振动分析技术
电厂设备检修的振动分析与诊断

电厂设备检修的振动分析与诊断在电厂中,设备的正常运行对于稳定供电和生产效率至关重要。
然而,随着设备的不断使用和老化,振动问题逐渐成为电厂运行中的一个主要隐患。
振动分析与诊断技术的应用可以及时发现设备的故障,并采取相应的维修措施,从而保障设备的可靠运行。
本文将介绍电厂设备检修中的振动分析与诊断技术,并探讨其应用的重要性和优势。
一、振动分析与诊断的基本原理振动分析与诊断是一种通过观察和分析设备的振动信号,来判断设备是否处于正常工作状态的技术。
其基本原理是,设备在正常运行时会产生一定的振动,而当设备出现故障时,其振动信号会发生变化。
通过检测和分析振动信号,可以判断设备的故障类型和程度,以便及时采取维修措施。
二、振动分析与诊断在电厂设备检修中的应用1.故障预测与预防通过对设备的振动信号进行实时监测和分析,可以发现故障的早期迹象,从而提前进行维修,避免故障进一步扩大和影响电厂的正常运行。
振动分析与诊断技术可以帮助电厂实现故障预测与预防,提高设备的可用性和可靠性。
2.故障诊断与维修当设备出现故障时,振动分析与诊断技术可以帮助确定故障类型和程度。
通过对振动信号的频谱分析、时域分析和统计特征分析,可以准确地判断设备的故障来源,为维修提供指导。
同时,振动分析与诊断技术还可以评估设备的维修效果,并监测设备的健康状况,以便及时调整维修计划。
3.设备性能监测与优化振动分析与诊断技术可以用于监测设备的运行状况和性能参数。
通过对振动信号的分析,可以获取设备的运行状态、轴承磨损情况、叶片失衡等信息,从而优化设备的运行参数,提高设备的工作效率和能耗性能。
三、振动分析与诊断技术的优势1.非侵入性振动分析与诊断技术可以通过传感器对设备的振动信号进行监测,无需对设备进行拆解或改造。
这一优势使得检修过程更加简便,同时也减少了对设备正常运行的干扰。
2.准确性高振动分析与诊断技术通过对振动信号的分析,可以准确地判断设备的故障类型和程度。
与传统的检修方法相比,振动分析与诊断技术具有更高的诊断准确性,并且可以实现对设备的实时监测和在线诊断。
管道系统的流固耦合振动分析与振动控制

管道系统的流固耦合振动分析与振动控制管道系统中的流固耦合振动是一种常见的动力学现象,对于系统的安全性和可靠性具有重要影响。
因此,对管道系统的流固耦合振动进行分析和控制是非常必要的。
本文将介绍管道系统的流固耦合振动的基本原理、分析方法和振动控制技术,并分析其在实际应用中的一些问题和挑战。
一、流固耦合振动的基本原理管道系统的流固耦合振动是指在流体通过管道时,由于流体与管道壁之间的相互作用,产生的流固耦合振动。
其基本原理可以通过流体力学和结构力学的分析来解释。
在流体力学方面,流体在管道中流动时会产生压力波动,这些波动会传播到整个管道系统中,引起管道壁的振动。
而在结构力学方面,管道壁的振动会引起流体内部的压力波动,形成一个闭环的流固耦合振动系统。
二、流固耦合振动的分析方法为了对管道系统的流固耦合振动进行准确的分析,可以采用两种主要的方法:数值模拟和实验测试。
1. 数值模拟方法数值模拟方法是通过数学建模和计算机仿真来模拟管道系统的流固耦合振动。
其中,计算流体力学(CFD)方法可以用来模拟流体流动,有限元法(FEM)可用于模拟管道振动。
