精馏节能技术
浅析化工精馏高效节能技术开发及应用
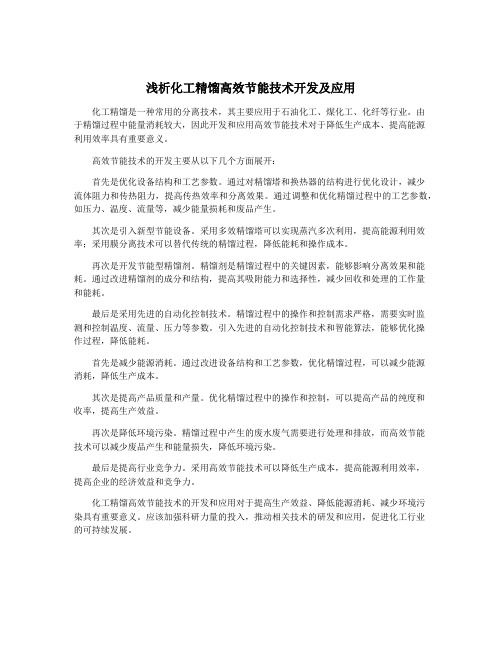
浅析化工精馏高效节能技术开发及应用化工精馏是一种常用的分离技术,其主要应用于石油化工、煤化工、化纤等行业。
由于精馏过程中能量消耗较大,因此开发和应用高效节能技术对于降低生产成本、提高能源利用效率具有重要意义。
高效节能技术的开发主要从以下几个方面展开:首先是优化设备结构和工艺参数。
通过对精馏塔和换热器的结构进行优化设计,减少流体阻力和传热阻力,提高传热效率和分离效果。
通过调整和优化精馏过程中的工艺参数,如压力、温度、流量等,减少能量损耗和废品产生。
其次是引入新型节能设备。
采用多效精馏塔可以实现蒸汽多次利用,提高能源利用效率;采用膜分离技术可以替代传统的精馏过程,降低能耗和操作成本。
再次是开发节能型精馏剂。
精馏剂是精馏过程中的关键因素,能够影响分离效果和能耗。
通过改进精馏剂的成分和结构,提高其吸附能力和选择性,减少回收和处理的工作量和能耗。
最后是采用先进的自动化控制技术。
精馏过程中的操作和控制需求严格,需要实时监测和控制温度、流量、压力等参数。
引入先进的自动化控制技术和智能算法,能够优化操作过程,降低能耗。
首先是减少能源消耗。
通过改进设备结构和工艺参数,优化精馏过程,可以减少能源消耗,降低生产成本。
其次是提高产品质量和产量。
优化精馏过程中的操作和控制,可以提高产品的纯度和收率,提高生产效益。
再次是降低环境污染。
精馏过程中产生的废水废气需要进行处理和排放,而高效节能技术可以减少废品产生和能量损失,降低环境污染。
最后是提高行业竞争力。
采用高效节能技术可以降低生产成本,提高能源利用效率,提高企业的经济效益和竞争力。
化工精馏高效节能技术的开发和应用对于提高生产效益、降低能源消耗、减少环境污染具有重要意义。
应该加强科研力量的投入,推动相关技术的研发和应用,促进化工行业的可持续发展。
精馏过程的节能途径及新型的精馏技术
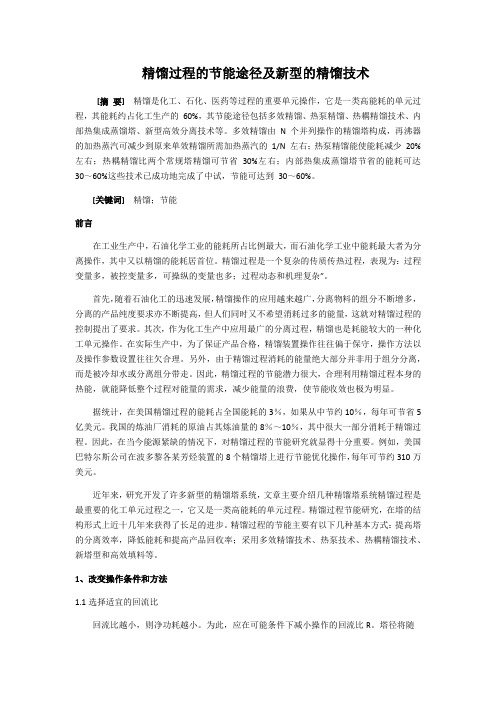
精馏过程的节能途径及新型的精馏技术[摘要]精馏是化工、石化、医药等过程的重要单元操作,它是一类高能耗的单元过程,其能耗约占化工生产的60%,其节能途径包括多效精馏、热泵精馏、热耦精馏技术、内部热集成蒸馏塔、新型高效分离技术等。
多效精馏由N 个并列操作的精馏塔构成,再沸器的加热蒸汽可减少到原来单效精馏所需加热蒸汽的1/N 左右;热泵精馏能使能耗减少20%左右;热耦精馏比两个常规塔精馏可节省30%左右;内部热集成蒸馏塔节省的能耗可达30~60%这些技术已成功地完成了中试,节能可达到30~60%。
[关键词]精馏;节能前言在工业生产中,石油化学工业的能耗所占比例最大,而石油化学工业中能耗最大者为分离操作,其中又以精馏的能耗居首位。
精馏过程是一个复杂的传质传热过程,表现为:过程变量多,被控变量多,可操纵的变量也多;过程动态和机理复杂”。
首先,随着石油化工的迅速发展,精馏操作的应用越来越广,分离物料的组分不断增多,分离的产品纯度要求亦不断提高,但人们同时又不希望消耗过多的能量,这就对精馏过程的控制提出了要求。
其次,作为化工生产中应用最广的分离过程,精馏也是耗能较大的一种化工单元操作。
在实际生产中,为了保证产品合格,精馏装置操作往往偏于保守,操作方法以及操作参数设置往往欠合理。
另外,由于精馏过程消耗的能量绝大部分并非用于组分分离,而是被冷却水或分离组分带走。
因此,精馏过程的节能潜力很大,合理利用精馏过程本身的热能,就能降低整个过程对能量的需求,减少能量的浪费,使节能收效也极为明显。
据统计,在美国精馏过程的能耗占全国能耗的3%,如果从中节约10%,每年可节省5亿美元。
