第六章 复合材料理论
合集下载
第6章 复合材料的界面

接触角
Contact angle
阶段II 增强材料与基体材料间通过相互作用而 使界面固定下来,形成固定的界面层。
界面层的结构: 界面粘合力的性质 界面层的厚度 界面层的组成
◇ 界面层的作用机理
化学键理论 弱边界理论 物理(浸润)吸附理论
机械粘结理论
界面的形成与作用机理
化学键理论(偶联理论)
三、水对复合材料及界面的破坏作用
水对树脂的降解 物理效应(可逆):破坏树脂内氢键或其他次价键,使
树脂增塑,热机械性能下降; 化学效应(不可逆):与树脂内化学键发生化学作用, 树脂降解
水溶胀树脂导致界面破坏 树脂溶胀,在界面上产生剪应力。当剪应力大于 界面粘接力时,界面破坏。
三、水对复合材料及界面的破坏作用
三、水对复合材料及界面的破坏作用
水的浸入(通过扩散作用进入界面) 从树脂宏观裂纹进入(有化学应力和热应力产生裂纹); 树脂内存在的杂质(水溶性杂质); 复合材料成型中在材料内部产生的气泡 水对玻纤的腐蚀 水溶解玻纤表面碱金属氧化物,溶液呈碱性,并加剧玻 纤表面腐蚀破坏,最后导致玻纤SiO2骨架破坏,玻纤强度 降低,复合材料性能下降。
界面反应性(与层剪强度有关)
反应性增加,强度增加
残余应力
残余应力增加,界面强度降低
热膨胀系数不同引起热引力; 树脂固化体积收缩引起的内应力
界面破坏机理
在复合材料中,受外力作用时,基体中会产生微裂纹, 并由基体逐渐扩展到纤维表面,使纤维脱粘(或拔出), 甚至断裂。 弱界面:韧性破坏(纤维脱粘或拔出) 强界面:脆性破坏(纤维断裂) 界面存在物理键(即范德华力)和化学键。其中化 学键是主要的,界面破坏时,二种键均受到破坏。
两相高聚物相互溶解、扩散 高聚物之间的粘接作用与其自粘作用(同种分子 间的扩散)一样,也是高聚物分子键与链段的相互扩 散(不同分子)引起的,由此产生强大的粘接力。
第6章 复合材料结构设计

2009-12-12
weizhou@
19
A 单层树脂含量的选择
一般根据单层的承力性质或单层的使用功能选取
单层的功用 主要承受拉伸、压缩、弯曲载荷 主要承受剪切载荷 用作受力构件的修补 主要用作外表层防机械损伤和大气老化 主要用作防腐蚀 固化后树脂的质量含量(%) 27 30 35 70 70~90
2009-12-12
玻璃/树脂 低 大 容易 中等 良好 多 丰富 较好 低 大 差 适中
凯夫拉49/树脂 中等 小 困难 好 最佳 厚度规格较少 不多 比拉伸强度最高 比压缩强度最低 中等 中等 差 沿纤维方向接近零
碳/树脂 高 中等 较容易 差 不透电波 厚度规格较少 较多 比拉伸强度最高 比压缩强度最高 高 小 好 沿纤维方向接近零
1)
2009-12-12
9
B 载荷情况
静载荷:缓慢地由零增加到某一定数值以后就保 持不变或变动得不显著的载荷。 2) 动载荷:能使构件产生较大的加速度,并且不能 忽略由此而产生的惯性力的载荷。
1)
2009-12-12
10
C 环境条件
力学条件:加速度、冲击、振动、声音等 2) 物理条件:压力、温度、湿度等 3) 气象条件:风雨、冰雪、日光灯等 4) 大气条件:放射线、霉菌、盐雾、风沙等
6.2 复合材料结构设计概述
图6-1
复合材料结构设计基本步骤
性能要求 载荷情况 环境条件 形状限制
原材料选择
1
1) 明确设计条件 2) 材料设计
2009-12-12
2 3
铺层性能确定 层合板设计
应力与应变分析
失效分析
典型构件设计 结构设计
4
3) 结构设计 4) 应力应变及失 效分析
复合材料的复合理论
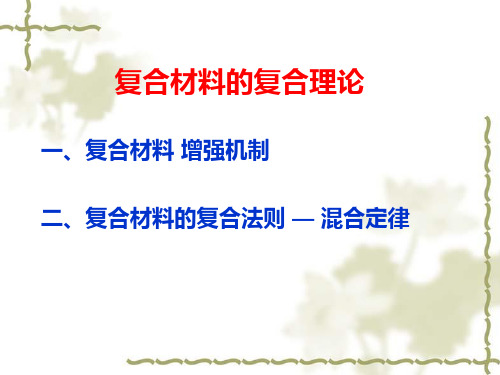
另外,复合材料中的裂纹的扩展在颗粒前受阻,发生应力钝 化或扩展路径发生偏转,同样可以消耗较多的断裂能,提高 材料的强度。
2、纤维(包括晶须、短纤维)复合材料增强机制
基体:通过界面将载荷有效地传递到增强相(晶须、纤 维等),不是主承力相。
纤维:承受由基体传递来的有效载荷,主承力相。
假定纤维、基体理想结合,且松泊比相同;在外力作用 下,由于组分模量的不同产生了不同形变(Байду номын сангаас移),在基 体上产生了剪切应变,通过界面将外力传递到纤维上(见 下图)。
Xc = Xm Vm + XfVf 或 Xc = XfVf + Xm1 - Vf) 式中: X:材料的性能,如强度、弹性模量、密度等;V: 材料的体积百分比; 下脚标 c、m、f 分别代表复合材料、 基体和纤维。
