轮对轴承跑合试验台技术部分
机车驱动装置例行跑合试验台信号处理与分析
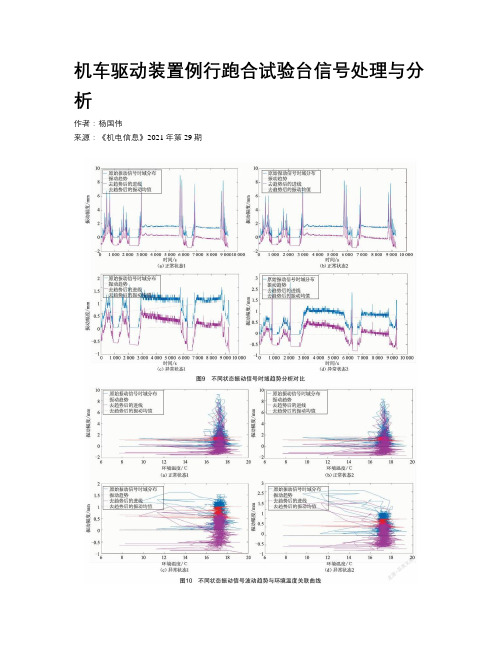
机车驱动装置例行跑合试验台信号处理与分析作者:杨国伟来源:《机电信息》2021年第29期摘要:高鐵、动车和地铁已经成为现代人们出行的重要交通工具,而其驱动装置的质量是出行的重要保障。
随着列车运行频率和工作时长的增加,驱动装置受损或老化成为不可避免的情况。
为了确保驱动装置安全可靠,在新造和大修时,需要对驱动装置进行跑合试验,来检验驱动装置零配件和装配的质量。
机车驱动装置跑合试验台,通过检测机车驱动装置的振动信号(振动烈度,mm/s)和温升,来判别驱动装置零配件和装置的质量,从而把故障排除在源头之外。
鉴于此,详细介绍了机车驱动装置例行跑合试验台振动信号的采集过程,通过小波分析等方法检测故障或亚健康状态,从而判断驱动装置的实际运行状况。
关键词:机车驱动装置;例行跑合试验;健康监测;小波分析;趋势分析0 引言机车驱动装置的例行试验是针对交流异步电机装配上减速齿轮箱后的空载运行试验,或只带轮对的轮对悬空试验。
通常可以由多种形式获取驱动装置的状态,如磁链、振动、温度、瞬时角速度、气隙转矩等。
其中对驱动装置的振动进行监测和诊断,是掌握其运行状态和发现故障的重要技术手段。
随着我国高速铁路、城市轨道交通等领域的高速发展,监测驱动装置的安全越来越重要,但是想要实时准确地判断驱动装置的运行状态,仅仅依靠现场工作人员的判断是远远不够的,需要研发一套优秀的智能监测平台。
工程实际检测到的信号往往混有不同程度的噪声,从振动角度来说,噪声就是无规律的振动;从信号处理角度来说,噪声分为白噪声和有色噪声,白噪声是指频率分量的能量均匀分布在整个给定带宽内,有色噪声是指频率分量的能量集中在给定带宽的某个频带内;从广义上讲,可以统称信号中有用成分以外的所有成分为噪声。
对于采集到的机车驱动装置的振动信号处理分析是机车驱动装置例行试验中的核心技术之一。
小波分析作为一种有效分析离散不规则信号的方法,可以通过振动信号来判断机器所处的状态。
而运用趋势分析可以弥补小波分析中选择函数困难的缺点,并对振动信号进行降噪处理。
轨道交通车辆轴承耐久度试验方法和标准
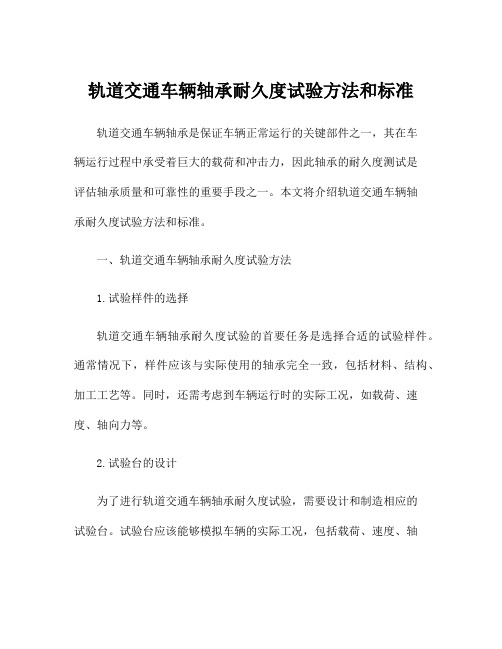
轨道交通车辆轴承耐久度试验方法和标准轨道交通车辆轴承是保证车辆正常运行的关键部件之一,其在车辆运行过程中承受着巨大的载荷和冲击力,因此轴承的耐久度测试是评估轴承质量和可靠性的重要手段之一。
本文将介绍轨道交通车辆轴承耐久度试验方法和标准。
一、轨道交通车辆轴承耐久度试验方法1.试验样件的选择轨道交通车辆轴承耐久度试验的首要任务是选择合适的试验样件。
通常情况下,样件应该与实际使用的轴承完全一致,包括材料、结构、加工工艺等。
同时,还需考虑到车辆运行时的实际工况,如载荷、速度、轴向力等。
2.试验台的设计为了进行轨道交通车辆轴承耐久度试验,需要设计和制造相应的试验台。
试验台应该能够模拟车辆的实际工况,包括载荷、速度、轴向力等。
同时,试验台还应该具备高精度的控制系统,可以对试验参数进行精确控制和记录。
3.试验条件的设置轨道交通车辆轴承耐久度试验中,试验条件的设置非常重要。
