刀具涂层技术及其发展
金属切削原理与刀具涂覆技术的发展趋势

金属切削原理与刀具涂覆技术的发展趋势金属切削是目前工业生产中常见的一种加工方法,它通过刀具与工件之间的相对运动来达到将材料去除的目的。
随着制造业的不断发展和进步,金属切削原理和刀具涂覆技术也在不断演进和改进。
本文将对金属切削原理与刀具涂覆技术的发展趋势进行探讨。
一、金属切削原理的发展趋势金属切削原理是指通过刀具与工件的相对运动,削除材料以实现精确加工的过程。
随着制造业的快速发展,人们对产品的精密度和质量要求越来越高,金属切削原理也在不断发展和完善。
1. 切削力控制:传统的金属切削过程中,切削力难以控制,容易产生振动和噪音。
而现代切削技术中,通过应用先进的切削力控制系统,可以实时监测切削力的大小和方向,并及时调整刀具和工件的相对运动,从而达到精密加工的效果。
2. 切削速度提高:随着材料科学和工艺技术的进步,新材料的不断涌现,传统切削原理所能适应的速度范围越来越小。
因此,金属切削的发展趋势之一是提高切削速度,以适应高硬度、高温度和高抗腐蚀性材料的加工需求。
3. 先进刀具材料的应用:为了满足高速切削的需求,刀具材料也在不断改进和创新。
硬质合金、陶瓷和超硬材料等先进刀具材料的应用,大大提高了刀具的耐磨性和切削效率,有效延长了刀具的使用寿命。
二、刀具涂覆技术的发展趋势刀具涂覆技术是指在刀具表面涂覆一层或多层特殊材料,以增加刀具的硬度、耐磨性和切削性能。
随着制造业对切削工具功能要求的提高,刀具涂覆技术也在迅速发展。
1. 高温耐磨涂层的应用:在高速切削、高温切削等特殊工况下,刀具容易受到高温热载荷的影响。
因此,刀具涂覆技术的发展趋势之一是研发高温耐磨涂层,以提高刀具的使用寿命和切削性能。
2. 先进涂层材料的研究:随着纳米技术和材料科学的发展,越来越多的先进涂层材料被应用于刀具涂覆技术中。
例如,纳米结构涂层、多层复合涂层等,提供了更好的耐磨性和抗腐蚀性能,同时减少了切削时的摩擦力和热量。
3. 绿色环保涂层:在现代制造业中,绿色环保已成为一个重要的方向。
国外刀具涂层技术的现状及发展趋势

维 克的工作 小组在 I M 位 于美 国圣 何塞 的研 究 中心 ,他们 目前 正在努 力研发 一种名 为 ” B
锂空气” 的新型电池。该电池应用的技术能极大提高 电动汽车 电池的效率 ,让 电动汽车每充 电一 次 即可跑 50 i,而 大 多数 目前市场上 销售 的 电动 汽车 充 电一次 只 能跑 10m。 0k n 0k 这种 电池在 理 论上能 够将 目前 电动 汽 车普遍使 用 的锂 电池能量 密度 提 高十倍 , 因为 这种 电池将空气作为反应物放入 电池 内部 。这意味着” 锂空气” 的储存装置要 比一般的锂 电池更 轻,这也很大程度提升了电动汽车的性能。 ” 我总是把这个研发 的过程 比喻成攀登珠穆朗玛峰,” 维克说,” 在过去 的两个月里,我 们只能算是刚刚起步而已,不过可喜的是,我们已经取得 了一些突破性进展。” 维克 不愿透 露 关于研 究 的详 细 内容 ,但 他表 示 ,这 种” 空气 ” 锂 电池 将 是可 以重复充 电使 用 的,还 将拥有 之 前锂 电池所 没有 的一 些功 能 。” 这个 研究 可 能花 费数年 , 同时也 是一 个具 有 极 高风 险的研 究项 目。” 虽然,维克的小组取得了一定的成果, 但是想要使电动汽车的电池既安全又经济,暂时 还 是 无法 实现 的 ,即便 金属 空气 电池也 是如此 。在金 属 空气 电池 中,空气 中 的氧 气被 当作锂 电极 的反应 物 。IM 研 究员纳 亚说 :” B 这样 电池 就像 一个燃烧 引擎 。现 在是 汽车 吸进空 气使 其与汽油一起燃烧, 将来空气将会用于电化学反应。 ⅢM 预计在 5 ” 年后生产出第一个样品, 而其他研究者则很谨慎地预计,这种研究方案需要耗时几十年。 从世界范围来看,电动汽车的研究者和开发商都把重点放在电池方面, 锂离子电池技术 代 表 了 当前的研 究水平 。2 纪 9 代初 ,索尼 生产 出 了第 一个 小型 的锂离 子 电池 , 由于 O世 0年 具备性能高、 寿命长、充 电时间短等优点,很快就在小型设备如移动电话、笔记本电脑和模 型飞机等方面得到了应用 。有趣的是,在汽车领域最初却没人愿意使用锂离子电池, 锂作 为 电极 材 料不仅 会 导致 电压 过高 ,而 且很容 易与其 他元素 进 行反应 。 目前 ,对 于锂 电池来 说,安全性 、耐用性 、放 电容 量 以及 快速 充 电都是 十分 重要 的,这 几 个要 素缺 一不 可 。 而 , 车 电池 的安全性 、放 电容量 和耐用 性是 相互 联系 、此消彼 长 的, 然 汽 电池制 造 商陷入 两难境 地 ,一方 面 的提 高大 多 以牺 牲其 它方 面为代 价 。
