聚晶拉丝模具和硬质合金拉丝模具的性能对比
金刚石性能介绍

书山有路勤为径,学海无涯苦作舟金刚石性能介绍金刚石在自然界材料中具有特别优异的机械性能、热学性能、透光性、纵波声速、半导体性能及化学惰性,是一种全方位的不可替代的特殊多功能材料。
用化学气相沉积(Chemical Vapor Deposition 简称CVD)方法生长的金刚石膜具有与颗粒状天然金刚石和高压人造金刚石几乎完全相同的性能,但却克服了小颗粒状天然金刚石和高压人造金刚石尺寸大小的限制。
材料学家一致认为只有这种连续性大尺寸块状材料,才能使得金刚石全部优异性能得到充分的发挥。
金刚石膜的优异性能主要表现在以下几个方面: 1.机械性能:金刚石在已知材料中硬度最高(维氏硬度可达10,400kg/mm2 本站注:约合102GPa)、耐磨性最好且摩擦系数极低。
CVD 金刚石膜中不含任何粘结剂,其多晶结构又使其在各个方向具有几乎相同的硬度,且没有解理面,因此其综合机械性能兼具单晶金刚石和聚晶金刚石(PCD)的优点,而在一定程度上又克服了它们的不足,而且价格低廉。
它不仅可代替天然金刚石、高压人造单晶金刚石和聚晶金刚石在机械领域应用而且大大拓宽了其应用范围:如制造各种适合拉制软硬丝的高性能拉丝模具;焊接型CVD 金刚石工具(使用寿命超过PCD 工具的1-3 倍);制作形状较为复杂的CVD 金刚石涂层硬质合金刀具(使用寿命比涂层前提高10-50 倍);其低摩擦系数还可用于摩擦部件如轴承的耐磨涂层等。
据国外专家统计,仅应用于超硬材料方面就可以开发、改造出二千多种新产品。
2.声学性能:金刚石在所有材料中的传声速度最快,为18.2km/s。
利用此性能不仅能制作频率响应超过5GHz 的声表面波器件(这种最高频响声表面波器件在通信领域的应用极其广泛)而且还可制作频响达60kHz 以上的超高保真扬声器及性能最优异的声传感器。
3.热学性能:天然金刚石热导率达20W/cm.K, 为所有物质中最高者, 比SiC 大4 倍, 比Si 大13 倍, 比GaAs 大43 倍, 是Cu 和Ag。
铜线拉丝工艺理论知识

PPT文档演模板
铜线拉丝工艺理论知识
铜导体为什么需要退火软化处理?
• 电线电缆导体经冷拔加工后,均存在硬化现象, 抗拉强度和屈服强度明显增加,塑性和韧性普遍 降低,伸长率的变化尤为显著。欲消除冷拔硬化 现象,提高延伸率,就必须进行退火处理,以消 除内部应力及缺陷,使之恢复到冷加工前的物理 及机械性能。如铜导体经550℃退火处理后,导线 柔软,不易被拉断。同时,导体的电阻率降低约 2.1%,减小了线路损耗。因此,退火软化是电线 电缆及漆包线生产过程的主要环节之一。
1.3 建议:由于真空退火炉工艺落后,能耗大,产品质 量不稳定,生产成本高,市场竞争能力低,建议尽 快淘汰真空退火炉。
PPT文档演模板
铜线拉丝工艺理论知识
2 热管式退火炉
热管式退火炉 也是比较传统的 退火工艺,其设 备的结构示意图 如图2所示。它 主要有:不锈钢 管、加热棒、测 温热电偶、冷却
水及导轮组成。
•导轮 •放线盘
•加热棒
•退火不锈钢管 •导轮
•收线盘
•冷却水
•图2 管道式退火炉结构示 意图
PPT文档演模板
铜线拉丝工艺理论知识
2 热管式退火炉
• 2.1 优点:技术简单,设备简陋,设备投资低,对 操作人员要求低,能够实现多头退火。
• 2.2 缺点:耗电量大,退火一吨铜丝耗电在225度 电以上;无法实现退火速度自动跟踪;穿线麻烦, 设备庞大。
垫、固定螺栓等组成。
•图1 真空退火炉结构示 意图
PPT文档演模板
铜线拉丝工艺理论知识
