多孔氧化锆陶瓷的设备制作方法与制作流程
二氧化锆的生产工艺流程

矿产资源开发利用方案编写内容要求及审查大纲
矿产资源开发利用方案编写内容要求及《矿产资源开发利用方案》审查大纲一、概述
㈠矿区位置、隶属关系和企业性质。
如为改扩建矿山, 应说明矿山现状、
特点及存在的主要问题。
㈡编制依据
(1简述项目前期工作进展情况及与有关方面对项目的意向性协议情况。
(2 列出开发利用方案编制所依据的主要基础性资料的名称。
如经储量管理部门认定的矿区地质勘探报告、选矿试验报告、加工利用试验报告、工程地质初评资料、矿区水文资料和供水资料等。
对改、扩建矿山应有生产实际资料, 如矿山总平面现状图、矿床开拓系统图、采场现状图和主要采选设备清单等。
二、矿产品需求现状和预测
㈠该矿产在国内需求情况和市场供应情况
1、矿产品现状及加工利用趋向。
2、国内近、远期的需求量及主要销向预测。
㈡产品价格分析
1、国内矿产品价格现状。
2、矿产品价格稳定性及变化趋势。
三、矿产资源概况
㈠矿区总体概况
1、矿区总体规划情况。
2、矿区矿产资源概况。
3、该设计与矿区总体开发的关系。
㈡该设计项目的资源概况
1、矿床地质及构造特征。
2、矿床开采技术条件及水文地质条件。
全瓷牙CAD·CAM制作流程

7.牙冠底部参数倒凹
1. 禁止填除倒凹 单选框若选中,软 件将不在自动填除倒凹。
2. 聚合度 后面的角度越大,会在填 倒凹的基础上进一步变大牙冠颈缘 部分开口 正比关系
3. 不要填除颈缘线附近的区域 颈缘 网上一定高度不填除倒凹,很有用。
4. 预设铣削 直径代表你加工时最细 的铣刀直径 +0.2就可以了 。越大 会对型态有一定影响,切断颌面变 空。
13.自由造型 解剖型态
14.使用釉膏进行上釉,使颜色更有层 次感,更接近真实牙(如有需要也可 以先进行外染) 。
14.自由造型适应调整
14.使用釉膏进行上釉,使颜色更有层 次感,更接近真实牙(如有需要也可 以先进行外染) 。
15.自由造型适应调整
14.使用釉膏进行上釉,使颜色更有层 次感,更接近真实牙(如有需要也可 以先进行外染) 。
6.牙冠底部参数边界
边界的作用是做颈缘的加厚(由于 加工中颈缘部分受力情况最差,大 部分模型不具备肩台) 。
1.从颈缘开始水平延伸一定宽度
2.倾斜是在水平基础上按照 角度 参数值斜向上延伸一定的宽度
3.角度 水平和倾斜之间的夹角
4.垂直 在倾斜基础上垂直向上延 伸,不推荐使用。
5.边缘线以下 颈缘线整体移动到 颈缘线以下一定高度 最大0.08
2.桥体连接杆顶住石膏模型,导致不能就位。由于桥体设计连接 杆在最后阶段添加,连接杆的添加不考虑和模型存在干涉的 行为。我们可以对设计完成后的桥体进行修改,具体点击右 键对已完成修复体自由造型,修改和模型干涉的部分,若已 烧结完成则打磨处理。
3.设计软件中错误的设置了禁止添图倒凹或者开始结束参数。 4.扫描仪采集时分离代型没有安装到位,导致数据采集是错误的。
氧化锆是什么材料
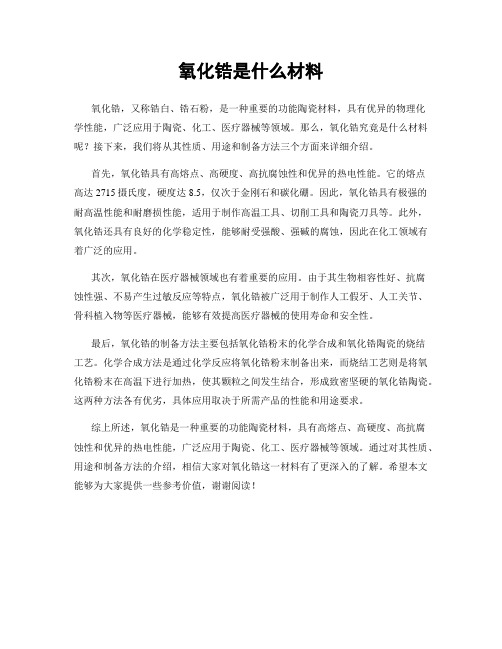
氧化锆是什么材料
氧化锆,又称锆白、锆石粉,是一种重要的功能陶瓷材料,具有优异的物理化
学性能,广泛应用于陶瓷、化工、医疗器械等领域。
那么,氧化锆究竟是什么材料呢?接下来,我们将从其性质、用途和制备方法三个方面来详细介绍。
首先,氧化锆具有高熔点、高硬度、高抗腐蚀性和优异的热电性能。
它的熔点
高达2715摄氏度,硬度达8.5,仅次于金刚石和碳化硼。
因此,氧化锆具有极强的耐高温性能和耐磨损性能,适用于制作高温工具、切削工具和陶瓷刀具等。
此外,氧化锆还具有良好的化学稳定性,能够耐受强酸、强碱的腐蚀,因此在化工领域有着广泛的应用。
其次,氧化锆在医疗器械领域也有着重要的应用。
由于其生物相容性好、抗腐