铣削加工中的刀具涂层技术

铣削加工中的刀具涂层技术随着现代制造业的不断发展,铣削加工作为一种重要的机加工方式,在工业生产中扮演着越来越重要的角色。
刀具作为铣削加工中的核心装备,直接影响加工质量、效率和成本。
因此,如何有效地提高刀具的使用寿命,就成为了铣削加工中的一个重要问题。
刀具涂层技术作为一种新的材料应用技术,被广泛地应用于刀具制造领域中,并取得了良好的效果。
一、刀具涂层技术的基本原理刀具涂层技术是一种在刀具表面上附着一层特殊材料的技术。
涂层可以在刀具表面形成一层保护层,有效地提高了刀具的硬度、耐磨性和抗腐蚀性能。
同时,涂层可以使刀具表面形成一层类似于黏着剂的“润滑剂”,使刀具在工作时摩擦减小,从而使加工质量和效率得到明显提高。
刀具涂层技术的基本原理是将特殊材料喷涂、熔覆或镀层在刀具表面上,形成一层附着牢固的涂层。
涂层的厚度一般在几个微米至数十个微米之间,并且涂层层次一般为单层或多层结构。
涂层的选择一般是根据刀具加工材料的不同、工艺要求和加工目的来确定的。
二、刀具涂层技术的分类1.气相沉积涂层技术气相沉积涂层技术是一种在高温高压下,将有机、无机气体和电弧等能量源催化分解、反应形成并沉积在刀具表面上的涂层技术。
具有涂层结构致密、成膜速度快、涂层厚度均匀等特点。
2.电化学涂层技术电化学涂层技术是利用电化学反应将特定的金属或合金沉积在刀具表面上形成致密性涂层的技术。
具有耐腐蚀性、耐磨性和附着力强等优点。
电化学涂层技术应用于镀铬、硬铬、镍、钼等金属或合金。
3.热化学涂层技术热化学涂层技术是在高温下在刀具表面上与基材直接反应形成化合物的技术。
热化学涂层技术涂层坚固、成膜速度快,涂层与基材的化学性能相似,耐磨性和耐蚀性能好,但成本相对较高。
三、刀具涂层技术的应用1.碳化物涂层碳化物涂层是一种含有碳团的型材涂层。
它在制造领域中被广泛应用于刀具加工领域,如车削刀具、铣削刀具、钻孔刀具和转插刀具等。
碳化物涂层具有硬度高、耐磨性、耐腐蚀性、降低摩擦系数等优点。
浅谈涂层刀具的应用现状和发展前景
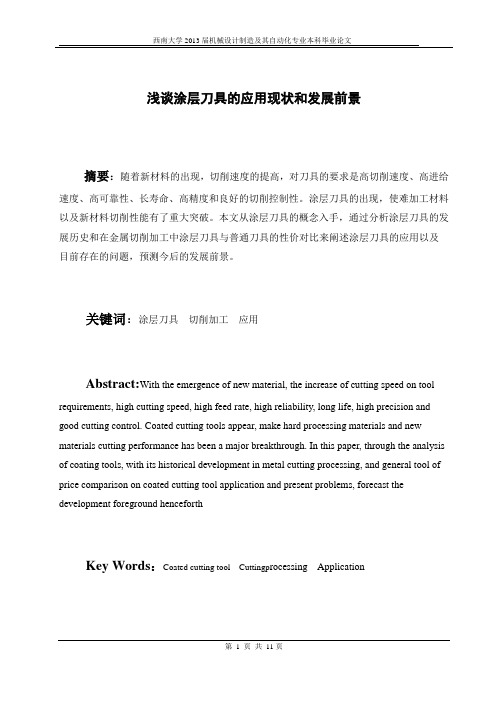
浅谈涂层刀具的应用现状和发展前景摘要:随着新材料的出现,切削速度的提高,对刀具的要求是高切削速度、高进给速度、高可靠性、长寿命、高精度和良好的切削控制性。
涂层刀具的出现,使难加工材料以及新材料切削性能有了重大突破。
本文从涂层刀具的概念入手,通过分析涂层刀具的发展历史和在金属切削加工中涂层刀具与普通刀具的性价对比来阐述涂层刀具的应用以及目前存在的问题,预测今后的发展前景。
关键词:涂层刀具切削加工应用Abstract:With the emergence of new material, the increase of cutting speed on tool requirements, high cutting speed, high feed rate, high reliability, long life, high precision and good cutting control. Coated cutting tools appear, make hard processing materials and new materials cutting performance has been a major breakthrough. In this paper, through the analysis of coating tools, with its historical development in metal cutting processing, and general tool of price comparison on coated cutting tool application and present problems, forecast the development foreground henceforthKey Words:Coated cutting tool Cuttingp rocessing Application引言对于机械行业来说,世界上目前发展的重要项目有:高速精密切削加工,少、无冷却润滑液的切削或干切削,高硬状态下切削加工。
涂层技术的发展和应用PPT资料

