PVD涂层技术的发展与应用
物理气相沉积技术的发展与应用
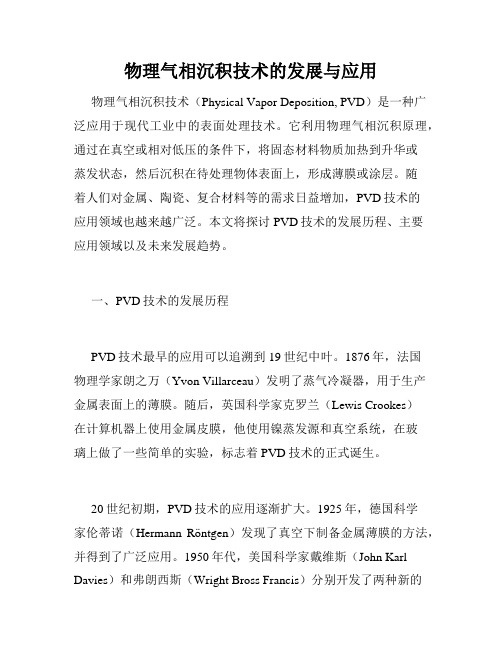
物理气相沉积技术的发展与应用物理气相沉积技术(Physical Vapor Deposition, PVD)是一种广泛应用于现代工业中的表面处理技术。
它利用物理气相沉积原理,通过在真空或相对低压的条件下,将固态材料物质加热到升华或蒸发状态,然后沉积在待处理物体表面上,形成薄膜或涂层。
随着人们对金属、陶瓷、复合材料等的需求日益增加,PVD技术的应用领域也越来越广泛。
本文将探讨PVD技术的发展历程、主要应用领域以及未来发展趋势。
一、PVD技术的发展历程PVD技术最早的应用可以追溯到19世纪中叶。
1876年,法国物理学家朗之万(Yvon Villarceau)发明了蒸气冷凝器,用于生产金属表面上的薄膜。
随后,英国科学家克罗兰(Lewis Crookes)在计算机器上使用金属皮膜,他使用镍蒸发源和真空系统,在玻璃上做了一些简单的实验,标志着PVD技术的正式诞生。
20世纪初期,PVD技术的应用逐渐扩大。
1925年,德国科学家伦蒂诺(Hermann Röntgen)发现了真空下制备金属薄膜的方法,并得到了广泛应用。
1950年代,美国科学家戴维斯(John Karl Davies)和弗朗西斯(Wright Bross Francis)分别开发了两种新的物理气相沉积技术,即电弧放电和磁控溅射。
60年代,PVD技术开始用于半导体和太阳能电池等领域。
70年代和80年代,随着微电子技术、薄膜电子技术、光学涂层技术等的快速发展,PVD技术逐渐成为了各种先进材料获得薄膜的最主要的手段。
二、PVD技术的主要应用领域1、半导体在半导体行业中,PVD技术被广泛应用于制造各种薄膜,如金属、氧化物、硅等。
这些薄膜被用于半导体器件制造的不同步骤,如金属接触、深度磨槽、浅孔孔板、薄膜电容器、光学涂层等。
利用PVD技术在薄膜中添加或掺杂一些特殊的元素,可以提高半导体器件的性能和稳定性。
2、工具涂层PVD技术在工具涂层方面的应用也比较广泛。
pvd真空渐变镀膜
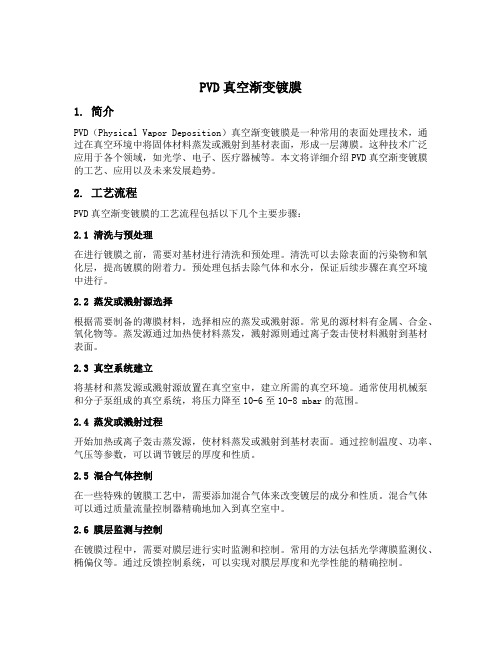
PVD真空渐变镀膜1. 简介PVD(Physical Vapor Deposition)真空渐变镀膜是一种常用的表面处理技术,通过在真空环境中将固体材料蒸发或溅射到基材表面,形成一层薄膜。
这种技术广泛应用于各个领域,如光学、电子、医疗器械等。
本文将详细介绍PVD真空渐变镀膜的工艺、应用以及未来发展趋势。
2. 工艺流程PVD真空渐变镀膜的工艺流程包括以下几个主要步骤:2.1 清洗与预处理在进行镀膜之前,需要对基材进行清洗和预处理。
清洗可以去除表面的污染物和氧化层,提高镀膜的附着力。
预处理包括去除气体和水分,保证后续步骤在真空环境中进行。
2.2 蒸发或溅射源选择根据需要制备的薄膜材料,选择相应的蒸发或溅射源。
常见的源材料有金属、合金、氧化物等。
蒸发源通过加热使材料蒸发,溅射源则通过离子轰击使材料溅射到基材表面。
2.3 真空系统建立将基材和蒸发源或溅射源放置在真空室中,建立所需的真空环境。
通常使用机械泵和分子泵组成的真空系统,将压力降至10-6至10-8 mbar的范围。
2.4 蒸发或溅射过程开始加热或离子轰击蒸发源,使材料蒸发或溅射到基材表面。
通过控制温度、功率、气压等参数,可以调节镀层的厚度和性质。
2.5 混合气体控制在一些特殊的镀膜工艺中,需要添加混合气体来改变镀层的成分和性质。
混合气体可以通过质量流量控制器精确地加入到真空室中。
2.6 膜层监测与控制在镀膜过程中,需要对膜层进行实时监测和控制。
常用的方法包括光学薄膜监测仪、椭偏仪等。
通过反馈控制系统,可以实现对膜层厚度和光学性能的精确控制。