通过将这两种方法耦合起来,可以得到较为准确的流固耦合振动特性。
2. 实验测试方法实验测试方法是通过搭建实验平台来进行流固耦合振动的测试。
通过在实验平台上设置不同的工况和参数,可以获取管道系统的振动响应。
常用的测试方法包括压力传感器、加速度传感器等。
通过实验测试,可以获取系统的振动特性,并验证数值模拟结果的准确性。
三、振动控制技术为了降低管道系统的流固耦合振动,需要采取一些有效的控制手段。
目前常用的振动控制技术有两种:被动控制和主动控制。
1. 被动控制技术被动控制技术主要包括减振器和阻尼材料的应用。
减振器可以通过改变系统的固有频率或阻尼特性来吸收振动能量,从而减小振动幅值。
阻尼材料可以通过吸收或传导振动能量来减小系统的振动响应。
2. 主动控制技术主动控制技术则是通过在系统中添加控制器和执行器来主动调节系统的振动响应。
振动分析技术在故障诊断中的应用

0机械 与电子 0
S IN E&T C N L G IF R A I N CE C E H O O Y N O M TO
21 0 0年 第 1 期 7
振动分析技术在故障诊断中的应用
曹 海江 ( 宝钢 集 团八钢 公 司能源 中心 新疆 乌 鲁木 齐 8 02 3 0 2)
线 80线 , 集 时 风 机 实 际转 速 在 5 6 r n左 右 波 动 , 机 的 转 频 f 0 采 0 0/ mi 风
约在 8 .3H 。频 谱 如 下 : 43 z
1 机 组 结构 及 参 数
1 ●
^
■
鼓 风 机 机 组结 构 为 电 机— — 齿 式 联 轴 器 — — 液 力 偶 合 器—; == k —二 .二 . 齿 式 联 轴 器— — 风 机 。 电机 功 率 :0 0 W , 速 :9 9/ i 液 力 偶 合 50k 转 2 8 r n, m ~== _ = = 一 器 为 增 速 型液 力 偶 合 器 , 出 可 达 5 0 ̄mi; 机 型 号 : 10 28 输 2(/ n 风 D10 — ./
水 平
19 . 22 .
备 注 靖 垂 直 萋
l3 _ 1 . 2
4 检 修 验 证
一
+对查 。风 机 自
由端 滑 动 轴 承正 常 。复 合 端 滑 动 轴 承 下 瓦损坏 , 瓦面 上 有 明显 的摩 擦 痕 迹 , 承 轴
一 ~ 越 _ . 舞 . 一 一
0 ‘
通过 数 据 采 集 对 该 风 机 复 合 端 振动 所 反 映 的 特征 信 号 分 析 , 集 采
时 观 察 可 明 显 看 出 振 动 稳 定 性 差 , 向 波 动 尤 为 明显 ; 个 方 向 上 的 径 三
振动诊断技术综述

振动诊断技术综述振动诊断技术可以追溯到19世纪初期的机械故障排除。
随着科学技术的不断发展,振动诊断技术也得到了迅速发展。
振动诊断技术是利用机械振动信号分析技术,对机器设备的故障状态进行判别和诊断的一种方法。
它是一种非常常见的无损检测方法,可以帮助工程师及时发现机器设备的故障,回避严重的后果。
振动诊断技术可以根据不同的应用和场合,分成不同的分类。
第一种分类是定期振动检测。
这种检测方法是针对机器设备定期进行振动检测,来确定它们的运行状态。
这种方法通常可以通过记录并分析机器设备的振动信号来识别故障信息。
如果振动信号发生了变化,就可以通过分析变化的振动信息来诊断出设备的故障。