我国的炼油厂消耗的原油占其炼油量的8%~10%,其中很大一部分消耗于精馏过程。
因此,在当今能源紧缺的情况下,对精馏过程的节能研究就显得十分重要。
例如,美国巴特尔斯公司在波多黎各某芳烃装置的8个精馏塔上进行节能优化操作,每年可节约310万美元。
近年来,研究开发了许多新型的精馏塔系统,文章主要介绍几种精馏塔系统精馏过程是最重要的化工单元过程之一,它又是一类高能耗的单元过程。
甲醇精馏技术应用和节能减排

甲醇精馏技术应用和节能减排1. 引言1.1 甲醇精馏技术概述甲醇精馏技术是一种高效的分离和净化甲醇的方法,通过蒸馏过程将甲醇和其他成分分离出来。
甲醇是一种重要的有机化合物,广泛应用于化工、医药、农业等领域。
甲醇精馏技术主要包括加热、蒸发、冷却和凝结等步骤,通过控制温度和压力,可以实现对甲醇的有效提纯。
甲醇精馏技术在工业生产中起着至关重要的作用,可以提高甲醇产品的纯度和质量,降低生产成本,增加产量。
甲醇精馏技术还可以有效减少能源消耗和减少废物排放,符合可持续发展的要求。
随着科技的发展,甲醇精馏技术不断创新,设备性能和效率不断提高,节能减排效果也日益显著。
未来,随着清洁能源和环境保护的重要性逐渐增强,甲醇精馏技术将会得到更广泛的应用和推广,在节能减排方面发挥更大的作用。
2. 正文2.1 甲醇精馏技术原理甲醇精馏技术原理涉及到甲醇在不同温度下的沸点,利用沸腾、冷凝和凝固等物理性质的差异,通过加热和冷却使甲醇蒸汽在一定温度范围内得以分离、浓缩、净化,最终得到纯净的甲醇产品。
具体来说,甲醇精馏技术利用甲醇和其他杂质的沸点差异,使其在不同温度下转变为气态或液态,然后通过冷却收集回流的液体,再次进行加热蒸馏分离,从而不断提高甲醇的纯度。
甲醇精馏技术的关键在于控制温度、压力和流速等参数,使得甲醇在不同阶段得以分离并提取。
通过反复蒸馏和冷凝的过程,可以逐渐去除杂质,提高甲醇的纯度和产量。
甲醇精馏技术的原理简单易懂,但在实际应用中需要严格控制各项参数,确保产品的质量和产量达到要求。
甲醇精馏技术的原理为甲醇产业的发展提供了技术支持和保障,也在节能减排方面发挥了重要作用。
2.2 甲醇精馏设备甲醇精馏设备是甲醇生产过程中非常关键的一部分,它主要包括蒸馏塔、冷凝器、沉淀器和分离器等组件。
蒸馏塔是甲醇精馏设备的核心部件,它通过加热液态甲醇使其汽化,然后通过冷凝器将汽相甲醇冷凝回液态,实现甲醇的分离和提纯。
冷凝器主要用于冷却和凝结汽相甲醇,将其转化为液态甲醇。
化工精馏技术的应用及节能措施

化工精馏技术的应用及节能措施摘要:化工企业作为能源消耗的重要企业,需要将节能减排放在重要位置,加强对化工精馏技术的应用,树立良好的节能减排观念,科学制定节能措施,保证能源资源在得到充分运用的同时,使能耗问题可以彻底解决,让化工生产过程更为环保,促进化工行业可持续发展目标的实现。
化工精馏技术经过多轮技术革新,已经在生产效率、节能环保、资源利用、精确控制方面有了长足进步。
本文主要分析化工精馏技术的应用及节能措施。
关键词:化工精馏技术;多效精馏技术;节能措施引言为有效促进化工行业精馏过程中能源利用率的提升,应该加强化工行业生产效率的提高,保证化工企业能获得更大经济利益,与此同时,满足环保节能需求,在确保经济效益的前提下,满足社会效益,做到可持续发展。
在运用化工精馏技术时,应该结合当前生产过程中存在的各类问题,不断对精馏技术优化和完善,增强精馏技术运用的规范性和可行性。
1、化工精馏的流程分析蒸馏是根据混合液中不同物质之间的相对挥发差异,对轻质混合液进行物理划分和重组的单元。
塔加热器提供混合液的热源,塔顶提供材料蒸汽制冷剂,蒸馏塔内的混合材料通过多种气体液之间的质量传递和能量传递,液相轻组分获得多气化能量,得到柱顶高纯度的轻馏分产物,气相重组组分多次向柱锅炉释放冷凝能量,得到高纯度的馏分产物。
