轴承淬火常见缺陷
NO.6轴承热处理知识讲义

BLSX4型炉(铁路货车轴承套圈渗碳)
适用于G20CrNi2MoA(电渣重熔) G20CrNi2Mo、 G20CrNiMoA 、 G20CrNiMo钢制铁路货车轴承套圈渗碳热处理一次淬、回火。 渗碳炉装盘工位器具的要求:
主 要 尺 寸 mm (长× 宽×高) 560 ×560 ×50 540 × 540 × 390 490 × 490
KH750/12滚筒炉热处理生产线
设备型号:KH750/12 淬火炉功率: 60KW 滚筒直径: 750 mm,12个螺旋 回火炉型号:KAL1000/8 功率:40KW 滚筒直径 :1000 mm,8个螺旋 生产率:110~180 kg/h 前清洗机功率:48kw 热油槽功率:36kw 后清洗机功率:18kw 加工范围:钢球5~30mm,滚子:≤30mm
钢的热处理原理(续)
钢的淬火:将钢加热至临界区(Ac1 或Ac3)以上 30~50℃、保温一定时间,然后快速冷却,使过冷奥氏 体转变为马氏体(或贝氏体)的一种操作方法。 其目的:1)提高工件硬度和耐磨性 2)与回火配合获得所需要的机械性能 钢的回火:将淬火钢重新加热至A1以下的某一温 度后, 以一定的方法冷却到室温的操作方法 其目的:1)减少或消除内应力 2)稳定组织、稳定尺寸 3)根据工件不同的技术要求,获得所需 要的 组织和性能。
RJGD-200辊底式电阻加热炉
总功率:200KW Ⅰ:68kw Ⅱ:68kw Ⅲ:30kw Ⅳ:34kw 额定电压:Ⅰ:116V Ⅱ:116V Ⅲ:107V 平均生产率:275kg/h 有效工作尺寸:6100×650×200mm 最高温度:950℃ 加工8000型套圈滚道向上、7000型、9000型 轴承内外圈大边必须向下,加工轴承套圈的外 径小于120mm以下必须采用装盘。
高碳铬轴承钢贝氏体等温淬火.
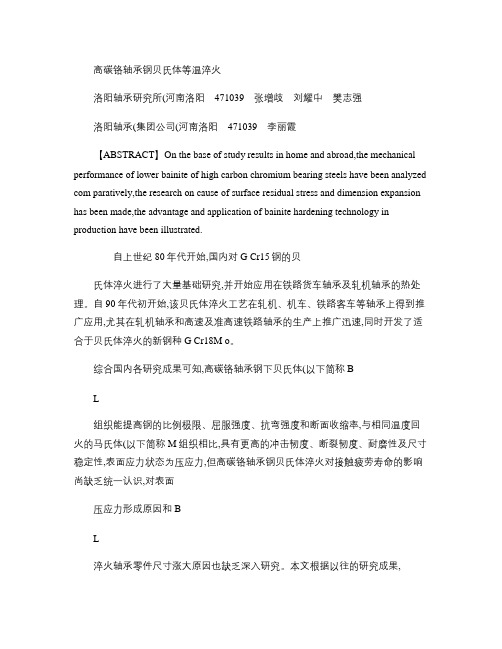
高碳铬轴承钢贝氏体等温淬火洛阳轴承研究所(河南洛阳471039张增歧刘耀中樊志强洛阳轴承(集团公司(河南洛阳471039李丽霞【ABSTRACT】On the base of study results in home and abroad,the mechanical performance of lower bainite of high carbon chromium bearing steels have been analyzed com paratively,the research on cause of surface residual stress and dimension expansion has been made,the advantage and application of bainite hardening technology in production have been illustrated.自上世纪80年代开始,国内对G Cr15钢的贝氏体淬火进行了大量基础研究,并开始应用在铁路货车轴承及轧机轴承的热处理。
自90年代初开始,该贝氏体淬火工艺在轧机、机车、铁路客车等轴承上得到推广应用,尤其在轧机轴承和高速及准高速铁路轴承的生产上推广迅速,同时开发了适合于贝氏体淬火的新钢种G Cr18M o。
综合国内各研究成果可知,高碳铬轴承钢下贝氏体(以下简称BL组织能提高钢的比例极限、屈服强度、抗弯强度和断面收缩率,与相同温度回火的马氏体(以下简称M组织相比,具有更高的冲击韧度、断裂韧度、耐磨性及尺寸稳定性,表面应力状态为压应力,但高碳铬轴承钢贝氏体淬火对接触疲劳寿命的影响尚缺乏统一认识,对表面压应力形成原因和BL淬火轴承零件尺寸涨大原因也缺乏深入研究。
