轮毂电机驱动车辆悬架系统设计及优化
电动牵引车的轮胎与悬挂系统优化设计
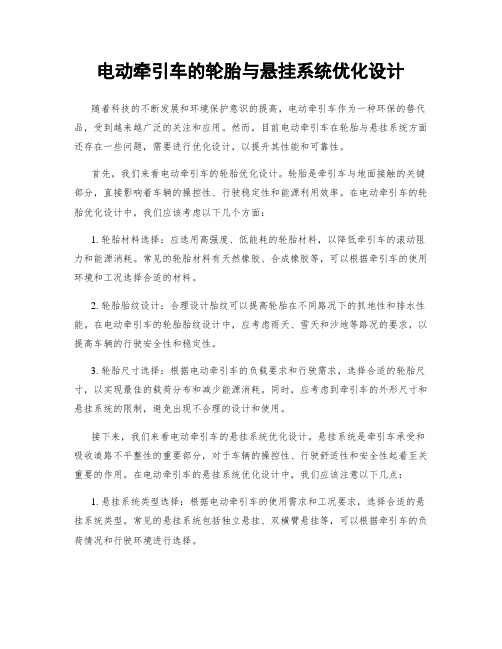
电动牵引车的轮胎与悬挂系统优化设计随着科技的不断发展和环境保护意识的提高,电动牵引车作为一种环保的替代品,受到越来越广泛的关注和应用。
然而,目前电动牵引车在轮胎与悬挂系统方面还存在一些问题,需要进行优化设计,以提升其性能和可靠性。
首先,我们来看电动牵引车的轮胎优化设计。
轮胎是牵引车与地面接触的关键部分,直接影响着车辆的操控性、行驶稳定性和能源利用效率。
在电动牵引车的轮胎优化设计中,我们应该考虑以下几个方面:1. 轮胎材料选择:应选用高强度、低能耗的轮胎材料,以降低牵引车的滚动阻力和能源消耗。
常见的轮胎材料有天然橡胶、合成橡胶等,可以根据牵引车的使用环境和工况选择合适的材料。
2. 轮胎胎纹设计:合理设计胎纹可以提高轮胎在不同路况下的抓地性和排水性能。
在电动牵引车的轮胎胎纹设计中,应考虑雨天、雪天和沙地等路况的要求,以提高车辆的行驶安全性和稳定性。
3. 轮胎尺寸选择:根据电动牵引车的负载要求和行驶需求,选择合适的轮胎尺寸,以实现最佳的载荷分布和减少能源消耗。
同时,应考虑到牵引车的外形尺寸和悬挂系统的限制,避免出现不合理的设计和使用。
接下来,我们来看电动牵引车的悬挂系统优化设计。
悬挂系统是牵引车承受和吸收道路不平整性的重要部分,对于车辆的操控性、行驶舒适性和安全性起着至关重要的作用。
在电动牵引车的悬挂系统优化设计中,我们应该注意以下几点:1. 悬挂系统类型选择:根据电动牵引车的使用需求和工况要求,选择合适的悬挂系统类型。
常见的悬挂系统包括独立悬挂、双横臂悬挂等,可以根据牵引车的负荷情况和行驶环境进行选择。
2. 悬挂系统刚度调整:合理调整悬挂系统的刚度可以提高牵引车的操控性和行驶稳定性。
根据不同的工况和使用环境,可以通过调整悬挂系统弹簧的刚度、减振器的阻尼等参数,达到最佳的悬挂效果。
3. 悬挂系统减震性能改进:减震器是悬挂系统的重要组成部分,对于牵引车的行驶舒适性和安全性至关重要。
应选用高性能的减震器,并定期进行维护和更换,以保证牵引车的悬挂系统减震性能的稳定性和可靠性。
轮毂电机驱动电动汽车的悬架定位参数优化分析
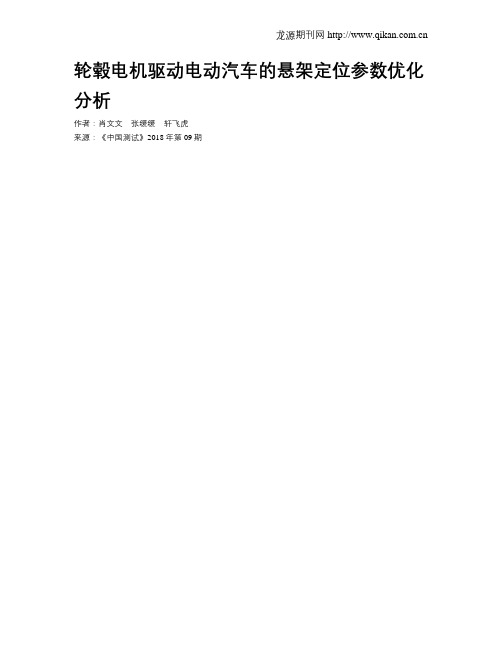
轮毂电机驱动电动汽车的悬架定位参数优化分析作者:肖文文张缓缓轩飞虎来源:《中国测试》2018年第09期摘要:针对轮毂电机驱动电动汽车由非簧载质量大而引起的平顺性问题,通过增加车轮的质量进行仿真实验验证非簧质量增大确实会影响轮毂电机驱动电动汽车的平顺性。
为改善轮毂电机驱动电动汽车的平顺性,通过多体动力学仿真软件ADAMS/Car建立某汽车的整车模型并对其进行平顺性仿真分析,建立的整车模型仿真实验主要由前后车轮、前后悬架、转向系统以及四柱实验台等组成。
通过选取适当悬架的硬点坐标作为优化变量,以影响悬架的前束角、主销内倾角、外倾角、主销后倾角等定位参数变化范围作为优化目标。
通过仿真实验可以看出,优化后的外倾角、前束角等影响悬架的定位角参数的变化优于优化前,从而使得悬架的综合性能达到最佳。
结果表明,优化之后的悬架硬点坐标可以有效地改善轮毂电机驱动电动汽车的平顺性。
关键词:电动汽车;轮毂电机;平顺性;定位参数;仿真分析中图分类号:U1463.33 文献标志码:A 文章编号:1674-5124(2018)09-0148-050引言轮毂电机驱动纯电动汽车在目前具有较好的发展前景,其具有可有效实现汽车尾气零排放、能源利用多元化、高效化等优点,且其直接或间接地把电机安装在车轮上,使得机械传动装置减少,这将提高电动汽车能源的利用率、续航里程和提供乘客更大的空间。