总之,化学蒸馏是净化分离的过程,在化学制造过程中,由于不同物质的性质不同,需要提取材料需求的特点来满足生产需求,可以说高能效蒸馏是操作的创新和优化传统蒸馏作业与高能效蒸馏作业有着根本的区别。
首先,在设备中,传统蒸馏应使用蒸馏柱进行。
主要工作原理是加热蒸汽,然后达到液体沸点,引起液体的物理气化反应,从而分离纯化。
其次,剩余的零部件必须用冷凝水进行冷却和循环利用,整个操作过程的能耗大、限制性强,蒸馏效率不理想。
因此,需要结合现代技术进行优化,高效节能的蒸馏技术将冷凝热与热能结合起来,以降低蒸馏过程中的能耗,通过分析液体性质和沸点,整个蒸馏过程能够有效地分离出部分组分,如下所示。
化工生产中降低精馏技术能耗的措施

化工生产中降低精馏技术能耗的措施摘要:精馏技术在工业化生产中是重要一部分。
化学精馏技术具备操作流程简单、实际转化效率较高、能源资源利用率较高以及投资成本较低等诸多优势,与其他先进技术的化学反应研究更加频繁,极大限度地促进了精馏技术理论体系的逐步完善和工业应用范围的不断拓宽。
在考虑化学反应过程和精馏技术匹配程度的基础上,充分体现精馏技术的工业生产优势,利用催化剂类型的选择、装填方式的选择等,保证精馏技术在工业生产过程中的大范围应用将是未来一定时间内精馏技术应用的重要趋势。
关键词:化工生产;降低精馏技术;能耗引言化工生产可以简单的分为三个阶段:1)原料的预处理阶段;2)原料在反应器内经催化剂催化生成产物的化学反应阶段;3)反应产物分离提纯得到目的产物阶段。
精馏操作在工业化的物料分离流程中有着普遍的应用。
发展节能高效的精馏技术既有利于高纯度产品的分离提纯技术的提高,也有利于日常生产过程中的能源节能。
1精馏技术的原理化学精馏技术是指将化学催化反应和精馏分离技术融为一体,且能进一步通过精馏塔实现非均质化学催化反应和精馏作用的全新化学工业生产技术。
化学精馏技术可进一步分为普通精馏技术和催化精馏技术两大类别。
其中,普通精馏技术是指利用汽相和液相两相之间的传递过程,实现汽相和液相质量推动,从而使气液两相之间由于组分浓度差而实现分离的化学过程,而催化精馏技术则是利用汽相和液相两相之间的传质作用和反应作用过程,包括利用汽相和液相之间的两相传递过程和浓度差反应效应,以化学反应方式实现对汽相和液相平衡的影响,使汽液两相之间由于组分浓度差和化学反应效应不同而实现化学分离过程。
2化工精馏高效节能技术开发及应用的意义2.1有利于降低化工精馏过程的能量消耗化工精馏过程是借助液相和气相之间的相互转化,将易挥发组分和难挥发组分进行有效的传质,从而实现物质分离的工艺流程。
研究人员加强对于化工精馏高效节能技术的开发应用,能够将传热反应速度进行有效的控制,对于出现的巨大蒸汽损耗进行有效的调整,从而对于蒸馏塔内部的温度差异进行灵活化的转变,将精馏塔内部的蒸汽热量进行充分的应用,借助分级换热技术的应用,将信号传递过程进行有效的数字化处理,从而提升信息传输的效率和精度,为热量调整方案的应用打下了坚实的基础。
热泵精馏技术进展介绍

热泵精馏技术进展介绍热泵精馏技术是一种新型的能源利用技术,它是在传统精馏技术的基础上,引入热泵技术,利用热泵对馏分进行加热,从而提高能源利用效率。
热泵精馏技术具有节能、环保、经济等优点,在石油、石化、化工等行业得到了广泛应用。
本文将从热泵精馏技术的基本原理、应用领域、发展现状等方面进行介绍。
一、热泵精馏技术的基本原理热泵精馏技术是将热泵技术应用于传统精馏技术中,其基本原理是利用热泵对馏分进行加热。
热泵是一种能够将低温热量转化为高温热量的装置,它利用制冷剂的循环来完成热量的传递。