1 真空退火炉
1.1优点:技术简单,设备简陋,设备投资 低,对操作 人员要求低。
1.2缺点:耗电量大,退火一吨铜丝耗电在230度电以 上;生产工艺不稳定,一旦漏气全炉均会氧化变色; 真空炉内的上下、左右温度不均匀,会出现内外电 线软硬不均,更有甚者,还会出现电线粘连现象; 不能在线连续退火,且退一罐线的周期太长。
铜拉丝退火上引讲义

特变电工(德阳)电缆股份有限公司铜上引拉丝退火工序讲义技术中心2007年7月18日铜上引工序一、 铜杆生产方法及性能比较1、铜杆生产方法a. 传统方法轧制定义:将铜锭通过加热炉加热,再经过轧机的轧辊反复轧制延伸成形而最后得到一定规格形状的铜杆。
这种加工方法称为轧制。
特点:生产效率高,废品废料少,内部质量好。
适于简单截面金属制品的批量生产。
工艺流程:铜锭—加热—粗轧—中精轧—绕杆—堆装—成品检验b. 连铸连轧生产铜杆工艺流程:电解铜—加料—竖炉—上流槽—保温炉—下流槽—浇煲—铸机—夹送辊—剪切机—坯锭预处理—轧机—清洗冷却管道—涂蜡—成圈—包装。
c. 浸涂法原理:利用冷铜杆吸热的能力。
用一根较细的冷纯铜芯杆或称种子杆,垂直通过一直能保持一定液位高低的铜水池(坩埚),坩埚内铜水与该移动的种子杆表面铜熔合在一起,并逐步凝固成较粗的铸态铜杆。
特点:含氧量低(2~18),具有无氧铜杆的优点,即柔软、工艺性能好、无氢脆、耐高温、可焊性优良、无氧化颗粒、导电率高、表面清洁、长度大、晶粒小等特点。
d. 上引连铸法 轧辊轧件是“多头连铸”生产铜杆方法中较为成功的一种。
最早是芬兰于1970年研制成功,实现了在一台设备上同时装12个头子,年生产能力12000t铜杆。
这种连铸系统不仅能生产铜杆,还可生产各种有色金属及合金杆棒,甚至生产空芯导线以及各种型材。
工艺原理:将结晶器下端伸入并浸没在熔化铜液面下,上端与真空泵连通,开始时将结晶器内空气抽出,在真空作用下,使管内产生负压,铜液被徐徐吸引向上,并在引升器附近很快凝固成光亮铸坯,铸杆尺寸决定于结晶器内径。
结晶后的铸杆,通过牵引轮慢慢地将铜杆从结晶器内提升出来,经过弧形拐弯轮至绕杆机收绕成圈。
工艺流程:电解铜—熔化炉—流槽—保温炉—连铸机—成圈机。
控制部分:熔化炉铜液由液压系统控制,保温炉内铜液液位用标尺显示,铜液温度由热电偶测温仪表显示,石墨模由跟踪装置使其保持一定的位置。
超硬材料及制品的基本知识

超硬材料及制品基本知识一、超硬材料概念:对于超硬材料的含义至今没有一个公认为满意的解释。
1981 年国际硬物质科学会议认为,硬度大于 1000HV 的物质均可称为硬物质,这就自然包括了金刚石和立方碳化硼。
后来对这个定义进行了补充,认为能加工诸如硬质合金(硬度 1600—1800HV )、刚玉(—2000HV)、碳化硅(—2200HV)等这一类物质的材料称为超硬材料。
目前由于金刚石和立方氮化硼等材料有其极高的硬度,所以统称为超硬材,具有硬度高、耐磨和热传导性能好、热膨胀系数低等优异性能。
二、超硬材料的分类:分为单晶超硬材料和聚晶超硬材料(也称为“复合超硬材料”)及 3.金刚石薄膜三类。
单晶超硬材料和聚晶超硬材料的主要区别为:单晶金刚石/立方氮化硼材料的特点为硬度更高、耐热性更好,但尺寸较小,多用于制造锯片等切割工具;聚晶金刚石/立方氮化硼是指以金刚石和立方氮化硼微粉等单晶超硬材料为主要原料,添加金属或非金属粘结剂通过超高压高温烧结工艺制成的聚晶复合材料。
它的特点是硬度、耐热性略逊于单晶材料,但是由于聚晶超硬材料是内部结构紧密的金刚石致密体,可以增加工具的切割面积,同时克服了单晶超硬材料由于粘结面积小造成的轻易从锯片表面脱落的弊端,具有更高的耐磨性。