蚀性强、不易产生过敏反应等特点,氧化锆被广泛用于制作人工假牙、人工关节、骨科植入物等医疗器械,能够有效提高医疗器械的使用寿命和安全性。
最后,氧化锆的制备方法主要包括氧化锆粉末的化学合成和氧化锆陶瓷的烧结
工艺。
化学合成方法是通过化学反应将氧化锆粉末制备出来,而烧结工艺则是将氧化锆粉末在高温下进行加热,使其颗粒之间发生结合,形成致密坚硬的氧化锆陶瓷。
这两种方法各有优劣,具体应用取决于所需产品的性能和用途要求。
综上所述,氧化锆是一种重要的功能陶瓷材料,具有高熔点、高硬度、高抗腐
蚀性和优异的热电性能,广泛应用于陶瓷、化工、医疗器械等领域。
通过对其性质、用途和制备方法的介绍,相信大家对氧化锆这一材料有了更深入的了解。
希望本文能够为大家提供一些参考价值,谢谢阅读!。
凝胶剂制备氧化铝多孔陶瓷工艺流程

凝胶剂制备氧化铝多孔陶瓷工艺流程英文回答:Sol-Gel Processing of Porous Alumina Ceramics.The sol-gel process is a versatile technique for the fabrication of porous alumina ceramics. The process involves the hydrolysis and condensation of a metal alkoxide precursor, typically aluminum sec-butoxide (ASB), in an alcohol solvent. The resulting sol is then gelled to form a rigid network, which is subsequently dried and sintered to produce a porous ceramic.The sol-gel process offers several advantages for the fabrication of porous alumina ceramics. First, the process is relatively simple and can be easily scaled up for commercial production. Second, the sol-gel process allows for the precise control of pore size and morphology. Third, the process can be used to produce ceramics with a wide range of properties, including high porosity, high surfacearea, and high thermal stability.The sol-gel process for the fabrication of porous alumina ceramics typically involves the following steps:1. Preparation of the sol: The sol is prepared by hydrolyzing and condensing ASB in an alcohol solvent. The hydrolysis reaction is typically carried out in the presence of a catalyst, such as hydrochloric acid. The condensation reaction is then carried out by adding water to the