2.7 冷却与退火镀膜完成后,需要进行冷却和退火处理,以提高薄膜的致密性和结晶度。
冷却过程中要避免快速温度变化,以防止薄膜出现应力和裂纹。
3. 应用领域PVD真空渐变镀膜技术在各个领域都有广泛的应用,下面列举几个常见的应用领域:3.1 光学镀膜PVD真空渐变镀膜在光学领域中应用广泛。
通过控制材料的组分和厚度,可以实现对光的透射、反射和吸收特性的调控。
2024年PVD市场前景分析
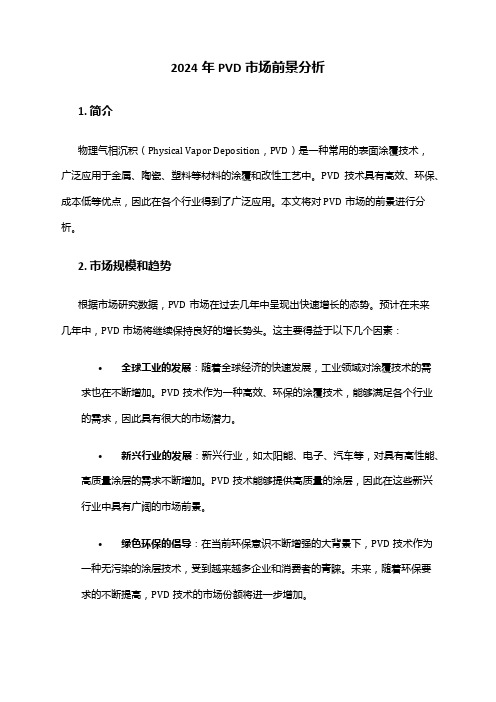
2024年PVD市场前景分析1. 简介物理气相沉积(Physical Vapor Deposition,PVD)是一种常用的表面涂覆技术,广泛应用于金属、陶瓷、塑料等材料的涂覆和改性工艺中。
PVD技术具有高效、环保、成本低等优点,因此在各个行业得到了广泛应用。
本文将对PVD市场的前景进行分析。
2. 市场规模和趋势根据市场研究数据,PVD市场在过去几年中呈现出快速增长的态势。
预计在未来几年中,PVD市场将继续保持良好的增长势头。
这主要得益于以下几个因素:•全球工业的发展:随着全球经济的快速发展,工业领域对涂覆技术的需求也在不断增加。
PVD技术作为一种高效、环保的涂覆技术,能够满足各个行业的需求,因此具有很大的市场潜力。
•新兴行业的发展:新兴行业,如太阳能、电子、汽车等,对具有高性能、高质量涂层的需求不断增加。
PVD技术能够提供高质量的涂层,因此在这些新兴行业中具有广阔的市场前景。
•绿色环保的倡导:在当前环保意识不断增强的大背景下,PVD技术作为一种无污染的涂层技术,受到越来越多企业和消费者的青睐。
未来,随着环保要求的不断提高,PVD技术的市场份额将进一步增加。
3. 市场竞争情况当前PVD市场存在着激烈的竞争。
主要竞争者包括国内外的PVD设备制造商、涂层材料供应商以及涂层服务提供商等。
这些竞争者通过技术创新、产品升级以及降低成本等手段争夺市场份额。
此外,市场上也出现了一些新的参与者,加剧了市场的竞争。
4. 市场机会和挑战PVD市场面临着许多机会和挑战。
其中,市场机会包括:•技术进步带来的机会:新材料、新工艺的出现为PVD技术带来了新的应用领域,如纳米技术、生物医学等领域。
•市场份额的扩大:随着新兴行业的不断发展,对涂层技术的需求将不断增加,这将为PVD市场带来更多的机会。
然而,PVD市场同样面临一些挑战:•高成本和技术壁垒:PVD技术的研发和设备制造需要大量的资金和专业知识,这对于一些中小型企业来说可能是一个挑战。
pvd电镀工艺

pvd电镀工艺PVD电镀工艺摘要:PVD(Physical Vapor Deposition)电镀工艺是一种新型的电镀技术,它通过将材料以固态的形式加热,使其转化为气相,然后在材料表面形成薄膜。
PVD电镀工艺具有很多优势,如高度均匀的薄膜质量、较高的附着力、较低的工件变形以及对环境的友好等。
本文将重点介绍PVD电镀工艺的原理、应用以及未来的发展方向。
第一部分:PVD电镀工艺的原理PVD电镀工艺的原理是利用高能粒子(离子、原子或分子)对材料表面进行沉积而形成薄膜。
PVD电镀工艺通常包括以下几个步骤:1. 蒸发:将金属材料以固态形式加热,使其转化为气相。
这个过程通常发生在真空环境中,以防止杂质的存在。
2. 沉积:将蒸发的金属材料沉积到待镀件表面。
沉积过程中,高能粒子会与金属材料表面发生反应,形成均匀的薄膜。
3. 附着:通过控制沉积条件,使薄膜附着在待镀件表面。
PVD电镀工艺通常具有很好的附着力,可以在各种形状和材料的表面形成均匀的薄膜。
4. 后处理:经过沉积和附着后,薄膜需要进行一些后处理步骤,如退火、抛光等,以提高膜层的性能。
第二部分:PVD电镀工艺的应用PVD电镀工艺由于其优秀的性能,在许多领域得到广泛应用。
以下是一些常见的PVD电镀工艺应用:1. 防腐蚀镀膜:PVD电镀工艺可以镀制出高硬度、高耐磨、高附着力的膜层,能够有效延长物件的使用寿命,提高物件的耐腐蚀能力。