2、连续纤维单向增强复合材料(单向层板)
2-1 应力 - 应变关系和弹性模量 在复合材料承受静张应力过程中,应力—应变经历以
复合材料的面内剪切强度:在垂直纤维方向承受剪切时,
剪切力发生在垂直
纤维的截面内,剪切力由基体和纤维共同承担。
复合材料的复合理论
一、复合材料 增强机制 二、复合材料的复合法则 — 混合定律
一、复合材料 增强机制
1、 颗粒增强复合材料增强机制
1)颗粒阻碍基体位错运动强化: 基体是承受外来载荷相;颗粒起着阻碍基体位错运动的作 用,从而降低了位错的流动性。
颗粒起着阻碍基体位错运动作用示意图
颗粒增强复合材料的强度直接与颗粒的硬度成正比,因为 颗粒必须抵抗位错堆集而产生的应力,另外,颗粒相与基 体的结合力同样影响着材料的强度。
下阶段: (1)基体、纤维共同弹性变形;2)基体塑性屈服、 纤维弹性变形;3)基体塑性变形、纤维弹性变形或基体、 纤维共同塑性变形;4)复合材料断裂。 对于复合材料的弹性模量: 阶段1:E = EfVf + Em(1-Vf) 阶段2:E = EfVf + ( dm/dm)(1-Vf)
2、纤维(包括晶须、短纤维)复合材料增强机制
基体:通过界面将载荷有效地传递到增强相(晶须、纤 维等),不是主承力相。
纤维:承受由基体传递来的有效载荷,主承力相。
假定纤维、基体理想结合,且松泊比相同;在外力作用 下,由于组分模量的不同产生了不同形变(Байду номын сангаас移),在基 体上产生了剪切应变,通过界面将外力传递到纤维上(见 下图)。
Xc = Xm Vm + XfVf 或 Xc = XfVf + Xm1 - Vf) 式中: X:材料的性能,如强度、弹性模量、密度等;V: 材料的体积百分比; 下脚标 c、m、f 分别代表复合材料、 基体和纤维。
2、连续纤维单向增强复合材料(单向层板)
2-1 应力 - 应变关系和弹性模量 在复合材料承受静张应力过程中,应力—应变经历以
复合材料的面内剪切强度:在垂直纤维方向承受剪切时,
剪切力发生在垂直
纤维的截面内,剪切力由基体和纤维共同承担。
复合材料的复合理论
一、复合材料 增强机制 二、复合材料的复合法则 — 混合定律
一、复合材料 增强机制
1、 颗粒增强复合材料增强机制
1)颗粒阻碍基体位错运动强化: 基体是承受外来载荷相;颗粒起着阻碍基体位错运动的作 用,从而降低了位错的流动性。
颗粒起着阻碍基体位错运动作用示意图
颗粒增强复合材料的强度直接与颗粒的硬度成正比,因为 颗粒必须抵抗位错堆集而产生的应力,另外,颗粒相与基 体的结合力同样影响着材料的强度。
下阶段: (1)基体、纤维共同弹性变形;2)基体塑性屈服、 纤维弹性变形;3)基体塑性变形、纤维弹性变形或基体、 纤维共同塑性变形;4)复合材料断裂。 对于复合材料的弹性模量: 阶段1:E = EfVf + Em(1-Vf) 阶段2:E = EfVf + ( dm/dm)(1-Vf)
复合材料的基本理论

层 板 模 型
几 种 主 要 的
力
学பைடு நூலகம்
模
型
几种主要的力学模型 层板模型
层板模型
3方向: E 3c = E m • f m + E I •〔1- f m 〕
2方向:
1 fm1fm 2 E2c Em EI
3 1
泊松比〔泊桑比、泊松收缩〕 νij:在i方向加力时,j方向上产生的收缩
23c
2.2 物理性能的复合法那么
对于复合材料,最引人注目的是其高 比强度、高比弹性模量等力学性能。但 是其物理性能(non-structural properties)也应该通过复合化得到提高。 物理性能包括 加和〔平均〕特性 乘积〔传递〕特性 构造敏感特性
复合材料的复合效应
线性效应
加和效应 平均效应 相补效应 相抵效应
✓ 颗粒的尺寸越小,体积分数越大,强化效果越好。
2) 连续纤维增强
并联模型
串联模型
基体 增强体
连续纤维增强〔并联模型,等应变模型〕
复合材料的载荷=基体载荷+纤维载荷 Pc=Pm+Pr
因为P=σ •A,所以σ c •A c= σ m •A m+ σ r •A r ----〔1〕
A c= A m+ A r
有限差分与有限元模型
a x 2 2 b y 2 2 c x 2 y d x e y f g h t 0
❖ 自变量:x、y〔空间〕;t〔时间〕 ❖ 函数:φ〔温度、浓度、电势、动量等〕 ❖ 拉普拉斯方程、泊松方程、高斯方程、
菲克方程、傅立叶方程、胡克方程、柯 西-雷曼方程、纳维-斯脱克斯方程等