sol.2. Gelation: The sol is gelled by heating it to a temperature above the gelation point. The gelation point is the temperature at which the sol transitions from a liquid to a solid state.3. Drying: The gel is dried to remove the solvent. The drying process is typically carried out at a low temperature to prevent the gel from cracking.4. Sintering: The dried gel is sintered at a hightemperature to produce a porous ceramic. The sintering temperature is typically between 1200°C and 1600°C.The sol-gel process can be used to produce a wide range of porous alumina ceramics with different pore sizes and morphologies. The pore size and morphology of the ceramic can be controlled by varying the sol preparation conditions, such as the hydrolysis ratio, the condensation ratio, andthe gelation temperature.Porous alumina ceramics fabricated by the sol-gel process have a wide range of applications, including filtration, catalysis, and sensors.中文回答:凝胶剂制备氧化铝多孔陶瓷工艺流程。
高锆砖制作流程

高锆砖制作流程
高锆砖是目前最常用的高温陶瓷材料之一,广泛应用于电子、陶瓷、
航空航天等领域。
其特点是耐高温、耐腐蚀、抗氧化、热物性稳定,
而且不易变形。
其制作过程主要包括以下几个步骤:
1.原材料选取
选择高纯度、细颗粒、均一分布的氧化锆和氧化钆作为主要原材料。
对于高锆砖来说,氧化锆的纯度一般需达到99.5%以上。
2.混合制备
将原材料称量后混合制备。
在混合过程中,应注意原材料的充分混合,避免出现杂质。
3.制备成型
将混合好的原材料放入制备成型机中,进行成型。
常用的成型方法包
括半干压法、等静压法和注浆法等。
4.烧结处理
在烧结处理过程中,高锆砖被暴露于高温高压环境下。
具体烧结条件因材质不同而异,但一般需要在1500℃-1700℃的高温下经历数小时的烧结时间。
而且,在烧结过程中,还需对烧结温度、时间和烧结气氛进行严格控制。
5.加工调整
在烧结完成后,需要对高锆砖进行加工、研磨和调整以达到所需规格和尺寸。
这些加工通常需要利用高精度的加工设备和工具进行。
总之,高锆砖的制作过程需要精密仪器设备的配合和高精度的技术操作,而且还要严格控制烧结温度、时间和烧结气氛等环节。
只有在整个加工过程中掌握好每一个环节,才能制造出优质的高锆砖产品。
一种电熔氧化锆生产工艺
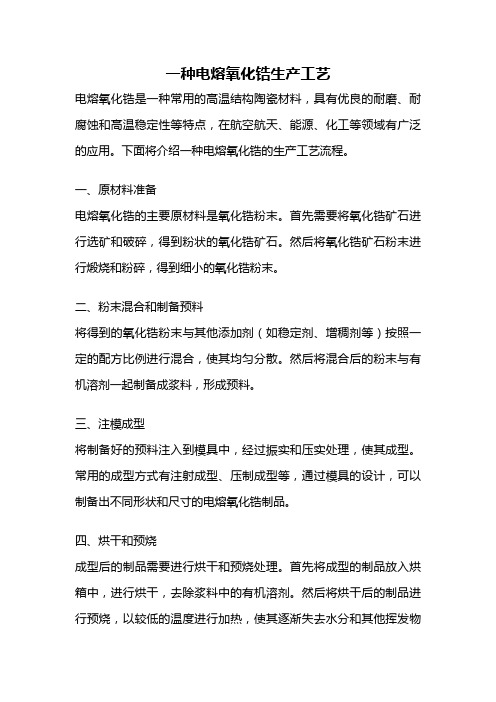
一种电熔氧化锆生产工艺电熔氧化锆是一种常用的高温结构陶瓷材料,具有优良的耐磨、耐腐蚀和高温稳定性等特点,在航空航天、能源、化工等领域有广泛的应用。