热泵精馏技术利用热泵对馏分进行加热,从而提高馏分的温度,使其易于挥发,从而达到提高精馏效率的目的。
热泵精馏技术不仅可以提高能源利用效率,还可以减少环境污染,具有很高的经济效益和社会效益。
二、热泵精馏技术的应用领域热泵精馏技术具有广泛的应用领域,主要包括石油、石化、化工等行业。
在石油行业中,热泵精馏技术可以用于提炼各种石油产品,如汽油、柴油、润滑油等。
在石化行业中,热泵精馏技术可以用于生产各种化工产品,如聚合物、合成纤维等。
在化工行业中,热泵精馏技术可以用于生产各种化工产品,如酸、碱、盐酸等。
三、热泵精馏技术的发展现状热泵精馏技术是一种新型的能源利用技术,近年来得到了快速发展。
在国内,热泵精馏技术已经得到了广泛的应用,各大石油、石化、化工企业都在积极推广和应用这项技术。
同时,国家也在加大对热泵精馏技术的支持力度,制定了相关政策和标准,为热泵精馏技术的发展提供了保障。
在国际上,热泵精馏技术也得到了广泛的应用,各大石油、石化、化工企业都在积极推广和应用这项技术。
四、热泵精馏技术的未来发展热泵精馏技术是一种具有广阔前景的技术,未来的发展前景非常广阔。
随着科技的不断进步和热泵技术的不断改进,热泵精馏技术将会更加成熟和稳定。
同时,随着环保意识的不断提高,热泵精馏技术将会越来越受到重视和关注。
未来,热泵精馏技术将会在各个行业中得到广泛的应用,为推进经济发展和环境保护做出更大的贡献。
精馏塔各种节能方式
精馏塔各种节能方式一、精馏塔节能方式之提高塔的操作效率精馏塔在化工生产里可是个重要角色呢。
要提高它的操作效率来节能呀,就像是给它做个“健身计划”。
比如说,优化操作参数,像调整回流比这个关键的数值。
回流比要是合适了,就像是给精馏塔找到了最舒服的工作状态。
回流比太大,那能源消耗就像开着水龙头不关一样浪费;回流比太小呢,又达不到理想的分离效果。
咱得找到那个刚刚好的点,就像给塔穿上了最合适的衣服,让它工作起来又高效又节能。
二、利用高效的塔板或填料这就好比给精馏塔换上更好的“牙齿”。
高效的塔板或者填料能让气液接触更充分。
就像我们吃薯片,要是每一片都能充分地蘸到酱料,那多美妙啊。
在精馏塔里呢,气液充分接触就能让分离效果更好,而且还能减少能量的消耗。
比如说新型的规整填料,就像是一群训练有素的小士兵,排列得整整齐齐,让气液在它们中间顺利地完成任务,达到节能的效果。
三、热集成技术的应用热集成听起来就很厉害的样子。
简单说呢,就是让热量在系统里循环利用起来。
精馏塔里面有些地方是需要加热的,有些地方是需要冷却的。
咱们要是能把那些要冷却地方的热量收集起来,送到需要加热的地方去,那不是一举两得嘛。
就像家里的暖气系统,如果能把排出去的热气再回收利用,既环保又省钱。
在精馏塔里运用热集成技术,就可以大大降低能源的消耗,让整个精馏过程更节能。
四、采用先进的控制系统这就像是给精馏塔请了个超级智能的管家。
先进的控制系统可以实时监测精馏塔的各种参数,像温度、压力、流量等等。
一旦发现有什么不对劲的地方,就马上进行调整。
比如说,要是温度有点偏高了,这个智能管家就会迅速调节加热装置,让温度回到合适的范围。
这样就能保证精馏塔一直处于最佳的工作状态,避免因为参数的波动而浪费能源。
五、优化进料状态进料状态对精馏塔的节能也很重要哦。
如果进料的温度、压力、组成等状态合适的话,就可以减少精馏塔内部的能量消耗。
比如说,要是能把进料的温度预热到接近塔内某个合适的温度,那在塔内就不需要再额外消耗很多能量去加热或者冷却这个进料了。
化工精馏高效节能技术开发与运用
化工精馏高效节能技术开发与运用摘要:现今能源短缺局势更加严峻,对于化工企业来讲,需要积极响应节能减排,实施节能举措。
化工装备主要涉及反应、分离两个过程,后者占消耗量的75%,其中精馏是核心过程,能耗占一半以上。