应该参考轴承的设计规范和实际工况,确定试验参数,如载荷、速度、轴向力等。
在试验过程中,还需要不断监测和调整试验条件,以保证试验的准确性和可重复性。
4.试验过程的监测和记录在轨道交通车辆轴承耐久度试验过程中,需要对试验样件的状态进行监测和记录。
可以使用各种传感器和仪器,如应力传感器、振动传感器、温度传感器等,对样件的载荷、振动、温度等参数进行实时监测和记录。
通过对这些数据的分析,可以评估轴承的耐久性能。
5.试验结束后的评估和分析试验结束后,需要对试验结果进行评估和分析。
可以通过对试验样件的破坏分析、表面形貌观察等手段,来评估样件的耐久性能。
同时,还可以对试验数据进行统计和分析,得出相关的参数和曲线,为轴承的设计和改进提供参考依据。
二、轨道交通车辆轴承耐久度试验标准1.《轴承-耐久性试验(循环载荷,低接触应力)》该标准适用于各种轴承的耐久性试验。
其中,循环载荷试验是轴承耐久性试验的核心内容之一,可以评估轴承在正常工作状态下的寿命。
2.《电力机车和动车组车辆轴承试验方法》该标准适用于电力机车和动车组车辆轴承的试验方法。
轮毂轴承试验规范修改_3

轿车轮毂轴承单元试验规范(草稿)轴承厂家需要提供的试验报告有:轮毂单元轮毂螺栓压人牢固性试验、轮毂单元泥浆/盐水喷溅试验、轮毂单元耐久性试验、轮毂单元法兰盘旋转疲劳试验、带ABS轮毂单元传感器电子信号检测、轮毂单元高温耐久性试验、轮毂单元静态侧向压力试验、漏脂试验我公司需要进行的试验为:轮毂单元泥浆/盐水喷溅试验、轮毂单元耐久性试验、带ABS轮毂单元传感器电子信号检测、轮毂单元法兰盘旋转疲劳试验规范、漏脂试验轮毂轴承泥浆/盐水喷溅试验规范作本试验前,轴承需经过24小时高低温交替循环理化处理,循环如下:高温(107±5℃)3小时,低温(-40±5℃)3小时注意事项:1、高低温交换时要让样件温度恢复到室温,防止样件的金属部分产生裂纹等损伤;2、需要加紧内圈,防止水分进入;3、防止对密封圈划伤磕碰;4、作完高低温后要将水分处理干净,避免水分进入轴承。
一、记录形式所有的试验数据都要记录在试验记录单上。
二、设备要求试验设备应满足各试验参数的要求,且符合试验方法的要求。
1 保持输入负荷不超过5%。
2 保证载荷循环时间不超过3%。
3 保证试验转速误差不超过2%。
4 监测试验轴承单元试验时的振动值。
5 保证泥浆/盐水的喷溅循环按规定要求执行。
6 保证载荷、电流、试验温度、振动值超标时能自动停机。
7 保证水泵的流量。
8 保证泥浆/盐水的配制比例,并混合均匀。
9 有能保证混合液循环的水箱和管路。
10 所有的控制元件应校准,且在规定的到期时间内。
11 在样品的非基准面上逐套编号,不得重号或缺号,轴承编号的位置应一致。
三、试验方法1 定义径向负荷是一垂直于轴承旋转轴线且作用于车轮中心线的一恒力。
轴向负荷是一平行于试验轴承旋转轴线的一周期性循环力。
它与旋转轴线的距离等于车轮滚动半径。
2 喷水管口距离轴承密封件表面距离为20mm。
3 水管直径为 9.5mm。
4 如果试验轴承出现任何包括面积为1mm2或更大的剥落,则应视为失效。
铁路机车、车辆、动车组转向架滚动轴承试验技术分析