本文根据以往的研究成果,对高碳铬轴承钢BL淬火后的力学性能进行对比分析,并就表面压应力和尺寸涨大的原因进行探讨,总结并分析生产中贝氏体淬火工艺的优势及其应用情况。
(完整word版)GCr15轴承钢热处理工艺设计要点

工艺课程设计(论文)题目:GCr15轴承钢热处理工艺设计院(系):专业班级:学号:学生姓名:指导教师:起止时间:课程设计(论文)任务及评语院(系):教研室:材料科学与工程教研室目录1 GCr15轴承钢热处理概述 (1)2 GCr15轴承钢热处理工艺设计 (2)2。
1 GCr15轴承钢的服役条件、失效形式及性能要求 (2)2.1。
1 服役条件、失效形式 (2)2。
1。
2 性能要求 (2)2。
2轴承钢材料的选择 (2)2.3 GCr15钢的C曲线 (3)2.4 GCr15轴承钢的热处理工艺设计 (4)2.4。
1 GCr15轴承钢的工艺流程 (4)2.4.2 GCr15轴承钢的热处理工艺设计 (5)2。
5 GCr15轴承钢的热处理工艺理论基础、原则 (8)2.5.1 GCr15轴承钢的球化退火工艺理论基础、原则 (8)2。
5。
2 GCr15轴承钢淬火工艺原理 (9)2。
5。
3 GCr15轴承钢回火工艺理论基础、原则 (12)2.6选择设备、仪表和工夹具 (13)2。
6。
1设备 (14)2.6。
2仪表 (15)2。
6.3设计工夹具 (16)2。
7 GCr15轴承钢热处理质量检验项目、内容及要求 (17)2。
8 GCr15轴承钢热处理常见缺陷的预防及补救方法 (18)2.8.1加热时常见的缺陷的预防及补救方法 (18)2。
8。
2淬火、回火缺陷与预防、补救 (19)2。
9热处理工艺卡 (21)2.9.1GCr15轴承钢球化退火工艺卡 (22)2.9。
2GCr15轴承钢淬火工艺卡 (23)2.9。
3GCr15轴承钢回火工艺卡 (24)3.参考文献 (25)1 GCr15轴承钢热处理概述对轴承钢的冶炼质量要求很高,需要严格控制硫、磷和非金属夹杂物的含量和分布,因为非金属夹杂物的含量和分布对轴承钢的寿命影响很大。
对轴承钢的基本质量要求就是纯净和组织均匀。
纯净就是杂质元素及非金属杂物要少,组织均匀是钢中碳化物要细小,分布要均匀。
轴承材料介绍
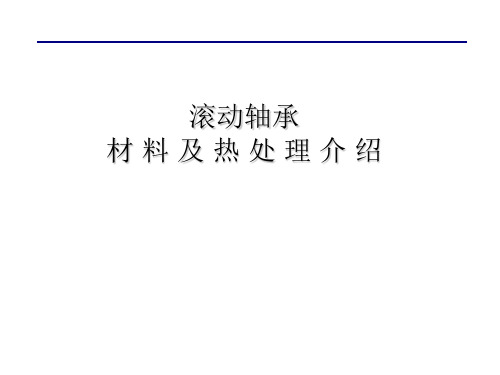
套圈材料及要求
套圈常用材料及基本要求
• 常用轴承钢国内外牌号对比
中国 GB GCr15 SAE 52100 美国 ASTM 52100 日本 JIS SUJ2 DIN 100Cr6 100CrMn 6 德国 材料号 1.3505 英国 BS 534A99 SKF3 SKF
GCr15SiMn
1· 3520
按照钢的品质分类: 普通钢(P ≤0.045%,S ≤0.055%) 优质钢(P ≤0.035%,S ≤0.035%) 高级优质钢(P ≤0.035%,S ≤0.030%) 按化学成份分类: 碳素钢 低碳钢C ≤0.25%,中碳钢0.25%≤ C ≤0.60%,高碳钢C > 0.6% 合金钢 低合金钢≤5%,中合金钢5%≤ C ≤10%,高合金钢> 10%
钢:碳钢和合金钢
铸铁:灰铸铁、球墨铸铁、可锻铸铁
金属材料基本知识
保持架SPCC 套圈、钢球GCr15、 55#、40Cr 黄铜HPb59-1
PA66、46、胶木保持架 NBR、ACM、FKM
金属材料基本知识
常用材料分类
习惯上,把含碳量>2.11%,或者<0.0218%的归类于铸铁或纯铁; 含碳量<2.11%归类为钢
五、人本集团目前常用轴承钢
GCr15、CU1、CU2、CU3、CU4、SKF3、100Cr6、52100、RB52100
套圈材料及要求
思 考 题
• 1、你公司所有零件都用到哪些金属材料?具体牌号能说出来吗?