因此,在装备能耗方面,减少精馏过程的消耗是关键点。
如今,一般的蒸馏程序难以让能耗减少,必须采取高效精馏技术。
实际上,该项技术目前仍然不是很成熟,存在不少可能给精馏带来影响的因素。
化工企业应对这一方面开展全方位研究,加大运用力度。
关键词:化工精馏;高效节能;物质分离1 化工精馏分析利用物质间某些性质的差异,选用不同的方法将它们分离,通常情况下需要借助精馏塔。
使用蒸汽热能组成汽化物料,然后借助塔板传递热量及传质,并且进行汽化分离,剩余物料在冷却之后进行回收,这就是蒸馏原理。
就普通蒸馏而言,其蒸汽损耗较为突出,会提高能耗,借助精馏能科学发挥这一部分热量的作用,继而实现节能目标。
其中,存在较多可能会影响精馏过程的因素,比如温度及塔压,塔压出现波动,会干扰塔板组成,使分离浓度出现变化。
对于冷凝器及加热釜,应该避免二者过多进料,否则,将难以确保产品质量。
物料温度变低时,冷负荷提高,也可能干扰分离情况。
通过加大回流比,进一步提高输出质量,让回流比处在适当范围,以便确保蒸馏效率。
就普通精馏而言,通常情况下都是一股进料,在塔底借助再沸器,通过热能量体提供热量,达成汽化目标,物料基于塔板对热量进行传递,利用组分持续冷凝及汽化,继而进行分离,最终气体至塔顶。
借助冷能量体,待有效完成冷凝,物料返回至塔顶,剩余的作为产品输出。
化工精馏中,冷凝会带走一定的热量,临近塔底利用热能量体供热,若有效借助冷凝热,则可以让能耗减少,实现节能增效目标。
通过冷凝热回收利用,组成各种节能型精馏流程,例如多效精馏。
2 技术开发与运用意义(1)减少化工精馏过程能耗。
对于化工精馏过程来讲,它利用气相液相彼此转化,将难挥发、易挥发组分进行传质,继而达到物质分离的目的。
浅析化工精馏高效节能技术开发及应用
浅析化工精馏高效节能技术开发及应用化工精馏是一种重要的分离技术,广泛应用于石油、煤化工、化肥、化学工程等领域。
传统的化工精馏过程存在能耗高、设备庞大、冷却塔效率低等问题,因此如何开发和应用高效节能的精馏技术成为了当前化工行业的研究热点之一。
一种常见的高效节能精馏技术是利用精馏塔内部多个板段进行分离操作。
通过在板段上设置理论塔板,可以有效增加提馏料和回流液之间的接触面积,提高分离效率。
还可以采用提馏料侧进料、回流液裂解等技术来提高精馏塔的分离效率。
在操作参数方面,通过调整塔内的温度、压力、流量等参数,可以进一步优化精馏过程,提高能量利用率。
另一种高效节能精馏技术是采用精馏塔内增容技术。
传统精馏塔通常只有一个塔体,通过增加塔体或引入新的分离层,可以使分离效率进一步提高。
在传统精馏塔上增设有限接触塔、萃取塔等增容设备,可以实现多级分离,提高分离效率。
还可以利用新型填料来提高精馏塔的分离效率。
采用高效填料,可以增加气液交换的面积,提高分离效果。
通过优化填料的形状和材料,可以减少压降,降低能耗。
除了上述技术,还可以采用先进的控制策略来提高精馏过程的效率。
通过合理控制馏出液的流量、温度、压力等参数,可以实现最优操作,提高能量利用率。
在实际应用中,化工精馏高效节能技术可以广泛应用于各行业。
在石油炼制工艺中,可以应用于原油分馏、汽车汽油制备等过程中。
在化肥工程中,可以应用于氨水脱碳、尿素生产等过程中。
在化学工程中,可以应用于有机合成、溶剂回收等过程中。
化工精馏高效节能技术的开发和应用对于提高工业生产效率、降低能源消耗、减少环境污染具有重要意义。
未来,随着科技的不断进步和发展,相信会出现更多创新的精馏技术,为化工行业的可持续发展做出更大贡献。
略谈化工生产中降低精馏技术能耗的措施
略谈化工生产中降低精馏技术能耗的措施摘要:随着经济的发展,化工行业变得日益重要,然而,目前国内化工行业普遍存在着装备落后、效率低下、能源消耗大、工艺复杂等问题。