铁路机车、车辆、动车组转向架滚动轴承试验技术分析发布时间:2021-07-12T01:36:33.361Z 来源:《中国科技人才》2021年第11期作者:林方勇刘缙熹[导读] 轴承应用性能需要通过轴承试验进行检测,针对铁路车辆、机车和动车组的转向架滚动轴承的质量检测,缺少系统化的试验技术方案,为此必须强化该方面的研究。
中车大连机车车辆有限公司辽宁大连 116021摘要:用于铁路车辆、机车和动车组的转向架滚动轴承的试验方法比较少,也不够系统化,因此很难检测出滚动轴承成品的质量,进而滚动轴承可能会在今后的应用中出现问题。
所以,加强此方面的研究,总结了主发电机轴承、牵引电机轴承、抱轴箱轴承、轴箱轴承、全悬挂空心轴承的试验方案以及试验台架,为今后铁路车辆用的轴承生产质量检测提供支持,以保证制造的轴承有良好性能。
关键词:铁路机车;车辆;动车组;转向架;滚动轴承试验技术轴承应用性能需要通过轴承试验进行检测,针对铁路车辆、机车和动车组的转向架滚动轴承的质量检测,缺少系统化的试验技术方案,为此必须强化该方面的研究。
1、滚动轴承试验技术研究背景铁路普通车辆、机车、动车组中应用的轴承均需集中在转向架上,车体上部应用的轴承,比如内燃机车中主发电机轴承的尺寸比较大,这是一种大型的滚动轴承,具有一定特殊性。
对轴承进行类型划分,包含了四点球轴承、深沟球轴承、调心滚子轴承、双列圆锥滚子轴承、双列圆柱滚子轴承、单列圆锥滚子轴承、单列圆柱滚子轴承[1]。
轴承规格多种多样,针对其进行检验的方法是轴承制造领域中基础的检验方法,但是能够匹配上动车车组、车辆和机车的试验方法比较少。
国内国外都有相应的试验标准和方法,但是以动车、车辆和机车的转向架用轴箱轴承台架试验方法为主,缺少其他种类轴承的系统化试验方法。
如果处于新品研制阶段的轴承,不能以试验方式获得此种轴承产品的使用性能,那么将会在实际应用中生成很多故障,类似动车组的轴承故障、和谐机车的故障等,最终造成多起批量的机破事故,这让铁路用户和主机制造商遭受了非常严重的经济损失[2]。
一种新型动车组轴承匀脂跑合机

工艺与装备
一种新型动车组轴承匀脂跑合机
周海泉,周文锦
(江西奈尔斯西蒙斯赫根赛特中机有限公司,南昌 330096)
摘要:针对现有动车组轴箱轴承匀脂机能耗高,效率低,无法进行负载跑合,匀脂跑合速度低等问题,将普遍采 用的轴箱固定、驱动轮对转动的匀脂模式改变为轮对固定、驱动轴承外圈旋转的匀脂模式,设计了一种新型动 车组轴箱轴承匀脂跑合机,通过试验证明了该设备匀脂效果良好。 关键词:滚动轴承;双列圆柱滚子轴承;轴箱轴承;润滑脂;均匀分布 中图分类号:TH133.33+2;TU502+.1 文献标志码:B DOI:10.19533/j.issn1000-3762.2021.07.007
轴承外圈滚道直径为 210mm,按动车组运行速度
200km/h及 300km/h可计算滚子线速度 v1 和 v2 范围为
200×195285≤
v1 ≤
200×158, 790
(1)
300×195285≤ v2≤ 300×175980,
(2)
由(1),(2)式可得 v1 为 569.37~666.67m/min, v2为 854.05~1000m/min。
图 1 匀脂跑合机整体结构示意图 Fig.1 Diagram ofoverallstructureofgreasehomogenizer
