在各种受力条件下的安全运行。
3. 压气机叶片的服役稳定载荷压气机叶片在实际运行中将承受多种载荷,包括常态载荷和非常态载荷。
常态载荷是指叶片在正常运行工况下承受的稳定载荷,包括离心力、气动力等。
非常态载荷是指叶片在工作过程中突发的、可能超过设计极限的载荷,如启动和停车过程中的冲击载荷。
对于压气机叶片的设计和制造来说,必须要考虑到这些常态和非常态载荷,以确保叶片在各种工况下的安全运行和寿命。
4. 压气机叶片的性能评估为了评估压气机叶片的性能和可靠性,人们通常会进行静态和动态测试。
静态测试是通过施加不同的静态载荷来评估叶片的强度和刚度。
动态测试是通过在叶片上施加动态载荷来评估叶片的振动特性和疲劳寿命。
这些测试是为了验证叶片的设计是否满足规定的性能要求,并为改进设计提供参考依据。
航空发动机设计手册第8册—压气机
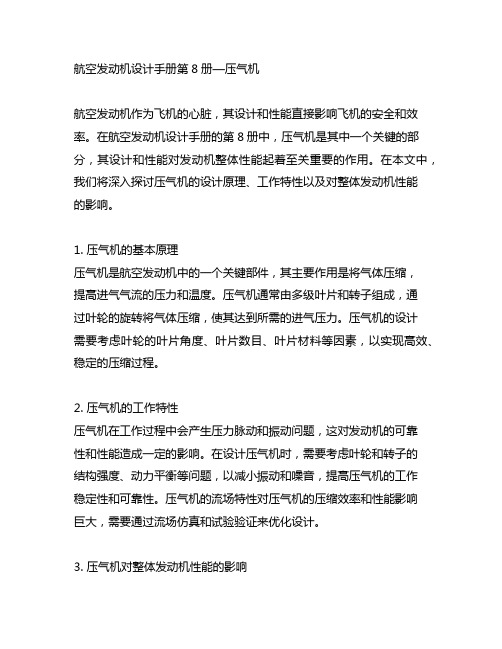
航空发动机设计手册第8册—压气机航空发动机作为飞机的心脏,其设计和性能直接影响飞机的安全和效率。
在航空发动机设计手册的第8册中,压气机是其中一个关键的部分,其设计和性能对发动机整体性能起着至关重要的作用。
在本文中,我们将深入探讨压气机的设计原理、工作特性以及对整体发动机性能的影响。
1. 压气机的基本原理压气机是航空发动机中的一个关键部件,其主要作用是将气体压缩,提高进气气流的压力和温度。
压气机通常由多级叶片和转子组成,通过叶轮的旋转将气体压缩,使其达到所需的进气压力。
压气机的设计需要考虑叶轮的叶片角度、叶片数目、叶片材料等因素,以实现高效、稳定的压缩过程。
2. 压气机的工作特性压气机在工作过程中会产生压力脉动和振动问题,这对发动机的可靠性和性能造成一定的影响。
在设计压气机时,需要考虑叶轮和转子的结构强度、动力平衡等问题,以减小振动和噪音,提高压气机的工作稳定性和可靠性。
压气机的流场特性对压气机的压缩效率和性能影响巨大,需要通过流场仿真和试验验证来优化设计。
3. 压气机对整体发动机性能的影响压气机的设计和性能直接影响整体发动机的性能和效率。
压气机的压缩效率、气动性能和工作稳定性会影响发动机的燃烧过程、推力输出和燃油消耗,直接关系到飞机的飞行性能和经济性。
在设计压气机时,需要综合考虑压气机与其他部件的协调配合,以实现最佳的整体性能和效率。
总结回顾通过对航空发动机设计手册第8册—压气机的深入探讨,我们对压气机的设计原理、工作特性以及对整体发动机性能的影响有了更深入的了解。
压气机作为航空发动机中的关键部件,在提高发动机性能和效率方面发挥着重要作用。
在今后的发动机设计和优化过程中,需要继续关注压气机的设计和性能问题,以实现更高水平的发动机性能和效率。
个人观点和理解作为发动机设计师,我深知压气机在航空发动机中的重要性。
压气机的设计和性能直接关系到整体发动机的性能和效率,对整个飞机的飞行性能和经济性影响巨大。
航空发动机压气机叶片工装标准化

航空发动机压气机叶片工装标准化发表时间:2006-12-3 云守军来源:e-works关键字:叶片工装标准化本文详细论述了航空发动机压气机叶片工装标准化的思路,以典型叶片工装结构为例介绍一些常用标准化方法,通过标准化来实现缩短工装设计制造周期,降低成本。
一. 前言我公司是从事航空发动机压气机叶片(以下简称叶片)精密锻造和机械加工的专业厂家,产品工艺主要特点是:叶身、缘板无余量精锻,机械加工叶片的安装等部位。
这过程中,几乎各个工序都要使用专用工装来加工和检测,工装设计的合理性、工装制造的精度直接决定能否研制出合格的叶片。
叶片工装种类多,数量大,空间角度多,设计制造技术难度大,周期长,常常不能满足研制周期的要求,大量工装现场存放管理维护费时费力。
为缓解这些压力,我们适时对叶片工装进行了大量的标准化工作,明显提高了设计效率,缩短了制造周期。
二. 工装结构的标准化完成某一工艺功能的叶片工装往往有多种常用典型结构,仔细分析它们的共性、个性、各方面优缺点,找出规律性,综合工艺及现场操作人员的意见,依据标准化原则,视不同情况将结构进行简化、统一化、系列化、通用化、组合化。
叶片的形状不规则性导致工装多数采用空间点、型线或型面来定位夹紧,这部分尺寸、结构变化较大,要完全标准化不太现实;但除此之外的其它零部件结构却有很多共性,经过对比筛选,可找出一般规律将它们不同程度的标准化。
我们对预终锻模、切边/叶尖模、进排气边铣削夹具、浇铸夹具、榫头铣削/拉削/磨削夹具、锻造缘板高度测具、榫头三坐标测具、投影测具、叶根最大轮廓过规、叶尖长度测具等工装进行了标准化,下面将就一些实例具体介绍。