金刚石薄膜是用化学气相沉积(CVD)法或其它方法在非金刚石衬底上制备出的超硬薄膜。
它不仅可用于制作各种金刚石刀具,还可作为功能材料用于制作声传感器、扬声器振动膜、红外窗口、X 光检测窗口等,应用领域十分广泛。
国际上从七十年代初开始进行金刚石薄膜的试制并迅速掀起金刚石薄膜研究开发热潮。
我国从八十年代中期开始此项研究,并已列入国家“863 计划”,现已能制备出 80mm、厚 2mm 的金刚石薄膜,并在应用研究方面取得了不少成果,但目前总体上仍处于研制阶段,尚未达到工业化应用阶段。
有人预计,金刚石薄膜将是 21 世纪金刚石工业的主要材料,各国科学家都在为使金刚石薄膜产业化而不懈努力。
硬质合金基础知识

五、被加工材料分类及工具材料选择
P类:钢、钢铸件。如普通碳素结构钢(代码如Q235-A.F)、优质碳素结构
钢(如45钢、50锰、20G等)、碳素工具钢(如T7、T7A、T8、T8A、T13、 T13A等),切削牌号一般选择W—Co —Ti类合金,如YT5、YT14、YT15、 YT15R、YT05、YT30、YC101、YC201、YC301、YC45等;
地质矿山工具:地质矿山工具同样是硬质合金的一大用途。 我国地矿用硬质合金约占硬质合金生产总量的25%,主要用 于冲击凿岩用钎头,地质勘探用钻头、矿山油田用潜孔钻、 牙轮钻以及截煤机截齿、建材工业冲击钻等。
2014/9/23
模具:用作各类模具的硬质合金约占硬质合金生产总量的 8%,有拉丝模、冷镦模、冷挤压模、热挤压模、热锻模、 成形冲模以及拉拔管芯棒,如长芯棒、球状蕊棒、浮动蕊 棒等,近十几年轧制线材用各类硬质合金轧辊用量增速很 快,我国轧辊用硬质合金已占硬质合金生产总量的3%。 结构零件:硬质合金用来作结构零件的制品很多,如旋转 密封环、压缩机活塞、车床夹头、磨床心轴、轴承轴颈等。 耐磨零件:用硬质合金制成的耐磨零件有喷嘴、导轨、柱 塞、球、轮胎防滑钉、铲雪机板等举不胜举。 耐高压高温用腔体:最重要的用途就是生产合成金刚石用 的顶锤、压缸等制品,顶锤、压缸用硬质合金已占我国硬 质合金生产总量的9%。 其他用途:硬质合金用途越来越广,近几年已在民用领域 不断扩展,如表链、表壳、高级箱包的拉链头、硬质合金 商标等。
CrC、VC—抑制剂,抑制WC晶粒的长大。
2014/9/23
四、硬质合金分类
1. 根据成分不同,可将硬质合金分为5大类。 ① 碳化钨基硬质合金:包括WC-Co、WC-TiC-Co、WCTaC-Co、WC-TiC-TaC(NbC)-Co等。 这些合金均以 WC为主成分。
细钼丝聚晶拉丝模孔型参数的探讨

PARAM [ ETE RS oF F D E M oLYBDENUM W Ⅱt E S
H UANG Li—f e ng . L I S hi — we i , LI U Ba o—q i n g , BU Ch un— y a n g
Abs t r a c t : T h e p a s s p a r a me t e r c h a n g i n g o f in f e mo l y b d e n u m wi l " e re a d e t e c t e d b y CU 一1 0 I n s p e c t o r i n a c c o r d a n c e wi t h f a c t o r yg a c t u a l p r o c e s s i n g,s u c h a s c o mp r e s s i o n a n