表 1 新型匀脂跑合机主要技术参数 Tab.1 Maintechnicalparametersofnewgreasehomogenizer
参数 下压装置行程 /mm 升降装置行程 /mm 主轴转速 /(r·min-1) 主电动机功率 /kW 轮对轨距 /mm 轴承外圈直径 /mm 轮对踏面直径 /mm 机床总功率 /kW
图 6 匀脂跑合前后染色润滑脂状态 Fig.6 Dyeinggreasestatebeforeandaftergreasehomogeni
TSD5603G 车轮轴承磨损耐久台架试验方法

丰田公司 第 次修改 翻译 译校起草:车辆工程部 注意:从接收本标准开始,本标准的使用者需保证遵守以下保密义务。
⑴本标准的使用者,在相关的工作结束不再需要本标准时,或在现行的标准文本修订时,应将标准文本粉碎、焚烧消毁或退还丰田公司。
车轮轴承磨损耐久台架试验方法1.适用范围标准规定了汽车前轴用车轮轴承磨擦点蚀情况评价试验方法。
备注: 本标准{ }中给出的单位和数值是基于常用的工程单位制,以供参考。
2.术语和定义本标准使用的术语如下定义(1)磨损磨损是指当两个部件的接触表面有微量的相对反复滑动时,接触表面产生的损伤。
在本标准中是指表面产生点蚀,也就是在车轮轴承的内外滚道、球或滚子上产生红锈。
(2)轴向负荷,径向负荷轴向负荷是指作用于轮胎与地面接触点的横向负荷,径向负荷是指作用于轮胎与地面接触点的垂直负荷。
(3)预加负荷预加负荷是指当轴承被压入轮轴和轮毂时,在轴承上产生的压力。
通常是由车轮转动时产生的启动扭矩或动磨擦扭矩表示。
(4)最大点蚀深度最大点蚀深度是指轴承的内外滚道所有表面上产生磨擦点蚀的最大深度。
(5)总的点蚀深度总的点蚀深度是指在轴承的内外滚道表面上产生的点蚀深度的总和,如内表面总的点蚀深度是指在内滚道表面上产生的点蚀深度的总和。
3.试件试件是从按标准程序生产、并检验过的产品中抽取,且必须通过如下所示的影响精度的参数检测。
(1)内外滚道表面粗糙度及其他表面质量(2)内外滚道表面外廓(滚道窝深等)(3)滚道接触角其他项目如果需要也应进行检测。
如:表面硬度及材质4.试验设备4.1 试验设备的结构型式原则上可以使用任何型式的试验设备,只要能产生一个动负荷(或振动)和一个静负荷,如图1所示:(1) 驱动装置(2) 固定装置(3) 试验试件(4) 负荷传递臂(5) 径向负荷发生器(6) 轴向负荷发生器图1 试验设备简图4.2 试验设备的功能试验设备应满足下面功能的需要:(1)转速:2000r/min(2)径向负荷:能产生到 4HZ的脉动负荷。
TBT3017.2-2016《机车车辆轴承台架试验方法第2部分:牵引电机滚动轴承》(第1号修改单)
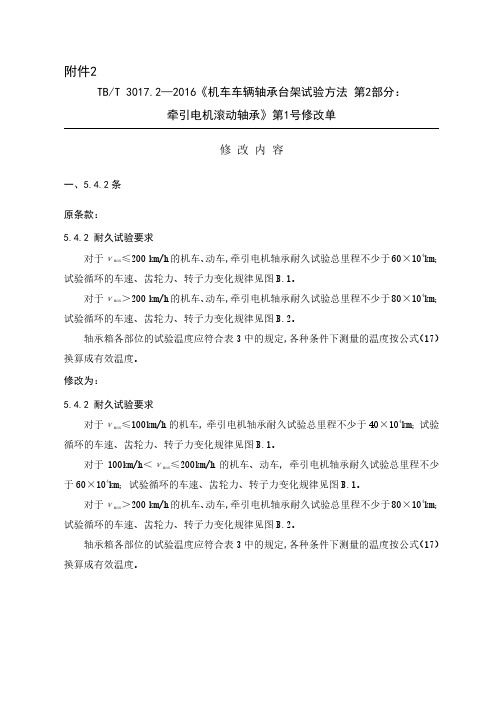
附件2
TB/T 3017.2—2016《机车车辆轴承台架试验方法第2部分:
牵引电机滚动轴承》第1号修改单
修改内容
一、5.4.2条
原条款:
5.4.2 耐久试验要求
对于νmax≤200 km/h的机车、动车,牵引电机轴承耐久试验总里程不少于60×104km;试验循环的车速、齿轮力、转子力变化规律见图B.1。