2. 装饰镀膜:PVD电镀工艺可以通过调整沉积条件,制备出具有不同颜色、光泽度和纹理的膜层,用于制作高档家居产品、手表、珠宝等。
3. 刀具涂层:PVD电镀工艺可以制备出高硬度、高刚度的涂层,用于制作刀具,提高刀具的切削性能和耐磨性。
4. 光学薄膜:PVD电镀工艺可以制备出具有特殊光学性能的薄膜,如折射率控制膜、反射膜、透明导电膜等,广泛应用于光学器件和显示器件中。
第三部分:PVD电镀工艺的发展方向随着科技的不断发展和社会对环境友好和可持续发展的需求,PVD 电镀工艺也在不断进步和改进。
PVD技术研究报告
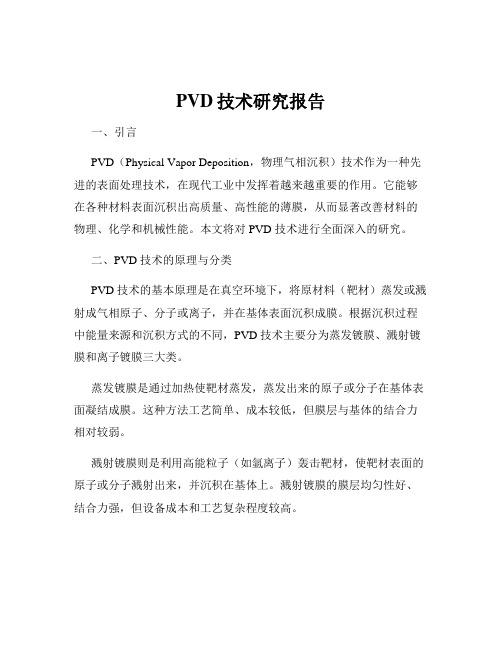
PVD技术研究报告一、引言PVD(Physical Vapor Deposition,物理气相沉积)技术作为一种先进的表面处理技术,在现代工业中发挥着越来越重要的作用。
它能够在各种材料表面沉积出高质量、高性能的薄膜,从而显著改善材料的物理、化学和机械性能。
本文将对 PVD 技术进行全面深入的研究。
二、PVD 技术的原理与分类PVD 技术的基本原理是在真空环境下,将原材料(靶材)蒸发或溅射成气相原子、分子或离子,并在基体表面沉积成膜。
根据沉积过程中能量来源和沉积方式的不同,PVD 技术主要分为蒸发镀膜、溅射镀膜和离子镀膜三大类。
蒸发镀膜是通过加热使靶材蒸发,蒸发出来的原子或分子在基体表面凝结成膜。
这种方法工艺简单、成本较低,但膜层与基体的结合力相对较弱。
溅射镀膜则是利用高能粒子(如氩离子)轰击靶材,使靶材表面的原子或分子溅射出来,并沉积在基体上。
溅射镀膜的膜层均匀性好、结合力强,但设备成本和工艺复杂程度较高。
离子镀膜是在溅射镀膜的基础上,引入了离子束辅助沉积,通过离子的轰击作用改善膜层的性能和结构。
离子镀膜具有膜层致密、硬度高、耐磨性好等优点。
三、PVD 技术的工艺流程PVD 技术的工艺流程一般包括以下几个主要步骤:1、基体预处理为了获得良好的膜基结合力和膜层质量,基体在镀膜前需要进行严格的预处理,包括清洗、除油、除锈、抛光等。
2、抽真空将镀膜室抽至一定的真空度,以减少气体分子对沉积过程的干扰。
3、加热基体根据需要,对基体进行加热,以提高膜层的沉积效率和质量。
4、沉积薄膜通过蒸发、溅射或离子镀等方式,使靶材材料沉积在基体表面形成薄膜。
5、后处理镀膜完成后,对膜层进行适当的后处理,如退火、淬火等,以改善膜层的性能。
四、PVD 技术的应用领域PVD 技术由于其独特的优势,在众多领域得到了广泛的应用。
1、刀具和模具行业通过在刀具和模具表面沉积耐磨、耐腐蚀的薄膜,如 TiN、TiCN 等,显著提高了其使用寿命和加工性能。
PVD涂层技术的发展与

PVD涂层技术在其他领域的应用案例
要点一
总结词
要点二
详细描述
拓宽应用领域、满足多样化需求
除了上述领域,PVD涂层技术还广泛应用于其他领域,如 珠宝首饰、光学仪器、医疗器械等。在珠宝首饰领域, PVD涂层可以用于制造各种彩色宝石和金属饰品的外观效 果;在光学仪器领域,PVD涂层可以提高镜片的抗反射性 能和耐磨损性能;在医疗器械领域,PVD涂层可以用于制 造人工关节、牙科材料等医疗器械,提高其耐磨性和生物 相容性。
航天器涂层
PVD涂层技术可以为航天器提供良 好的耐高温、抗氧化和耐辐射等性 能,保证航天器的长期稳定运行。
电子工业领域的应用
磁头涂层
PVD涂层技术可以为磁头提供耐磨、耐腐蚀和抗氧化等性能,提 高磁头的稳定性和寿命。
太阳能电池涂层
PVD涂层技术可以为太阳能电池提供高反射性和高耐候性等性能, 提高太阳能电池的光电转换效率和长期稳定性。
在制备硬质涂层、耐磨涂层等领域应 用广泛。
溅射镀膜
广泛应用于制备陶瓷、金属复合涂层 等。
PVD涂层技术的选择
根据应用需求选择