第二种分类是故障诊断。
这种方法主要是针对机械故障诊断做出的。
它可以通过分析机械振动信号来判断机械设备是否发生故障,故障类型以及故障严重程度。
通过对振动信号的分析,我们可以确定故障的类型,然后根据类型来采取针对性的措施。
第三种分类是状态监测。
这种方法可以说是振动诊断技术中最重要的一种应用。
它可以检测设备的运行状态,预测故障的发生以及判断是否需要进行保养维护。
通过状态监测,设备的寿命可以被大大延长,同时节省了维护成本。
振动诊断技术是复杂的技术系统,其中包括了很多不同的技术方法。
它涉及到机械振动、材料力学、信号处理、人工智能等多个领域知识。
从振动检测、故障诊断到状态监测,振动诊断技术依赖于多种技术手段支持,必须在实践中尝试和实施。
总之,振动诊断技术在现代工程中发挥着至关重要的作用。
它可以保障设备的安全可靠,提高生产效率和质量,减少维护成本以及环保化产业。
因此,振动诊断技术将会越来越普及和深入到现代工程中。
火电厂汽轮机常见的振动故障分析及故障诊断技术
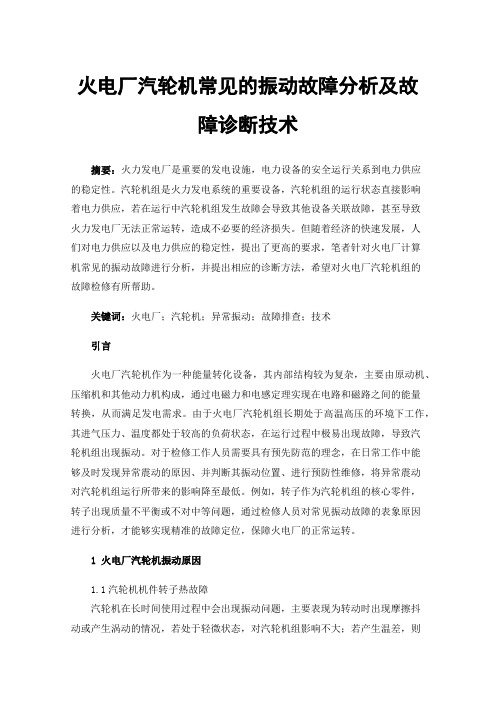
火电厂汽轮机常见的振动故障分析及故障诊断技术摘要:火力发电厂是重要的发电设施,电力设备的安全运行关系到电力供应的稳定性。
汽轮机组是火力发电系统的重要设备,汽轮机组的运行状态直接影响着电力供应,若在运行中汽轮机组发生故障会导致其他设备关联故障,甚至导致火力发电厂无法正常运转,造成不必要的经济损失。
但随着经济的快速发展,人们对电力供应以及电力供应的稳定性,提出了更高的要求,笔者针对火电厂计算机常见的振动故障进行分析,并提出相应的诊断方法,希望对火电厂汽轮机组的故障检修有所帮助。
关键词:火电厂;汽轮机;异常振动;故障排查;技术引言火电厂汽轮机作为一种能量转化设备,其内部结构较为复杂,主要由原动机、压缩机和其他动力机构成,通过电磁力和电感定理实现在电路和磁路之间的能量转换,从而满足发电需求。
由于火电厂汽轮机组长期处于高温高压的环境下工作,其进气压力、温度都处于较高的负荷状态,在运行过程中极易出现故障,导致汽轮机组出现振动。
对于检修工作人员需要具有预先防范的理念,在日常工作中能够及时发现异常震动的原因、并判断其振动位置、进行预防性维修,将异常震动对汽轮机组运行所带来的影响降至最低。
例如,转子作为汽轮机组的核心零件,转子出现质量不平衡或不对中等问题,通过检修人员对常见振动故障的表象原因进行分析,才能够实现精准的故障定位,保障火电厂的正常运转。
1 火电厂汽轮机振动原因1.1汽轮机机件转子热故障汽轮机在长时间使用过程中会出现振动问题,主要表现为转动时出现摩擦抖动或产生涡动的情况,若处于轻微状态,对汽轮机组影响不大;若产生温差,则会导致转子变形,此时转子呈不平衡运转状态,汽轮机组振动幅度明显提升。
产生此问题的主要原因是受热机件在安装过程中不够精准,未按照标准规范要求进行检测,导致部件受热不均衡,出现膨胀或变形等情况,转子运转失衡而产生振动。
在维修过程中,可通过更换磨损机件配件、调效间隙,减少轴位与密封位置摩擦[1]。
非线性振动分析技术在机械工程中的应用研究

非线性振动分析技术在机械工程中的应用研究随着科技的不断发展,机械工程领域也在不断更新迭代。
其中非线性振动分析技术便是其中一个不可或缺的环节。