下面将介绍一种电熔氧化锆的生产工艺流程。
一、原材料准备电熔氧化锆的主要原材料是氧化锆粉末。
首先需要将氧化锆矿石进行选矿和破碎,得到粉状的氧化锆矿石。
然后将氧化锆矿石粉末进行煅烧和粉碎,得到细小的氧化锆粉末。
二、粉末混合和制备预料将得到的氧化锆粉末与其他添加剂(如稳定剂、增稠剂等)按照一定的配方比例进行混合,使其均匀分散。
然后将混合后的粉末与有机溶剂一起制备成浆料,形成预料。
三、注模成型将制备好的预料注入到模具中,经过振实和压实处理,使其成型。
常用的成型方式有注射成型、压制成型等,通过模具的设计,可以制备出不同形状和尺寸的电熔氧化锆制品。
四、烘干和预烧成型后的制品需要进行烘干和预烧处理。
首先将成型的制品放入烘箱中,进行烘干,去除浆料中的有机溶剂。
然后将烘干后的制品进行预烧,以较低的温度进行加热,使其逐渐失去水分和其他挥发物质,增强其强度和稳定性。
五、电熔烧结预烧后的制品需要进行电熔烧结处理,以提高其致密性和机械性能。
将预烧后的制品放入电熔炉中,通过高温下的电热作用,使其表面熔化和烧结。
在电熔炉中,通过控制温度和热处理时间,使氧化锆颗粒之间发生烧结反应,形成致密的晶体结构。
六、后处理经过电熔烧结处理后的制品还需要进行后处理。
包括去除表面氧化物、调整制品的形状和尺寸等工艺步骤。
最后,通过抛光、清洗等工序,得到最终的电熔氧化锆制品。
以上就是一种电熔氧化锆的生产工艺流程。
通过选矿、破碎、煅烧和粉碎等步骤,制备出细小的氧化锆粉末。
然后将粉末与添加剂混合,制备成浆料,注入模具中进行成型。
成型后的制品经过烘干、预烧和电熔烧结等处理,最终得到高密度、高强度的电熔氧化锆制品。
这种生产工艺具有工艺简单、成本低、制品质量稳定等优点,广泛应用于各个领域。
氧化锆陶瓷烧成注意事项
氧化锆陶瓷烧成注意事项氧化锆陶瓷是一种应用广泛的高性能陶瓷材料,常用于制作人工牙齿、耳科植入物、髋关节假体等医疗器械,以及高温工业领域的零件。
在氧化锆陶瓷的烧成过程中,需要注意以下几个方面。
1. 烧结温度控制:氧化锆陶瓷的烧结过程需要在高温下进行。
一般来说,烧结温度应该控制在1450以上,但不能超过其熔点2700。
烧结温度过低会导致陶瓷致密性不足,力学性能低;而烧结温度过高则容易使陶瓷发生烧结收缩不均匀、显微组织不稳定等问题。
因此,需要根据具体情况选择适当的烧结温度。
2. 烧结时间控制:氧化锆陶瓷的烧结时间通常较长,一般需要10到12小时。
在烧结过程中,需要确保陶瓷在足够长的时间内保持在高温下,使其完全烧结。
短时间的烧结可能导致陶瓷的致密性不足,力学性能下降。
3. 烧结环境控制:在氧化锆陶瓷的烧结过程中,烧结环境对其性能具有重要影响。
一般来说,氧化锆陶瓷的烧结需要在氧气或惰性气体环境下进行,以避免烧结反应中氧化锆与空气中的氧气发生反应产生杂质。
同时,烧结环境中的湿度也需要注意,湿度过高会导致陶瓷表面出现气泡。
4. 烧结压力控制:烧结过程中的压力对氧化锆陶瓷的致密性和力学性能有一定影响。
一般来说,适当的烧结压力可以促进陶瓷颗粒之间的结合,并提高陶瓷的致密度。
但过高的烧结压力可能导致陶瓷烧结收缩不均匀,产生应力集中现象。
5. 烧结添加剂的控制:为了改善氧化锆陶瓷的烧结性能,有时会在原料中添加适量的助烧剂,如氧化铝、氮化硅等。
添加剂的控制需要根据具体情况,以避免添加剂过量或不足造成的问题。
总之,氧化锆陶瓷的烧成过程需要综合考虑多个因素,如烧结温度、烧结时间、烧结环境、烧结压力和添加剂的控制。
只有合理控制这些因素,才能获得具有良好性能的氧化锆陶瓷制品。
工业陶瓷的工艺流程
工业陶瓷的工艺流程工业陶瓷是一种特种陶瓷,具有很高的机械强度、耐磨性和耐高温性能,广泛应用于机械、电子、航空航天等领域。