但由于轮毂电机安装在车轮上使得电动汽车的非簧载质量增加,势必影响到电动汽车的平顺性。
平顺性主要是保持汽车在行驶过程中产生的振动和冲击环境对乘员舒适性的影响在一定的界限之内。
本文尝试通过优化悬架的定位参数,改善轮毂电机驱动纯电动汽车的平顺性。
首先利用ADAMS/Car建立整车汽车模型对其进行平顺性仿真分析,通过改变车轮的质量分析悬架的底盘加速度的变化、悬架动挠度的变化以及车轮动载荷的变化来评价是否会对轮毂电机驱动纯电动汽车的平顺性产生恶化。
然后利用ADAMS/INSIGHT对所建立的悬架进行定位参数的优化,将优化之后的悬架重新装配到整车模型中,对比分析优化的悬架是否可以有效地改善轮毂电机驱动纯电动汽车的平顺性。
电动汽车轮毂电机——双横臂悬架系统设计与优化
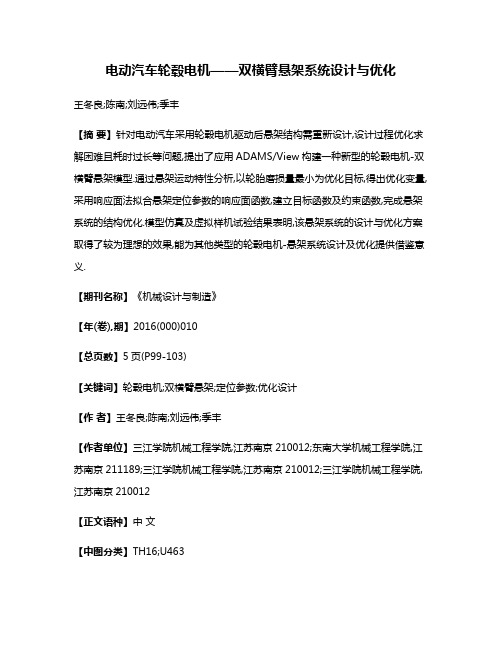
电动汽车轮毂电机——双横臂悬架系统设计与优化王冬良;陈南;刘远伟;季丰【摘要】针对电动汽车采用轮毂电机驱动后悬架结构需重新设计,设计过程优化求解困难且耗时过长等问题,提出了应用ADAMS/View构建一种新型的轮毂电机-双横臂悬架模型.通过悬架运动特性分析,以轮胎磨损量最小为优化目标,得出优化变量,采用响应面法拟合悬架定位参数的响应面函数,建立目标函数及约束函数,完成悬架系统的结构优化.模型仿真及虚拟样机试验结果表明,该悬架系统的设计与优化方案取得了较为理想的效果,能为其他类型的轮毂电机-悬架系统设计及优化提供借鉴意义.【期刊名称】《机械设计与制造》【年(卷),期】2016(000)010【总页数】5页(P99-103)【关键词】轮毂电机;双横臂悬架;定位参数;优化设计【作者】王冬良;陈南;刘远伟;季丰【作者单位】三江学院机械工程学院,江苏南京210012;东南大学机械工程学院,江苏南京211189;三江学院机械工程学院,江苏南京210012;三江学院机械工程学院,江苏南京210012【正文语种】中文【中图分类】TH16;U463悬架是电动汽车的车身与车轮的弹性连接总成[1]。
它的运动特性直接关系到车辆的行驶平顺性、操纵稳定性以及轮胎磨损特性等性能[2]。
电动汽车采用轮毂电机驱动方式,取消了传统车辆的换挡装置、传动轴和差速器等,使车辆的结构简洁、空间利用率变大。
轮毂电机驱动的电动汽车具有较好的动力学控制功能,且可实现灵活的驱动方式[3]。
目前,关于传统车辆的悬架系统运动学特性分析及优化,国外的一些学者已做了大量的研究工作[4-9]:文献[4、6]中基于数据回归分析法分析了麦弗逊悬架悬架的运动特性;文献[9]则采用变量离散寻优方法对单横臂悬架进行优化。
通过对不同类型的悬架特性分析,发现双横臂悬架的定位参数精确可调,且悬架结构在设计优化过程中有较大的自由度,通过合理的空间杆铰接点位置和控制臂长度可将双横臂悬架定位参数变化范围缩小,提升车辆的整体操纵稳定性。
悬挂系统设计与优化

悬挂系统设计与优化悬挂系统作为车辆安全性和舒适性的核心组成部分,承担着支撑车身、减震和消除路面不平衡的重要任务。
在车辆的设计和制造过程中,悬挂系统的合理设计与优化是至关重要的。
本文将探讨悬挂系统的设计原理、优化方法以及未来的发展方向。
1. 悬挂系统设计原理悬挂系统设计的原理是通过弹簧和减震器等组件,将车身与车轮之间的振动分离,使车辆能够稳定行驶。
在设计过程中,需要考虑多个因素,如车辆的质量、行驶条件和驾驶需求等。
传统的悬挂系统包括独立悬挂和非独立悬挂。
独立悬挂系统的优势在于每个车轮都有独立的弹簧和减震器,并能够相互独立响应路面不平。