本文将探讨非线性振动分析技术在机械工程中的应用研究。
一、非线性振动分析技术的简介非线性振动分析技术是指当系统从平衡位置发生微小偏移时,反映系统不同部位之间相互作用出现的非线性现象。
与传统线性振动不同,非线性振动分析技术具有涉及到的电子、力学、材料科学、流体力学、大气科学等众多领域,可谓是一门跨学科的学科。
非线性振动分析技术广泛应用于车辆、飞机、船舶、机械、电子等领域。
其中机械工程中的应用最为广泛。
二、非线性振动分析技术在机械工程中的应用非线性振动分析技术在机械工程中的应用主要包括三个方面:非线性动力学分析、非线性振动信号处理和非线性振动控制。
1. 非线性动力学分析非线性动力学分析是指对非线性系统进行振动分析的过程,非线性振动分析技术在其中占有重要的作用。
非线性振动分析技术能够帮助工程师研究和预测系统的稳定性、振动响应和运动轨迹等。
例如,非线性振动分析技术在发动机机械系统中的应用,能够帮助工程师在研究基础振动、振动传递路径、非线性振动及其控制等方面得到很好的支撑。
2. 非线性振动信号处理非线性振动信号处理是指通过非线性振动信号的分析、处理,从中提取出有效信息的方法。
非线性振动信号处理的目的是为了实现故障诊断和预测。
非线性振动信号处理技术可以应用于飞机、管线、轴承等系统的故障诊断。
与传统线性信号处理技术相比,非线性信号处理技术更加适用于复杂系统中故障的诊断。
3. 非线性振动控制非线性振动控制是指通过控制技术,在系统发生非线性振动时,通过控制振动的幅值、频率和相位,以达到改善机械设备运行效果的目的。
非线性振动控制的主要方法有磁流变阻尼器、主动振动控制、阻尼跳跃等。
三、非线性振动分析技术在今后的应用前景随着科技的不断发展,非线性振动分析技术将在未来得到更加广泛的应用。
机械振动分析技术在故障预测中的应用案例
机械振动分析技术在故障预测中的应用案例引言:故障预测是机械维护和设备管理的重要组成部分,通过分析机械振动数据可以提前发现故障迹象,预测设备的运行状态。
机械振动分析技术可以帮助企业提高设备可靠性,降低维修成本,提高生产效率。
本文将介绍两个机械振动分析技术在故障预测中的应用案例,分别是基于时域分析和频域分析的方法。
案例一:基于时域分析的机械故障预测方法背景:某工厂的离心泵是生产装置中的关键设备,但近期频繁出现故障,造成生产中断和高额维修费用。
为了提前发现故障迹象,降低故障率,工厂决定采用机械振动分析技术。
方法:1. 数据采集:工程师安装加速度计和振动传感器,定期采集泵的振动数据。
2. 时域分析:将采集到的振动数据进行时域分析,计算出振动信号的包络谱和时域波形图。
3. 故障诊断:通过对包络谱和时域波形图的分析,识别泵的故障迹象,并查找可能的故障源。
4. 故障预测:根据故障迹象和振动特征,建立故障预测模型,并对未来的振动数据进行预测。
结果:经过分析和诊断,工程师发现泵的轴承存在严重的磨损,可能导致泵的故障。
根据振动数据建立的故障预测模型预测了轴承的寿命,并提出了维修建议。
工厂按照建议进行维修,成功地避免了设备故障和生产中断。
案例二:基于频域分析的机械故障预测方法背景:某电力公司有一台重要的汽轮发电机组,但近期出现了振动异常的情况,令人担忧。
为了保证发电机组的安全运行,电力公司决定采用机械振动分析技术。