非线性效应
乘积效应 系统效应 诱导效应 共振效应
6 金属基复合材料
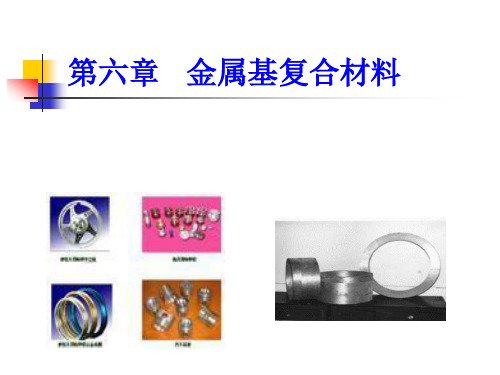
6.2.2金属基复合材料的基本性能
5. 耐磨性好 6. 良好的疲劳性能和断裂韧性 良好的界面结合状态可有效传递载荷, 阻止裂纹的扩展, 提高材料的断裂韧性. 7. 不吸潮, 不老化,气密性好
6.2.3 金属基体在复合材料中的作 用
1. 固结增强体 2. 传递和承受载荷 3. 赋予复合材料一定形状, 保证复合材 料具有一定的可加工性. 4. 复合材料的强度、 刚度、密度、耐高 温、 耐介质、 导电、导热等性能均与基 体的相应性质密切相关.
二、钛及钛合金
钛及其合金由于具有比强度高、耐热性好、耐 蚀性能优异等突出优点,自1952年正式作为结构材 料使用以来发展极为迅速,在航空工业和化学工业 中得到了广泛的应用。化学性质十分活泼,缺点是 在真空或惰性气体中进行生产,成本高,价格贵。
钛基复合材料
二、钛及钛合金
(一)纯钛 钛是一种银白色的金属,密度小,熔点高,高的 比强度和比刚度,较高的高温强度。钛的热膨胀系数 很小,热应力较小,导热性差,切削、磨削加工性能 较差。在空气中,容易形成薄而致密的惰性氧化膜, 在氧化性介质中的耐蚀性优良,在海水等介质中也具 有极高的耐蚀性;钛在不同浓度的酸( HF 除外)以及 碱溶液和有机酸中,也具有良好的耐蚀性。 纯钛具有同素异构转变,在882.5℃以上直至熔点 具有体心立方晶格,称为β —Ti。在882.5℃以下具有 密排六方晶格,称为α —Ti。
(二)钛合金
钛合金分为α 型钛合金 β 型钛合金 α +β 型钛合金 以TA、TB和TC表示其牌号
三、铜及铜合金
在自然界中既以矿石的形式存在,又以纯金属的形 式存在。其应用以纯铜为主。铜及铜合金的产品中, 80%是以纯铜被加工成各种形状供应的。
(一)纯铜 呈紫红色,又称紫铜。属重金属范畴,无同素异构 转变,无磁性。最显著的特点是导电、导热性好,仅次于 银。 高的化学稳定性,在大气、淡水中具有良好的抗蚀 性,在海水中的抗蚀性较差。 纯铜具有立方面心结构,极优良的塑性,可进行冷热 压力加工。
第六章金属基体复合材料

铜在复合材料中的主要用途是作为铌基超导体 的基体材料。
6、金属间化合物
通常是一些高温合金(如硅化物、铝化物、铍化物 等),使用温度可达1600℃决定金属间化合物相结构的主 要因素有电负性、尺寸因素和电子浓度等 使用温度界于高温合金和高温结构陶瓷之间。根据其组成, A、B两元之间可形成AB、A2B、A3B、A5B3 、A7B6等化 合物;根据组成元素,可分为铝化物、硅化物和铍化物。
高性能发动机则要求复合材料有高比强度和比模量,耐 高温性能。此时应选择钛合金、镍合金以及金属间化合物作 为基体材料。
在汽车发动机中要求其零件耐热、耐磨、导热、高温强度 等,同时成本低廉,适合于批量生产,选用铝合金作基体 材料与陶瓷颗粒、短纤维组成颗粒(短纤维)/铝基复合材 料。
工业集成电路需要高导热、低膨胀的金属基复合材料作为 散热元件和基板。因此,选用具有高导热率的银、铜、铝 等金属为基体与高导热性、低热膨胀的超高模量石墨纤维、 金刚石纤维、碳化硅颗粒复合成具有低热膨胀系数和高导 热率、高比强度、高比模量等性能的金属基复合材料。
当韧性金属基体用高强度脆性纤维增强时,基体的屈服和塑 性流动是复合材料性能的主要特征,但纤维对复合材料弹性 模量的增强具有相当大的作用
4)片状复合材料
增强材料是片状的,基体主要是韧性和成型较好 的金属
片状复合材料的强度和大尺寸增强物的性能比较 接近,在增强平面的各个方向上,薄片增强物对 强度和模量都有增强效果 薄片增强相的强度不如纤维增强相高,因此片状 复合材料的强度受到限制
钛合金
通过添加不同的合金元素,可以改变钛同素异 形体的转变温度。添加铝、氧、氮、碳等元素, 可以扩大相区,称为稳定剂。添加钼、钒、 铌、钽等元素,可以扩大相区,所以称为稳 定剂
6、金属间化合物
通常是一些高温合金(如硅化物、铝化物、铍化物 等),使用温度可达1600℃决定金属间化合物相结构的主 要因素有电负性、尺寸因素和电子浓度等 使用温度界于高温合金和高温结构陶瓷之间。根据其组成, A、B两元之间可形成AB、A2B、A3B、A5B3 、A7B6等化 合物;根据组成元素,可分为铝化物、硅化物和铍化物。
高性能发动机则要求复合材料有高比强度和比模量,耐 高温性能。此时应选择钛合金、镍合金以及金属间化合物作 为基体材料。