须具备高的硬度、耐磨性、耐热性和足 技术的进步起着非常重要的作用涂层刀
够的韧性和强度。刀具表面涂层技术是 具已经成为现代刀具的标志,西方国家
应市场需求发展起来的一种优质表面改 新型数控机床所用切削刀具中有80%左右
性技术,它不仅能大幅度提高刀具使用 使用涂层刀具,而且随着科技的发展,
寿命,而且能满足现代机械加工高效率、涂层刀具的比例将进一步增加目前在制
1.PVD涂层技术的发展现状
物理气相沉积 (PhysicalVapourDeposition--PVD)和 化 学 气 相 沉 积 ( Chemical VapourDeposition—CVD ) 被 广 泛 应 用 于刀具涂层。 TiAlN 是含有抗氧化能力良好的的一种涂层,通常采用 PVD( 物理气相沉积) 方法来制备,在切削过程中 Al氧化而形成 ,从而起到抗氧 化和抗扩散磨损的C作V用D,技在 高术速是切利削 时用,气涂层态刀具的的切先削驱效果反优于应TiC物和T,iN涂层刀具,主要原因是 TiAlN 涂层刀具的硬度抗氧化和 抗在粘对结 系能统通力预高抽过,真尤空原其以是后子由,、于充入T分i适AlN当子涂压间层力刀的反具惰具性应有气很体生高,成的一高般固温选硬用态度Ar涂。作为层气体的放电的载体,溅射气体压力一般处于0. 如果没有技额外术装置。的控C制V,D产的生的涂弧将层会材随机料地在是阴由极表反面随应即气漂移体,靶通材的浸蚀也将是随机不可控,这样将会减少靶材的利用率。 但PV是D,工与艺过9对0环年化境代无不学不同良反,影国应响内,已而符淡合化实目了现前薄绿膜的色制工备,业技的对术发的反展基方础应向研。究物工和作。生成 每个阴极物斑点的产生选高速择的具阴极有材料一喷定射,的离子局流限相当性于总。弧电C流V的D7%和~1热0%。 对度于的刀 下具降生材。料长来说过,C程VD中涂层,目前化只学适用反于硬应质需合金要刀具通,且过因热为其效高的应沉积温度导致涂层沉积后硬质合金的强度、韧性出现一定程 图2-4 Ti-A来l-N实薄膜现的表,面形因貌而:(涂a)层阴极制弧蒸备发过沉积程,(中b)基磁控体溅所射 处 的环境温度一般较高,这在很大程度上 限制了基体材料的选取。对于刀具材料 来说,CVD涂层目前只适用于硬质合金 刀具,且因为其高的沉积温度导致涂层 沉积后硬质合金的强度、韧性出现一定 程度的下降。
刀具涂层技术的应用

刀具涂层技术的应用自20世纪60年代化学气相沉积(CVD)涂层硬质合金刀片问世发来,涂层技术被广泛应用于硬质合金可转位刀具的表面处理。
而20世纪80年代初,TiN物理气相沉积(PVD)涂层高速钢刀具的出现,以使高速钢刀具的性能发生了革命性的变革。
由于涂层技术可有效提高切削刀具的使用寿命,使用刀具获得优良的综合机械性能,大幅度地提高机械加工效率,因此涂层技术已经在切削刀具提高性能的工艺中得到极为广泛的应用于。
刀具涂层技术通常可分为化学气相沉积(CVD)技术和物理气相沉积(PVD)技术两大类,本文拟从这两方面分别介绍国内外刀具涂层技术的应用情况。
1、刀具涂层技术的应用(1)CVD涂层技术的应用CVD是使挥发性化合气体发生分解或化学反应,并在被镀工件上形成沉积成膜的方法。
在CVD工艺中,气相沉积所需金属源的制备相对容易,可实现TiN、TiC、TiCN、TiBN、TiB2、AL2O3等单层及多元多层复合涂层。
CVD涂层镀层密实,涂层与基体结合强度高,附着力强,均匀性好,形状复杂的工件也可得到合金副的镀层,薄膜厚度可达5—12微米,因此CVD涂层具有更好的耐磨性。
但其工艺处理温度高,易造成刀具材料抗弯强度的下降,薄膜内部为拉应力状态,使用中易导致微裂纹的产生,因此只适合于硬质合金车削类刀具的表面涂层,其涂层刀具适合于中型、重型切削的高速加工及半精加工。
自1968年第一批CVD涂层硬质合金刀具问世至今,该涂层技术已发展了近35年。
在这35年间,CVD涂层技术从单一成份发展到多种成份、从单一膜层发展到多元多膜层,经过大量的试验,完成了批量大规模的工业化生产。
如今,CVD涂层硬质合金在涂层硬质合金刀具中占到了80%以上的份额,CVD涂层技术已广泛应用于各类硬质合金刀具。
其涂层工艺的主要发展阶段及应用领域见下表:1968——TiN、TiN——方法CVD——硬质合金刀具、模具涂层1973——TiCN、TiC+AL2O3——CVD ——硬质合金刀具、模具涂层1981——TiC+AL2O3+TiN、AL-O-N——CVD——硬质合金涂层1982——TiCN——MT-CVD——硬质合金刀具涂层1986——Diamond、CBN——CVD、PVD——硬质合金刀具涂层1990——TiN、TiCN、TiC——PCVD——模具、螺纹刀具、铣刀等1993——TiN+TiCN(CVD)+TiN(PVD)——CVD+PVD——硬质合金铣削类刀具涂层1993——厚膜纤维状TiCN——MT-CVD——硬质合金车削类刀具涂层(用于粗、半精加工)从上表可以发现,CVD涂层技术主要用于硬质合金类各种切削刀具。