对于νmax>200 km/h的机车、动车,牵引电机轴承耐久试验总里程不少于80×104km;试验循环的车速、齿轮力、转子力变化规律见图B.2。
轴承箱各部位的试验温度应符合表3中的规定,各种条件下测量的温度按公式(17)换算成有效温度。
修改为:
5.4.2 耐久试验要求
对于νmax≤100km/h的机车,牵引电机轴承耐久试验总里程不少于40×104km;试验循环的车速、齿轮力、转子力变化规律见图B.1。
对于100km/h<νmax≤200km/h的机车、动车,牵引电机轴承耐久试验总里程不少于60×104km;试验循环的车速、齿轮力、转子力变化规律见图B.1。
对于νmax>200 km/h的机车、动车,牵引电机轴承耐久试验总里程不少于80×104km;试验循环的车速、齿轮力、转子力变化规律见图B.2。
轴承箱各部位的试验温度应符合表3中的规定,各种条件下测量的温度按公式(17)换算成有效温度。
二、表B.1
原表:
表B.1 8h循环工况对应时间
修改为:
表B.1 8h循环工况对应时间
三、表B.2
原表:
表B.2 4h循环工况对应时间
修改为:
表B.2 4h循环工况对应时间。
铁道车辆轮对及轴承的结构与检修

铁道车辆轮对及轴承的结构与检修一、引言铁道车辆轮对及轴承是铁路运输中的重要组成部分,对车辆的牵引、支撑和导向起着关键作用。
轮对是铁道车辆与铁轨之间的接触部分,承受着车辆的重量和牵引力,而轴承则负责支撑和导向轮对的运动。
本文将重点介绍铁道车辆轮对及轴承的结构和检修方法。
二、铁道车辆轮对的结构铁道车辆轮对由车轮、轮轴、轴箱和轴承组成。
车轮是直径较大的圆盘状零件,由高强度钢材制成。
轮轴是连接两个车轮的轴杆,通常采用优质合金钢或碳素结构钢制造。
轴箱是轴承座的外壳,起到固定轮轴和减少摩擦的作用。
轴承则用于支撑轮轴并减少摩擦。
三、轴承的结构和类型轴承是铁道车辆轮对中的关键部件,其结构大致可分为内圈、外圈、滚动体和保持架。
内圈与轴轴颈配合,外圈与轴箱孔配合,滚动体则位于内圈和外圈之间,通过滚动减少摩擦力。
保持架则用于保持滚动体在轴承内的正确位置。
根据轴承的结构和使用条件,轴承可分为滚动轴承和滑动轴承两种类型。
滚动轴承由滚动体和保持架组成,常见的有球轴承、圆锥滚子轴承和圆柱滚子轴承。
滑动轴承则是利用润滑油膜实现轴与轴承之间的相对滑动,常见的有滑动滚子轴承和滑动片轴承。
四、轮对及轴承的检修方法1. 轮对的检修方法轮对的检修主要包括轮缘磨削、轮轴检查和轮对动平衡。
轮缘磨削是为了保证轮对与轨道之间的良好接触,避免轮缘磨损过快或轮轴偏心。
轮轴的检查则包括对轮轴的表面、直径和长度进行检测,以确保其符合技术要求。
轮对的动平衡是为了减少车辆在高速运行时的振动,提高运行的平稳性。
2. 轴承的检修方法轴承的检修主要包括清洗、检查和润滑。
清洗轴承时,应使用适当的溶剂将轴承内外的污垢清除干净。
检查轴承时,需要检查内外圈的表面是否有损伤或磨损,滚动体是否有裂纹或损坏,保持架是否变形等。
润滑是轴承正常运转的关键,应根据工作条件和要求选择合适的润滑脂或润滑油进行润滑。
五、结论铁道车辆轮对及轴承是铁路运输中不可或缺的组成部分,其结构和性能的良好与否直接影响着车辆的运行安全和平稳性。