g l e,l e n g t h o f t h e s i z i n g re a a,o v li a t y,a nd e t c .T he n t h e b e s t o p e r a t — i n g s c o p e o f p a s s p ra a me t e r i s d e t e r mi n e d S O t h a t t h e d r a wi n g d i e s q u li a t y a n d o p e r a t i n g l i f e re a i mp r o v e d. Ke y wo r ds : mo l y b d e n u m wi r e; d r a wi ng d i e; c o mp r e s s i o n a n g l e; s i z i n g a r e a; o v a l i t y
硬质合金刀具材料性能和特点
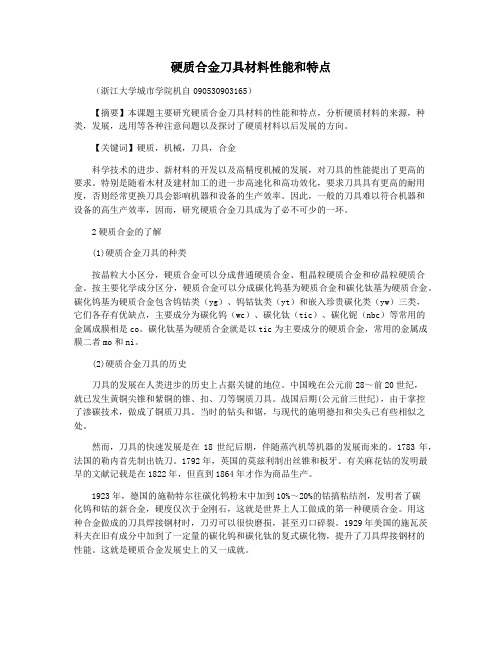
硬质合金刀具材料性能和特点(浙江大学城市学院机自************)【摘要】本课题主要研究硬质合金刀具材料的性能和特点,分析硬质材料的来源,种类,发展,选用等各种注意问题以及探讨了硬质材料以后发展的方向。
【关键词】硬质,机械,刀具,合金科学技术的进步、新材料的开发以及高精度机械的发展,对刀具的性能提出了更高的要求。
特别是随着木材及建材加工的进一步高速化和高功效化,要求刀具具有更高的耐用度,否则经常更换刀具会影响机器和设备的生产效率。
因此,一般的刀具难以符合机器和设备的高生产效率,因而,研究硬质合金刀具成为了必不可少的一环。
2硬质合金的了解(1)硬质合金刀具的种类按晶粒大小区分,硬质合金可以分成普通硬质合金、粗晶粒硬质合金和矽晶粒硬质合金。
按主要化学成分区分,硬质合金可以分成碳化钨基为硬质合金和碳化钛基为硬质合金。
碳化钨基为硬质合金包含钨钴类(yg)、钨钴钛类(yt)和嵌入珍贵碳化类(yw)三类,它们各存有优缺点,主要成分为碳化钨(wc)、碳化钛(tic)、碳化铌(nbc)等常用的金属成膜相是co。
碳化钛基为硬质合金就是以tic为主要成分的硬质合金,常用的金属成膜二者mo和ni。
(2)硬质合金刀具的历史刀具的发展在人类进步的历史上占据关键的地位。
中国晚在公元前28~前20世纪,就已发生黄铜尖锥和紫铜的锥、扣、刀等铜质刀具。
战国后期(公元前三世纪),由于掌控了渗碳技术,做成了铜质刀具。
当时的钻头和锯,与现代的施明德扣和尖头已有些相似之处。
然而,刀具的快速发展是在18世纪后期,伴随蒸汽机等机器的发展而来的。
1783年,法国的勒内首先制出铣刀。
1792年,英国的莫兹利制出丝锥和板牙。
有关麻花钻的发明最早的文献记载是在1822年,但直到1864年才作为商品生产。
1923年,德国的施勒特尔往碳化钨粉末中加到10%~20%的钴搞粘结剂,发明者了碳化钨和钴的新合金,硬度仅次于金刚石,这就是世界上人工做成的第一种硬质合金。
金刚石涂层

化学气相沉积法制备金刚石涂层金刚石是硬度最高的固体物质(HV= 100GPa),性质稳定,耐磨,但却难以加工成各种所需的零件和制品。
采用气相沉积法制备金刚石涂层,可以使金刚石性质得以从分利用,同时也节约了成本。
下面以金刚石涂层拉拔模具的制备为例,简单介绍化学气相沉积法金刚石涂层的制备方法。
金属线材行业是我国的主要传统产业,而金属线材生产企业重要的易消品就是拉拔模具,其使用方式如图1所示,拉拔模具的性能决定了金属线材的质量、生产效率和生产成本。