不同的PVD涂层技术适用于不同 的应用领域,需要根据具体需求 进行选择。
根据材料性质选择
不同材料的物理和化学性质不同, 需要选择合适的PVD涂层技术以 获得最佳的涂层效果。
根据工艺参数选择
PVD涂层技术的发展 与应用
目 录
• PVD涂层技术的概述 • PVD涂层技术的种类 • PVD涂层技术的应用领域 • PVD涂层技术的发展趋势与挑战 • PVD涂层技术的应用案例
01
PVD涂层技术的概述
PVD涂层技术的定义
01
PVD涂层技术是指通过物理气相 沉积的方法,将金属或非金属材 料涂覆在基体表面,形成一层具 有特殊性能的涂层的技术。
pvd离子镀
pvd离子镀PVD离子镀引言:PVD离子镀(Physical Vapor Deposition)是一种常用的表面处理技术,通过在材料表面沉积薄膜来改善其性能。
本文将介绍PVD 离子镀的原理、应用领域以及一些相关的发展趋势。
一、PVD离子镀的原理PVD离子镀是利用物理方法将金属、合金或陶瓷等材料的原子或分子沉积在基材表面,形成一层薄膜。
其主要原理包括蒸发、溅射和离子镀三个过程。
1. 蒸发:通过加热源将材料加热至蒸发温度,使其原子或分子脱离表面并进入气相状态。
2. 溅射:通过离子轰击的方式,使材料离子从材料表面剥离,并在真空中扩散,最终沉积在基材表面。
3. 离子镀:通过施加电场,将离子加速并定向沉积在基材表面,形成一层致密、均匀的薄膜。
二、PVD离子镀的应用领域PVD离子镀技术广泛应用于各个领域,主要包括以下几个方面:1. 电子行业:PVD离子镀可以制备金属、氧化物或硅等材料的导电薄膜,用于电子元器件、集成电路和显示屏等的制造。
2. 光学领域:通过PVD离子镀,可以制备具有特定光学性质的薄膜,如反射镜、透镜、滤光片等,广泛应用于光学仪器和光电子设备中。
3. 机械工业:利用PVD离子镀技术可以在刀具、模具等工具表面形成耐磨、耐蚀的涂层,提高其使用寿命和耐用性。
4. 汽车工业:PVD离子镀被广泛应用于汽车外观件的镀膜,如车身镀铬、车灯镀膜等,提高汽车的装饰性和耐候性。
5. 医疗领域:PVD离子镀可以制备生物相容性材料的表面涂层,用于人工关节、牙科种植等医疗器械,提高其生物相容性和耐腐蚀性。
三、PVD离子镀的发展趋势随着科学技术的不断进步,PVD离子镀技术也在不断发展和创新。
以下是一些PVD离子镀技术的发展趋势:1. 高效率:研究人员不断改进蒸发源和离子源的设计,提高蒸发和离子镀的效率,减少能源消耗和材料浪费。
2. 多功能性:将不同材料的离子镀技术结合起来,可以实现多层复合薄膜的制备,拓展PVD离子镀的应用领域。
高性能陶瓷涂层的制备与应用
高性能陶瓷涂层的制备与应用高性能陶瓷涂层是一种非常有用的表面处理技术,可以为基材提供保护、改善表面性能的功能性材料。
它广泛应用于航空航天、汽车制造、电子设备等领域,对于提高产品的性能和寿命具有重要作用。
一、高性能陶瓷涂层的制备技术1. 物理气相沉积(Physical Vapor Deposition, PVD)物理气相沉积是一种常用的制备高性能陶瓷涂层的技术。
它通过将陶瓷材料蒸发、离子化,然后沉积在基材表面上。
这种方法可以控制材料的成分及微观结构,从而提高涂层的性能。
常见的PVD方法有蒸发、溅射、离子束沉积等。
2. 溶胶-凝胶法(Sol-Gel)溶胶-凝胶法是一种简单、低温、多功能的涂层制备方法。
其原理是通过在溶液中形成“溶胶”,然后经过凝胶化得到一种凝胶状的材料,最后将凝胶烧结成陶瓷涂层。
这种方法可以精确控制涂层的成分、纳米结构以及厚度,因此被广泛应用于光学涂层的制备。
二、高性能陶瓷涂层的应用领域1. 航空航天领域高性能陶瓷涂层在航空航天领域中有着广泛的应用。
例如,在航空发动机中,涂层可以提供高温氧化、腐蚀、磨损、摩擦的保护和减少摩擦阻力的功能。