• 2、什么是钢和什么是铁?举例说明。 • 3、GCr15钢含碳量在什么范围?轴承钢质量好坏主要从哪两大类进 行评价? • 4、人本目前有哪几个等级的GCr15钢?你公司主要用哪个或哪几个 等级的材料? • 5、国内常用轴承钢钢厂有哪几家?源自不锈轴承钢特殊性能钢
轴承套圈淬火胀大量的分析及解决方法

 ̄
—
I
—
 ̄
O
— . 一
Q
— , .
O
— , —
I
— 一
 ̄
— — 一
O
— — 一
Q
—
 ̄
—
 ̄
 ̄
I
 ̄
O
Q
 ̄
 ̄
( N a n j i n g K e r u n L u b i r c a n t s C o . , L t d . , N a n j i n g J i a n g s u 2 1 1 1 0 0, C h i n a )
Abs t r a c t :I n t h i s p a p e r ,r e a s o n s o f q u e n c h i ng s we l l i n g o f b e a r i ng r i n g we r e a n a l y z e d,i t c o n t r a s t e d t h e d i f f e r e n c e o f q ue n c h i n g s we l l i n g i n di f f e r e n t q u e n c h i n g o i l a n d c o o l i n g c y c l e s y s t e ms t h r o u g h e x p e ime r n t s .
An a l y s i s a n d R e s o l v e n t o f Qu e n c h i n g S we l l i n g o f Be a r i n g R i n g
带状碳化物对轴承钢性能的不利影响

带状碳化物对轴承钢性能的不利影响
带状碳化物对轴承钢的各种性能造成以下不利影响: 1)导致轴承钢材料化学成分的严重偏析。
在碳化物带上的碳含量高达1.3~1.4%,铬含量大于2.0%;而在碳化物的带间则碳含量较低,一般只有0.6~0.7%,铬含量小于1%。
2)由于碳化物带状造成轴承钢材料中化学成分的不均匀,导致在轴承零件退火后的组织中的碳化物分布不均匀,并且在两条碳化物带状之间的球化组织不完全。
3)因为碳化物带间的碳、铬含量较低,容易形成粗针状马氏体组织。
如果组织超过标准规定的级别要求,则整批轴承零件必须重新进行热处理;如果在轴承成品检验时发现由于碳化物带状造成热处理组织超标,则整批轴承零件将全部报废,这给轴承生产厂家造成很大的经济损失。
由于轴承的特点所致,在有关滚动轴承零件热处理的标准中对轴承零件热处理淬火回火的硬度及硬度的均匀性有着非常严格的规定,如果在轴承钢材中存在着较为严重的碳化物带状组织,极易造成轴承零件在热处理后的硬度和硬度不均匀方面达不到标准的相关规定。
4)热处理淬火工艺难以调整。
容易在碳化物带状的附近区域出现针状马氏体,而同时有时区域出现屈氏体组织。
5)淬火加热时过热敏感性增加,在热处理过程中容易出现淬火裂纹。