所以,对一些例如化工生产的企业来说,有必要采用更好的管理方式,转变落后的生产理念,采用新的设备和新技术,从而更好地减少能耗,获得更大的生产优势。
关键词:化工生产;精馏技术;措施前言:近几年来,在各行业迅速发展的同时,由于对能耗问题的忽视,导致了我国的能耗问题日益突出。
其中,化工生产企业作为我国经济发展的一个关键部分,在运用精馏技术进行化工生产的时候,会消耗大量的能量来完成生产工作,因此会对我国的能源消耗产生很大的影响。
所以,在进行化工产品的过程中,化工企业应该对精馏技术的内容进行优化,通过减少精馏技术的能耗,保证化工产品的数量和品质,从而能够对化工公司的发展起到积极的作用,让我国的能源能够步入可持续发展的轨道。
一、精馏技术的概述精馏工艺以消耗与补偿为主,将塔底的低温区转变为高温区,经过塔顶,在塔底进行再沸器至热源处利用。
按其制造技术及流程不同,可将其划分为两种:一种是直接热泵式,另一种是间接热泵式。
二、化工生产中精馏技术运用的影响因素(一)压力因素在特定的塔压条件下,精馏工艺及塔结构均需在特定的塔压条件下完成,因此,如何保证塔压的恒定,将直接影响到精馏工艺的整体性能。
当塔中的压力骤然上升时,液相物质的挥发度将会降低,这时就不能对液体中的各种物质展开蒸馏分离,并且气相的重性也会随之提高,这样就会大大降低了蒸馏的效率,对生产效率和产物的品质造成了严重的影响,其次,对产品品质和物料平衡造成了严重的破坏,当操作压力提高的时候,气相组成成分的浓度将会显著提高,并且其质量比也会随之变大,本该蒸发出去的气相很有可能会由于压力过大而发生液化,并与原来的液相物质混合在一起,从而达到不了蒸馏分离的效果。
(二)温度因素在采用精馏工艺生产化学品的情况下,为了避免由于工艺条件的改变而造成的不良后果,在生产中应对工艺条件进行严格的控制。
- 1、下载文档前请自行甄别文档内容的完整性,平台不提供额外的编辑、内容补充、找答案等附加服务。
- 2、"仅部分预览"的文档,不可在线预览部分如存在完整性等问题,可反馈申请退款(可完整预览的文档不适用该条件!)。
- 3、如文档侵犯您的权益,请联系客服反馈,我们会尽快为您处理(人工客服工作时间:9:00-18:30)。
热泵精馏工艺分析 化工行业是能耗大户, 其中精馏又是能耗极高的单元操作, 而传统的精馏方式热力学效率很 低,能量浪费很大。 如何降低精馏塔的能耗, 充分利用低温热源, 已成为人们普遍关注的问 题。对此人们提出了许多节能措施, 通过大量的理论分析、 实验研究以及工业应用表明其中 节能效果比较显著的是热泵精馏技术。 热泵精馏是把精馏塔塔顶蒸汽加压升温, 使其用作塔 底再沸器的热源,回收塔顶蒸汽的冷凝潜热。
热泵精馏在下述场合应用,有望取得良好效果: (1) 塔顶和塔底温差较小,因为压缩机的功耗主要取决于温差,温差越大,压缩机的功耗越 大。据国外文献报导,只要塔顶和塔底温差小于 36C,就可以获得较好的经济效果。
(2) 沸点相近组分的分离,按常规方法,蒸馏塔需要较多的塔盘及较大的回流比,才能得到 合格的产品, 而且加热用的蒸汽或冷却用的循环水都比较多。 若采用热泵技术一般可取得较 明显的经济效益。
(3) 工厂蒸汽供应不足或价格偏高 ,有必要减少蒸汽用量或取消再沸器时。 (4) 冷却水不足或者冷却水温偏高、价格偏贵,需要采用制冷技术或其他方法解决冷却问题 时。
(5) —般蒸馏塔塔顶温度在 38〜138 C之间,如果用热泵流程对缩短投资回收期有利就可以采 用,但是如果有较便宜的低压蒸汽和冷却介质来源,用热泵流程就不一定有利。