剃刀刀片涂层专利技术发展分析
剃刀刀片涂层专利技术发展分析剃刀刀片是我们日常生活中必不可少的日用品,其质量和切割效果直接关系到用户的体验和满意度。
近年来,剃刀刀片的涂层技术得到了持续发展和创新,涂层技术的稳定性、耐用性、切割效果均有了大幅提高,为消费者带来了更好的使用体验。
本文将对剃刀刀片涂层技术的发展进行分析和总结。
早期剃刀刀片没有涂层技术,所使用的刀片材料多为不锈钢或其他金属材料。
北京理工大学化工与环境工程学院硕士考生于雯在她的硕士论文《剃须刀刀片涂层工艺如何提高胶水的附着力?》中提到,早期剃须刀刀片的使用寿命较短,容易出现锈蚀和损坏。
这不仅影响了刀片的使用效果,而且会对用户的健康带来隐患。
20世纪70年代,剃刀刀片涂层技术开始应用于生产中。
最早的涂层技术为TiN(氮化钛)涂层,TiN涂层的硬度和耐磨性比不涂层的刀片要高,大大提高了刀片的使用寿命,同时也降低了锈蚀和损坏的风险。
此后,剃刀刀片涂层技术得到了长足发展,涂层材料也从TiN转变为TiC(碳化钛)、CrN(氮化铬)和VC(碳化钒)等材料。
二、剃刀刀片涂层技术的优势1.延长使用寿命:涂层材料能提高刀片的硬度和耐磨性,从而延长其使用寿命。
2.提高切割效果:涂层材料能减小切口摩擦系数,从而提高切割效果和顺滑性。
3.增加使用舒适度:涂层材料能减小刀片表面的残留物,从而减少割伤和过敏等问题,增加使用舒适度。
1.成本:涂层技术的加入,会在一定程度上提高生产成本,可能会导致部分消费者对产品的接受度下降。
2.涂层稳定性:涂层技术对于刀片的稳定性和抗腐蚀性能要求较高,如果涂层稳定性不佳或脱落,对消费者的使用安全会产生影响。
3.涂层环保问题:涂层技术会涉及到一些化学物质,如果不严格遵守环保标准,会对环境产生负面影响。
四、结论剃刀刀片涂层技术是剃刀行业的重要创新之一,得到了广泛应用和市场认可。
涂层技术的发展也彰显了剃刀生产行业对于创新和质量控制的重视。
未来,涂层技术将继续在剃刀生产中发挥重要作用,并为提高产品质量和改善消费者使用体验做出更大贡献。
刀具涂层技术
刀具涂层技术一、概述刀具涂层技术是一种将刀具表面涂上一层特殊材料的技术,目的是提高切削性能、延长使用寿命和降低生产成本。
随着制造业的发展,刀具涂层技术已经成为了现代制造业中不可或缺的重要技术之一。
二、刀具涂层的分类根据不同的涂层材料和工艺,刀具涂层可以分为以下几类:1.物理气相沉积(PVD):是利用真空蒸发、离子镀等方法,在刀具表面形成一层硬质化合物薄膜。
常用的PVD涂层有TiN、TiCN、AlTiN等。
2.化学气相沉积(CVD):是利用化学反应在高温下将气态物质沉积在刀具表面形成一层质量优良的陶瓷薄膜。
常用的CVD涂层有TiC、TiCN、Al2O3等。
3.离子注入(IBAD):是将金属离子注入到刀具表面形成一定深度的硬化区域,增强其耐磨性和抗热性能。
三、刀具涂层的优势1.提高切削速度:由于涂层具有高硬度、低摩擦系数和良好的耐热性能,使得刀具可以承受更高的切削速度,从而提高生产效率。
2.延长使用寿命:涂层可以有效地保护刀具表面不被磨损和氧化,延长其使用寿命。
3.降低生产成本:由于涂层可以延长刀具的使用寿命,减少了更换刀具的次数,降低了生产成本。
4.提高加工质量:由于涂层可以减少表面粗糙度和毛刺,提高加工质量。
四、选择合适的涂层在选择合适的涂层时,需要考虑以下几个因素:1.加工材料:不同材料需要不同类型的涂层。
例如,钢材需要TiN或TiCN等PVD涂层;铸铁需要Al2O3等CVD涂层。
2.加工条件:不同加工条件需要不同类型的涂层。
例如,高速加工需要AlTiN等PVD涂层;重负荷加工需要TiC等CVD涂层。
3.加工要求:不同的加工要求需要不同类型的涂层。
例如,高精度加工需要Al2O3等CVD涂层;高温加工需要ZrN等PVD涂层。
五、刀具涂层的应用刀具涂层技术已经广泛应用于各种行业,如机械制造、汽车制造、航空航天、医疗器械等。
其中,高速钢刀具、硬质合金刀具和陶瓷刀具是最常见的应用对象。
六、总结刀具涂层技术作为现代制造业中不可或缺的重要技术之一,已经成为了提高生产效率、降低生产成本和提高产品质量的重要手段。
涂层刀具的涂层材料、涂层方法及发展方向