而非独立悬挂系统则共享一个弹簧和减震器,其结构相对简单,成本较低。
2. 悬挂系统优化方法悬挂系统的优化是为了提高车辆的操控性、行驶平稳性和乘坐舒适性。
常见的优化方法包括弹簧刚度调整、减震器参数设定以及悬挂结构改进等。
首先,弹簧刚度的调整可以影响车身的姿态和悬挂系统的响应速度。
较硬的弹簧可以提高车辆的操控性和稳定性,但会降低乘坐的舒适性。
相反,较软的弹簧可以提供较好的减震效果,但在高速行驶时容易产生车身倾斜。
其次,减震器的参数设定是悬挂系统优化的重要一环。
减震器通过控制弹簧的振动速度来消除车身的颠簸感,提高悬挂系统的响应速度。
在参数设定时,需要综合考虑车辆负载、驾驶方式以及路况变化等因素。
最后,悬挂结构的改进也是悬挂系统优化的一个方向。
通过改变悬挂系统的结构,可以提高系统的刚度和稳定性,降低车身的倾斜和颠簸感。
螺旋弹簧和气囊悬挂等新型设计可以在一定程度上改善悬挂系统的性能。
3. 悬挂系统的未来发展随着汽车工业的快速发展,悬挂系统也在不断演进。
未来,悬挂系统的设计与优化将更加关注以下几个方面。
首先,随着电动汽车的普及,悬挂系统需要针对电动车的特点进行优化。
电动车较重的电池和电动机会对悬挂系统提出更高的要求,以保证车辆的稳定性和乘坐舒适性。
其次,智能化悬挂系统将成为未来的发展趋势。
电动汽车用轮毂电机的设计与优化
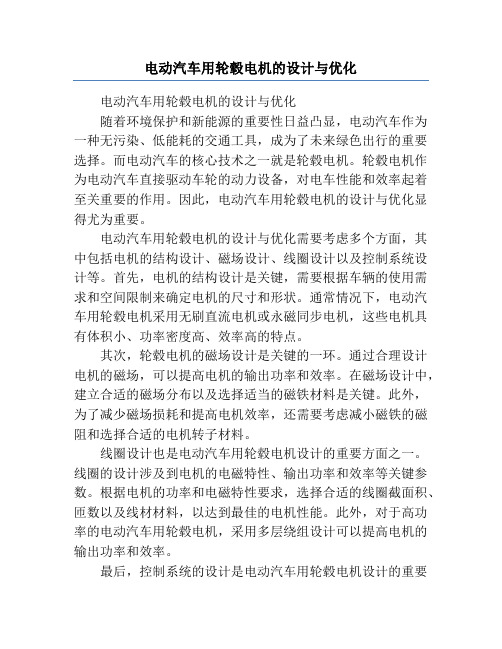
电动汽车用轮毂电机的设计与优化电动汽车用轮毂电机的设计与优化随着环境保护和新能源的重要性日益凸显,电动汽车作为一种无污染、低能耗的交通工具,成为了未来绿色出行的重要选择。
而电动汽车的核心技术之一就是轮毂电机。
轮毂电机作为电动汽车直接驱动车轮的动力设备,对电车性能和效率起着至关重要的作用。
因此,电动汽车用轮毂电机的设计与优化显得尤为重要。
电动汽车用轮毂电机的设计与优化需要考虑多个方面,其中包括电机的结构设计、磁场设计、线圈设计以及控制系统设计等。
首先,电机的结构设计是关键,需要根据车辆的使用需求和空间限制来确定电机的尺寸和形状。
通常情况下,电动汽车用轮毂电机采用无刷直流电机或永磁同步电机,这些电机具有体积小、功率密度高、效率高的特点。
其次,轮毂电机的磁场设计是关键的一环。
通过合理设计电机的磁场,可以提高电机的输出功率和效率。
在磁场设计中,建立合适的磁场分布以及选择适当的磁铁材料是关键。
此外,为了减少磁场损耗和提高电机效率,还需要考虑减小磁铁的磁阻和选择合适的电机转子材料。
线圈设计也是电动汽车用轮毂电机设计的重要方面之一。
线圈的设计涉及到电机的电磁特性、输出功率和效率等关键参数。
根据电机的功率和电磁特性要求,选择合适的线圈截面积、匝数以及线材材料,以达到最佳的电机性能。
此外,对于高功率的电动汽车用轮毂电机,采用多层绕组设计可以提高电机的输出功率和效率。
最后,控制系统的设计是电动汽车用轮毂电机设计的重要环节。
电机的控制系统要能够根据车辆的实时运行状态来调整电机的输出功率和电机转速,以满足车辆的动力需求。
同时,为了提高能源利用率和电池寿命,电机的控制系统还需要考虑能量回馈和能量回收等特点。
为了优化电动汽车用轮毂电机的设计,可以采用模拟仿真和实验验证相结合的方法。
通过使用电磁仿真软件对电机的磁场分布和电磁特性进行优化,并借助实验数据来验证仿真结果的准确性。
通过反复优化和调整,可以得到最佳的电动汽车用轮毂电机设计方案。
电动机悬挂系统设计与优化

电动机悬挂系统设计与优化悬挂系统在现代汽车设计中起着至关重要的作用。
它不仅能够提供舒适的乘坐体验,还能够增加车辆的稳定性和操控性能。