在汽车发动机中要求其零件耐热、耐磨、导热、高温强度 等,同时成本低廉,适合于批量生产,选用铝合金作基体 材料与陶瓷颗粒、短纤维组成颗粒(短纤维)/铝基复合材 料。
工业集成电路需要高导热、低膨胀的金属基复合材料作为 散热元件和基板。因此,选用具有高导热率的银、铜、铝 等金属为基体与高导热性、低热膨胀的超高模量石墨纤维、 金刚石纤维、碳化硅颗粒复合成具有低热膨胀系数和高导 热率、高比强度、高比模量等性能的金属基复合材料。
当韧性金属基体用高强度脆性纤维增强时,基体的屈服和塑 性流动是复合材料性能的主要特征,但纤维对复合材料弹性 模量的增强具有相当大的作用
4)片状复合材料
增强材料是片状的,基体主要是韧性和成型较好 的金属
片状复合材料的强度和大尺寸增强物的性能比较 接近,在增强平面的各个方向上,薄片增强物对 强度和模量都有增强效果 薄片增强相的强度不如纤维增强相高,因此片状 复合材料的强度受到限制
钛合金
通过添加不同的合金元素,可以改变钛同素异 形体的转变温度。添加铝、氧、氮、碳等元素, 可以扩大相区,称为稳定剂。添加钼、钒、 铌、钽等元素,可以扩大相区,所以称为稳 定剂
第六章复合材料结构设计

为了修正误差,有人建议在上述公式的基本模量上乘以 修正系数0.63,即
E f ( 0 . 63 E m ) v f 3 (1 v f )
X
c
2v f
(拉压型)
X
c
0 . 63 G m 1 v
f
(剪切型)
6.2.2单层性能的确定 设计的初步阶段,为了层合板设计、结构设计的需要,必须 提供必要的单层性能参数,特别是刚度和强度参数。为此,通常 是利用细观力学分析方法推得到预测公式确定的。而在最终设计 阶段,一般为了单层性能参数的真实可靠,使设计更为合理,单 层性能的确定需用试验的方法直接测定。 A.单层树脂含量的选择
Ⅱ
2、横向弹性模量
并联模型的横向弹性模量与串联模型的纵向弹性模量相同。故
ET E L E f v f E m vm
Ⅱ
复合材料单层基本强度的预测
1. 纵向拉伸强度Xt 单层在承受纵向拉伸应力时,假定(1)纤维与基体之间没有 滑移,具有相同的拉伸应变;(2)每根纤维具有相同的强度,且 不计初应力。则在工程上发生上述两种破坏模式: A 基体延伸率小于纤维延伸率时 在应变达到εmu时,基体将先于纤维而开裂,但是纤维尚 能继续承载,直至应变达到εfu时,纤维断裂,复合材料彻底 破坏。对此,可偏于安全地认为纵向拉伸强度只取决于纤维。
1、串联模型的弹性常数 A 纵向弹性模量ELΙ
由模型І取出代表性体积单元, 作用平均应力δ1,在平面应力状态 下,如右图所示。这如同材料力学 中由两种材料并联组成的杆受拉时 的分析。由材料力学知道,已知纤 维材料的弹性模量Ef和基体材料 的弹性模量Em,欲求单元应变
ε1或纵向弹性模量EL的问题是 一次超静定问题。
第6章 复合材料性能

复合材料基本力学特性-破坏机理
(1)脆性破坏
(2)脆性破坏 伴随纤维拔出
(3)不规则破坏
复合材料基本力学特性-破坏机理
纤维的表面都会有缺陷,使纤维沿长度方向存 在弱点,尤其是脆性纤维对这种缺陷敏感性强 缺陷在复合材料中或多或少地随机分布,纤维 在外力作用下将在缺陷处出现断裂,可见断裂 很难发生在一个平面内 纤维中的缺陷不仅位置不同,而且严重程度也 不同
复合材料基本力学特性-破坏机理
复合材料的破坏特征
⒈ 聚合物复合材料的拉伸σ~ε关系,呈脆 性破化特征(纤维无屈服) ⒉ 破坏形貌(拉伸)
⑴ 脆性破坏 况(见图a) 断面平滑整齐对,发生在f-r间粘附较好的情
⑵ 脆性破坏纤维拔出 断面较不规则,有纤维拔出对应σb较 低, 发生在r-f粘附较差的情况(见图b) ⑶ 不规则破坏 断面很不规则,纤维拔出很多,对应σb最 低,发生在r-f粘附很差的情况,产生大量脱胶现象(见图c)
复合材料基本力学特性-力学效应
σ f Ef = σ m Em
组分应力比与相应的弹性模量比相等: 为了在纤维中达到高应力以充分发挥高强度 纤维的效用,纤维的弹性模量应远大于基体 的弹性模量。
复合材料基本力学特性-力学效应
横向拉伸模量(串联模型)
1 / E2 = V f / E f + Vm / Em
强度
σ Tu = σ mu
ET Em
1 ⎞ ⎛ ⎜1 − V f 2 ⎟ ⎠ ⎝
失效应变
ε Tu
⎛ ⎞ = ε mu ⎜1 − V f ⎟ ⎝ ⎠
1 2
复合材料基本力学特性-力学效应