涂层刀具的涂层材料、涂层方法及进展方向在切削加工中,刀具性能对切削加工的效率、精度、表面质量有着决议性的影响。
刀具性能的两个关键指标硬度和强度(韧性)之间好像总是存在着冲突,硬度高的材料往往强度和韧性低,而要提高韧性往往是以硬度的下降为代价的。
在较软的刀具基体上涂覆一层或多层硬度高、耐磨性好的金属或非金属化合物薄膜(如TiC、TiN、Al2O3,等)构成的涂层刀具,较好的解决了刀具存在的强度和韧性之间的冲突,是切削刀具进展的一次革命。
涂层刀具是近20年来进展最快的新型刀具。
目前工业发达国家涂层刀具已占80%以上,CNC机床上所用的切削刀具90%以上是涂层刀具。
1涂层刀具、涂层材料及涂层方法涂层刀具的特点涂层刀具结合了基体高强度、高韧性和涂层高硬度、高耐磨性的优点,提高了刀具的耐磨性而不降低其韧性。
涂层刀具通用性广,加工范围显著扩大,使用涂层刀具可以获得明显的经济效益。
一种涂层刀具可以代替数种非涂层刀具使用,因而可以大大削减刀具的品种和库存量,简化刀具管理,降低刀具和设备成本。
但是刀具在现有的涂层工艺进行涂层后,因基体材料和涂层材料性质差别较大,涂层残留内应力大,涂层和基体之间的界面结合强度低,涂层易剥落,而且涂层过程中还造成基体强度下降、涂层刀片重磨性差、涂层设备多而杂、昂贵、工艺要求高、涂层时间长、刀具成本上升等缺点。
常用的涂层材料及性质常用的涂层材料常用的涂层材料有碳化物、氮化物、碳氮化物、氧化物、硼化物、硅化物、金刚石及复合涂层八大类数十个品种。
依据化学键的特征,可将这些涂层材料分成金属键型、共价键型和离子键型。
涂层材料的性质金属键型涂层材料(如TiB2、TiC、TiN、VC、WC等)熔点高、脆性低、界面结合强度高、交互作用趋势强、多层匹配性好,具有良好的综合性能,是最一般的涂层材料。
共价键型涂层材料(如B4C、SiC、BN、金刚石等)硬度高、热胀系数低、与基体界面结合强度差、稳定性和多层匹配性差。
涂层刀具材料研究现状与发展思路
涂层刀具材料研究现状与发展思路摘要:制造业的飞速发展对刀具材料的要求也越来越高,涂层技术实现了涂层材料的特殊优异性能,使刀具的使用寿命和切削性能等都得到了极大的提高。
因此,涂层技术的应用领域正在日益扩大,在制造业中必将显示更加重要的地位。
本文介绍了刀具涂层材料的研究现状,对其制备工艺及分类两方面进行了综述,并探讨了涂层刀具材料的发展趋势。
关键词:纳米涂层;物理气相沉积;化学气相沉积;超硬刀具引言19世纪70年代,用于研究的简单涂层设备开始出现;到20世纪70年代商品化的涂层设备供应于世;20世纪80年代涂层技术进入工业化大生产;21世纪初,涂层技术成为世人瞩目的新技术。
涂层技术是应市场需求发展起来的一种表面处理技术。
近10年来,涂层技术在刀具行业的应用得到了快速普及,涂层刀具已成为切削加工不可或缺的主流刀具。
与此同时,随着切削技术向高速、高效、强力、干式的方向发展,刀具涂层技术成为了左右切削技术发展的主要因素。
由于这项技术可使工、模具表面获得优良的综合机械性能,从而大幅度提高机械加工效率及延长工、模具使用寿命,因此它已成为满足现代机械加工高效率、高精度、高可靠性要求的关键技术之一,而且其应用领域正在迅速扩展。
涂层发展正面临前所未有的机遇。
因此,对于刀具涂层及其性能的研究,并开发满足不同加工条件的高性能刀具涂层,对促进制造业发展具有重要意义。
1.涂层刀具材料的制备及发展现状涂层刀具结合了基体高强度、高韧性和涂层高硬度、高耐磨性的优点,提高了刀具的耐磨性而不降低其韧性。
涂层刀具通用性广,加工范围显著扩大,使用涂层刀具可以获得明显的经济效益[1] 。
涂层技术的发展已从当初单一的TiC、TiN涂层发展为TiC-Al2O3-TiN复合涂层和TiCN、TiAlN等多元复合涂层,涂层的性能有了很大的改善,使用范围不断扩大,涂层刀具的基体材料范围也在扩大,高速钢、硬质合金、陶瓷刀具都可以进行涂层。
新的涂层工艺不断出现,如生产上常用的涂层方法有两种:物理气相沉积(PVD)法如图1和化学气相沉积(CVD)法如图4。
- 1、下载文档前请自行甄别文档内容的完整性,平台不提供额外的编辑、内容补充、找答案等附加服务。
- 2、"仅部分预览"的文档,不可在线预览部分如存在完整性等问题,可反馈申请退款(可完整预览的文档不适用该条件!)。
- 3、如文档侵犯您的权益,请联系客服反馈,我们会尽快为您处理(人工客服工作时间:9:00-18:30)。
2007年12月Dec.2007第24卷第4期Vol.24No.4硬质合金CEMENTEDCARBIDE
!!!!"!"!!!!"!