电动汽车悬挂系统的设计和优化尤为重要,因为电动机的特点使得它在车身上的布置方式与传统内燃机有所不同。
本文将探讨电动机悬挂系统的设计原理和优化方法。
首先,我们需要了解电动机悬挂系统的主要组成部分。
电动汽车悬挂系统通常由减震器、悬挂臂、转向节、扭力梁等组件组成。
其中,减震器是悬挂系统的核心部件,它能够减缓车身的震动,提供舒适的乘坐体验。
同时,减震器还能够控制车辆的姿态,保持良好的接地性。
在电动汽车悬挂系统的设计中,我们需要考虑电动机的布置和车重分布对悬挂系统性能的影响。
由于电动机的体积较大且重量较重,通常将电动机安装在车辆的底盘中央,以实现前后轴的平衡。
此外,电动汽车的电池组通常分布在车辆的底盘下方,以降低车辆的重心,提高行驶稳定性。
设计电动机悬挂系统时,需考虑减震器的选型和参数配置。
减震器的类型有多种选择,如气压减震器、液压减震器等。
在电动汽车中,由于电池组的重量较大,需选择具有较强承载能力的减震器。
同时,减震器的参数配置也需要根据车辆的使用场景进行调整,以充分发挥减震器的效能。
另外,悬挂臂和扭力梁的设计也影响着电动汽车的行驶性能。
悬挂臂可分为前悬挂臂和后悬挂臂,它们负责支撑车轮并承受路面的冲击力。
在电动汽车的悬挂系统设计中,需根据车辆的重量和动力性能,选择合适的悬挂臂材料和结构设计,以保证悬挂系统的强度和刚度。
扭力梁是连接悬挂臂的重要部件,它通过扭曲的方式来减少车轮间的滚动。
在电动汽车的悬挂系统优化中,需注意扭力梁的材料选择和结构设计,以提高车轮的接地性和操控性能。
除了上述组成部分的设计,还需要关注电动机悬挂系统的优化方法。
一种常见的优化方法是采用主动悬挂系统。
主动悬挂系统通过传感器感知车辆的姿态和路面状况,利用电子控制单元实时调整减震器的硬度,从而提供更好的悬挂性能。
轮毂电机电动汽车悬架系统优化研究

0 前言目前汽车行业的发展重心为新能源电动汽车,在众多种类的电动汽车中,轮毂电机这种驱动形式渐渐走入众多学者和企业的眼中,受到各个国家的高度重视[1],与其他形式驱动的电动车相比,轮毂电机直接驱动的电动汽车具备更好的空间利用率、NVH、安全性以及更简化的底盘结构。
但不可忽视的是,由于轮内电机的引入,将增加汽车的簧下质量,使车辆的垂向性能发生了很大变化,恶化车辆行驶的平顺性和操纵性。
文献[2]通过建立汽车二自由度垂向振动模型,在其他因素保持不变的情况下只改变非簧载质量,并对比分析不同簧载质量下汽车平顺性评价指标的变化,分析簧载质量对汽车平顺性的影响大小。
文献[3]和[4]分析了轮毂电机驱动形式与集中电机驱动形式的不同之处,并得出了二者非簧载质量不同是造成平顺性恶化的根本原因。
随着此种驱动类型技术难题的不断攻关,轮毂电机电动汽车拥有巨大的市场前景。
为了提高轮毂电机驱动汽车的平顺性及操纵性,对其悬架系统的研究有十分重要的意义[5]。
1 轮内减震系统设计研究1.1 轮毂电机驱动系统的研究图1 轮毂电机驱动汽车电动轮结构此种驱动形式最早由美国人发明,在1950年代,罗伯特发明了一种电机、传动系统、制动系统一体的轮毂装置。
目前来说,此种驱动系统共分为两类,第一类为装备内定子外转子类型电机的电动轮系统,第二类为装备内转子外定子类型电机的电动轮系统,但是此系统需要为电机适配一个减速机构。
我国对轮毂电机驱动系统的研究起步较晚,但也取得了一定成果,如我校自主研发的轮毂电机驱动汽车采用内定子,外转子型电机,并且可以实现四轮独立控制,其轮内结构如图1所示。
1.2 轮内减震系统设计研究虽然由轮毂电机驱动的电动汽车已经研发多年,并成功造出了实车,但为了使轮毂电机能够完美的安装在电动汽车上,消除由于簧下质量增加产生的垂向负效应,国内外学者以及各大企业进行了很多研究。