下面将介绍工业陶瓷的主要工艺流程。
首先,工业陶瓷的原料采购是工艺流程的第一步。
工业陶瓷一般由氧化铝、氧化锆、碳化硅等材料组成,这些原料需要根据产品的要求进行选购。
同时,还需要采购配套的助剂和添加剂,如粘结剂、稀释剂等。
第二步是原料的制备和配料。
首先将采购的原料进行研磨和筛分,得到粉末。
然后按照设计配方,将不同种类的原料按照一定比例混合。
混合可以采用机械混合或湿法混合的方式进行,以确保混合均匀。
第三步是成型。
成型是将配料好的陶瓷粉末转变为固态的过程。
常见的成型方法有压制成型、注射成型、挤出成型等。
压制成型是将陶瓷粉末放入模具中,用压力使其成型。
注射成型是将陶瓷粉末与稀释剂混合,通过注射机将混合物注射到模具中成型。
挤出成型是将陶瓷粉末与稀释剂混合后放入挤出机中,通过挤出机将混合物挤出模具成型。
第四步是烧结。
烧结是将成型后的陶瓷坯体进行高温处理,使其形成致密的陶瓷材料。
烧结过程中需要控制烧结温度、时间和气氛,以保证陶瓷材料的性能。
烧结可以分为单向烧结和等温烧结两种方式。
单向烧结是将陶瓷坯体放入炉中,在升温和降温的过程中控制温度梯度进行烧结。
等温烧结是将陶瓷坯体放入炉中,在一定温度范围内保持恒温进行烧结。
第五步是加工和精密加工。
烧结后的陶瓷材料一般需要进行加工,以获得所需的几何形状和尺寸。
常见的加工方式有精密研磨、打磨、抛光等。
精密加工是在已烧结的陶瓷材料上进行,需要使用专业的设备和工具进行。
最后一步是质量检验和包装。
质量检验是对加工后的陶瓷产品进行检查,确保其符合设计要求和标准。
常见的检验项目包括外观质量、尺寸精度、物理性能等。
合格的产品经过检验后,将进行包装和标识,以便运输和使用。
综上所述,工业陶瓷的工艺流程包括原料采购、原料制备和配料、成型、烧结、加工和精密加工、质量检验和包装等步骤。
- 1、下载文档前请自行甄别文档内容的完整性,平台不提供额外的编辑、内容补充、找答案等附加服务。
- 2、"仅部分预览"的文档,不可在线预览部分如存在完整性等问题,可反馈申请退款(可完整预览的文档不适用该条件!)。
- 3、如文档侵犯您的权益,请联系客服反馈,我们会尽快为您处理(人工客服工作时间:9:00-18:30)。
本技术公开了一种多孔氧化锆陶瓷的制备方法,先将氧化锆和氧化钇按重量配比混合均匀制备混合料;然后制备聚丙烯醇水溶液和氯化铵水溶液:将所得混合料和溶液一起放入球
磨机中进行球磨;向球磨后的浆料中加入粘结剂、淀粉溶液、表面活性剂,继续球磨
30min;之后加入10%的氯化铵水溶液,高速下球磨3min,迅速倒入模具中成型;将模具和模具中的浆料放入烘箱中进行发泡;然后放入冷冻箱中冷冻,形成凝胶;将凝胶样品进行脱模,经干燥后烧结,得到多孔氧化锆陶瓷。
本技术用磷酸锌作为粘结剂,提高了粘结强度,降低了污染,得到的多孔氧化锆陶瓷孔隙率高,孔径均匀,提高了多孔氧化锆陶瓷的性能。
权利要求书
1.一种多孔氧化锆陶瓷的制备方法,其特征在于包括以下步骤:
(1)制备氧化锆混合料:首先将氧化锆粉末和氧化钇粉末按照重量配比混合均匀;
(2)制备聚丙烯醇水溶液:将聚丙烯醇与去离子水按照一定比例混合,配制聚氯丙烯醇水溶液;
(3)制备氯化铵水溶液:用分析纯氯化铵与去离子水配制成质量分数为15%的氯化铵水溶液;
(4)制备浆料:将步骤(1)-(3)所得混合料和溶液一起放入球磨机中,再放入刚玉球,球磨3h,得到浆料;
(5)向球磨后的浆料中加入粘结剂,并加入质量分数为3%的淀粉溶液,同时加入表面活性剂,然后继续球磨30mi n;之后加入一定量质量分数为10%的氯化铵水溶液,然后在高速下球磨3mi n,之后迅速倒入模具中成型;
(6)将模具和模具中的浆料放入烘箱中进行发泡;然后将模具和模具中的浆料放入冷冻箱中
冷冻8h,冷冻的温度为零下15度,在冷冻过程中形成凝胶;