"综合评述
刀具涂层技术及其发展雒有成(河南理工大学高等职业学院,河南焦作454000)
摘要随着切削技术向着高速、高效、干式的方向发展,刀具涂层技术得到了广泛的应用,并成为了左右切削技术发展的主要因素。本文介绍了各种刀具涂层材料、刀具涂层结构和刀具生长工艺的研究现状。对刀具涂层的发展方向提出了个人见解。关键词涂层刀具涂层材料涂层结构涂层工艺
作者简介:雒有成(1966--),男,本科,讲师。工作单位:河南理工大学高等职业学院。研究方向:机械加工。随着现代化金属切削加工的发展,未来的刀具需要满足高切削速度、高进给速度、高可靠性、长寿命等,并且需要适应高度自动化生产需求。传统无涂层刀具由于高温性能差,易磨损已经无法适应现代高效、高精密加工的发展要求。涂层技术在刀具上的应用为现代化金属加工技术开辟了新的航线[1]。在切削加工中,刀具性能对切削加工效率、精度、加工表面质量等有着决定性的影响。刀具性能的两个关键指标———硬度和强度(韧性)之间又存在着矛盾,硬度高的材料往往强度和韧性低,而要提高韧性往往是以硬度的下降为代价的。涂层技术通过改进刀具力学性能,有效调解了这两者的矛盾,同时刀具的耐磨性、高温强度等也得到大大改善。在相对较软的刀具基体上涂覆一层或多层硬度高、耐磨性好的金属或非金属化合物薄膜(如TiAlN、TiC、TiN、Al2O3等)组成的涂层刀具,是切削刀具发展的一次革命[2]。涂层刀具与未涂层刀具相比,具有明显的优越性:显著降低摩擦系数,改善刀具表面的摩擦学性能和排屑能力;显著提高耐磨性和抗冲击韧性,改善刀具的切削性能,提高加工效率和刀具寿命;提高刀具表面抗氧化性能,使刀具可以承受更高的切削热,有利于提高切削速度及加工效率,并扩大了干切削的应用范围,从而减少或消除切削液对环境的影响。在先进制造业中,硬质合金刀具及高性能高速钢刀具,80%以上都采用了表面涂层技术,CNC机床上所用的切削刀具90%以上是涂层刀具。由于涂层刀具的切削速度高、生产效率高,约80%的加工量由涂层刀具完成。本文重点关注以旋转刀具为对象的涂层技术及其发展。
1刀具涂层材料刀具的涂层材料主要是一些具有高硬度的耐磨化合物。常用的涂层材料有碳化物、氮化物、碳氮化物、氧化物、硼化物、硅化物、金刚石及复合涂层八大类数十个品种[2]。近年来,涂层技术得到了飞速的发展,涂层材料方面,从最早的TiN涂层,已开发出TiCN、(Ti,Al)N、Al2O3、CrN、C3N4、ZrN等硬涂层及超
硬涂层材料,以及MoS2、WS2、WC/C等软涂层材料,从而满足各种切削工艺的要求。1.1含钛硬涂层氮化钛(TiN)是工艺最成熟,应用最早、最广泛的硬涂层材料。它具有较高的化学稳定性,可以大大减少刀具与工件之间的摩擦系数。目前工业发达国家TiN涂层高速钢刀具的使用率已经占高速钢刀具
的50%~70%,有的不可重磨的复杂刀具的使用率已超过90%。但是TiN涂层的耐氧化性较差,使用温度达500℃时,膜层明显氧化而被烧蚀,硬度较低,不能满足现代金属切削对刀具的技术要求[3]。碳氮化钛(TiCN)是通过多元合金化方法,向TiN涂层中加入C元素得到的。由于C元素的引入,涂层的硬度和抗氧化温度都得到了提高。TiCN涂层第24卷在常规加工、温度低于500℃的条件下表现出比TiN及TiAlN涂层更优越的性能———涂层硬度高、表面粗糙度和摩擦系数小。此外,该涂层可以和TiN涂层形成多层膜结构,不但可以保持TiN涂层与基体材料良好的结合和表面抗氧化性能,同时多层涂层形成的TiN/TiCN内界面能改变单一涂层的柱状晶生长结构,提高涂层的韧性,从而提高涂层刀具的切削性能。氮铝化钛系列涂层[(Ti,Al)]N是非常成功的一种涂层材料,具有高硬度、氧化温度高、热硬性好、附着力强、摩擦系数小、导热率低等优良特性,用其加工高温合金、不锈钢、钛合金和镍合金时刀具的寿命比TiN涂层刀具高3 ̄4倍[4]。