纵向压缩性能的复合效应
纵向压缩载荷作用下,单向复合材料的失效模式有三种:
- 1、下载文档前请自行甄别文档内容的完整性,平台不提供额外的编辑、内容补充、找答案等附加服务。
- 2、"仅部分预览"的文档,不可在线预览部分如存在完整性等问题,可反馈申请退款(可完整预览的文档不适用该条件!)。
- 3、如文档侵犯您的权益,请联系客服反馈,我们会尽快为您处理(人工客服工作时间:9:00-18:30)。
F fFV f m Vm fFV f m (1 V f )
纤维临界体积分数和纤维最小体积分数:
C
F mF D
E m A
OC表示纤维受应力与 纤维体积分数的关系
B
DF表示基体强度与纤 维体积分数的关系
O
V f min
V fcr
Vf
F
• 随纤维体积分数增大,纤维受载荷线性增加,基体载荷线性减少。 V fcr 当纤维体积分数达到 时,纤维承受的载荷与基体承受载荷相等。 B点所对应的纤维体积分数为临界纤维体积分数,B点称为等破坏 F mF 点,在B点,复合材料强度为
如果质点直径为d,体积分数为Vp,质点弥散且均匀分布,根据体式 金相学有如下关系:
2 2 D p ( d / V p ) 2 (1 V p ) 3
可得:
1 2 2 2 y Gmb / ( d / V p ) (1 V p ) 3
1
因此:质点尺寸越小,体积分数越高,强化效果越好,一般Vp=10~15%,d =0.1~0.01um
当体积分数较小时,根据模型1,在横向载荷P作用下,复合材料的横 向伸长量 lT 等于纤维横向伸长量与基体横向伸长量之和
lT l fT lmT
在弹性变形范围内,复合材料额定流动应力为:
式2-21
0T
lT ET 1 T ET 1 lT
即
lT 0T lT / ET 1
m Em m
• 可以得到: EL E f f V f Em mVm • 因为:
f m
• 所以:
EL E f V f EmVm E f V f Em (1 V f )
• 2)横向弹性模量:当纤维条件分数较小时,纤维和基体成串联, 简化成模型1。当纤维含量较高时,纤维紧密接触,期间有基体但 及薄,可认为这部分基体变形与下午一致,就是说可以看成沿横 向互相接触儿连通,简化成并联模型2:
Ec k1 E f V f Em (1 V f )
c k2 f V f m (1 V f )
•强度增强率:复合材料强度与基体强度之比,它表示复合材料的增强 效果。
•分散强化的强度增强率:Fs
y Gmb(3V p ) m 2d (1 V p ) m
纤维强化时的强度增强率:
f c Ff k V f (1 V f ) m m
1) Al-C 2) Al-SiO2 3) Al-Al2O3 4) Ag-Al2O3 5) Cu-W
6) Al-不锈钢
7) 钢 8) 高温合金
6.1.4连续纤维增强复合材料得复合准则
• 6.1.2 颗粒增强原理
• 颗粒增强复合材料是由尺寸较大(>1微米)的坚硬颗粒与金属基 体复合而成。 • 载荷主要由基体承受,但颗粒也承受载荷并约束基体的变形。颗 粒阻止基体位错运动的能力越大,增强效果越好。 • 在外力作用下,基体内位错的滑移在基体-颗粒界面上受到阻止, 并在颗粒上产生应力集中,
E fT
l fT lT
mT lmT
EmT
lmT lT
Vf
Vm
0T
ET 1
fTV f
E fT
mT Vm
EmT
• 根据假设:
0T fT mT
• 代入得:
Vf Vm 1 ET 1 E fT EmT
当纤维含量较大时,纤维和基体之间发生胶联,、摩擦灯作用,纤 维之间连通,增加了载荷传递部位,影响或阻止了横向变形,简化 成模型2。 结果:
l f l f mlm
• f • 在弹性变形时,由虎克定律: f
Gf
m
m
Gm
得:
G1
l
f
Gf
lf
m
Gm
lm
G1
f
Gf
Vf
m
Gm
Vm
由假设可知
f m
因此:
1 V f Vm G1 G f Gm
模型2是纤维与基体轴向并联,纤维被基包围,且假设纤维与基体 结合良好,在扭矩的作用下,纤维与基体产生相同剪应变,但剪 应力不同,所以模型2为等应变假设。 在扭矩得作用下,纤维与基体受力不等,在横截面上 M M f M m 总扭矩用截面上平均切应力 表示:
纤维受应力为:
fT E fT fT E fT
基体应力为:
l fT l fT
l fT fT l fT / E fT
mT EmT mT EmT
lmT lmT
lmT mT lmT / EmT