为了应对轮毂电机驱动系统垂向性能变差的问题,目前主要有三种解决思路:第一种是轻量化设计;第二种思路是对轮毂电机安装方式进行改进研究;第三种是对改进原车的悬架系统,如重新匹配减震器参数等。
电动车的轮胎与悬挂系统优化分析
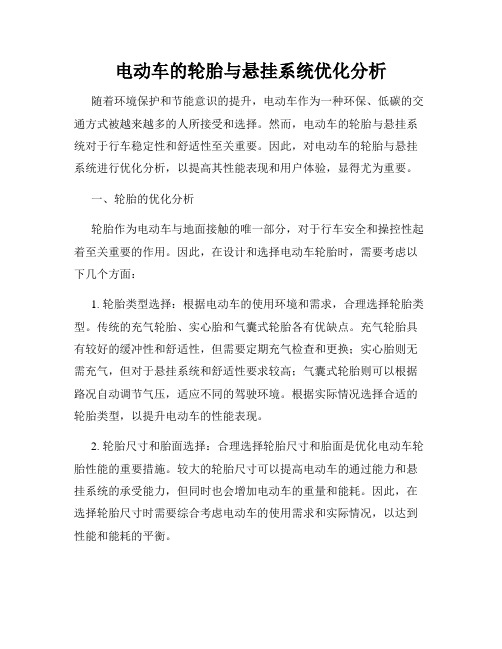
电动车的轮胎与悬挂系统优化分析随着环境保护和节能意识的提升,电动车作为一种环保、低碳的交通方式被越来越多的人所接受和选择。
然而,电动车的轮胎与悬挂系统对于行车稳定性和舒适性至关重要。
因此,对电动车的轮胎与悬挂系统进行优化分析,以提高其性能表现和用户体验,显得尤为重要。
一、轮胎的优化分析轮胎作为电动车与地面接触的唯一部分,对于行车安全和操控性起着至关重要的作用。
因此,在设计和选择电动车轮胎时,需要考虑以下几个方面:1. 轮胎类型选择:根据电动车的使用环境和需求,合理选择轮胎类型。
传统的充气轮胎、实心胎和气囊式轮胎各有优缺点。
充气轮胎具有较好的缓冲性和舒适性,但需要定期充气检查和更换;实心胎则无需充气,但对于悬挂系统和舒适性要求较高;气囊式轮胎则可以根据路况自动调节气压,适应不同的驾驶环境。
根据实际情况选择合适的轮胎类型,以提升电动车的性能表现。
2. 轮胎尺寸和胎面选择:合理选择轮胎尺寸和胎面是优化电动车轮胎性能的重要措施。
较大的轮胎尺寸可以提高电动车的通过能力和悬挂系统的承受能力,但同时也会增加电动车的重量和能耗。
因此,在选择轮胎尺寸时需要综合考虑电动车的使用需求和实际情况,以达到性能和能耗的平衡。
3. 轮胎材料和结构优化:轮胎的材料和结构直接影响其耐磨性、抓地力和舒适性。
通过优化轮胎材料的选择和结构的设计,可以提高轮胎的耐久性和抓地力,同时减轻电动车的整体重量,降低能耗,提升行驶效率和舒适性。
二、悬挂系统的优化分析悬挂系统作为连接电动车车身和轮胎的关键部件,对于保证车辆的操控性和乘坐舒适性具有重要作用。
因此,对电动车的悬挂系统进行优化分析,可以提高其性能和用户体验。
1. 悬挂系统类型选择:常见的悬挂系统类型包括独立悬挂系统和非独立悬挂系统。
独立悬挂系统对电动车的操控性和乘坐舒适性具有较好的表现,但造价较高,适用于高端电动车型。
非独立悬挂系统则适用于低成本和城市通勤型电动车,对于舒适性要求相对较低。
- 1、下载文档前请自行甄别文档内容的完整性,平台不提供额外的编辑、内容补充、找答案等附加服务。
- 2、"仅部分预览"的文档,不可在线预览部分如存在完整性等问题,可反馈申请退款(可完整预览的文档不适用该条件!)。
- 3、如文档侵犯您的权益,请联系客服反馈,我们会尽快为您处理(人工客服工作时间:9:00-18:30)。
轮毂电机驱动车辆悬架系统设计及优化引言本文介绍了轮毅电机式驱动车辆的发展历史和发展现状,针对高校自主开发的电动汽车实体平台的特点,以及传统悬架的自身优势,选取麦弗逊悬架作为匹配对象,进行虚拟样机模型的建立,并进行仿真分析及优化,进而在此基础之上完成整车模型的创建,进行整车操纵稳定性和平顺性的试验仿真,得到试验结果并进行评价。
本文结介国外的最新的科技,全而的介绍了电动轮悬架系统与电动轮本身高度结介的主动轮技术,这是未来悬架的发展方向。
在本文中,首先,根据悬架各部件之间的相对位置,在ADAMS \ Ca:中建立麦弗逊前悬架的虚拟样机模型,并对其进行了双轮同向激振仿真运动学仿真,分析得到悬架参数的变化规律;其次,利用ADAMS \ Insight模块对原始悬架模型进行结构优化,根据仿真结果确定悬架系统更为介理的结构;再次,根据实车参数建立整车虚拟样机模型,并进行进行转向盘转角阶跃输入试验、转向盘转角脉冲输入试验、稳态回转试验和蛇行试验四项车辆操纵稳定性试验仿真,以及汽车三角凸块脉冲输入平顺性试验仿真;最后对仿真结果进行评价。