此外,高性能陶瓷涂层还可用于航天器的热保护和飞行器的气动外形设计。
2. 汽车制造领域在汽车发动机的气缸内壁上应用高性能陶瓷涂层,可以降低摩擦和磨损,提高燃烧效率,减少油耗和排放物的排放。
此外,高性能陶瓷涂层还可用于汽车零部件的磨损和腐蚀保护。
3. 电子设备领域高性能陶瓷涂层在电子设备中也有很多应用。
例如,在集成电路制造中,采用陶瓷介电涂层可以提高电子器件的绝缘性能和可靠性。
此外,高性能陶瓷涂层还可用于显示屏的抗刮伤、反射控制以及导电层的保护。
三、高性能陶瓷涂层的发展趋势1. 纳米涂层技术随着纳米技术的发展,纳米涂层成为高性能陶瓷涂层的一个重要方向。
纳米涂层具有独特的物理、化学和力学性能,可以在不同领域发挥重要作用。
例如,纳米涂层可以增强材料的硬度、抗氧化性能和耐磨性,提高产品的使用寿命。
2024年PVD涂层设备市场分析现状
2024年PVD涂层设备市场分析现状1. 引言PVD涂层设备是目前广泛应用于各种行业的表面涂层技术之一。
它通过物理蒸发沉积方法,将材料蒸发成蒸汽,并在材料表面形成均匀的薄膜。
本文将分析PVD涂层设备市场的现状,并探讨其发展趋势。
2. 市场规模根据市场研究报告,PVD涂层设备市场在过去几年里快速增长。
预计到2025年,全球市场规模将达到100亿美元。
其中,亚太地区是最大的市场,占据了市场份额的40%。
北美和欧洲地区也是重要的市场,分别占据市场份额的30%和20%。
3. 应用领域PVD涂层设备在多个领域都有广泛的应用。
主要应用领域包括:•汽车行业:PVD涂层设备可用于汽车零部件的表面涂层,提供耐磨、耐腐蚀和防刮擦的功能。
•电子行业:PVD涂层设备可用于电子元件的表面涂层,提供保护和绝缘功能。
•航空航天行业:PVD涂层设备可用于飞机发动机零部件的表面涂层,提供耐高温和耐磨损的特性。
•工具制造业:PVD涂层设备可用于刀具和刀片的表面涂层,提高切削性能和延长寿命。
4. 市场竞争格局PVD涂层设备市场竞争激烈,主要厂商包括:•退火蒸发法:Veeco Instruments、Applied Materials、Oerlikon Balzers 等。
•磁控溅射法:AJA International、Ulvac、Kobe Steel等。
这些厂商通过不断的技术创新和产品升级来提高市场竞争力。
同时,由于市场需求的增长,一些新的参与者也进入市场。
5. 技术趋势PVD涂层设备领域的技术趋势主要包括以下几个方面:•发展向大规模和高效率方向发展,提高生产效率和降低涂层成本。
•绿色环保型涂层材料的研发和应用,减少对环境的污染。
•继续改进涂层质量和性能,提高涂层的硬度、耐磨性和耐腐蚀性。
•发展多功能涂层技术,满足不同行业的需求。
6. 挑战与机遇虽然PVD涂层设备市场增长迅速,但还面临着一些挑战。
其中主要的挑战包括高成本和设备复杂性。
真空镀膜(PVD 技术)
真空镀膜(PVD 技术)1. 真空涂层技术的发展真空涂层技术起步时间不长,国际上在上世纪六十年代才出现将CVD(化学气相沉积)技术应用于硬质合金刀具上。
由于该技术需在高温下进行(工艺温度高于1000ºC),涂层种类单一,局限性很大,起初并未得到推广。
到了上世纪七十年代末,开始出现PVD(物理气相沉积)技术,之后在短短的二、三十年间PVD 涂层技术得到迅猛发展,究其原因:(1)其在真空密封的腔体内成膜,几乎无任何环境污染问题,有利于环保;(2)其能得到光亮、华贵的表面,在颜色上,成熟的有七彩色、银色、透明色、金黄色、黑色、以及由金黄色到黑色之间的任何一种颜色,能够满足装饰性的各种需要;(3)可以轻松得到其他方法难以获得的高硬度、高耐磨性的陶瓷涂层、复合涂层,应用在工装、模具上面,可以使寿命成倍提高,较好地实现了低成本、高收益的效果;(4)此外,PVD 涂层技术具有低温、高能两个特点,几乎可以在任何基材上成膜,因此,应用范围十分广阔,其发展神速也就不足为奇。