• 代入得:
0T lT
ET 1
• 式中:
fT l fT
6.1.6 单向连续纤维增强复合材料的强度
• 1 单向连续纤维增强复合材料的纵向拉伸强度 • 复合材料在纵向受拉时,由力平衡可知复合材料纵向平均应力为
0 L f V f mVm
f V f m (1 V f )
复合材料变形第一阶段,纤维和基体都是弹性变形,则有 f m 因此:
6.1.5单向纤维增强复合材料的剪切模量
• • • • • • • • • • 模型1是纤维和基体轴向串联模型, 在扭矩的作用下,圆筒受纯剪应力, 纤维和基体剪应力相同,但因剪切 模量不同,剪应变不同,所以模型1 为等应力假设。(在纤维含量较低时) 假设圆筒在扭矩M的作用下产生剪应变 变形前圆筒的母线为oa,变形后为oa‘, a点周向位移为纤维和基体段位移之 和,即:
• 复合材料的弹性模量是由组成材料的特征、增强材料 的取向和体积分数决定的。
• 1) 纵向弹性模量:假设增强纤维连续、均匀、平行排 列于基体中,形成单向增强复合材料,纤维轴向为纵 向(L),垂直于纤维轴向为横向(T)。 • 在L方向受拉时,计算模型如下图所示。
设L向拉力P,且纤维与基体界面牢固,变形时无相对滑动, 既基体与纤维应变相同,基体将力通过界面完全传递给纤 维,根据力平衡关系,有:
y GmG p b /( D p C )
2 2 D p ( d / V p ) (1 V p ) 3
把质点直径、体积分数和质点间距的关系式代入得:
3GmG p bV
1 2 p
1 2
y
2d (1 V p )C
因此:质点尺寸越小,体积分数越高,强度越高,颗 粒对复合材料的增强效果越好。
在实际用的颗粒增强复合材料中,增强颗粒直径为 1~50微米,体积分数为5~50%。
• 6.1.3 纤维增强原理
• 纤维增强复合材料是由连续纤维或不连续(短)纤维与金属基体 复合而成。复合材料受力时,高强度、高模量的增强纤维承受大 部分载荷,而基体主要作为媒介,传递和分散载荷。 • 通常纤维增强复合材料的弹性模量和断裂强度与各组分性能关系 如下:
• •
bm 为基体总宽度。当沿纤维 设b为复合材料总宽度, b f 为纤维总宽度, 纵向受力时,纵向产生应变 L ,横向应变 T , 因此有:
•
T L L 两边乘以b得: b T b L L
T b b bm bf
b f fT b f f fLb f
•
在切应力 的作用下,位错滑移,遇到硬质点位错线弯曲,位错弯曲部 分曲率半径R为:
R Gmb / 2
• •
式中:Gm-基体剪切模量 b-柏氏矢量 若质点间距为Dp,在剪应力的作用下,位错线曲率半径R=Dp/2时,复 合材料产生塑性变形,此时剪应力为复合材料的屈服强度:
y Gmb / Dp
σ
σ
i
•
其值:
n i
•
由位错理论,应力集中因子为:
n Dp /(Gmb)
• 得到:
i 2 Dp /(Gmb)
• 当应力集中达到颗粒断裂强度时,颗粒开始破坏,产生裂纹,引起复合 材料变形,有:
i p D p /(Gmb)
2
Gபைடு நூலகம் C
•
因此颗粒增强复合材料的屈服强度为:
0 L E f f V f Em m (1 V f )
纤维承受载荷与基体承受载荷之比为:
Pf / Pm E f f V f / Em m (1 V f ) E f V f / Em (1 V f )
Ef • 当Vf一定时, E m 比越大,纤维承受载荷越 大,增强作用就越大。因此复合材料要采用高 强度、高模量的增强纤维,而基体用低强度、 低模量的材料,但基体韧性要好 Ef Em • 当 值一定时, Vf值越大,纤维贡献越大。 理论计算Vf最大可达0.9069,但实际Vf大于 0.80时,复合材料的强度不但不随纤维含量的 增大,反而下降。这是因为纤维太多,没有足 够的基体去润湿和渗入纤维,造成纤维粘结不 好,有空隙,因此强度不高。实际使用体积分 数为0.3~0.6。
bm mT bm m mL bm
L Lb m mL bm f fLbf
• 假设纵向应变协调,纤维和基体应变相等,且等于复合材料纵向应变, 即:
L mL fL
• 所以有
Lb mbm f b f
• 即:
L mVm f V f m (1 V f ) f V f
3GmG p bVp
1 2
1 2
y •颗粒增强复合材料强度增强率: Fp m
2d (1 V p )C
/ m