关键词:轮毅电机式电动轮;麦弗逊悬架;优化;操纵稳定性;凡顺性一、论文背景和意义1.1.1论文背景近年来,随着科技的不断发展和人民生活水平的提高,汽车在作为传统的代步工具越来越多的融入人们生活的同时,也从一个侧面反映了国家的工业水平和科技水平,成为衡量一个国家的发达程度的重要标志。
在当今经济危机愈演愈烈,世界经济陷入低谷难以自拔的时刻,汽车工业因其自身与上下游诸多工业联系广泛的特点,在成为首当其冲的对象之后,有责任和能力带领其它实体工业走出困境。
而在世界能源危机愈演愈烈,全球生态环境日益恶化以及汽车保有量不断增加的背景之下,如何能够使整个逆势反弹、转危为安,技术创新是必不可少的动力之一。
在此背景之下,世界各国及各大汽车公司将新能源汽车作为技术研发的重点,而其中具有不依赖传统燃料、高效率、低污染等特点的电动汽车成为了各大厂商技术攻关的重中之重。
当前电动汽车的驱动方案主要有两种:差速半轴方案和电动轮方案。
其中电动轮方案以其高度集成化、轻质量、高效率的优势,成为了作为未来最具市场潜力和竞争力的结构方案。
1. 1.2研究意义电动轮技术,尤其是轮毅电机驱动的电动轮技术,使整车本身具有很多传统车辆无法比拟的优势。
由于取消了离合器、变速器、传动轴、差速器等部件,底盘结构大为简化,整车质量减轻,各车轮通过电机的独立控制,无论加速还是减速,响应速度快且容易测量,并且其工作噪声极低,零污染的特点很好了迎合了未来环保科技的潮流。
但由于电动轮结构的特殊性,以及主动悬架技术的尚不成熟,电动汽车大多选择可靠的传统悬架结构与其匹配,新技术与老结构的融合,势必会给悬架本身的定位和整车的操纵稳定性和平顺性等性能带来改变。
二、结论本文以课题组轮毅式电动汽车实体平台为蓝本,采用传统的麦弗逊悬架结构进行虚拟样机的建模并优化,完成整车的操纵稳定性和平顺性分析,得到仿真数据为电动轮汽车研究的深入提供支持,为将来科研工作的进一步开展打下夯实的基础。
轮毅电机式电动轮独立驱动电动汽车被普遍认为是电动汽车未来发展的方向,其同步甚至领先于当今全球电动汽车研发及其产业化的进程。
由于自身令人瞩目的应用前景,受到学术界和工程界的一致推崇和高度关注。
本文系统地而全面的阐述了轮毅电机式电动轮的发展历史和发展现状,针对当今设计中电动轮大多匹配传统悬架的现状,基于高校自主开发的电动汽车实体平台,选取了适合的悬架类型,利用ADAMS软件进行动力学仿真分析,揭示了与悬架息息相关的车轮定位参数随车轮跳动的变化规律,并对其进行了虚拟样机的结构优化,以得到更完善的空间结构。
在此基础上建立了整车仿真模型,进行了整车操纵稳定性和平顺性试验仿真分析并对试验结果进行评价。
本文的主要工作内容如下:(1)重点针对轮毅电机式电动轮,阐述了其历史及发展现状,并结合当今的科技前沿,全面的介绍了电动轮悬架系统及电动轮本身的未来发展方向。
<2)基于ADAMS/Car创建了麦弗逊前悬架模型,并对其进行了双轮同向激振仿真运动学仿真,得到包括四个主要的前轮定位参数、主销偏距、侧倾角刚度、轮距等参数随车轮跳动的变化规律,并利用Insight模块选取若干硬点,进行结构优化,以得到更为合理的结果。
<3)建立包括前后悬架、转向系、轮胎、车身等在内的整车虚拟样机动力学仿真分析模型,进行转向盘转角阶跃输入试验、转向盘转角脉冲输入试验、稳态回转试验和蛇行试验四项车辆操纵稳定性试验,以及汽车三角凸块脉冲输入平顺性试验,得到一系列试验结果图线数据,并对其进行评价。