不仅如此,在(Ti,Al)N涂层中如果有合适的铝浓度,切削加工时在刀-屑界面上容易产生一层硬的、惰性的保护膜,该膜不仅可以阻止涂层进一步被氧化,而且具有较好的润滑性能及隔热性,可以有效地用于高速切削。(Ti,Al)N涂层的机械物理性能优于TiN、TiCN等涂层,并可以与其他涂层配合组成多元多层复合涂层,如TiAlN/Al2O3多层PVD涂层,这种涂层的硬度可以达到HV4000,涂层的层数可以达到400层。目前(Ti,Al)N涂层的发展方向为:提高涂层中的铝含量;改进涂层成分,在(Ti,Al)N涂层中添加C(或Si)作为粘结剂强化涂层的显微结构改善其性能,添加Cr(或O)进一步提高涂层的氧化温度;改善涂层的结构。多层、梯度和纳米化也是其发展趋势。1.2无钛硬涂层AlCrN涂层是具有代表性的一种无钛涂层,与TiAlN相比,它具有更高的红硬性及抗氧化性能,使用温度可以达到1000℃,该涂层工艺适合于硬质合金及高速钢材料涂层,用于铣削和车削加工切削速度可以达到400m/min以上[5]。氧化铝(Al2O3)涂层材料具有非常好的抗氧化磨损和抗扩散磨损性能。Al2O3的高温耐磨性、耐热性和抗氧化能力比TiC和TiN好,月牙洼磨损率低,适合于高速、大切削热切削。但是由于与基体材料的物理、化学性能差别太大,单一的涂层无法制成理想的涂层刀具[6]。CBN涂层的硬度和导热率仅次于金刚石,热稳定性极好,在大气中加热至1000℃也不发生氧化。CBN对于铁族金属具有极为稳定的化学性能,与金刚石不宜加工钢材不同,它可以广泛用于钢铁制品的精加工、研磨等。CBN涂层除具有优良的耐磨损性能外,还可以在相当高的切削速度下加工耐热钢、钛合金、淬火钢,能切削高硬度的冷硬轧辊、渗碳淬火材料和对刀具磨损非常严重的Si-Al合金等。
其它新型开发硬涂层材料包括氮化碳(CNx)、多
晶氮化物超点阵涂层等。如氮化碳(CNx)涂层能够形成β-C3N4,理论上可以计算出其硬度将超过金刚石,已经有氮化碳合成的报道。多晶氮化物超点阵涂层是一种很有希望的新型刀具涂层,多晶TiN/NbN和TiN/VN超点阵涂层的硬度分别为50960N/mm2和
54880N/mm2,超点阵涂层由于层内或层间位错导致
其硬度很高。同时还有CrC和CrN涂层、Hf(Zr,Ti,
Ta等)的碳化物和硼化物涂层和Hf(Zr,Ti,Al,Be等)的氧化物涂层。CrC涂层的硬质合金刀具摩擦系数小(0.1~0.15),抗氧化温度高。由于材料的亲和性,以上含钛硬质合金涂层刀具不适合加工钛和钛合金类材料,而CrC和CrN涂层硬质合金是一种无钛涂层,可有限地切削钛、钛合金、铝以及其它软材料。1.3金刚石涂层工具金刚石薄膜具有接近天然金刚石的高硬度、高导热系数、低摩擦系数、低热膨胀系数等优异性能,这些特性使其在切削刀具领域具有广泛的应用前景。Norton公司指出,CVD金刚石无论厚薄都比PCD硬度高、导热性好和更耐高温。在铣削含SiC的增强型铝基复合材料A356-T6的试验中,Norton公司的一把φ9.54mm的DT-100厚膜金刚石立铣刀,在切削速度为359m/min,即转速为12000r/min时,其寿命为硬质合金铣刀的300倍。CVD金刚石涂层刀具是通过化学气相沉积法在硬质合金、陶瓷等刀具材料基体上沉积一层很薄的金刚石膜制成的。金刚石涂层刀具具有很高的刀具耐磨性和良好的刀具韧性,涂层摩擦系数小,导热性能好,抗冲击性能好,在高硅铝合金、金属基复合材料、工程陶瓷、有色金属、纤维增强聚合物层压制品等材料的切削加工领域应用前景十分广泛,该种刀具制造工艺相对简单,成本较低,尤其可以通过在刀具基体上直接沉积而制造复杂形状金刚石涂层刀具,因而研制开发高性能的CVD金刚石涂层刀具将不仅直接冲击未涂层或其它涂层硬质合金刀具和陶瓷刀具市场,而且还成为PCD聚晶金刚石刀具强有力的竞争对手。尽管国内外制备的金刚石薄膜刀片已有在生产上试用成功的报道,光明的应用前景已经出现,但金刚石涂层刀具仍未真正实现规模化生产。原因有两