目前线材行业所用的模具主要为硬质合金模具和聚晶金刚石模具两大类。
硬质合金模具寿命短,易粘料,生产效率低;聚晶金刚石模具价格高,制作较大尺寸模具和异形模具非常困难,且韧性较差。
本文应用化学气相沉积(chemicMvaperdepsdition,CVD)金刚石涂层技术,制成金刚石涂层拉拔模具,克服了硬质合金拉拔模具不耐磨和聚晶金刚石拉拔模具韧性较差的缺点,成为新一代的拉拔模具。
金刚石涂层拉拔模具的制备过程:金刚石涂层拉丝模具是以YG6硬质合金模具为基体,经过特殊的表面处理后,用气相沉积方法,在硬质合金拉丝模具基体工作区域表面沉积10—30p,m的多晶金刚石膜。
经修整、抛光、镶套后制作成成品,具体过程如图2所示。
(1)准备工作选择YG6牌号硬质合金模具,坯料孔型和尺寸与所要制备的成品模具相适应,通过内孔研磨修整工艺将模具坯料修整为合适的形状,预留30u m 左右的尺寸余量,以配合涂层厚度尺寸。
将修整完毕的硬质合金模具进行喷砂处理,去除表面的污染物和疏松层,再使用蒸馏水、酒精在超声波清洗机中清洗。
最后将模具在配制好的酸、碱液中进行表面腐蚀处理,并采用蒸馏水、酒精超声波清洗,完毕后将试件装入自制的热丝CVD金刚石沉积设备中。
(2)涂层沉积通人H2和CH4,将热丝加热至2500℃左右,调节气体流量、热丝温度、气压、基体温度等工艺参数,使模具表面沉积厚度约40 um的金刚石膜,制成金刚石涂层拉拔模具。
- 1、下载文档前请自行甄别文档内容的完整性,平台不提供额外的编辑、内容补充、找答案等附加服务。
- 2、"仅部分预览"的文档,不可在线预览部分如存在完整性等问题,可反馈申请退款(可完整预览的文档不适用该条件!)。
- 3、如文档侵犯您的权益,请联系客服反馈,我们会尽快为您处理(人工客服工作时间:9:00-18:30)。
聚晶拉丝模具和硬质合金拉丝模具的性能对比
来源:特种电缆
与硬质合金相比,聚晶金刚石的抗拉强度仅为常用硬质合金的70%,但硬度是硬质合金的2.5倍。
这样,使得聚晶金刚石模比硬质合金模有更多的优点。
用聚晶金刚石制成的拉丝模耐磨性能好,内孔磨损均匀,抗冲击能力强,拉丝效率高。
因此目前聚晶金刚石模在金属线材拉拔行业中开始逐渐被重视。
与硬质合金模相比,使用聚晶金刚石模拉丝模具有以下明显的优点:
1. 拉拔效率高。
拉丝模在使用过程中必要的保养对拉丝模的使用寿命和线材的表面质量都非常重要,通常建议客户对聚晶金刚石拉丝模每24小时进行一次保养。
在24小时内聚晶金刚石拉丝模具的孔径变化小,拉拔出的线材线径变化率也很小。
对于整个生产过程来说,每一只拉丝模的线径压缩率都比较稳定,投入和产出的比值大。
2. 耐磨性好,寿命长。
聚晶金刚石拉丝模寿命约为硬质合金模的30~50倍,这样在拉拔过程中就不需要经常停机更换模具。
聚晶拉丝模孔径在单位时间内变化很小,拉拔出的线材尺寸变化小,这对卷筒绕丝非常有利。
一般拉拔出的线材缠绕圈数是固定的,若线材成品尺寸很快变大,缠绕圈数相对迅速减少,这就需要不断改变卷筒尺寸,不利于生产效率的提高。
3. 节约原材料。
如果拉制表面镀有金属的线材,停止拉拔过程中电镀过程并没有停止,这就导致正在电镀的线材表面电镀层厚度超标,重新开始拉拔时需将厚度超标的线材剪掉,造成极大的浪费,停机次数越多浪费越大。
采用聚晶金刚石模则可以大大减少这种浪费。
4. 减少劳动强度。
由于聚晶金刚石拉丝模寿命长,扩号慢,不需要经常更换模具,也不像用硬质合金拉丝模必须要时刻注意线材尺寸的变化,大大减少了工人的劳动强度,一个工人在生产过程中能兼顾4~5台拉丝机。