真空涂层技术发展到了今天还出现了PCVD(物理化学气相沉积)、MT-CVD (中温化学气相沉积)等新技术,各种涂层设备、各种涂层工艺层出不穷。
目前较为成熟的PVD 方法主要有多弧镀与磁控溅射镀两种方式。
多弧镀设备结构简单,容易操作。
多弧镀的不足之处是,在用传统的DC 电源做低温涂层条件下,当涂层厚度达到0.3 um 时,沉积率与反射率接近,成膜变得非常困难。
而且,薄膜表面开始变朦。
多弧镀另一个不足之处是,由于金属是熔后蒸发,因此沉积颗粒较大,致密度低,耐磨性比磁控溅射法成膜差。
可见,多弧镀膜与磁控溅射法镀膜各有优劣,为了尽可能地发挥它们各自的优越性,实现互补,将多弧技术与磁控技术合而为一的涂层机应运而生。
在工艺上出现了多弧镀打底,然后利用磁控溅射法增厚涂层,最后再利用多弧镀达到最终稳定的表面涂层颜色的新方法。
2. 技术原理PVD (Physical Vapor Deposition) 即物理气相沉积,分为:真空蒸发镀膜、真空溅射镀膜和真空离子镀膜。
- 1、下载文档前请自行甄别文档内容的完整性,平台不提供额外的编辑、内容补充、找答案等附加服务。
- 2、"仅部分预览"的文档,不可在线预览部分如存在完整性等问题,可反馈申请退款(可完整预览的文档不适用该条件!)。
- 3、如文档侵犯您的权益,请联系客服反馈,我们会尽快为您处理(人工客服工作时间:9:00-18:30)。
3.2 氮化碳涂层
近年来,氮化碳(C3N4 ) 作为一种新型的超硬材料,已成为 有实用价值的刀具涂层材料对于高速钢刀具,经过C3N4涂层,对 刀具耐磨性的提高极为显著,其 效 果 超 过 了 TiN涂 层; 高 速 钢 麻 花 钻,经 过C3N4涂层,能使其耐用度大为提高,可取代常用 的TiN涂层麻花钻; 硬质合金刀片( 刀具) ,经过C3N4涂层,亦能提 高刀片( 刀具) 的耐用度,但提高幅度不如高速钢刀具那样大。美 国物理学家A.M.Liu和M.L.Cohen 首先用分子工程理论,设计出 超硬无机化合物氮化碳,根据体弹性模量的计算,可能达到金刚 石的硬度氮化碳作为一种超硬薄膜材料,除了具有高硬度外,还 有低摩擦系数高导热性能很好的化学稳定性和抗氧化性能,能切 削加工铁族元素,作为刀具涂层材料具有广阔的应用前景。
3.刀具PVD涂层技术的应用
3.1 金刚石薄膜
金刚石薄膜的应用在许多方面 取得突破,金刚石涂层工具能加 工非铁合金如合金陶瓷纤维增强 塑料和木材等,具有巨大的前景 金刚石涂层具有一种高度小平面 形的组织结构,这使得在刀片的 前面呈显微粗糙的表面这种粗糙 的金刚石小平面的作用可比喻为 显微断屑器,而在刀片的后面, 这种小平面会导致工件加工表面 光洁度变差当今,汽车工业在加 工硅 铝 合 金( 特 别 是系列) 零件 时,主要是使用金刚石涂层刀具, 金刚石涂层刀具还有望在加工金 属基复合材料碳-碳复合材料和木 材加工业等领域获得应用。
高精度、高可靠性的要求,因此该技术 造业所用硬质合金刀具上采用较多的涂
与材料、加工工艺并称为切削刀具制造 层有TiN、TiC、TiCN、TiAlN以及新出现
的三大关键技术。在刀具表面沉积高硬 的TiCrAlN、CrSiAlN涂层等等,刀具寿
度或低摩擦系数的涂层能改善刀具的耐 命明显提高另外涂层在钻头铰刀齿轮滚
Of Technology, Guangzhou 510006)