方法:1. 数据采集:工程师使用振动传感器采集发电机组的振动数据,并记录下来。
2. 频域分析:将振动数据转化为频域信号,进行频谱分析,得到频谱图和频域特征。
3. 故障诊断:通过对频谱图和频域特征的分析,识别异常振动的频率和幅值,并与故障手册中的故障特征进行对比。
4. 故障预测:根据异常振动频率和幅值的变化趋势,预测发电机组的故障类型和发展趋势。
结果:经过分析和诊断,工程师发现发电机组的转子存在磨损,导致了振动异常。
设备故障诊断技术
设备故障诊断技术设备故障诊断技术是指通过专业的技术手段,对设备出现的故障进行系统性的分析和解决的过程。
设备故障是一种常见的问题,尤其是在工业生产等领域中,设备故障对生产效率和生产成本都会产生很大的影响,因此设备故障诊断技术的研究越来越受到重视。
设备故障诊断技术主要包括以下几个方面:1.性能测试技术设备故障往往与设备性能的变化有关,通过对设备的性能进行测试,可以进一步确定设备的工作状态和故障原因,以及应采取的措施。
例如运用振动分析技术、噪音分析技术、热测量技术、红外成像技术等一系列技术手段,可以比较准确地判断出设备的故障原因。
2.数据采集技术通过数据采集技术,可以收集实时的设备数据,对设备进行在线监测和故障诊断,有效提高设备可靠性和增强设备运行效率。
例如运用传感器、计算机网络、通信技术等手段,可以实现网络化的数据采集和处理,对设备的状态进行实时监测,并对设备故障提供相应的预警和报告。
3.故障诊断系统故障诊断系统是一种基于专家系统、模糊控制和人工智能技术的工具,可用于快速分析和判断设备的故障原因,并提供相应的维修方案。
例如运用模糊排序法、神经网络算法等技术,可以从大量的故障信息中快速确定故障原因和维修方案。
4.可靠性工程技术可靠性工程技术是一种将可靠性设计理论与实际生产相结合的技术,通过在设计过程中考虑设备的健康状况、维护需求等因素,提高设备的可靠性和生命周期维护成本,并降低设备的故障率和停机时间。
例如运用良好的设计原则、可靠性模型、故障树分析等方法,可以快速识别和排除设备的故障原因。
综上所述,设备故障诊断技术是一个复杂而重要的领域,需要多种技术手段相互配合,才能够有效的解决设备故障的问题,提高设备的可靠性和生产效率。
同时,为了应对不断发展和变化的市场需求和技术创新,我们还需要不断加强故障诊断技术的研究和应用,开发出更加先进和有效的工具和技术,为人们的生活和生产提供更加便捷和可靠的服务。
随着科学技术的快速发展和应用范围的不断扩大,各行各业的设备故障问题也日益增多。
利用振动分析诊断设备故障与性能问题
利用振动分析诊断设备故障与性能问题振动是各类机械设备中常见的现象,因此利用振动分析技术诊断设备故障和性能问题已经成为重要的手段之一。
通过观察和分析设备的振动情况,可以提前发现潜在的故障,及时采取措施进行维修,从而避免设备损坏和生产中断。
本文将从设备故障与性能问题的振动特征、振动分析技术和振动诊断方法三个方面进行阐述。
设备故障与性能问题的振动特征当设备运行时,由于内部部件的摩擦、不平衡等原因,会产生振动。
不同故障和问题引起的振动特征各不相同。
例如,当设备存在轴承问题时,会出现低频振动,而齿轮问题则会引起高频振动。
同时,设备故障还会导致振动的幅值、频率和相位发生变化。
通过分析振动的幅值、频率和相位的变化规律,可以准确判断设备的故障和性能问题,并针对性地采取相应的维修措施。