(6) 蒸馏塔底再沸器温度在 300 C以上,采用热泵流程往往是不合适的。 以上只是对一般情况而言 ,对于某个具体工艺过程,还要进行全面的经济技术评定之后才能 确定。 根据热泵所消耗的外界能量不同,热泵精馏可分为蒸汽加压方式和吸收式两种类型 1 .蒸汽加压方式 蒸汽加压方式热泵精馏有两种:蒸汽压缩机方式和蒸汽喷射式。 1.1 蒸汽压缩机方式 蒸汽压缩机方式又可分为间接式、 塔顶气体直接压缩式、 分割式和塔釜液体闪蒸再沸式流程。
1.1.1 间接式 当塔顶气体具有腐蚀性或塔顶气体为热敏性产品或塔顶产品不宜压缩时, 可以采用间接式热 泵精馏,见图 1 。 图1间接式热泵精馏流程图 它主要由精馏塔、压缩机、蒸发器、 冷凝器及节流阀等组成。 这种流程利用单独封闭循环的 工质(冷剂)工作:冷剂与塔顶物料换热后吸收热量蒸发为气体,气体经压缩提高压力和温 度后,送至塔釜加热釜液,而本身凝结成液体。液体经节流减压后再去塔顶换热, 完成一个 循环。
于是塔顶低温处的热量,通过冷剂的媒介传递到塔釜高温处。 在此流程中,制冷循环中的冷 剂冷凝器与塔釜再沸器合为一个设备。在此设备中冷剂冷凝放热而釜液吸热蒸发。
间接式热泵精馏的特点是: (1) 塔中要分离的产品与冷剂完全隔离; (2) 可使用标准精馏系统,易于设计和控制; (3) 与塔顶气体直接压缩式相比较,多一个热交换器 (即蒸发器),压缩机需要克服较高的温差 和压力差,因此其效率较低。
考虑到工质的化学稳定性,间接式热泵精馏应用的温度范围限制在 130 C左右,而许多有机产 品的精馏塔却在较高的温度下操作。
与普通制冷剂相比, 水的化学和热稳定性好, 泄漏时对人和臭氧层无负效应,价格便宜,而 且具有极好的传热特性, 在热交换中所需的换热面积较小, 特别适合精馏塔底温度较高的精 馏系统。
表1是以水为工质,用间接式热泵精馏分离乙苯 -对二甲苯的节能结果。虽然单独工质循环 式热泵精馏比常规精馏的总投资费用大,但回收期短,一般在一年之内。 耗褪及费用 當规精谓 塔顶言接 热泵精超 间接式魏 泵精is
蒸汽i 26 0
电kU n
㈣
冷却水TT1 '* h 120 14J.J
蒸汽■'元"h 507 0 21)
电元小 0 M7. 75 100. 75
冷却水元■ h 45. 5 4J) 4 55
总操作费用元, 5 91.65 !嘅?
节能效益元从 1) 2. 2
投资回收期年 0 1L3 <1 23
表1不同热泵精馏流程处理乙苯-对二甲苯溶液的节能及经济效果
1.1.2塔顶气体直接压缩式 塔顶气体直接压缩式热泵精馏是以塔顶气体作为工质的热泵,其流程见图 2,精馏塔顶气体 经压缩机压缩升温后进入塔底再沸器,冷凝放热使釜液再沸,冷凝液经节流阀减压降温后, 一部分作为产品出料,另一部分作为精馏塔顶的回流。
图2塔顶气体直接压缩式热泵精馏流程图 塔顶气体直接压缩式热泵精馏的特点是: (1) 所需的载热介质是现成的; (2) 因为只需要一个热交换器 (即再沸器),压缩机的压缩比通常低于单独工质循环式的压缩 比; (3) 系统简单,稳定可靠。
塔顶气体直接压缩式热泵精馏适合应用在塔顶和塔底温度接近, 或被分离物质因沸点接近难 以分离,必须采用较大回流比的情况下,因此需要消耗大量加热蒸汽 (即高负荷的再沸器),
塔底产物 压 机 或在低压运行必须采用冷冻剂进行冷凝。 为了使用冷却水或空气作冷凝介质, 必须在较高塔 压下分离某些易挥发物质的场合。 塔顶气体直接压缩式热泵精馏应用十分广泛,如丙烯 -丙烷的分离采用该流程,其热力学效 率可以从3.6%提高到8.1%,节能和经济效益非常显著。 某厂采用热泵精馏的结果见表 2,由此可见,当选用热泵精馏时,能源费用急剧下降。此时, 冷却水温度已不再是决定因素, 精馏塔可在更低的压力下操作, 既简化了分离过程, 又降低 了设备成本。