三、附录参考文献[1]潘筱,刘永,杨爱军.ADAMS在汽车动力学仿真中的应用研究[[J].轻型汽车技术,2006(10)[2]孙中辉,孙中红,郭彦颖,李幼德.车辆悬架系统数学模型改进及仿真研究【J].系统仿真学报,2008(3):720一728[3]于海峰.基于ADAMS/Car的悬架系统对操纵稳定性影响的仿真试验研究.大连理工大学硕士论文,2007[4]于海波,李幼德,门玉琢,邓阳庆.双横臂独立悬架ADAMS建模及运动特性分析【J].汽车技术,2007(3):5-8[5]刘虹,王其东.基于ADAMS双横臂独立悬架的运动学仿真分析.合肥一r.业大学学报(自然科学版),2007(1):57一59[6]明巧红,钟绍华.基于ADAMS的双横臂独立悬架的优化设计[[J].专用汽车,2008(10):56-59[7]陈清泉,孙逢春,祝嘉光.现代电动汽车技术(第1版).北京:北京理工大学出版社,2002.1-93[8]李莉.基于ADAMS/Car的某轿车平顺性仿真分析与改进.吉林大学硕士论文,2007[9]郭晓强。
基于ADAMS的虚拟仿真技术在汽车中的应用.吉林大学硕士论文,2005[10]方飞.麦弗逊前独立悬架汽车的操纵稳定性研究.武汉理工大学硕士论文,2006[11]毛金明.麦弗逊悬架仿真分析.南京林业大学硕士论文,2003[12]李臣,司景萍.基于ADAMS/Car的麦弗逊悬架建模与仿真[[J].公路与汽运,2007 (3):8- 10[13]刘进伟,吴志新,徐达.基于ADAMS/Car的麦弗逊悬架优化设计[[J].农业装备与车辆工程,2006(9):34-38[14]汤静,高翔,路丹.基于ADAMS/Car的麦弗逊前悬架优化研究[[J],计算机辅助工程,2004(3):28一32[15]中华人民共和国国家标准,汽车操纵稳定性试验方法蛇形试验,GB/T 6323.1-1994[16]中华人民共和国国家标准,汽车操纵稳定性试验方法转向瞬态响应试验(转向盘转角阶跃输人),GB/T 6323.2一 1994[ 17]中华人民共和国国家标准,汽车操纵稳定性试验方法转向瞬态响应试验(转向盘转角脉冲输入),GB/T 6323.3-1994[ 18]中华人民共和国国家标准,汽车操纵稳定性试验方法稳态回转试验,GBIT 6323.6-1994[19]中华人民共和国国家标准,汽车操纵稳定性指标限值与评价方法,QC/T 480-1999[20]顾云青,张立军.电动汽车电动轮驱动系统开发现状与趋势[[J].汽车研究与开发,2004(12):2723[21]陈俊,MSC.ADAMS技术与_I.程分析实例,中国水利水电出版社[22]张立军、段敏、何辉.汽车前后悬架固有频率的匹配研究.汽车一工程,19986(3)[23 ]赵振东,雷雨成.橡胶元件在汽车悬架中的应用分析[[J].汽车技术,2006(1): 19^-23[24]陈加国.前轮定位参数及其动态变化对汽车操稳性能的影响[[J].机械设计与制造,2004(1):115一116.[25]王连明.汽车平顺性建模及其仿真研究.哈尔滨工业大学学报,1998(10)[26』刘俊.电动汽车电动轮驱动技术仿真研究.吉林大学硕士论文,2006[27]王康.电动汽车电动轮驱动系统控制技术的研究.武汉理工大学硕士论文,2007[28]杨树凯.橡胶衬套对悬架弹性运动与整车转向特性影响的研究.