ABSTRACT: Physical vapor deposition (physical vapor deposition, PVD) is the use of a physical process, such as thermal evaporation of the material or subject to the phenomenon of particle bombardment, the surface atoms of a substance such as sputtering, depositing a coating from a source material to a controllable transfer material atoms process, which is deposited on the scale of the molecules, atoms level. PVD coating technology with low deposition temperature, the substrate can be prepared multilayer nanocomposites structure, environment friendly and so on . In this paper, a brief overview of the PVD coating technology for tools development, operating principles and its application.
1.PVD涂层技术的发展现状
物理气相沉积 (PhysicalVapourDeposition--PVD)和 化 学 气 相 沉 积 ( Chemical VapourDeposition—CVD ) 被 广 泛 应 用 于刀具涂层。
CVD技术是利用气态的先驱反应物, 通过原子、分子间反应生成固态涂层的 技术。CVD的涂层材料是由反应气体通 过化学反应而实现的,对反应物和生成 物的选择具有一定的局限性。CVD和热 生长过程中,化学反应需要通过热效应 来实现,因而涂层制备过程中基体所处 的环境温度一般较高,这在很大程度上 限制了基体材料的选取。对于刀具材料 来说,CVD涂层目前只适用于硬质合金 刀具,且因为其高的沉积温度导致涂层 沉积后硬质合金的强度、韧性出现一定 程度的下降。
刀具PVD涂层技术的发展与应用
(广东工业大学 机电工程学院,广州 510006)
摘要 物理气相沉积(physical vapor deposition, PVD)是利用 某种物理过程,如物质的热蒸发或受到粒子轰击时物质表 面原子的溅射等现象,实现物质原子从源物质到沉积涂层 的可控转移过程,是在分子、原子的尺度上沉积涂层。 PVD涂层技术具有沉积温度低、对基体影响小、能制备多 层复合纳米涂层结构、绿色环保等特点。本文主要对刀具 PVD涂层技术的发展、工作原理以及其应用做一个简要的 概述。
2.2 阴极弧蒸发沉积技术原理
图2-3阴极弧沉积的示意图 阴极弧蒸发是利用弧蒸发电极材料作为沉积源的PVD沉积手段弧 是由低电压、高电流经过电极材料的气体或蒸汽而产生,其特点是电 弧源产生高度离化和较高能量的等离子体。该方法使用低电压,高电 流在阴极局部放电,全部电流集中于阴极表面上一个或多个小的发亮 斑点,其电流密度非常高;电压仅仅需要接近被蒸发材料的气体或蒸 汽的离化电势。当高的电流密度、低电压的电子束经过高真空环境下 的近距离的电极时形成弧,并在表面形成蒸发材料而组成等离子体。 通常为了点燃弧,两电极会在起弧的瞬间接触。阴极上的接触点
3.3 TiN、TiC基涂层
TiC是一种高硬度的耐磨化合物,有良好的抗后刀面磨损和抗月 牙洼磨损能力。 TiN涂层材料是目前应用最广的一种薄膜材料,它的 硬度稍低,但它与金属的亲和力和润湿性能好,在空气中抗氧化能力 比TiC好,但由于它的耐高温抗氧化性能不高限制了它的更广泛的应 用为改善单层薄膜的性能,涂层的 多 元 化( 加入其它合金元素) 和 多 层化成为了研究的热点。
关键词 PVD 刀具涂层 溅射 纳米复合结构
The Development And Application Of PVD Coating Technology For Tools