表2不同精馏形式下丙烯-丙烷分离的节能和经济效果比较 1.1.3分割式热泵 分割式热泵精馏组成及其流程如图 3所示。
图3分割式热泵精馏流程图 分割式热泵精馏流程分为上、 下两塔,上塔类似于直接式热泵精馏, 只不过多了一个进料口;
F 下塔则类似于常规精馏的提馏段即蒸出塔, 进料来自上塔的釜液, 蒸汽则进入上塔塔底。 分 割式热泵精馏的节能效果明显,投资费用适中,控制简单。 分割式热泵精馏的特点是可通过控制分割点浓度 (即下塔进料浓度)来调节上塔的温差,从而 选择合适的压缩机。在实际设计时,分割点浓度的优化是很必要的。 分割式热泵精馏适用于分离体系物的相图存在恒浓区和恒稀区的大温差精馏,如乙醇水溶 液、异丙醇水溶液等。 表3是某工厂采用常规精馏、塔顶直接式热泵精馏和分割式热泵精馏工艺处理异丙醇水溶液 的结果。
耗能及费用 常规楕憎 塔顶直接 热泵精憎 分割式热 泵
精镭 蒸汽 36
电4毗 U 240() 3 2(10
冷却水 1 tXHI KM)
菱汽/元斥' 0 20
电丿元E 0 I6W N4
冷却水'元儿“ 21) 2 2
总操作费用'元小」 ]?() 106
节能效益'元 0 2(X1 2fU
表3不同精馏形式下异丙醇溶液分离的节能和经济效果比较 1.1.4闪蒸再沸 闪蒸再沸是热泵的一种变型, 它以釜液为工质,其流程如图4所示。与塔顶气体直接压缩式 相似,它也比间接式少一个换热器, 适用场合也基本相同。 不过,闪蒸再沸在塔压高时有利, 而塔顶气体直接压缩式在塔压低时更有利。
从表3可以看出,分割式可选择单级压缩机, 昂贵的多级压缩机。其耗电量几乎是分割式的 其耗电量大大降低; 而塔顶直接式就必须选择 2
倍。 塔底出料 图4闪蒸再沸式热泵精馏流程图 1.2蒸汽喷射式 图5是采用蒸汽喷射泵方式的蒸汽汽提减压精馏工艺流程。 在该流程中,塔顶蒸汽是稍含低 沸点组成的水蒸气,其一部分用蒸汽喷射泵加压升温, 随驱动蒸汽一起进入塔底作为加热蒸 汽。
在传统方式中,如果进料预热需蒸汽量 10,再沸器需蒸汽量30,则共需蒸汽量40。而在采 用蒸汽喷射式热泵的精馏中, 用于进料预热的蒸汽量不变, 但由于向蒸汽喷射泵供给驱动蒸 汽15就可得到用于再沸器加热的蒸汽 30,故蒸汽消耗量是25,可节省37.5%的蒸汽量,所
以节能效果十分显著。
采用蒸汽喷射泵方式的热泵精馏具有如下优点: (1) 新增设备只有蒸汽喷射泵,设备费用低; (2) 蒸汽喷射泵没有转动部件,容易维修,而且维修费用低。 蒸汽喷射式热泵精馏如果在大压缩比或高真空度条件下操作,蒸汽喷射泵的驱动蒸汽量增 大,再循环效果显著下降。 因此,这种方式的热泵精馏适合应用在: (1)精馏塔塔底和塔顶的压差不大; ⑵减压精馏的真空度比较低的情况下。
2吸收式 吸收式热泵由吸收器、 再生器、冷却器和再沸器等设备组成, 常用溴化锂水溶液或氯化钙水 溶液为工质。由再生器送来的浓溴化锂溶液在吸收器中遇到从再沸器送来的蒸汽, 发生了强 烈的吸收作用,不但升温而且放出热量 的吸收器即为精馏塔的蒸发器。
浓溴化锂溶液吸收了蒸汽之后,浓度变稀,即送再生器蒸浓。再生器所耗用的热能 是热泵的原动力。从再生器中蒸发出来的水蒸气, 在冷却器中冷却、冷凝, 而后送入精馏塔 冷凝器,在此冷凝器中,塔顶馏出物被冷凝,而水又重新蒸发进入吸收器。由此可见,精馏 塔的冷凝器也是热泵的再沸器,详见图 6。
吸收式热泵按照机内循环方向的不同可分为: 冷凝器压力大于蒸发器压力的第一类吸收式热泵 (I型)和蒸发器压力高于冷凝器压力的第 二类吸收式热泵(n型)。第一类吸收式热泵需要高温热源驱动,但不需要外界冷却水,热量 能得到充分利用,主要应用于产生热水;第二类吸收式热泵可利用低品位热能直接驱动, 以 低温热源与冷却水之间的温差为推动力,可产生低压蒸汽。
表4吸收式热泵的特点