振动分析技术振动分析技术是一种通过检测和分析设备振动信号,以获取装置性能和故障状况信息的方法。
常见的振动分析技术主要包括频谱分析、时域分析和相位分析。
频谱分析是将振动信号变换到频域的一种方法,通过计算振动信号在不同频率上的幅值,可以得到频谱图。
频谱图能够清晰地展示不同频率的振动成分,帮助我们判断设备存在的故障和问题。
时域分析是对振动信号进行时间上的分析。
通过分析振动信号的波形、脉冲和振幅等特征,可以判断出设备的运行状态、异常情况以及故障。
相位分析是分析振动信号中不同频率分量的相位差。
相位差的变化能够反映设备不同部分之间的相对运动情况,从而帮助我们判断设备是否存在问题。
振动诊断方法针对不同的设备故障和性能问题,可以采用不同的振动诊断方法进行分析和判断。
对于轴承故障,可以通过测量设备振动信号的幅值和频率变化来判断故障的类型和程度。
同时,可以使用频谱分析技术,观察振动信号在波形上的特点,比如是否存在阻尼振动或失谐振动等。
对于齿轮故障,可以利用振动信号频谱分析技术,检测高频振动的频率和幅值变化,判断齿轮是否存在磨损、断齿、断裂等问题。
除了频谱分析外,时域分析也是一种常用的方法。
振动光谱法 ir
振动光谱法 ir振动光谱法(infrared spectroscopy,简称IR)是一种常见的物质分析技术,使用红外线光谱仪对样品进行分析,通过样品中分子振动引起的红外辐射频率与强度变化,可以确定分子的结构、成分和化学键。
本文将介绍IR 的基本原理、仪器构造、与其他分析技术的比较,以及在实际应用中的一些限制和优缺点等方面。
一、基本原理 IR的基本原理是利用样品中吸收的红外光谱来分析样品的成分及化学键信息。
IR的样品通常为固、液、气三种形态。
当样品吸收辐射能量后,分子振动状态发生变化,产生特征的红外光谱。
样品在光路上必须处于红外区间,通常范围为4000~400 cm-1。
IR的波长在红外区间,紫外后,波长范围为7000—200 cm-1,对应频率范围为1.4286 ~ 50 THz。
IR不仅能够探测样本中化学键的振动,还能够确定化学键的位置和取代基的数量和类型等。
二、仪器构造 IR光谱仪是将样品放在一个光学窗口上,透过红外光源(例如红外线灯,光栅分光仪等),选定特定波长,在搭配检测器,如DTGS探测器,采集样品光谱光强信号曲线,再通过软件处理,得到样品完整的振动光谱图。
IR光谱仪是一种相对比较简单的设备,由样品盘、光源、分光机构、检测器和光谱获取装置组成。
其中分光机构包括光源、分光器和检测器。
光源一般是一种强度稳定的红外辐射源,并具有波长选择性。
分光器用于将红外光按波长分解成不同的光谱线。
检测器通常使用热电电应动器(TEA)或红外线探测器,以检测不同频率的红外光。
三、与其他分析技术的比较与其他分析技术相比,IR 具有以下优点:1. 非破坏性:在IR分析中,样品不会被破坏或损坏,可以反复使用,不会造成浪费。
2. 快速、方便:IR分析是一种快速、高效、非常方便的分析技术,只需很少的样品量(纳克级至毫克级),分析时间短(一般几秒到几分钟),操作简单,样品准备也很容易。
3. 用途广泛:IR分析广泛应用于生命科学、化学和材料科学等领域,可用于分析各种类型的样品,包括无机和有机,固体和液体以及气态。