(7)将凝胶样品进行脱模,然后将凝胶样品放入乙醇水溶液中10h;
(8)将凝胶样品从乙醇溶液中取出,经干燥后在氩气氛保护下进行烧结3h,烧结后自然冷却至室温,得到多孔氧化锆陶瓷。
2.如权利要求1所述的方法,其特征在于:步骤(1)所述氧化锆粉末和氧化钇粉末的重量比为20:1。
3.如权利要求1所述的方法,其特征在于:步骤(2)将聚丙烯醇与去离子水按照一定比例混合后,于70摄氏度下超声分散1h,配制成质量分数为10%的聚丙烯醇水溶液。
4.如权利要求1所述的方法,其特征在于:步骤(5)所述粘结剂为磷酸锌粘结剂,该磷酸锌粘结剂的加入量为步骤(1)氧化锆混合料质量的2-6%。
5.如权利要求1所述的方法,其特征在于:步骤(5)所述的表面活性剂为十二烷基硫酸钠,十二烷基硫酸钠的加入量为步骤(1)氧化锆混合料质量的2-4%。
6.如权利要求1所述的方法,其特征在于:步骤(5)所述氯化铵水溶液的加入量为步骤(1)氧化锆混合料质量的3-5%。
7.如权利要求1所述的方法,其特征在于:步骤(6)烘箱温度为90℃,发泡时间为2h。
8.如权利要求1所述的方法,其特征在于:步骤(8)干燥的温度为120℃,干燥的时间为12h,所述的烧结温度为1600℃。
技术说明书
一种多孔氧化锆陶瓷的制备方法
技术领域
本技术涉及多孔陶瓷技术领域,具体涉及一种多孔氧化锆陶瓷的制备方法。
背景技术
多孔陶瓷由于兼有良好的机械性能、化学和热稳定性,作为一种绿色材料其过滤性能广泛应用。
氧化锆材料具有优良的物理、化学性能,用氧化锆材料制作多孔材料能够兼具良好
的机械性能、化学和热稳定性以及选择透氧性。
多孔陶瓷的制备方法有多种,比如:添加造孔剂法,有机泡沫法和发泡法。
添加造孔剂法是利用有机造孔剂在高温下燃尽或者挥发而在陶瓷体中留下孔隙,这种方法工艺简单,孔隙率可调节,但孔隙率低,制备过程中会排放污染物。
有机泡沫法是利用有机泡沫所具有的开孔三维网状骨架的特殊结构,将制备好的浆料均匀地涂敷在有机泡沫网状体上,干燥后烧掉有机泡沫体而获得一种网眼多孔陶瓷。
该方法制备过程中有机体的强度和弹性对多孔材料的结构和性能有很大影响,同时易产生残留体和有毒气体,对环境造成污染。
发泡法制备的多孔陶瓷孔隙率一般可以大于70%,发泡法一般会添加一些有机物,在陶瓷浆料发泡后固化浆料,这些有机会都会在烧结时燃烧或挥发,污染环境。
上述方法均存在孔隙率不高,排放污染物的问题。
技术内容
本技术旨在提供一种多孔氧化锆陶瓷的制备方法,用磷酸锌作为粘结剂,增强了粘结剂与氧化锆陶瓷的适应性,提高了粘结强度,而且降低了污染,用淀粉做造孔剂,得到的多孔氧化锆陶瓷孔隙率高,可以达到80%以上,孔径均匀,没有明显的特大孔,以中孔为主,提高了多孔氧化锆陶瓷的性能。
本技术的目的及解决其技术问题是采用以下技术方案来实现的。
依据本技术提出的一种多孔氧化锆陶瓷的制备方法,包括以下步骤:
(1)制备氧化锆混合料:首先将氧化锆粉末和氧化钇粉末按照重量配比混合均匀;
(2)制备聚丙烯醇水溶液:将聚丙烯醇与去离子水按照一定比例混合,配制聚氯丙烯醇水溶液;
(3)制备氯化铵水溶液:用分析纯氯化铵与去离子水配制成质量分数为15%的氯化铵水溶液;
(4)制备浆料:将步骤(1)-(3)所得混合料和溶液一起放入球磨机中,再放入刚玉球,球磨3h,得到浆料;
(5)向球磨后的浆料中加入粘结剂,并加入质量分数为3%的淀粉溶液,同时加入表面活性剂,然后继续球磨30min;之后加入一定量质量分数为10%的氯化铵水溶液,然后在高速下球磨3min,之后迅速倒入模具中成型;
(6)将模具和模具中的浆料放入烘箱中进行发泡;然后将模具和模具中的浆料放入冷冻箱中冷冻8h,冷冻的温度为零下15度,在冷冻过程中形成凝胶;
(7)将凝胶样品进行脱模,然后将凝胶样品放入乙醇水溶液中10h;