•在分散强化和颗粒增强复合材料中,强度增强率与质点或颗粒体积分 数、直径及其分布有关,一般说,质点越细,增强率F越大。分散强化 时,质点尺寸在0.1~0.01微米时,F=4~15。质点再细就容易形成固溶 体,质点较大,在0.1~1微米时,F=1~3,增强效果不明显:主要质 点尺寸在此范围内易产生应力集中,强度下降。
纤维临界体积分数和纤维最小体积分数:
C
F mF D
E m A
OC表示纤维受应力与 纤维体积分数的关系
B
DF表示基体强度与纤 维体积分数的关系
O
V f min
V fcr
Vf
F
• 随纤维体积分数增大,纤维受载荷线性增加,基体载荷线性减少。 V fcr 当纤维体积分数达到 时,纤维承受的载荷与基体承受载荷相等。 B点所对应的纤维体积分数为临界纤维体积分数,B点称为等破坏 F mF 点,在B点,复合材料强度为
如果质点直径为d,体积分数为Vp,质点弥散且均匀分布,根据体式 金相学有如下关系:
2 2 D p ( d / V p ) 2 (1 V p ) 3
可得:
1 2 2 2 y Gmb / ( d / V p ) (1 V p ) 3
1
因此:质点尺寸越小,体积分数越高,强化效果越好,一般Vp=10~15%,d =0.1~0.01um
当体积分数较小时,根据模型1,在横向载荷P作用下,复合材料的横 向伸长量 lT 等于纤维横向伸长量与基体横向伸长量之和
lT l fT lmT
在弹性变形范围内,复合材料额定流动应力为:
式2-21
0T
lT ET 1 T ET 1 lT
即
lT 0T lT / ET 1
m Em m
• 可以得到: EL E f f V f Em mVm • 因为:
f m
• 所以:
EL E f V f EmVm E f V f Em (1 V f )
• 2)横向弹性模量:当纤维条件分数较小时,纤维和基体成串联, 简化成模型1。当纤维含量较高时,纤维紧密接触,期间有基体但 及薄,可认为这部分基体变形与下午一致,就是说可以看成沿横 向互相接触儿连通,简化成并联模型2:
Ec k1 E f V f Em (1 V f )
c k2 f V f m (1 V f )
•强度增强率:复合材料强度与基体强度之比,它表示复合材料的增强 效果。
•分散强化的强度增强率:Fs
y Gmb(3V p ) m 2d (1 V p ) m
纤维强化时的强度增强率:
f c Ff k V f (1 V f ) m m
1) Al-C 2) Al-SiO2 3) Al-Al2O3 4) Ag-Al2O3 5) Cu-W
6) Al-不锈钢
7) 钢 8) 高温合金
6.1.4连续纤维增强复合材料得复合准则
• 6.1.2 颗粒增强原理
• 颗粒增强复合材料是由尺寸较大(>1微米)的坚硬颗粒与金属基 体复合而成。 • 载荷主要由基体承受,但颗粒也承受载荷并约束基体的变形。颗 粒阻止基体位错运动的能力越大,增强效果越好。 • 在外力作用下,基体内位错的滑移在基体-颗粒界面上受到阻止, 并在颗粒上产生应力集中,
E fT
l fT lT
mT lmT
EmT
lmT lT
Vf
Vm
0T
ET 1
fTV f
E fT
mT Vm
EmT
• 根据假设:
0T fT mT
• 代入得:
Vf Vm 1 ET 1 E fT EmT
当纤维含量较大时,纤维和基体之间发生胶联,、摩擦灯作用,纤 维之间连通,增加了载荷传递部位,影响或阻止了横向变形,简化 成模型2。 结果:
l f l f mlm
• f • 在弹性变形时,由虎克定律: f
Gf
m
m
Gm
得:
G1
l
f
Gf
lf
m
Gm
lm
G1
f
Gf
Vf
m
Gm
Vm
由假设可知
f m
因此:
1 V f Vm G1 G f Gm
模型2是纤维与基体轴向并联,纤维被基包围,且假设纤维与基体 结合良好,在扭矩的作用下,纤维与基体产生相同剪应变,但剪 应力不同,所以模型2为等应变假设。 在扭矩得作用下,纤维与基体受力不等,在横截面上 M M f M m 总扭矩用截面上平均切应力 表示:
纤维受应力为:
fT E fT fT E fT
基体应力为:
l fT l fT
l fT fT l fT / E fT
mT EmT mT EmT
lmT lmT
lmT mT lmT / EmT
• 代入得:
0T lT
ET 1
• 式中:
fT l fT
6.1.6 单向连续纤维增强复合材料的强度
• 1 单向连续纤维增强复合材料的纵向拉伸强度 • 复合材料在纵向受拉时,由力平衡可知复合材料纵向平均应力为
0 L f V f mVm