6)由于化学成分的差异,在碳化物带上和带间的机械性能不一致。
7)轴承零件切削加工的表面光洁度差,刀具易磨损。
8)降低轴承的使用寿命。
碳化物带状评级达到3~4级可使轴承钢材的接触疲劳寿命降低30%
左右。
训练4轴承套圈的淬火和回火(高级工)

•
4)加热时间的确定。各厂对加热时间的确定不完全相同,一般经过预 热后的加热时间为:盐炉l 5~1 8 s/mm,箱式电炉48 ~ 60s/ mm。不经预热的加热时间为:盐炉25~30s/mm,箱式电炉72~ 90s/mm。本例中M12丝锥经预热后在盐炉中的淬火加热时间为 3.5min,考虑装炉量取4min。
•
经上述工艺淬火后,Tl 2A钢制Ml 2丝锥得到如下组织:
• 表层,贝氏体+马氏体+残留渗碳体+少量残留奥氏体(厚度为2~3 mm); • 中心,托氏体+贝氏体+马氏体+未溶渗碳体+少量残留奥氏体。 • 表层硬度>60HRC,中心硬度较低,韧性较好。实践证明,这样的淬 火组织和性能完全能满足手用丝锥工作条件的要求。 • 手用丝锥淬火后还需进行低温回火,以降低内应力、稳定组织,并 仍保持较高的硬度。
(4)热处理工艺分析 •
1)球化退火。若原材料已经过球化退火且硬度和金相组织符合要 求,可直接进行切削加工成形。若原材料金相组织不合格,则需严格 按图8—27球化退火工艺进行球化退火。如果钢中有较严重的网状渗 碳体时,应正火后再球化退火。为了防止氧化脱碳,可将丝锥装箱并 填充铸铁屑或小块木炭,并用耐火泥密封,进行保护退火。 • 球化退火后,根据GB/T l 298--2008《碳素工具钢》技术要求进 行检验,硬度<207 HBW,珠光体球化级别应为2~4级,残余碳化
(2)显微组织。淬火、回火后显微组织需在套圈纵断面上进行取样,用金
相显微镜进行检查,放大倍数为500倍,也允许用450~600倍评定
轴承贝氏体淬火
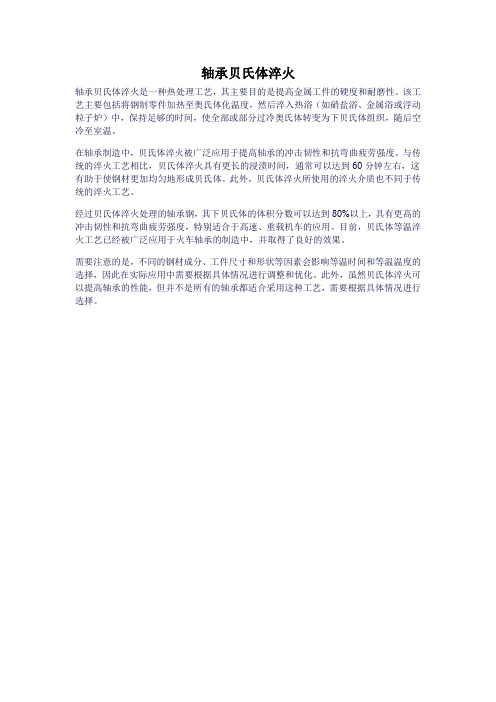
轴承贝氏体淬火
轴承贝氏体淬火是一种热处理工艺,其主要目的是提高金属工件的硬度和耐磨性。
该工艺主要包括将钢制零件加热至奥氏体化温度,然后淬入热浴(如硝盐浴、金属浴或浮动粒子炉)中,保持足够的时间,使全部或部分过冷奥氏体转变为下贝氏体组织,随后空冷至室温。
在轴承制造中,贝氏体淬火被广泛应用于提高轴承的冲击韧性和抗弯曲疲劳强度。
与传统的淬火工艺相比,贝氏体淬火具有更长的浸渍时间,通常可以达到60分钟左右,这有助于使钢材更加均匀地形成贝氏体。
此外,贝氏体淬火所使用的淬火介质也不同于传统的淬火工艺。
经过贝氏体淬火处理的轴承钢,其下贝氏体的体积分数可以达到80%以上,具有更高的冲击韧性和抗弯曲疲劳强度,特别适合于高速、重载机车的应用。
目前,贝氏体等温淬火工艺已经被广泛应用于火车轴承的制造中,并取得了良好的效果。
需要注意的是,不同的钢材成分、工件尺寸和形状等因素会影响等温时间和等温温度的选择,因此在实际应用中需要根据具体情况进行调整和优化。
此外,虽然贝氏体淬火可以提高轴承的性能,但并不是所有的轴承都适合采用这种工艺,需要根据具体情况进行选择。