(8)将凝胶样品从乙醇溶液中取出,经干燥后在氩气氛保护下进行烧结3h,烧结后自然冷却至室温,得到多孔氧化锆陶瓷。
本技术的目的及解决其技术问题还可采用以下技术措施进一步实现。
前述的一种多孔氧化锆陶瓷的制备方法,其中,步骤(1)所述氧化锆粉末和氧化钇粉末的重量比为20:1。
前述的一种多孔氧化锆陶瓷的制备方法,其中,步骤(2)将聚丙烯醇与去离子水按照一定比例混合后,于70摄氏度下超声分散1h,配制成质量分数为10%的聚丙烯醇水溶液。
前述的一种多孔氧化锆陶瓷的制备方法,其中,步骤(5)所述粘结剂为磷酸锌粘结剂,该磷酸锌粘结剂的加入量为步骤(1)氧化锆混合料质量的2-6%。
前述的一种多孔氧化锆陶瓷的制备方法,其中,步骤(5)所述的表面活性剂为十二烷基硫酸钠,十二烷基硫酸钠的加入量为步骤(1)氧化锆混合料质量的2-4%。
前述的一种多孔氧化锆陶瓷的制备方法,其中,步骤(5)所述氯化铵水溶液的加入量为步骤(1)氧化锆混合料质量的3-5%。
前述的一种多孔氧化锆陶瓷的制备方法,其中,步骤(6)烘箱温度为90℃,发泡时间为2h。
前述的一种多孔氧化锆陶瓷的制备方法,其中,步骤(8)干燥的温度为120℃,干燥的时间为12h,所述的烧结温度为1600℃。
本技术用磷酸锌作为粘结剂,增强了粘结剂与氧化锆陶瓷的适应性,提高了粘结强度,而且降低了污染,利用淀粉溶液进行造孔,不产生有害气体,并且得到的多孔氧化锆陶瓷孔隙率高,可以达到80%以上,且孔径均匀,没有明显的特大孔,以中孔为主,提高了多孔氧化锆陶瓷的性能,其耐压强度可达到2.2MPa。
具体实施方式
以下参照具体的实施例来说明本技术。
这些实施例仅用于说明本技术,其不以任何方式限制本技术的范围。
本技术提供了一种多孔氧化锆陶瓷的制备方法,具体分为8个步骤:
(1)制备氧化锆混合料:首先将氧化锆粉末和氧化钇粉末按照重量比为20:1的比例混合均匀;
(2)制备聚丙烯醇水溶液,将聚丙烯醇与去离子水按照一定比例混合,于70摄氏度下超声分散1h,配制质量分数为10%的聚丙烯醇水溶液;
(3)制备氯化铵水溶液:用分析纯氯化铵与去离子水配制成质量分数为15%的氯化铵水溶液;
(4)制备浆料:将步骤(1)-(3)所得混合料和溶液一起放入球磨机中,再放入刚玉球,球磨3h,得到浆料;
(5)向球磨后的浆料中加入磷酸锌,该磷酸锌的加入量为步骤(1)氧化锆混合料质量的2-6%,并加入质量分数为3%的淀粉溶液作为造孔剂,同时加入十二烷基硫酸钠作为表面活性剂,然后继续球磨30min;之后加入一定量质量分数为10%的氯化铵水溶液,此时,氯化铵水溶液的加入量占步骤(1)氧化锆混合料质量的3-5%,然后在高速下球磨3min,迅速倒入模具中成型;
(6)将模具和模具中的浆料放入烘箱中进行发泡,淀粉溶液在浆料中造孔,烘箱温度为90度,发泡时间为2h;然后将模具和模具中的浆料放入冷冻箱中冷冻8h,冷冻的温度为零下15度;在冷冻过程中形成凝胶;
(7)将凝胶样品进行脱模,然后将凝胶样品放入乙醇水溶液中12h,用乙醇替换其中的水份,避免后期干燥和烧结过程中水份蒸发造成样品收缩。
(8)将凝胶样品从乙醇中取出,于120℃下干燥12h,然后在氮气氛保护下进行烧结3h,烧结温度为1600℃。
烧结后自然冷却至室温,得到多孔氧化锆陶瓷。
经测试,所得多孔氧化锆陶瓷的孔隙率为85%,抗压强度为2.2MPa。
以上所述,仅是本技术的较佳实施例而已,并非对本技术做任何形式上的限制,虽然本技术已以较佳实施例揭露如上,然而并非用以限定本技术,任何熟悉本专业的技术人员,在不脱离本技术技术方案范围内,当可利用上述揭示的技术内容做出些许更动或修饰为等同变化的等效实施例,但凡是未脱离本技术技术方案的内容,依据本技术的技术实质对以上实施例所做的任何简单修改、等同变化与修饰,均仍属于本技术技术方案的范围内。