f V f m (1 V f )
复合材料变形第一阶段,纤维和基体都是弹性变形,则有 f m 因此:
6.1.5单向纤维增强复合材料的剪切模量
• • • • • • • • • • 模型1是纤维和基体轴向串联模型, 在扭矩的作用下,圆筒受纯剪应力, 纤维和基体剪应力相同,但因剪切 模量不同,剪应变不同,所以模型1 为等应力假设。(在纤维含量较低时) 假设圆筒在扭矩M的作用下产生剪应变 变形前圆筒的母线为oa,变形后为oa‘, a点周向位移为纤维和基体段位移之 和,即:
• 复合材料的弹性模量是由组成材料的特征、增强材料 的取向和体积分数决定的。
• 1) 纵向弹性模量:假设增强纤维连续、均匀、平行排 列于基体中,形成单向增强复合材料,纤维轴向为纵 向(L),垂直于纤维轴向为横向(T)。 • 在L方向受拉时,计算模型如下图所示。
设L向拉力P,且纤维与基体界面牢固,变形时无相对滑动, 既基体与纤维应变相同,基体将力通过界面完全传递给纤 维,根据力平衡关系,有:
y GmG p b /( D p C )
2 2 D p ( d / V p ) (1 V p ) 3
把质点直径、体积分数和质点间距的关系式代入得:
3GmG p bV
1 2 p
1 2
y
2d (1 V p )C
因此:质点尺寸越小,体积分数越高,强度越高,颗 粒对复合材料的增强效果越好。
在实际用的颗粒增强复合材料中,增强颗粒直径为 1~50微米,体积分数为5~50%。
• 6.1.3 纤维增强原理
• 纤维增强复合材料是由连续纤维或不连续(短)纤维与金属基体 复合而成。复合材料受力时,高强度、高模量的增强纤维承受大 部分载荷,而基体主要作为媒介,传递和分散载荷。 • 通常纤维增强复合材料的弹性模量和断裂强度与各组分性能关系 如下:
• •
bm 为基体总宽度。当沿纤维 设b为复合材料总宽度, b f 为纤维总宽度, 纵向受力时,纵向产生应变 L ,横向应变 T , 因此有:
•
T L L 两边乘以b得: b T b L L
T b b bm bf
b f fT b f f fLb f
•
在切应力 的作用下,位错滑移,遇到硬质点位错线弯曲,位错弯曲部 分曲率半径R为:
R Gmb / 2
• •
式中:Gm-基体剪切模量 b-柏氏矢量 若质点间距为Dp,在剪应力的作用下,位错线曲率半径R=Dp/2时,复 合材料产生塑性变形,此时剪应力为复合材料的屈服强度:
y Gmb / Dp
σ
σ
i
•
其值:
n i
•
由位错理论,应力集中因子为:
n Dp /(Gmb)
• 得到:
i 2 Dp /(Gmb)
• 当应力集中达到颗粒断裂强度时,颗粒开始破坏,产生裂纹,引起复合 材料变形,有:
i p D p /(Gmb)
2
Gபைடு நூலகம் C
•
因此颗粒增强复合材料的屈服强度为:
0 L E f f V f Em m (1 V f )
纤维承受载荷与基体承受载荷之比为:
Pf / Pm E f f V f / Em m (1 V f ) E f V f / Em (1 V f )
Ef • 当Vf一定时, E m 比越大,纤维承受载荷越 大,增强作用就越大。因此复合材料要采用高 强度、高模量的增强纤维,而基体用低强度、 低模量的材料,但基体韧性要好 Ef Em • 当 值一定时, Vf值越大,纤维贡献越大。 理论计算Vf最大可达0.9069,但实际Vf大于 0.80时,复合材料的强度不但不随纤维含量的 增大,反而下降。这是因为纤维太多,没有足 够的基体去润湿和渗入纤维,造成纤维粘结不 好,有空隙,因此强度不高。实际使用体积分 数为0.3~0.6。
bm mT bm m mL bm
L Lb m mL bm f fLbf
• 假设纵向应变协调,纤维和基体应变相等,且等于复合材料纵向应变, 即:
L mL fL
• 所以有
Lb mbm f b f
• 即:
L mVm f V f m (1 V f ) f V f
3GmG p bVp
1 2
1 2
y •颗粒增强复合材料强度增强率: Fp m
2d (1 V p )C
/ m
•在分散强化和颗粒增强复合材料中,强度增强率与质点或颗粒体积分 数、直径及其分布有关,一般说,质点越细,增强率F越大。分散强化 时,质点尺寸在0.1~0.01微米时,F=4~15。质点再细就容易形成固溶 体,质点较大,在0.1~1微米时,F=1~3,增强效果不明显:主要质 点尺寸在此范围内易产生应力集中,强度下降。