图1 转子叶片浇铸夹具2.1 浇铸夹具的标准化首先,统一结构。
浇铸夹具有立式、卧式两种结构,由于立式结构体积较大,密封效果不太好,操作也不太方便,而卧式结构则相对较好,产品质量也较稳定,最终把卧式结构的浇铸夹具确定为标准结构。
见图1所示。
图2 浇铸夹具底座其次,简化结构。
- 1、下载文档前请自行甄别文档内容的完整性,平台不提供额外的编辑、内容补充、找答案等附加服务。
- 2、"仅部分预览"的文档,不可在线预览部分如存在完整性等问题,可反馈申请退款(可完整预览的文档不适用该条件!)。
- 3、如文档侵犯您的权益,请联系客服反馈,我们会尽快为您处理(人工客服工作时间:9:00-18:30)。
Copyright © 2000-2006. All rights reserved
SoftInW ay, In c., 35 Corpo rate Dr., Burlington, MA 01803. Tel: (781)685-4942 TURBOMACHINERY DESIGN WITH AxSTREAM™
DESIGN OF THE 43.3" LSB
The Design of the Last Stage (L-0) of the steam turbine LP is a compromise between creating the
aerodynamically perfect set of blade profiles and making it fitted the requirements of durability and reliability. This takes a large amount of time and efforts, requires high skilled designers and is a real bottle-neck of a whole design process.
AxSTREAM ™ provides designers with the complex solution of gasdynamic / structural design and
optimization for L-0. Additionally, the airfoils profiling / stacking with regard to the stresses caused by the centrifugal forces and aerodynamic loads are performed.
The result of design with AxSTREAM ™ is a 3D model of blade surface and geometry representation suitable to immediate building the models for 3D CFD simulation with CFX and FLUENT.
The design capabilities provided by AxSTREAM ™ dramatically reduce time consumption for the L-0 stage design.
The link below leads to an example of AxSTREAM ™-aided design of the 43.31" blade (D/l = 2.37) at 3000rpm. The stage power is 19 MW, efficiency - 62 %.
Totally, the design procedure takes near 30 hours. At that, 12 hours have been spent on calculation and optimization of the stage with concern on the flow irregularity along the blade height, while the rest of time was dedicated to the airfoils profiling considering actual flow characteristics, stress distribution and smoothness of the blade surface.。