- 1、下载文档前请自行甄别文档内容的完整性,平台不提供额外的编辑、内容补充、找答案等附加服务。
- 2、"仅部分预览"的文档,不可在线预览部分如存在完整性等问题,可反馈申请退款(可完整预览的文档不适用该条件!)。
- 3、如文档侵犯您的权益,请联系客服反馈,我们会尽快为您处理(人工客服工作时间:9:00-18:30)。
轴承淬火常见缺陷
轴承零件热处理的常见缺陷
轴承零件经热处理后常见的质量缺陷有:淬火显微组织过热、欠热、淬火裂纹、硬度不够、
热处理变形、表面脱碳、软点等。
1.过热
从轴承零件粗糙口上可观察到淬火后的显微组织过热。但要确切判断其过热
的程度必须观察显微组织。若在GCr15钢的淬火组织中出现粗针状马氏体,则为淬火过热组
织。形成原因可能是淬火加热温度过高或加热保温时间太长造成的全面过热;也可能是因原
始组织带状碳化物严重,在两带之间的低碳区形成局部马氏体针状粗大,造成的局部过热。
过热组织中残留奥氏体增多,尺寸稳定性下降。由于淬火组织过热,钢的晶体粗大,会导致
零件的韧性下降,抗冲击性能降低,轴承的寿命也降低。过热严重甚至会造成淬火裂纹。
2.欠热
淬火温度偏低或冷却不良则会在显微组织中产生超过标准规定的托氏体组
织,称为欠热组织,它使硬度下降,耐磨性急剧降低,影响轴承寿命。
3.淬火裂纹
轴承零件在淬火冷却过程中因内应力所形成的裂纹称淬火裂纹。造成这种裂
纹的原因有:由于淬火加热温度过高或冷却太急,热应力和金属质量体积变化时的组织应力
大于钢材的抗断裂强度;工作表面的原有缺陷(如表面微细裂纹或划痕)或是钢材内部缺陷
(如夹渣、严重的非金属夹杂物、白点、缩孔残余等)在淬火时形成应力集中;严重的表面
脱碳和碳化物偏析;零件淬火后回火不足或未及时回火;前面工序造成的冷冲应力过大、锻
造折叠、深的车削刀痕、油沟尖锐棱角等。总之,造成淬火裂纹的原因可能是上述因素的一
种或多种,内应力的存在是形成淬火裂纹的主要原因。淬火裂纹深而细长,断口平直,破断
面无氧化色。它在轴承套圈上往往是纵向的平直裂纹或环形开裂;在轴承钢球上的形状有S
形、T形或环型。淬火裂纹的组织特征是裂纹两侧无脱碳现象,明显区别与锻造裂纹和材料
裂纹。
4.热处理变形
轴承零件在热处理时,存在有热应力和组织应力,这种内应力能相互叠加或
部分抵消,是复杂多变的,因为它能随着加热温度、加热速度、冷却方式、冷却速度、零件
形状和大小的变化而变化,所以热处理变形是难免的。认识和掌握它的变化规律可以使轴承
零件的变形(如套圈的椭圆、尺寸涨大等)置于可控的范围,有利于生产的进行。当然在热
处理过程中的机械碰撞也会使零件产生变形,但这种变形是可以用改进操作加以减少和避免
的。
5.表面脱碳
轴承零件在热处理过程中,如果是在氧化性介质中加热,表面会发生氧化作
用使零件表面碳的质量分数减少,造成表面脱碳。表面脱碳层的深度超过最后加工的留量就
会使零件报废。表面脱碳层深度的测定在金相检验中可用金相法和显微硬度法。以表面层显
微硬度分布曲线测量法为准,可做仲裁判据。
6.软点
由于加热不足,冷却不良,淬火操作不当等原因造成的轴承零件表面局部硬
度不够的现象称为淬火软点。它象表面脱碳一样可以造成表面耐磨性和疲劳强度的严重下
降。