雒有成:刀具涂层技术及其发展253・・硬质合金第24卷点,其一,各种陶瓷刀片、聚晶金刚石复合刀片、金刚石厚膜刀片和高性能硬质合金刀片的应用使金刚石薄膜刀片的市场占有份额极为有限;其二,高质量金刚石薄膜刀片的制备工艺欠稳定,切削性能一致性差。国外在金刚石涂层刀具的研究中所反映的主要问题包括提高金刚石薄膜与刀具基体附着强度、增加金刚石薄膜沉积速度率和面积、有效而快速地进行附着强度检测、金刚石薄膜的高效抛光等,其中,有关研究表明[7,8],金刚石薄膜刀具在试用中,因薄膜开裂脱落造成的刀具非正常失效与因正常磨损造成的失效之比为10:1。可见,金刚石薄膜与刀具基体结合强度低是导致刀具非正常失效的主要原因,并成为金刚石薄膜刀具实现产业化的主要障碍,金刚石薄膜刀具制备需要解决的关键问题是金刚石薄膜与刀具衬底之间的附着强度问题,国外围绕这一关键技术,从刀具材料的优选、刀具衬底表面预处理、CVD沉积工艺控制及附着强度的检测评价等方面开展了大量的工作,并取得了重要的研究成果。钨钴类硬质合金和Si3N4陶瓷是作为刀具基体直接沉积金刚石薄膜最常用的材料。但硬质合金中的钴相在CVD的条件下会促使金刚石向石墨转化,是导致金刚石膜附着强度低的重要原因[9]。一般是采取酸液浸蚀表面的方法去钴;Si3N4陶瓷脆性大,只适于精加工,为此须采取SiC晶须增韧方法。文献研究表明[10,11],用机械研磨、离子束轰击、激光照射以及等离子刻蚀等表面预处理方法,可以改变WC-Co基体表面的微观结构和化学成分,使钨钴类硬质合金基体表面成核密度增大,同时抑制Co的催石墨化作用,从而增加金刚石薄膜与刀具基体的结合强度。金刚石薄膜与基体材料热膨胀系数不同导致的内应力也是获得高附着强度金刚石薄膜的又一障碍,文献[12]在WC-Co基体和金刚石薄膜之间沉积一多层中间过渡层,其结构是WC-8%Co/B/TiB2/B/金刚石,中间层既可以作为Co或C的扩散障碍层,又可以缓解因热膨胀系数不同导致的金刚石薄膜与基体间应力梯度,提高金刚石薄膜附着强度。中间过渡层方法是研究提高金刚石薄膜附着强度的一个研究热点问题,该方法对金刚石、多层膜中间层及基体之间的晶格匹配性和热学匹配性要求严格,控制环节多,过程复杂,对设备条件要求较高,离应用到刀具还有较大距离。因此,如果综合各种方法的优点,特别是从产业化的角度,研究一种相对简便的CVD涂层工艺,在低成本地制备高附着强度金刚石薄膜方面取得更好的效果,对于CVD金刚石涂层刀具的推广应用至关重要。如何在获得高附着强度的同时能够尽可能地降低金刚石薄膜摩擦系数和表面粗糙度,也是金刚石涂层刀具实用化过程中的难题。据报道[12]Kazuhisa采用离子注入法往金刚石薄膜中注入碳,使薄膜摩擦系数减小,比无碳薄膜的摩擦系数及磨损率降低两个数量级,因此开展这方面CVD涂层新工艺研究,对于提高金刚石薄膜表面的光洁度,改善金刚石涂层刀具的性能将具有非常重要的意义。1.4软涂层(自润滑涂层)软涂层刀具通常也称为自润滑刀具,追求的目标是低摩擦系数,增加刀具表面的润滑性能,在切削加工中减少工件与刀具之间的摩擦,防止积屑瘤的产生从而提高加工表面质量,延长刀具寿命。在某些情况下,一些材料并不适合采用硬涂层刀具加工,如在航空航天中的一些高强度铝合金、钛合金等。这些材料在加工中非常粘刀,在刀具前刀面生成积屑瘤,不仅增加切削热、降低刀具寿命,而且影响加工表面质量。采用软涂层材料刀具可获得更好的加工效果。通常的软涂层有MoS2、WS2、WC/C、TaS2/Mo等。