Huangjian (Institute of Manufacturing Technology, Guangdong University
PVD技术有以下几种类型: 1.阴极电弧法(CathodeArcDeposition) 2.热阴极法(Hot CathodePlating)
3.磁控溅射法(MagnetronSputter Plating) 4.磁控溅射附加阴极电弧法
目前国内已较多采用的技术, 可用于多种薄膜的制备。
5.空心阴极附加磁控溅射及阴极电弧 法
图2-2 溅射沉积示意图
图2-2为溅射沉积薄膜示意图,靶材是需要溅射的材料,作为阴
极。阳极可以接地,也可以是处于浮动电位或是处于一定的正、负
电位。在对系统预抽真空以后,充入适当压力的惰性气体,一般选 用Ar作为气体放电的载体,溅射气体压力一般处于0.1~10Pa的范围 内。Ar原子在正、负电极高压的作用下电离为Ar+和可以独立运动的 电子,其中电子飞向阳极,带正电的Ar+离子在高压电场的加速作用 下高速飞向作为阴极的靶材,并在与靶材的轰击过程中释放其能量。 靶材原子在Ar+离子高速轰击下获得足够的能量脱离靶材的束缚而飞 向基体形成薄膜,其次,离子与靶材的碰撞还会引起阴极辐射二次
称之为“阴极点”,阴极点的电流密度达到10A/cm2,高的电流密度 引起弧侵蚀并完成蒸发材料的离化。靶材侵蚀过程中,参与放电的导 电介质由高度离化的阴极材料所组成,这是由阴极斑点中强烈的金属 蒸气发射所产生。阴极材料的蒸发是由于阴极表面局部的高温所造成。 非常高的功率密度形成小的熔池。每个阴极斑点产生高速的阴极材料 喷射,离子流相当于总弧电流的7%~10%。如果没有额外装置的控制, 产生的弧将会随机地在阴极表面随即漂移,靶材的浸蚀也将是随机不 可控,这样将会减少靶材的利用率。为了使靶材的侵蚀过程处于可控 状态,通常在阴极背后加一磁控系统来控制弧在靶材表面的运动(类 似于磁控溅射控制电子的运动),用以控制靶材的侵蚀。
磨、耐腐蚀等特性,并有效地解决了刀 刀丝锥上也都获得很好的应用效果随着
具材料中硬度与强度之间的矛盾。
科技的发展,刀具涂层技术将不断提高,
刀具涂层材料也日新月异 。
1. PVD涂层技术的发展现状 2. PVD技术的工作原理和主要技术
2.1 溅射沉积技术原理 2.2 阴极弧蒸发沉积技术原理 3. 刀具PVD涂层技术的应用 3.1 金刚石薄膜 3.2 氮化碳涂层 3.3 TiN,TiC基涂层 4. PVD技术存在的问题 4.1 技术上存在的问题[22] 4.2 涂层设备开发制造上存在的问题 4.3 整体配套性差, 应用基础研究缺乏 5. 未来发展方向
电子、离子、光子等。在溅射过程中,由于在高速离子的轰击作用
下离开靶材的溅射原子的无方向性,导致很多溅射原子不能沉积在
基体形成薄膜,降低了沉积效率和沉积速率;另外,低的气体离化
率影响了薄膜沉积粒子的能量,沉积粒子的表面扩散能力有限而不
能得到致密的薄膜结构,与此同时,低的气体离化率也导致了低的 靶材溅射率而降低了薄膜的沉积速率。
须具备高的硬度、耐磨性、耐热性和足 技术的进步起着非常重要的作是 具已经成为现代刀具的标志,西方国家
应市场需求发展起来的一种优质表面改 新型数控机床所用切削刀具中有80%左右
性技术,它不仅能大幅度提高刀具使用 使用涂层刀具,而且随着科技的发展,
寿命,而且能满足现代机械加工高效率、涂层刀具的比例将进一步增加目前在制
图2-1溅射和阴极弧蒸发沉积示意图
2.1 溅射沉积技术原理
溅射沉积是在由低压放电气体组成的等离子体环境中完成,它利用 带有电荷的离子在电场中加速后具有一定动能的特点,将离子引向欲 被溅射的靶电极。在离子能量足够的情况下,靶表面的原子在入射离 子的轰击下被溅射出来。这些被溅射的原子带有一定的动能,并且会 沿着一定的方向射向基体,从而实现在基体上薄膜的沉积。