吉林大学硕士论文,2008[29] Michelin Company MICHELIN ACTIVE WHEEL 2008 Paris Motor Show Press Kit, 2008[30] Michelin Company Bibendum Forum&Rally Press Kit, June 2005[31] M. Terashima, T. Ashikaga, T. Mizuno, et al. Novel Motors and Controllers for High-Performance Electric Vehicle with Four In-Wheel Motors: Industrial Electronics,IEEE Transactions, 1997: Volume 44, Issue 1,28一38[32] Muzechuk Richard A Hydraulic Mounts-Improrved Engine Isolation.SAETrans.840410[33] Clark M.Hydraulic Engine Mount Isolation.SAE Trans.851650[34] Katsuhiko Iijima, Kazuo Itami. Electric Wheel Drive. United States Patent, No.4799564,Jan.24, 1989[35] Shiro Matsugaura, Kiyomoto Kawakami, Hiroshi Shimizu. Evaluation of Performances for the In-Wheei Drive System for the New Concept Electric Vehicle“KAZ":Proceedingsof the l9th international Electric Vehicle Symposium. Busan} Korea. 2002[36] Mutsumi Kawamoto, Hidemitsu Inagaki, Satoru Tanaka. Motor Driving Device Provided with Decelerator and Electric Vehicle. United States Patent, No.5014800, May 14, 1991[37] Hiroshi Shimizu, Kiyomoto Kawakami, Yuko Kakizaki, et al. "KAZ" The super electric vehicle: Proceedings of the 18th International Electric Vehicle Symposium. Berlin,Germany. 2001[38] Katsuhiko Kamiya, Junichi Okuse, Kazufumi Ooishi, et al. Development of the Micro EV Car "COMS": Proceedings of the 18th International Electric Vehicle Symposium. Berlin,Germany. 2001[39] Prashant S. Rao, David Roccaforte and Ron Campbell.Developing an ADAMS Model of an Automobile Using Test Data. SAE TECHNICALPAPER SERIES 2002-01一1567[40] Andrew Miller,Testing a Formula SAE Racecar on a Seven-Poster Vehicle Dynamics Simulator. SAE TECHNICAL PAPER SERIES#2002-01-3309。